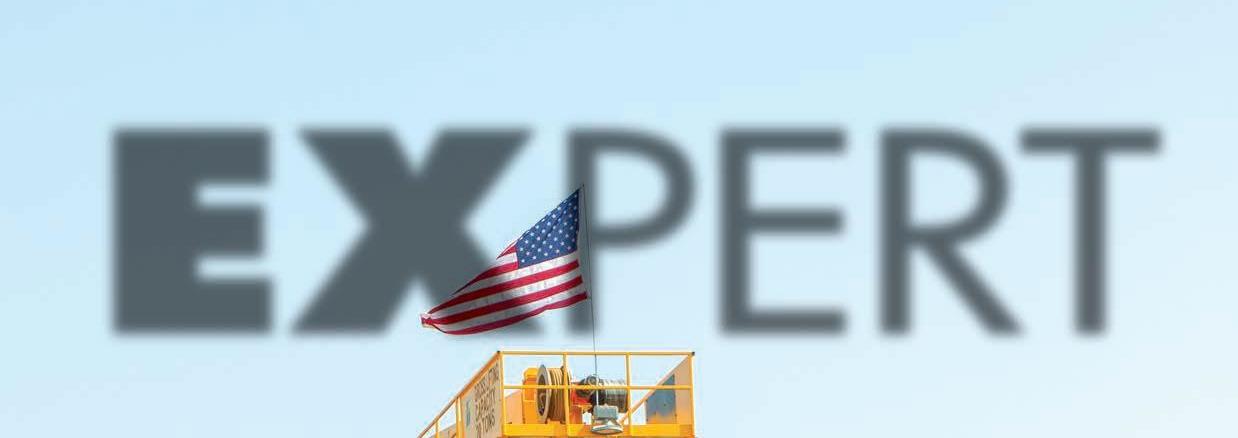
14 minute read
DEMPSEY WOOD PRODUCTS
PROJECT EXPERT
By Jessica Johnson South Carolina SYP timbers producer, Dempsey Wood Products, keeps lighting up the scoreboard.
ORANGEBURG, SC
In a time when greenfield southern yellow pine sawmills are popping up like seedlings, Dempsey Wood Products (DWP) has been standing strong in South Carolina at its 32-year-old site. DWP, led by Ronald Dempsey, son Parker Dempsey and project (and mill) manager Michael Gulley, has been moving about the mill the last few years, implementing major projects from one corner to the next. It’s not greenfield, but they’ve nearly built a complete new mill.






For Parker and Gulley, the greenfield designs aren’t as fun. The challenge, and fun, comes in putting together the puzzle pieces. For Gulley, who isn’t family but is pretty close having grown up alongside the younger Dempsey and been nosing around the mill since high school, having owners who want to invest in the mill keeps it exciting. But also, he says, looking forward to the projects helps keep him, and the staff of more than 100, always on their toes.
Dempsey credits the constant project mode to his father, Ronny: “He’s the true visionary behind it all. He’s the one that thought it all through and was the inspiration behind it all.” A common joke between Gulley and Dempsey is what is the next project on Ronnie’s mind. The pair laughs and agrees, “He keeps us busy.”
Like most mills, a challenge at DWP is real estate. There is only so much area to put in new machines. “Most of the time we’re challenged in what we have available because we weren’t a greenfield mill,” Dempsey says.
They don’t mind it. “Seems like each project has inspired another project and opened the door to new visions and new opportunities,” Dempsey says.
As of late, those visions and opportunities have been non-stop. First in 2016 was the addition of a Cone-Omega tru-position sharp chain two-sided canter system, with optimized log rotation and positioning. DWP was kind enough to let Timber Processing in the door in November 2016 to show it off. The next year DWP installed a USNR 68 ft. natural gas batch drying double track kiln to bring drying in-house. But for the Dempseys, this was just the beginning.
“It sometimes seems as though we do things a little backwards and by doing that we can create bottlenecks,” Dempsey admits with a grin. In 2019 DWP started up an entire BID Comact sawmill line that picked up where the Cone-Omega line stopped at the primary breakdown, and a Wellons 84 ft. natural gas drying double track kiln.
Dempsey explains, “We chose to focus on the sawmill first to see what our production could actually be. Once we knew that, we moved on to the rest of the projects.”
“The rest” Dempsey references is new log yard equipment, converting one of the batch kilns to a continuous kiln, extending the other kiln and a two-phase planer mill upgrade that they’re in the middle of now.
The Comact project was a major project that basically created a new facility, Dempsey says. “That drastically changed the footprint of our operation. We went from 65MMBF on a single 60 hour weekly shift to 100MMBF on a single 50 hour weekly shift. This year with the additions, we’re hoping to get to 120MMBF; operating on the same 50
Dempsey Wood Products was FiberPro’s first full line, multi-saw merchandising line installation.
Logs are kicked on a Cone-Omega tru-positioning sharp chain for primary breakdown.
Installing a new BID Comact sawmill line was a major jumping off point for DWP.
With the latest round of improvements in the sawmill and planer mill, DWP now cuts 120MMBF annually.
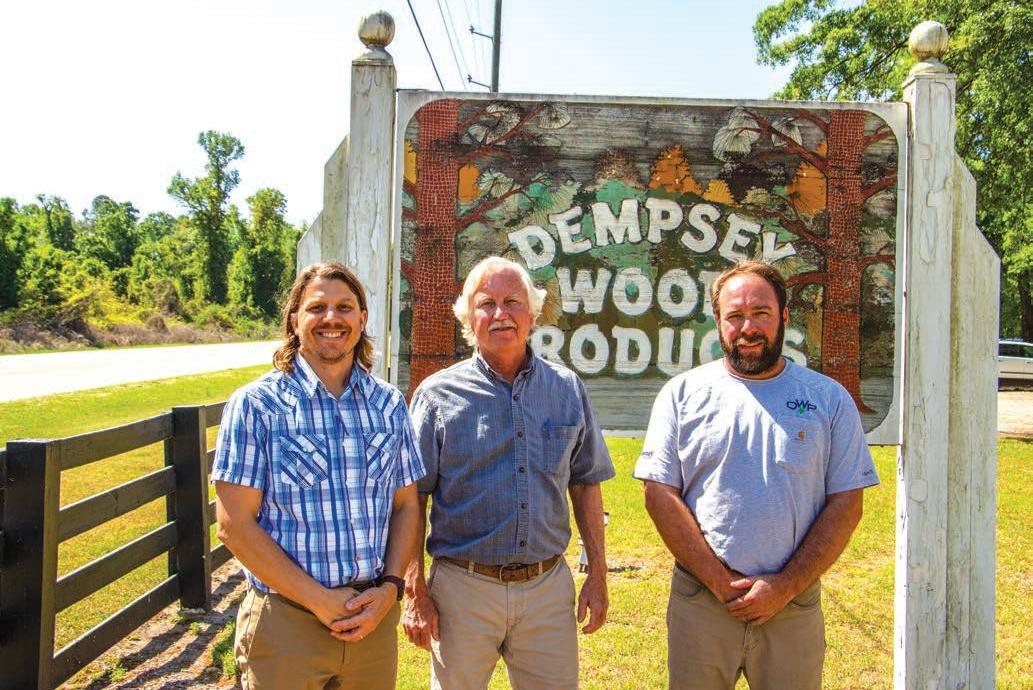
From left, Parker Dempsey, Ronald Dempsey and Michael Gulley

hour single shift,” he adds. “What’s impressive is we've done all the work with very minimal downtime.”
NEW LINE
The Comact installation included a primary breakdown profiler and quad saw box to get sideboards, as well as a TBL3 shape saw and gang with profiling. It finishes with a Comact trim line (double unscrambler, revolving tong lug loader, infinite fencing system, trim saw and smart gate tipple); Comact 50 bay sorter with sorter manager and auto bundle tracking; Moco lumber stacker with automatic stick laying. All controls and optimization were provided by Comact.
At quick glance, this Comact system seems fairly typical of the newer mills in U.S. South. But what makes DWP different is its product mix—shying away from dimension lumber in favor of timbers. Dempsey explains that while most Comact mills are geared up towards mainly dimension lumber production, DWP’s focus is 4x4, 6x6, 5/4x6 decking and 2x4 prime. However, the mill has the option and is set up to run dimension lumber.
Scanners were placed on the sawmill line and trim line to see knots, something new for DWP. “Vision was important to us,” he adds, as the mill tries not to push grades and instead pushes quality. “We try to make a good product hoping that through the dry and planing process we don’t have a lot of downfall and don’t have to push the grade, because we grade harder than we have to at the planer.”
As with all startups, there were things that had to be struggled through, but Dempsey and Gulley have no complaints about the support received from Comact. “Things are not going to be perfect,” Dempsey says. “As long as we get the support on the back end, I can’t complain. And, they are 45 minutes down the road—that was a big reason we went with them, being right there, for parts and service,” he adds, referring to Comact’s facility at St. George, SC.
Adding the Comact upgrade and increasing production capacity in the sawmill meant a bottleneck at drying and planing, and once again Dempsey says he feels like they may have done things a little backwards. At the same time the Comact sawmill line was being installed, DWP added a Wellons 84 ft. batch dry kiln. This helped alleviate some of the pressure, but didn’t completely remove the bottleneck. Dempsey and the team decided to add on to the Wellons, extending it 42 more feet in 2021, but keeping it a batch kiln, while the USNR installation from 2017 was converted to a continuous dry kiln in 2020. Dempsey liked how the Wellons dried 6x6s especially as a batch kiln so instead of converting it to a CDK it was left alone.

LOG YARD
A log yard project has been on the Dempseys minds since before the ConeOmega project in 2016, knowing that at some point this would need to be done. That time finally took priority: The November 2020 shutdown to replace the 32 year old Fulghum 87 ft. radius crane with a new electric crane and 25 ton Mack rotating grapple, an almost identical crane to the old one with the exception of the hydraulics. It was the smoothest upgrade and install Dempsey says he’s ever been a part of. “It was almost like flipping a switch,” he says. The old crane was down and new one running in under three weeks. The sawmill never missed a beat with the help of a knuckleboom and wheel loader.
As with many projects at DWP one thing usually serves as a jumping off point, and for the log yard the crane was it. Next came an updated Valon Kone 22 in. ring debarker, supported by an MDI metal detector, USNR Bio-Luma optimization and UNSR controls (with Mill Track) on a FiberPro multi-saw merchandising log bucking system. This was among the first full-line installations for Josh Krauss’ new venture, FiberPro. Dempsey was pleased with USNR’s controls work on the line: It was close coupled in areas, which can make controls work a challenge, but after a challenging start USNR rose to the occasion and “did a really great job overcoming the challenge and getting everything to click.” Because of the FiberPro equipment design and USNR controls, DWP is able to operate the complete merchandiser line with only one operator.
DWP had a good relationship with Krauss before he began FiberPro, and Dempsey says all involved at DWP were impressed by the how fast and smooth the system, from the clockwork stem singulator through the five saw merchandiser to the electric pinball kickers, was. DWP stepped



First installed in 2017, DWP’s dry kiln from USNR was converted to a CDK in 2020.

out a little on faith in selecting the first screw feeder and cam loader Krauss (and his team at FiberPro) ever built. Dempsey says what sold him was that the system even ends the log and loads it in a forward motion onto the Cone-Omega saw line.
“It gives us a precise gap between the logs going into the saw line, which we put a lot of attention towards, because if you’re not cutting fiber out of the log, you’re cutting air,” he explains. “A lot of mills may focus more on feed speed,
A new USNR trim line in the planer mill kicked off phase one of DWP projects in 2021.
which is great too and we push that as well. But, if you run 600 feet a minute with a 20 foot gap, you’d be better off running 500 feet a minute with a 10 foot gap. There’s definitely a relation there between feed speed and gap.”
PLANER MILL
Because of the expected increased production and efficiency from the log yard and dry kiln production, Dempsey knew they better be looking at increasing the planer mill capacity, so it was time to dive into the two-phase planer mill project slated for 2021. In January, a new USNR trim saw, USNR stacker, Samuel strapper and Carter Machine planer feed table were added to the existing planer mill. Phase two will be completed during the second part of the year and includes a USNR Transverse High Grader (THG), lug loader, infinite fence system feeding into the trimmer and sorter, as well as adding a
A new Samuel strapper was also part of planer mill phase one.
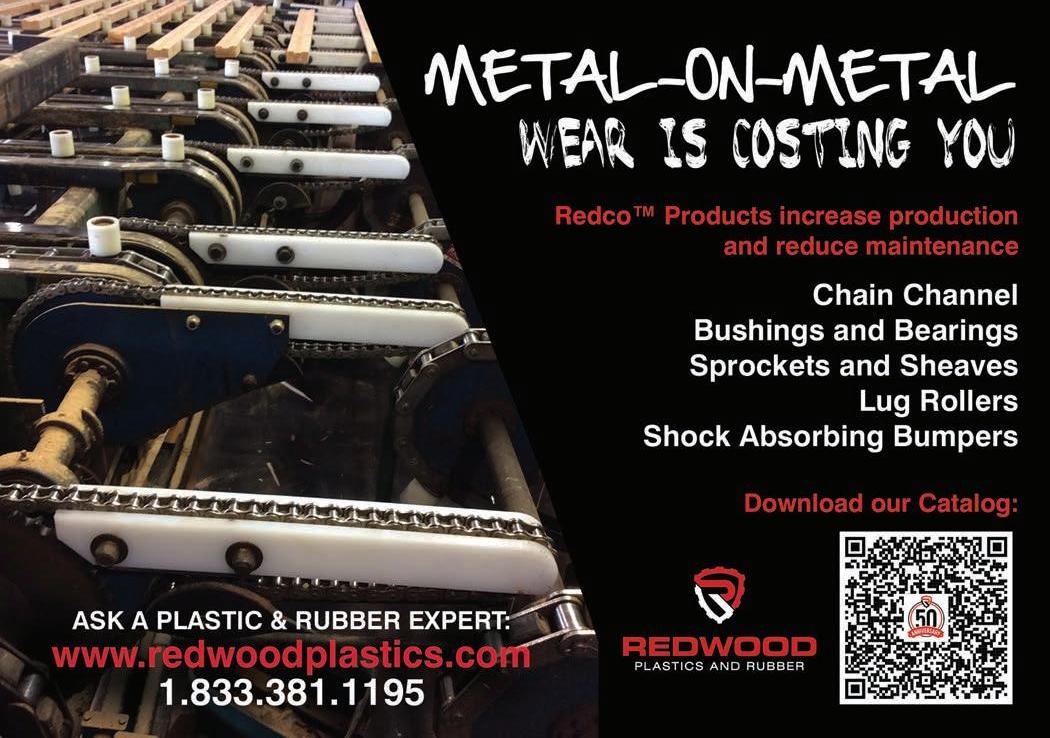
bridge to the existing Yates A20 planer, and a USNR semi-continuous double stack tilt hoist installed on the infeed.
Dempsey admits that the planer is beyond need of replacing and is a bottleneck. Several planers are quoted, but the team wants to get through phase two first, getting the flow handled better, before increasing feed speed at the planer itself.
Instead of going with a single vendor in the facility, Dempsey says each new project is a new opportunity, and the team sets out to build relationships with a variety of equipment vendors, from Cone-Omega to FiberPro to Comact to USNR and onward.
He says, “We try not to judge it on price, but try to judge it on who has the best design for our applications. Most always we are not a cookie cuter design. It takes creative thinking and who’s willing to come up with the best plan. Both the cutting and the handling of our variety of products are unique.” Of course, lead time is a factor as mills and equipment companies have been incredibly busy lately.
Dempsey does concede that one single vendor would be easier at times, before adding, “At the same time it’s probably good we have it spread out a little bit too. We’ve been treated very well by every one—always been treated like we’re a huge customer even though we’re not a multi-mill, huge corporation.”
MILL FLOW
After all phases of the planer mill project are done, Dempsey says his goal to focus on day-to-day operations and efficiencies. Then again, he says every year he and Gulley laugh, wondering what the elder Dempsey might have on his mind: “We’re always kicking around other options, never know how serious we will get.”
DWP processes logs from a 60 mile radius in sizes no bigger than 18 in. “It’s important for us to target our ideal log size,” Dempsey says, “which is around 12 in. DBH.” Overall, log availability is good. “We are blessed with quality wood suppliers,” he says.
Logs are trucked in and purchased at the gate. Unloading happens with the new Fulghum crane, and then is either processed using the new FiberPro merchandising line, or put into storage. From the Valon Kone debarker to the FiberPro line, logs are kicked onto a Comact scan chain with Comact scanning, then to the Cone-Omega tru-position sharp chain primary breakdown line, which produces two-sided cants, using Key Knife chip heads. From there cants are further processed using the new Comact sawmill line, by profiling at the primary and running the two-sided cant through Comact’s TBL3 shape sawing gang on the secondary. From the saw line, pieces flow through the Comact trim line, past the unscrambler, to the sorter, and the Moco stacker in preparation for drying and finishing.
Once dried, either in the batch kiln or the CDK, pieces move to the planer mill, planed using the Yates A20 and then trimmed, stacked and strapped for shipping. Industrial markets and applications are also a part of what DWP manufactures and sells.
HINDSIGHT
Many have toured through DWP over the years as the mill continues to put in new equipment, and to Dempsey those tours offer opportunities to look back on the projects—what he would have tweaked and what he’s been impressed by. He says most times, he looks back in hindsight and sees one or two little things

DWP’s Dry End Division is the latest area of the mill to receive significant capital expenditure.
he would have done differently, but does point specifically to getting the Comact lug loader on the trim line dialed in as a great success, especially considering the variety of products DWP focuses on.
None of it would be possible without the key employees. Dempsey says he wants to develop a good culture around the mill, and continuously works at doing so, but most of how DWP operates on a daily basis has just happened naturally, thanks to the people. He credits their “whatever it takes” attitude to the successes of the projects over the years, while also still being able to keep moving production upward.
Dempsey makes notice of the large group of veteran employees, many that have been with the family operation for 20-30 years. Dempsey is also excited about the group of young talent that has taken on major key roles, all of which are under the age of 40, including Dempsey himself and Gulley. They’ve had time to listen to (and learn from) the DWP veterans. "Sawmilling isn’t the same every day,” Ronny Dempsey says. “But, best we can tell this group is here to stay and we’re excited about the future.”
His sentiments are echoed by Gulley who says that without the great people willing to work hard, the new equipment would be almost an insurmountable hurdle. “With something new comes new problems and new challenges,” Gulley says.
But those startup mode challenges aren’t used as a crutch at DWP. “You’ve got to push on through. I don’t care what vendor you go with, you’ve got to work through those challenges,” Dempsey says.
For Gulley, he can always look back and see areas where things could have been done differently. “At the time you think you have all your bases covered on a project, but that is rarely the case. Always learn after the fact and then use it on the next one.”
And with DWP, it’s clear there will be a next one. TP

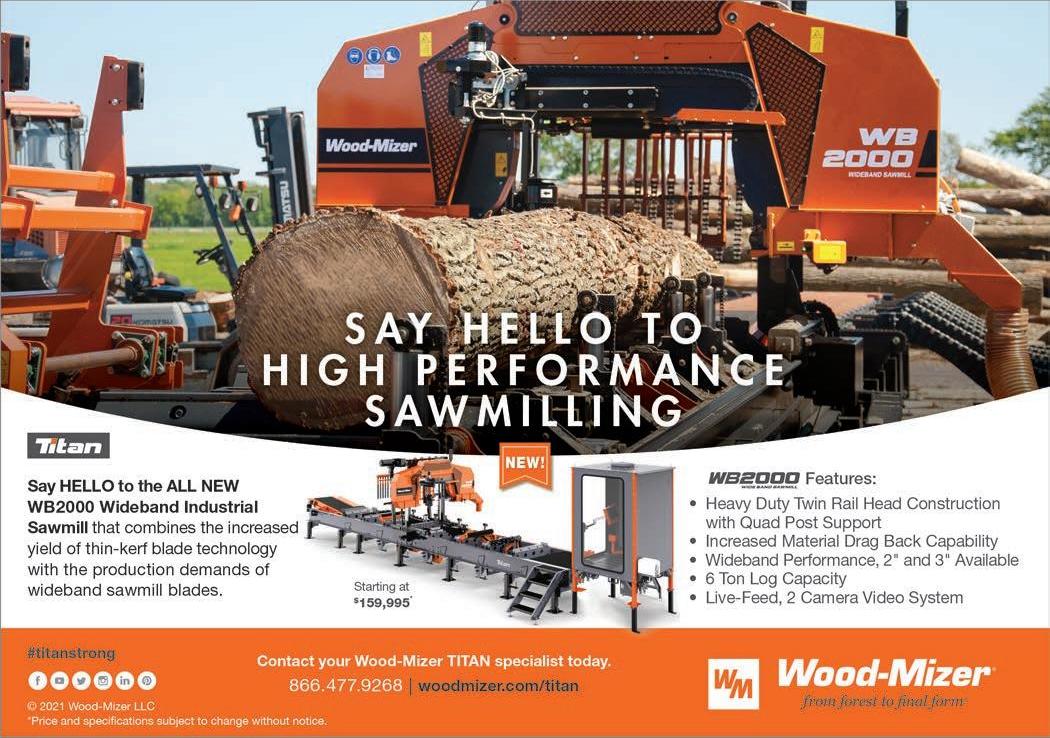


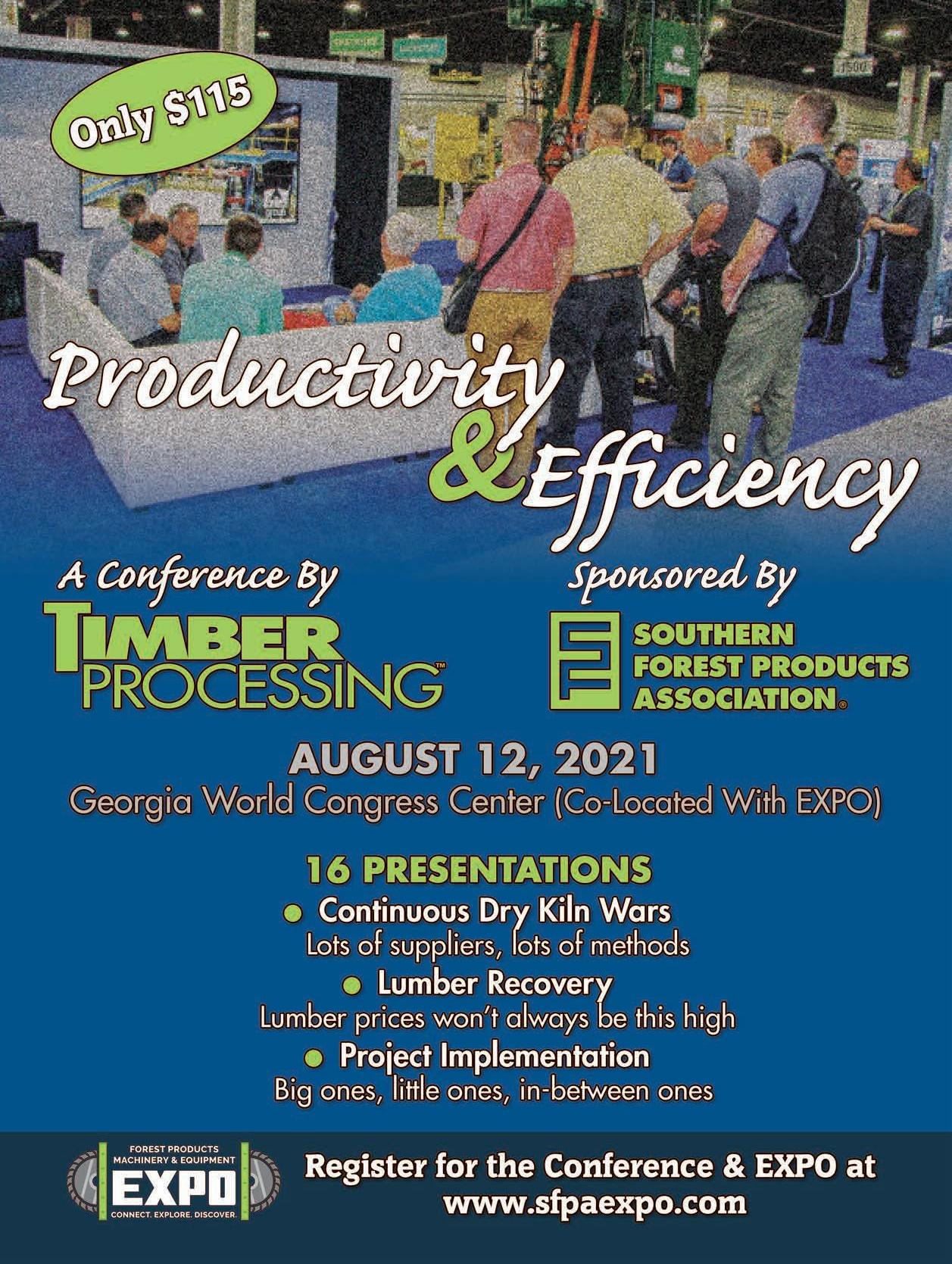