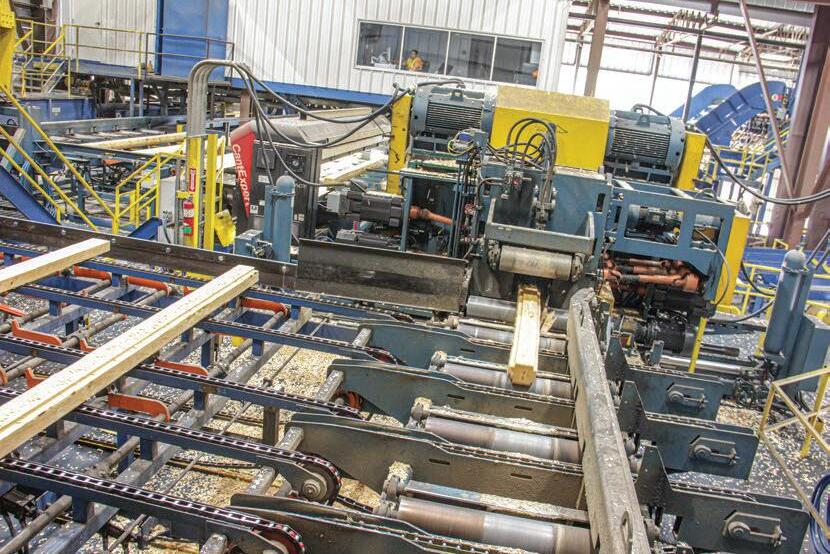
7 minute read
RESOURCE CHANGING
EFFINGHAM, SC
By David Abbott
Achieving success is difficult enough in the first place; maintaining it over the long haul can be even trickier. To do so, businesses often find it necessary to adapt to changing conditions, make adjustments, alter strategies. What worked yesterday may not be right for today, and knowing when to change can be critical.
Charles Ingram Lumber Co., Inc., has displayed this capacity more than once through the years. The southern yellow pine producer operates two separate sawmills on opposite ends of the same property here. One side processes large logs, while the other is devoted to smaller logs (they call it the Willow Creek mill). Charles Ingram Lumber originally added the small log line in the early 2000s in response to a glut of pulpwood in this region.
“We were having trouble getting rid of pulpwood off some tracts we had bought,” recalls Jesse Moore, who at the time was a forester for Charles Ingram and now oversees mill production. “We built this small log mill to try to capture a super pulpwood type of tree. And it worked well for about 10 years. Then the glut was gone, and competition for that wood started getting a lot stronger from the paper mills.”
Paper mills surround the Charles Ingram facility on all sides. As competition for smaller diameter trees grew extremely tough, the company was forced to make a choice: a big investment aimed at adjusting to a “larger” smaller log, or shutting the Willow Creek line down.
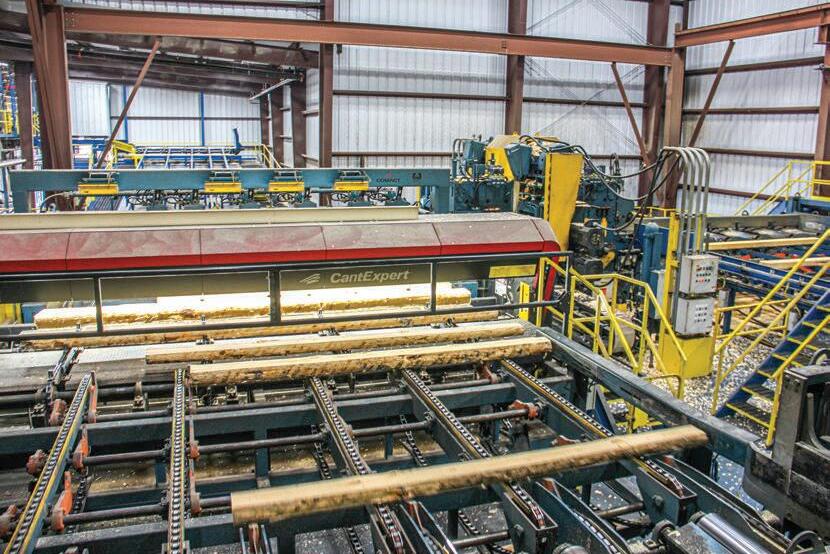
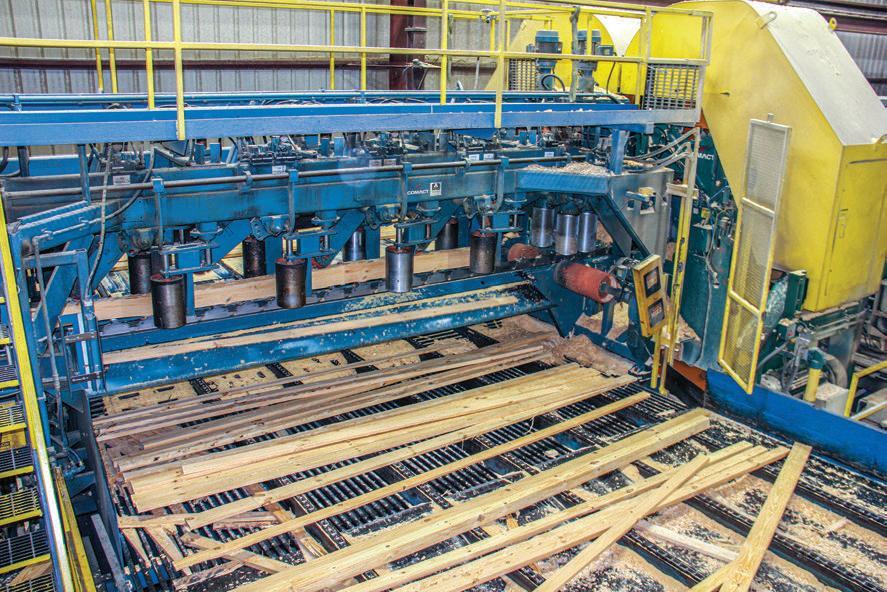
“Fortunately, the lumber market after COVID allowed us to fix the problem,” Moore says. In an effort to continue op- erating the Willow Creek mill, Charles Ingram Lumber reinvested in much needed upgrades.

“I was a forester for a long time and saw first hand how quickly the resource changed,” Moore says. “It was fast. So we pivoted, we reinvested a lot of money to get it right.”
The solution was fairly obvious: The small log line just didn’t need to be quite so small anymore. In fact some of the butt cut logs were being taken from the small side over to the large log mill. “We don’t have the glut of super pulpwood material, but we also don’t have the large logs anymore either,” Moore states. “It is somewhere in between. So this (setup) fits the log resource we now have.”
He says they don’t do titles here, but Moore, a forester who once served as procurement manager, now helps manage day-to-day operations and production at Charles Ingram Lumber, while Thomas Brodie focuses on regulatory and financial management as well as quality control for the family-owned operation in business since the 1930s. In senior management are Jim Anderson (production) and Thomas’ father Furman Brodie (regulatory/financial).
New Line
The Charles Ingram Lumber team took out the entire sawing system on the small log line, everything after the bucking line and before the trimmer/ sorter, right down to the concrete floor. They removed the Willow Creek line’s Comact DDM6 profiling line and replaced it with a BID Group-Comact infeed optimized sharp chain (OSC) with chipper canter on 30° V slides, chipping-profiling heads module and twin band. It’s preceded by new True-shape C1-Scan scanners and quad rolls flying log turner.
They had already bought the Cetec twin band and had it in storage. “Comact came in to help get the older Cetec twin band saws up to speed and modernized,”
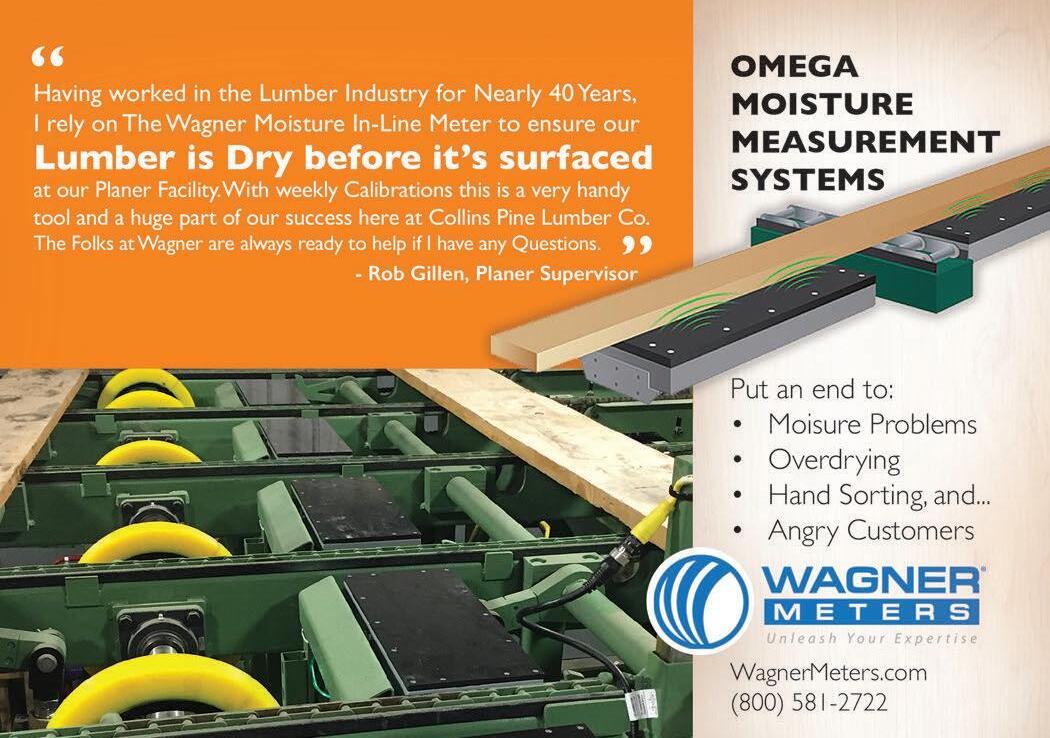
There was some space constraint and the new line configuration had to be modified some. An edger wasn’t an option due to space constraints, so they went with the profilers before the twin, and they also installed a new Comact mini-curve-canter with profiler and transversal infeed position table preceded by a Comact CantExpert transverse scanning and optimization system with A1 software. The mill constructed a new building to contain the Comact mini-can-
Tinsley Consulting Group from Hot Springs, Ark., handled engineering on the project. “Without their support and vision, this project would have never gotten off the ground,” Moore notes.
With the upgrades completed, Charles Ingram Lumber successfully achieved its goals for the Willow Creek mill. “Since this project we have really done well and have seen results in everything,” Moore asserts. “The gain in yield is considerable. Production has gone from 150MBF a day to 250MBF or so,” while maximum log size increased from 10.5 in. to 16 in.
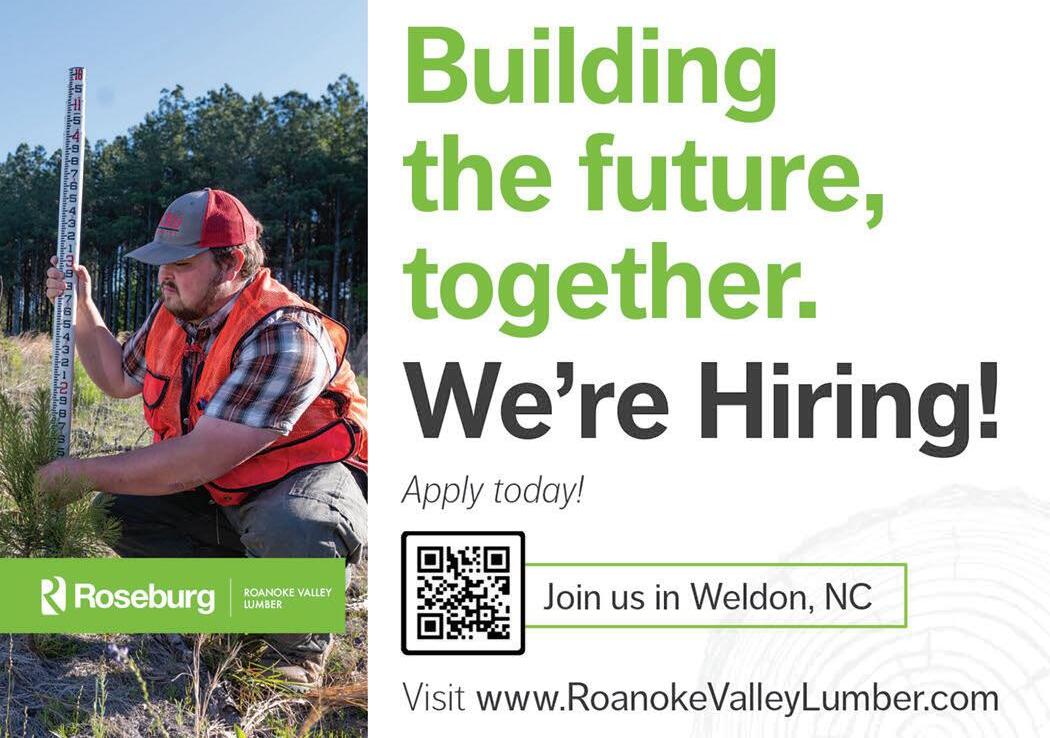

“Everyone knows not every project goes so smooth,” Moore adds. “But this was a dream project. The equipment vendors were excellent. I can’t say enough about Comact and Columbia Construction. They did a really good job. The follow up from Comact and Columbia Construction was excellent, and the machines worked. They do what they’re supposed to do.”
The mill shut down Willow Creek on October 28, 2021 to begin the upgrade. The project was completed in about two months, with the new system running just before January 2022. “We spent January working out bugs and really got it going in February, just about a year ago,” Moore says. “After a project of that magnitude, where you literally tore it down to the ground, and built the minicanter and gang off line in a hole where nothing was there before…to do all that in two months was really good.”
Mill Flow
Each mill has its own crane. A LogPro crane, bought from Timber Automation, unloads on the small log yard. A 22 in. Nicholson A8 debarker, added in fall 2022, and an existing MDI metal detector complement the original Huot fixed saw slasher deck, built with the small log mill in 2001.
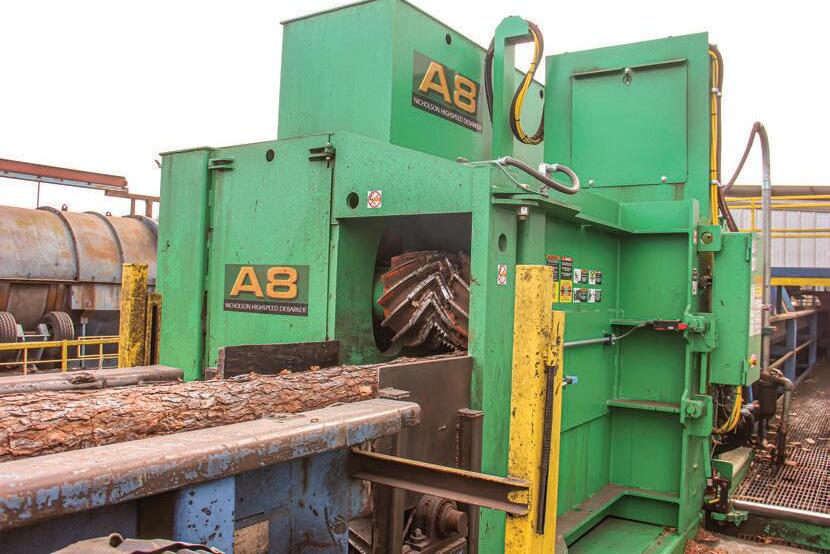
Bucked logs progress to one of six decks; three lead to the sharp chain infeed, one to a chipper and two are for rejects (oversized or defective logs). “When we were running smaller logs, it was critical to have those bins because you were kicking out a lot,” Moore says. “We had a narrow window for optimum log size. Very little gets kicked out now.” A Comact scanner sorts logs automatically to the appropriate deck. Oversized logs go across the property to the big mill. Undersized and defective logs transfer to a Fulghum 96 in. chipper.
As for the three infeed decks to the mill: one has a Brunette flare butt reducer, middle deck is for 12 ft. logs and the third is for 16 ft. logs. That one loads into a Comact wave feeder, while the other two decks still use the original Huot feeder. Logs from all three decks ultimately load onto the Omega sharp chain and through the new Comact twin band profiling line. Cants and sideboards flow into the new adjacent building, where some cants are profiled at the mini-canter, before running through the Columbia Construction gang. Profiler knives are from Lindsay Forest Products.
Longtime sawmill machinery innovator and fabricator Scott Bye at Columbia Construction built the gang saw. “We feel like we got a hot rod,” Moore says. “It is a very nice gang, with 800HP direct coupled to the saw arbor.” According to QC supervisors Kevin Johao Vitiry and Paxton Smith, the gang can run up to 600 FPM. “Saws don’t shift on the arbor,” Smith says. “The whole saw box moves. The press rolls are pre-positioned on the mini-canter and the gang from 4 to 6 in. thicknesses.” (At the big mill they cut up to 2x12s.)
From the gang’s exit, boards flow back around under the twin band outfeed toward a hybrid sorter line (half Carbotech, half Timber Automation), moving up to an unscrambler with screw rolls built by David Reiter of RTS (Reiter Technical Services). “He did a very good job,” Moore says. “He has built transfer decks for us before.” In fall 2022, the mill further added a new Comact board dealer to speed up the handoff to the Baxley trimmer, which has a Timber Automation trimmer optimizer. The small side operates a Gillingham-Best stacker.
Other Work
Willow Creek wasn’t the only beneficiary of recent investments. The large log mill has three lines: a twin band, a quad band and a headrig/carriage. A Corley carriage with Salem 6 ft. bandmill headrig was another recent project, just completed fall 2022. That line and the twin band line feed lumber through a Columbia gang, while the quad band line leads to an Omega gang saw. Everything from both gangs flows to the same trimmer sorter line.
Green lumber from both Willow Creek and the large log mill ends up at the dry end. Charles Ingram Lumber runs several continuous dry kilns including NOREV DPK (dual path kiln) dry kilns (for more on this, see the article featured in the February 2021 issue of Timber Processing). A Timber Automation parallel sorter was added to a Miller Mfg./BID Group high-speed planer line around the same time as the small line upgrades. “That was another good project,” Moore says.
The company has also invested in a well-equipped filing room in recent years, choosing not to farm out filing. They now have separate rooms for circle saws and bands, featuring an array of the latest sharpening, tipping and leveling equipment.
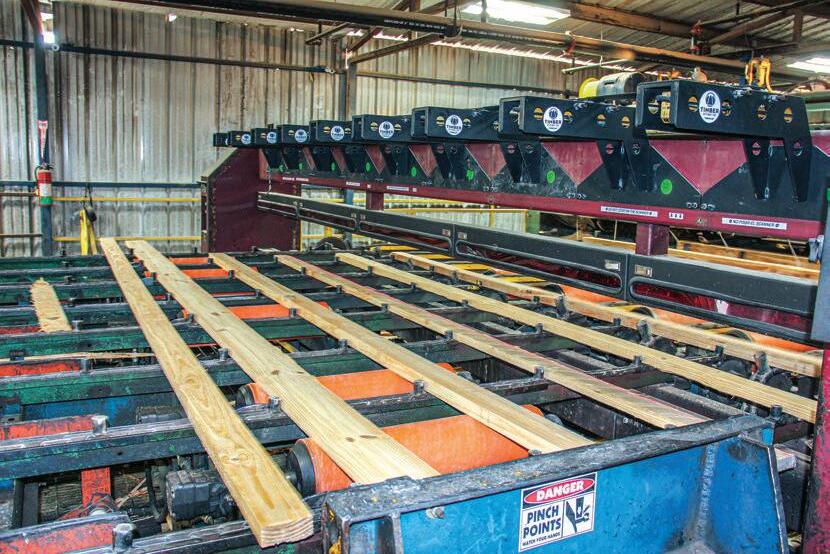
Another late 2021 addition: Charles Ingram Lumber is now in the wood pellets business, as Effingham Pellets LLC. Seeking additional markets for planer shavings besides MDF plants, the company seized an opportunity to convert shavings into pellets and export via Savannah to the biomass power industry in Europe. They operate a Prodesa pellet mill.
“It has been a learning experience,” Moore says, acknowledging that they had no prior experience in this arena. “It is highly affected by atmospheric conditions like relative humidity, ambient temperature, and the moisture content of the shavings.”
While investment in upgraded equipment is important, Moore emphasizes that the company’s greatest resource remains its people. “We have the best employees in the world,” he believes. “You can have the best equipment and processes, but at the end of the day have to have the right people to run it. We are very blessed with some very good, intelligent people who believe in what they’re doing and come to work with the right attitude. It is a pleasure to work with them.”

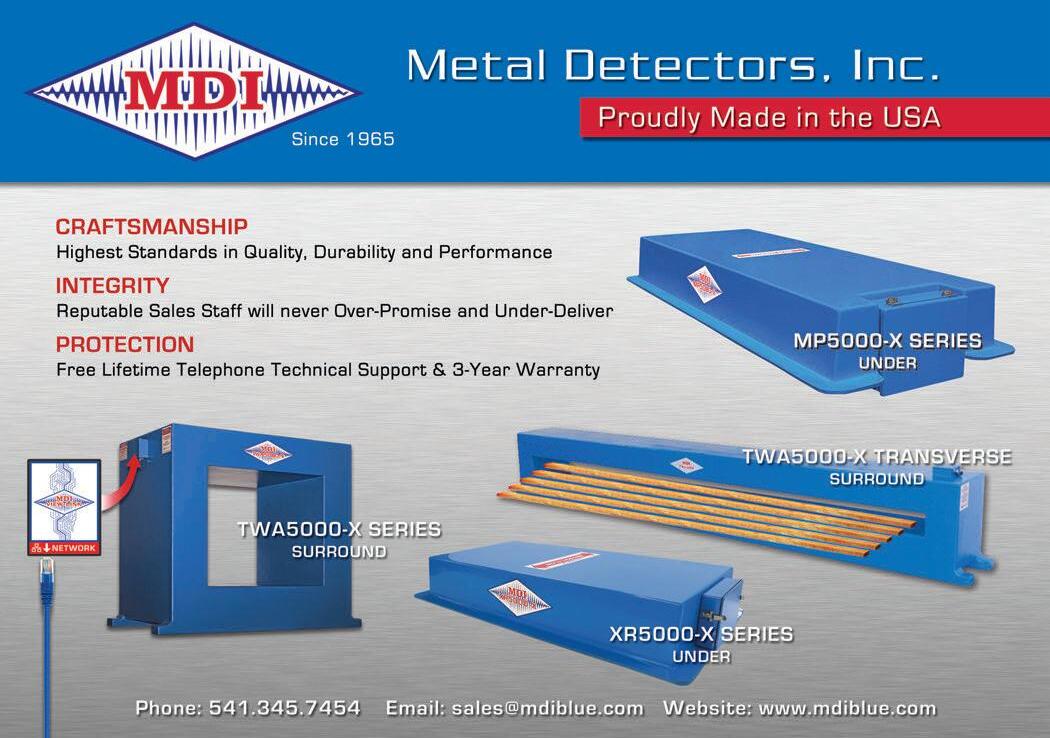