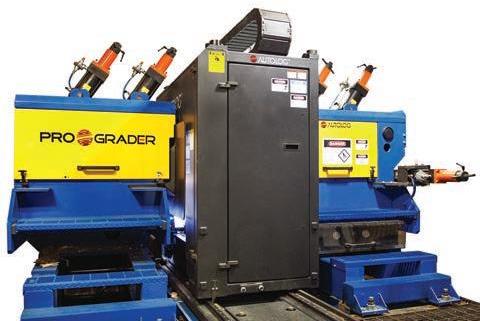
19 minute read
PLANER MILL BONANZA
EDITOR’S NOTE: The following companies submitted these editorial profiles and images to complement their advertisements placed elsewhere in this issue. Please refer to those advertisements for web site and contact information. All statements and claims are attributable to the companies.
AUTOLOG
Autolog’s ProGrader Linear Planer Optimizer has been quoted by mill personnel as one of the easiest grading systems to work with.
What does easy to use mean exactly? It means you can quickly leverage the knowledge and the experience of your key graders. At many locations, graders with limited computer knowledge can learn and delve into the system in order to extract the most value out of every piece. Easy to use means that your resources will be autonomous.
Autolog’s ProGrader is a linear optimizer designed to fully automate the grading process of dressed lumber at the planer. Being positioned just after the planer, its group of sensors (geometric, vision and tracheid), which face each side of the board at 90 degrees, provide an unobstructed reading as well as stop any major planer mechanical production issue. It is a reliable and fast system that can be installed closed coupled or Autolog ProGrader is built with mill personnel in mind. not, processing all dimensions between 1x3 to 6x12, 6 ft. and up.
The 3D geometric sensors measure dimensions, skip, wane, holes and warp; the 2D vision sensors measure knots, rot, splits and shakes, bark, etc.; and the tracheid sensors measure slope of grain and detect knots and unsound wood.
The ProGrader LTS (Linear Tracking System) control module provides information on all data that is collected and how it is trending. It integrates the analysis of detailed and precise data on the tracking and synchronization of boards, keeps track of the board gap and synchronizes its speed with your electrical planer. It monitors and leverages information from all sensors, moisture reader and MSR to maximize the board value.
The ProGrader Linear Planer Optimizer offers the best price-performance ratio with less than one-year payback. Autolog’s automation solution can seamlessly integrate your selection of equipment from the tilt hoist to the stacker.
BID GROUP
What happens when an experienced planerman decides to design and manufacture the most reliable high-speed planer? BID Group’s Miller Planer.
The design of the Miller planer is based on an in-depth knowledge of the needs and problems in the planer mill. The result is innovative design and top-quality material and technology used to facilitate operation, maintenance and ensure maximum uptime. BID Group’s Miller Planer is designed for maximum efficiency and uptime.
The planer is mounted on the heaviest frame and sub-base in the industry to handle the most demanding applications and ensure durability. All planer parts are manufactured with materials that reduce wear and metal fatigue, no matter the price or the complexity. The objective is to ensure maximum uptime, the fastest speed and absolute accuracy.
The planer can process pieces that are 8 ft. + in length (there is no length limit) and 1x3 to 6x12 in. width, with speeds up to 3,000 FPM.
The Miller planer offers many automated functions, and several adjustments can be performed easily on the outside of the machine.
The new Integrated Force Position (IFP) technology allows the feed of thick, thin and wavy lumber even when it is partially covered with snow or ice. The planer has industry leading setworks that ensure repeatability, anti-backlash jacks, hydraulic locks and it is servo driven.
The planer dashboard user interface was recently improved to facilitate interaction and usability. The dashboard panel displays data to provide visibility of all operating conditions, which facilitates troubleshooting and maintenance. Recent features include the machine asset health as well as the vibration and temperature analysis.
The new Profile Splitter module can be installed after the planer to execute the splitting of pieces. It can split the whole range of board sizes and finish the edges and corners. For example, if you split 2x8 in two 2x4s you can process up to 1,200 FPM, so it is actually a production of 2,400 FPM of 2x4.

CARBOTECH
Over the past few years, Carbotech has undertaken many planer mill projects that have put our board handling expertise to the test. Whether it was for normal production or a high-speed production line, standard or custom projects, our customers have been very impressed by our savoir-faire in lumber handling. Now, with our new range of high-performance products like the dual-action electric tilt hoist, high-speed lug loader, new high-speed low-inertia trimmer and dual fork stacker, Carbotech has the perfect competitive solution for any production speed, with any wood species, and in any conditions.
In fact, we at Carbotech have always enjoyed working on custom design projects. Companies are always welcome to come to us with their unique needs. For instance, our lug loader has the ca- The Carbotech team: meeting each customer’s needs. pacity to handle big sections of wood (like 4x4, 6x6 and 4x12 products) that other equipment manufacturers may not be interested in supporting. We know larger sizes can be challenging, but we’re more than comfortable dealing with them.
Our trimmer saw box is equally versatile—whether you have a sawmill, a planer mill, or even a hardwood mill, we can design the perfect saw configuration to make clean, precise trims for softwood and hardwood lumber alike.
Finally, we have many options available to handle your end products: vertical bin sorters, regular- and high-speed tray sorters, special stackers for hardwood and pine with special stacking features, and more. Our mission is to meet our customers’ needs perfectly!
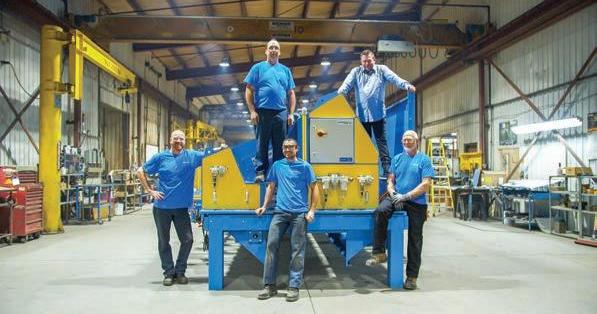
GILBERT PRODUCTS
For 30 years, Gilbert Products has been a leader in the design and manufacturing of sawmilling, construction and forestry equipment. At Gilbert, understanding our customers’ needs, and adapting our planer accordingly, has always been a priority. From smaller operations to high speed planer mills, Gilbert presents five different models of planers: l Gilbert S Series planer for smaller operations and slower speeds from 100 FPM up to 1800 FPM, l Gilbert 6 Roll planer for mid-size operations up to 2800 FPM, l Gilbert High Speed planer, the fastest and biggest model up to 4000 FPM, l Gilbert Moulder for special patterns and profiles Gilbert’s line of planers suits every mill’s needs. l Gilbert Mass Timber planer for big glulam and CLT operations.
One of Gilbert’s valuable customers, Andrew James at Red Stag Timber in Rotorua, New Zealand, explains the benefits of Gilbert’s Pull-Through technology.
“Gilbert’s 8 Roll planer has been a big improvement on the previous planer we had. The pull-through technology has meant we are able to run boards through the planer that would otherwise have to be trimmed or removed from the production line, improving recovery and throughput.
“The control over so many axes and functions like jointing, skip adjust, pressures/guides, with the use of servo motors, which allows fine adjustments to be made remotely, is a game changer in terms of safety as it allows true hands-free operation of the planer, at a safe distance for our planermen/operators.”
How does Andrew rate Gilbert’s after-sales service, even from the other side of the globe?
“I would rate Gilbert’s service very highly; we asked for things that had never been done on a Gilbert planer before. They had to develop not only the hardware but the software to go with it.”

LEDINEK
Ledinek successfully installed its first 3300 FPM heavy duty multi-spindle planing and molding machine, Stratoplan, for the Swedish company Setra. Ledinek developed this high-performance system for robust use in big sawmills that are looking to upgrade operations with planing/sorting lines. It is particularly suitable for processing planed timber and construction timber or as pre-planing in combination with a scanner for processing laminated timber lamellas and for splitting.
The machine at Setra has 10 spindles: The first two are a thickness-thickness planer combination (top-bottom). Spindles 3-4 and 5-6 are double vertical pairs. With associated tools, these two pairs allow switching to any board thickness without the machine having to stop for tool change. Spindles 7-8 are final planing shafts and ensure a perfect surface. The last two spindles 9-10 are a saw combination for splitting with a radius cutter.
Ledinek calls this Stratoplan a “revolutionary evolution.” The engineers redesigned the Stratoplan model at all important points
especially with regard to the feeding of the individual boards. Pro gressive damping was implemented in the upper pressure units and kickback dampening feed rollers were built in, which are lighter but at the same time stronger. The splitting saw combination is also new: The planing machine can accommodate saw blades with a diameter of up to 500 mm. Special system with water mist cools the saw blades. The combined motor power of the two saw units is 235 kW.
Splitting tools are clamped on a Ledinek interchangeable shaft and can be exchanged within a short period of time. Ledinek also supplied Setra with the infeed and outfeed systems. The infeed device “Powerfeed” is designed for an output of 220 boards per minute. When accelerating, the boards reach speeds of up to 5000 FPM over a Gapless high-quality planing and molding at 3300 FPM distance of 10.5 m to the planing machine. The Stratoplan processes the pieces of wood piece by piece—without gaps at 3300 FPM. The system can also be set to operate with micro gaps for better processing of some woods species.
“With this machine we have achieved a new milestone in planing. The new planing system delivers superior finish of wood surface never seen at such processing speeds before. We are looking forward to introducing the system also to North American sawmills and operators of planing lines,” comments Andrej Holc, sales engineer at Ledinek.
Family owned Ledinek has a decades long tradition and know-how in development and implementation of industrial scale wood planers and molders as well as in planing and sorting lines. In last two decades they additionally focused on providing complete solutions in fields of straight and curved glulam, CLT and solid constructional timber. Their best-known patent is one of the IWF 1994 Challengers Award Winners: a calibrating milling system for wood (also known as the rotary planing machine) known under the name Rotoles in Europe and as Rotoplane in North America.

MELLOTT MANUFACTURING
Mellott Manufacturing Co. Inc. introduces its redesigned tilt hoist that incorporates some major improvements since first designed in 1992. The simple design keeps maintenance and downtime to a minimum.
Mellott offers standard machine designs in a 7-ton tilt hoist and a 15-ton tilt hoist. Both models can be customized as required. The Mellott tilt hoist design features a base frame constructed in two pieces so that the forks are able to be assembled onto the columns for shipping and ease of installation. The steel columns are welded to a 10 in. diameter pivot tube on the 7-ton tilt hoist and a 16 in. diameter pivot tube on the 15-ton tilt hoist, with flame cut plates that completely wrap the tube. At the top is a 3 in. square tube to tie all the columns together for extra strength. Steel rollers are used in each of the Mellott’s redesigned tilt hoist keeps downtime to a minimum. forks in order to distribute the load to all of the columns.
The lift cylinders, lift chains and leveling chains are protected behind removable steel plates. This prevents kiln sticks from sliding into this area, limiting damaged and broken sticks.
The tilt hoist is hydraulically powered by dual lift and dual tilt cylinders, cushioned and rated at 3,000 psi. Dual heavy leaf chains are used in an ‘X’ arrangement for load leveling. Packages are lifted using RC240 roller chains on the 15-ton tilt hoist and RC160 roller chains on the 7-ton tilt hoist.
The tilt hoist can be operated with manual or automatic PLC controls. Complete control systems including the main disconnect, and all motor controls can be provided and fully tested at the factory.
The tilt hoist can be a stand-alone machine or can be supplied with conveyors and controls systems to meet production demands.
Mellott manufactures equipment for throughout the mill from log handling and merchandising systems, to band headrigs, linebars, resaw breakdown systems, drop saw trimmers, grading and lumber sorting and conveyors to efficiently handle waste wood material. Mellott also offers a line of tie handling equipment, which includes stackers, sorters, a newly redesigned tie dapper and mat drilling machine. Motor controls packages are offered for Mellott systems.
Mellott systems are custom designed as required. Customers benefit by having manufacturing along with in-house engineering and design capabilities and a willingness to work together to provide the best options for each project.
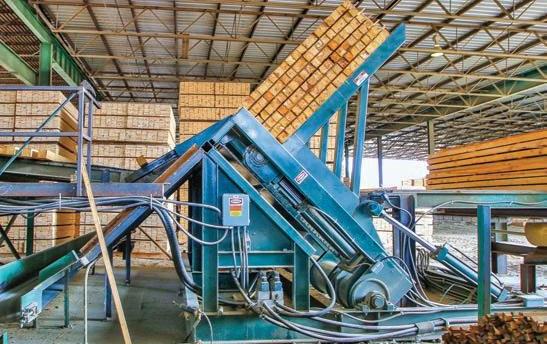
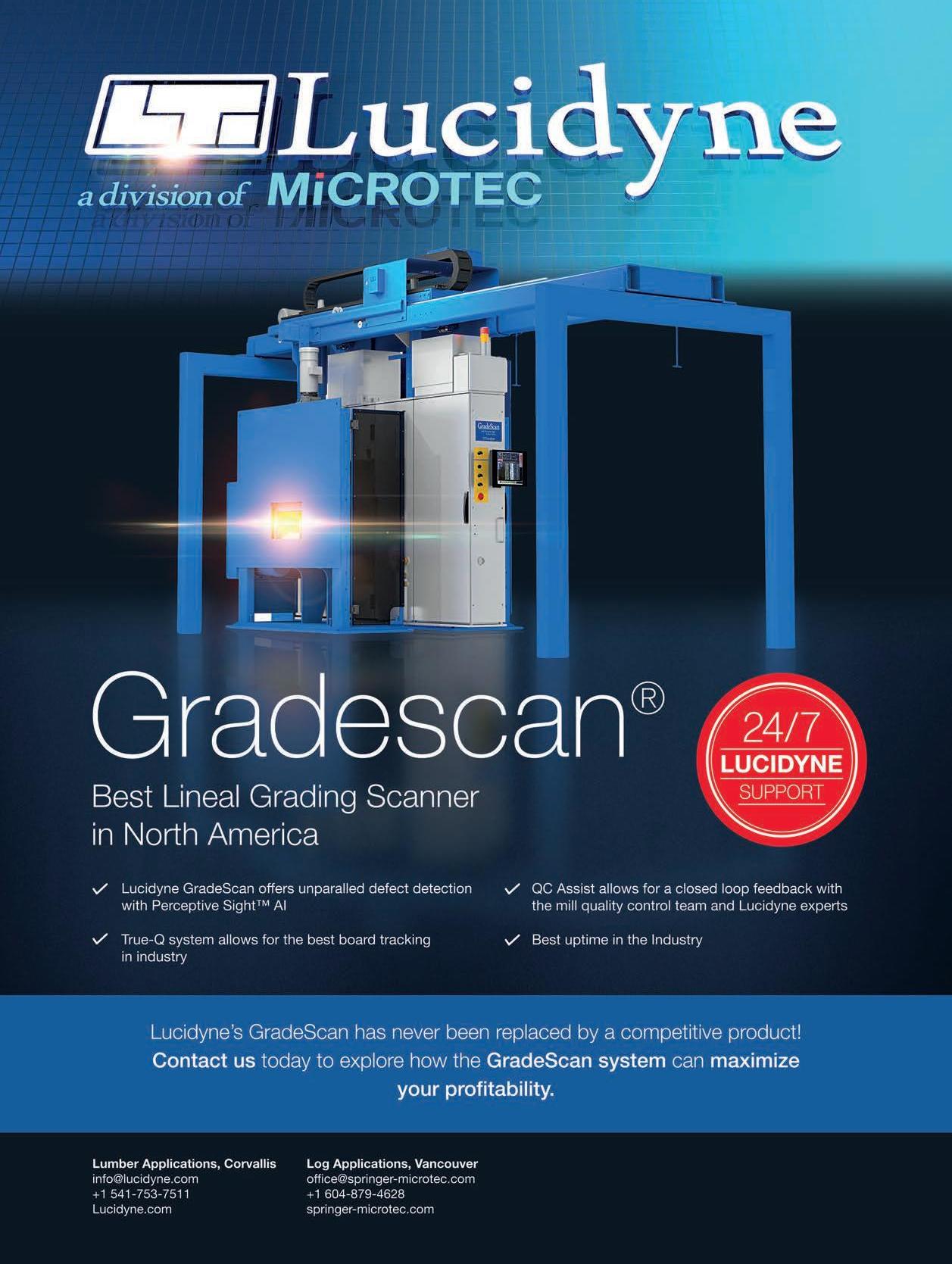
MURRAY LATTA/PROGRESSIVE MACHINE
The Pro Edge-Tec III fully automatic cutterhead grinder is the result of our own “in house” design and engineering department. We have gone to great lengths to listen to our customers in terms of what they would like to see in a fully automated multi purposed grinding machine. User and ergonomically friendly are two terms used very often these days when describing machinery. The Pro Edge-Tec III not only addresses these two issues, it has been designed and built with quality and durability in mind.
Specifications include: l Compact footprint l Proven high reliability l Touch screen set up panel l Simple, intuitive, user-friendly controls l Ethernet access via standard Ethernet switch l Automatic traversing, indexing and downfeed l Fully automatic top, bottom or sidehead grinding l Grinds up to 15 in. length knives to within .002 in. tolerance Automatic sidehead grinder grinds flat knives as well. l Allows Murray Latta service technicians to provide off-site troubleshooting
Murray Latta/Progressive Machine is the official 2009 merger of two very established companies: Progressive Mill Supplies (est. 1954) and Murray Latta Machine (est. 1918).
What hasn’t changed is our pride in workmanship and dedication to providing the highest customer service experience; this has been the key to our longevity. We hire skilled, experienced and certified tradespersons, and we make sure all equipment and materials we use are fit for optimal performance. We do this because we believe in putting quality and safety first—because it isn’t just our reputation on the line, it’s yours as well. We stand behind our work, every time. Guaranteed.
Piché electric tilt hoist: versatility and a clean environment Samuel Coding sends a clear message.

PICHÉ
Piché’s tilt hoist is heavy duty in design, durable and has low mechanical complexity, which requires minimal maintenance. It is 100% electric to ensure a clean work environment. Its automated lubrication system makes sure the cams roll smoothly to minimize wear and maintenance. It offers the possibility of producing single or double packs no matter the length of wood used. The technology uses two individually chained servo-motors which means you can make precise row adjustments even on crooked packs.
The tilt hoist also offers the possibility to save precious time by combining it to a secondary hoist so the operator does not have to wait while the next bundle is being picked up. The speed of operation, durability and minimal downtime makes the Piché tilt hoist fast enough to supply any planer in the industry.

SAMUEL CODING & LABELING
Samuel Coding and Labeling Div. is an industry leader in custom and off-theshelf solutions for the wood products industry. With years of experience in the wood products industry, we are uniquely suited to provide you with solutions that are tailor made to suit your facilities. We provide a full system solution with design, fabrication, installation and ongoing support. With hundreds of installations across North America we offer unparalleled industry experience.
Samuel Coding & Labeling systems for wood products include ink jet grade mark systems, ink jet printers for marketing information, ink jet stencil machines for sawmills and planer mills, automatic board bar coding for retail sales, automatic package tag systems to print labels and staple them to finished packages, and product tracking by integrating printers and scanners utilizing 2D bar codes.


TIMBER AUTOMATION
Timber Automation provides engineered equipment, control systems, optimization technology and turnkey construction services for wood yards and sawmills that maximize yield, increase uptime and reduce production costs.
Baxley’s planer mill lineshaft trimmer has features you are more likely to see under the hood of your car: l 75 HP line shaft drive assembly l Rigid couplings for easy belt change and vibration reduction l Airlift saw ladders, belt driven l Heavy-duty piloted flange bearings l Airlift via cushion stroke airlift cylinders l Base mounted air valves and air cylinders plumbed with hydraulic hoses l All air hoses pre-plumbed to trimmer frame plenum pipe l All solenoid valves pre-wired to terminal strips in an electrical junction box on the near end l Configured for 20 in. diameter saws l Anti-kickback fingers l Heavy-duty single pivot hold-down shoes with airbags l Folding maintenance platform l Integral door and maintenance platform HPU l Precision end trim available
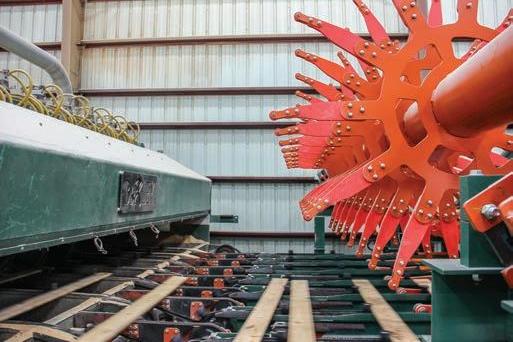
Baxley planer mill trimmer provides mechanical efficiencies.
TS MANUFACTURING
TS Manufacturing designs and manufactures all equipment in the planing mill, except for the planer itself. At the front end, our tilt hoists have great features such as high speed servo lift, automatic leveling sensors and a continuous tilt hoist design with secondary hoist arms for high speed applications.
After the planer, lumber is put into lugs with our high speed Versacam lug loader with speeds up to 120 pcs/min. Bin sorters hold the wood that is sorted by the TS AccuTally software program. Developed a year ago to meet all the demands our customers needed in a tally program, TS now has more than 40 installed and operating. Singulating unscramblers feed lumber onto TS’s electric TS Manufacturing tilt hoist secondary arms servo stacker with servo fork control, servo lift control, servo pull back to skew layers for stability until banded and air gapping in green applications.
A recent installation has our new secondary hoist arm design allowing the customer to start making the next pack while the hoist arms finish lowering the pack and while it exits out of the way.
Next on the list is the end bump and side squeeze before strapping and exiting rollcase and transfer chains. Other than our great machinery, in house controls and second-to-none after sales support help us stand out as industry leaders in in planing mill equipment.

COMING IN JUNE
A SPECIAL REPORT U.S. SAWMILL OPERATIONS & CAPITAL EXPENDITURE SURVEY

USNR
“The new planer mill from USNR has improved our overall efficiency and relieved our bottleneck, resulting in a reduction of over 20% in planer mill run hours. Our packages also look better and neater.” —Mike Kusar, Mill Manager, Montrose Forest Products, Montrose, Colo.
USNR planer mill designs feature proven products that deliver efficient, high-speed productivity to lumber manufacturing operations. Montrose Forest Products has experienced the benefits.
Their new planer mill line is designed to run at speeds of 180 lpm and above, depending on product size. The supply begins with the planer infeed featuring a continuous tilt hoist, stick and dunnage collection, planer, Quad Cam lug loader, Multi-Track fence, back-to-back lineshaft multi-saw trimmer with P.E.T. saws on a second shaft downstream from the trim saws, 30-bin pusher lug sorter, high-speed Low-Profile stacker with magazine lath USNR equipment installation at Montrose Forest Products planer placer, and quad paper feeder and cutter. The Low-Profile stacker mill before the building was finished. operates around 23 tiers per minute.
Included in the project is USNR’s Transverse High Grader (THG) with Deep Learning technology for the best automated grading capability. THG features an end grain scanner used to locate a board relative to its parental log. This provides the optimizer with data for use in knot projection and pith location. The THG integrates USNR’s WinTally system to manage sorts for targeted products the mill wishes to produce. USNR’s MillTrak machine vision-based system manages the flow of boards at the planer infeed, and the MyMill mobile sorter control monitors and controls the sorter from any location within the mill’s network.
THG shares the same Deep Learning optimization platform with all other USNR vision grade scanning products: Lineal High Grader, BioVision for green mill grade scanning, and AddVantage chop and rip scanners for the secondary manufacturing sector.
Kusar sums up the project: “With this new technology we look forward to being able to offer more products to our customers than previously. It also contributes to a safer, more efficient, and more profitable operation.”
Vecoplan VHZ 1600 wood scrap shredder

VECOPLAN
Woodgrain Lumber in Emmet, Idaho has purchased its first Vecoplan shredder to process planer end cuts. The only scrap Woodgrain does not use in-house, the planer end cuts are shredded before sold to a composite building materials manufacturer.
The selection of the VHZ 1600 model, a heavy-duty large wood shredder, was based on two main reasons. Vecoplan produces uniform pieces, which will help a Woodgrain key customer feed better quality material into its production line. Prior experience at another facility is another reason that drove Woodgrain to choose a Vecoplan shredder.
“I was put in charge of improving our planer end cut waste process so we could serve a major customer,” says Ryan Skinner, Emmet’s production manager. “We chose the Vecoplan machine because of the quality and consistency in the material output.”
Vecoplan Midwest, LLC is a subsidiary of North Carolinabased Vecoplan, LLC, both of which are part of Vecoplan AG located in Germany. The companies manufacture industrial and mobile shredders for size reduction of virtually any material, selling into plastics, wood, biomass, paper, recycling, and waste-to-energy markets. Vecoplan Midwest focuses on the wood and biomass business, and sells pelletizing equipment in addition to shredders.
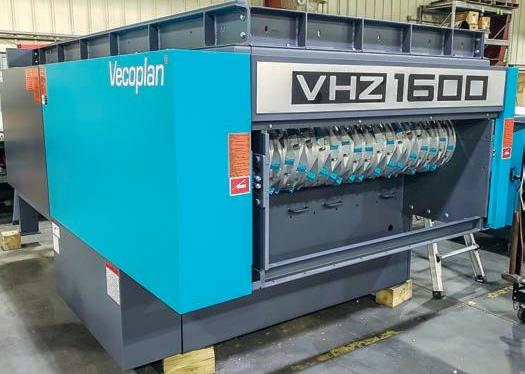

SECOND LOOK ALBANY
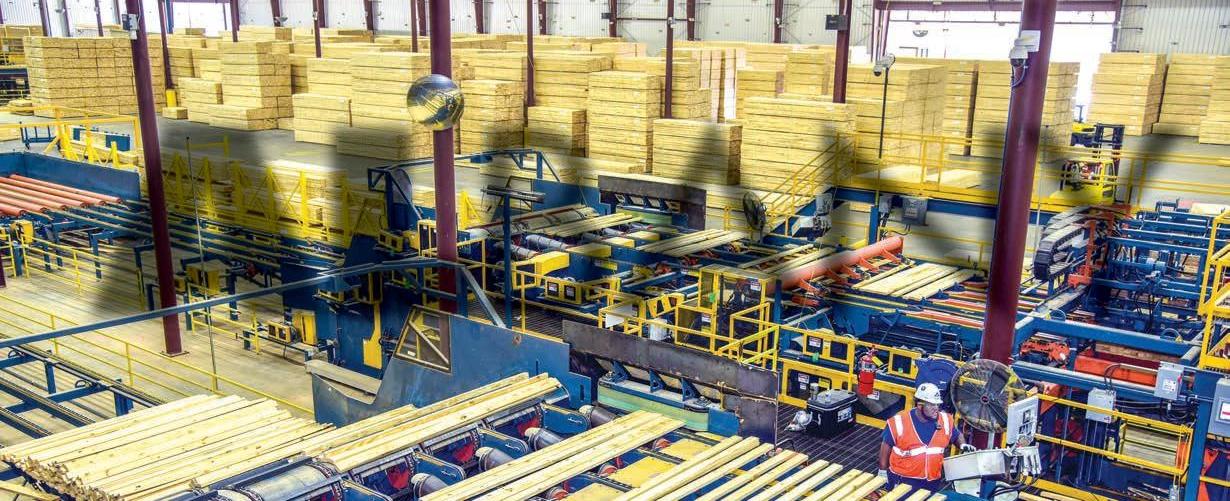
The cover story of the March issue was the startup of the new Georgia-Pacific greenfield sawmill in Albany, Ga. The Albany mill fulfilled the “hat trick” of an amazing series of new mill startups by GP that occurred in under three years. The Albany mill followed startups at Talladega, Ala. and Warrenton, Ga. GP worked closely with BID Group on all three projects, which combined added another 900MMBF of lumber production capacity to GP’s portfolio. “A big part of what made this possible was our ability to leverage talent, knowledge and skills from across all of Georgia-Pacific and Koch Industries,” commented Fritz Mason, GP Lumber President. (Photos courtesy of GP and Todd Stone Photography)
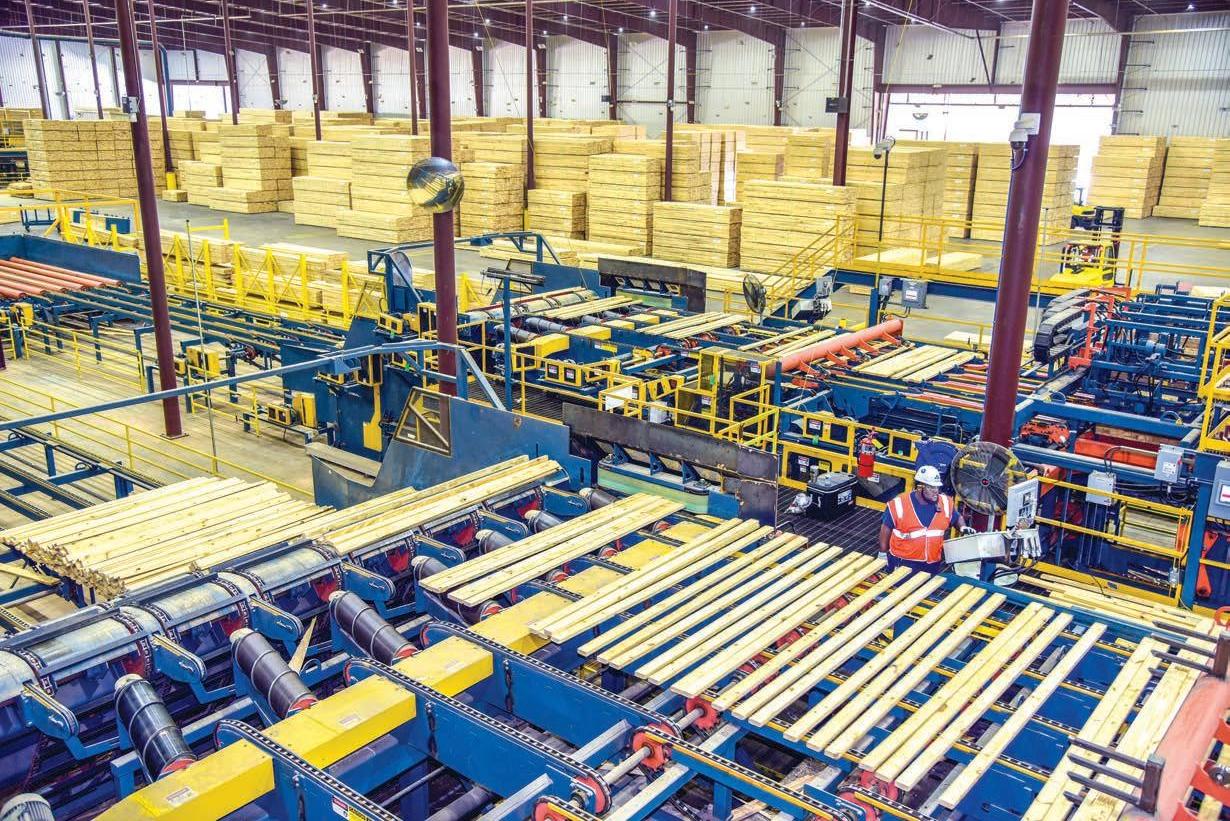
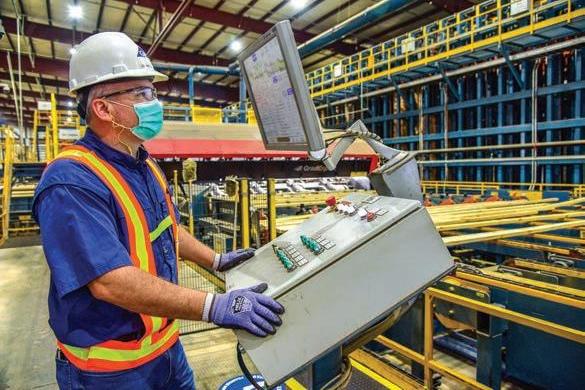
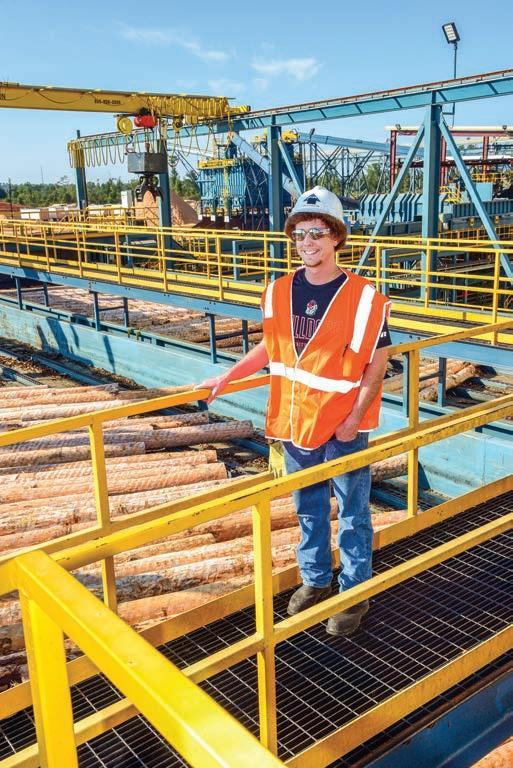
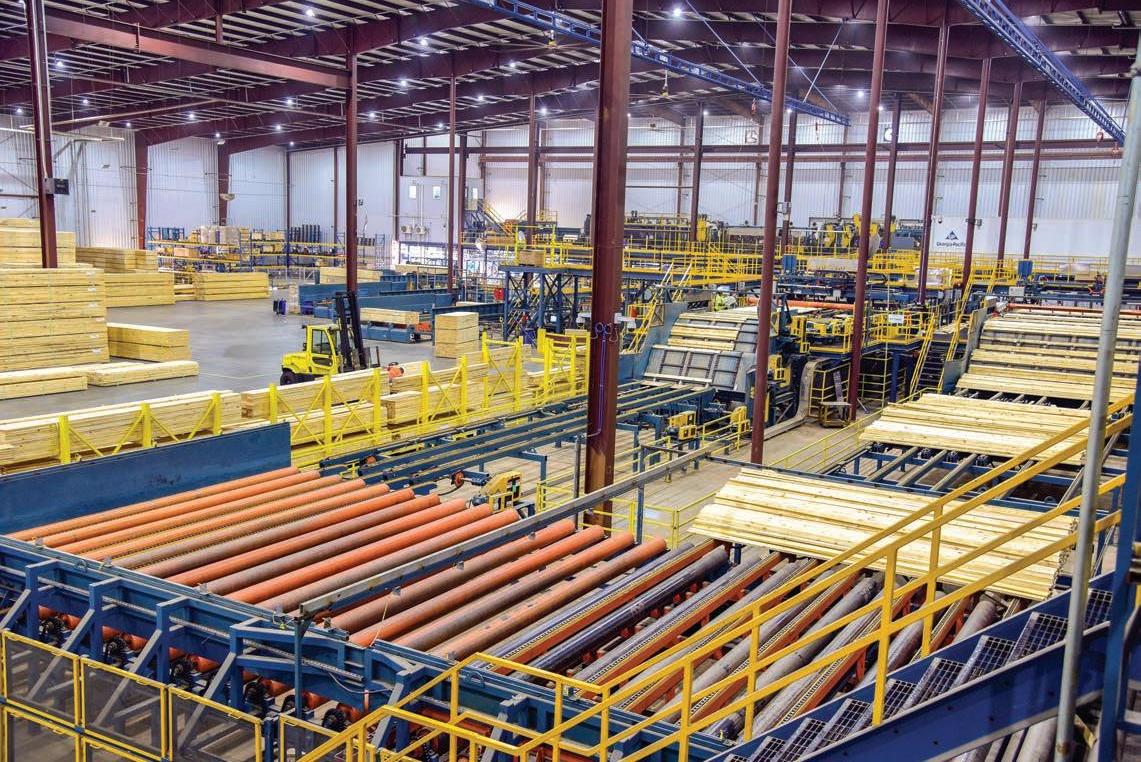

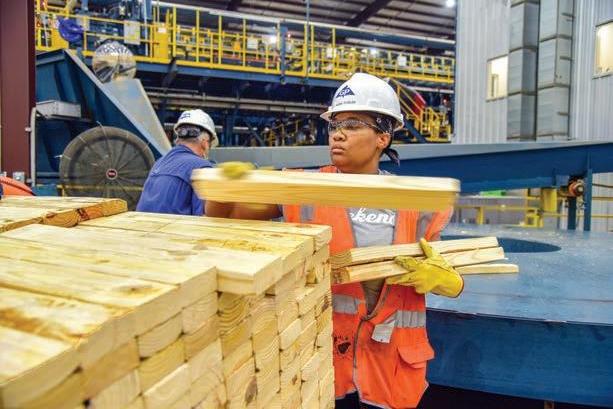
