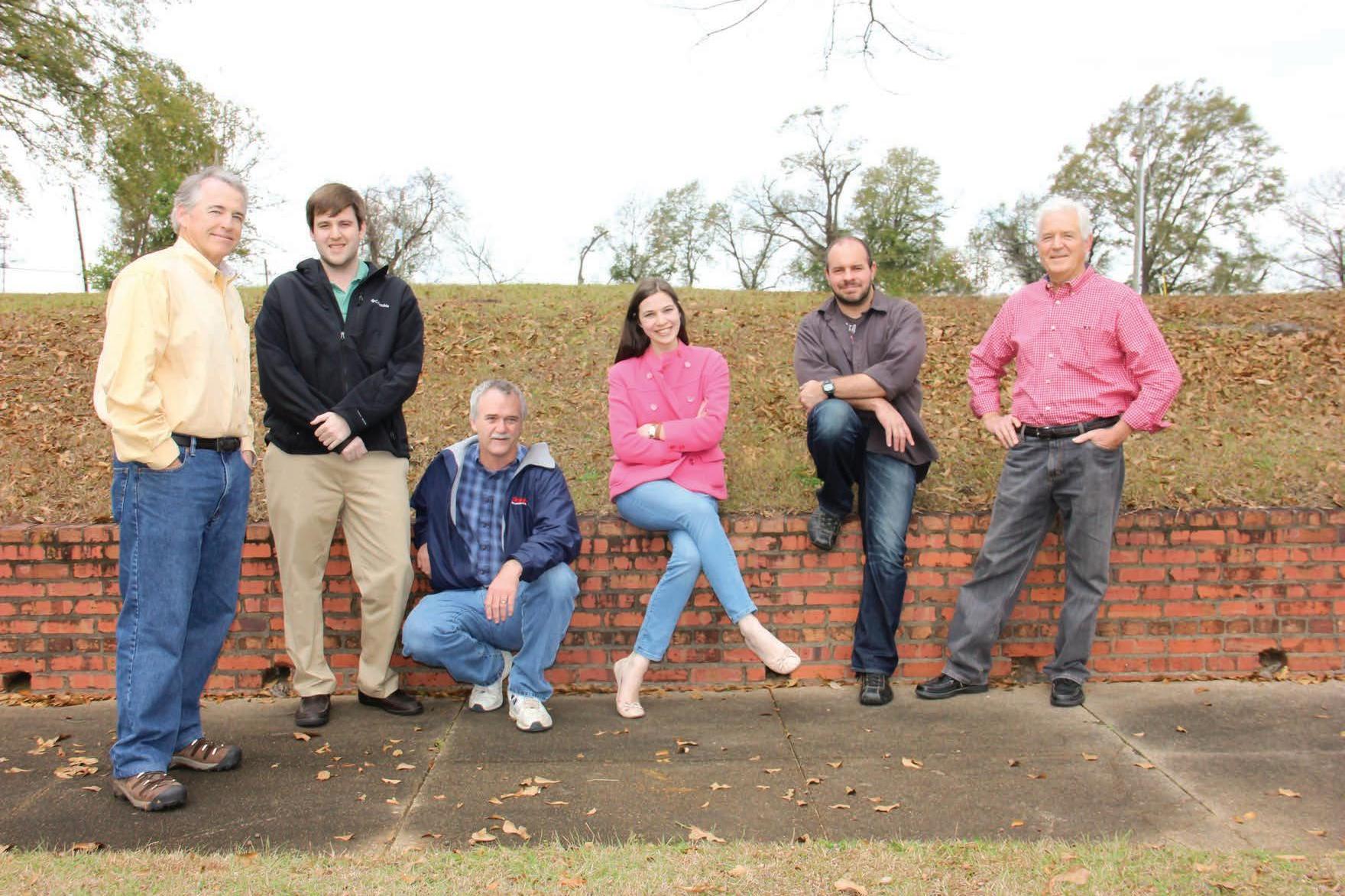
38 minute read
Southern Stumpin
By David Abbott • Managing Editor • Ph. 334-834-1170 • Fax: 334-834-4525 • E-mail: david@hattonbrown.com
Optimistic Outlook
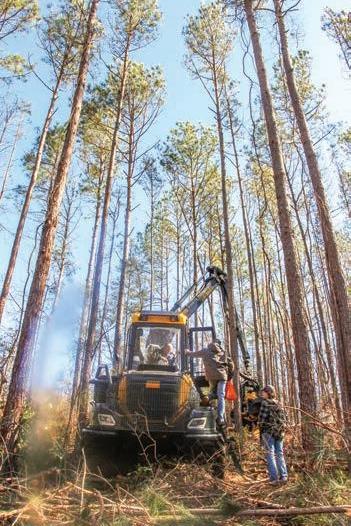
Forestry industry shows, association meetings and live demos have been a rarity for the last year, many replaced by virtual meetings. But in perhaps a sign of growing confidence that a return to normalcy could be in sight, Alabama logging machinery dealer Equipment Link, Inc. hosted a live demo on Saturday, February 20. The Maplesville-based dealer is opening its second location near the demo site in Grove Hill in March, about 100 miles from Maples ville. This event served to introduce Equipment Link to potential custo mers in the region. “This was part of our open house,” The demo attracted loggers and landowners from Alabama and Mississippi. owner Tommy Moore says. “The last time, we did its opportunities in the South. At least one logging business. In the ’80s and ’90s he worked with both it from Maplesville and we did live demos in the operation from Mississippi is reportedly planning Mike Guy at Barko (and later Tigercat) dealer morning then served lunch in the shop. But right to buy a Ponsse set after seeing it in action, and G&S Equipment in Prattville, Ala. and Gene Taynow, with Covid, we opted out from all that due to Moore reports several other promising connections lor at Timberjack (and later John Deere) dealer social distancing.” They decided this year to keep it were made. Warrior Tractor. For five years he was in business outdoors, with a morning demo in the woods, serv- Laneville Mulching and Grading owner Dave with Clark Salie, the son of Bill Salie, who used to ing on site grilled Conecuh dogs (a popular sausage Wenger sent a Barko carrier fitted with a Denis own timber dealer Bama Wood in Montgomery. made in Conecuh County, Alabama). Cimaf mulching attachment for the event. Wenger Later he went to work with the Parnell family’s
Equipment Link carries Barko, CSI, Delfab, is a friend and customer to Moore, and they’ve timber operation based in Maplesville. Rotobec, Big John trailers and Eco-Tracks, and known each other a long time. “He bought a 930 “Jimmy Parnell and I went to school together at added Ponsse to the lineup a year ago. Representa- Barko from us last year,” Moore says. With land - Auburn, and when he became president of Alatives from several of the manufacturers were on owners among those in attendance, this provided a bama Farmers Federation, I kind of filled his role,” hand to support their dealer and meet with cus- good opportunity to give exposure both to the Bar - Moore says. He was a manager for Parnell, Inc., he tomers. A number of Ponsse people made the trip ko machine and to Wenger’s business. Micah Hol- says, with the vision of one day maybe getting from Wisconsin to answer questions about their cut loway, who supervises the mulching side of Lane - back into the equipment end of it. An opportunity to length system. David Sanders with Rotobec was ville’s business, operated the mulcher for the demo. soon manifested. “Lo and behold, in April of 2017, there, as were Andy Weisel and Kevin Lee from Moore estimates about 100 folks showed up the late Brad Massey from Barko came to me askBarko. Tom Hirt of Delfab had planned to attend from Alabama and Mississippi, not counting dealer ing if I was interested in taking on the Barko line,” but couldn’t make it due to the recent winter and manufacturer employees. He was proud to he recalls. weather crisis in Texas; weather also prevented have such strong attendance. “It was a wet week Shortly thereafter, Moore received a cancer diagCSI’s Ralph Metcalf and Dennis An drews from and we could have been limited on our crowd nosis. He says his service manager and the Parnells coming down. All of the support, even from those because people needed to work,” he says. “But stepped up to carry the load while he was in treatwho couldn’t make it in person, was much appreci- they still came out, so we were very thankful.” ment. With cancer now in his rear view mirror, he ated. “We had very good representation from our The new Equipment Link location in Grove Hill says, it afforded him time to reflect on and apprecimanufacturers,” Moore says. “We were very has been in development for about a year but has ate all the blessings in life. “Our industry is such a pleased, they were very supportive.” been delayed by pandemic-related factors and tight knit group,” he says. “The relationships you
Ponsse brought a Buffalo forwarder and Ergo weather. Moore expects to have the doors open by build is probably the most rewarding part of it, harvester, allowing attendees to take a ride with an middle of March. The Maplesville store opened in because it can be a tough business monetarily and a experienced operator and see firsthand what the April 2018. challenge more often than not, but that’s what CTL machines can do. Ponsse is optimistic about Moore himself has a long background in the keeps you going.” SLT
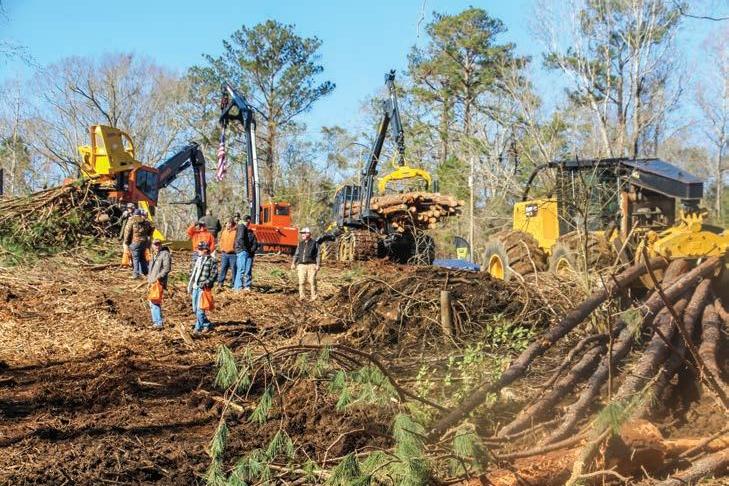
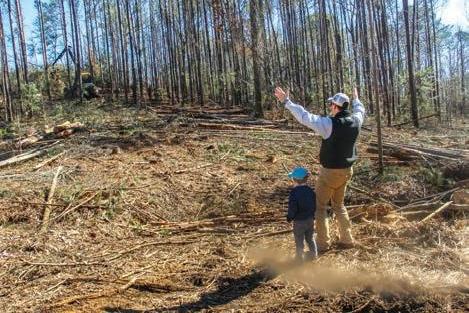
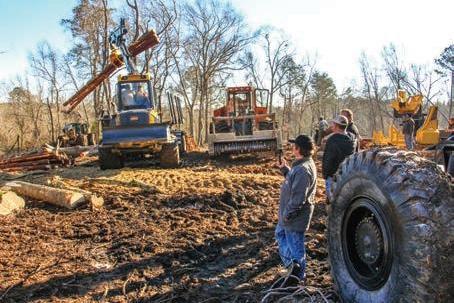
YouTuber Levi Spring will be posting a video to his Buckwild with Bubbarudy channel. Tommy Moore, left, visited friends, vendors and customers. For many, it was a family affair.

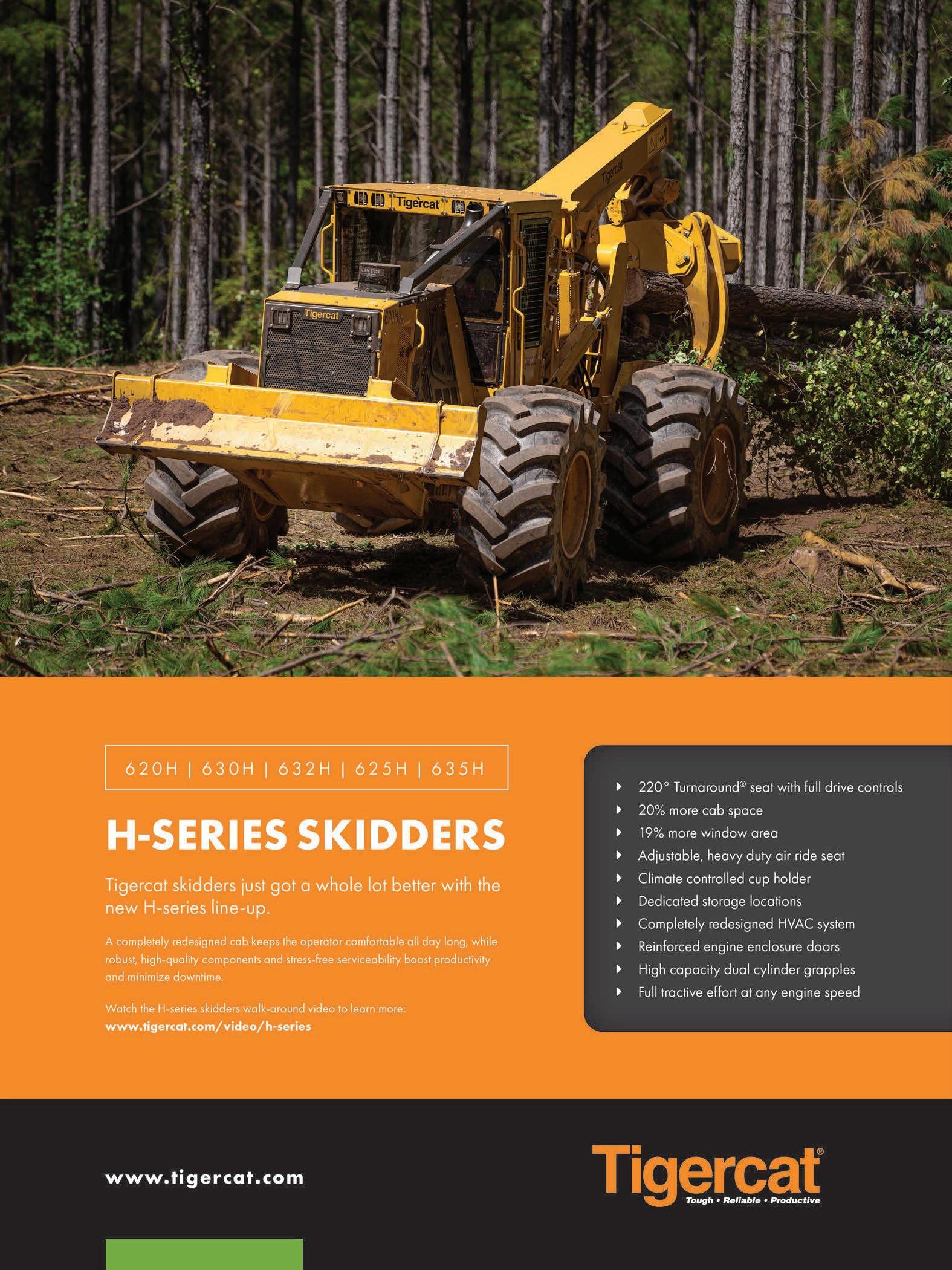
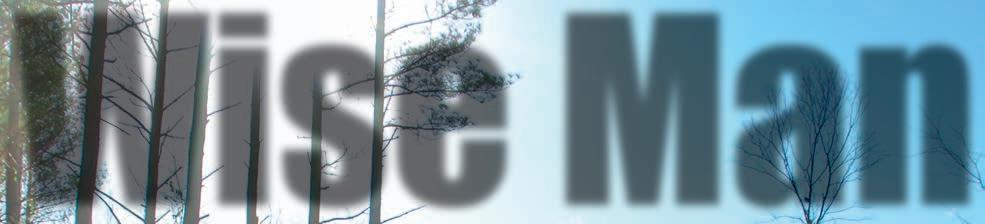
■ Pastor Dennis Wiseman juggles running two crews with his responsibilities as a minister of God.
By David Abbott

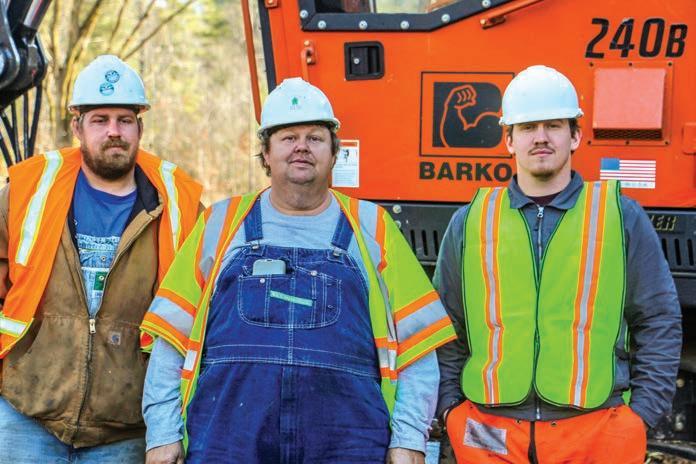
NIOTA, Tenn.
It may be a few months past Christmas, but there’s room for Jesus stories all year. While Matthew’s Gospel may not explicitly identify them as “Three Kings of Orient” like the song says, it does tell of three wise men who went to Bethlehem seeking the newborn Savior, the baby Jesus.
Wise men, it’s said, still seek Him. The Bible also says, in Proverbs 9:10, that the fear of the Lord is the beginning of wisdom. On both counts, surely, Dennis Wiseman, 45, embodies his surname well.
A lifelong logger, Wiseman is, first and foremost, a man of faith, raised in a Baptist church. But that didn’t keep him from going astray in his youth. “I was an alcoholic, and a bad one,” he’s strong enough to admit. “I got on drugs and about died, but God put me in my place and the Lord saved me one day.”
He was around 30 then. “God changed me completely, changed my world all the way around,” he testifies. “I mean it has just been amazing.”
Wiseman believes God called him to preach shortly after he experienced salvation. “I ran from it for a little while but finally answered the call,” he says. He’s been a pastor for a little over a decade, and now leads his third church, Victory Baptist Church in Madisonville, Tenn.
Pulling double duty as pastor and logger is a challenge, he admits. “It’s a lot of long hours, but God has always given me the ability and the opportunity to do both.”
Through the global pandemic of the past year, the church has been having just one service on Sunday morning—there are a lot of older people in his congregation, he ex plains, so it’s important to be responsible and considerate of their health. Normally, they also hold Wednesday and Sunday night services. Wiseman is a multitasker; he gets his sermons when he’s on one of his machines, wisely using his time to get two jobs done for the price of one. “That is just my time with the Lord, especially on Saturdays,” he says. “I can get on the cutter and spend all day by myself, just me and the Lord.”
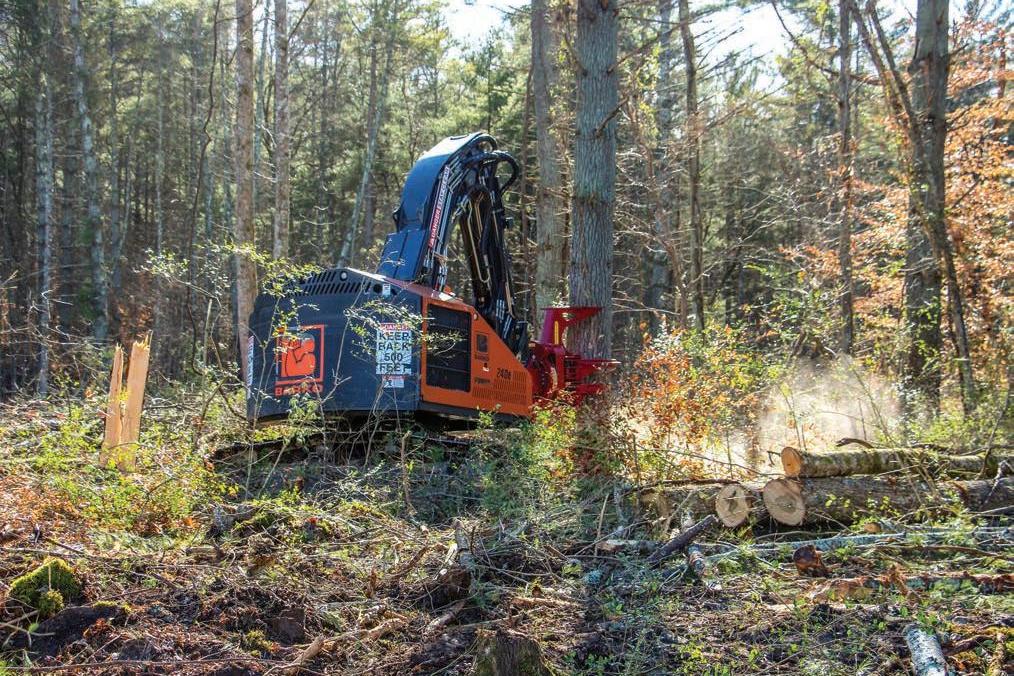
Wiseman loves his new Barko track cutter, which he says is perfect for the terrain in which he usually works.
Three Wise Men: Dennis Wiseman, middle, flanked by his sons Tyler Wiseman, left, and Jacob Wiseman, right
8 l MARCH 2021 l Southern Loggin’ Times Double Time
Wiseman Logging has two crews. Crew 2 often works in higher elevation tracts. “There is a lot on my shoulders but I have good men on the mountain helping me,” Wiseman asserts. In early January, when Southern Loggin’ Times stopped by, this crew was cutting near Jones Gap Road, up Flat Top Mountain in the Soddy-Daisy area. Temperatures were cool, and cooler still at that elevation; in fact they’d been working in snow just a week earlier.
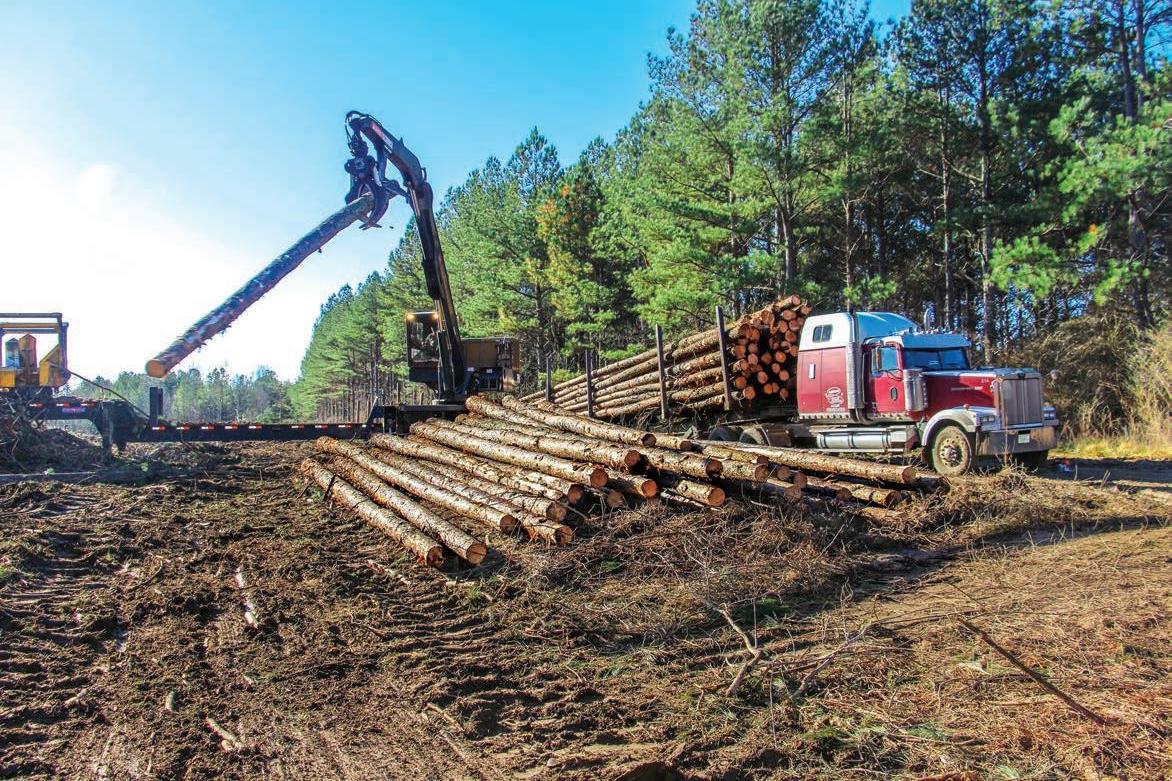
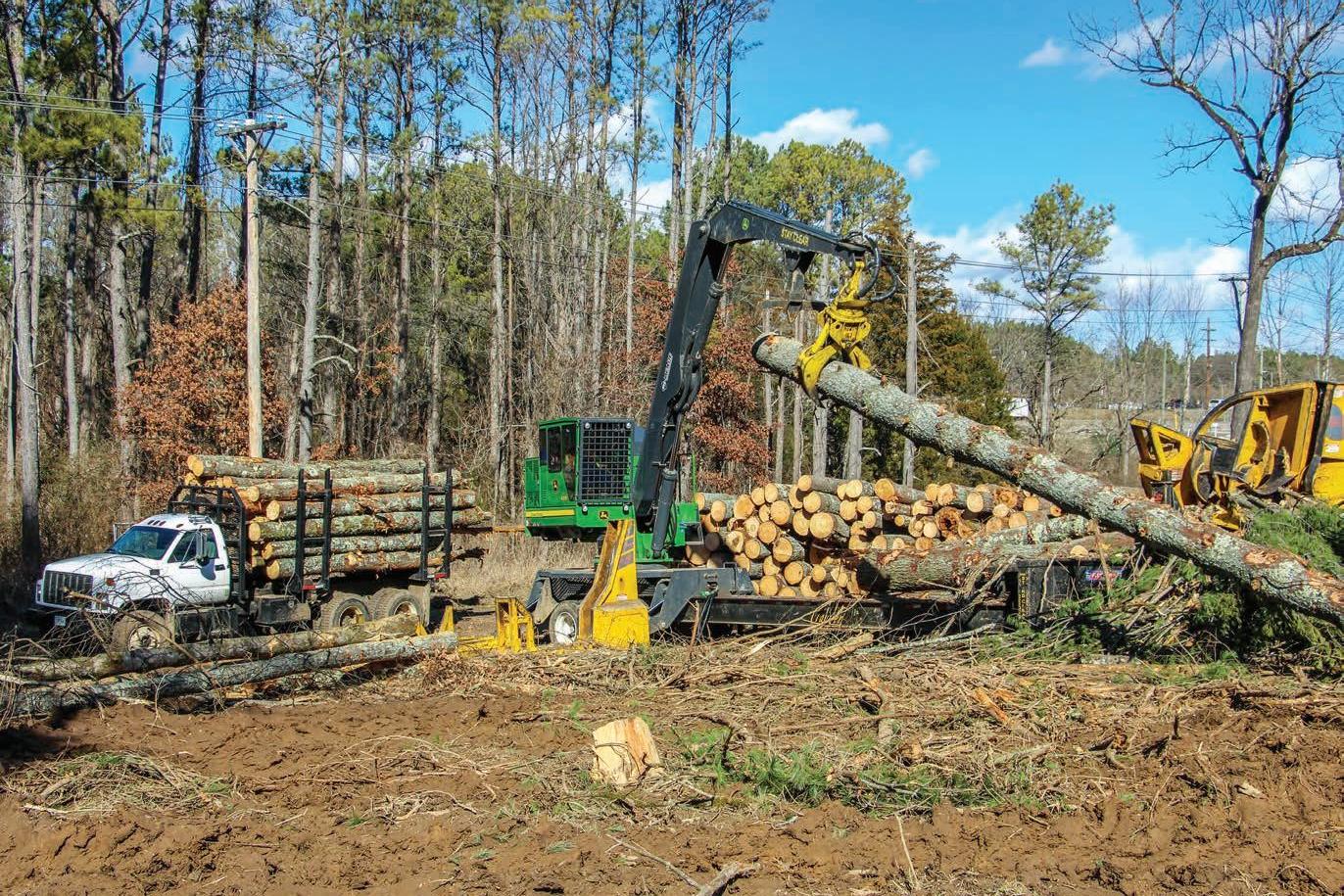
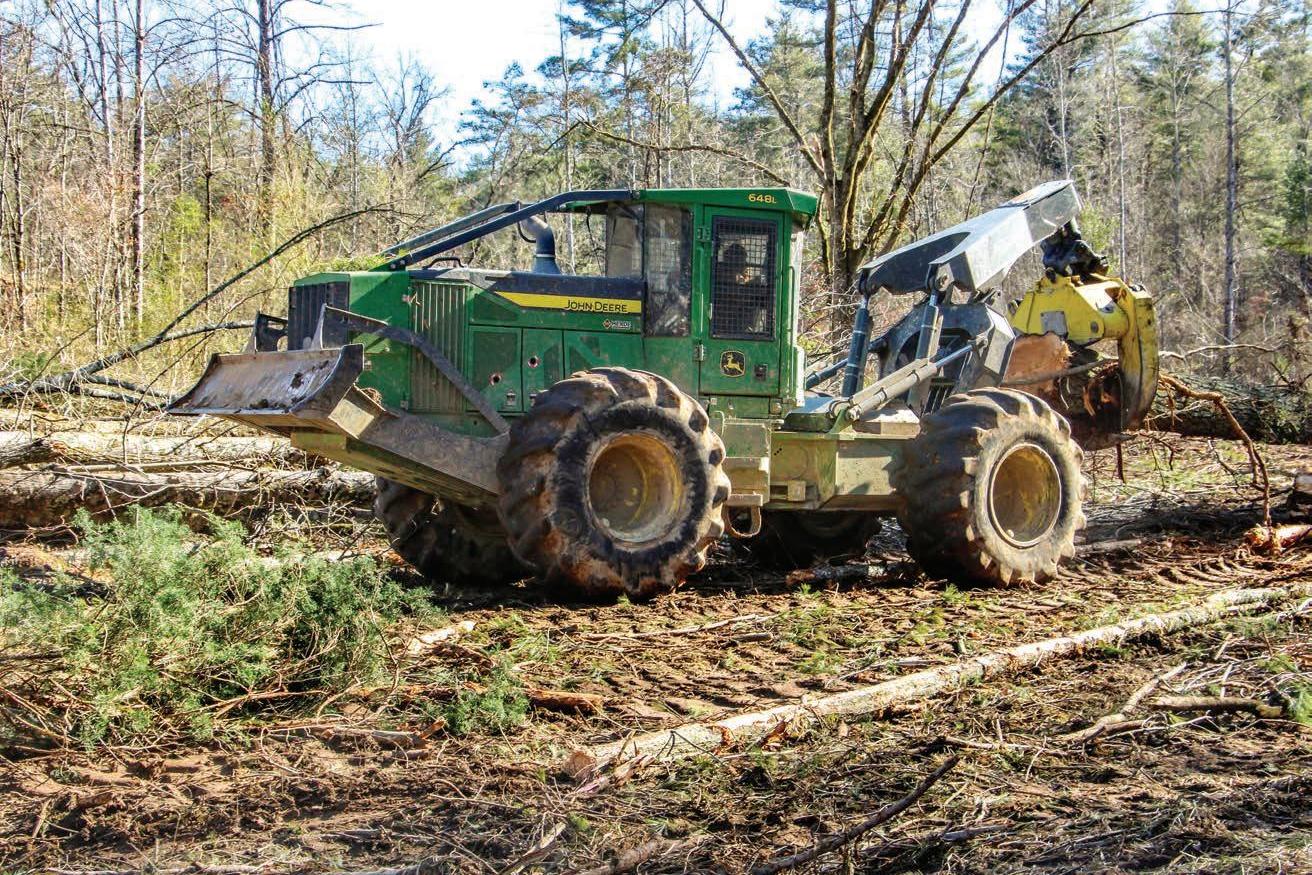
On Crew 1, Wiseman works with his sons to haul about 20 loads a week.
This crew uses a Barko 595 loader, John Deere 843L-II rubber-tired feller-buncher and Deere 748L-II skidder. They also have a second, older Deere skidder as a backup or to help out on long skids. John Jenkins mans the cutter. He and Wiseman went to school together. “We’ve known each other since diapers,” Wiseman says. Jenkins had his own logging business for years. “He decided he’d come to work for me, and I’m glad he did. He’s a good operator and a good supervisor.” Jenkins works closely with Dean Rollins, the loader operator, and skidder driver Ralph Cathey.
“One thing I do try to do is take care of my men,” Wiseman says. “God told me one day, ‘If you take care of my men, I’ll take care of you.’ And for the most part I have had some good workers over the years.”
Wiseman actually started Crew 1 last winter. He had a good operator running a track cutter who decided to move on to other things, forcing Wiseman to restructure his operation. “That left me holding the bag because I was running that crew,” he says.
Rollins, at the time a contract truck driver, stepped up and said he’d rather run the loader than drive a truck. “I bought his truck from him and he’s been running the loader for that crew ever since,” Wiseman says. Around the same time, Jenkins joined Wiseman as well. That gave him a crew he could trust to run on their own, freeing him up to start a second crew with his sons.
Wiseman’s older son, Tyler, had already been working with his dad for about three years; younger son Jake joined the family business more recently. Their dad’s intention is for them to learn how to run
John Deere machines on both crews come from Meade Tractor in Knoxville.
Contract truckers haul most Wiseman loads from both crews.
every machine and eventually the financial side of the business as well. “Then dad will work for you,” he’s told them.
When SLT visited, Crew 1 was working in Oak Ridge, about 40 miles from their home and about 75 miles from the other crew. On this job, Wiseman and sons use a Barko 240B tracked cutting machine, John Deere 437E loader, and Deere 648L skidder.
All the primary machines on both crews are 2016-2017 or 2020 models; until a few years ago, Wiseman worked with ’60s model Franklin and Prentice machines. “God gave me the opportunity to be able to update like that,” he believes.
Meade Tractor (John Deere) and Power Equipment (Barko), both in Knoxville, are Wiseman’s equipment dealers. Larry Prater is his salesman at Power Equipment. Insurance is with Forestry Mutual.
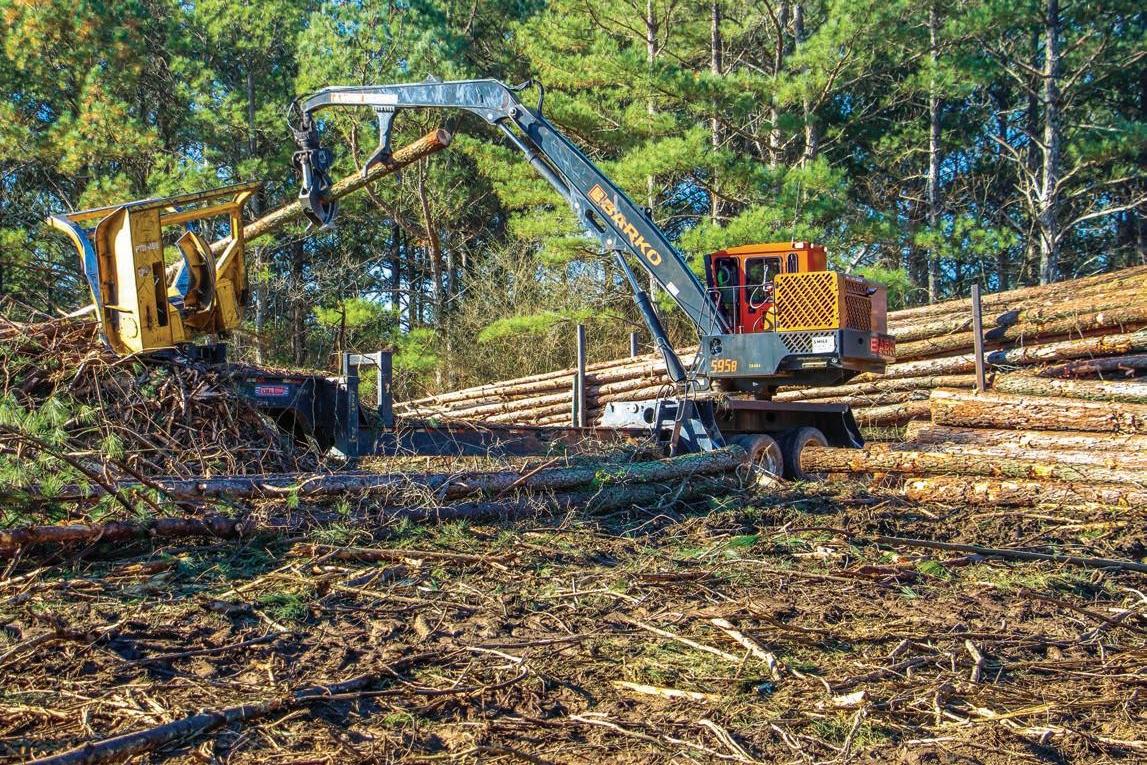
Upgrades
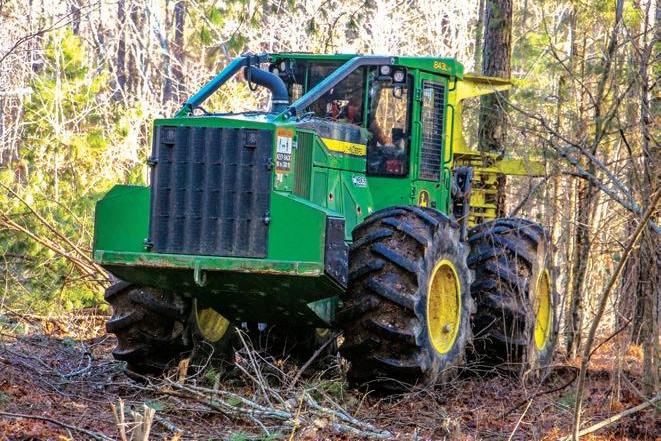
Wiseman has been in logging all his life. “We loaded it by hand when I was a kid,” he recalls. “I had my first pulpwood truck when I was 16 years old. My papaw logged, my mom’s dad, Ray Best. He was really special to me and taught me a lot. One thing he taught me was how to treat people and to always be on top of everything. In this business, you can lose $50,000 quick.”
The first rubber tired skidder Wiseman owned, purchased in the early ’90s, set him back a whopping $2,500, not counting what it cost to get it running. He paid another $5,000 for an old G model Prentice loader. Set up as such, he stayed small, hauling about 10 tandem loads a week, for years.
“And then one day, it just seemed like I couldn’t get it together,” he recalls. “I asked the Lord, ‘God what am I doing wrong? I’d like to have more.’ I knew the Bible teaches us not to covet. But the Lord spoke to me and said, ‘If you want more, you’ve got to put more into it.’” Following as he felt led by the Lord, Wiseman stepped out in faith…and it worked.
“Where I am today is because of Him,” the logger insists, “I have not forgotten where I came from. That 1967 model stuff, I thank Him just as much for that as for what I have today.” Persistence, he says, is one thing he’s learned. “Stick with it, don’t give up, look up, God will pull you through,” he advises.
“I have had some really rough times since I bought newer equipment but by the grace of God I have always been able to make the payments and God has blessed me beyond measure,” he says.
“There have been people who said that I’d never pay the first piece off.” By the grace of God, he says, he paid off his first new piece in midJanuary. “I have plenty more to go and I hope by the grace of God I am able to pay for every bit of it.”
His goal now, after paying off the rest, is to start trading every three years. “It seems so much better to stay in warranty,” he explains. “It’s easier to pay the payment than it is to pay the very expensive breakdowns that come up along the way.”
Barko loader on Crew 2 and cutter on Crew 1 come from Power Equipment in Knoxville.
Crew 2 is the high elevation and high production job.
Making Tracks
His newest piece is the Barko track cutter, added in July, 2020. It had a few little issues at first, he says, but Power Equipment has it working in good condition now. “The more I run it the better I like it,” he says. “I prefer it over a wheel cutter, for average Tennessee terrain. A wheel cutter is great, they’re fast, and they work real good in pine plantations, but these ditches and crevices just work so much better with the track cutter.”
Before this one, he had another track cutter, a John Deere 859M, but it was a lot bigger than what he typically needs for his normal logging applications. “The Deere was a great machine,” he stresses. “It performed great, it was stout and strong. It was just overkill.” Needing something more compact, he replaced it with the Barko.
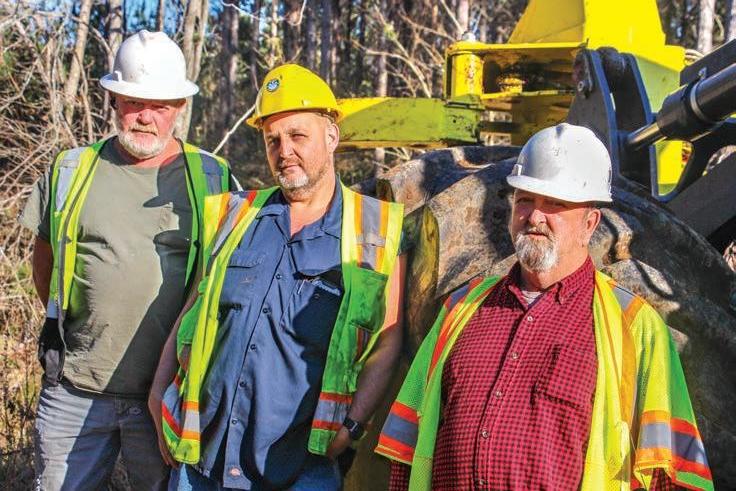
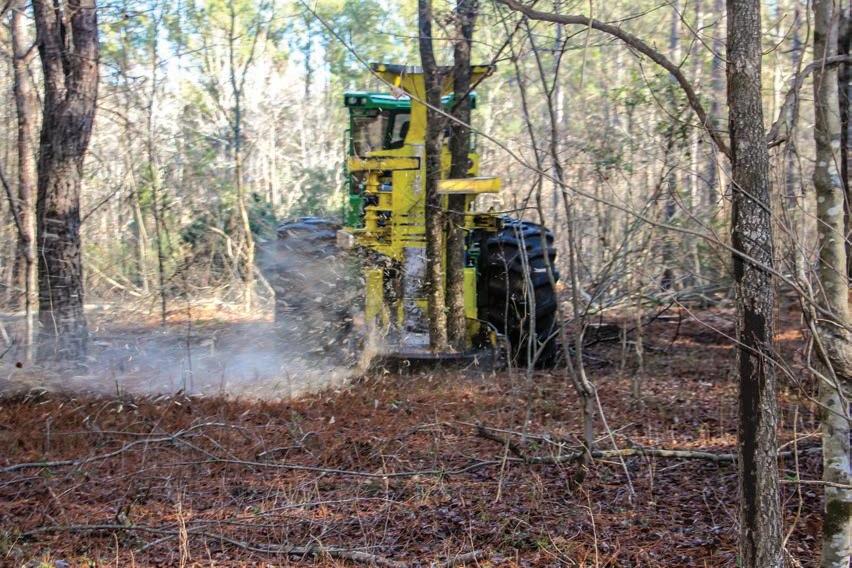
From left: Dean Rollins, John Jenkins, Ralph Cathey
On Tract
Ironically, the Deere track cutter would have been perfectly sized for the tract he was working in January. “This tract here is just a way better than average tract,” he says.
An exception to the norm for him, this privately-owned tract is 78-year-old white pine with some scattered natural hardwood growth mixed in. It is, he estimates, 70% pine. He is doing a 66-acre clearcut, and will come back later to complete another 33-acre select cut on a different section.
“Most of the time I cut primarily pulpwood,” Wiseman says. “I don’t cut a whole lot of log timber.” Here, though, they are getting some good sized pine saw logs, some as much as 36 in. diameter. The average, Wiseman says, is two feet at the stump.
Wiseman bought this tract on a
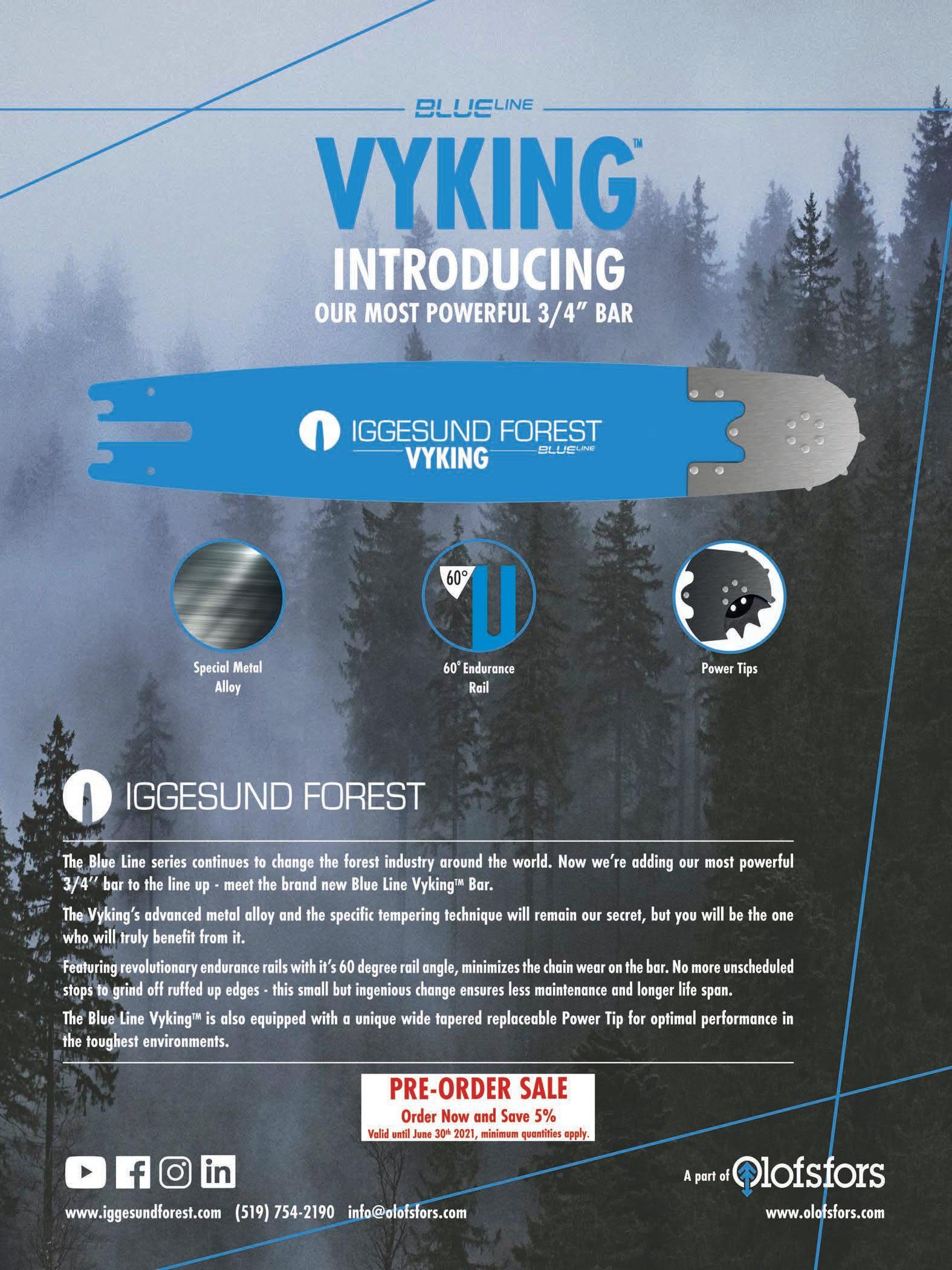
The crews work about 75 miles apart.
sealed bid sale from IndusTree Timber of Wetumpka, Ala., a company for which he had done some work in the past. IndusTree had closed their local office near here. “They had a log yard and I sent some logs there and got acquainted with them,” Wiseman says.
Usually he buys timber from two companies, Canal Wood and Valley Timber. His foresters are Jonathan Nelson at Valley and Scotty Guffie at Canal.
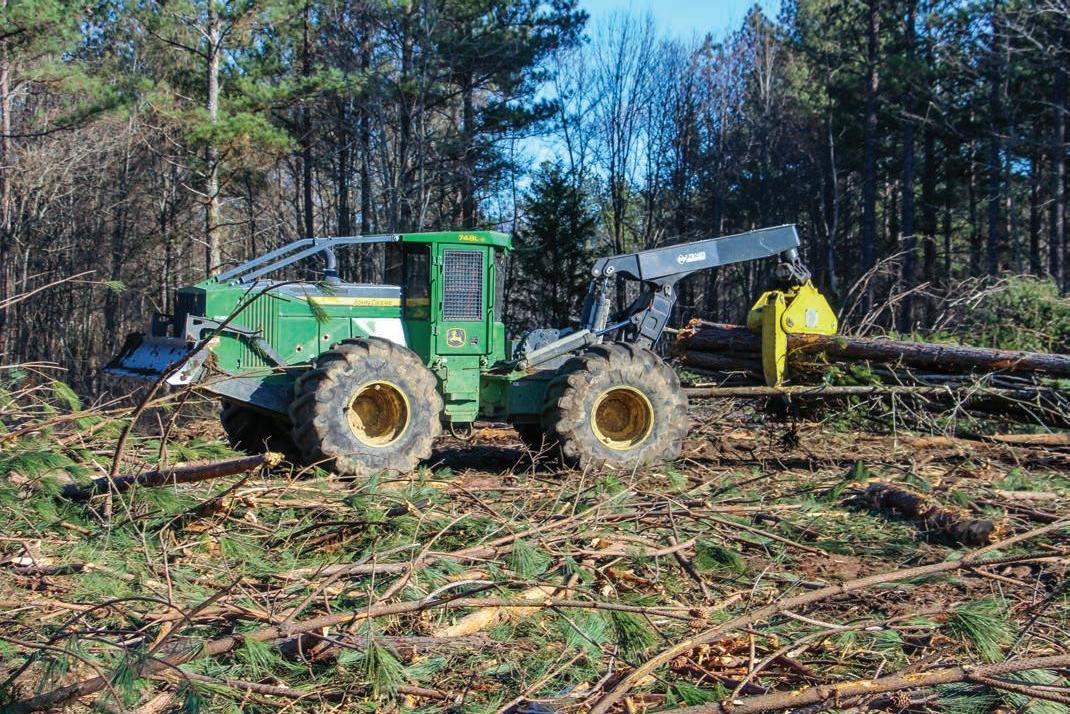
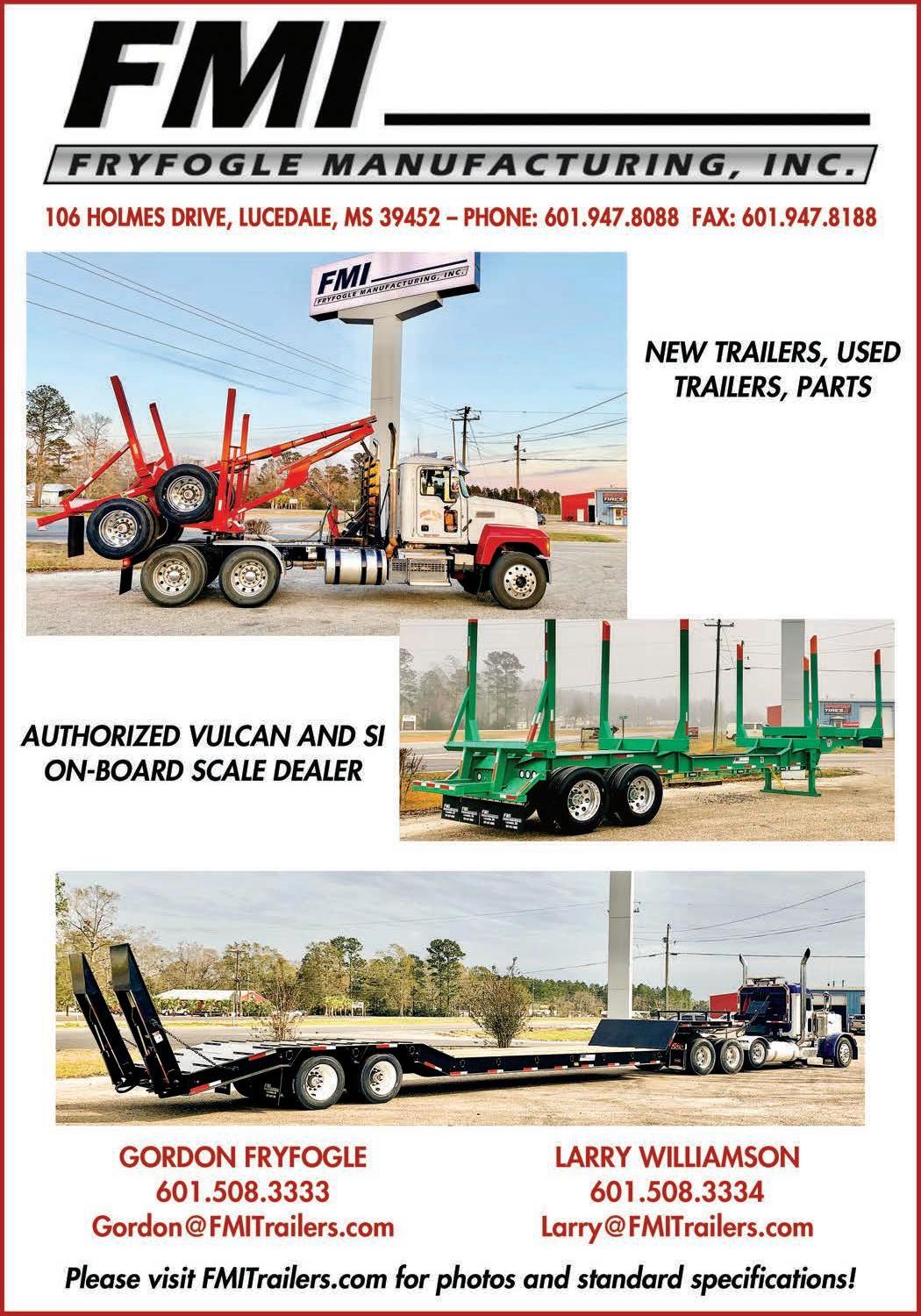
Hauling
On this tract, Crew 1 averages 15-20 loads a week, though they have done 40 loads some weeks. “It gives me more opportunity to train these boys when we are not so high production, and that was my goal,” Wiseman says. Most of the major production is on the mountain crew, which gets 40-60 loads a week.
Wiseman has a Chevy tandem truck and the Peterbilt he bought from loader man Rollins. Contractors haul the balance. The tandem truck isn’t full time; he uses it mainly in the winter, when road conditions get tough. “I guess if I was going to say what is the most stressful, it is dealing with trucking,” Wiseman ad mits. “Now don’t get me wrong; I have got some good men helping me, and have had some real good men in the past. Where I have struggled is when quota has trucks back ed up at the mills, and they have to sit and wait, sometimes for two or three hours. And I understand; it gets to the point that it is taking family time away from them. And they get paid by the ton so if they can’t deliver enough product, they don’t make money either. But I have had some good truckers, and really not any bad ones.” The market for pine saw timber has been slow, he admits, but happily reports it has picked up a lot stronger than it has been for the last several years.
“This economy is tough,” he ad mits. “It’s been tough. I can’t ex plain it all other than God is in it. I guess that’s as simple as I can put it. People have come along the way and have told me, ‘Dennis you can’t pay for that stuff the way things are today.’ If you say it can’t be done, but it is getting done, then you ought to realize there is a higher power involved helping me.”
Besides the two boys, Wiseman has a teenage daughter, Halie. He and his wife Samantha will have been married 29 years on July 6.
“I’ll work till they throw dirt on me,” Wiseman predicts. “I guess that is the way I’ll be. I’m not happy if I’m not working.” SLT

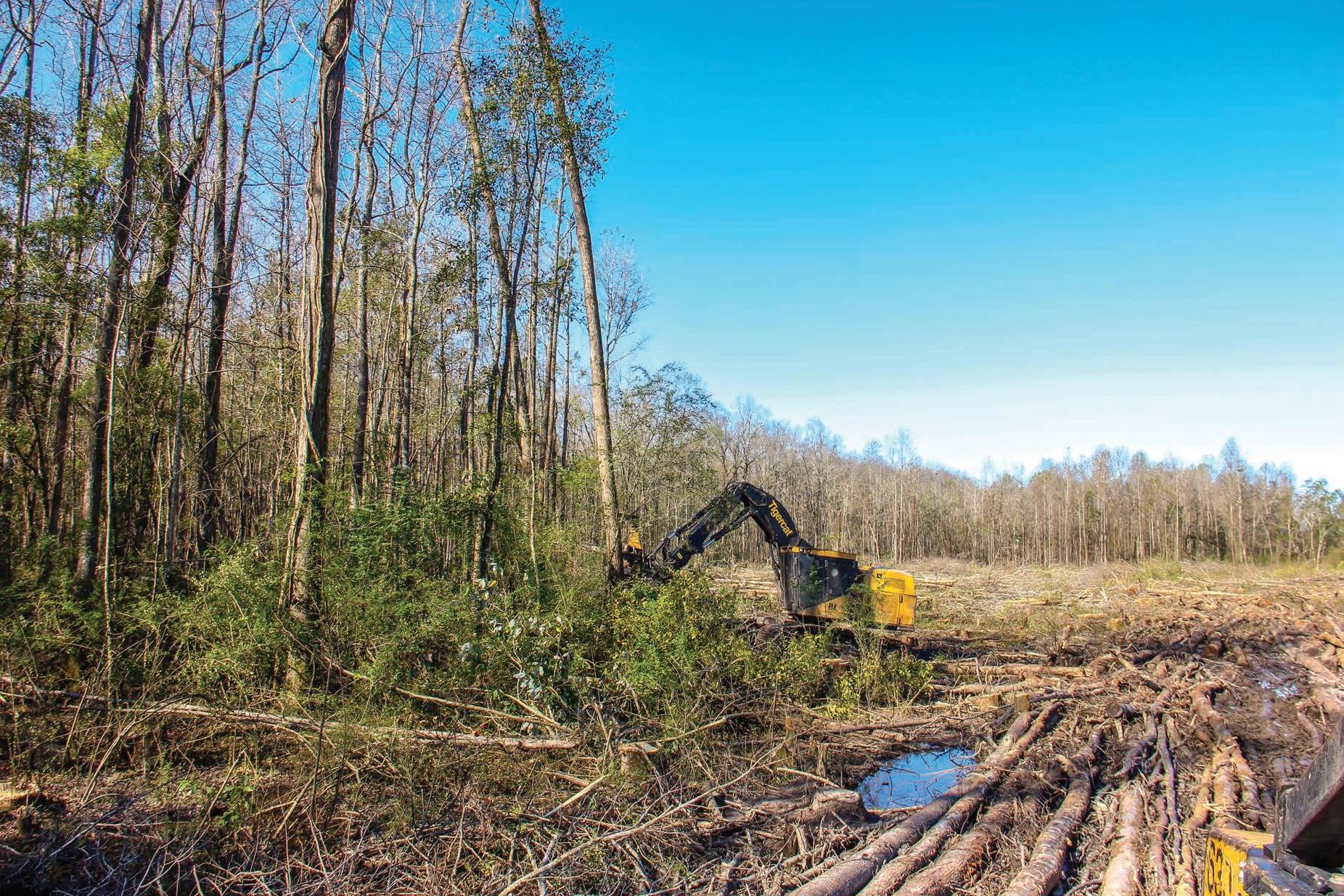
Blood Line
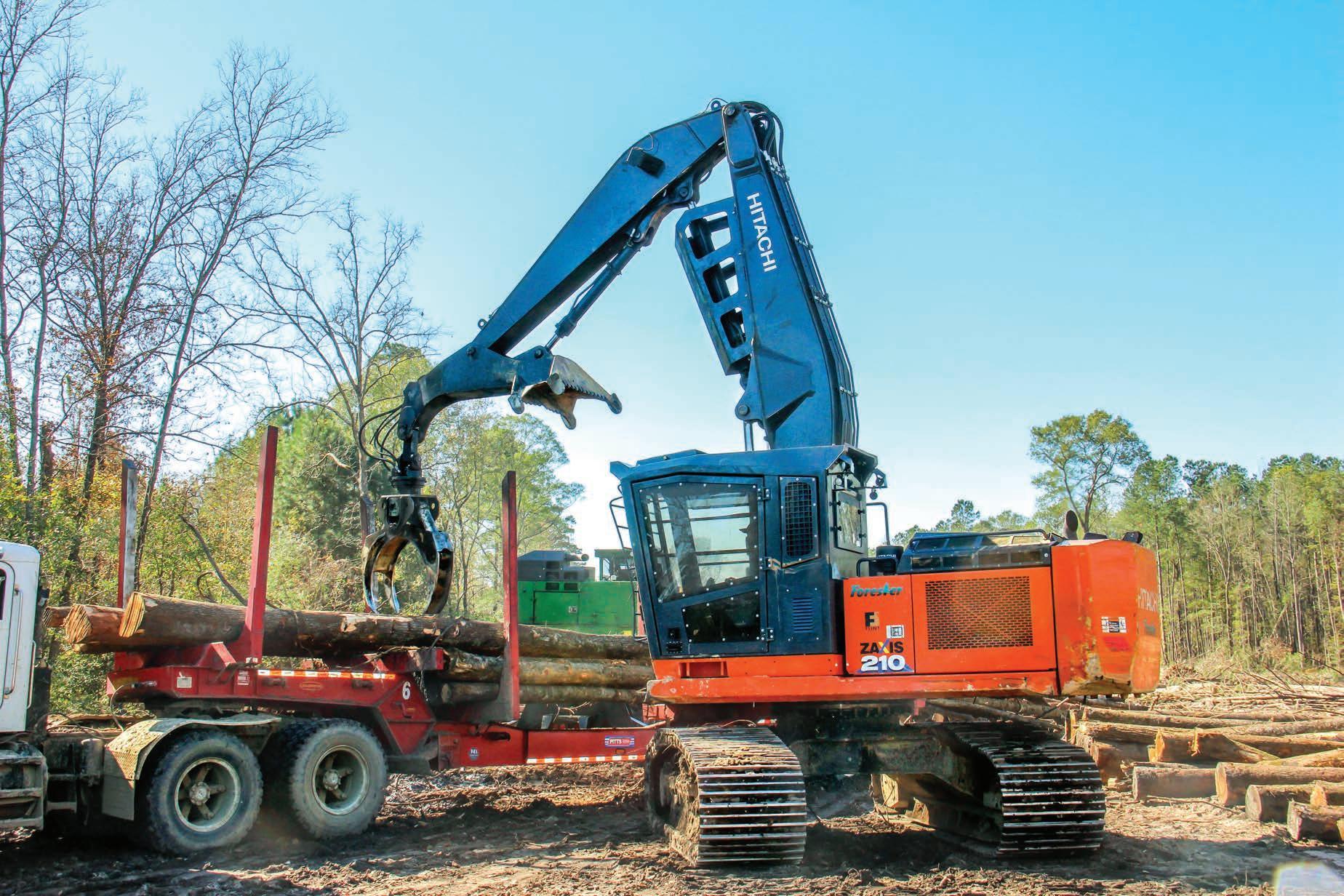
■ Three generations of Carters tackle tough swamp terrain together.
By Patrick Dunning
FLORENCE, SC
When Southern Loggin’ Times visited the T. Carter Logging crew, the clan’s patriarch and elder statesman, Thomas Carter, 83, had one question: “Are we almost finished? I’ve got to get back in the cab and get to work.” At an age when some men might have already been retired for nearly two decades, this one was itching to get back on the job. Like most loggers, he has pine sap coursing through his veins, and undoubtedly he’s passed it down to his son and partner, Tony Carter, Sr., 53, and grandson, Tony Carter, Jr., 31, both of whom share his innate passion for their life’s vocation. The latter, youngest of the three Carters, is better known as Bubba.
The senior-most Carter found ed his company, Thomas Carter & Sons Logging, in 1965. He rebranded the family enterprise to T. Carter Logging, Inc., in 1988 when he and Tony decided to go into business together.
Under either name, the Carter family business has come a long way from two-man saws and mules pulling log carts with 9 ft. wagon wheels, as Thomas saw in his young er days. “That’s all they had to cut timber with,” Tony says of the time in which his father came up in the woods. “An older man named Mr. Isaiah cut limbs with a dual bladed axe and Tillman Fin ners, who daddy worked for, would ride around cruising tracts of timber on a horse.”
Thomas remembers when he work ed for his own dad cutting cross ties that were hauled to a railroad steam engine yard in Andrews, SC. He recollects commuting from Hemingway to Florence with his brother when the only roads to be travelled were those of the dirt variety.
It was normal practice then for men to buy a tract of timber and set up a portable sawmill, sawing everything on the stand and loading it onto trucks. “We called them ground saw mills back then with the gas engine,” he reflects. “We’d load wood onto ’50s and ’60s model trucks, that no where near had the same brakes they do now, and hauled wood down to Charleston.”
Throughout the family’s long history in logging, the Carters say they have been first in the state to try a couple of different things. In 1972,
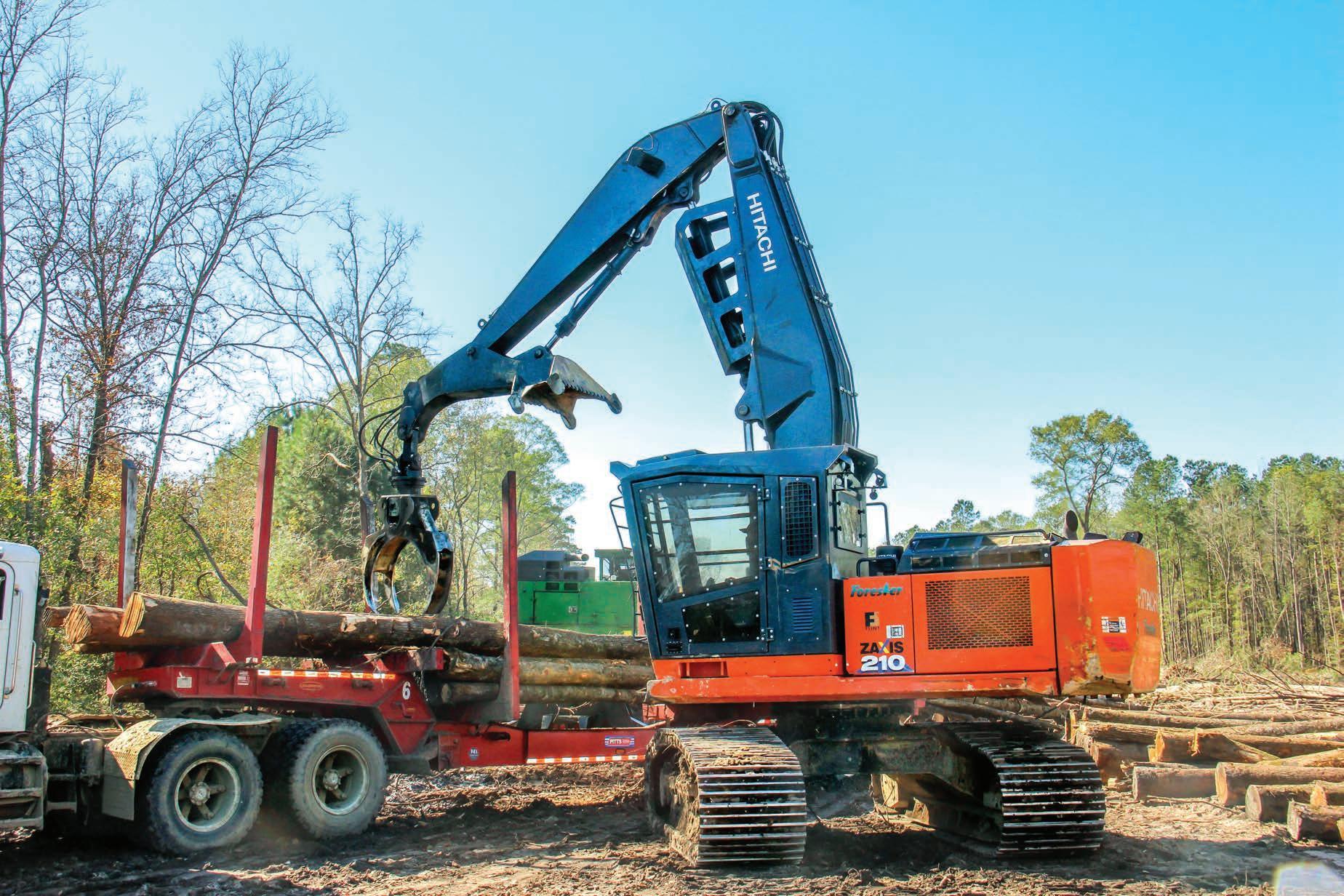
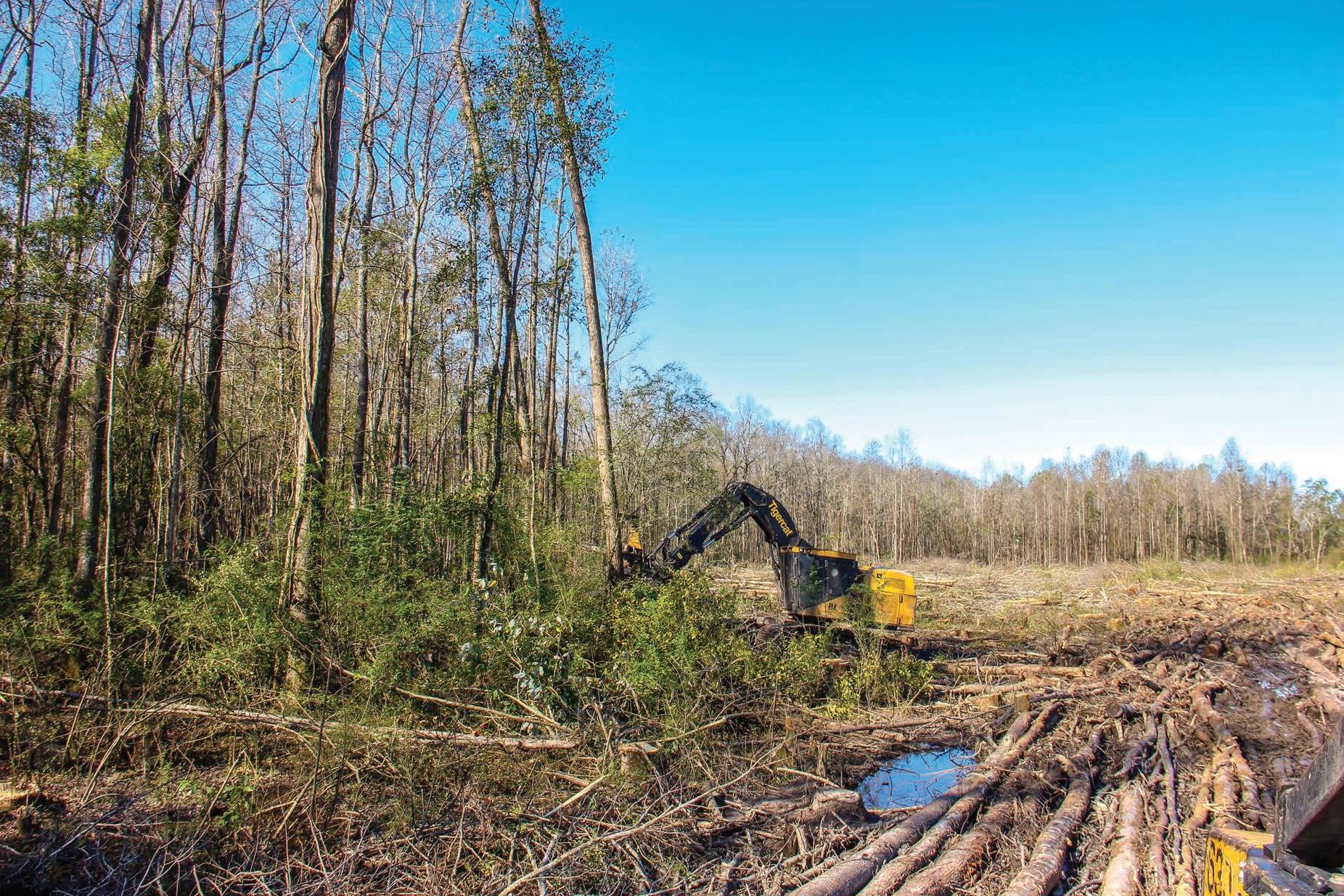
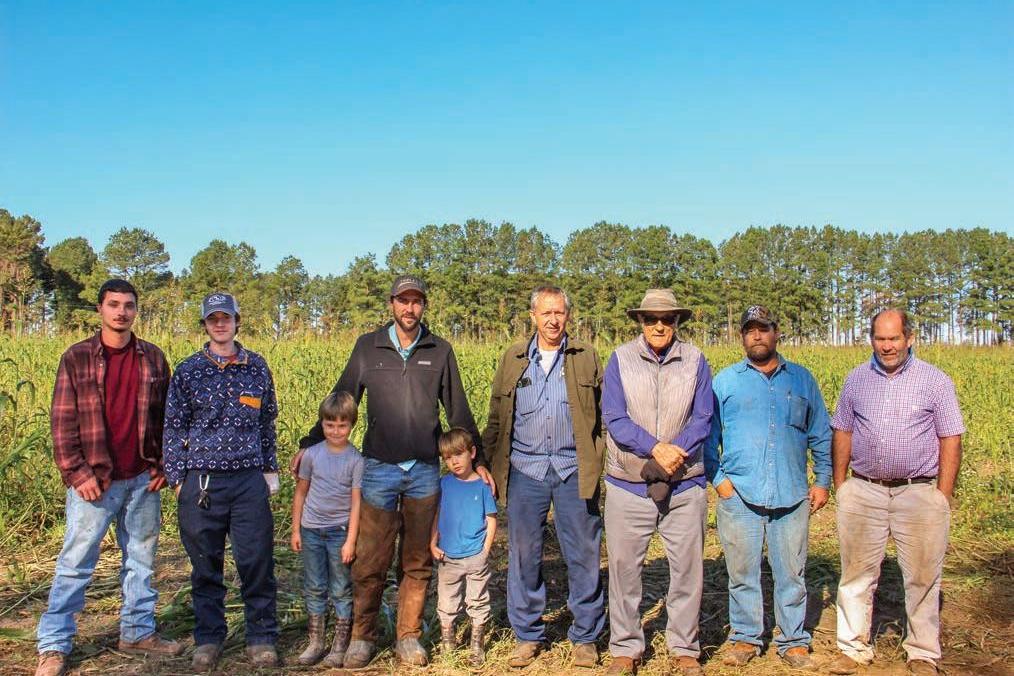
From left: Zach Norton, truck driver; Jackson Rogers, skidder operator; Tony Carter Jr., cutter operator, and his two sons, Colton and Brantley; Tony Carter Sr., owner; Thomas Carter, shovel operator; Chad Powell, loader operator; Daniel Carter, skidder operator
Tony Jr. approaches the swamp with their ‘17 Tigercat 855E track cutter, brushing stumps down and building roads between high stumps.
An average of 2,500 tons of wood are hauled a week with a large portion going to Edwards Wood Products mills in North and South Carolina.
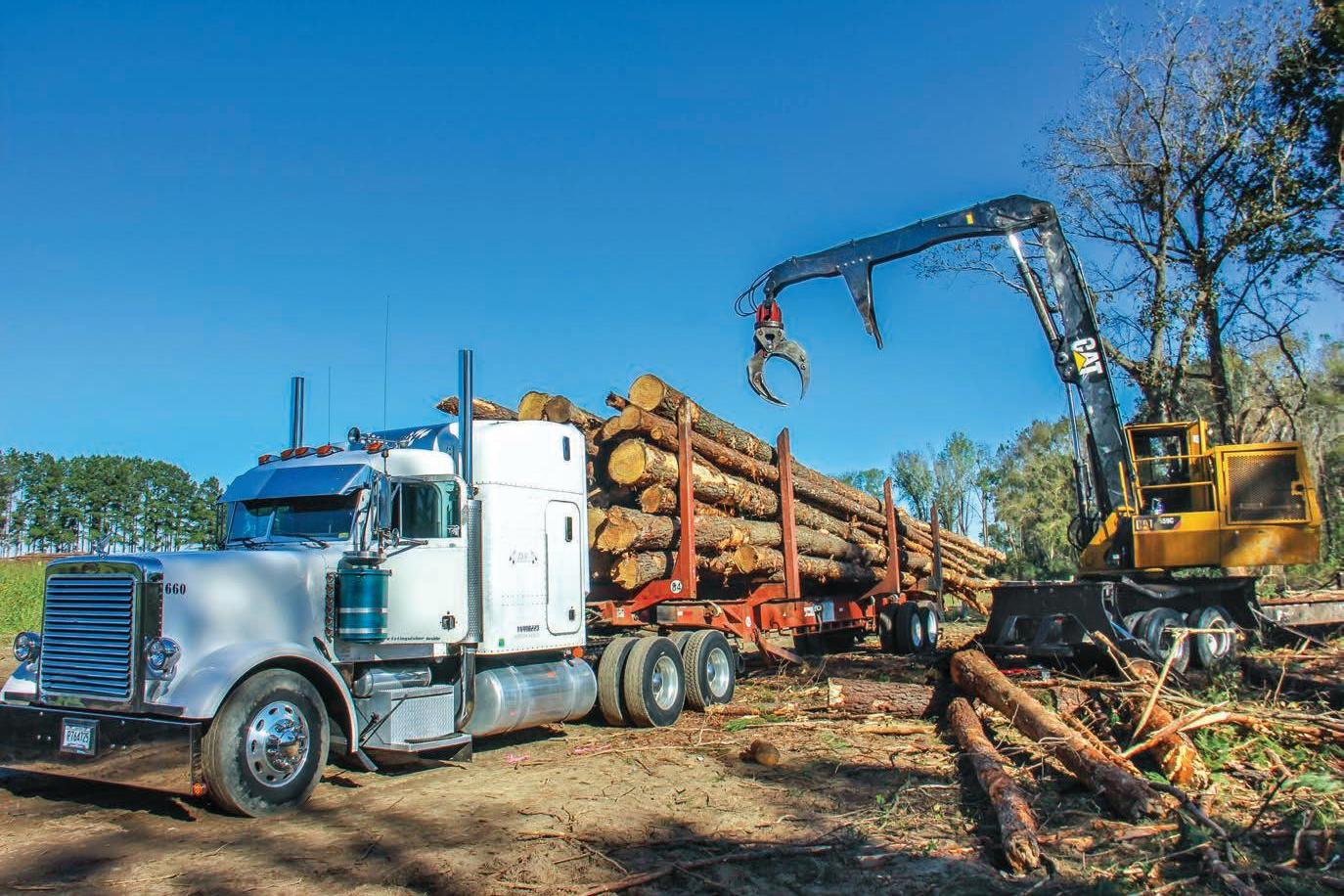
The ’16 Tigercat 635E bogie skidder performs half-mile drags on occasion.
Thomas says he was the first logger in South Carolina to buy a Kenworth diesel truck and haul logs with it. In 2000, Bubba says they purchased the first Tigercat clambunk skidder sold in South Carolina, from Tidewater Equipment in Conway.
Triple Play
Three generations of loggers working side-by-side isn’t an overly common sight. But then again, this family operation isn’t quite the common, typical, conventional crew. The Carters thrive in tough environments; they especially know their way around a swamp.
It was 1996 when Thomas and Tony purchased a pair of brand new items, a ’97 Peterbilt and ’97 model Timberjack track cutter, enabling the family to start swamp logging. That’s been their bread and butter since.
When SLT caught up with them, T. Carter Logging, Inc. was working on a 170-acre tract in Marlboro County, thinning 15 acres of standing yellow pine and shovel logging the rest for Canal Wood LLC, in Conway, SC. “It’s 95% shoveling in swamps,” Bubba says. “It’s not necessarily hardwood we shovel, it’s whatever tracts the landowners can’t get someone to cut. We favor the swamps.” Equipment

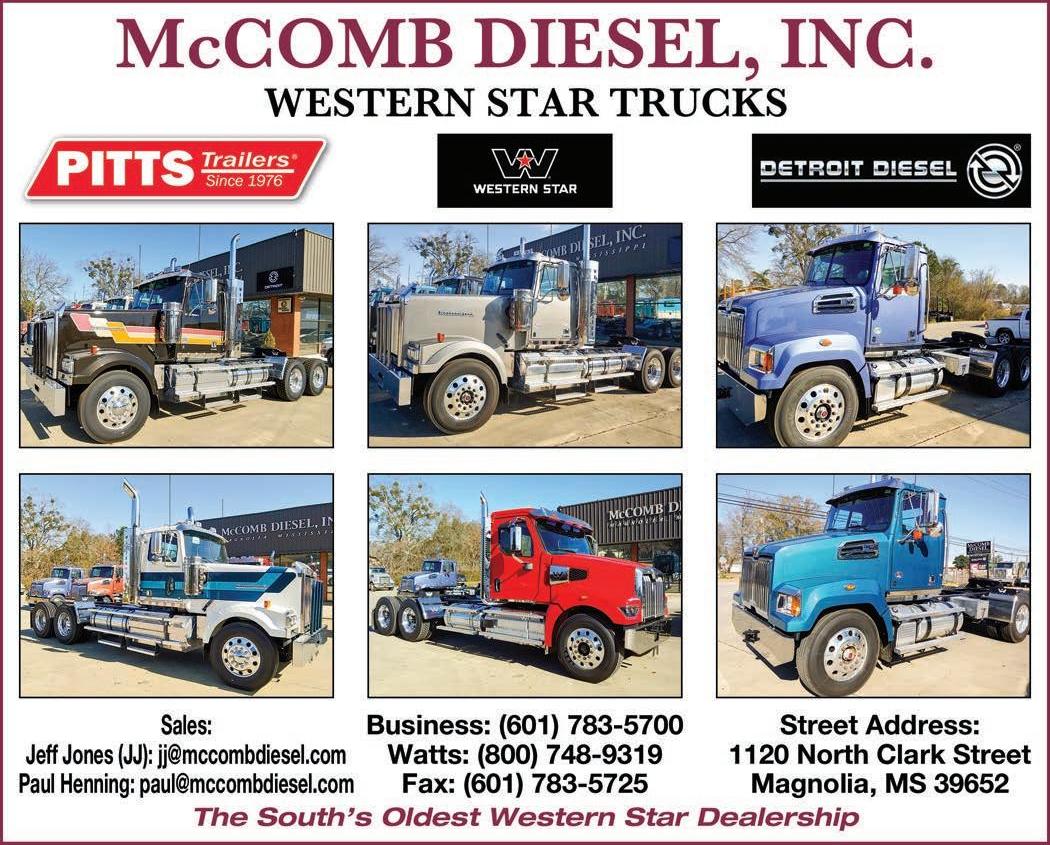
The Carters approach wet ground with a cutter and brush the stumps down, building their skid roads between high stumps to create a boundary within which to keep the logs. Their ’17 Tigercat 855E track cutter has triple grouser pads and Bubba says he’ll keep logs underneath him when he’s deep in a bottom. They also have a John Deere 843L rubber-tire cutter that features dual 30.5x30.5 tires. Their ’16 Tigercat 635E bogie skidder has dual tires with 35.5x32s on the inside front axles and 28x32s bolted on the outside.
The rear of the bogie has 30.5x32s on the inside and 28s outside. “We stay dualed up,” Bubba says. “The flotation on the bogie tractor can go places you can’t walk. It’s unreal.”
They set up two loaders, a ’14 559C Tigercat and 437E John
Deere, both equipped with CSI delimber and CSI bucksaw. Their ’18 Hitachi 210 forester equipped with triple grouser pads completes their woods equipment lineup.
At dealer Flint Equipment,
Aynor, SC, salesman Mike Marter meets the Carters’ John Deere equipment needs. The Carters work with Jeremy Strickland at
Tidewater Equipment in Conway for all things Tigercat.
To help them handle routine maintenance and repair in the woods, the Carters converted an old loader trailer into their service trailer. In it they keep a 2,000-gallon offroad fuel tank, hoses and hose makers, air compressor, extra filters, and a chain sharpener for delimber and bucksaw chains. Oil
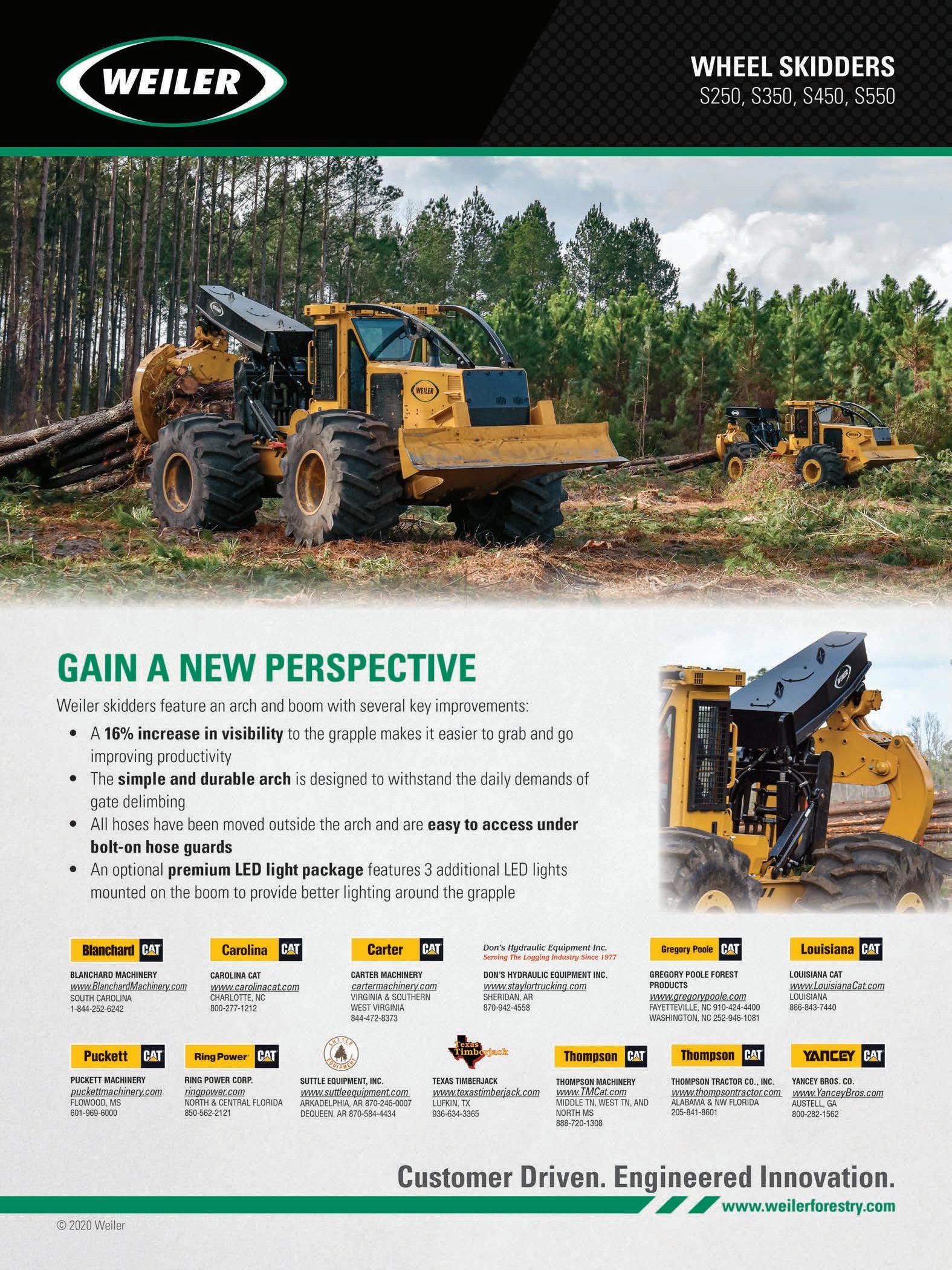
To circumvent 2020’s downward market trends, wood was hauled farther, sometimes a 100-mile radius.
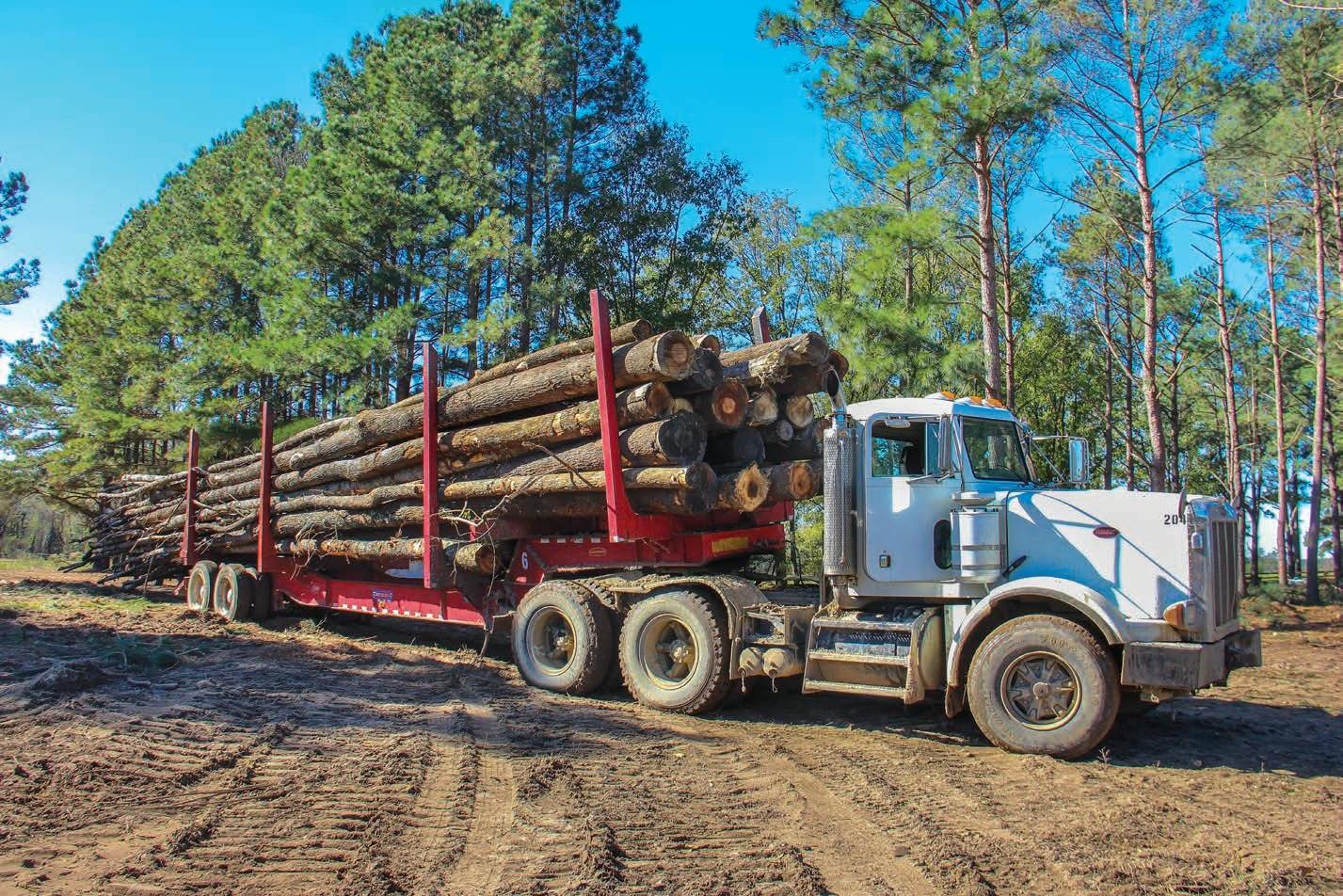
is changed every 500 hours on the Hitachi forester and in 250-hour cycles on all other woods equipment using Rotella 15W-40. Truck oil is changed every 15,000 miles and all machines are greased weekly.
T. Carter Logging runs three log trucks (Peterbilt, Kenworth and Freightliner) pulling Pitts, Evans, and Big John trailers with an average of 2,500 tons of wood hauled to respective mills each week. They target species including gum, hickory, cypress, ash and poplar.
Markets
The family has a longstanding relationship with Edwards Wood Products, hauling various products to several different Edwards mills both north and south of the Carolina state border. Hardwood pulpwood and pallet material go to the Laurin-
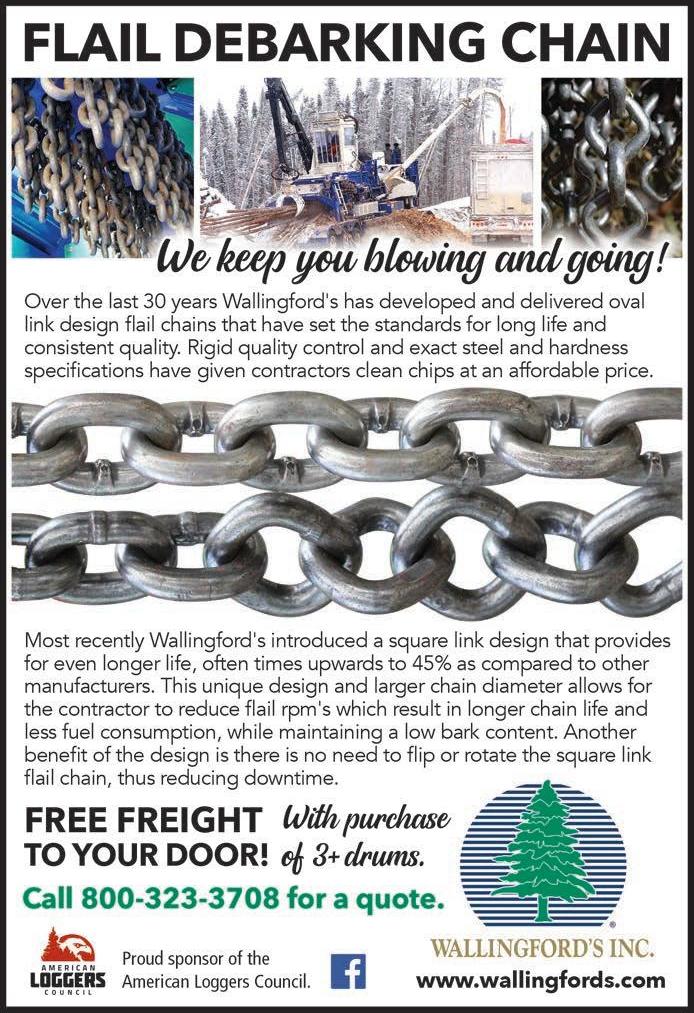
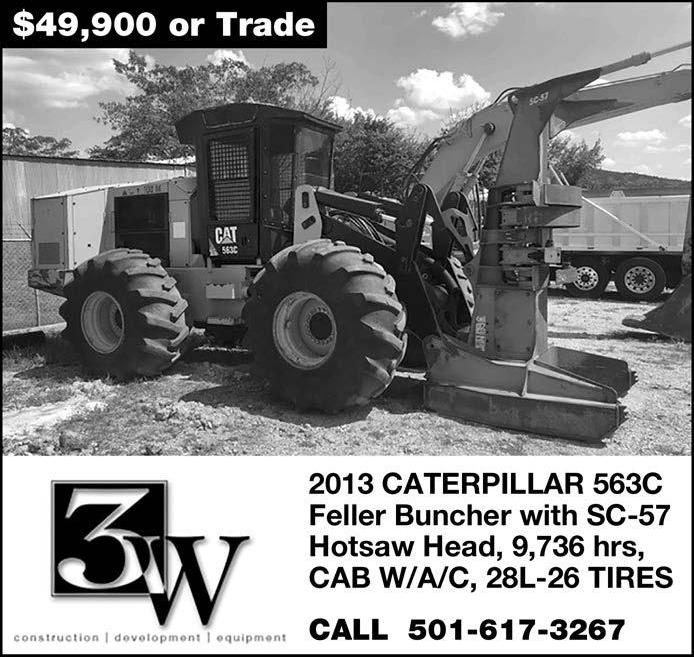
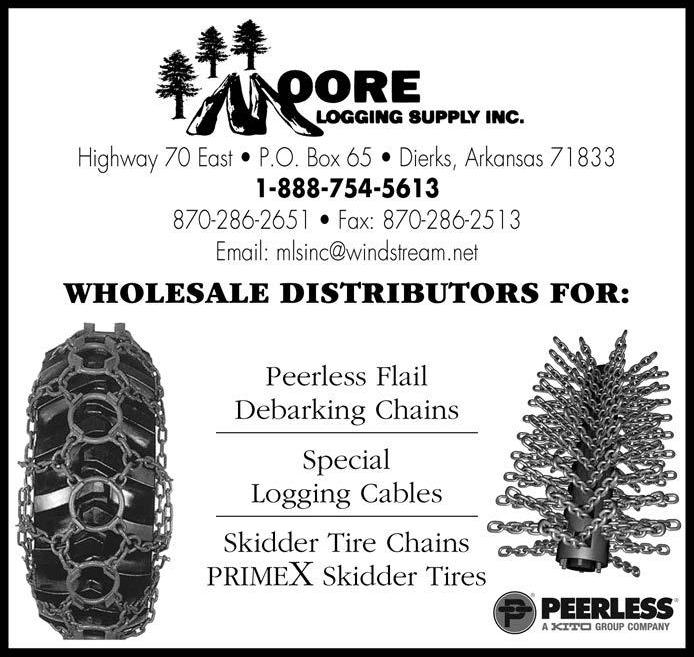
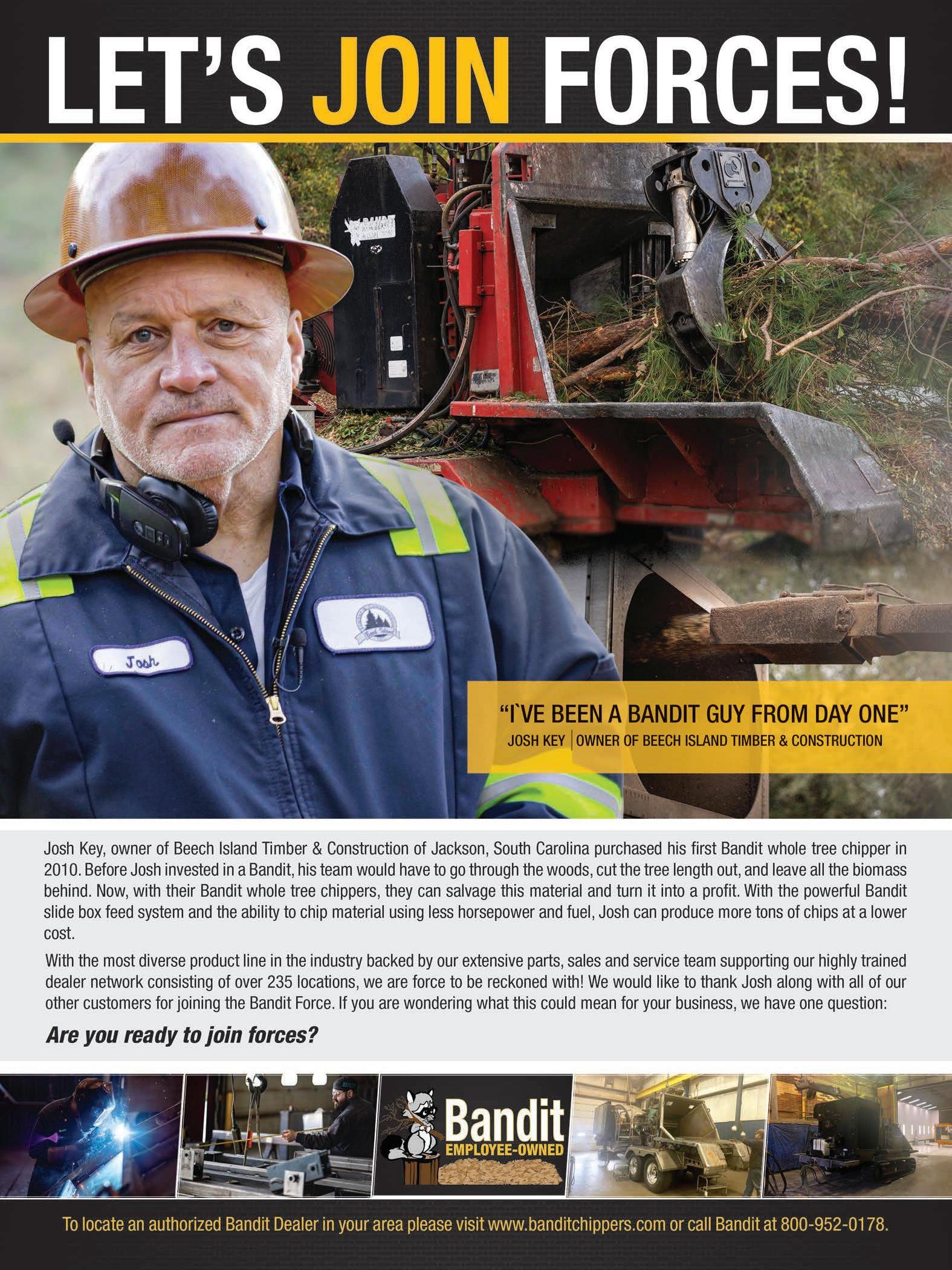
From left: Zach Norton, truck driver; Tony Carter Jr., cutter operator; Thomas Carter, shovel operator; Daniel Carter, skidder operator; Chad Powell, loader operator
burg, NC mill, gum logs to Peachland, NC. Carter Logging sends grade maple, oak, poplar and ash to the Edwards mill in Marshville, NC, and cypress to either Edwards in Alcolu, SC or Turn Bull Lumber Co. in Elizabethtown, NC. They haul some hardwood pulp to Domtar in Bennettsville, SC. Virgin pine logs go to Jerry G. Williams & Sons Lumber, Inc., Smithfield, NC.
Tony says markets were decent in 2020, though he notes that his pine markets shuttered temporarily when
Canfor shut down two of their mills in Darlington and Camden for several months. He says they experienced logging rates drop to $5-6 a ton when some mills weren’t honoring rates. “That’s hard when you’re paying for swamp equipment,” he says.
“Swamp logging is more expensive. Logging rates got cut but we were still able to haul wood. Some loggers flooded the pine markets and got put on quotas.”
To circumvent some of 2020’s market woes, the Carters simply drove a little farther for timber, sometimes 100 miles, and relied on other outlets: WestRock, Florence, SC; Domtar, Bennettsville,
SC; Enviva, Hamlet, NC; Sonoco
Products Company, Hartsville, SC, and Charles Ingram Lumber, Florence, SC. Tony says being able to haul to these mills has helped cash flow. “You have to have more than one place to haul,” he says.
“Sometimes it may be a long way and you don’t want to but you have to.”
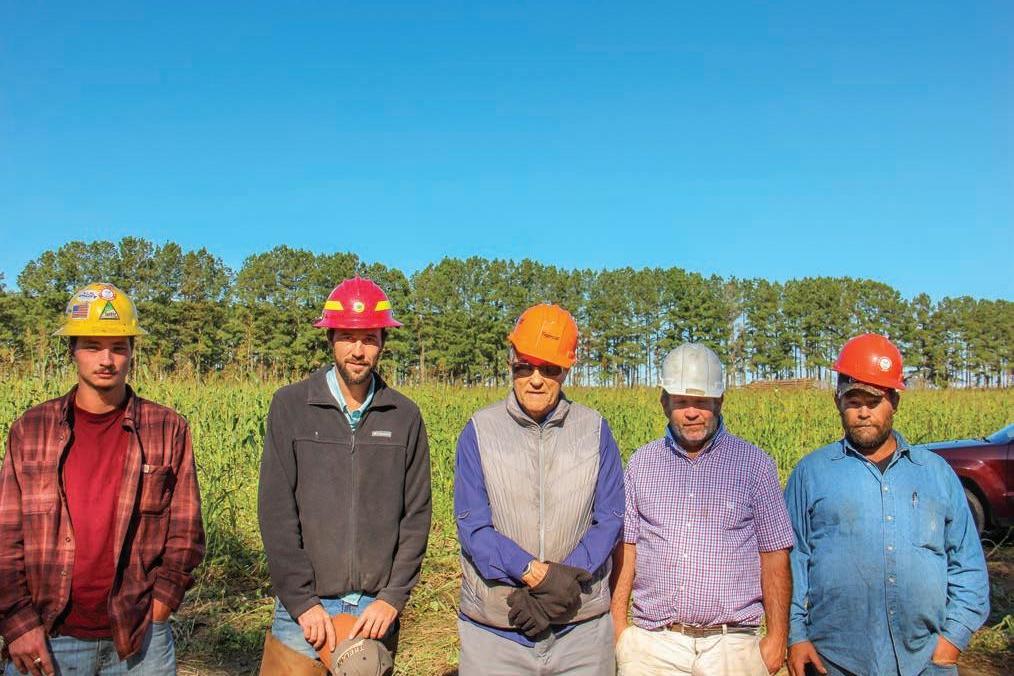
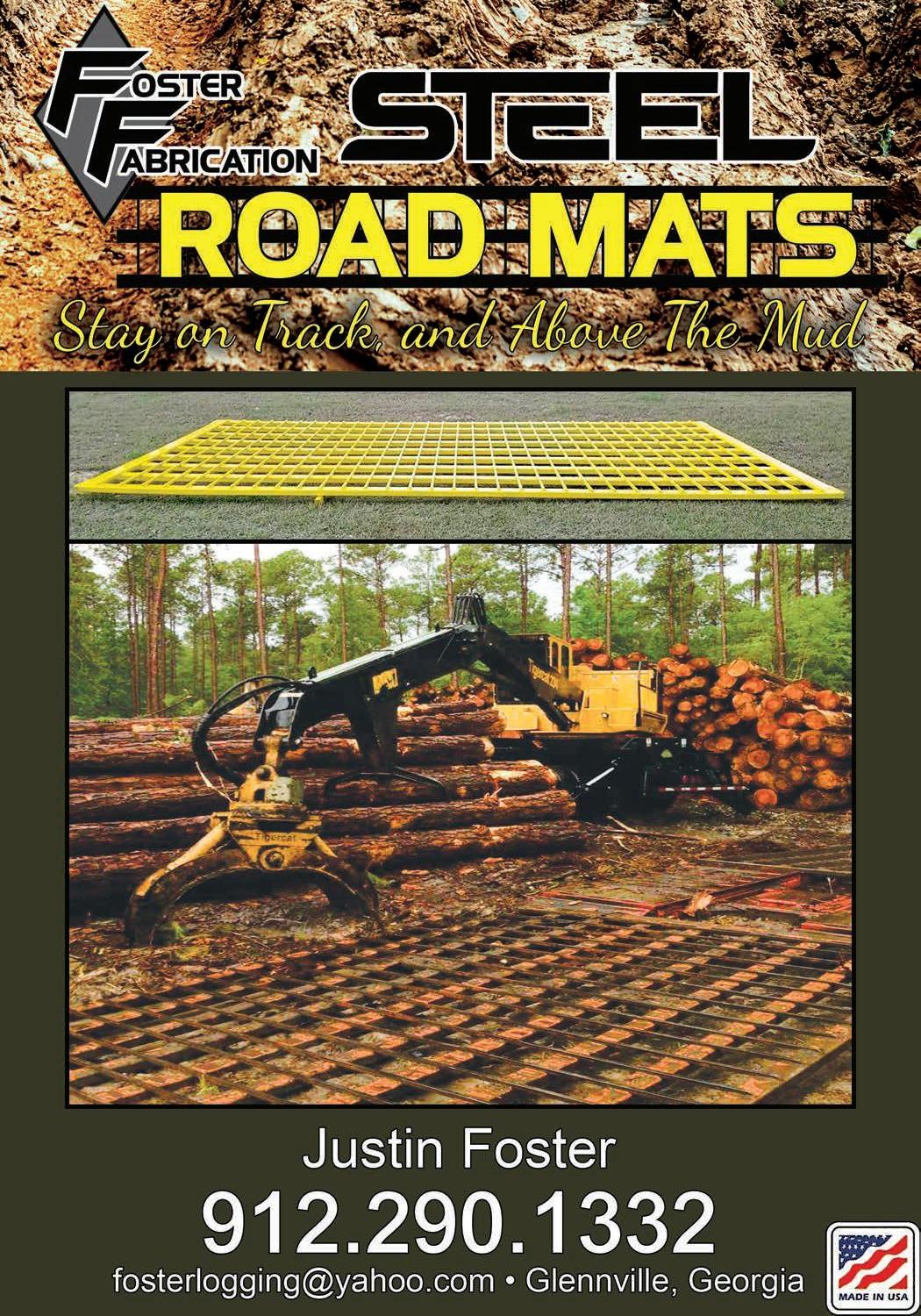
Manpower
Moving forward, Bubba has been taking on a larger role in the business. Tony, Sr. and Bubba often split up their crew of seven and run separately and independently. T. Carter Logging’s crew includes truck driver Zach Norton, Daniel Carter and Jackson Rogers in skidders and Chad Powell on a loader. Bubba mans a cutter and Thomas Carter is the shovel machine operator. Tony, Sr. is the owner.
ArborOne Farm Credit is a local farm credit system institution and covers the family logging operation’s insurance needs. The Carters conduct tailgate safety meetings routinely. SLT


Rain Or Shine
■ Wet and low ground loggers know how to harvest wood in the Southeast’s hardwood bottoms.
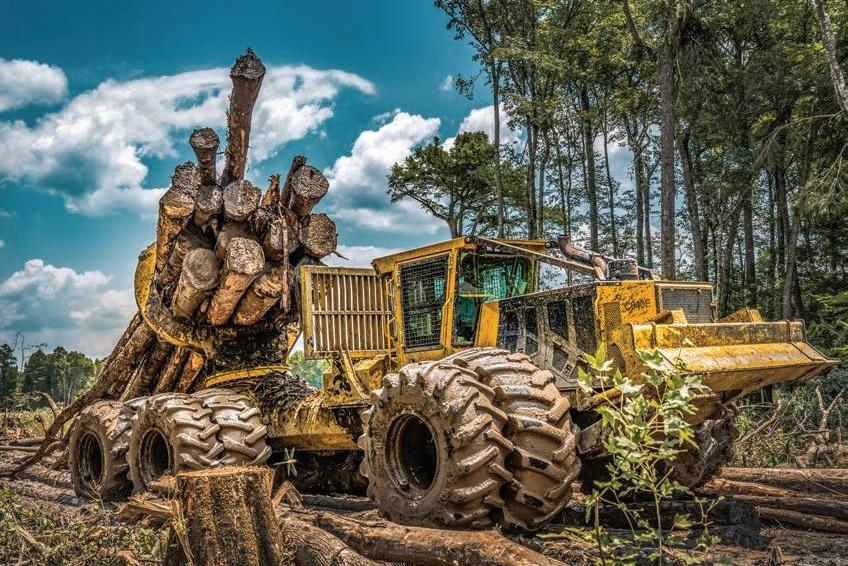
By Patrick Dunning
Dopson says sound access roads something nobody else is doing.” pressure harvest. T here’s a small percentage of loggers equipped to harvest hardwood timber in wet are vital for haul trucks to be able to get from the woods to mills. His crew typically works backwards when conducting clear-cut prescripWatkins says Dopson’s Tigercat 860 track cutter equipped with a 5702 head will go places you can’t walk. Tidewater’s standard Berco 36 Watkins oversees almost 150 customers at Tidewater’s Hazlehurst location and out of the 20 swamp loggers he assists, none of ground bottomland. It requires tions and builds shovel roads from in. triple grouser pad is ideal for the them run track chains on their specificed machinery to the back to the front. area and aggressive enough to woods equipment. avoid ruts that can “The way we do it is maneuver over submerged stumps. “In the swamps you have stumps affect soil quality and find the high ground One uncanny trick often used by and places where if that chain grabs future growth, and an and access it with the swamp loggers is utilizing the something it’s going to give, pop an emphasis on leaving a loader, then we start in machine’s boom to keep wood under axle, pop a drive shaft, so we don’t smaller footprint while the back of the swamp the tracks for additional traction. sell chains,” he says. remaining productive. with a shovel road and “You can flip the head around, The 860C model has a 75 in. tail
The handful of men work our way toward take a tree and stick it underneath swing and is the biggest machine who have found a the landing,” Dopson the tracks and walk around out there Watkins’ Tidewater location offers. niche in swamp log- explains. “That’s what with it while cutting wood,” Each time the tail swing is ging are utilizing mats, we’re accustomed to Watkins explains. increased the machine’s swing track machines, dual tires and in some cases Timmy Dopson doing.” When it’s wet they mat to stay above The wider the track shoes, the higher the pressure on the links radius is reduced but it’s smoother to operate. Watkins says, “Timmy’s track chains for extra grip in low the mud to avoid disturbing the between the pins and bushings. 860 is like riding in a car.” spots. Regardless of a machine’s ground. Track shoes have to be adjusted to The 5702 Tigercat single-tower capabilities, productivity depends The Dopsons’ family business the terrain the machine is working processing head on Dopson’s track on the performance of the overall started 104 years ago cutting high- in to minimize the wear process and feller-buncher has less accumulating traction system. ground hardwood pine and was ini- reduce the chance of chain break- capacity than the 5500 or 5600
Timmy Dopson, owner of Dopson tially exposed to track machines age, Watkins says. The wider the model but its centered pocket is Timber LLC, Valdosta, Ga., has a and excavators doing construction track shoe, the lower the ground more stable which is pertinent to six-wheel Tigercat 632 skidder and land clearing projects. pressure which results in less soil have in a swamp instead of transfergeared up with dual Firestone tires, Sawmills were constructed in the disturbance. ring weight from one side to another. running 35x5x32s on the inside and area and along with those came Dopson previously ran double The 5702 model is best suited for 24x5x32s on the outside. The three- more dealers and loggers. This grouser track shoes for extra hold- larger diameter trees and intended axle skidder has 23 sq. ft. of grapple forced Dopson to expand his reach ing power on hills but couldn’t for drive-to-tree track cutters with a capable of dragging close to half a and separate himself from the pack. avoid catching debris and stumps in single-cut capacity of 23 in. load of wood in a single turn. Dop- He runs three crews: a three-piece bottoms and repeatedly broke pins. Tigercat’s smaller heads are son runs exclusively Tigercat equip- pine crew, roadside operation and Triple grouser pads give when nec- designed to accumulate more trees ment including: two 860 track feller- his specialty swamp logging crew. essary, and Watkins says the cleats with its pocket holding trees 20 in. bunchers, two S860 shovel loggers, “It got so competitive, we decid- are thick enough to tackle Georgia’s and smaller to the side. But what 250D track loader, 630E and 630C ed to do swamp logging because timber bottoms near the Ocmulgee loggers often find in bottoms is a 20 grapple skidder. there wasn’t anyone doing it,” Dop- River where Dopson’s swamp crew in. diameter tree at breast height
Dopson’s Tidewater equipment son says. “You have to go hunt is currently doing a low-ground with a 30 in. swelled butt, requiring dealer, Jimmy Watkins, a couple approaches to fell. Hazlehurst, Ga., says the “Everyone I know in the three-axle bogie skidder swamps uses the 5702 head distributes weight better because it can cut a bigger than the heavier two-axle stump up to 23 in.,” and works well in wetter Watkins says. “It’s remarktopography. able how it performs.”
“In a swamp the main Norman Ratzloff, partner thing a logger wants is in Ratzloff Logging Inc. something to bring out the with his brother Glenn, run most wood at a time. Every Tigercat machines for their stem you leave behind swamp crew as well and could be another grapple operate out of southwestern full,” Watkins says. “Keep Louisiana in DeRidder. in mind the bogie wheels The brothers are outfitted turn just like a two-wheel with a six-wheel Tigercat skidder but the bogie is 635 bogie skidder, 822 and like a motor grader moving 845 model track cutters up and down so not only is with 5702 processing it pulling, it’s climbing heads, H250D processor, with the terrain up and and 234 and 250 Tigercat down. That’s how you get knuckleboom track loaders extra force.” Dopson’s bogie skidder (since sold) is capable of dragging close to half a load in a single turn. with 36 in. grouser pads.

The 635 model runs with a dual Goodyear tire setup: 35x5s and 24 in. dimensions on the front tires and 30x24s in the back. When they first started mat logging, they were running 30.5s on the outside and continuously broke axles and wheels, Norman says.
His equipment dealer at PatrickMiller Tractor Company, Inc., Many, La., Glenn Campbell, suggested he move his back, outside tires to 24 in. and they haven’t had any trouble since.
“We aren’t having any issues since we switched to 24s,” Norman says.
The 635 bogie pulls 95% of their wood and up to 7-8 MPH with a good access road.
Norman says his crew spends most of its time doing mat logging for Louisiana Timber Procurement in the West Bay Wildlife Management Area, a nearly 60,000-acre tract of protected and sensitive land near Elizabeth in Allen Parish, La. While they do dabble in some natural stands, he prefers thick and wet parcels.
“We have to be on a pretty decent plantation,” he says. “The company we work for takes care of our roads which makes it easier for us.”
When the Ratzloffs move onto a tract, they’ll prepare a gravel road, sometimes to the corner of a tract and skid up to ¾ mile on mats. At ¾ mile, their bogie skidder can pull close to 20 loads a day. Norman says the last tract his crew was working on they skidded 140 acres to the backside of the property and constructed a road with their bogie skidder.
Red Williamson, store manager at B&G Equipment, Magnolia, Miss., has been working with Olofsfors and outfitted a 635 Tigercat with Olofsfors’ new CoverX track for optimal flotation and traction for Randall Sibley, Sibley’s Logging Inc., Walker, La.
Sibley’s 630E skidder features dual F2 Nokian 35x5s matched with 24x5s while the 635 bogie has 35x5s on the front and 780x50x28.5s in the back complemented by CoverX track chains.
When Sibley originally made the deal with Williamson he went with the 26mm CoverX pads but they didn’t last 4,000 hours in the woods so Sibley switched to a wider 30mm.
“It’s a taller tire setup and the ground was so abrasive to the pins,” Williamson says. “So, they bought another set that had ribs in the tires. That way they have traction and don’t have to run the tracks until it’s wet enough.”
The F2’s tread pattern offers an increased straight section of the ribs and grooves on the center point. This newer pattern keeps the track crossbars straight on the surface of the tire and reduces stress on the tires and bogies.
Though still in an experimental phase, Williamson believes they’ll have success with their combo of Nokian tires and CoverX tracked traction systems.
“We might see some chaffing on them but lower PSI on the bogie skidder’s weight is distributed a lot better than your regular skidder,” he says. “When it’s dry you’re fine, and when it gets wet just lay the tops or brush down to help get a bite and any stumps that are there it will stick to.”
Olofsfors’ track chains are installed on the bogie’s back tires when needed and help with flotation in wet spots with minimal ground disruption and steep inclines.
“The top side of the tire rolls a little bit so your tracks follow it really good,” Williamson says. “This tread has a different design to it.”
CoverXs and tracked systems are a fairly new market for Williamson. They’ve sold similar brands but Williamson says CoverX offers a wider pad that hopefully leads to longer life. B&G has sold two Olofsfors track systems so far.
Sibley’s Logging Inc. also uses a single grouser padded LX830D Tigercat feller-buncher with a 5702 Tigercat saw and a 340° wrist, 2156G John Deere track loader with a Waratah 623 processing head, and a T2654 Tigercat track loader. SLT
Note: This article previously appeared in the November/December 2020 issue of Timber Harvesting.
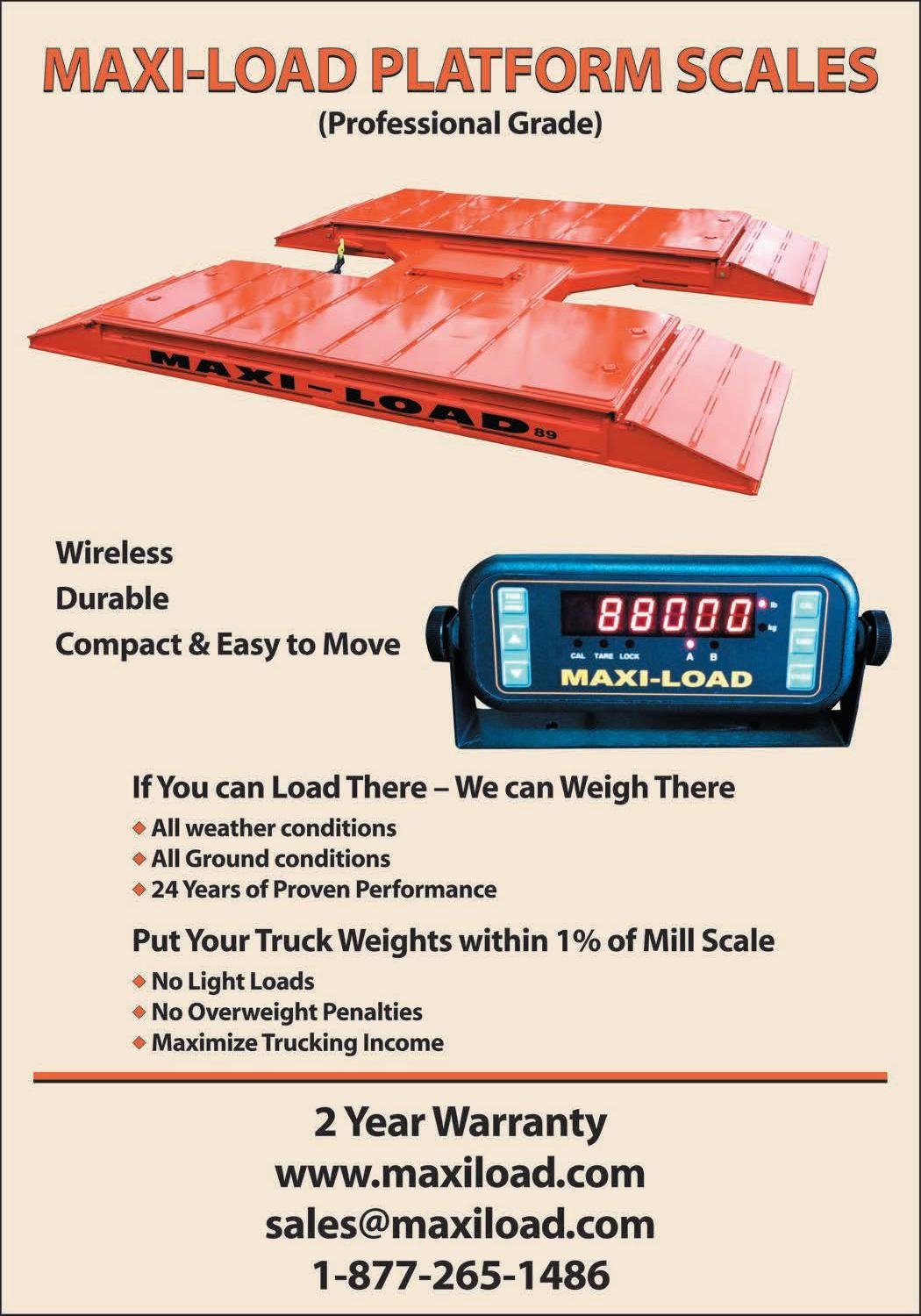
Pulpwood Markets Adapt To Product, Demand Changes
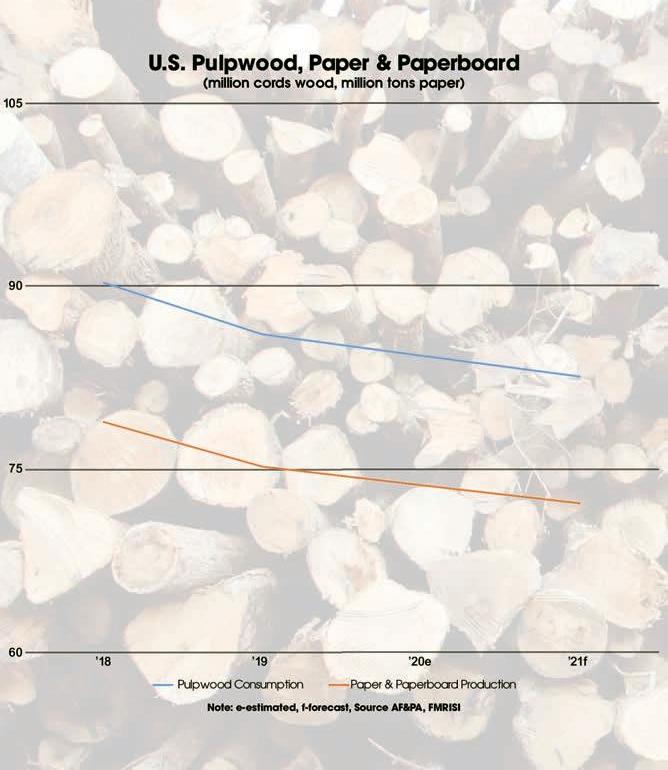
By Chris Lyddan
After the COVID year and social/political turmoil that nobody predicted for 2020, picking market winners and losers for next year seems like calling the weather: pretty dicey. But that’s what analysts and others do this time of year. When asked again by Southern Loggin’ Times for a timber market review and outlook, I was happy to comply and represent RISI (what is now Fastmarkets RISI, or FMRISI). There’s one note, however: Due to short timing, data is shown in original sector units, not converted to standard tons.
Currently, softwood log and lumber markets are hot and quite positive for loggers, sawmills and landowners, but pulpwood is a mixed bag and a complex story.
Harvest Up. Overall U.S. timber harvest should rise about 2% in 2021, compared to this year, with softwood up 3% while hardwood declines about 2%. That would total just over 400 million cubic meters next year, according to FMRISI projections on UN and Wood Resources Intl. data. That’s about 400 million tons in U.S. terms. The harvest mix will likely run just under 25% hardwood and just over 75% softwood.
Overall, nearly equal volumes of sawlogs and pulpwood came out of the woods in 2019—but that’s where the similarities ended and much has changed. Looking ahead, and breaking it down, logs gain in overall loads delivered in 2020-21 while pulpwood is quite mixed: Expect shrinking deliveries to paper-grade mills (heavy to hardwood) yet rising deliveries to packaging mills (mostly softwood).
Winner: Lumber. Softwood sawlogs and lumber, longtime timber value drivers, are already strong in second half 2020 and should step up another 5% in volume nationwide in 2021, to 38 billion board feet (BF) production, lumber basis, according to FMRISI forecasts (see harvest table). That gain equals an additional 1.8 billion BF for the U.S. next year.
By region, the South remains clear leader in U.S. softwood production growth. Some mills will ramp up recent multi-million dollar capacity projects in the New Year, while others, led by Canadian operators now dominating the South, will simply run hard on strong orders and healthier crews next year, COVID willing.
Specifically, the South should see a solid 6% volume gain in softwood log/lumber production in 2021, up about 1.2 billion BF to 21.3 billion BF. And the West rises an estimated 4%, up 500MMBF to about 14.2 billion BF for 2021.
Loser: Pulpwood Grades. While softwood logs and lumber are quite positive, as mentioned, pulpwood is a mixed and complex story. And difficult to predict. What is clear: Expect falling quotas/lower demand from various paper-grade mills, while paperboard facilities should gain volume in 2021, led by the South.
It’s crucial to distinguish grades, as outlooks vary greatly. There were 122 remaining pulp mills operating in the U.S. at the start of 2020. But
Going into the new year, regional pulpwood markets are facing tough going depending on whether they are focused on paper or paperboard production.

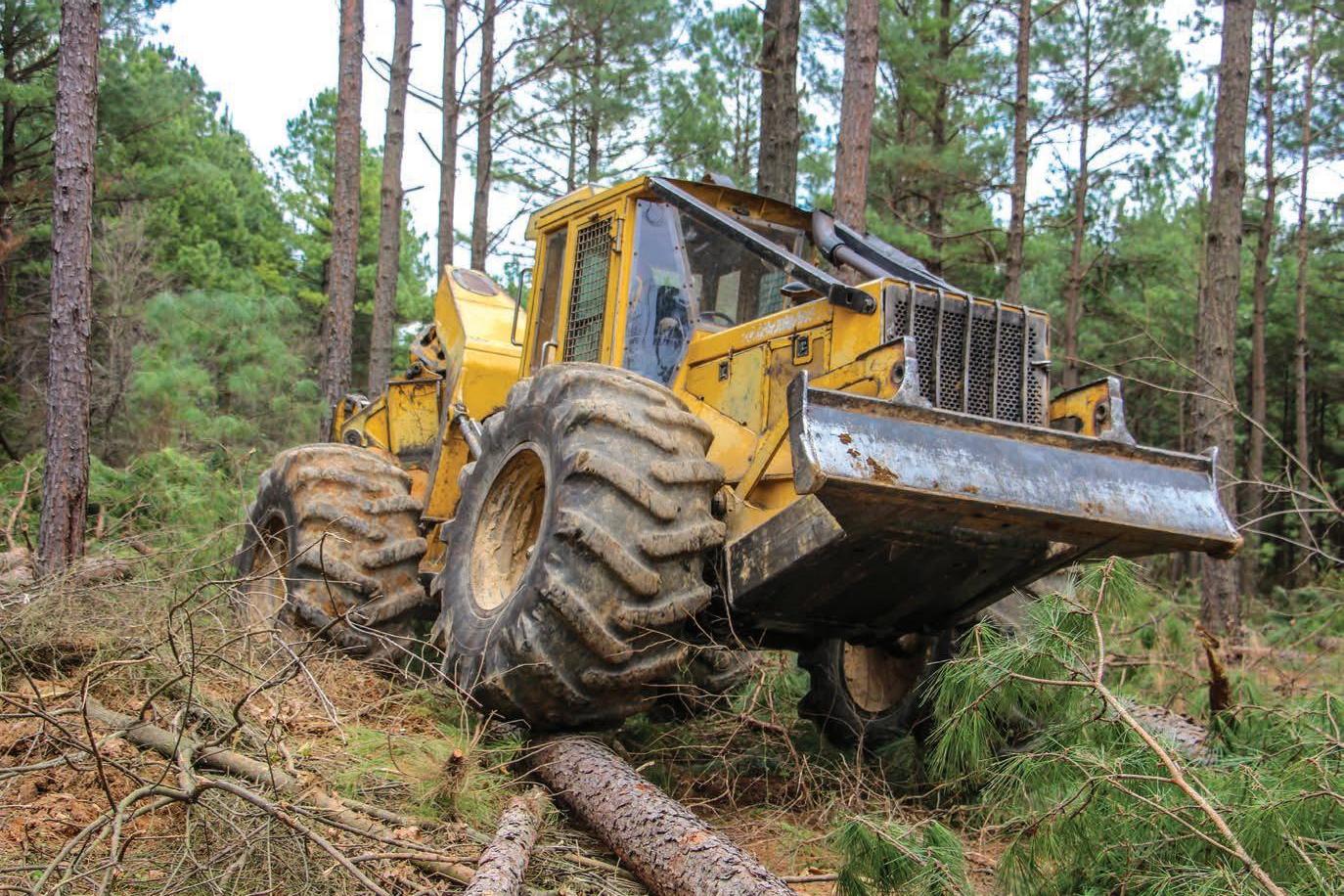
numerous machine and mill closures plus market-related outages occurred during 2020 and the last several years. Altogether, 2019-20 will mark a modern-day low for U.S. pulpwood consumption. Peak to trough, pulpwood usage is down fully 25% from the all-time high in 1999. That’s right, off one-quarter in 20 years.
Two Bright Spots. Much smaller than everything pulp-related, but significant in some regions, higher wood use by OSB and pellet mills counters some of the widespread pulp mill losses. As the secondbiggest U.S. wood market OSB ran aggressively in 2020, consuming an estimated 28 million tons of roundwood, and should top that in 2021, up about 14%, or 4 million tons, to 32 million tons. The South holds more than 80% of the nation’s OSB capacity.
Third-ranked pellet producers exported a preliminary 7.3 million metric tons of product this year, up 6.5% over the prior year and growing considerably. Led by Enviva and its greenfield mills in the Gulf South, exporters are on track to boost output a combined one million tons (2.2 million tons wood) in 2021.
Many in the timber business hold high hopes for continued pellet export expansion. The segment, Southern based, launched its first vessel load barely 10 years ago and now accounts for more than 16 million tons of wood demand, record setting growth.
Paper Trends. Tumbling paper grades include the printing and writing group (so called free sheet and mechanical, both in coated and uncoated finish), which was down a combined 21% year to date through October 2020. Those losses follow years of gradual decline on shifts to internet advertising. Indeed, most printing and writing grades slumped further and faster this year on COVID school and office closings, many of which will extend into 2021. These grades are typically heavy to hardwood.
For evidence, recall multiple paper mill and machine closures over recent years at Luke, Kingsport, Port Hudson, Ashdown, Evadale, Crossett, Naheola, Catawba and Augusta, among others. Countless communities and businesses large and small have suffered mightily. Common to most was hardwood furnish, off fully 20% industry-wide the last several years.
Outside of paperboard, only the tissue segment (softwood) grew this year, up 5% to October.
Paperboard Strengths. In stark contrast, the industry’s largest segment by far, paperboard grew in 2020 as home-delivered shopping consumed millions of boxes. So far in 2020 to October, sub-categories linerboard and medium rose smartly, up 4% and 3%, respectively, and should match that growth again next year.
Just out, November 2020 paperboard production numbers remained quite strong as box shipments rose 5% versus the same month a year ago. Liner mills ran hard at 93% capacity in November, while corrugating medium was especially strong, running at 98%. That boosted pulpwood orders late in the year, when things normally slow just before Christmas.
So, with many moving parts at year-end, a reliable grade-by-grade pulpwood forecast for 2021 is not yet complete. However, one broad prediction is clear: Paper grades should decline another 5-9% next year while paperboard should gain about 2%. That leaves the entire group down a combined 2% in 2021, continuing that multi-year decline. SLT
Chris Lyddan with FastMarkets RISI is Executive Editor, North American Woodfiber & Biomass Markets, Timberland Market Reports. He co-founded International Woodfiber Report in 1995 and Timberland Market Reports in 2000. He holds a B.S. in Industrial Forestry from Virginia Tech.
Note: This article previously appeared in the January/February 2021 issue of Timber Harvesting.
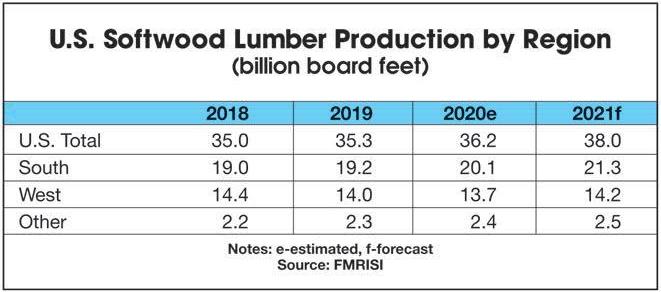
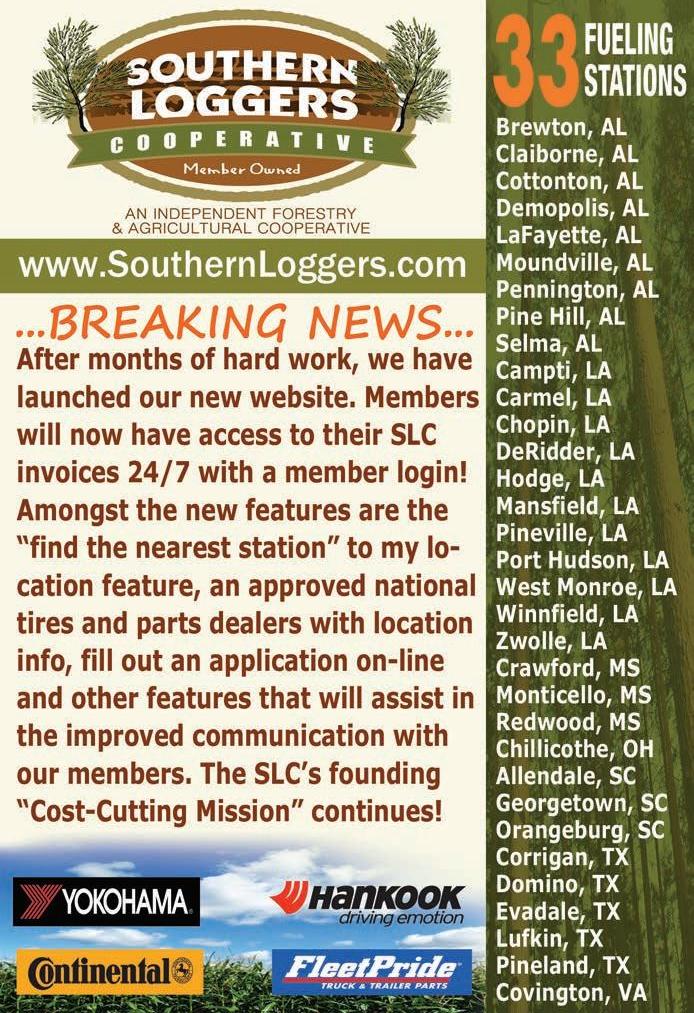
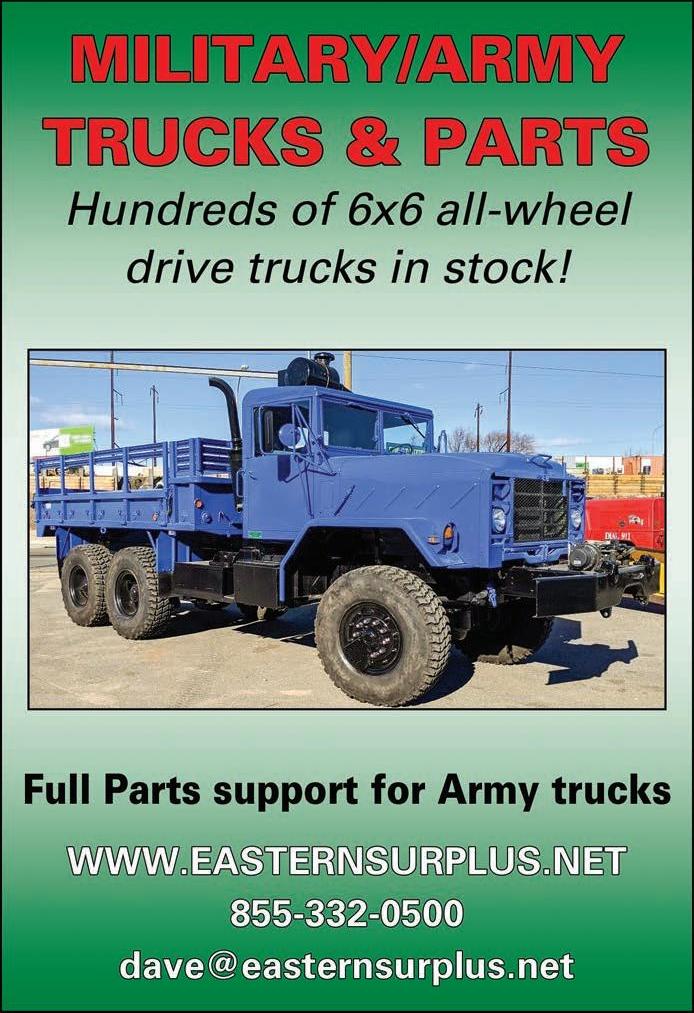