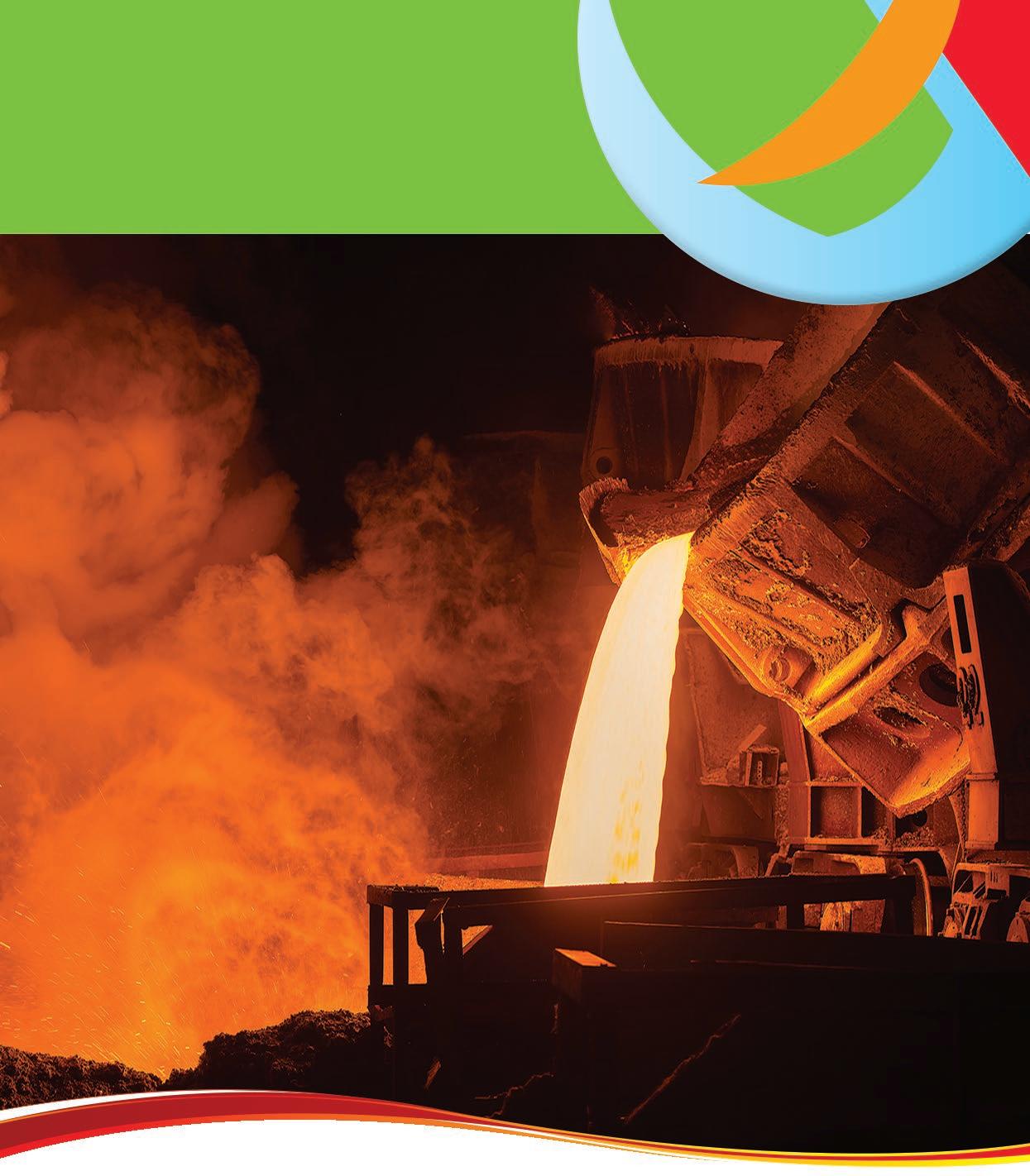

We finally got to experience our first full year with no lockdowns or restrictions; transitioning back into a sense of normalcy. Something I know we have all missed very much. Since our last Connections in May, it has been incredible to witness the milestones and achievements of our members. The 2nd half of the year brought incredible triumphs towards radical innovations and sustainability, a mixture for success when it comes to driving the circular economy forward.
First, we begin with a story of the future! Meta has developed a new Artificial Intelligence (AI) model that optimises concrete mixtures for sustainability and strength. Last year, Meta achieved net-zero in their operations. Now, they’re turning their attention to achieving net-zero across their value chain by the end of 2030. Make sure to read about the special way they plan on doing this.
Next up we explain how the Illawarra could help reduce 88% of Australia’s emissions outlined in a new report by the Australian Industry Energy Transitions Initiative (ETI). The report highlights that this immense figure amounts to removing all emissions from cars and light commercial vehicles across Australia. You don’t want to skip past this one.
Keeping the theme of radical innovation and sustainability, ASA member Harsco has announced the world’s first Carbon Negative Steel Slag, an aggregate-based asphalt using lignin binder product made from trees. A very important read that documents the ongoing practices in achieving net-zero.
We share an ongoing project involving ASA member Infrabuild, who continue to supply a suite of capabilities to the world class infrastructure, Sydney Gateway. Their involvement has been critical to the success of the project. Read all about it in this issue.
As we continue to make tremendous steps toward the development of slag, it’s always inspiring to reflect on the past and acknowledge the outstanding projects that have utilised cement replacement products - The Sydney Harbour Tunnel being one of them! This flashback story details the clever design and utilisation of slag products that have guaranteed to stand the test of time.
More recently, we discuss Holcim’s third edition of the Start-up Accelerator Program that aims to accelerate sustainable construction across the world. Looking closer to home, we specifically address the need for embracing Net Zero Goals by 2050 by finding material solution to reduce CO2 footprint of concrete. You can learn all about the intensive 6-month program in this issue.
Have you heard of the High-density Geopolymer Concrete (GPC) at Port Kembla's Northern Breakwater? The University of New South Wales has published its 2nd monitoring report on the in-field performance of GPC. In this issue you can find the critical outcomes documented from the extensive trials.
We also share a local story of ASA member, Australian Steel Mill Services who has joined forces with the University of Wollongong to commence a new research project at the Steel Research Hub. The research entitled ‘Transport Infrastructure Construction Using Steel Furnace Slag (SFS)’ will explore possibilities of utilising SFS in engineering applications and integrating it with by-product materials. Read all about the innovative research project in this issue.
ASA member BlueScope has recently contributed to the revised ResponsibleSteel Standard. A standard that will introduce strict new requirements to reflect the growing need for sustainability measures and responsible sourcing. Make sure to read all the details on The International Standard V2.0
We bring you another blast from the past that is very telling in terms of the research and development that was undertaken at the time, as well as the continuing ‘debate’ on sustainability that ultimately brought us to where we are today. You don’t want to skip past this one.
Next up, ASA member Holcim are currently constructing a facility to import and distribute low carbon cement replacement products. New Zealand currently uses 1.6 million tonnes of traditional cement. However, Holcim is working with the construction industry to achieve 25% replacement by 2025 – reducing 300,000 tonnes per annum. This issue details the exciting infrastructure with peak operations scheduled for the end of 2022.
The 15th Global Slag Conference, Exhibitions and Awards are officially back with a major topic of ‘Maximising Profits from Slag.’ If your business includes slag, make it your business to attend the 15th Global Slag Conference!
Lastly, we present you with a story on our Executive Director Craig Heidrich’s noteworthy virtual presentation at the 11th EUROSLAG Conference. For those who were unable to attend the prestigious event, we have compiled what you need to know about the standard specification for low-carbon concrete using iron and steel slags, as well as the innovative journey the association has embarked on, and the many discoveries made along the way.
Finally, The Australasian (iron & steel) Slag Association would like to say a big thank you to our members for their support and contributions over the past 12 months -- this issue of Connection wouldn’t be possible without your amazing achievements. We look forward to reporting on your 2023 achievements next year and continuing to work together into the future.
Last year, Meta achieved net-zero in their operations. Now, they're turning their attention to achieving net-zero across their value chain by the end of 2030. The way they aim to do this is definitely in their special way- by using new technological processes to speed up the process.
AI is used to learn and optimise specific outcomes within high dimensional spaces, where data sets with many attributes can be modelled. When a valid data set is available, AI can be used to estimate or “learn” the feasible high-dimensional space in terms of relevant parameters, such as strength and sustainability. To develop this type of model, Meta acquired the work of researchers at the University of Illinois at Urbana-Champaign, including AI expert Prof. Lav Varshney from the electrical and computer engineering department, and concrete expert Prof. Nishant Garg from the civil engineering department.
Using the input data on concrete formulas along with their corresponding compressive strength and carbon footprint, the AI model was able to generate several promising new concrete mixes that could meet Meta's stated data centre requirements with a lower embodied carbon impact than the industry standard.
Meta released in a recent post that "With AI, we were able to accelerate the discovery process and validate good formulas within weeks. In this effort, the low-carbon concrete formulas generated by the model entailed significant replacement of cement (upwards of 70%) with a combination of two types of low-carbon substitutes, namely fly ash and slag," they said. After a process of elimination, the final mix was chosen and immediately headed for practical testing.
After the final formula was tested in a controlled lab environment, Meta agreed to test the mix on multiple (noncritical) structures, which included using the mix in their DeKalb data centre, where it can now be found in the guardhouse floor slab and the floor slab of the construction management team’s temporary office space building. "This refined concrete formula entailed upwards of 50% cement replacement with a combination of fly ash and slag," Meta stated, showing their commitment to developing practical solutions.
The field tests confirmed that the resulting low-emission concrete formula exceeded the seven-day and 28-day strength requirements found in industry standard requirements, with a carbon impact 40% lower than the regional benchmark. However, to enable faster, more efficient construction required for Meta's priorities, they explained the concrete needs to meet specific strength thresholds earlier than seven days.
With the help of this AI model, Meta has been able to successfully design and use concrete that meets their long-term strength requirements and has a 40% lower carbon impact than the regional benchmark. But they are just getting started. "While we are encouraged by the success of this pilot, further developments and tests are needed to scale the impact of this innovation. This includes a few factors:
First, we need to understand and optimize the performance of the mixes under different weather conditions, such as the cold weather in Illinois. Each data centre location has unique attributes that must be accounted for in the design and testing of concrete. There are also improvements to be made to optimize for early strength gain (i.e., to have it set faster) to accommodate a tighter construction schedule. There is an opportunity to directly optimize for such logistical considerations.
Finally, there is a need to understand how novel materials could be used in place of cement in concrete, particularly as the supply of traditional cement substitutes like fly ash and slag is projected to decrease in the long run. Material availability is an important factor in construction; identifying novel materials that could be used in concrete can open new opportunities. Additionally, novel materials can further enhance the strength and sustainability of new concrete formulas," they said.
The resulting concrete mixes from Meta's model can be used outside of data centre construction, and there is an opportunity to further develop this model to address other use cases. In efforts to find the best solution, Meta plans to continue researching and developing concrete mixes whilst also looking into how building design can help lower emissions.
In collaboration with researchers at the University ofIllinois
atUrbana-Champaign,
Facebook's parent company, Meta has developed a new Artificial Intelligence (AI) model that optimises concrete mixtures for sustainability and strength.
As outlined in a new report by the Australian Industry Energy Transitions Initiative (ETI), an 88% cut to heavy industry emissions is possible and would set up key regions for the net-zero transition, says research backed by 18 of Australia’s largest companies.
Major Australian industrial regions such as the Pilbara, Kwinana, Hunter, Illawarra, and Gladstone have the natural resources, workforce and baseline infrastructure that can be expanded to support Australia’s netzero transition the report said.
Together, these regions are set to achieve an 88% reduction in their current emissions, which account for one-eighth of Australia's total emissions. The report highlights that this immense figure amounts to removing all emissions from cars and light commercial vehicles across Australia.
The ‘Setting up industrial regions for net zero’ report is the result of a two-year collaboration between the ETI and some of Australia's biggest companies. It was prepared for the ETI by not-for-profits, Climateworks Centre, based at Monash University, and Climate-KIC Australia, which are 'co-conveners' of the initiative.
The report shows that industrial regions can contribute to reaching state and national net zero emissions targets by 2050 while driving employment growth and building Australia’s climate resilience.
In creating this report, the ETI hopes to bring together key industry partners to accelerate action towards achieving net-zero emissions in supply chains by 2050, across critical sectors that have higher abatement/ exit costs.
The ETI focuses on reducing supply chain emissions across five sectors that include iron and steel, aluminium, Liquified natural gas (LNG), and other metals including copper, nickel, lithium, and chemicals, such as fertilisers and explosives.
The 18 initiative participants include Australian Gas Infrastructure Group, APA Group, Aurecon, AustralianSuper, BHP, BlueScope Steel, bp Australia, Cbus, the Clean Energy Finance Corporation, Fortescue Metals Group, HSBC, Orica, National Australia Bank, Rio Tinto, Schneider Electric, Wesfarmers Chemicals, Energy & Fertilisers,
"Through this analysis of the decarbonisation potential of five important industrial regions, we have gained invaluable insights into the opportunities and on-the-ground challenges in the net-zero transition," said Australian Industry ETI Chair, Simon McKeon AO, Chancellor of Monash University, former CSIRO Chairman, and former Australian of the Year.
The report finds Australia’s industrial regions can capitalise on global demand for low-carbon products and energy exports.
"This is achievable if we rapidly deploy existing technology solutions and support the development and demonstration of emerging opportunities through more proactive regional coordination and collaboration," said Climateworks CEO Anna Skarbek.
However, the report revealed later on that an additional 25-47% (or 68.3 to 125.9 TWh of energy) of Australia's total electricity generation would be needed to decarbonise these industries.
"This will require an unprecedented transformation of the energy system. Governments will have a significant role to play in achieving this, with supportive policy, programs, and support for regional leadership efforts, especially in infrastructure which is an enabler of decarbonisation," said Ms Skarbek.
The report has a set of recommendations to assist the acquisition of net-zero targets. This includes the formation of clustered industrial precincts in hard-to-abate sectors that are concentrated to assist with troubleshooting.
ASA member BlueScope Steel says, "BlueScope welcomes the release of the Australian Industry ETI Phase 2 Report: A guide to decarbonisation opportunities in regional Australia. Our regions are important contributors to the Australian economy that also present significant opportunities to leverage existing infrastructure and skilled workforces to decarbonise Australia’s key supply chains and remain competitive in a decarbonising global economy," said Greta Stephens, Chief Executive Climate Change & Sustainability of BlueScope.
With pressure increasing on these industries to decarbonise, the next phase of ETI's initiative will focus on setting decarbonisation pathways that prevent global warming to 1.5 degrees Celsius.
HERE'S
SteelPhalt has introduced the world’s first carbon-negative steel slag aggregate-based asphalt using lignin binder product made from trees. Harsco Corporation, a global market leader providing environmental solutions, announced SteelPhalt, a part of its Harsco Environmental division has launched a carbon-negative asphalt product.
SteelPhalt’s asphalt products use 95% recycled steel slag. Prior SteelPhalt asphalt products use bitumen to bind the asphalt. Bitumen is an oilbased binder product with a significant carbon footprint. SteelPhalt’s new asphalt product, called SteelSurf ECO+, uses kraft lignin-based Lineo®, a renewable bio-based substance, supplied by GautamZenUK in collaboration with Stora Enso, as an alternative to bitumen dramatically reducing the product’s carbon footprint.
“In our journey to become the world's most sustainable asphalt supplier, this is a huge step forward,” said Julian Smith, SteelPhalt Strategic Growth Director. “This product is an example of what our team’s collective passion for innovation and sustainability can deliver, while making the world a greener place.”
Harsco's Environmental division is the largest and most comprehensive provider of onsite material processing and environmental services to the global metals industry, with operations at over 130 customer sites across more than 32 countries. The division is a technology partner to cleaner, more efficient metal production, providing customers with economically and environmentally viable solutions for the treatment and reuse of production by-products.
Visit www.harsco-environmental.com to learn more.
www.asa-inc.org.au
Sydney Gateway is an above-ground, toll-free, high-capacity connection from St Peters Interchange to the International and Domestic terminals. The world-class infrastructure will reduce congestion, divert trucks from local streets around Mascot, and improve traffic flow. A needed investment as Sydney’s population grows exponentially to similar sizes of London and New York by 2056.
The construction is being delivered over two sections. First, the International Terminal and Qantas Drive connection, and secondly, the arterial road connection that will create access for the Domestic Airport Terminals.
Infrabuild's involvement and product supply with this world-class infrastructure has been ongoing since November 2020 and from the commencement, has supplied 1,400 tonnes of reinforcing bars, 2,000 tonnes of prefab, pile cages, reidbars, mesh, and accessories such as Ancon products, sonic tubes, and related steel reinforcing products.
Project Manager of Infrabuild, Steve Niven explains, "We’re probably around 15 per cent into the job. It’s a 15,000-tonne job so we’re still very early days”, he said. In total, Infrabuild will be supplying 1,800 tonnes of piling cages, which will be used in 15 of the new bridges and viaducts.
Throughout this process, Infrabuild has reflected on the key learnings from their involvement, namely their expertise in preplanning, that has kept the project on target. Sales Manager for Infrastructure and Major Projects, Peter Markuse, explains, “we recently received a big rap from the customer because we spent a lot of time preplanning. We’ve been working with them from the start due to the volume of the piling cages that were involved," he said.
He continued, "We said we’d like to start delivering early, so we started delivering two to three months earlier. That kept the program up and has been a significant factor for us, particularly with the unpredictable weather," he said.
He continues, “Being in front has been a real benefit, and a real key learning for infrastructure jobs going forward. When we talk to customers on new jobs, we talk to them now about how we can start supplying earlier and discuss how they can find some room for that, to maintain the program. That’s important and has been a major lesson,” explains Peter.
There is no doubt that Infrabuild's involvement has been critical to the success of the Sydney Gateway project bringing a suite of capabilities including:
• An experienced team, with two full-time detailers committed to the project.
• Weekly meetings with site engineers.
• Technical expertise, 5D modelling for headstocks, piling cages, sonic tube installation, inclinometer, and production capability on detailed workshop drawings and mechanically coupled tension piles.
The project is due for completion in December 2024.
www.asa-inc.org.au
In this story we go back to the early 2000’s – life was simpler, yet remarkable engineering achievements were extremely prevalent. The Sydney Harbour Tunnel was one of those projects, an incredible structure with an impressively simple concept and clever design, it showed an array of beneficial results from the use of cement replacement methods. Take a read below.
AMIDST the euphoria of the Olympics 2000 and its associated massive construction program, it’s easy to overlook some of the remarkable engineering achievements of the recent past such as the Sydney Harbour Tunnel.
Today as we drive through, we tend not to think about this remarkable structure, but only watch our speedo with the certain knowledge of the speed cameras’ presence. However, the Tunnel proposal as recently as a decade ago was looked upon with much concern by some in the engineering fraternity. Although immersed tube concrete structures were relatively common in cities such as Hong Kong, this project was proposed for under our Sydney Harbour and somehow this was different.
It’s surprising that something that caused so much concern in the late 1980’s is now accepted so completely in the late 1990’s. It opened to traffic on 31 August 1992, a date that was set by the contractor Transfield-Kumagai Joint Venture well before the construction commencement date of January 1988.
The concept of the project was impressively simple. Tenders were called by the Government for a second vehicle crossing of the Harbour to and from North Sydney, which resulted in a variety of bridge designs, all of which had a common self-destructing component. That was because extensive resumptions of properties – most containing homes and commercial premises were required to provide road access on both sides of the harbour.
The Transfield-Kumagai proposal was an exquisite example of lateral thinking. It identified the bottleneck as the existing beloved Harbour Bridge with its eight traffic lanes. The constriction was created because there were twelve lanes on the North Shore and twelve lanes on the city side adjoining the bridge having to merge into eight.
We all know the hassles of the common road situation of two lanes leading into one – very few drivers are prepared to readily allow merging. The Transfield-Kumagai proposal simply offered the practical alternative of adding four more lanes to the bridge, which gave twelve uninterrupted vehicular access lanes from the city to the North Shore. The punch was that the lanes were not hung off the bridge as some had suggested but laid down beside it - but under water.
Clever design meant that no resumption of properties was required which was a major positive factor in the tender evaluation process. This of course was only possible by using a precast tunnel across the floor of the harbour instead of the conventional bored tunnel which would have to be much deeper underground creating unacceptable grades to keep the new roadway within the existing publicly owned road system. Transfield-Kumagai had retained MacDonald Wagner (now Connell Wagner) to advise in structural design was in turn commissioned Freeman Fox (now Acer Consultants) to assist. The following extracts in italics are taken from a paper prepared jointly by Dr Lewis Gomes of Connell Wagner and Martin Morris of Acer Consultants.
Their paper was presented at a conference “Concrete for The Nineties” held in Leura, NSW 3-5 September 1990. The overwhelming concern facing the designers was that of durability with the then Department of Main Roads nominating that a minimum life span of 100 years was required of the structure. The problem of a submerged tube section is that it is subject to the “hollow leg” syndrome.
The chemical process of chloride and sulphate attack on the concrete matrix and the electro-chemical process of reinforcement corrosion has been well described by others (Eglington 1987). However, some aspects of durability are of particular relevance to immersed tube construction and are briefly reviewed below.
In a seawater environment, sulphate attack is diminished by the presence of chloride ions. This is because the expansive sulphoaluminate salts (ettringite) which result from sulphate attack on the tricalcium aluminate (C3A) content are more soluble in chloride solutions enabling them to be leached out prior to disruptive expansion.
The more serious concern is chloride penetration which neutralises the natural alkalinity of concrete and renders the reinforcement susceptible to corrosion, and subsequent spalling. The rate of chloride penetration is directly linked to the permeability of the concrete matrix
so that durability requires a sound, dense mix. The presence of cracks accelerates the rate of penetration over local areas, and therefore crack control also forms an inherent part of designing for durability.
Reinforcement corrosion is dependent on oxygen supply and since in permanently submerged concrete this is dependent on dissolved oxygen and diffusivity through saturated concrete, the process is significantly inhibited relative to reinforced concrete in the splash zone.
Nevertheless, concrete exposed to seawater on one side and air on the other, as in an immersed tube, is a special case of the corrosion process. The mechanism was first postulated during the ‘Concrete in the Oceans’ research program by CIRIA/UEG on offshore gravity structures and applied to hollow legs of oil platforms.
The relatively free availability of oxygen at the inside surface enables the inner reinforcement to become highly cathodic and set up galvanic action with the outer layer of reinforcement. The resistance of the electrolyte is reduced by saturation by water and further still by chlorides, so that the true “hollow leg effect” has to be assessed from actual penetration of seawater chlorides into structural concrete.
It can be seen that whilst concrete totally immersed in seawater would normally be “low risk”, the presence of oxygen within the tube contributes to a greater than normal risk.
It is obvious that the cement used in a structure such as this will play a major role in achieving low chloride penetration, low heat of hydration and minimal drying shrinkage cracking. With prior knowledge that
blended cements gave better performance with these characteristics than Ordinary Portland Cement (OPC) it was decided to further investigate the following blends:
• OPC with pulverised fuel ash (pfa)
• OPC with ground granulated blast furnace slag (ggbfs)
• OPC with pfa and ggbfs (triple blend)
The aggregates used would also play an important role in the concrete particularly with drying shrinkage, which was one of the stringent requirements of the concrete specification for obvious reasons.
As the tunnel units were to be cast in Port Kembla, a choice of two economically available aggregates were considered viz South Coast basalt and iron blast furnace slag.
It was concluded that a high replacement blend of ggbfs or pfa, or a triple blend of both could offer the benefits of:
• reduced heat of hydration (equal to Type C)
• very high resistance to chloride penetration
• good sulphate resistance (without increasing chloride ingress)
• acceptable stripping times
• ready availability
Further, good quality high density natural aggregates were readily available, but the use of slag as an aggregate might have cost and shrinkage advantages. Accordingly, a series of laboratory trials were set up to test these conclusions quantitatively.
The time/temperature plots showed that by using cement replacement methods, it was possible to simulate the approximate level of heat of hydration output from low heat Type C cement. The ACSE/ggbfs (50/50) mix using natural aggregate produced marginally the best result based on these particular tests. An ACSE/ggbfs (35/65) mix would be expected to produce a better result.
Accordingly, it was decided to concentrate on ggbfs mixes, particularly with their high resistance to chloride attack, and wide use in Europe for marine structures. Despite the excellent shrinkage performance of the slag aggregates, no precedent for its use in major marine structures could be found outside Australia.
Since the test results also confirmed its density to be about 3% less than equivalent Dunmore basalt mixes, it was reluctantly decided not to pursue the use of slag aggregate.
The problem of a submerged tube section is that it is subject to the “hollow leg” syndrome.
Holcim is one of the largest integrated suppliers and manufacturers of building materials and solutions in Australia and New Zealand. The business is immersed in the challenges of building solutions for a sustainable future and taking responsibility for the impact its products have on our planet. With innovation and sustainability at the heart of everything they do, Holcim launched the Holcim start-up Accelerator Program in 2018, dedicated to speeding up low-carbon innovation along the construction value chain. The program is open to start-ups from around the world, challenging them to accelerate sustainable construction with their disruptive solutions. Each participant is invited to apply for one of nine Accelerator country challenges that best match their start-up criteria.
This year the challenges encompassed a range of global opportunities that work towards the world's transition to net zero. These included:
• Social housing in Columbia.
• Data management in the USA.
• Bio-based Concrete Solutions in France.
• Smart building designs in Switzerland.
• Sustainable building materials in Canada.
• Carbon prestressed concrete technology in Germany.
• Circular economy systems in the UK.
• Reuse demolition waste such as slag in Mexico.
Looking closer to home, the Australian construction industry is equally embracing Net Zero Goals by 2050. The challenge is to find material solution to reduce CO2 footprint of concrete that contribute to these goals. Australian Steel Mill Services** (ASMS) through its partnerships with Australasian (iron & steel) Slag Association and Cooperative Research Centre for Low Carbon Living have used co-products such as steel slag to significantly reduce the CO2 footprint of concrete using alternative binder systems. Trials conducted demonstrate the system can be used without any technical challenges and possess the strength and stability to that of traditional construction materials available on the market.
**Our member the Australian Steel Mill Services (ASMS), which is 50/50 owned by Cement Australia and Levy in the United States. Cement Australia is a 50/50 joint venture between Holcim and Hanson.
The intensive 6-month program is conducted over a virtual platform, granting world-class access to a powerful mix of business and technical expertise across different markets and geographies. CEO at Holcim, Jan Jenisch emphasises the importance of the Accelerator program explaining, "At Holcim, we work with hundreds of start-ups around the world to accelerate innovation for sustainable construction. The Holcim Accelerator Program allows us to connect with the world's brightest minds to drive disruptive breakthroughs," she said.
The third edition of Holcim's Start-up Accelerator Program is well underway, running from May to November 2022, with start-ups presenting their work during Holcim's Demo Day from the 13 - 15 December 2022, in the hope that inspiring ideas and solutions are produced to shift gears in the construction industry.
It is programs like this that fosters the co-creation of innovative solutions and the pioneering of new technologies that ultimately accelerate our world closer to a circular economy.
Stay tuned for the innovative solutions that come from this world-class program.
This Australian Government led initiative is funded by the Cooperative Research Centre (CRC) for Low Carbon Living Ltd, with financial contributions through the Ash Development Association of Australia (ADAA) and Australasian (iron & slag) Slag Association (ASA), and significant in-kind support from the Australian Steel Mill Services (ASMS), Independent Cement & Lime, and Wagners and Cleary Brothers.
The anticipated rise in coastal wave energy and the continuing environmental attack from climate change scenarios are predicted to cause catastrophic impact on coastal protection structures, signalling an inherent need for upgrades to withstand the stronger wave actions and higher rates of damage.
To facilitate this need, UNSW research team developed a unique high-density low barbon geopolymer concrete (GPC) incorporating steel furnace slag (SFS) as aggregates, which is about 20-25 per cent heavier than natural basalt occurring as a by-product of steelmaking. This density has significant coastal engineering advantages.
This low carbon construction solution means a reduced dependency on fossil fuels and emission intensive constructions materials like Portland Cement thus, contributing to the target carbon neutrality by 2050.
Extensive trials were undertaken by the UNSW research team, to determine the beneficial use of steel furnace slag (SFS), both fine and course as concrete aggregates in a predominantly low calcium binder using GGBFS and fly ash. After formulating several mix designs comprising of exclusively slag cement and fly ash for the binder, researchers observed that SFS aggregates did not display and adverse expansion characteristics when used in conventional concretes. Furthermore, the mix designs performed well in ambient curing environment for strength gain.
The laboratory mixes utilised 65% fly ash and 35% ground granulated blast furnace slag by mass, respectively, activated with an alkaline solution of sodium hydroxide and Grade D sodium silicate solution blended in proportions to maintain a modulus ratio of 1.5 and a Na2O percentage of 5.5. The critical outcome from the trials is the successful incorporation of the SFS aggregates in the mix and thus, achieving a higher density margin.
Following the trials, the laboratory mix design was optimised by Wagners from Toowoomba QLD to adapt to the commercial batching methods (ready-mix trucks), with concrete batching completed in three pours. A total of thirteen armour units were cast in three pours utilising approximately 90m3 high-density GPC.
The compressive strength and splitting tensile strength of GPC batched in the lab trials and poured on-site in Port Kembla were evaluated using cylinder specimens cured in air and saline water.
Critical outcomes included:
• Lab trialled high-density GPC: steady increase over time with about a 14% rise in compressive strength from four (4) weeks to three (3) years.
• Air-cured samples: samples collected (cylinders) from pour 1 and pour 2 show significant strength reduction held in the laboratory watertanks. For instance, with respect to the 90 days strength, pour 1 had 54.6% strength reduction and pour 2 had 33.8% strength reduction in three years from air curing. These results were 'Test method' related and future changes are proposed for handling samples.
• On-site samples: higher strength than air-cured specimens collected from site pours and conditioned in the laboratory.
The utilisation of steel furnace slag (SFS) in low carbon Geopolymer Concrete (GPC) offers a unique concrete product to upgrade the coastal breakwaters to withstand climate change scenarios, save material consumption, and allow for greater stability without restructuring current Handbar amour unit designs.
ASA member, Australian Steel Mill Services (ASMS) has joined forces with the University of Wollongong (UOW) to commence a new research project at the Steel Research Hub.
The research project entitled Transport Infrastructure Construction Using Steel Furnace Slag (SFS) will be undertaken by a PhD student at UOW with a focus on developing an alternative composite SFS material for transport infrastructure construction, in partnership with UOW-based supervisors and industry partners.
The Steel Research Hub facilitates research projects with an overarching goal to support the transition of Australia's steel manufacturing industry into a more sustainable position by adopting practices and advanced manufacturing processes that help to reduce emissions and reach net zero.
SFS is the co-product of the steel-making process in the basic oxygen system (BOS). The slag is removed from the vessel after the exothermic refinement of molten iron and recycled steel in the presence of fluxes and oxygen. This process has limited applications compared to ground granulated blast furnace slag (GGBFS) because of its potentially expansive properties when hydrated.
Technical research undertaken in this project will explore possibilities of utilising SFS in engineering applications and integrating it with byproducts from other industrial processes. For example, SFS can be blended with by-product materials such as coal wash, plastic, cement, lime, or lignosulfonate, and serve as a landfill or a pavement material. The Australian Steel Mill Services (ASMS) is a joint venture between Cement Australia and Edward C Levy Co (USA) to service the slaghandling contract at BlueScope Port Kembla NSW. ASMS are contracted to collect and treat molten slag from the blast furnace and steel-making processes. Each year, ASMS process and market approximately 1.2 million tonnes of slag.
The UOW research team consists of multi-skilled individuals, with project leader Associate Professor Jayan S Vinod, Dr Pabasara Wanniarachchige, and PhD candidate Yeshwant Sunkara. The team will assess the engineering behaviour of the steel slag mixtures to try and optimise the mix designs with additives of other waste streams for the beneficial use in transport infrastructure construction.
We're excited to see institutions collaborating with critical industry partners in the form of Mr. Gavin Tory, Chair of the Australasian (iron & steel) Slag Association (ASA) and his ASMS colleague, Mr. Benjamin Muscat.
ASA member BlueScope have contributed to the revised ResponsibleSteel Standard. A standard that will introduce strict new requirements to reflect the growing need for sustainability measures and responsible sourcing.
ResponsibleSteel is a not-for-profit organisation and the industry's first global multi-stakeholder standard and certification initiative for responsible steel supply chains. Their first standard was first established in 2019 and was designed to ensure customers, stakeholders and consumers can be confident that the steel they use has been sourced and produced responsibly and as sustainably as possible.
The revised standard - The International Standard V2.0 will ensure steelmakers gain the credible recognition for the progress they make towards decarbonisation and allow customers to specify it in what they ask of their suppliers. The standard now incorporates additional requirements on GHG emissions and the sourcing of input materials as well as 13 Principles, 61 Criteria and over 500 individual requirements.
It comes after a multitude of hours was spent by experts from across the steel value chain including BlueScope, NGOs, academics and many others who offered their expertise to the ResponsibleSteel team in establishing a working standard; setting a clear direction for the steel industry.
ResponsibleSteel Forum III in Memphis, held from the 31 October - 1 November, was the next pivotal step in providing the opportunity to assess how the revised standard will shape steel decarbonisation and sustainability in the globalised steel value chain. The International Standard V2.0 has now edged us even closer to sustainable, net zero steel, projecting the industry on a critical journey with sustainability at its core.
Sustainability has come a long way since 1999. This article is very telling in terms of the research and development that was undertaken at the time, as well as the continuing ‘debate’ that ultimately brought us to where we are today. Enjoy this blast from the past!
MUCH has been written and spoken about the environment and the impact of human activity. In all of this, there are extremes of view, from those who would believe that the world is in imminent danger of destruction through global warming, through to those who want to debate the science underpinning such claims.
Whilst we may debate global warming, there is no doubt that human activity does have an impact. There is a greater appreciation of environmental impact of human endeavour at least in the developed countries. The notion of Ecologically Sustainable Development (ESD) emphasises that there
For quite several years now, the benefits of using high slag cements to enhance the durability of structures has been recognised. One example is the nagh Medal Award from the CIA for excellence in Concrete Structures.
rified matter separated during the reduction of a metal from its ore”.
Innovation is no stranger to the Slag industry. Recent research on alkali activation of ground granulated slag has yielded promising early strength results. Solutions proposed by this work are more practical than those usually offered the activation of cementitious materials without the use of Portland Cement. A new granulation facility at Port Kembla replaces capacity lost with the closure of primary production at Newcastle and provides
ASA member, Holcim, are currently constructing a facility to import and distribute low carbon cement replacement products within New Zealand.
New Zealand currently uses 1.6 million tonnes of traditional cement, equalling 1.3 million tonnes of C02 emissions.
However, in recent times, New Zealand has had minimal access to low-carbon cement alternatives, with the replacement of traditional cement equating to only 2%; in comparison to 26% in Australia. Holcim is working with the construction industry to achieve 25% replacement by 2025, which will aim to reduce 300,000 tonnes per annum.
This facility comes at the perfect time by providing a positive step toward New Zealand's Government Zero Carbon ambitions as well as Holcims 2050 net-zero pledge, which include 2030 targets certified by the Science Based Targets initiative (SBTi).
The low-carbon cement alternative will involve the use of Australian fly ash, a by-product of the iron-making process, and ground granulated blast furnace slag from Japan, formed when molten Blast Furnace Slag (BFS) is rapidly quenched from the furnace, rather than left to solidify by air-cooling slowly.
Executive General Manager of Holcim New Zealand, Kevin Larcombe, emphasises the benefits of the replacement products containing supplementary cementitious materials explaining, “These new products will absolutely deliver much lower embodied carbon...they also offer superior performance over standard cement. Depending on the application there are significant benefits," he said.
By the end of 2022, the facility will be at peak operation with 100,000 tonnes of ordinary Portland cement replaced with blended low-carbon cement, creating downward pressure on carbon emissions, and driving the circular economy even further into the future.
The 15th Global Slag Conference, Exhibition and Awards is back with a major topic of 'Maximising Profits from Slag.' If your business includes slag, you don't want to miss this.
After a long hiatus from face-to-face events due to COVID-19 restrictions, the conference is back and will be held in Dusseldorf, Germany from 7th - 8th June 2023.
The conference will allow attendees to maximise their profits from slag - both ferrous and non-ferrous, keep them up to date with the industry state-of-the-art, and provide extensive networking and business opportunities for both producers and users of slag and slag-based products.
If your business is slag, make it your business to attend the 15th Global Slag Conference!
Nominations are already open for the Global Slag Awards until March 2023.
• Slag and slag cement market trends
• Non-ferrous slags
• Slag product trends
• Beneficiation of slag and slag products
• Slag cement production and use
• Case studies
• New applications for slag and slag products
• Slag producers
• Slag-product users
• Cement producers and users
• Equipment vendors
• Traders and shippers
• Academics and researchers
For those interested to learn more about the Global Slag Conference, registrations and information can be found at
WWW.GLOBALSLAG.COM
The main agenda for the presentation addressed the standard specification for low-carbon concrete using iron and steel slags. In particular, the journey the association has embarked on, and the things discovered along the way.
Every journey comes with its challenges, and this was no exception. The use of steel furnace slag (SFS) found its way into traditional aggregate markets such as asphalts and road bases. However, Craig spoke about the opportunity to look beyond this by utilising granulated blast furnace slag (GBSF) in cementitious applications; a challenge the association set for themselves.
This journey started in 2012, with the hope of eliminating a Portland cement system using ambient temperature curing. This addressed the opportunity to use those materials and capture their intrinsic nature such as increased density.
Craig elaborated on the inherent need to transition into afield environment whereby case studies and learnings across the supply chain from resources to the end user are utilised, foregoing the laboratory and university-level testing which is consistently undertaken.
Craig also discussed the innovation journey towards new standards related to low-carbon concrete, with the prevalence of observing the key enablers regarding the adoption of new materials like iron and steel slags. This was achieved by looking across the supply chain of resources, processors, value adders, users/consumers, and influencers, all of which were ranked with issues regarding manufacturing, placing and finishing, durability, variability, economics, and standards and codes. Subsequently, the primary enabler being standards and codes.
We have all witnessed the ongoing charade of ESG reports, net zero goals, events, and sustainability jargon in various reports documenting the environmental impact of concrete and cement, although genuine action on the ground is few and far between. However, the emergence
of product category rules (PCRs) to develop environmental product declarations (EPD) is coming to the forefront. Craig makes a powerful observation, specifying the need to address the international consistency regarding PCRs and to establish the boundaries around how we quantify energy inputs or carbon footprint on the contributing materials.
To inform people of the new types of concretes and provide a howto for the engineering community, critical information for the separate standard specification was found through a series of demonstration projects. This included Toowoomba Wellcamp airport, the deep-sea water port at Port Kembla, and the City of Sydney. All projects received ongoing monitoring and evaluations of the materials and performed exceptionally well with further intrinsic benefits found. The Toowoomba Wellcamp airport consisted of a 70,000 square metre runway all built out of low-carbon concrete and using conventional paving equipment. Although challenging, it proves to be a huge milestone project. Craig explains, “This demonstrates we can build these large pieces of infrastructure and monitor them to demonstrate they are still performing well,’ he said. Additionally, a study at Port Kembla which utilised steel furnace slags witnessed a 20% increase in density – a very positive characteristic.
Projects like these helped form the new Standard Specification for Geopolymer Low Carbon Concrete.
Craig emphasises the importance of the specification explaining, “I truly believe it’s the first of its type across the globe in terms of holistic standard specifications interacting with a major code and addressing all of the adjustments you need to do in terms of the testing methods and how you would design for the durability requirements," he said.
Standards and specifications remain a key enabler for change, Craig explains, "If you can't get those elements right it can't provide the right tools to the design community to essentially have a crack at these types of concretes and increase uptake," he said.
He continues, “EPDs are going to be playing an important role but they must be internationally aligned with PCRs to accelerate the uptake of EPDs and to demonstrate the nature of these materials in a product status… EPDs are just one part of the whole equation and require a balanced approach," he said.