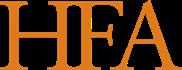
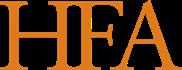
Statement of Qualifications
Industrial + Logistics
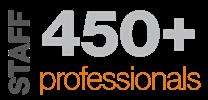
OFFICES
5 COUNTRIES
10,000+ projects permitted across
2 1900+ communities licensed in states
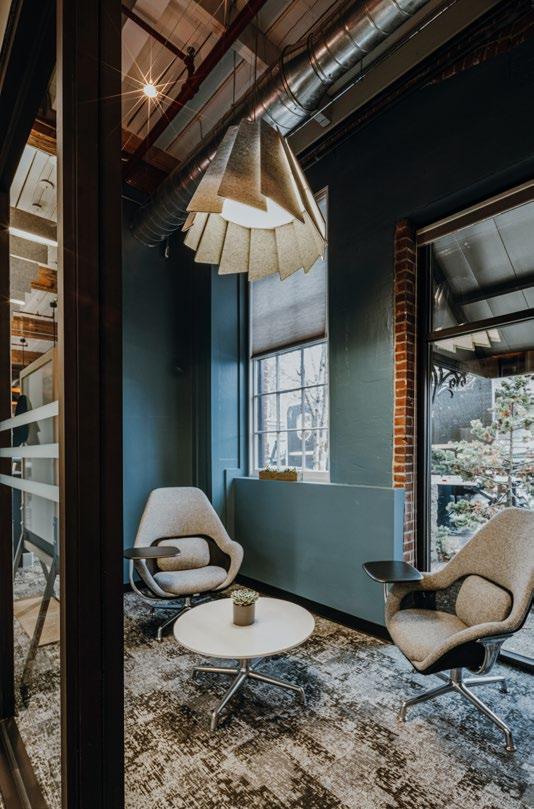
Employee Owned. People Powered.
Project Map
national coverage Coast to Coast + Licensed in 50 States

We have over 450 professionals working coast to coast, and licensure across all 50 states, so we can collaborate no matter where you’re based. We seek to deliver the right balance of simplicity and innovation to align teams and technology around what matters most—your customer.
single-source studio
Bring your whole design team together.
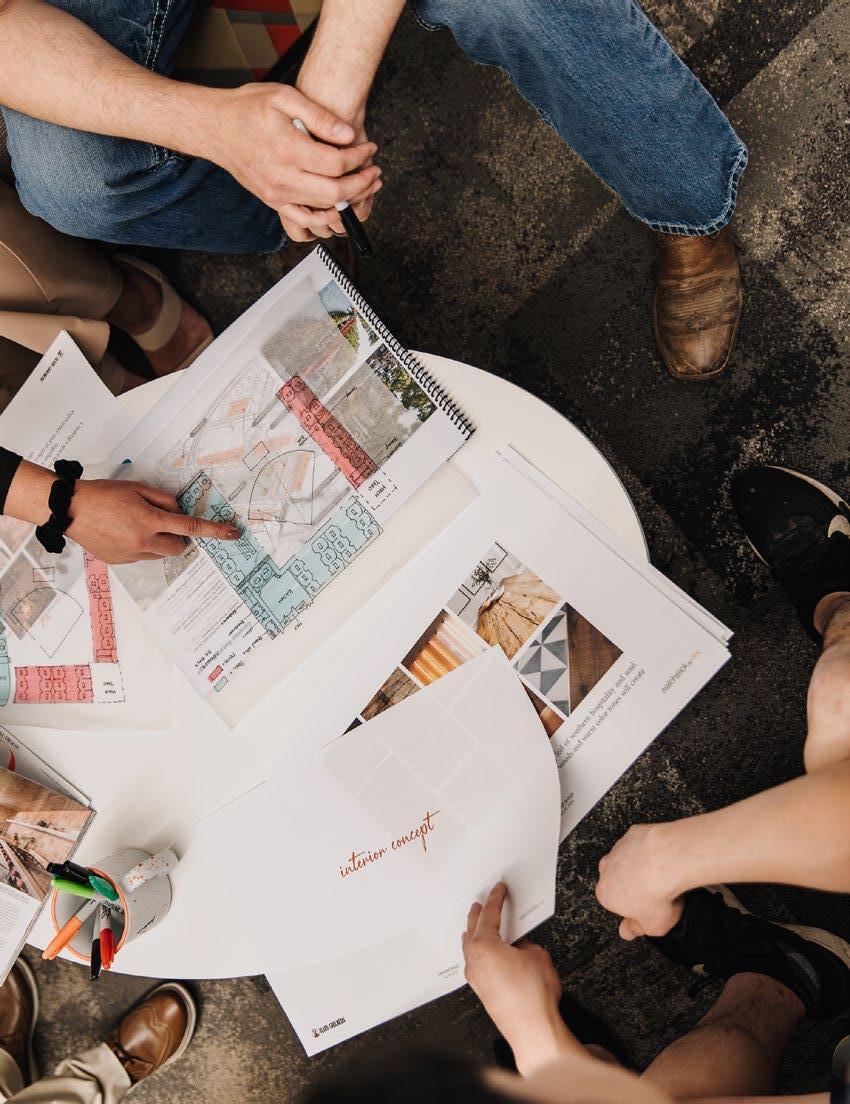
At HFA, we unite the expertise of our multi-discipline team of architects, engineers, permitters, and other industry professionals, so you can:
+ Maximize coordination across disciplines
+ Streamline communications and gather feedback earlier
+ Create higher quality documents that can be delivered sooner
fully integrated disciplines
Architecture
Electrical Engineering
Fire Protection Engineering
Civil Engineering
Landscape Architecture
Fueling Design
Mechanical Engineering
Plumbing Engineering
Structural Engineering
Interior Architecture
Refrigeration
Commissioning
Energy Modeling



Technology + Collaboration
Our collaborative processes are supported by advanced technologies. All disciplines work in the same Revit models, updated in real time, thus allowing the entire team access to detailed project information at different stages before, during, and after construction.
We continue to use and expand on Autodesk BIM 360. The software drastically improves efficiency by allowing the client, project team and other stakeholders to work together on one model in the cloud. It reduces changes later in the project to coordinate and manage project data and designs.
More, Better, Quicker
HFA quickly and efficiently iterates through design changes and options through advanced techology in software and hardware. The client benefits due to frequent communication and difffering views. A collaborated multi-discipline BIM model enables swift moves from one type of visualization service to another while keeping the cost of services low.
HFA, BIM + Revit
Since 2007, HFA has been using Revit on projects. The multi-disciplinary staff at HFA is competent in Revit and training sessions and helpful tips are available to them each week to help refine their skills. This ensures that the teams at HFA will utilize Revit to produce models that are consistent in quality and accuracy. To continue to stay current, some staff members attend conferences such as Autodesk University to learn and apply the latest in the design and construction industry.
Project Team
Architecture
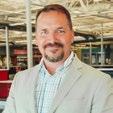
Marc Jennings Vice President of Industrial + Logistics

Read Industrial + Logistics Sr Lead / Architect
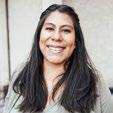

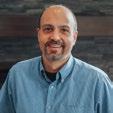
ROBOTICS INTEGRATION SPECIALIST ARCHITECTURE LEAD, LEED AP BD +C
MEP Engineering

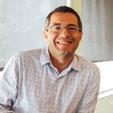
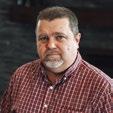
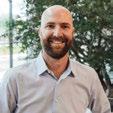
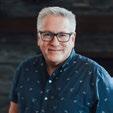
Barry
Andrew Akerhielm Sr Architect / Client Lead
James Harte Team Lead / Architect
Daniela Villagran Team Lead / Architect
Greg Schluterman Sr Vice President
Jaime Castañeda MEP Program Lead / Electrical Engineer
John Mullins Sr Mechanical Engineer
Rob Couts Sr Electrical Designer / Client Lead
Tim McCabe Team Lead / Electrical Engineer
Refrigeration + Commissioning + FP Engineering

Miguel Purdy Discipline Lead / Sr Refrigeration Engineer

Martin Khallaf Commissioning Discipline Lead
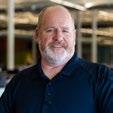
Gary Sims Sr Fire Protection Designer
Structural Engineering + Client Partnerships

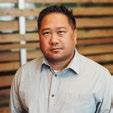
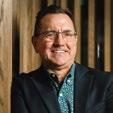
Ed
Sr Client Partnerships Lead

Lungshen Tsao Sr Structural Engineer
Giancarlo Botazzi Vice President
Damphousse
Project Team

Marc Jennings, ncarb
Vice President of Industrial + Logistics
Education
Bachelor of Architecture, University of Texas at Arlington, 1999
Registration Licensed in TX
Marc Jennings is the Vice President of Logistics at HFA. Jennings brings more than 25 years of industry experience to his role within the architecture, construction, and development community in the Dallas/ Fort Worth Metro. He recently joined HFA to help grow our Industrial and Logistics programs and to help lead the Fort Worth studio. Jennings is an empathetic problem solver at heart. He loves to build and maintain lasting client partnerships by putting himself in their shoes, always keeping their best interests at the forefront of his solutions-based approach to design and development. Jennings is a licensed architect in the state of Texas.
Client Varied JLL Aldi FedEx Scope
Industrial (cold storage, manufacturing, distribution), logistics, office, medical, and retail projects (new + remodel)
Role: Architect
~30 major QSR + food processing remodel projects per year
Role: Development Manager
30+ retail and distribution center remodels with cooler/freezer relocations and expansions
Role: Construction Manager
Authored, implemented, and executed plan for 1,000+ minor remodels over 18 months
Role: Architect + Project Manager
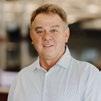
Barry Read, aia
Industrial + Logistics Sr Lead / Architect
Education
Bachelor of Science, Architecture, University of Texas at Arlington, 1982
Registration
Licensed in TX
Barry has an extensive background in Design/Build and Design/Bid/Build projects for the public and private sector facilities. Public sector projects include federal, state, and municipal projects, including the Department of Defense (DoD), State Department, Army Corps of Engineers (USACOE), Veterans Administration (VA), General Services Agency (GSA), State of Texas, and several city projects. Private sector projects include food service, retail, office, medical, maintenance facilities, distribution centers, and industrial building types. He has also provided architectural and project management services for the aviation industry, sports stadiums, national and state veteran’s cemeteries, and municipal water and sewer treatment plants.
Client Walmart
Haliburton
DeCA Scope
Multiple and ongoing Distribution Center remodel and conversions into full automated storage and retrieval systems (ASRS) facilities.
Design of several Halliburton Field Camps which included all services required to maintain equipment used in oil well exploration. Some of the facilities included in the field camps are; materials testing laboratory, administration office building, truck maintenance facility, truck wash facility, chemical storage facility, sand plant, cement mixing facility, and explosives loading facility totaling more than 260,000 square foot of buildings on approximately 150-acre sites.
Design of numerous facilities for Defense Commissary Agency (DeCA) containing insulated storage rooms for both refrigerated and frozen food storage and processing.


Daniela Villagran
Team
Lead / Architect
Education
Bachelor’s Degree in Architecture, Instituto Tecnologico de Estudios Superiores de Monterrey (ITESM), 2019
Daniela Villagran is an experienced architect with six years of industry experience. Throughout her career, she has worked on a variety of projects, including industrial, advanced manufacturing, distribution centers, retail, and office buildings in the US, Canada, and Mexico. Daniela has proven her leadership skills by successfully leading a team of 12 members and providing quality control for construction documents. Currently, she holds the position of Team Lead at HFA. Daniela’s strong communication, problem-solving, teamwork, planning, and resiliency skills make her a valuable asset to any project. She has also achieved significant accomplishments, such as managing and ensuring the quality of production teams for large-scale advanced manufacturing buildings and collaborating with teams across different locations to establish and update company standards. Above all, Daniela takes pride in being a part of a team with genuine intentions and strong values.
Client
JD Sports (Rollout Retail) - Several Locations
Amazon (Slingshot)Alberta
Scope
Creation and implementation of Revit template for rollout stores. Sports apparel stores including racks fixed to ceiling and walls. Back of house included restroom and office area, as well as storage.
Construction Documents and Design Bulletins. Automated 5 story pre-cast warehouse sortation facility with implementation of the Amazon Robotic Sortation Center (ARSC). 2.9 million square foot building, including office and training areas. Stair towers and elevators on the sides of the warehouse allowed for a planned and well distributed circulation for packages, equipment and people.
Costco - Morriston Warehouse Target
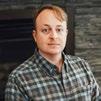
Construction Documents, Design Addenda and Construction Administration. PEMB warehouse facility of 1 million square feet with tilt-up panels in the docking areas. Building includes restroom areas along the perimeter of the building as well as office and fitness areas.
Construction Documents. Tilt-up distribution center with office area covering 1.2 million square feet, along with IMP maintenance buildings, guardhouses and pump house distributed throughout the property servicing the distribution center.
James Harte is a licensed Architect with a diverse background in construction. He brings more than 15 years of various experiences within the construction and A+E industry to his role at HFA. In his capacity as a leader for the Automation wing of the Logistics Team, James manages a multi-million-dollar client and leads a multi-disciplined team in all aspects of the design process from inception to realization.
Client Walmart
Education
Bachelor’s Degree in Architecture, Virginia Tech, 2007
Registration
Licensed in VA
Division of Consolidated Laboratories
SVEC
Department of Corrections (VA)
Scope
Architect & Client Lead for multiple ongoing distribution center ASRS retrofits (many of them 1M+ SF). Scope includes design, code analysis (and authoring in some cases), vendor coordination.
BSL4 infectious disease research facility, BSL3 infections airborne toxins facility, BSL3 server room.
Industrial truck maintenance garage facility.
Master planned & design for 100K SF multi-building dairy facility.
Team Lead / Architect
James Harte, aia, ncarb
Project Team

Andrew Akerhielm, aia, ncarb, leed ap bd+c
Sr Architect / Client Lead
Education
B.S. in Architecture, University of Texas at Arlington, 2001
Master of Architecture, University of Texas at Arlington, 2003
Registration
Licensed in AR, CA, CO, FL, GA, HI, KS, KY, LA, MA, MN, MO, NE, NJ, NM, NV, ND, SC, TN, TX, UT and WA
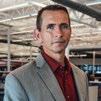
Greg Schluterman, pe, leed ap bd+c, cxa, ashrae beap + bemp
Sr Vice President
Education
Bachelor of Science in Biological Engineering, University of Arkansas, 1999
Masters in Mechanical Engineering, University of Arkansas, 2002
Registration
Licensed in all states except AL, AK, HI, ID, IN, IA, NE, NH, NM, ND, OH, SD, VT, WI, WY
Andrew is a highly creative, results-driven Senior Architect with more than 20 years of experience within the industry. He is also a Team Lead and has a strong client satisfaction record across various projects, including commercial, office, retail, and industrial projects. He manages a multi-million dollar per year client and leads a multi-disciplined team during all phases of design, including site surveys, space planning, design development, construction documents, and construction administration.
Client
Haliburton
Milk Processing Facility
Scope
Industrial projects including Operations Buildings, Truck Shops, Truck Washes, Bulk Cement Plants, & Sand Plants. Projects included Halliburton’s largest ever new field camp that consisted of multiple buildings on a 150-acre site.
Logistics design for inbound raw milk from dairies and outbound distribution to stores. Manufacturing design of high-bay facility for pasteurizing, testing, additives, onsite milk container fabrication, bottling, and ASRS for palletization.
Optimal Manufacturing Facility
Relocation of existing facility to optimize layout and add additional equipment lines for precision optical components and testing.
As a Vice President, Greg provides 18 years of industry experience and mentorship to the people at HFA. He is dedicated to making each individual stronger and helping them achieve their goals as well as the goals of the company. Greg oversees the mechanical, electrical, commissioning, and refrigeration teams and is a registered Professional Mechanical Engineer in 36 states. He oversees several national accounts ranging from ground-up construction to remodels. He is a LEED Accredited Professional, Certified Building Energy Auditing Professional, Certified Building Modeling Professional, and a Certified Commissioning Authority (CxA) established by the Associate Air Balance Council (AABC). Greg is currently a voting member for ASHRAE 90.1 Energy Cost Budget Subcommittee and assists with fundraising efforts for his local ASHRAE chapter.
Client
OK Foods Walmart Target Culinary + Innovation Center
Scope
Various locations, food processing plants. Mechanical work ranging from designing steam boiler plant and thermal process piping to space pressurization.
DC ASRS scopes serving as EOR on air compressor tank farm designs to handle robotic equipment as well as design of the of the fire sprinkler systems.
Design guidelines for DC conversion including the addition of ~ 100,000 SF freezer space and medium voltage switchgear.
13,000 SF kitchen testing facility overseeing mechanical + plumbing design for the project.


Jaime Castañeda, pe
MEP Program Lead / Electrical Engineer
Education
B.S. in Electrical Engineering, John Brown University, 2000
Registration
Licensed in all states except AK, HI, IA, ID, KY, ME, MT, ND, NH, SD, UT, VT, WY Client Frito Lay NWA Food Bank

Miguel Purdy, pe
Discipline Lead / Sr Refrigeration Engineer
Education
Bachelor in Science in Agricultural Engineering, University of Arkansas, 1986
Registration
Licensed in AR, AZ, GA, IA, ID, IL, IN, KY, LA, MN, MS, NC, ND, NV, NY, OH, OK, SC, SD, TX, WI, WV
Lead Electrical Engineer for design of indoor substation that included a 2500kVA transformer and a 3000A 480V draw-out style switchgear lineup with Arc Flash reduction for safety and transformer bushing monitoring system for reliability improvements at the Frito Lay Scoops production lines.
80,000 SF, two story food distribution, cold storage and processing with supporting offices and community center with commercial kitchen services. Project included standby generator.
Distribution Center remodel conversions into full ASRS facilities including large electrical service upgrades at 480V and 208V to serve MHE equipment and include MW scale UPS systems for backup of Critical Operations.
Miguel has more than 30 years of project management, mechanical design development, and schematic design of refrigeration systems for new buildings and remodels of existing structures in commercial, food processing, and manufacturing spaces. His knowledge of building and process mechanical systems, including design, operation, installation, and energy usage, allows HFA to provide owners with solutions meeting varying parameters while using his experience to help owners better define the needs of their facility.
Jaime brings 20 years of experience to HFA in lighting design, power distribution, short circuit analysis, voltage drop analysis, load diversity, life safety, and communication systems, and design of backup emergency and critical power systems. Jaime is responsible for various commercial facilities’ electrical design, including retail, grocery, maintenance, and manufacturing, healthcare, industrial and storage facilities. Jaime’s primary roles at HFA include responsibility for accuracy, constructability, code compliance of overall electrical designs and calculations, and electrical staff training. Client Hudson Foods
Design and Project Management for poultry slaughter, further processing, and distribution freezer projects at the company’s 7 production facilities.
Provided mechanical, piping, plumbing and refrigeration services at multiple facilities, including 1 ASRS distribution project. Projects ranged from small remodels to full plant redesigns with all services coordinated.
Provided full mechanical, piping, plumbing and refrigeration design for a new 3,000 head/day $110M slaughter facility.
Project Team
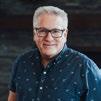
John Mullins, pe
Sr Mechanical Engineer
Education
B.S. in Aerospace Engineering, Texas A&M University, 1980
Graduate studies, Business College, Texas A&M University, 1981-1982
Registration
Licensed in CA, IN, MN, MT, OK, SC, TX
John Mullins is a Senior Mechanical Engineer at HFA. He brings more than 25 years of mechanical systems design experience to his role and has worked in the commercial, industrial, military, and institutional facility industries. John is a licensed professional engineer and is proud of his proficiencies in HVAC design, energy analysis, hydronic piping and air systems design, fuel gas and compressed air systems, project management, and construction administration and management. He supports several teams and programs at HFA, acting as a technical resource who monitors a project’s process and performs quality control. He also assists with proposal development and training for fellow mechanical engineers throughout the studio.
Client Aldi Publix
Tyson Foods
Mrs. Baird’s Bakery
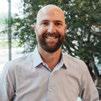
Team Lead / Electrical Engineer Tim McCabe, pe, leed ap
Multiple new 500K SF DC’s/warehouses. Projects included offices, ~100 dock positions, dry, refrigerated, and freezer storage.
Frozen Food DC. Mechanical and Plumbing design for 200K SF frozen food distribution center. The building was a single-story (75-foot-tall) ASRS rack supported IMP wall structure.
DC & processing plant renovation. Project design accounted for new 10,000 lbs. per hour production lines, upgrades to ammonia refrigeration systems, and upgrades to all plant utilities.
Served as Mechanical Engineer for HVAC design for new bread plant, vehicle maintenance facility and corporate offices.
Tim McCabe is the Team Lead for the Industrial and Logistics MEP team at HFA. Tim brings more than 16 years of industry experience on projects spanning various markets such as industrial, logistics, horticulture, retail, EV charging, municipal, education, and hospitality, among others. A large part of his role includes coordination and management between internal teams, external departments and clients, as well as electrical design for his projects. He is passionate about engineering and lighting design, and prides himself in his ability to create strong cross-discipline relationships among his teams and with his clients.
Client
NWA Food Bank
Walmart
Target Scope
80,000 square foot food distribution facility including cold storage, frozen storage, dry storage, refrigerated and dry docks, office, conference, and community spaces.
Various existing distribution center retrofit projects including electrical infrastructure, robotic and mechanical material handling, security upgrades, and employee office remodels.
Various existing distribution center retrofit projects including electrical infrastructure, employee office/break area remodels, truck trailer maintenance and parking upgrades, as well as prototype development.

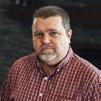
Rob Couts, ei
Sr Electrical Designer / Client Lead
Education
Bachelor of Science Degree in Electrical Engineering, John Brown University, 1995
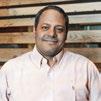
Martin Khallaf, pe, cem, cbcp, cxa, ccp
Commissioning Discipline Lead
Education
Bachelor of Science in Mechanical Engineering, Ain Shams University, 2006
Registration
Licensed in CA, NJ, NY, TX
Rob Couts is Senior Electrical Designer/Client Lead at HFA. With more than 27 years of experience, Rob understands the ins and outs of retail electrical engineering, from remodels to new ground up projects. His knowledge of automation applications is also vital to our growing involvement in retail distribution centers and micro-fulfillment centers.
Client
Walmart MFC Program Scope
Design of DC remodel conversions into full ASRS facilities utilizing Symbotics warehouse automation systems. Scopes also typically include large electrical service upgrades and heavy coordination with local utility providers for MW scale services.
Electrical design for 40,000 SF MFC (micro fulfillment center) cold storage ASRS environment. Project involved a utility service upgrade for entire facility to support MFC operations. Project also included a drone delivery system for selective items to customers.
Martin Khallaf is an accomplished mechanical engineer with 18 years of experience in the design, commissioning, and optimization of commercial building MEP (Mechanical, Electrical, and Plumbing) systems. As the leader of the Energy and Commissioning discipline, Martin oversees the strategic direction and execution of energy efficiency and commissioning initiatives across various projects. His expertise spans building automation, energy management, and commissioning, with a particular focus on driving innovation and improving building performance.
Throughout his career, Martin has been deeply involved in projects that emphasize sustainable design and energy efficiency. He is passionate about collaborating with teams to find innovative solutions that enhance building performance while reducing environmental impact. His work has helped clients optimize energy use and ensure that MEP systems are functioning at peak efficiency.
Client
Whisper Valley
Bristol Myers
Port Authority
World Trade Center
Transportation Hub
Port Authority
Vehicular Security Center
Social Security Administration Building
Scope
Supervised the design of the Geothermal infrastructure of the community to verify it provides the required capacity. Recommended system modifications to ensure cooling and heating capacity is distributed properly to all the assets.
Conducted periodic site visits to check the construction process and verify all the installed equipment are in compliance with the design drawings and all the installations are in compliance with the codes.
Worked on design work and reviews and written specifications and verified they are being done per all applicable codes such as NYC Building Code, NYC Plumbing Code, NYC Mechanical Code, NYC Fuel Gas Code and NYC Energy Conservation Code.
This project had an initial construction budget of $2 billion. it is the vehicle screening center for the new built transportation hub.
This new build data center was designed to be operational 24/7 with redundancy to insure the critical loads and IT equipment in the building will never lose power even under severe circumstances.
Project Team
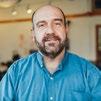
Giancarlo Botazzi, pe
Vice President
Education
B.S. in Civil Engineering, Northeastern University, 1985
Master of Science in Engineering, University of Texas, 1986
Registration
Licensed in AL, AR, CO, CT, DE, FL, GA, IN, MA, MD, ME, MI, NC, NE, NH, NJ, NY, OK, PA, RI, TN, TX, VT
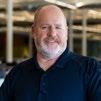
Gary Sims, et Registration
Certified by NICET in Fire Protection/ Building Systems Programs. Certification Number 89485 in:
• Water-Based Systems Layout Level III
• Special Hazards Systems Level II
• Inspection + Testing of Water-Based Systems Level I
As the Vice President of Structural Engineering at HFA, Giancarlo spearheads a dynamic team of engineers and designers, bringing nearly four decades of extensive experience in diverse building structural engineering projects across the United States. With a profound understanding of design standards and codes encompassing structural steel, concrete, precast concrete, masonry, and wood, Giancarlo is well-versed in the International Building Code (IBC) and specific state building code requirements. Giancarlo’s portfolio showcases his proficiency in designing intricate new structures and addressing challenging structural rehabilitation and renovation projects. His collaborative approach enables him to effectively partner with project design teams and building owners, devising creative and cost-efficient solutions that align with architectural design criteria and client objectives. Licensed in 23 states and Puerto Rico, Giancarlo is also an esteemed member of the National Council of Examiners for Engineering and Surveying (NCEES).
Client Chase Farms
Beacon Power
Bluefin Robotics Corp. Markley Group Scope
98,800 high bay freezer storage warehouse & DC, 28,000 square foot Processing Area, and 10,240 square foot Receiving/Loading dock area. Long span joist and joist girder roof structure & special detailing at IMP’s.
20 MW Frequency Regulation Facility, world’s first grid-scale, mission critical, continuously operating, flywheel-based energy storage plant.
54,000 SF renovation of three level facility housing engineering, manufacturing, and administrative functions for undersea robotic vessels.
Multi-tenant, mission-critical telecommunications, and data center facility.
Gary Sims is a seasoned professional with over 36 years of experience in fire suppression and protection design. Beginning his career in the contracting industry in 1989, Gary transitioned to the consulting field in 2009, bringing decades of expertise to complex fire protection projects. As a Senior Fire Protection Designer, Gary leads and supervises a three-person team, managing design work, conducting site surveys, performing water flow testing, and attending project coordination meetings.
Gary’s extensive portfolio spans small commercial developments, large industrial facilities, government and military projects, as well as international ventures. He holds multiple NICET certifications in Fire Protection/Building Systems Programs, including Water-Based Systems Layout (Level III), Special Hazards Systems (Level II), and Inspection and Testing of Water-Based Systems (Level I). His additional qualifications include OSHA 10 certification and proficiency in Revit/BIM technology, project management, and owner advocacy. With a meticulous attention to detail and a commitment to safety and efficiency, Gary continues to deliver innovative solutions to meet the unique needs of his clients.
Client Walmart Distribution Centers
Truckworx Facillity
Sysco Scope
Buckeye, AZ | Over three-million square feet. Currently working on phase 1 of the symbotic projects. This project also includes multiple rack storage, restrooms and offices renovation work.
Birmingham, AL | Renovation of an old Home Depot style facility to be a new Truckworx location. Revamped systems to meet owner’s needs. Included office area, truck maintenance, truck wash, paint booths, sales, etc.
Cleveland, OH | New facilities for distribution and office facilities
Sr Fire Protection Designer

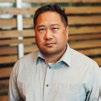
Lungshen “Tiger” Tsao,
pe, se
Sr Structural Engineer
Education
Bachelor of Science in Architectural Engineering, University of Wyoming, 1999
Registration
Licensed in all states except AK
Lungshen first obtained his Structural PE in 2004 and SE in 2012. He is a designated Model Law Structural Engineer by the National Council of Exams for Engineers and Surveyors, and a TBPE approved and TDI appointed Windstorm Special Inspector in the State of Texas. Lungshen has designed and completed building structures in the most severe site conditions across the continental US, such as in Fort Pierce, Florida (160 mph wind load); Apple Valley, California (Seismic Design Category D) and North Conway, New Hampshire (90 psf ground snow load). He has more than 19 years of diversified project experience and completed over 1500 projects in educational, religious, commercial, medical, retail, industrial, and municipal developments throughout the United States. He possesses a wide range of design knowledge on Steel, Concrete, Timber/Wood & Masonry structures. Lungshen is an expert on conventionally framed structures and several other non-traditional building systems.
Client Georgia Pacific Walmart
NWA Food Bank Scope
Structural design for 138,000 SF addition to paper goods manufacturing facility. Project featured concrete tilt-up panels, mezzanines, interior 2 story office compound, high bay structure, multiple complex connections to existing buildings, and unique loading associated with roof mounted manufacturing equipment.
Milk Processing Facility structural design housing manufacturing, food processing, and ASRS elements.
Tilt-wall structural design for two story project featuring food distribution, cold storage and processing with supporting offices, and community center.
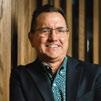
Ed
Education
Bachelor of Art in Economics, University of New Hampshire, 1987
Ed Damphousse is HFA’s Sr Client Partnerships Lead with a primary focus of identifying, developing, and maintaining long lasting client relationships. With over 30 years of direct industry experience, Ed has built his career in sales, marketing, and business development roles within the AEC Industry at local, regional, and national levels. His experience spans a wide range of market sectors including retail, mixeduse, multi-family, office/industrial and hospitality. Ed has a reputation of being a natural relationship builder and developing strong client rapport through his ongoing attention, project understanding, communications, and follow-through. Always looking out for his client’s best interests, he provides a unique understanding and perspective of how architecture and engineering ultimately supports project proformas and long-term business goals.
Ed started his career in the AEC industry with R.S Means Company, considered the industry standard in construction cost information. His national client base included some of the largest Fortune 500 companies and federal government agencies including the General Services Administration and the U.S. Tri-Services (Army/Navy/Air Force), all of which developed and managed distribution, fulfillment, and logistics property assets. He has since brought his cost engineering experience into roles within Construction Management and Architectural/Engineering Firms. Always looking out for his client’s best interests, he provides a unique understanding and perspective of how architecture and engineering ultimately support project proformas and long-term business goals.
Sr Client Partnerships Lead
Damphousse
Project Experience
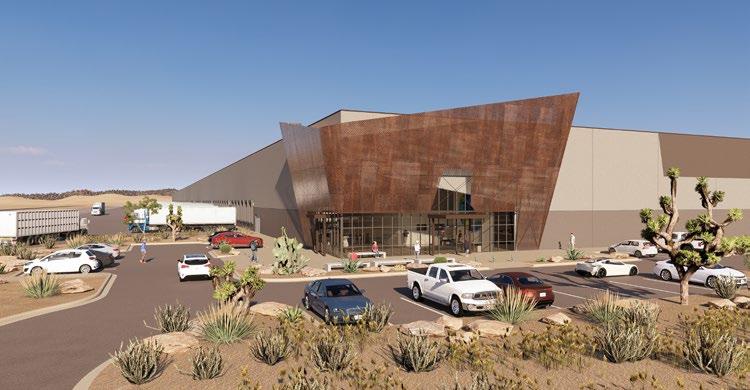
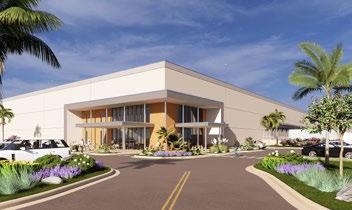
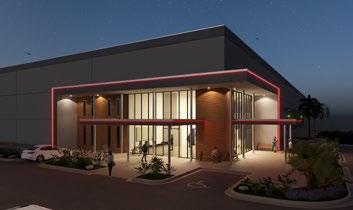
Distribution Centers
HFA developed these 1,000,000- square foot distribution center designs considering future offices, amenity spaces, ASRS-ready structural systems, and cross-dock access. Utilizing our team’s expertise, we were able to create designs for both facilities that allowed for the widest range of speculative uses based on their respective geographic locations. User considerations accounted for included traditional distribution and bulk storage, perishable goods, refrigerated and freezer storage, onsite truck maintenance operations, as well as MW scale future electrical service expansion capabilities.
Location Size Arizona | Florida
~1,000,000 Sq. Ft.

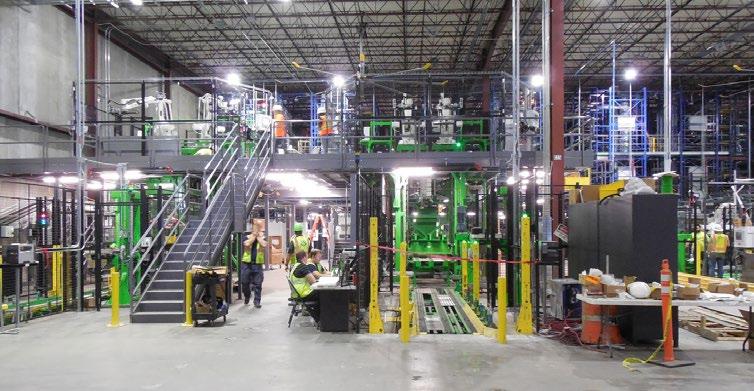
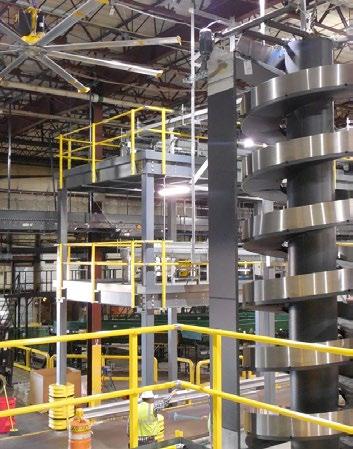
Walmart Robotics Distribution Centers
With the advent of warehouse automation systems, HFA has been able to assist the retailer revolutionize the way their warehouse operates to quickly access the product. HFA helps with the conversion of older legacy distribution centers into state-of-the-art systems that are able to store and retrieve the product using computer based algorithms that minimize the time taken with limited human intervention. The expertise that HFA has developed, has help guide retailers through this conversion with little or no downtime through a phased approach. Location Size Various + 100,000 Sq. Ft. Each
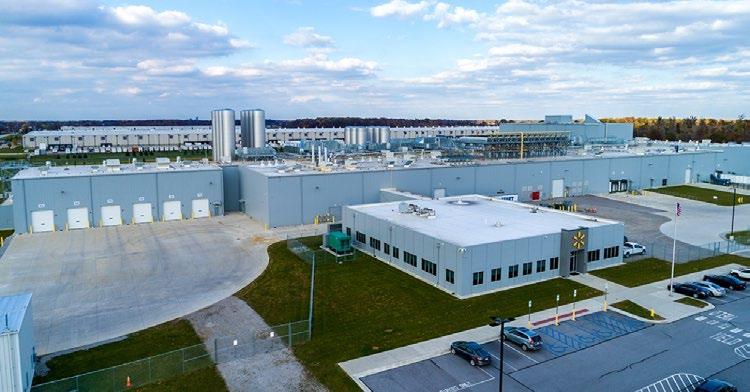
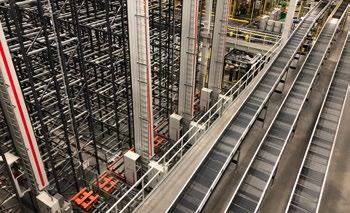
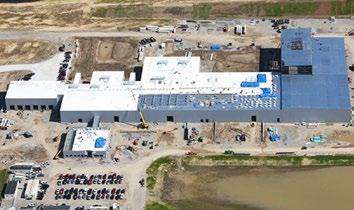
Walmart Fluid Milk Facility
Dairy facilities house one of the most highly regulated processes, requiring superbly sanitized working environment. The building design must be easy to clean in order to inhibit germ growth. The design must utilize cleanable materials with minimum flat surface areas.
• 238,720 sf with 12,000 sf administrative office building and 11,500 sf Truck Maintenance Garage with fueling island
• Six bay raw milk receiving 60 trucks daily processing 2 million gallons per week
• 25,000 sf cooler storage with 69,600 cubic feet of Automatic Storage Retrieval System (ASRS) with 12 bays of distribution
• Constructed of structural steel frame and metal bar joists; envelope and interior partitions of Insulated Metal Panels.
Location Size Fort Wayne, IN
238,720 Sq. Ft.

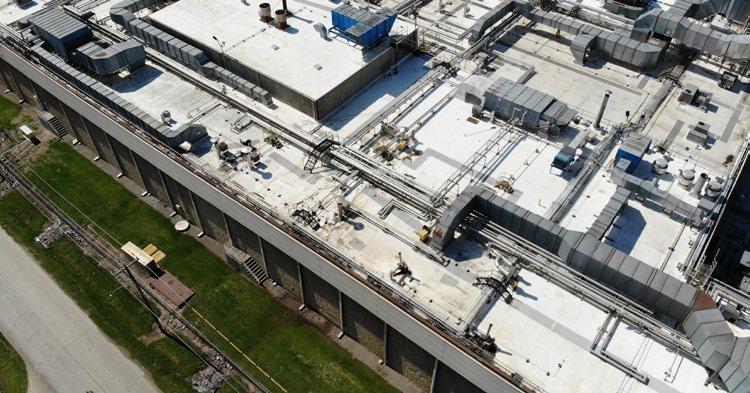
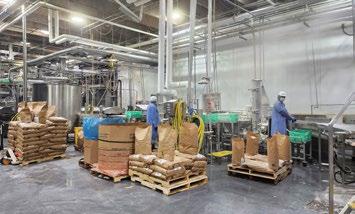
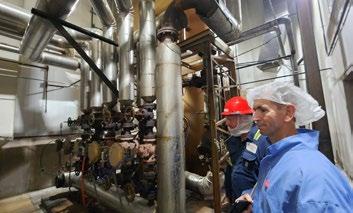
OK Foods
HFA designed for a Spiral Freezer Replacement, where a completed Mass Energy Balance was needed to verify existing capacity for the compressors and condensers.
In addition, at numerous OK Foods sites HFA designed the emergency ventilation system and control sequence to bring the existing machinery room into compliance.
Location Size Various Various
Project Experience

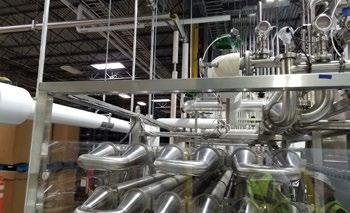

Nestle Waters
Utility systems design project that started in Fall of 2018 that was split into two phases.
Phase one: product line expansion for an added a pasteurizer to accommodate new product distribution.
Phase two: system design expansions adding a boiler and a CIP unit which are now under construction.
Location Size Dallas, TX
238,720 Sq. Ft.

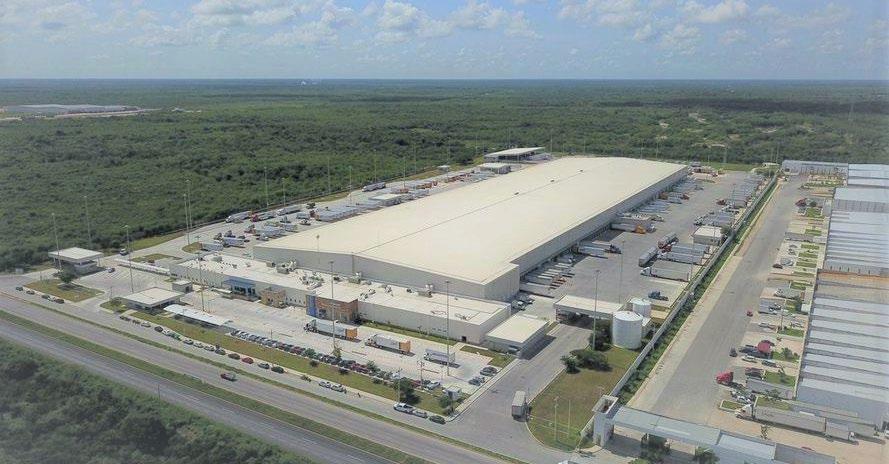
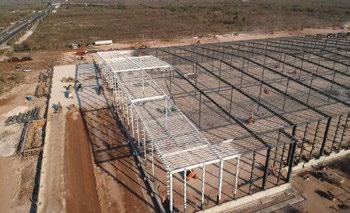
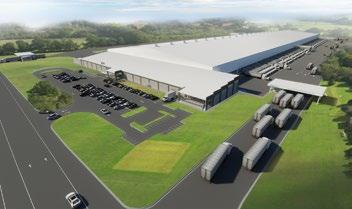
Walmart CEDIS
The warehouse has 178 dock doors for shipping and receiving included 9 devoted to smaller delivery trucks. At the entrance side of the warehouse is an office, administration, training, conference, cafeteria and kitchen area of over 37,500 square feet. Ancillary buildings include truck maintenance, pallet and wrapping storage, fueling, truck scales, a separate hazardous storage enclosure.
Due to the location, the facility will provide on-site utilities including storm sewer, sanitary sewer, fire protection water, domestic water, potable water with associated storage tanks and pump stations and an on-site electrical substation with a 10MW emergency plant capable of supporting the entire site in the event of a power outage.
Location Size Baja California, Mexico
500,000 Sq. Ft.
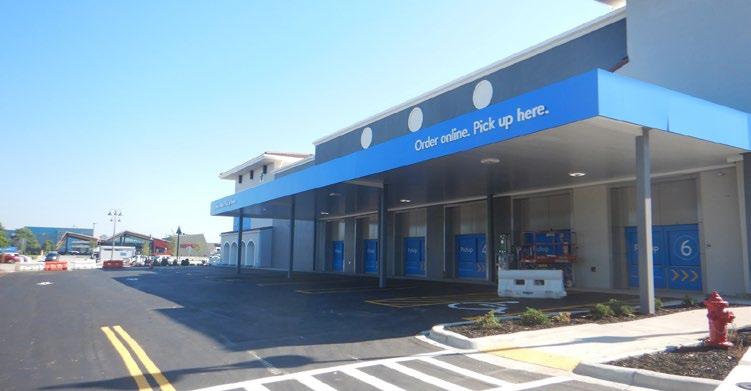

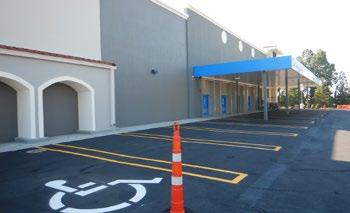
Walmart MicroFulfillment Centers
HFA partnered with Walmart to design, construct, and launch automated Micro-Fulfillment Centers (MFCs) in existing U.S. stores.
We utilized our architectural, structural, mechanical, electrical, plumbing, and refrigeration disciplines, and coordinated with Walmart’s designated vendors for automation, refrigerated/freezer boxes, and both civil and structural engineers. We also facilitated life safety systems with each local jurisdictions’ fire marshals, providing valuable construction administration expertise.

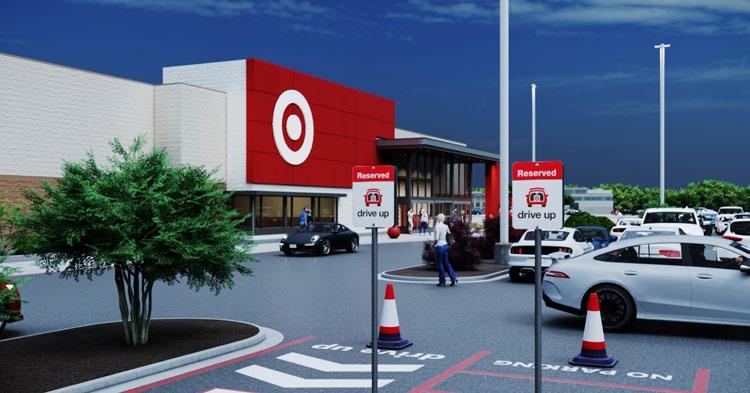
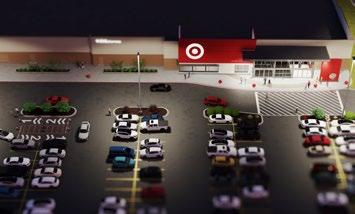
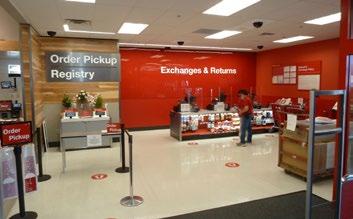
Target MicroFulfillment Centers
HFA is partnering with Target to help implement a new strategy in several stores to better accommodate online pickup area(s). Improvements include: new cooler and freezers at pickup storage areas to house refrigerated online order items, new exterior updates, online pickup brand signage, new/expanding exterior pickup doors for team members, and high-volume structural storage racks and sprinkler design upgrades in pickup areas.
Location
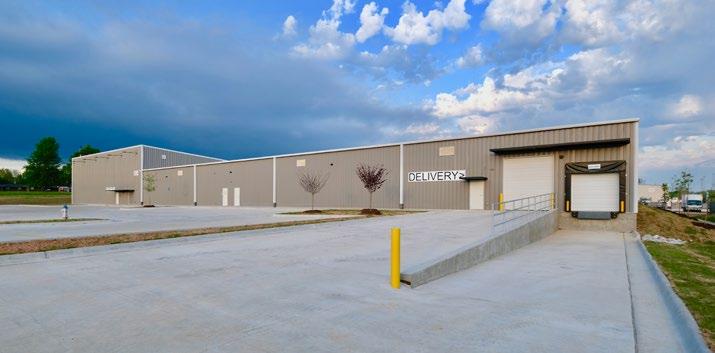
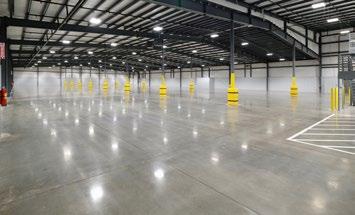
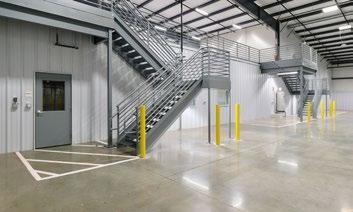
Arkie Lures
What started out with $30, a lard bucket full of tire weights and an idea in the early 1960’s has now transformed into the company today known as Arkie Lures Inc.. Founded by Bob Carnes, Arkie Lures soon revolutionized the Bass Jig market into what it is today. For over 50 years, Arkie Lures was housed in a facility just as old.
The business recently moved into an up-to-date, modern facility with high design and functionality. This 45,000 square foot, preengineered structure houses the corporate offices for Arkie Lures as well as a storage mezzanine, production area, warehouse and distribution capabilities. Attention to detail and intended use was our design directive which was achieved by taking advantage of every square inch as well as using the large front façade as a “billboard” for company signage.
Location Size Bentonville, AR
45,000 Sq. Ft.

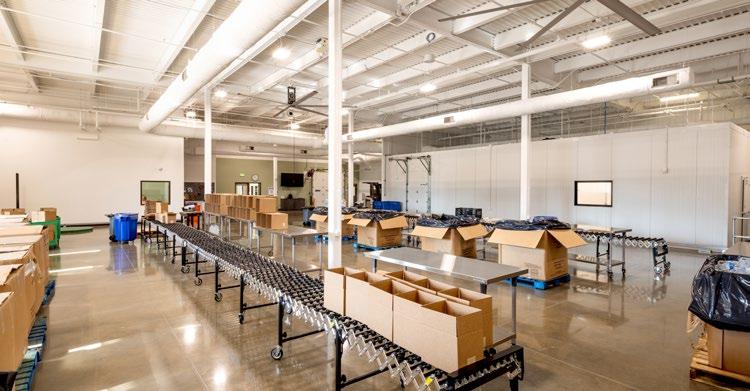

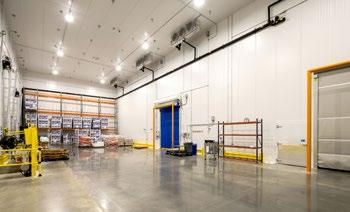
NWA Food Bank
HFA developed multiple space planning diagrams to establish options for building configurations for a new 80,000 sq.ft. food distribution, office and community center facility that includes refrigerated dock and cold storage operations. HFA architects and engineering team toured other food bank projects in Texas to assess future needs of the NWA Food Bank in conjunction with planning goals and objectives. The project team used SiteOps to analyze a number of site location options to determine the most optimum site and site development costs.
Location Size Northwest Arkansas

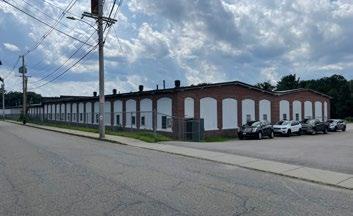
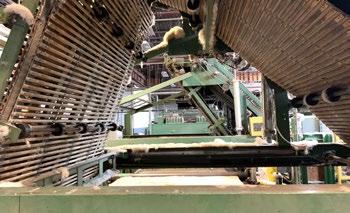
Franklin Factory Square
Factory Square is an existing multi-building redevelopment into an industrial campus with some of its original structures built in the early 1900’s. HFA has been working with the Owner since 2021 to renovate the existing buildings to meet the demands of new manufacturing and warehouse tenants. HFA’s architectural and structural teams have been heavily involved in diligent evaluations of the existing structures and implementation of new details and repairs to bring the structures up to compliance with current building codes while maintaining their historic design intent.

Cold Storage
Having Refrigeration Design In-House Improves Project Coordination
For consistency of standards, HFA internal refrigeration team works with our clients when required to make certain they meet functional requirements.
With 50+ years of refrigeration project experience, our refrigeration team has experience in a wide range of project types, including:
• Critical Cold Storage Facilities
• Food Manufacturing
• Food Distribution
• Grocery Stores
• Convenience Stores
• Restaurants
HFA’s Refrigeration Team Offers System Design + Analysis of Existing Systems Including:
• Full Service Engineering
• Complete Walk-in Coolers & Freezer Design
• Complete Large-scale Cooler & Freezer Design
• Block Flow Diagrams
• Commercial Refrigeration and Controls System Design
• Industrial Performance Criteria Package
• PSM Audit & Design
• Existing System Evaluations
• Troubleshooting
• Functional Performance Testing
Additional Refrigeration Projects
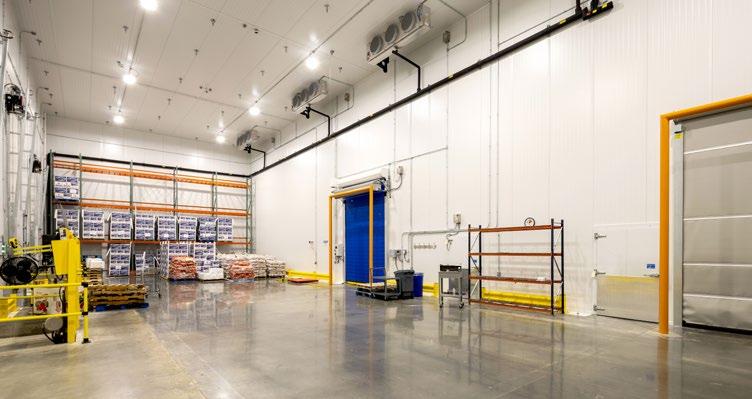
Project + Location
*Aldi DC’s + Stores (Architectural)
Mulitple Locations
NWA Foodbank (Electrical) Lowell, AR
*Hudson Foods (Refrigeration
Multiple Locations
*Tyson Foods (Refrigeration)
Multiple Locations
Description
30+ retail and distribution center remodels with cooler/freezer relocations and expansions.
Two story food distribution, cold storage and processing with supporting offices and community center with commercial kitchen services. Project included standby generator.
Design and Project Management for poultry slaughter, further processing, and distribution freezer projects at the company’s 7 production facilities.
Provided mechanical, piping, plumbing and refrigeration services at multiple facilities, including 1 ASRS distribution project. Projects ranged from small remodels to full plant redesigns with all services coordinated.
*Smithfield Beef (Refrigeration)
Location Withheld
Various MFC Programs (Fire Protection)
Multiple Locations
*Aldi DC’s (Mechanical)
Multiple Locations
*Publix (Mechanical)
Location Withheld
*Tyson Foods (Mechanical)
Location Withheld (AR)
*Chase Farms (Structural)
Location Withheld
*Smithfield Foods (Refrigeration)
Multiple Locations

Provided full mechanical, piping, plumbing and refrigeration design for a new 3,000 head/day $110M slaughter facility.
Fire Protection design for multiple MFC (micro fulfillment centers) cold storage ASRS environments utilizing pre-action (dry pipe) and new listed antifreeze systems. Projects included the use of independent burn tests on proprietary ASRS arrangements at UL laboratories.
Multiple new 500K SF DC’s/warehouses. Projects included offices, ~100 dock positions, dry, refrigerated, and freezer storage.
Frozen Food DC. Mechanical and Plumbing design for 200K SF frozen food distribution center. The building was a single-story (75-foot-tall) ASRS rack supported IMP wall structure.
DC & processing plant renovation. Project design accounted for new 10,000 lbs. per hour production lines, upgrades to ammonia refrigeration systems, and upgrades to all plant utilities.
98,800 high bay freezer storage warehouse & DC, 28,000 square foot Processing Area, and 10,240 square foot Receiving/Loading dock area. Long span joist and joist girder roof structure & special detailing at IMP’s.
PSM specialist for multiple facilities, including maintenance on processing/ packaging/refrigeration equipment. Daily visual inspections of facilities to ensure correct operation, as well as author, trainer, and compliance for all LOTO maintenance procedures.
* Project experience from project team members while employed with other firms.
Additional Distribution Center Projects
HFA Industrial Project Map
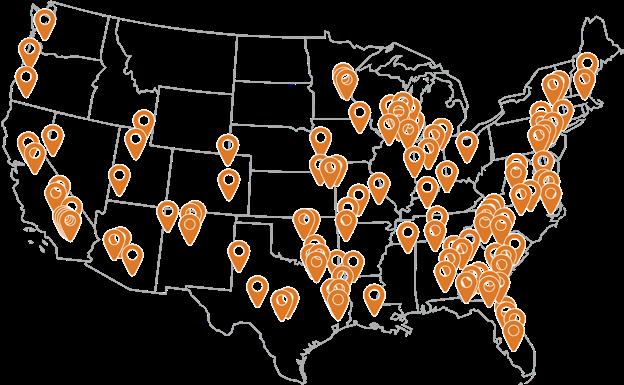
Project + Location
Walmart DC
Various Locations
Target DC
Various Locations
*Tyson Foods
Various Locations
Sam’s Club DC
Jacksonville, FL
Description
Food (with and without ASRS), perishable, and regional DC’s, as well as bulk storage. 20+ year ongoing program including greenfield, renovation, and expansion projects
Multiple and ongoing DC renovation, prototype, and new projects including designs for receive centers, flow centers, and onsite support infrastructure.
Multiple processing poultry plant remodels and additions.
~1,000,000 sq ft TI scope in new build to suit distribution center facility.
*Shopko Warehouse + Distribution Center Omaha, NE
*Randall’s - Safeway Grocery Distribution Center Expansion + Renovation Roanoke, TX
*Ben E. Keith Grocery Distribution Center San, Antonio, TX
Walgreens Distribution Center Moreno Valley, CA
*Lowe’s Regional Flatbed Distribution Center Stockton, CA
*Staples DC Terre Haute, IN
*Poland Springs Hollis, ME
*Conagra Lufkin, TX
*Toys R Us DC
Lee’s Summit, MO

New 535,000-square-foot Shopko Distribution Center on 80-acre property located in the Sarpy West Industrial Submarket of Omaha.
~37,000 SF freezer expansion at DC for groceries. Project included facilitywide Ammonia refrigeration upgrades and all infrastructure upgrades to support the expansion
Expansion involving two sides of the distribution center with project phasing allowing the distribution center to remain 100 percent operational throughout the construction process.
New 650,000 SF green field pharmaceutical DC facility with ASRS, warehouse, and office areas, a 7,000 SF truck maintenance facility, and a 2,000 SF truck wash area.
Renovation of two (2) 120,000 SF World War II-era, wood-framed buildings to serve as a flatbed DC for Lowe’s bulky building material products.
New 550,000 SF distribution center and a later 273,000 SF expansion.
Bottling Plant / Warehouse Expansion (for Nestle Waters North America). Project added 314,000 SF to the original facility.
RTE Food full facility renovation, phased, to allow continuous operation during construction.
419,000 SF product distribution center with high bay storage area, and a sophisticated materials handling and storage system.
* Project experience from project team members while employed with other firms.
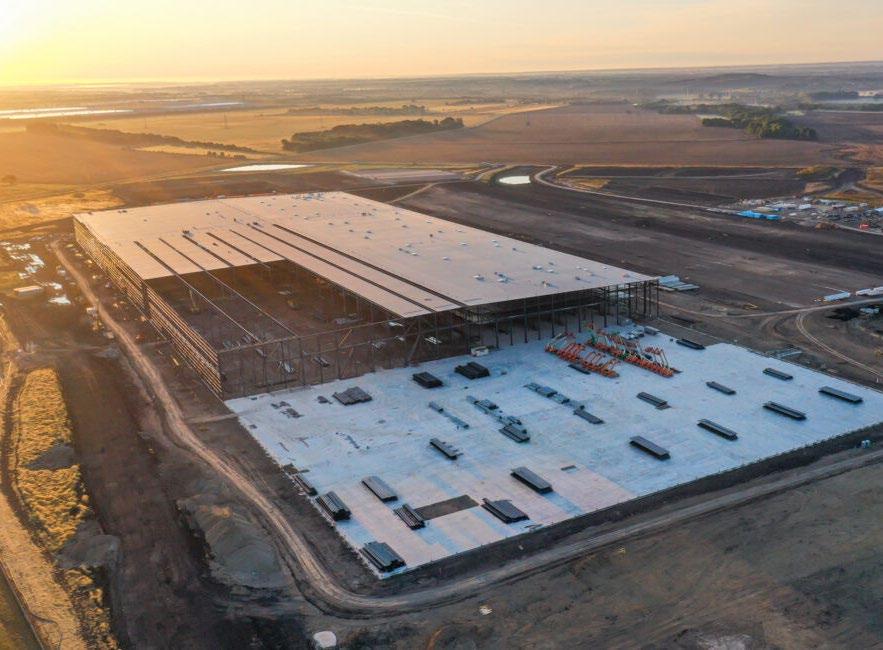
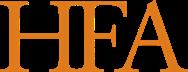