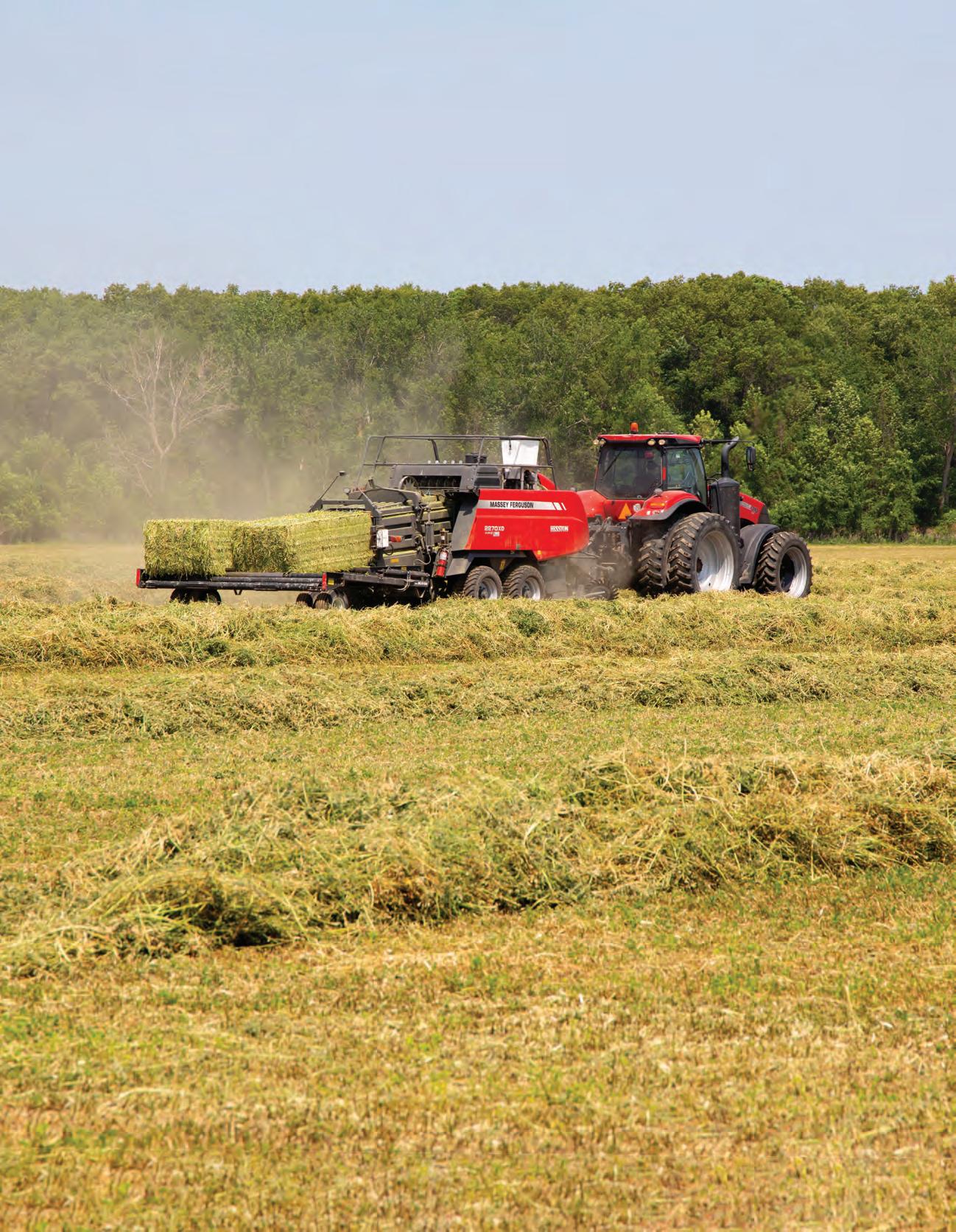

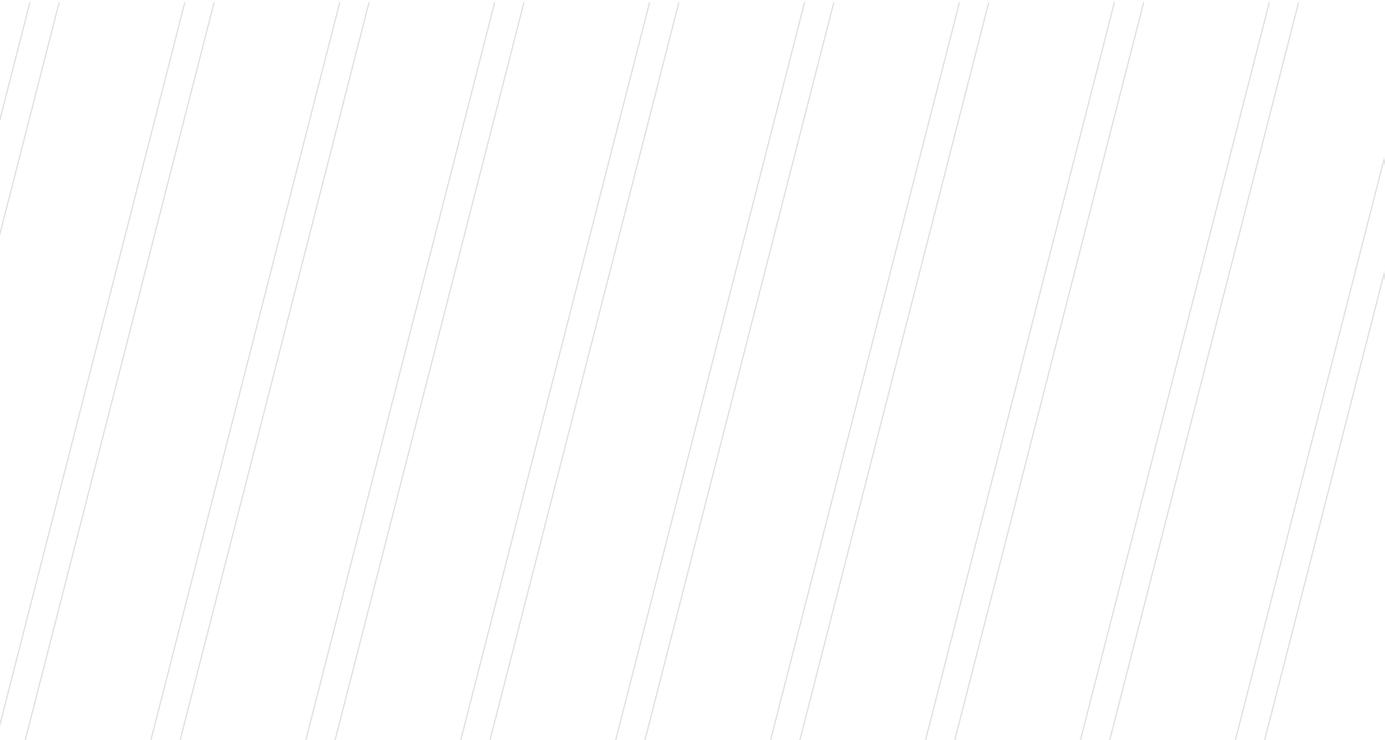
elevate your hay and forage operation!
KRONE Rotary Rakes make a high-quality windrow, regardless of conditions and without contamination for cleaner forage and faster baling speeds!
FIND YOUR LOCAL KRONE DEALER!
Irrigation water from the Missouri River feeds over 1,700 acres of timothy, orchardgrass, alfalfa, and mixed hay grown by sixth-generation farmer Brandon Flynn and his business partner, Jordan Sheaver, near Townsend, Mont.
Haytech takes bale storage to new heights
MANAGING EDITOR Michael C. Rankin
ASSOCIATE EDITOR Amber M. Friedrichsen
ART DIRECTOR Todd Garrett
EDITORIAL COORDINATOR Jennifer L. Yurs
ONLINE MANAGER Patti J. Hurtgen
DIRECTOR OF MARKETING
John R. Mansavage
ADVERTISING SALES
Kim E. Zilverberg
kzilverberg@hayandforage.com
Jenna Zilverberg jzilverberg@hayandforage.com
ADVERTISING COORDINATOR
Patti J. Kressin pkressin@hayandforage.com
W.D. HOARD & SONS
PRESIDENT Brian V. Knox
EDITORIAL OFFICE
28 Milwaukee Ave. West, Fort Atkinson, WI, 53538
WEBSITE www.hayandforage.com
EMAIL info@hayandforage.com
PHONE 920-563-5551
Haytech probes allow producers to continuously monitor bale temperatures and estimate quality losses from their smartphone screens. The nitty-gritty of net wrap and baler twine
There is not one perfect hay binding option. Product selection depends on forage species, harvest equipment, and handling practices.
It’s all hands on deck when baling hay at Strieter Hay Farms near Bay Port, Mich. John and Mike Strieter run an impressive hay operation that grew from humble beginnings. The farm features both a hay press and three hay-drying units. Read more about the operation beginning on page 20.
Photo by Mike Rankin
Mike Rankin Managing Editor
WELCOME to our first issue of Hay & Forage Grower XL. It’s not that our standard six issues don’t have information that larger farms can’t use, but this issue is exclusive to that demographic. So, chances are good that if you received this publication in your mailbox, your harvested forage acreage counter is something north of 500.
As we put together this mailing list, we didn’t discriminate between dairy farms that chop their hay or commercial operations that compress their dry forage into a bale. Custom forage harvesters — you’re included, too. It also doesn’t matter whether you grow alfalfa, bermudagrass, or some other forage that is mechanically harvested.
Of course, “big” is a relative term, and that’s true of all things. At 6-foot, 1-inch, and 235 pounds, the XL designation has followed me around most of my life in the tags that adorn the lion’s share of my Carhartt-dominated wardrobe. Apparently, apparel manufacturers have deemed me as big — in fact, extra-large — but an XXL wearer might view me as famished, although that’s a description that I admittedly don’t often hear.
From a farm-size perspective, the term “big” has changed dramatically over the course of my lifetime. Somehow, we got to the point where 1,000 dairy cows and their associated land base isn’t considered big any more by many people.
If I’ve learned anything over the course of my nearly 70 years, it’s that farm size — as solely determined by either the number of acres or livestock — doesn’t define a farm in terms of its success, impact on the environment, or makeup of the people who own and run the operation. I’m guessing a lot of you already know this. I cut my agricultural teeth on a small farm that milked 30-some cows. That farm has more than doubled in size now, and it’s still one of the most successful farms I know of, even though it remains small by almost all of today’s standards.
Since those early days of my life, I’ve been on hundreds of farms across the country that metaphorically wear the XL to XXXL Carhartt shirts. I’ve come to understand in many ways why family farms have gotten bigger, and in a plethora of cases, extra-large. The easy answer is simply economies of scale, spreading overhead costs over more acres and/or animals. Of course, big doesn’t necessarily guarantee profitability, but it can often help reach that end.
My take is that there’s an even more compelling reason why a lot of farms get big, and it has less to do with profitability than it does with family. Time and time again I hear stories from owners of large operations who tell me they grew in an effort to keep sons or daughters on the farm. Sometimes these farms simply grow in scope from what they were currently doing; other times, new enterprises were added to the operation and overseen by one or more of the siblings.
Large acreages of mechanically harvested forages bring into play some unique challenges. Row-crop harvest has some degree of timeliness involved, but not to that of forage production where consecutive dry days at the right time are needed to harvest a high-quality crop. This must not occur just once, but often three to seven or more times during the course of a growing season. With big acres, big machines are also needed just to meet the timeliness demands of a high-quality crop and minimize labor requirements. During interviews for farm stories, weather and labor are almost always cited by farmers as their two biggest challenges.
As a graduate student in college, our small forage group didn’t get the attention or resources that the corn, soybean, and weed management groups received within the agronomy department. It was then that I learned forage crops didn’t always hold the high esteem directed toward those with row-crop leanings.
That sort of underdog status remains in agriculture for forage crops today; however, it is heartening to see technology being advanced in forage harvesting equipment to help match what has been in row-crop machinery for many years. A lot of these new technologies, though costly, are helping large-acreage farms do more with less, especially from a labor standpoint. Other technologies, such as the HarvXtra trait in alfalfa, also provide additional benefit to larger farms from the standpoint of extending the harvest window for high-quality forage.
Bigger may not always be better or the only way, but bigger is the reality of the agricultural landscape. For that reason, this issue is for you. Wear your Carhartt XLs proudly. •
Happy foraging,
by Mike Rankin, Managing Editor
FROM its headwaters, the Missouri River takes a circuitous route through Montana, North Dakota, and South Dakota. It then forms Nebraska’s eastern border before slicing through its namesake state from Kansas City to St. Louis, where it ultimately greets the Mississippi River. The Missouri constitutes the longest river in the U.S., and its longest single state trek occurs in Montana, where it originates just north of Interstate 90 near Three Forks.
Not far north of the river’s headwaters, southeast of Townsend, Mont., the Missouri is the primary source of water for sixth-generation farmer Brandon Flynn, who owns and operates Flynn Hay & Grain along with his wife, Vanessa, their four children (ages 10 to 17 years old), and his mother, Peggy, who still does all of the swathing and helps with other field operations when available.
Flynn took over the operation in 2017 after his father, Joel, passed away.
Through the generations, the look of the Flynn’s farm operation has evolved and grown, but today’s version touts a hay focus and the addition of a recent partner, a young farmer named Jordan Shearer. The partnership with Shearer, who has a neighboring farm, involves the sharing of labor and equipment
between the two business entities.
“We serve several different hay markets, so we try to keep our hay enterprise diversified as well,” Flynn explained.
“We have stands of pure timothy, orchardgrass, and alfalfa, but we also have a lot of alfalfa-orchardgrass acres. This allows us to meet any customer’s needs.” In total, the operation makes about 1,700 acres of hay each year. Most of those acres are irrigated with pivots. The farm raises an almost equal number of acres of cereal grains and operates 1,600 acres of dryland ground.
Located between two mountain ranges, the farm’s valley location only averages about 10 to 13 inches of precipitation per year, most of which comes
Most of Flynn’s small square bale production is targeted for the equine market in Kentucky. That market has proved to be stable for both hay volume and price.
during the winter. Flynn’s irrigation water is mostly derived from the Missouri River and is controlled through an irrigation district. “We generally never have water availability problems,” Flynn noted.
All of Flynn’s fields are soil sampled on grids and fertilized accordingly. He typically applies phosphorus and potassium to alfalfa both before (March or April) and after first cutting. Grass fields receive a nitrogen application. “I’ve become more interested in soil health the past several years,” Flynn said. “This has led me to do more experimenting with biologicals, and I think, in some cases, we’ve seen some positive results.”
The Montana haymaker uses Roundup Ready alfalfa when seeding a new field. Like the pure orchardgrass fields, alfalfa is typically harvested three times per year. Timothy only yields one or two good cuttings. “We start looking for a cutting window around June 1, but that didn’t happen in 2023,” Flynn lamented. “Our first cutting was closer to July 1 because of an unusually wet June.”
Alfalfa fields are harvested for four or five years, then they are interseeded with orchardgrass in the spring. “This allows us to get another three to four years from those stands and supplies us with some alfalfa-grass hay,” Flynn said. “Once the field is terminated, we’ll usually leave it out of alfalfa for three years, using wheat or sometimes potatoes as a rotation crop.”
Fields are cut with a Case IH 16-foot disc mower that gets traded every two to three years. “That’s one piece of equipment that we like to keep fresh,” Flynn noted. The farm runs three Vermeer basket rakes and one Twin Star basket rake. A Krone tedder is used on grass fields.
“For alfalfa, whatever is raked during the morning is usually baled that night, generally between 10 p.m. and 2 a.m., depending on the time of year,” Flynn said. “Grass fields get baled during the day.”
The farm runs six in-line Massey Ferguson small square balers, three 3x3 balers, three 3x4 balers, and one 4x4 baler, which is typically only used on outside rounds where there has been grass or weed encroachment. “We moved from 4x4 bales to 3x4s a few years ago because we can get more tonnage on the trucks for shipping out of state,” Flynn explained.
For the big square bales, Flynn hires a custom service using Stinger units to pick up and move bales from the field to storage. Small square bales are stacked and moved with three New Holland bale wagons belonging to the farm.
“Lately, hay storage has been a bit of challenge,” Flynn explained. “We lost five big hay sheds that we leased but were recently sold by the owner. We currently have three other open-sided hay sheds of our own that we use and are temporarily storing hay in our machine shed. Once those facilities get full, we’ll have to tarp the remaining production, although it won’t all get a full wrap.”
Most of Flynn’s 120-pound small square bales and 3x3 bales get shipped to Kentucky’s equine market. The farm’s 3x4 bales are targeted for the beef market as feeder hay in Montana and other Western states. As is the case with many hay producers, Flynn and Shearer also co-own a 120-cow beef herd, and that’s where most of their lower quality 4x4 production gets fed.
Flynn said they truck hay themselves that stays in Montana. Out-of-state shipments, which comprise most of their production, are trucked by a third party. “Our Kentucky horse market has been pretty stable both in terms of volume and price,” Flynn noted. “Horse customers rarely request a forage test. They just want green,” he chuckled.
In contrast, Flynn does test his alfalfa hay that is targeted to dairies in Washington state. “They usually take an early first cutting or our third cutting, which is often our highest quality hay,” he said.
As all hay producers are aware, the hay market was significantly down in 2023 compared to 2022. “It wouldn’t be so bad if our input costs had dropped accordingly, but they didn’t,” Flynn bemoaned. “I guess that’s just part of being a hay producer. Markets are going to fluctuate, and you have to adjust. Even though we’re pretty far north, our challenges aren’t much different than everybody else’s. We all struggle with weather, labor, and high input costs. I’d say we have fewer insect pest problems than those farther south,” he added.
As for the future, Flynn hopes the farm’s viability will continue with the same kind of metaphorical length characterized by the neighboring Missouri River, and that one or more of his children will show an interest in the business. Already, his 17-year-old son has proven to be a big help on the operation and is leaning toward a farming career. It sounds like another generational farming headwater has been formed. •
Increase tonnage without sacrificing quality with Rhyzogreen, “The Soil Stimulant That Pays For Itself.”
20-30% avg. increase in tonnage (across 45+ on-farm trials)
62% avg. increase in soil microbial biomass (across 236 on-farm trials)
13% avg. increase in crude protein (across 21 on-farm trials)
“It was a 22% increase in tonnage... I don’t know very many products or business models that generate a 4:1 return... You can make money doin' that.”
- boone huffman, nebraska
Rhyzogreen is a liquid blend of superfoods that stimulates & feeds the native soil microbes. It awakens dormant microbes that serve to unlock the nutrients that are “tied up” in the soil and make them available to the plant.
by Amber Friedrichsen, Associate Editor
TECHNOLOGY is evolving faster than ever before, and farming technology is no exception. Automated equipment that has become a mainstay on both large and small operations demonstrates just how quickly everyday tasks can be simplified with innovative solutions.
For hay producers, one of these tasks is bale monitoring. The heat generated from hay respiration combined with elevated moisture levels and exposure to oxygen creates the ideal environment for bacteria in bales to thrive — and multiply. As more and more microorganisms respire, bales generate additional heat and hay temperatures rise. Most microorganisms die when bales reach 130°F to 140°F, and then bale temperatures fall as bacteria populations decline. This heating cycle can occur for weeks after harvest without posing a major fire threat if there is adequate airflow between bales. What is cause for concern, though, is when thermophilic bacteria are present in hay. These heat-loving species incite a second heating phase, exacerbating the risk of fire.
According to the National Ag Safety Database, thermophilic bacteria can outlast temperatures up to 170°F, which is when hay fires are imminent and spontaneous combustion becomes a concern. Although it is recommended to regularly check hay temperatures using bale thermometers and manual probes, many of these tools do not provide continuous monitoring.
Haytech hay probes automatically track bale temperatures around the clock and alert farmers when hay gets too hot. The wireless plug-and-play system developed by the global tech company Quanturi includes 16-inch probes that are inserted into small square bales and relay hay temperature to a repeater installed inside a barn.
The repeater amplifies this information to a base station that sends hay temperature data to the cloud, making it accessible on the Quanturi app.
When farmers open the Quanturi app, they have an overview of the Haytech probes installed in their bales, whether they are contained in a single barn or stored across several locations. Data from individual probes are displayed on graphs that show hay heating over time so users can assess the rate at which hay temperatures are climbing.
In addition to collecting and visualizing data, Haytech alerts farmers when bale temperatures hit a predetermined threshold. Users can customize their alert settings and notification preferences based on their risk tolerance, and they can edit the display name of individual probes to make it easier to locate a specific lot of hay in an emergency.
Aside from fires, a more common outcome of hay heating is forage quality loss. Excess heat and moisture encour-
age mold growth, which depletes energy stored in plant tissues. Anaerobic conditions can also alter protein structure in hot hay, resulting in a caramelized product that, despite being more palatable to livestock, has little nutritional value.
Haytech addresses these issues with its Feed Value Indicator. This app feature estimates the decline in forage quality based on the rate of rising hay temperatures, adding another layer of data to the bale monitoring system. The Feed Value Indicator does not directly measure forage quality, but it can help farmers make decisions about storing and feeding bales that may have experienced heat damage.
Insurance companies are the poster children for risk management, includ-
ing the risk of hay fires. That is why Nationwide forged a partnership with Quanturi after Vicente Rico, senior risk management consultant, learned about the hay probes. Promoting the bale monitoring system to producer customers and incentivizing its use with preferred pricing expedites the adoption of new approaches to preventative action.
“It’s all about mitigating risk at the end of the day,” said Rico, who understands the threat of farm fires growing up on a dairy in the drylands of West Texas. “If we can put technology into the hands of our customers to see that there are ways to automate old processes, it will help them enhance their operations.”
Laramie Sandquist, farm-agribusiness risk management leader for Nationwide, said using the hay probes is like adding a tool to the toolbox to lower the odds of on-farm disruptions. He believes the company’s partnership with Quanturi strengthens the message of safer hay management across all aspects of an operation and the agricultural industry at large.
Rico and Sandquist acknowledged some customers are skeptical of sharing farm information with the tech company when they use the bale monitoring software. Even so, most of the feedback they have received from those who go all in on the equipment is overwhelmingly positive. Not only has the Finnish company put down roots in the western United States to reduce the number of time zones between customer service calls, but the developers of Haytech are eager to visit farms to troubleshoot set-up issues and establish personal relationships with their clients.
“The way to get producers to fully commit and understand what the technology can do for their operation is to have boots on the ground at the haystack, putting in the probes, and installing the repeaters themselves,” Rico said.
On the dialing end of many of these customer service calls has been Jeffrey Bushnell, who manages White Mountain Ranch in Dyer, Nev. He started using Haytech probes to prevent fire emergencies on the 3,000-acre commercial hay operation but also to justify an asking price for the high-quality alfalfa he sells to a large dairy. Nearly all of the hay he makes goes to a single customer, so maintaining a consistent product is essential.
“If moisture isn’t where buyers want it, they can ding you on price because they don’t feel comfortable storing it in their barn, and it can create a hassle for them to try and feed it right away,” Bushnell explained. “If our buyer is concerned about hay moisture in a certain stack, I can put the probes in to monitor bales on an hourly basis and show them that there is no issue at all.”
Bushnell said the Haytech system alerts him when a particular stack surpasses what he has set as his safe maximum temperature. When this happens, he separates bales for better airflow, allowing for more heat regulation.
“Roughly a week after hay is baled, it stops sweating and moisture dissipates naturally. Hay temperature should correlate with this process, peak, and then drop,” he said. “If the temperature doesn’t drop, or worse, it keeps climbing, the probes will tell you that.”
Since Haytech probes were designed for small square bales, Bushnell has gotten creative to make the system work with large square ones. He built a solar-powered base station that can sit outside in his stackyards as opposed to being mounted
inside a barn, and he has been experimenting with how to position probes in his bales for the most accurate readings. For example, at 16 inches long, the probes can almost extend the width of a small square bale, but they only penetrate a portion of a large square one.
This obstacle was evident during the 2023 growing season when unusually wet weather drove ambient moisture to unprecedented levels in Nevada, the driest state in the country. Bushnell said his bales wicked excess moisture from the air and soaked up rainwater from the ground, causing bale cores to be much wetter and hotter than normal. Unfortunately, his hay probes didn’t reach deep enough into the side of the bales they were inserted to account for the difference.
Instead of letting this discourage further use of Haytech, Bushnell has been working with Quanturi to identify best practices for the hay probes in large square bales. He hopes his on-farm research will guide recommendations and inform product development to ensure hay producers of all bale shapes and sizes can benefit from the technology and mitigate fire and other financial risks on their farms.
“We are still figuring out what location on the bale works best to be able to track peak temperature in a large square bale versus a small square,” Bushnell asserted. “The technology is fully developed, and the user interface of the software is phenomenal. Trying to utilize the hay probes to be as efficient as possible for large square bale farmers is what we are focusing on now.” •
by Haley Ruffner
LTHOUGH the USDA has Hay Quality Designation Guidelines (see tables) based on nutrition tests for alfalfa, that alone does not cover all of the terms and grades we use to describe hay. Many of the terms we use are subjective since not everyone follows the USDA chart, or if they do, it may not be comprehensive enough to fully determine quality. For example, “premium” hay means something different to a dairyman in Texas than it does to a feed store manager in Florida.
A customer asking for “good” hay may be referring to hay with a relative feed value (RFV) of 160, or they may be simply asking for mold-free hay that is safe to feed their animals. Asking questions to determine what kind of animals they have, if they have specific nutritional requirements, and what their quality expectations are will provide better insight and let them describe in their own words the grade of hay they are looking for. Brokers dealing with more than one type of customer should be able to describe hay in concrete, specific terms in addition to those the USDA provides.
For dairy and feedlot customers who are mixing a ration, a forage nutrient test may be the deciding factor in determining value of a hay lot. If hay is ground or put through a total mixed ration (TMR) mixer, secondary characteristics like bleaching, stack damage, small amounts of mold, and stem size are largely irrelevant. While these factors still impact the overall quality of hay and are necessary information for customers to have, they may not carry as much weight for dairy and feedlot customers who are buying primarily based on a test.
Feed store and horse customers, on the other hand, may not consider a forage nutrient test at all when purchasing hay. Unless they are feeding horses with specific dietary requirements or metabolic issues, they are more concerned with the overall aesthetics of the hay and want good color, smell, and palatability more so than a specific nutritional profile. Although these customers may not ask for a test, it still provides necessary information for a broker to have in being able to accurately grade hay. Coastal bermudagrass hay, for example, can be high in neutral detergent fiber (NDF), causing it to be indigestible to horses and lead to colic.
Alfalfa that tests high in protein and RFV may be too rich for horses accustomed to lower testing hay and can also cause health issues if they are not transitioned slowly. Part of the value a hay broker provides to customers is the ability to educate and anticipate problems before they arise, so being able to decipher a forage test analysis and accurately share what that means for a customer’s animals is integral.
Hay sellers must consider storage when grading hay as it will impact the quality over the weeks and months after baling. Hay stored outside with no tarps will begin degrading almost immediately, being impacted by sun bleaching, rain or snow, and shrink from wind and exposure to elements. Hay that is graded as “supreme” quality in the field upon baling but not stored
Good 9 to 13
Fair 5 to 9 Utility
correctly will not retain that same grade for long, even if it takes one rain shower before being tarped. The resulting bleached color and moisture will impact the price and caliber of customer it can be delivered to.
If farmers are unwilling or unable to store hay and prefer to sell out of the field, their options become limited to more local shipments due to the dangers of shipping uncured hay. Shipping out of the field is not an effective way to bypass setting up storage because new hay needs adequate space and airflow to allow it to heat and cure. Fresh hay loaded on a dry van and shipped across the country is liable to heat and mildew, arriving to the customer with significant damage. Likewise, fresh hay that survives shipping but is packed into a customer’s barn upon delivery also poses a risk of fire if all parties are not diligent about monitoring moisture levels.
Considerations of storage are almost as important as looking at the quality of the hay itself upon baling, especially for customers using large quantities of hay over longer stretches of time. A stack of hay that will ship over the course of sev-
eral months, especially if it’s stored outside in a region that gets significant precipitation, will degrade substantially over time.
Our senses can help us grade hay — the color, smell, texture, and other visible and tactile qualities play a part in determining its quality. Horse customers, in particular, are usually much more concerned with the look of the hay over its nutrient analysis. Does the hay smell musty or fresh? Is it bright green, or has it been sun bleached? Does it feel coarse to the touch, or is it soft and leafy?
Taking a close look at the hay for different grasses and legumes will give a clear idea of its contents in terms of how “pure” it is or the mix of plants it contains. A visual examination to look for weeds, rocks, or trash that may have been baled up is important in being able to accurately describe the hay’s quality to potential customers.
Hay that tests well, is barn stored, has good color and softness, but contains foxtail on visual examination must be graded as such and disqualified for sale as horse hay. Although a nutrient test used in conjunction with physically looking at the hay offers a more well-rounded picture of its true grade, we can get a lot of information from a stack’s sensory qualities.
Visual analysis of a haystack can be effective in validating nutrient test results or giving a preliminary idea as to what the test’s results may be before the lab sends them back. For example, alfalfa with good color and excellent leaf retention that doesn’t shatter when pulling a handful of hay from the bale will likely test higher than alfalfa that appears bleached and falls to dust and stems when opened. Grass hay that appears stemmy and is more mature will be less palatable and lower in nutrients for horses than softer, finer-stemmed hay that was cut earlier.
Consistency within a batch of hay is largely a matter of attention to detail by the farmer across all stages of the growing, cutting, and storage processes. How clean do the fields look before they are cut? Are there weeds or trash visible, or does the hay appear to be uniform? How old are the stands of hay, and does the farmer sort or grade old stands separately from newer stands?
Hay that is consistent prior to being cut must also be baled in similar conditions, either by way of using a steamer to imitate ideal dew conditions or through careful timing by the farmer putting the hay up. Is it one farmer putting up hundreds of acres alone, or is there a crew that comes in to make sure fields are all baled at the optimum moisture level? Conditions can vary drastically even in fields that are close together, so talking to farmers about their baling practices will give insight into the level of consistency to expect in the finished product. Consistency in storage will also determine the hay’s grade over a period of time. If one stack of hay is stored in a barn with no sides and another stack is in a fully enclosed barn, the outside bales in the open barn will degrade much more than those in the four-sided barn. A batch of hay that tested within the USDA-described “premium” range upon baling but was stored with some stacks tarped and some untarped will no longer be the same quality by the following spring, especially if it comes from a region that gets significant rain or
snow over the winter. The untarped stacks will have experienced enough stack damage that at least the top bales will have to be sold as a different grade of hay.
While not all customers are overly concerned with the minute details of hay across a large batch as long as variations fall within one grade (for example, a certain range of RFV), some will expect to know if stem size will be slightly larger from one load to the next.
Even for less particular cattle or feedlot customers, consistency in bale weights is key to ensure that the value is the same across a series of loads. If there is variation in a product, being able to set that expectation with customers and building allowance for it into pricing will go a long way in providing accurate grading and quality assurance to customers. Having the conversation about growing, baling, and storage practices with farmers will give a clear picture on the level of attention to detail and consistency to expect across a batch of hay.
Different types of customers will have different priorities in grading hay, so the ability to accurately describe a lot of hay in terms of its nutrient analysis, storage, physical qualities, and level of consistency will mitigate potential misunderstandings. Developing a clear line of communication with a customer in order to understand what their needs are is just as important as grading the hay itself. Matching a batch of hay to the right customer is equally a measure of having a clear picture of what a customer is asking for and being able to accurately evaluate and describe the product. •
• Models for skid steers, tractor front loaders and select telehandlers.
• Pick-up two 4’ x 4’ x 8’ or three 3’ x 3’ x 8’ rectangular bales.
• Features five bolt-in spears with useable length of 40.5” and four upper balance spears.
by Chris Wacek-Driver
LFALFA has been termed the “Queen of Forages.” Unfortunately, her highness is a fickle ruler. Harvesting her wares and maintaining optimal quality requires precise attention from her subjects. Ignore her requirement for a correct and uniform moisture at harvest and the likelihood of a clostridial fermentation is high, which results in the spewing out of butyric acid, biogenic amines, and putrid odors.
The queen’s ideal moisture requirement often converges with Mother Nature’s tendency to be a bit cranky heading into harvest time. Additionally, the two ladies’ obstinate natures seem to coincide when nutrient parameters are optimal. In the heat of the moment, it may seem easier to risk the queen’s wrath and the possibility of a poor fermentation. However, optimal nutrient parameters and digestibility coupled with an undesirable fermentation still equals poor forage quality and disappointing animal performance.
Clostridial spores require two conditions to grow and thrive in alfalfa: high moisture and high pH. While high moisture is implicated as the culprit
for clostridial fermentations, these fermentations ultimately occur due to a lack of sugar and the failure to reach an effectively low pH endpoint. Table 1 shows both typical sugar contents of different forage crops and the amount of sugar these crops require at different moistures to reach a pH endpoint. The numbers in bold indicate when enough sugar should be present to attain adequate fermentation.
For alfalfa, note that when the dry matter is below 35%, or moisture is above 65%, there is simply not enough sugar to reach a desirable pH endpoint. Keep in mind that the table is indicative of ideal conditions. Situations where valuable sugar is lost before the crop is ensiled, such as rained on forage (either in the field or pile), delayed fill, or prolonged wilting time, will lower the actual moisture concentration when clostridial activity occurs.
The addition of large numbers of undesirable microbes can overwhelm the fermentation and include such events as manure application on the growing crop or excessive soil contamination. Another complicating factor pertaining to bunkers and piles is they often remain open during harvest until physically covered and sealed with plastic and tires, exacerbating the problem. This contrasts with bagging
or upright silos where some sealing occurs during fill.
Systems, particularly those involving biology, are complicated. A key outcome has emerged on farms that are successful versus those that struggle with desirable alfalfa fermentations. The successful farms have a designated person to monitor moisture. This individual must be dedicated to determining the moisture concentration of the fresh crop and serve as the point person on swath merging and chopping decisions. Often this individual is the herd manager or farm owner because they are most affected by mediocre quality forage and the resulting subpar animal performance.
The order fields are cut is not necessarily the order fields should be merged or harvested due to field moisture differences. Merging often slows or stops the forage drying rate. Below is a protocol that offers the key steps needed to help ensure optimal forage quality and animal performance are achieved.
1. Designate one person to be responsible for determining forage moistures and the field order of merging and harvesting. This person is also responsible for monitoring the incoming truckloads of forage to ensure target moisture concentra-
tions are being met.
2. Cut mowed alfalfa into small pieces and dry it to determine moisture with a Koester tester or equivalent.
3. Order fields for harvesting with a focus on potentially higher moisture spots. Think heavier alfalfa growth, shaded areas, low spots, and pure alfalfa stands.
4. The ideal harvest moisture is between 53% and 63%. At these levels, commence merging to slow or stop further moisture loss.
Make it a priority
A second protocol is needed when alfalfa moisture is above the ideal range but harvest needs to commence. In such situations, implement these steps:
1. Use a proven anti-clostridial inoculant.
2. If a lfalfa is above 65% moisture, a separate pile is advisable. Do not mix excessively wet forage with ideal forage.
3. Fill the pile quickly and pack well.
4. Cover and seal immediately. Sealing needs to happen the day of harvest to conserve sugar content.
5. Al low alfalfa to ferment for two weeks prior to opening.
6. Feed as soon as possible, ideally within two months.
7. Keep the feedout rate as high as possible. Ideally, a foot or more.
In general, if these steps are implemented and the situation isn’t extreme, wet forage can be fed before it turns clostridial. A key part of the above system is to cover and seal the forage immediately to conserve valuable sugar for acid production and encourage a drop in pH. Not sealing and letting the forage properly ferment is akin to piling green chop on the ground and hoping for the best. It will spoil and turn into compost.
Even with careful implementation of the rescue protocol there is risk of fermentation failure. Heavily rained on crops, hay that is already merged and rained on, excessive field drying time, and forage laid in heavy, narrow windrows all contribute to sugar loss. Another notable exception is alfalfa that has excessive soil or manure contamination, which can overwhelm the forage with clostridial organisms. Manure applications on alfalfa are often cited as a necessity on farms. If manure needs to be applied to growing alfalfa, research suggests applying it immediately after harvest — prior to
*Typical sugar content at harvest (% DM): Alfalfa 4 to 15, Grass 10 to 20, and Corn 8 to 30 Bold type indicates ranges in which typical sugar levels are sufficient for maximum pH reduction. Leibensperger and Pitt, Journal of Dairy Science, Vol. 71:1220.
any green-up — to reduce clostridial fermentation risk on the subsequent crop. Appeasing royalty can be difficult. A multitude of biological factors that defy control add to the hardship. However, strategic planning, proper decision making, and careful implementation of protocols prior to and during the harvest can significantly enhance the odds of success. •
The author owns and operates a forage consulting business, Forage Innovations LLC, in Bay City, Wis.
by Amber Friedrichsen, Associate Editor
POCKET gophers have a face only a mother could love and a reputation for causing serious production losses. The rodents really have no redeeming qualities unless they are caught in a gopher trap or taking the bait in a rodenticide probe.
Although they can be pocket-sized, pocket gophers are actually named for the fur-lined pouches on the outside of either side of their mouths that they use to carry food. The rodents can range in color from brown to black to white and measure 5 to 14 inches long. Despite being relatively small, pocket gophers can cause significant issues in alfalfa fields and irrigation systems — especially in the western U.S.
Pocket gophers readily feed on alfalfa roots as they tunnel through the soil profile, and their burrows can make it diffi-
numbers when it comes to digging, tunneling, and chewing through irrigation lines and utility wires.
At the 2023 Western Alfalfa & Forage Symposium in Sparks, Nev., Mark Nelson with Utah State University compared several methods and machinery for pocket gopher control. The Beaver County extension agent explained how different approaches vary in cost, efficiency, and safety while sharing some research results and anecdotes.
Rodenticide baits. Nelson said strychnine is a common type of pocket gopher bait that is exclusively used belowground. This product is lethal to pests in a single dosage and can be an effective form of control if it is strategically placed in a primary burrow.
Anticoagulant bait is less toxic than strychnine bait, which may be desirable if livestock, pets, or other wildlife are subject to consuming rodenticide. However, this means anticoagulant bait can be less effective, and two doses are typically required to kill pocket gophers. After one bad experience, Nelson said pests can develop a “bait shyness” and learn to avoid it.
“In most cases, [pocket gophers] have to eat it twice,” he said about anticoagulant bait. “If you eat something bad one day for lunch, are you going to eat it again the next day? Probably not.”
Nelson noted rodenticide bait can also be deadly to predator species — like hawks and eagles — that prey on pocket gophers that have consumed toxic products. Other methods like fumigation, combustion, and trapping are contained underground and pose less of a threat to other animals, although these forms of control still require serious precautions.
Fumigation. Aluminum phosphide and carbon monoxide are two common fumigation gases. The former comes in a tablet form and reacts with moisture in the ground to produce a toxic phosphine gas. Nelson recommended waiting until it has rained or snowed to fumigate with aluminum phosphide.
Aluminum phosphide is a restricted-use product and requires the operator to have a pesticide applicator license. The lethal gas is toxic to all mammals and can be detrimental to human safety; however, the Gopher General is a relatively new machine that is designed to mitigate these risks and eliminate contact with aluminum phosphide.
“What [the Gopher General] does is distribute aluminum phosphide tablets belowground, and the fumigant gas stays belowground. It spreads throughout the tunnels and moves throughout the soil,” Nelson explained. “The nice thing about it is you never have to touch the tablets.”
Carbon monoxide fumigation can be carried out with a pressurized exhaust rodent controller, also known as a PERC machine. It works by capturing carbon monoxide from a gas engine and driving it into a compressor where it is cooled, pressurized, and injected into a pocket gopher burrow. Nelson pointed out that soil moisture is less of a factor for carbon monoxide fumigation compared to aluminum phosphide.
Combustion. Controlling pocket gophers via combustion
involves forcing propane and oxygen into burrows and igniting the gases. The explosion kills pests and collapses their tunnel systems in one fell swoop, and a contraption called the Rodenator is specifically designed for this type of combustion.
“This is one of those products that has a question mark as to how effective it is, but I will tell you one thing, it is a stress reliever,” Nelson chuckled. “But you have to be careful. Make sure you follow the label instructions.”
Trapping. Nelson stated this method is more of an art than a science as farmers must dig up pocket gopher burrows, locate the openings to underground tunnels, and set a trap in each hole. Even so, it may be safer — and more reassuring — to trap pocket gophers than to handle lethal fumigation gases or initiate a combustion reaction.
“The nice thing about trapping is you know you’ve killed that gopher,” Nelson asserted. “When you put out the bait, or you put out the gas, you hope you’ve killed it, but you can’t be sure. When you’ve actually got that gopher in your hand, then you know.”
In 2023, Nelson was a part of a study that compared different control methods in fields with significant pocket gopher pressure across eight Utah counties. Each site included three plots: one to test strychnine bait, one to test Gophinator traps, and one to serve as a control.
Researchers used applicator probes to insert strychnine bait in the ground, and Gophinator traps were placed inside both tunnel holes within each pocket gopher burrow. These traps were
checked three times a week for four weeks, and if a trap was sprung upon checking, it was reset.
After four weeks, data showed the trapping plots had the lowest number of new pocket gopher mounds compared to the strychnine bait plots and the control plots. With that said, Nelson pointed out that setting traps was the most time-consuming method and demanded more labor than the other treatments.
“The take home message is, if you have pocket gopher problems on small acreages or in your yard, trapping is something you should consider,” he concluded. “If you have a lot of acres to treat, you may want to look into baiting or fumigating.”
Farmers and ranchers aren’t the only ones who find satisfaction in getting revenge on a rodent that once ravaged their alfalfa fields. This became apparent through the Gopher Abatement Project, in which Nelson recruited youth in Beaver County to learn how to set pocket gopher traps and incentivized their trapping activities.
Last year, 65 children and parents attended two inaugural Gopher Abatement Project Trapping Workshops. Most participants had never set a gopher trap before, but after practicing at the training, each student left with five gopher traps a piece.
Over the next few months, kids earned $3 for every pocket gopher, ground squirrel, and rock chuck tail they returned to the country extension office. Those looking for a greater challenge acquired foot traps to catch raccoons, for which the going price was $5 per tail. The project was funded by local conservation districts, and from early March through mid-October, participants trapped more than 575 pocket gophers. Total payouts exceeded $3,700.
“The kids were happy to do it. It’s what I would call a win-win project,” Nelson said. “Not only did we trap 1,155 rodents, but we gave the kids an opportunity to do something besides play on their phones or watch TV all day.” •
On the Market since 1979 (and still unbeatable)
We are a non-GMO seed house! Never a positive hit for GMO
Never a Report of Winter Kill
Greenway Alfalfa
This Alfalfa has been called a tetraploid anomaly by alfalfa breeders. On the market since 1979, and being improved twice, It remains the highest yielding, low water alfalfa on the market!
HERE’S WHAT GROWERS ARE SAYING: (More testimonials available on our website)
When Planting Dryland Alfalfa always use coated seed! (Let us prove it!)
"We run out of water often times by June 1, but the 360-D yielded 6-3/4 tons! We’ve ordered another ton of 360-D"
Jordan Dillon - Rivers Edge Dairy - Hesperus, CO
“In our extremely tough and pure dryland conditions, 360-D has become our only ‘fall-back-mainstay’ variety.”
Max Wilson - Camas Prairie (elev 5060ft) - Fairfiled, ID
"360-D yielded 7 ton under a pivot that only pumped 375 gal./min."
Everett Messner - Salmon Track - Hollister, ID
“We planted 360-D in an irrigated pivot that was very short on water. Side by side was a pivot with normal water. The 360-D yielded with the well irrigated adjacent field! No difference in yield!
Ryan Telford - Richfield, ID
Alan Greenway Seedsman
Over 50 Years Experience
Greenway Seeds Caldwell, ID
Alan Greenway
208-250-0159 (cell) 208-454-8342 (message)
√ Will produce AT LEAST 80% of crop with 50% of water
√ Will produce a subsequent cutting after water is gone
√ Plant on dryland/ guaranteed to out yield Ranger or Ladak
*
√ Plant under pivots that only pump 400 gal/
√ Plant on elds that have only early season creek water
√ Plant under end guns on pivots
√ Plant in the late fall with your dormant seeded grasses
*Plant in your pivot corners. Two ton bonus per acre per year.
“Modern Forages Sold Nationwide and Canada”
by Mike Rankin, Managing Editor
T’S often difficult to sort out circumstance, coincidence, and luck. But, along with a heaping helping of hard work and good judgment, these three uncontrollable factors usually play a role in success. That’s certainly the case for John Strieter and his older brother, Mike, who operate Strieter Hay Farms in Michigan’s Thumb Region.
The farm sits less than 2 miles from Lake Huron’s Saginaw Bay that forms the western Thumb’s shoreline. It’s not a location where you would anticipate finding a commercial hay farm. The landscape is mostly characterized by row crops and large dairy farms that prefer their forage out of a bunker or pile.
It was circumstance that the brothers set down roots here. This was where their grandparents had a small farm
that they worked on in their younger years and would eventually inherit. The brothers’ father had to quit farming because of health concerns.
“As kids, we only baled a little straw,” John recalled. “I started baling some hay in high school on grandma’s farm in the mid-1990s, then slowly started adding hay ground and renting land from neighbors. We really didn’t ramp up the hay business until about 2006 when Mike, who by
that time was married and employed elsewhere, came back to the farm to help me, and we bought our first big square baler.”
In those early years, most of the baling was for wheat straw, which was plentiful in the region. Over time, John started making new connections for selling hay, and that business grew.
“Early on, we were putting up a lot of small square bales and trying everything possible not to have to purchase a hay press, including pulling two balers at a time with double hitches. We had five small square balers back then. Still, we could only do 100 acres a day with those little balers but did 300 acres a day with our big square balers.
At one point, we ramped up to doing 5,000 acres of just straw. Of course, we only had about 250 acres of hay at that time,” he added.
In addition to their own farm, John and Mike had been asked by another much older brother pair to help them with their crop farm when available. The Strieters accepted the offer and had helped out for seven years when that duo decided to retire in 2015 and offered John the first chance at renting their over 2,000-acre farm and an opportunity to purchase their farm equipment on contract, which John was able to work out with his banker. Circumstance, coincidence, or luck — take your pick.
“Once we got established with small square balers and bought a new stack wagon to add to our others, we still couldn’t get enough done, especially with the added acreage,” John said. “I saw a Steffen bale press out in Oregon and basically determined that we could have one of those for the cost of our small square bale equipment. We already had two 3x4 big square balers for straw and rained on hay and soon added a third baler. The hay press gave us a small bale marketing option without actually needing to use small
square balers,” he further explained.
“Having the high-density big balers and the press increased our capability to add more acres,” John noted. “We also started doing some baleage, but
the market wasn’t that great for us. That’s when we started thinking about adding hay dryers.”
In 2018, Strieter Hay Farms installed their first two Chinook hay dryers. Four years later, an Agri Green dryer was added, and soon later, a bale cooling bed was installed. About 20% to 30% of the hay goes through the dryers, depending on the year.
“Both the press and the dryers offer us more flexibility from a production
and marketing standpoint,” John said. “We can move product as big squares or small squares depending on market dynamics.”
These days, Strieter Hay Farms consists of 5,000 acres, most of which are leased. There are 1,800 acres of hay, and they bale 7,000 to 8,000 acres of wheat straw each year. The farm also grows corn, soybeans, winter wheat, and sugarbeets. John heads up the business end of Strieter Hay Farms, while Mike is an accomplished machinery mechanic.
The farm’s hay acres consist of an equal number of pure alfalfa and alfalfa-orchardgrass mixtures. Occasionally, some timothy is grown. “Because there’s not a lot of dry hay made in the area, I feel this gives us a competitive advantage when leasing land because we can offer a perennial forage in the crop rotation, which is something a lot of landowners find appealing,” John surmised. “We also feel our hay crops enhance our row-crop yields, but the hay ground remains our most profitable acreage.”
Alfalfa seedings are done both in the spring and late summer. When
Large square bales are picked up, stacked, and then loaded on trucks in the field. Each truckload goes across the Strieter’s on-farm scale so that yields can be determined.
spring seeded, the new stands usually follow sugarbeets from the year before. Late-summer seedings are made after winter wheat is harvested. Both are done into a conventional, tilled seedbed using 15 to 20 pounds per acre of coated Roundup Readytraited seed. Fields that are mixed alfalfa-grass are seeded with straight alfalfa and then sprayed with glyphosate in the seedling stage. It’s then that the orchardgrass is interseeded. The Strieters are able to get three to four cuttings per year on established stands, with first-crop cutting generally beginning toward the end of May. Alfalfa stands are kept in production for four to six years, and average annual alfalfa yields across the farm
range from 4.5 to 5 dry matter tons per acre.
Hay is cut and laid into 9-foot swaths with two Pöttinger triple mowers equipped with Circle C conditioning rolls. To enhance field drying, they use a hay fluffer/tedder designed and built by fellow Ohio haymaker John Russell. Windrows are formed with three Circle C wheel rakes with the center dividers. In lighter cuttings, two Oxbo mergers are used to further enlarge windrows and ensure the balers are running at full capacity to maintain flake count and minimize leaf loss.
“All of our tractors are set up to straddle the swath,” John said. “We
never drive on cut hay and actually end up driving in the same tracks with the mower, fluffer, rake, and baler. I think we gain yield by doing that,” he added.
The Strieters’ three Massey Ferguson high-density 3x4 balers are equipped with preservative applicators, Gazeka moisture monitors, Bale Skis, and PhiBer bale accumulators. Mike explained that they like to target a 45-flake count for each bale, which has been made easier with the continuously variable transmissions (CVT) on their tractors.
Bales are picked up out of the field with Pro Ag pull-type stack wagons and stacked at the field’s edge where they are loaded on a truck with a telehandler. An on-farm drive-over scale is used to weigh everything that is baled. John tracks the production from every field of hay and straw. This offers an accurate means of determining his own yields, but it also enables him to pay landowners by the ton for windrowed straw that he purchases in the field. For many years, the Strieters would need to tarp some of their hay and straw, but with the recent addition of a few new sheds, all of the hay is now stored under a roof.
The bulk of the Strieters’ hay customers are either local dairy farms or horse operations in the eastern U.S. John explained that most of their equine and retail store hay is moved through a broker, but he has more direct involvement with his dairy hay and straw clients. A lot of the straw sold to dairies is included in total mixed rations. Over the years, John said they’ve been
able to build and develop a consistent customer base, as most successful hay producers do.
As for now, John has no immediate intentions of growing the operation much larger. They currently have six full-time employees and numerous part-time seasonal workers. Like many hay farms, weather and the availability of good labor remain their biggest challenges. John and his wife, Amanda, have two young boys, and Mike and his wife, Lesley, also have two children with his oldest son, Lane, already helping out on the farm.
John currently serves on the board of directors of the National Hay Association (NHA). He will become president of that organization later this year. A strong proponent of the NHA, John said, “I’ve really gotten a lot of return from my participation in the National Hay Association. It seems like every year I attend the meetings I’m able to make money by forging a new client connection or hearing about a new product or practice that I can use.”
focus on efficient field drying and baling, coupled with artificial hay drying when needed, has enabled them to offer a quality product that can meet or exceed any customer’s needs. •
by Brian Luck
WHEN it’s time to harvest alfalfa for silage or hay, we are usually concerned about getting the crop cut at the right time, hitting weather windows for good drying conditions, and removing the crop from the field while maintaining the correct moisture and quality. How often do we give any thought to the machines we use in terms of tire pressures, ground pressure from machinery tires on plant regrowth, and machinery traffic patterns in the field during harvest?
Research at the University of Wisconsin-Madison suggests that these considerations are also important to alfalfa yields and stand persistence. Ensuring we minimize damage to alfalfa stands during harvest will protect yield over time, extend stand life, and boost profit margins.
Ideally, when harvesting alfalfa, we would use the lightest machines possible. All of these machines would be fitted with radial agricultural tires capable of being operated at low tire pressures, and these machines would only be in the field when soil conditions were optimal for minimizing damage to alfalfa crowns without causing soil compaction. Unfortunately, farming doesn’t work that way. Often, an efficient harvest is required as opposed to operating in ideal weather and soil conditions.
Most machinery associated with alfalfa harvest use agricultural tires and are required for their specific operations. However, some of the greatest
offenders to ground pressure applications are the machines used to transport the harvested crop from the field to the storage site. This is true for both alfalfa silage and hay production where trucks designed for on-road travel are used to haul the silage or hay and are driven in the field to collect the harvested crop.
In the case of silage harvest, our research showed that on-road trucks, specifically semi tractor-trailers, were the most efficient method for transporting silage from the field to the storage site. These machines have reasonable in-field speed, high carrying capacity, and high on-road speed that makes the transport of silage from the field to the storage site most efficient. In the same study, straight-framed trucks and tractor-towed carts were less efficient than semitrucks and trailers but were not statistically different from each other. This indicates that some level of transport and harvest efficiency can be maintained by utilizing machines equipped with agricultural tires compared to on-road tires.
Parker Williams at the University of Wisconsin-Madison surveyed multiple machines associated with alfalfa harvest and tabulated the average weight and associated ground pressure applied by these machines. This work revealed that machines involved in alfalfa harvest equipped with agricultural tires apply ground pressures ranging between 100 to 220 pounds per square inch (psi), while machines equipped with on-road tires apply ground pressures ranging between 520 to 820 psi. This increase in ground pressures applied by these on-road tires has great potential for lasting damage
to the alfalfa crop. Whenever possible, try to utilize agricultural or floatation tires in alfalfa fields. These tires provide a wider and longer ground contact area that distributes the weight of the machine over that larger area, having less impact on the growing crop.
Tire pressure also plays an important role in reducing damage to growing alfalfa plants. Williams calculated an average jump in ground pressure of 7.2 psi for every 1 psi of tire inflation pressure for agricultural tires. This rise is due to the ground contact patch of the tire being reduced as the inflation pressure increases.
Our research showed that vegetative index variations in regrowing alfalfa were impacted by machinery wheel traffic at various tire inflation pressures. Plots with machinery traffic applied by tires operated at lower inflation pressures showed more regrowth 10 days postcutting than those that had traffic applied with higher tire inflation pressures. Minimizing ground pressure by maintaining a lower tire inflation pressure will reduce damage to regrowing alfalfa and minimize soil compaction.
Alfalfa yield reduction is not the only concern when considering machinery traffic in alfalfa fields. In some instances, the wheel traffic damage can be severe enough to kill the entire plant. This has implications for the longevity of alfalfa stands and how many years the fields will be productive.
The University of Minnesota’s Deborah Samac showed that wheel traffic reduced alfalfa yield between 12% and 17% when applied two days after each forage harvest. This study also showed that wheel traffic from machinery significantly reduced plant counts.
If wheel traffic is managed well in a field, the productivity of that field could be better maintained over time, allowing producers to leave fields in alfalfa longer. This would provide additional soil health benefits while maintaining desired feed production and forage quality levels.
In an ideal world, all of our machinery would have working widths that are multiples of each other so that the tires fall on the same lines within a field, but I can’t imagine a farmer or custom harvester selling or replacing a perfectly good machine just because the work-
ing width did not match with the other machines in the fleet. Since this is the case, true controlled traffic is costly and difficult to achieve in the purest sense. However, there are some steps that can be taken to minimize the area of the field impacted by machinery tires and minimize the damage caused by the machines. This is accomplished by controlling when machines are in the field.
Research conducted at the University of Wisconsin-Madison has shown that most of the damage caused to regrowing alfalfa plants when exposed to wheel traffic happens as more regrowth is present. When new shoots are present and growing, the wheel traffic has a much better probability of causing damage. This may not impact yield at the next harvest, but it does require the plant to “catch up” compared to plants that were not exposed to wheel traffic and possibly expend more resources to do so.
Limiting the number and type of machines in the field as more days past cutting occur is a good way to minimize damage. Also, having oper -
1. TIRE PRESSURE : Check the tire pressures on all machines entering the field and ensure that they are within manufacturer’s recommendations. Aim to be on the low inflation pressure side of those recommendations to optimize the ground contact patch of the tire. If operating on the road and in the field, compromise on a midrange inflation pressure to reduce tire wear.
2. TIRE TYPE: Minimize the use of on-road tires. Use floatation tires when possible or
ators understand the importance of limiting the area impacted by wheel traffic is another good practice. If it is obvious that a machine has passed over a certain area, the subsequent machines can follow those wheel tracks to reduce the area impacted by tires. Defining in-field “roads” on headlands and when traveling to the chopper or collecting bales reduces the total area impacted by the tires. The plants within the “roads” will undoubtedly be damaged, but the total area impacted will be reduced. There is a lot to consider when har-
radial agricultural tires to lower the ground pressure of the machines.
3. IN -FIELD ROADS : Define “roads” in the fields so that the total field area impacted by machinery tires is reduced.
4. TI MING: Minimize machinery traffic in alfalfa fields as time passes after cutting and regrowth begins. The taller the new shoots, the more susceptible they are to permanent damage.
vesting alfalfa for silage or hay. Giving some attention to the machinery used in the harvesting process can pay dividends over time in terms of alfalfa yield and persistence. •
BRIAN LUCK
The author is an associate professor and machinery systems and precision agriculture extension specialist with the University of Wisconsin-Madison.
by Amber Friedrichsen, Associate Editor
HAVE you ever stopped to ponder the integrity of a plastic grocery bag? How such a thin material can support several pounds of apples, potatoes, jars of pasta sauce, a jug of orange juice — even a gallon of milk? It’s a wonder the flimsy sacks don’t spill their contents on the journey from the trunk of the car to the kitchen counter more often.
Hay binding is a similar feat of engineering, albeit at a much larger scale. Net wrap and baler twine configured out of plastic as thin as five-thousandths of an inch thick can hold the shape and support the weight of bales well over 1,000 pounds. Add in the explosive capabilities of densely baled forage and the proper selection and use of hay binding becomes that much more critical to safe handling and storage.
Choosing the right type of hay binding extends beyond the physical strength of net wrap or baler twine, though. Round bales can be bound by either product, depending on the harvest machinery on the farm, whereas square balers are
Norden provides a full range of bale handling options for passionate producers of quality small square bales.
inevitably set up for twine. Unit price and cost efficiency are among the other factors to consider before buying a season’s worth of binding. Even more important is the forage species and the end-use of the hay being baled.
This is what Mike Schon calls the “application” of hay binding, or the way it will be used to package, store, and feed out bales to meet consumer and market demands.
The vice president of sales and marketing for Bridon USA, an agricultural baler twine and net wrap manufacturing company based in Dubuque, Iowa, believes identifying the application of hay binding will not only point hay producers toward a specific product, but also inform the best practices to achieve their goals.
“Are you going to store bales inside or outside? For what amount of time? Will it be fed in three months or 12 months? How explosive is the type of forage in your environment?” Schon prompted. “Choosing hay binding is all about the application of it and what the farmer is going to use it for and if they are going to push the envelope.”
Net wrap typically outshines baler twine when it comes to efficiency. For example, if a baler turned four times to apply four layers of net wrap to a round bale, it would need to turn up to 30 times to put on an equivalent amount of twine. John Hilgart, a regional sales manager with Bridon USA, noted these extra revolutions could take up to one minute longer per bale to complete.
“One minute doesn’t sound like a lot, but you can go from averaging 25 to 30 bales an hour with twine to averaging 45 to 60 bales an hour with net wrap. If you take that over a fiveor six-hour day, you can make up to 180 more bales using net wrap,” Hilgart said.
Net wrap also offers hay better protection because of its ability to shed water, which is especially crucial for bales that are stored outside. Picture the flat end of a 5-foot round bale with a red circle painted around the outer 6 inches of its face. This painted layer of hay is the most susceptible to weathering, and it represents up to one-third of the bale’s total volume. Without proper protection from the elements, a bale can experience significant dry matter loss.
Learn how the Norden bale accumulator system can equip nearly every producer of small square bales. Best equipment for quality control and ease of handling. All the way from your field to the horse stable.
Moreover, moisture-wicking net wrap safeguards forage quality that would otherwise diminish if bales got wet. This added protection and better efficiency often comes at an additional cost, but Hilgart said it is an investment that pencils out to higher profits overall. Net wrap enables farmers to make the same number of bales using less fuel and less labor in less time compared to twine, which all translate to greater savings.
“A lot of people think it’s cheaper to put on twine because the product itself costs less, but then we look at how we are using much less fuel per bale, fewer man hours per bale, and creating less wear and tear on our equipment with net wrap,” Hilgart stated. “It may cost slightly more upfront, but
Fuel
6
Extra cost/bale to use twine $0.61/bale
it actually costs about 60 cents less per bale to use net wrap than twine.”
Despite the niceties of net wrap, many round balers are set up for twine, and twine is the default binding option for square bales. These polypropylene or sisal strands are categorized by knot strength, which is essentially a measure of tensile strength, or the maximum load a material can withstand without breaking.
The higher the bale density — and the larger the bale — the greater the knot strength required to contain forage. Mismatching knot strength with bale density and size could lead to what Schon and Hilgart refer to as “pain points” in the field, or broken knots, misties, and bales that fall apart altogether.
“It goes back to application,” Schon said. “There is a difference between the most intensive baling conditions and the most efficient. If you want twine that will hold up when you try to make a bigger bale or need to pack bales more densely to fit travel restrictions, you might have to increase your knot strength to achieve that.”
Some forage species require stronger knot strengths as well. For instance, alfalfa tends to be relatively easy to bale and hold together with twine, whereas crops like wheat straw and bermudagrass can put up more of a fight to stay bound.
“Think about if you took a handful of drinking straws and squeezed them together,” Hilgart explained. “The second you let go of the straws, they are going to release and expand again, and that is what wheat straw and bermudagrass want to do in a bale.
strength, this becomes more important when baling more compressive forages, like wheat straw.
Net wrap and baler twine have their differences, but both are available with variable degrees of ultraviolet (UV) protection. Without it, hay binding is subject to solar degradation, which threatens forage quality preservation and can present challenges to bale handling and transport.
“Those products, which are holding bales together when you pick them up to put in the feeder or on a truck for transport, start to deteriorate without an appropriate amount of UV protection. In a very short period of time, those bales will start to fall apart,” Schon asserted.
“As soon as that net wrap, in particular, starts to break down, it’s not shedding water as well. Water will start to penetrate the bale, and we can lose the quality of that outer one-third of bale volume within a few months,” Hilgart added.
Selecting the right type of hay binding may seem like a small step in the haymaking process, but it is one that must be approached from many angles. Producers can make the most of their investment by understanding the application of net wrap or baler twine and knowing how the aspects of each option will serve their operation. Next time you make a bale — or pick up a plastic grocery bag — consider the value of what’s inside. Then, take a minute to assess the product that you chose to contain and preserve the contents. •
“Crops like that generally need a higher knot strength because even though these bales would weigh less than alfalfa bales of the same size, there is much more compression in wheat straw and bermudagrass, so it takes greater strength to hold that forage intact,” he continued.
Another descriptor of baler twine to deliberate is tail length. Longer tails are more forgiving when bales stretch and expand in the same way longer shoestrings are less likely to come untied when the laces are pulled tight. Similar to knot
by Dan Undersander
GROWING concern has been that many farmers lose too many leaves during the harvesting process. Leaf percentage of harvested alfalfa affects both yield and forage quality. This is illustrated from samples taken by students in the Winfield intern program shown in Table 1. The alfalfa was cut at a 3-inch height prior to mowing and then hand separated into leaves and stems. All fields were harvested for haylage. The interns also sampled the harvested forage and hand separated it into plant components.
On average, the leaf content was 8.9% less in the harvested forage than the standing alfalfa. With hay at $207 per ton (University of Wisconsin Midwest Hay Market Report, June 11, 2024), this represents a yield loss of $36.85 per acre for a 2 tons per acre yield, a forage quality loss of $102.35 per acre, and crude protein loss (with soybean meal at $365 per ton) of $4.23 per acre. The total loss then sums to $143.43 per acre for the 2 tons per acre dry matter yield. Some fields showed leaf losses approaching 20%!
Leaf loss measured
Leaf loss can occur prior to harvest due to disease or insects and based on the method of harvest. To help farmers
better assess their alfalfa production and success in holding leaves, a near infrared spectroscopy (NIRS) equation for leaf percentage was developed by Forage Genetics International. NIRS is able to predict leaf content due to the different composition of leaves and stems. Figure 1 shows that NIRS is able to predict leaf content with 84% accuracy.
The NIRS equation was licensed to forage testing laboratories and run on samples when the analysis was requested. The results to date from
three laboratories offering the test are shown in Table 2.
Alfalfa is generally about 50% leaves at the bud stage. The means of all samples submitted ranged from 50.5% to 55.7%. This is higher than expected, but likely indicates that only better samples were submitted.
The standard deviation is the range that includes two-thirds of the samples. Considering that the standard deviation is about 10%, 16% of the samples were above 60% leaves and perhaps harvested too early with significant yield loss.
The test results can also encourage
30 measurements across 1st, 2nd, and 3rd harvests in Midwest
improved management for the 16% of samples below 40% leaves. Farmers harvesting these samples lost about $160 per acre with today’s prices and a 2 tons per acre yield.
Farmers with significant leaf loss should evaluate and determine what can be done to improve leaf content. Some losses due to environmental effects are unavoidable; however, there are factors that can be managed:
1. Diseases and insects can cause substantial leaf loss, so the use of fungicides and/or insecticides might be worthy of consideration.
2. Moisture content of forage is important to leaf retention. This is why fields harvested as dry hay yield less than haylage (or baleage) fields.
3. Drier forage at harvest also results in leaf loss, so some farmers harvest with dew present to keep more leaves. Farmers in more arid regions bale at night and/or use a steamer to artificially create dew.
4. Equipment type, settings, and speed are important. Leaf loss is accelerated by use of a flail rather than roll conditioner, conditioning too aggressively, raking/merging too fast, or setting pickup speed faster than ground speed on the baler or chopper.
Knowing the leaf percentage of harvested alfalfa forage can aid in managing alfalfa production and harvesting to improve forage yield and quality. Consider having the test run on a few samples this year to help assess current harvest practices. •
The author is a forage professor emeritus with the University of Wisconsin-Madison.
by Mike Rankin, Managing Editor
TAYLOR Gramm helps to oversee a custom harvesting business that has more forage harvesters than primary clients it chops for. Normally, that would seem like a business model destined for failure, but that’s not the case here.
Gramm works for C.R. Koehl & Sons, which is located in west central Minnesota, about 20 miles from the South Dakota border. The custom forage harvesting business that consumes his time is just one enterprise of the much larger 9,500-acre farm that grows and harvests organic and conventional corn, edible beans, sugarbeets, carrots, and alfalfa. They also run a 2,200-head feedlot, a large hog operation, and operate a feed supply retail outlet.
So how do you pull off owning and operating two large forage harvesters and associated harvesting equipment with only one client? That one client, Riverview LLP, owns two nearby dairies that milk 15,000 cows between them and require thousands of acres of feed. Before coming to C.R. Koehl & Sons seven years ago, Gramm spent 12 years working for Riverview as a crop and forage harvesting manager. At that time, Riverview cut back on their ownership
of harvesting equipment and Gramm’s current employer doubled their capacity from one forage chopping system to two. A system is defined as a chopper, two mergers, two dozer tractors, and five to eight trucks. Three triple mowers do the alfalfa cutting.
“Ninety-five percent of the chopping income comes from Riverview,” Gramm noted. “The remaining 5% is mostly for our own company’s feedlot and those of neighbors.”
Alfalfa provides a beneficial rotational crop for the vegetable growers in the area, including C.R. Koehl’s acreage. All of the alfalfa and corn silage harvested for the two Riverview dairies comes from land owned by area crop and vegetable farmers. “For our farm and others, alfalfa helps control diseases and weeds, especially on the organic acres,” Gramm explained. “We currently have about 10% of our acres in an organic program and are hoping to get to about 20% over the next few years. Alfalfa has been beneficial to that conversion process.”
Gramm said their two harvest systems handle about 3,000 acres of alfalfa and 5,000 to 6,000 acres of corn for silage each year. Three Claas triple mowers and
four Oxbo mergers are run ahead of two Claas 990 choppers for the haylage harvest. C.R. Koehl & Sons have four trucks of their own and contract with neighbors for the remaining units needed. Although communication and coordination are always key when several forage harvesting outfits are harvesting at the same time in different locations for the same farm, corn silage harvest raises the stakes. “We all talk to each other every day so that we can stay in sync with each other,” Gramm said. “Riverview has a person that oversees their two farms in this county, and he looks at the big picture, determining how many choppers are needed for a given day and where. Our farm also has a person who monitors field maturity, and he stays in close contact with Riverview. We’re all like one big happy family,” Gramm chuckled.
When harvesting corn silage, the forage is chopped into large dump wagons, which then is unloaded into the waiting trucks at the field’s edge. The wagons also are used for haylage on an as-needed basis, usually when fields are wet. Each tracked dump cart can hold as much feed as a full semitrailer — about 24 tons of wet corn silage — and has its own scale. This eliminates having to run trucks across a driveover scale on the farm, which saves time. “When everything is working, the chopper never stops,” Gramm noted. With the dump-cart system, Gramm said that their truck repairs have gone way down, and it’s much easier to train truck drivers. The downside is that a 500
HP tractor is needed to pull the carts. During the corn silage harvest season, choppers run around the clock. Employees are placed on one of two 12-hour shifts starting at 2 p.m. and 2 a.m. That’s adjusted on Sundays to help protect the employee’s day when no chopping occurs. “We try to be home by midnight on Saturday night,” Gramm said. “Nothing happens on Sunday.”
Gramm said that they like to hire local people and family members that
them,” he added.
“The farm owners at C.R. Koehl & Sons like to hire a lot of young people, too, and train-up the next generation,” Gramm said. “We want to get them on the farm and teach them to love agri-
challenge with labor,” he said. “There’s a lot of competition for good employees around here.”
Communication is a skill that is highly stressed at C.R. Koehl & Sons. “We talk all of the time so everyone knows what’s going on,” Gramm explained. “This helps keep people awake and alert. If an employee thinks they will sit in the tractor and listen to podcasts all day, they usually don’t make it with us,” he added.
Gramm said that they try to make their farm a desirable place to work and maintain a family atmosphere. “We all take a break time every day at 9:30 a.m. and 3:30 p.m., he explained. “Our wives will often fix meals and bring them out to the field, where we’ll pause and eat together.
“Employee safety is front and center every day,” Gramm asserted. “We bring up safety at every meeting and employees have the opportunity to share both their mistakes and ideas to make for a safer work environment. Rather than a safety policy, we try to instill a safety attitude,” he added. •
“Best gopher control I’ve ever seen. Our cost per acre has gone down after the first season of use. Just added a second machine to cover all M.B. Walla Walla, WA
by Shelby Gruss
FORAGE sorghum, sorghum-sudangrass, and sudangrass are all excellent options for warm-season annual forage species that can produce large amounts of biomass, especially in drought years or when you are running short on forage. These species can be grazed or harvested for hay within 35 to 40 days of growth under the right growing conditions.
Although sorghum species can pose a risk of prussic acid poisoning, it is possible to safely and effectively utilize these types of forage with proper management. The breakdown of dhurrin, a secondary metabolite found in sorghum species, leads to the release of prussic acid, which highlights the importance of understanding and managing this aspect of plant physiology for safe and effective utilization of sorghum forage. Proper management strategies to mitigate the effects of prussic acid poisoning include avoiding grazing
livestock on plants under 18 inches tall as young plants can have higher prussic acid potential. It is also critical to avoid grazing plants that have undergone frost stress for at least one week (rolling suggestion), and to avoid utilizing plants that have been under drought stress. These conditions tend to elevate the dhurrin content present in the crop, and thus the potential for prussic acid poisoning. Additionally, when prussic acid is a concern, cutting for silage, green chop, or hay is traditionally recommended. The chopping action of harvesting
sorghum species for silage and greenchop can help cause a breakdown of dhurrin and release of prussic acid before feeding. Furthermore, animals cannot be as selective with what plant tissues they choose to eat as they may be when they are in a grazing system. It is important to note that leaves contain higher dhurrin content than stems. After chopping forage, the fermentation process of silage may reduce dhurrin content even more.
Making hay has been previously reported to mitigate prussic acid poisoning potential in sorghum species by up to 75% during the sun-curing process. Despite this, the lab I worked for at Purdue University received a call from a Kansas farmer back in 2020 asking how he killed his cattle by feeding them sorghum-sudangrass hay. Through initial investigation, the cause of death was identified to be prussic
conducted and the results can be found at bit.ly/HFG-dhurrin-breakdown.
acid toxicity, which contradicts the idea that dry down and sun curing equates to safe sorghum hay.
As a result of the situation in Kansas, we wanted to evaluate how dhurrin content is affected by dry down through sun curing and storage for up to two months. Through a series of trials, we dried sorghum leaves and whole sorghum plants in the greenhouse, allowing for direct and indirect sunlight without the risk of forage being rained on or other inclement weather concerns. We found that during the drying period and sun-curing process, dhurrin content remained stable, and it did so for at least two months in the dry hay material. Additionally, another research study found dhurrin to be stable in oven-dried material for up to 10 years, suggesting it could be stable for much longer in sun-cured forage material. Dhurrin is only inherently dangerous if it is broken down into prussic acid. When testing forage for prussic acid release using water for rehydration, there was a significant delay in prussic acid being released. After discovering this, we then wanted to test what would happen when dhurrin is broken down in a cow’s rumen. Using rumen fluid from a fistulated dairy cow, we found prussic acid was quickly being released from the dried samples. In fact, treated paper disks inserted in the vials containing forage samples changed color within about 15 minutes after adding the rumen fluid. More information on how this study was
So, what does this mean for producers? Our research indicates that drying or sun curing forage does not necessarily reduce prussic acid poisoning potential, highlighting the importance of careful forage management. For those concerned
with high dhurrin levels, it is recommended to cut for silage or potentially green chop, but making hay will not help alleviate high prussic acid concerns. This emphasizes the need for ongoing research and awareness to ensure the safety and effectiveness of sorghum-based feeds. In conclusion, sorghum, sorghumsudangrass, and sudangrass offer valuable benefits as warm-season annuals for biomass production, especially under unprecedented growing conditions or when forage is scarce. While prussic acid poisoning poses a risk, proper management strategies such as avoiding grazing on young or frost- and drought-stricken plants and opting for silage or greenchop can mitigate these dangers. •
SHELBY GRUSS
The author is the state forage specialist with Iowa State University.
Wisconsin Farm Technology Days
August 13 to 15, Cadott, Wis.
Details: wifarmtechdays.org
Farm Progress Show
August 27 to 29, Boone, Iowa
Details: farmprogressshow.com
Husker Harvest Days
Sept. 10 to 12, Grand Island, Neb.
Details: huskerharvestdays.com
National Hay Assn. Convention
Sept. 18 to 21, Scottsdale, Ariz.
Details: nationalhay.org
World Dairy Expo
World Forage Analysis Superbowl
October 1 to 4, Madison, Wis.
Corn silage entries due July 10
Hay crop entries due August 22
Details: bit.ly/HFG-WFAS
Sunbelt Ag Expo
Southeastern Hay Contest
October 15 to 17, Moultrie, Ga.
Hay contest entries due August 30
Details: bit.ly/HFG-SHC
Heart of America Grazing Conference
October 15 to 17, Elizabethtown, Ky.
Details: forages.ca.uky.edu/events
Penn State Dairy Cattle
Nutrition Workshop
November 6 and 7, Hershey, Pa.
Details: bit.ly/HFG-DNW
MFGC Annual Conference
November 13 and 14, Lake Ozark, Mo.
Details: missourifgc.org
Western Alfalfa & Forage Symposium
December 10 to 12, Sparks, Nev.
Details: calhaysymposium.com
American Forage & Grassland
Council Annual Conference
January 12 to 15, Kissimmee, Fla.
Details: afgc.org
Harvested hay acres in the U.S. were estimated to be down 2% this year in USDA’s June Acreage report. Total harvested hay acres are expected to reach 51.5 million acres compared to the 52.8 million acres harvested in 2023.
Weather conditions in the West have generally been good and export demand for alfalfa and grass hay have reportedly been firm; however, the unwaveringly strong U.S. dollar raises questions as to how long current pricing strategies will be effective.
The prices below are primarily from USDA hay market reports as of mid- to late June. Prices are FOB barn/stack unless otherwise noted.
For weekly updated hay prices, go