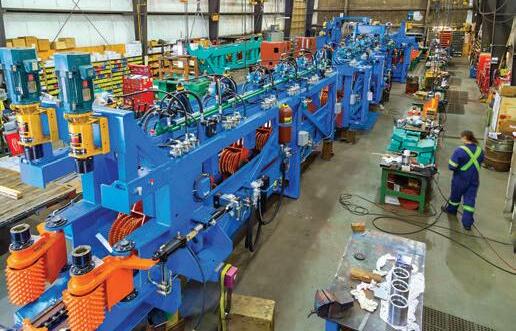
2 minute read
CANTERSPROFILERS
Optimil
Optimil’s canter profiler feed section consists of a heavy duty auto rotation conveyor, a log turner and a skewing-slewing-tilting infeed. An extended (DLI) length infeed precisely positions the log to achieve maximum yield as calculated by optimization software. Logs are fed through the infeed system on a pneumatically tensioned high speed roller chain and work in conjunction with the coupled overhead hold-down rolls to maintain control of all log sizes and to ensure accurate log transport. In order to pre-position spiked rolls and control the log as it enters the bottom head chipping assembly or sharp chain system, linear positioners are seamlessly incorporated along the line.
The two-sided canter systems, typically used in conjunction with secondary horizontal curve-sawing systems, use conical side heads to produce two-side cants in which logs feed through on a sharp chain. These conical disc chipping heads are positioned on the log 30° sideways, incorporating low friction linear bearings to produce high quality chips and achieve optimum accuracy. Optimil’s patented non-rotating anvil provides superior log guiding and minimum deviation throughout the chipping section.
Optimil’s four sided canter utilizes drum type heads and a mini spline guiding to offer feed rates of 750 FPM while maintaining chip quality. The new four-sided canters have been developed to promote dust and chip containment.
More feed rolls have been added for better control through the entire system; all chip heads and feed rolls are driven by U-joint drive shafts operated through remote Rex gear boxes. Side board profilers can be added to both two and four sided canters to help eliminate the load at the board edger system. These heads are positioned by the optimized solution sent by the scanner located in the extended length (DLI) system. The side board solution can be skewed up or down the side of the cant.
Usnr
USNR has a long history manufacturing gangs and has developed upgrades that can increase production levels, efficiency and profitability in your mill. We combine the latest technology with innovative design to develop high performance, end-to-end, valuefocused solutions. Whether your goal is improving yield, expanding production, or entering new markets, we can help you get there.
Improve the performance and accuracy of your curve-sawing gang with the Remote Saw Mismatch Adjuster. A linear positioning hydraulic cylinder moves the top arbor sawguides to match the bottom arbor. The system also ensures alignment between saws on the top and bottom arbors during spline cuts and can be biased from the HMI. The result is little to no saw mismatch in your boards.
The pivoting drive base upgrade offers a strong and accurate motor base for arbor drives, enabling users to tension and/or replace the poly chain belts without causing misalignment between the motor shaft and the arbor. This keeps the poly chain sprockets perfectly aligned after adjustment. The pivoting drive base replaces the original 4-post motor base and alleviates the need for a sprocket alignment after every belt tensioning/replacement procedure.
The pantograph arm conversion for the McGehee GEN-I double arbor gang is designed to improve uptime and reduce maintenance, while maintaining safe operation. With fewer belt changes required, the conversion provides ongoing time savings for your maintenance and production staff. It also offers improved access while maintaining safety features. Other key features include larger sprockets and belts, eccentric jackshafts, and opening belt guards.The motor drive arrangement upgrade improves access to the HSS arbor drive components by rotating the motors 180°. This places the belt drives outside for better access and faster belt changes. Belts drive the arbors using jackshafts, torque-limiting couplings, and drivelines. Arbor and jackshaft rotation sensors offer improved troubleshooting.
When mills work with manufacturers to find ways to improve equipment performance, solutions can be found that may enable them to run for another 10-15 years. USNR is proud to offer performance-enhancing upgrades with quick paybacks.
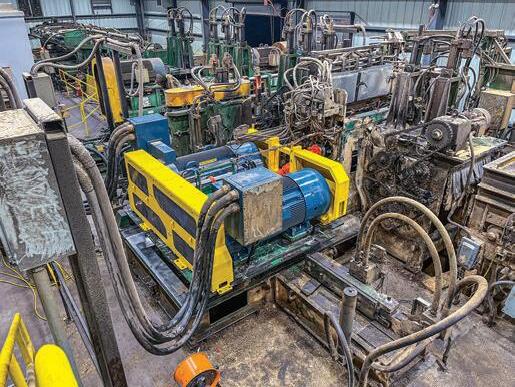