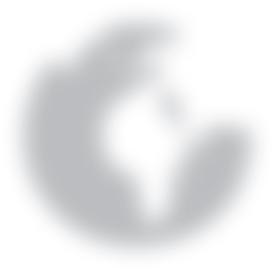



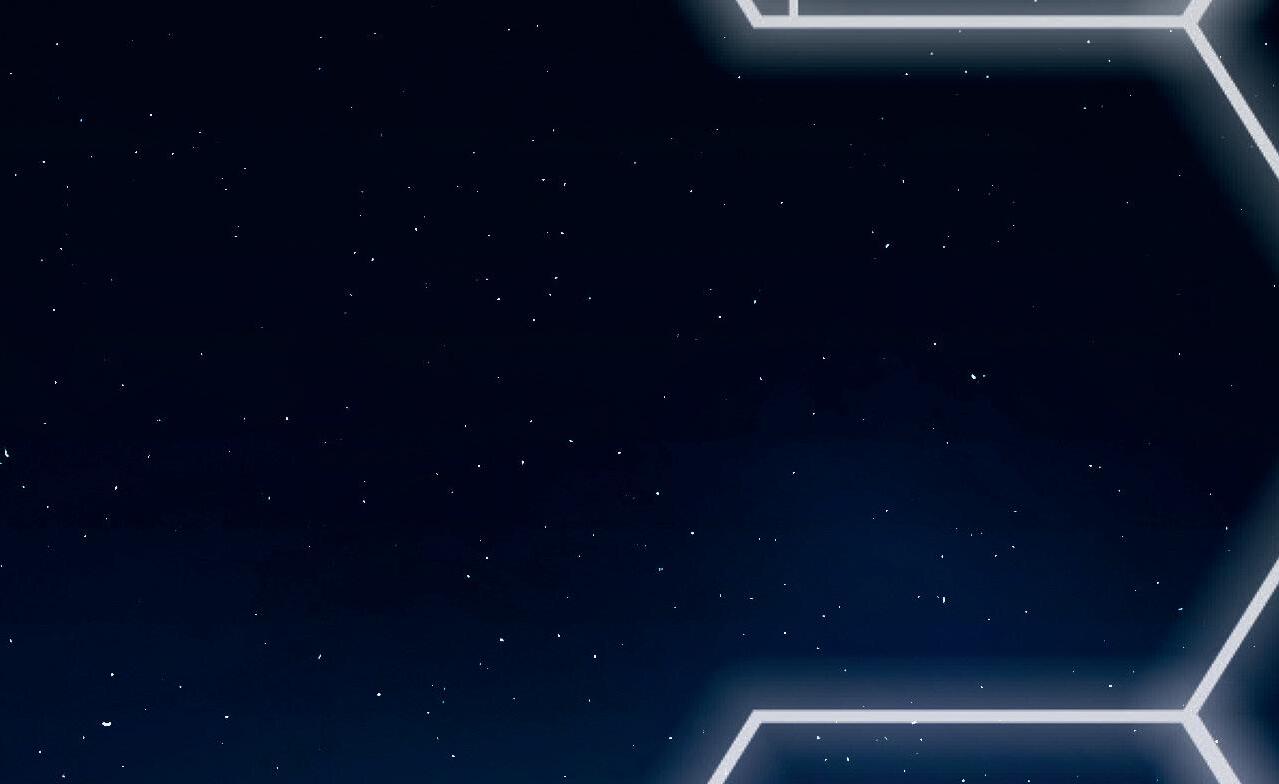

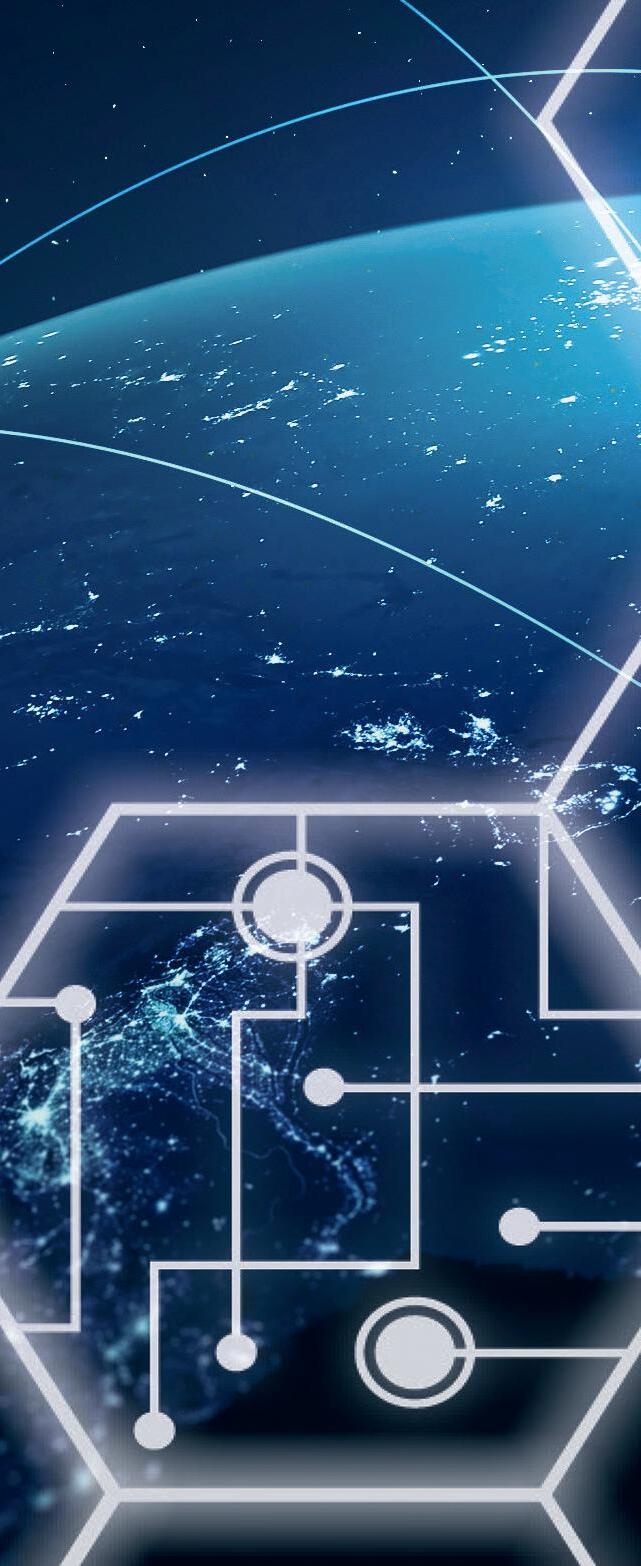
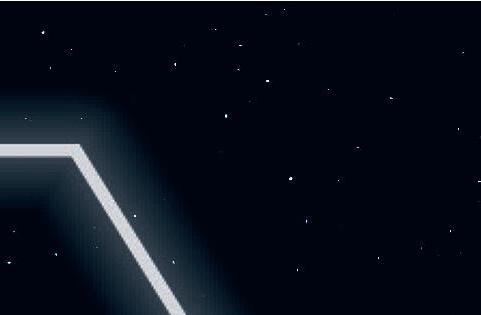
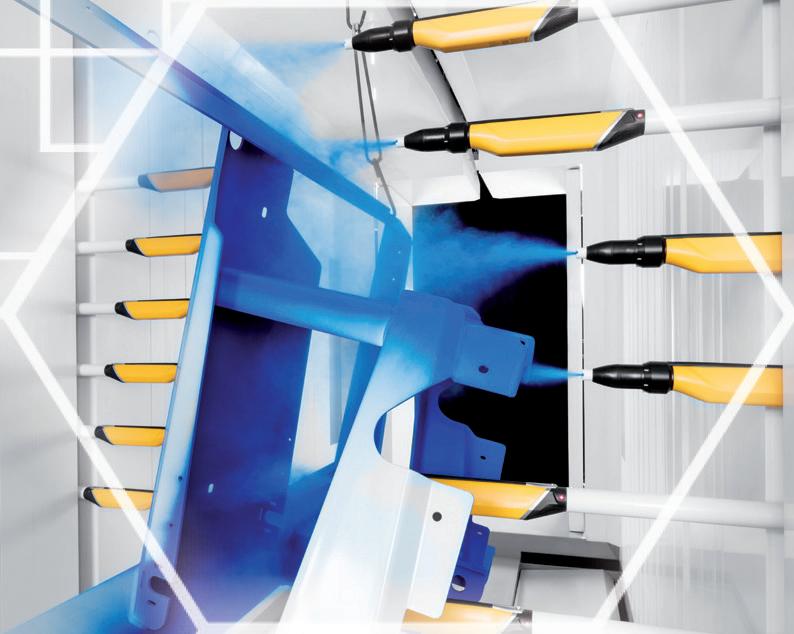
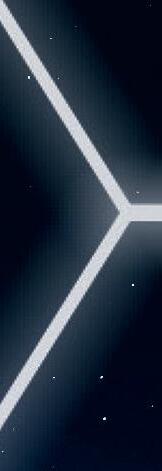
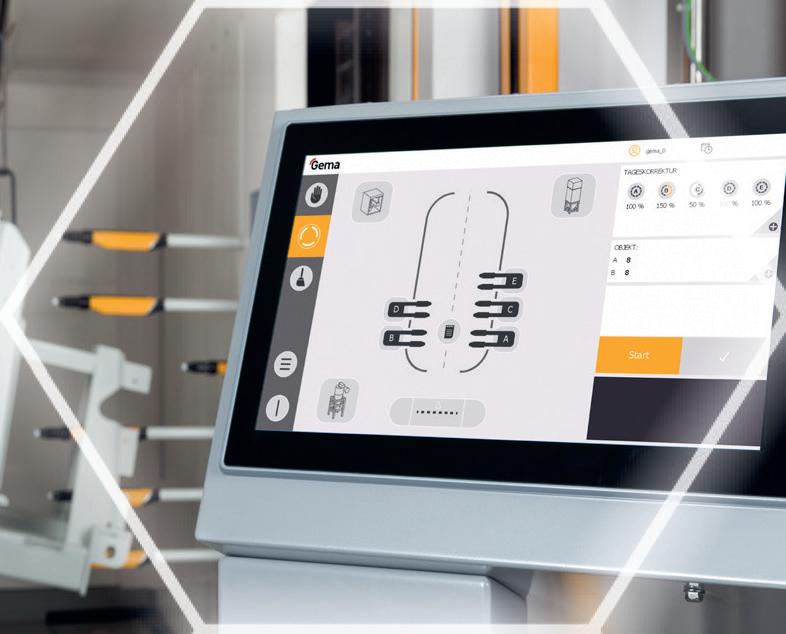
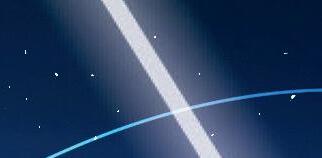
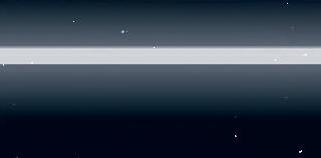
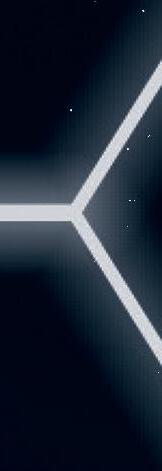

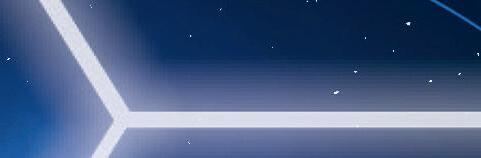
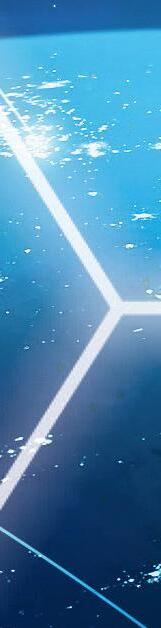
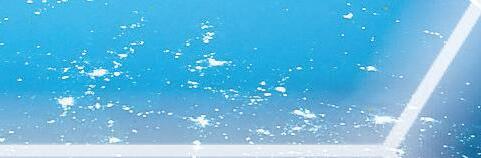
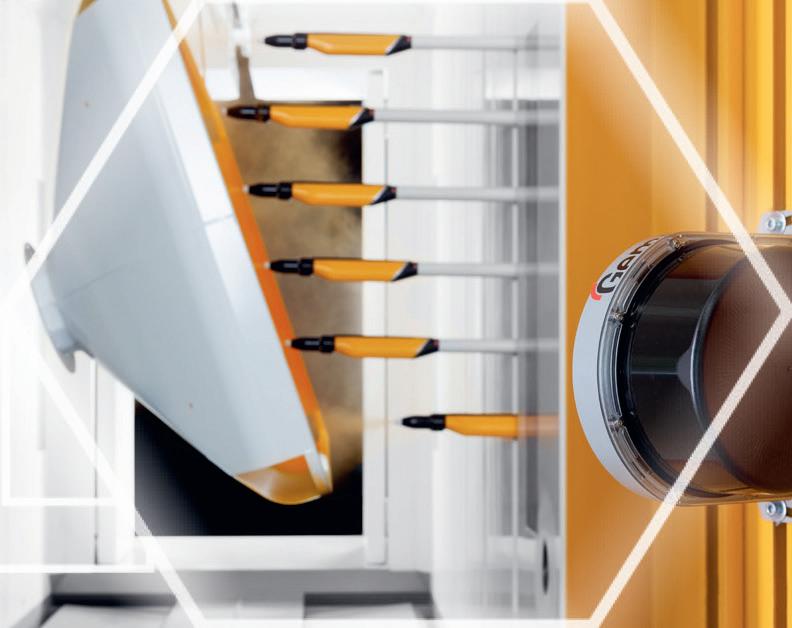
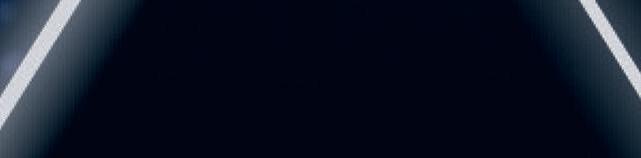
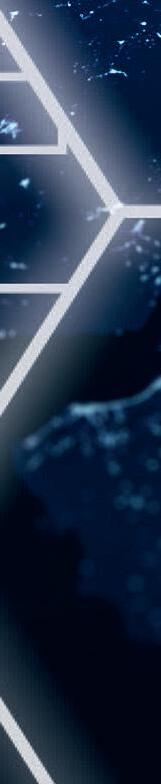
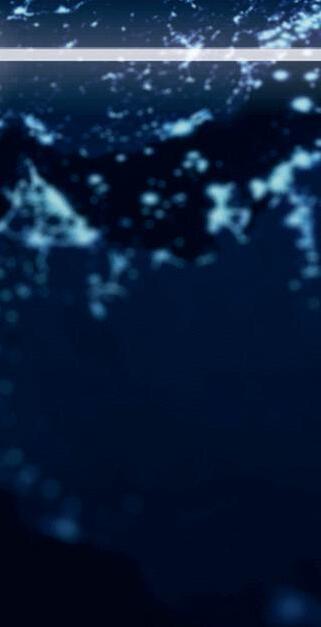
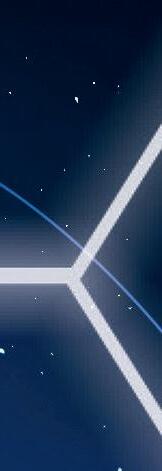

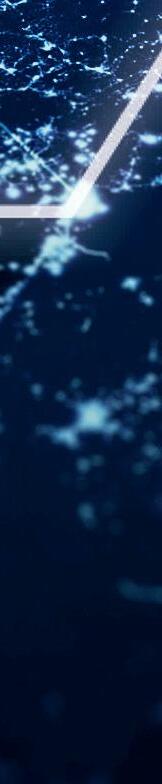
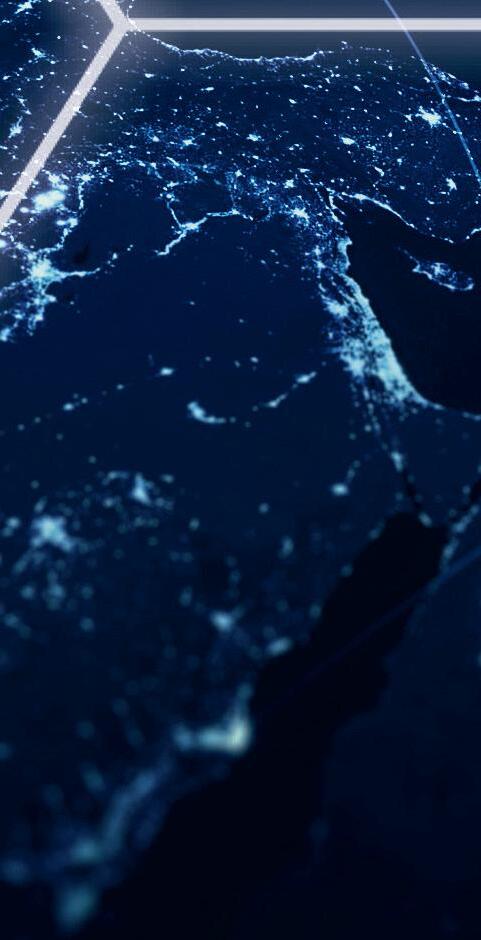
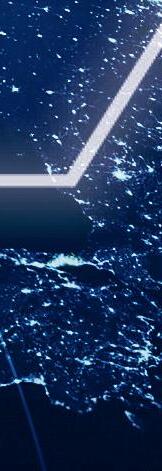
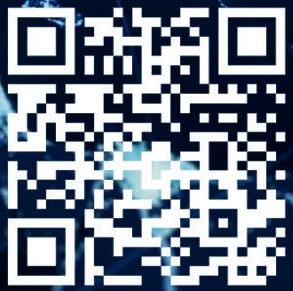
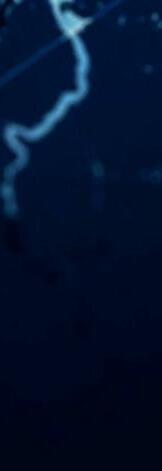
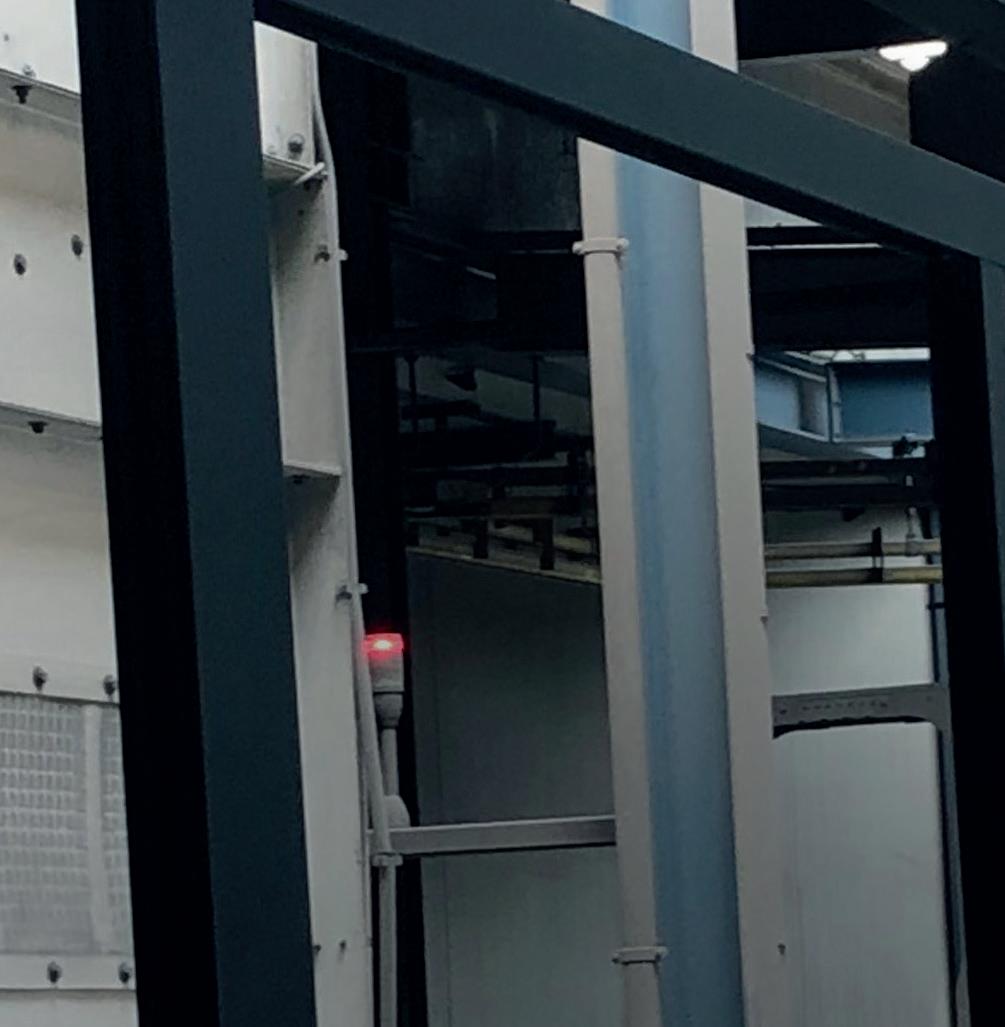
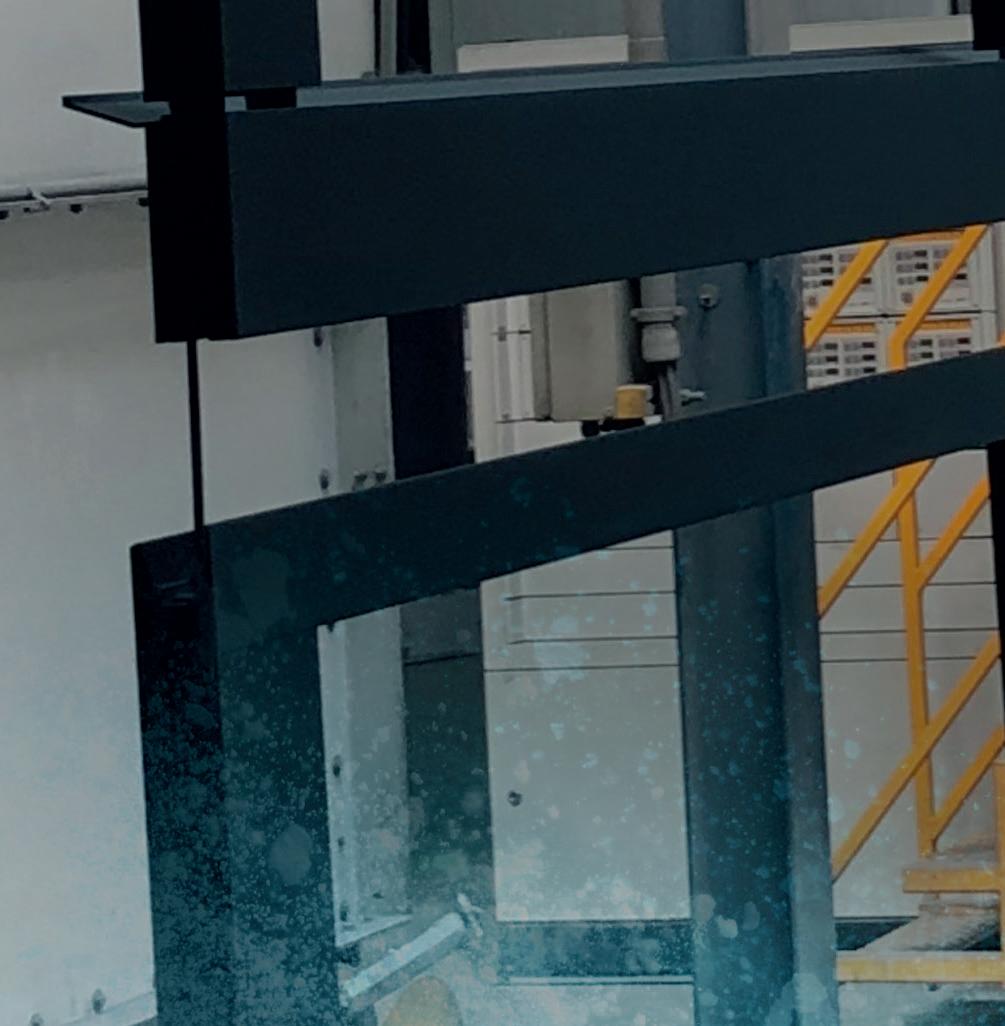
With our new Interpon D1036 Low-E powder coating, we’ve created an industry first: a powder coating that can cure as low as 150°C while still being Qualicoat class one certified. It can also cure up to 25% faster than conventional powders, reducing both energy consumption and carbon emissions, and significantly improving your coating line efficiency. Easy to apply Interpon D1036 Low-E has the same application properties as standard formulation, is backed by an Environmental Product Declaration (EPD) and has a global warranty of up to 15 years to deliver the quality performance, color and style your customers need. It is an innovation that supports our collective commitment to sustainability throughout the value chain.
MANAGING DIRECTOR & ADVERTISEMENT DIRECTOR
Nigel Bean
t: +44 (0) 1442 826826
e: nigelbean1@aol.com nigelbean@surfaceworld.com
EDITOR & GRAPHIC DESIGNER
Jane Soones
e: janesoones@aol.com janesoones@surfaceworld.com
CIRCULATION & SUBSCRIPTION DEPARTMENT
Sheena Burrus e: sheenaburrus@hillmedia.com
EXHIBITION ORGANISER
Sheena Burrus e: sheenaburrus@hillmedia.com
Hill Media Ltd, Marash House
2-5 Brook Street, Tring, Hertfordshire HP23 5ED, United Kingdom.
The Surface World magazine is published 12 times a year by Hill Media Ltd. Although every effort is made to ensure the accuracy and reliability of material published in Surface World, Hill Media Ltd and its agents accept no responsibility for the veracity of claims made by contributors, manufacturers or advertisers. Copyright for all material published in this journal remains with Hill Media Ltd and its agents.
© Hill Media Ltd – 2024 ISSN 1757-367X
We are pleased to announce an update to our quality label to recognise all powder coating that conforms to the QUALICOAT Specification.
This revision to our brand identity does not alter our fundamental principles or mission. QUALICOAT remains steadfast in its commitment to the vision, mission, and company values that have guided us for almost 40 years.
We look forward to sharing with you the future of quality Architectural Powder Coating in the next 40 years.
IRELAND
At Baril Coatings, we enable our clients to protect their assets sustainably while reducing their environmental footprint. By extending the lifespan of materials with less coating, minimizing harmful substances, and producing in a low-emission manner, we contribute to a more sustainable world.
We constantly push ourselves to enhance our products in sustainability, efficiency, and quality. Our coatings must meet the highest standards because we believe our customers shouldn’t have to choose between sustainability, performance, and cost-effectiveness.
Within this mission, a new major step towards sustainability is achieved. We are happy to announce that from now on, we are committed to using 100% recycled chalk only, in all of our coating products. This decision reflects our mission to innovate sustainably and reduce our environmental impact. Curious? Here’s how we do it:
The chalk is sourced from the process of drinking water production. Groundwater is extracted and softened, creating small chalk pellets. These are used in our bio-based products. Selecting the right regions to meet our demand and ensure the perfect whiteness is no small feat, but it’s worth the effort for this giant leap forward.
We use chalk, produced through an innovative method to turn mining waste into reusable, certified material. Although mining itself isn’t ideal, repurposing this byproduct from mining, into high-quality coatings is a significant sustainable win. It is realising a 65% lower carbon footprint on our entire chalk use.
Given that our total raw material procurement for our coatings is 20% chalk, this is a substantial step toward our mission. This shift is another step in our journey to make our industry greener and leave a smaller footprint on the planet.
Baril Coatings embraces a ‘oneplanet’ philosophy, recognizing our responsibility as a producer.
Reducing Dust, Waste & Disposal
4 operators can blast all day
4 operators can blast all day
Reduce abrasive consumption by up to 20%
Reduce abrasive consumption by up to 20%
Increase blasting production by up to 30%
Increase blasting production by up to 30%
EASILY SWITCH BETWEEN 4 FUNC Mist Blast Dry Blast Wash Down Blow Down TIONS
AVAILABLE IN 3 DIFFERENT PACKAGES
Single Outlet Blast Pot (6.5 cu ft) Combo Skid with Air Dryer 4-Outlet Mega MistBlaster
Does the Work of 5 manual blasters
Up to 646 ft² per hour
Use 3 (#10) nozzles simultaneously
Automate timing and speed
Blast walls, floors, even upside-down
We rigorously assess our entire business process, continuously searching for more sustainable solutions without compromising on quality. We are a company of action, proving our commitment through tangible results. Our big goal?
To become the greenest paint company in the world. And our mission is clear: 100% renewable by 2030, where we just made a giant step in.
We aim for a greener future, making a difference with and through coatings. That’s what we call #paintingarenewablefuture. We have a coating-solution for every surface.
We invite you to discover more on this win-win solutions for your industry, by visiting our website, visiting our LinkedIn-page or contacting our sales-team.
Email: info@barilcoatings.nl Visit: www.barilcoatings.com
Are you involved with the application of coatings to enhance and protect your products? Do you need to meet client specifications to ensure the longevity of your components? Does the complex world of surface engineering and materials finishing cause you headaches?
If so, the courses offered by the Institute of Materials Finishing (IMF) could be your solution!
The IMF have been promoting knowledge in the surface finishing industries, both inorganic surface treatments including plating and the application of organic paints, lacquers and varnishes for many years. Large numbers of engineers and technicians across a multitude of industries have benefitted from the knowledge gained to enhance their careers, their standing within industry and the ability to problem solve the many challenges they face in their daily working lives!
Starting with the Foundation level course, students gain knowledge on all aspects of materials finishing, specifically aimed at their own industry requirements, but to include sections on Health & Safety, the Environment and Surface Finishing and Corrosion Protection. There is no need for a science background to be able to successfully complete a foundation course.
The Foundation Course requires study of 15 sections and requires the submission of 2 marked assignments followed by an end examination. The course, conducted by distance learning will take 16 weeks to complete. There are three specific study routes to choose from; electroplating, organic coatings and aerospace finishing. On successful completion, the student is awarded the Foundation Certificate.
To follow on, students can then elect to progress to the Technician level modules, which give more in-depth knowledge for key finishing technologies, their application and best practice methods. Again, both inorganic and organic technologies can be studied to match the industry requirements. There is a choice of eight modules, which provide study in applicable areas of surface finishing best matched to your needs.
Like the Foundation course, study is by distance learning, and the student is required to complete four marked assignments and pass an examination.
Passing two technician modules leads to the award of Technician Certificate; passing four modules leads to the award of an Advanced Technician Certificate.
If you feel your career could benefit from being a recognised specialist in your particular branch of Surface Engineering or Materials Finishing, then contact the IMF today.
Speak with our training manager Karen Yates on +44 (0)121 622 7287 or email karen@materialsfinishing.org.
Move your career to the next level and join the finishing community and all the benefits that gives through the IMF.
Introduction to surface coating
The need for process control
Pretreatment
Various plating processes
Effluent
Experience plating test pieces
Analysis of plating solutions
Micro sectioning of test pieces
IMF member Price £450 per person
The Non-Member Price is £550 per person
Please note: other course topics may be available in the future, please enquire.
ELECTROPLATING
• 12 AND 13 MARCH 14 AND 15 MAY TO BE HELD AT POETON INDUSTRIES GLOUCESTER
622 7387
By Chris Mansfield - QUALICOAT Chair
QUALICOAT UK & Ireland, one of sixteen worldwide General Licensees for the QUALICOAT organisation, has seen rapid growth in the adoption of the freely available QUALICOAT Specification. A growing number of powder coating companies in the UK and Ireland are requesting to be third party inspected so they can prove that they are coating to the Specification and be able to use the coveted QUALICOAT logo on all their documentation and promotional media. The current logo has seen worldwide use for many years and has remain unchanged since the inception of QUALICOAT back in 1986. The organisation is now set to launch a refreshed logo for its future stages of growth whilst maintaining its position to offer the very best methodology for architectural powder coating and its sustainability.
Updating a quality label reflects a commitment to staying relevant, modern, and aligned with the evolving values of an organisation. The logo is more than just a visual element; it is a powerful representation of QUALICOAT’s identity and mission. As the organisation grows and adapts to new challenges and opportunities, it is crucial that branding communicates who the organisation is today, not just who the organisation was when the original logo was designed. The updated logo symbolises a fresh
chapter, embracing innovation while respecting the legacy of QUALICOAT’s past.
This rebranding effort also aims to strengthen QUALICOAT’s connection with stakeholders, including members, partners, and the broader community. A refreshed logo enhances recognition and fosters a sense of unity, professionalism, and trust. It reflects the organisations forwardthinking approach and reinforces relevance in a competitive and
rapidly changing environment. By modernising its visual identity, QUALICOAT aims to inspire confidence and enthusiasm, ensuring the brand remains impactful and resonates with future generations.
To specify, simply state powder coating must conform ‘to the QUALICOAT Specification’ on orders for powder coated aluminium or fabricated products, where installations are located in harsher environments, such as near to coastal waters, request the involvement of a specialist coater at the early design stages of any installation. The specification ensures a vertical integration of the best quality pre-treatment systems and powders as well as the recognition of quality of the powder coater which is regularly independently verified.
All QUALICOAT UK & Ireland members are available to offer advice and can be found on the Association website at qualicoatuki.org
Technical expert Raj Kumar is celebrating three decades of electroplating and specialist surface coatings with the Anochrome Group – and is looking forward to taking on new responsibilities in 2025.
Raj, from Oldbury, has worked in various roles since joining the business days after the UK’s first National Lottery draw in 1994, including Quality Control, Supervisor and Works/Production Manager.
He is currently Technical Sales Manager at Walsall-based Anochrome Ltd, offering first-class specialist advice to customers across the UK and further afield.
This year will also see, Raj, taking to the road for more regular faceto-face meetings with customers.
Raj, 50, said: “I can’t believe it’s been 30 years since I first started with the Anochrome Group. It has been, predominantly, a very enjoyable career, which has seen me progress through the ranks.
“I have acquired a lot of technical knowledge during that time, so I enjoy
fielding questions and queries from customers and coming up with solutions to their problems.
“As part of the senior team, I also assist throughout the organisation with quoting, pricing, planning, H&S, environmental, quality to name a few.
“This year I am looking forward to getting out on the road a lot more to meet both existing and new customers.
“Working for one organisation for so many years, you need to be able to get on with the people you work with on a daily basis.
“Both past and present, the management team have supported me in my progression as well.”
To contact Raj, email raj.kumar@anoltd.co.uk
• AirBench takesdustandfumes awayfromyourbreathingzone
• AirBench drawsthemthrough theworksurface,capturingthem insidethebench
• AirBench isavailableinawide rangeofsizesandfiltertypes tosuityourapplication
• AirBench isplugandgo-only needingunwrappingandplugging intoa13ampsocket
•Yougetextractionandwork benchinonecompactunit
Contactusforanon-sitedemonstration. Doubtitcanbethatsimple?
TheVertExmodularbooth system.Dustissuessolved...
• Modular systemforfast installationandassembly.
• LowEnergy throughtheuse ofhighefficiencyfans-upto 20,000m3/hat3kw.
• FiltrationOptions fromthe standardAirBenchrange.
• WeldingandGrinding boothsalso availablewithHEPAfinalfilter.
• RapidReconfiguration -standard componentsmeanVertExbooths canbereconfiguredondemand.
Doubtitcanbethatsimple?
Unrivaled probe interchangeability for all of your inspection needs.
Coating Thickness Probes
n Ferrous n Non-Ferrous n Combination n Ultrasonic
Surface Profile Probes
n Depth Micrometer n Replica Tape Reader
Environmental Conditions Probes
n Integral n Cabled Magnetic Probe n Anemometer Probe
n 1/2” NPT n Infrared
Hardness Probes
n Shore n Barcol
Salt Contamination Probe
n Bresle Method
Ultrasonic Wall Thickness Probes
n Corrosion n Multiple Echo Thru-Paint n Precision
n Low Frequency n Xtreme
Customized Inspection Kits...
Build your own kit from a selection of gauge bodies and probes to suit your needs.
Backwards Compatibility! The redesigned PosiTector gauge body accepts ALL coating thickness (6000/200), environmental (DPM), surface profile (SPG/RTR), salt contamination (SST), hardness (SHD/BHI), and ultrasonic wall thickness (UTG) probes manufactured since 2012.
01442 879494 f: 01442 879595
www.dftinstruments.co.uk e: sales@dftinstruments.co.uk
Leading global coatings company, Axalta Coating Systems (NYSE: AXTA), and innovative mechanical and plant engineering firm, Dürr Systems AG, have entered into a partnership to provide a digital paint solution, combining Axalta’s NextJet™ technology with Dürr’s robotics integration.
Digital paint, also referred to as overspray-free application, is an advanced paint application that allows for precise paint placement. Under the terms of the agreement, Dürr will serve as the robotics integrator for Axalta NextJet™ for light vehicle Original Equipment Manufacturers (OEM).
“The maskless application of paint for two-tone and graphics takes collaboration,” said Hadi Awada, President, Global Mobility Coatings,
Axalta. “Through our partnership with Dürr, we can better serve OEM customers, building on Axalta’s coatings know-how and Dürr’s robotics integration. Together we are driving the future of digital paint technology.”
Dr. Lars Friedrich, CEO, Dürr Systems AG, added “We are excited to collaborate with Axalta on the next generation of digital paint. As a pioneer in the field of oversprayfree application, Dürr understands the requirements that OEMs demand for individual designs on their vehicles. This agreement will enable our joint technology to come faster to market and meet the needs of our customers.”
This partnership leverages the digital paint expertise both Axalta and Dürr have cultivated over recent years.
In 2023, Axalta and Xaar announced their digital paint partnership that brought their unique capabilities together to offer solutions to light vehicle OEMs. Xaar will continue to be an integral part of the digital paint solutions that Axalta and Dürr will offer to the OEM market.
Demonstrations with Axalta NextJet™ on Dürr robotics have already begun at Dürr’s test center in BietigheimBissingen, Germany. OEMs can reach out to their Dürr or Axalta representative for more information.
Carlisle Fluid Technologies, a leading global manufacturer of products and systems for the supply, application and curing of sprayed and dispensed materials, is excited to announce its official rebrand to Binks, marking a new chapter in the company’s long history. The rebrand aligns with the company's vision for the future and its continued commitment to innovation in service of reliable advancements in consistency, efficiency, and sustainability for customers around the globe.
Carlisle Fluid Technologies had long been at the forefront of developing process solutions for a wide range of material application demands. As the company expands its product offerings and services, it has chosen to unify under the Binks name. Together with a variety of sub-brands, the company’s more than 375 years of collective experience is now coalescing to streamline its market presence and reinforce its reputation as a trusted partner that simplifies complexities for customers worldwide, from a product level to a holistic system level.
“Our new name, Binks, pays homage to our roots while reflecting the exciting future that lies ahead,” said [Fred Sutter], CEO of Binks.
“This rebrand is an exciting milestone for our company. It represents the strength of our heritage, the innovation at the heart of our culture, and our
unwavering commitment to supporting our customers’ success with industry-leading solutions.
We are confident that the Binks name will resonate with our customers and partners, both old and new, as we continue to evolve and grow.”
The company chose to elevate a sub-brand to the level of a parent brand that has long-standing success as a strong, recognizable brand in the marketplace, reflecting the company’s ongoing innovation, cutting-edge technology, and ability to meet the challenges of modern industries. The rebrand brings with it a new logo, updated branding materials, and a fresh website will follow, designed to improve user experience and reflect Binks’ innovative mindset.
Binks will continue to provide its comprehensive portfolio of products
and services, including pumps, valves, spray guns, filtration, and automation systems, all designed with a focus on efficiency, sustainability, and reliability. Along with the rebranding, Binks is poised to unveil new product innovations and initiatives in the coming months.
Binks, formerly known as Carlisle Fluid Technologies, is a leading global manufacturer of products and systems for the supply, application and curing of sprayed and dispensed materials. Binks serves a variety of industries, including automotive, pharmaceuticals, food and beverage, and manufacturing. With decades of experience, Binks continues to set the standard for precision, reliability, and innovation in fluid technology solutions.
For more information, visit www.binks.com
A partnership between the Interpon team at AkzoNobel and PowderTek, a powder coater in Northern India, is helping to provide architects with colors and styles to enhance their creations and provide the warranties to protect their buildings for years to come.
PowderTek chose to work exclusively with Interpon to coat the aluminum facades, windows, doors and similar architectural products that feature in many Bollywood star bungalows and homes throughout the region. As well as using Interpon D Futura, Anodic and Stone Effect powder coatings, PowderTek is also the first business in the region to use 100% Interpon D STF powder and basecoat to give surfaces a natural, wood-like finish.
Since partnering with AkzoNobel and working with its Technical Services team to give the firm a meaningful competitive advantage through bespoke colors and operational efficiencies, PowderTek has grown its operations by a factor of three and expects to double in size over the next 12 months.
It is similarly a champion of Interpon bonded metallic powder coatings. With AkzoNobel’s special bonding techniques, the Interpon team can significantly improve the lustre and finish of its premium special effect metallic powder coatings to deliver a uniform metallic finish with even greater color consistency and
performance. Two colors that are especially trending at present are Steel Bronze and Golden Beach.
Kshitij Anand, CEO of PowderTek, describes it as a genuine partnership: “We are expert coaters; the Interpon team are experts in powder. If we are using a new shade, then the Technical Services team will help us stabilise the use of that shade on the line. If the temperature isn’t consistent in the oven, then the variation in shade becomes more prominent. They give us the guidance and we follow the steps.”
Sustainability is similarly important. The new generation of metallic effects is reducing the use of liquid coatings, while still providing the stunning effect that ‘real’ metals deliver. Powder coatings are completely free of Volatile Organic Compounds (VOCs) and any overspray can be captured and reused.
Narasimha Rao, Country Sales Manager India, Nepal, Sri Lanka & Bangladesh says: “Kshitij and his PowderTek team are among the top coaters in the region, who trust the quality of our products and our technical support. We’re helping not only to give
them a point of difference through colors and finishes that are always on trend, but also further improve their production processes to be more sustainable and efficient.”
“With AkzoNobel as our partner, and their commitment to working only with the best, we are excited about how they can help us in becoming the biggest powder coatings brand across the whole country,” Kshitij concludes.
For more information, visit: https:// www.interpon.com/gb/en/insights/ powdertek-testimonial
Non-contact Uncured Powder Thickness Gauge
Affordably measures uncured powder coatings using non-contact ultrasonic technology to predict a cured thickness
Dedicated stand-alone unit is ready to measure right out of the box
Fast measurement speed—ideal for moving lines and swinging parts
Scan Mode continuously takes measurements—ideal for analyzing large areas
Storage of 999 readings with onscreen averaging. Stored readings can be downloaded to PosiSoft Desktop Software
Powder Inspection Kits
Complete solutions for measuring powder coating before and after cure are available
Services Director at Wedge Group Galvanizing Ltd,
David Nobes, had the honour of sharing his expertise on sustainability strategy and its successful implementation with an international audience during a recent visit to Madrid (Spain).
David was invited by Juan Campos, MBA Program Coordinator at the Universidad Autónoma de Madrid (UAM), to deliver a presentation to students at the university. Separately, Juan Carlos Higueras, Director of MBA Programs at the EAE Business School, extended an invitation for him to deliver the same presentation to students at EAE. Both events reflect the institutions’ commitment to bridging academic theory with practical application to address global environmental challenges.
“Juan Campos from the UAM had visited the UK over the summer and expressed a strong interest in the work I’ve been doing as part of my MSc in Sustainable and Ethical Business Management at Derby University.”
David said. “He was particularly intrigued by Wedge Group’s journey
towards Net Zero and the innovative practices we’ve implemented to reduce our carbon footprint.”
“It was a privilege to share these insights with international students, exploring the challenges organisations face when implementing sustainable processes, as well as the ambitious targets set by governments worldwide. It was also an opportunity to highlight the inherent sustainability of galvanizing as an industry and the significant progress Wedge Group Galvanizing has made to enhance its eco-friendly credentials.”
David concluded by expressing his gratitude to both institutions: “I would like to thank Juan Campos at the UAM for his kind invitation, as well as Juan Carlos Higueras at EAE Business School for inviting me to share this
presentation. My sincere thanks also go to Karyn Suárez at EAE Business School for her role in facilitating the sessions and ensuring everything ran smoothly. The engagement and curiosity of the students was truly inspiring.”
Wedge Group Galvanizing Ltd is the largest hot-dip galvanizing organisation in the UK, with a history dating back over 155 years. With 14 plants strategically placed across the country, the firm offers a truly national galvanizing service.
For further information please contact Wedge Group Galvanizing on 01902 601944 or visit www.wedge-galv.co.uk
Hot dip galvanizing provides you with long-term protection against rust and corrosion of steel products.
With 14 plants across the UK, Wedge Group Galvanizing is the UK’s largest hot dip galvanizing organisation offering a national service, collection and delivery and 24hr turnaround on request. The group can process anything from small components to 29m structural beams.
Anochrome Technologies, a high-quality spray coatings, anodising and aluminium passivation specialist, has received a new automotive industry certification in recognition of its quality management system.
Bloxwich-based Anochrome Technologies Ltd has been certified to the automotive technical standard IATF 16949 following a rigorous inspection process.
The award was developed by The International Automotive Task Force (IATF) - a group of automotive manufacturers and their respective trade associations - and approved by the International Organization for Standardization (ISO). It is the globally recognised standard for quality management systems in the industry.
Anochrome Technologies, part of the Anochrome Group, uses manual, automatic and robotic techniques to produce premium finishes for several industry sectors including automotive, industrial, aerospace, wind energy, marine, and many more. Group Compliance
Manager Sue Guilmant praised the team for achieving the certification.
“The process of achieving this certification took six months of planning and sheer hard work by the team at Anochrome Technologies,” said Sue.
“The speed at which it was completed was primarily down to the fact that this site has a great team and had already applied many of the automotive quality disciplines within their day-today functioning for many years.
“I am so proud to be working with such a fantastic team to achieve this.”
The certification also recognises a business' commitment to continual improvement whilst reducing defects and waste in the supply chain.
Mark Jones, Anochrome Group Managing Director, said: “We are delighted that Anochrome Technologies has achieved IATF 16949. The certification is an enabler to trade in international markets and will allow us to grow the business still further.”
Anochrome Technologies is the fifth company within the Anochrome Group to be certified to IATF 16949, following in the footsteps of Anochrome Ltd, WEP, Inlex and Anocote Czech Republic. The business also holds management system certifications ISO 9001 and ISO 14001.
See all of Anochrome Group’s accreditations here: https://anochrome.com/ accreditations/
BYK-Gardner GmbH – worldwide partner of the automotive, paint and plastics industries for quality control of color, appearance, and physical properties – is announcing the new byko-visc CP Rotational Viscometer.
Accurate control and measurement of the viscosity of samples is a key step in the quality assurance process of paints and coatings. To meet your requirements BYK Instruments now offers a new product line of Cone and Plate Viscometers to help with the exact determination of viscosity where it matters most.
These Cone and Plate viscometers are available in two different versions, each
with a Lite option. The low temperature model from 5 to 75 °C is the ideal instrument for room temperature measurements in any environment. Its Peltier technology allows for the rapid cooling as well as heating of the sample plate allowing for quick and accurate temperature control. The high temperature model from 50 to 235 °C is ideal for samples that need to be evaluated at higher temperature such as polymer melts.
All models feature an electronic cone lift that automatically lowers the cone onto the robust tungsten carbide sample plate. All driven by a robust direct drive motor. Cones are attached and seamlessly switched by a bayonet coupling. No need for recalibration!
These new Cone and Plate Viscometers offer the same intuitive Design as our rotational viscometers.
For more information please contact, the free service no. 0-800-gardner (0-800-4273637) or on the internet at http://www.byk-instruments.com
BYK is one of the world’s leading suppliers in the field of additives and measuring instruments. Additives
are chemical substances which, when used in small quantities, improve product properties such as scratch resistance or surface gloss. Manufacturing processes are also optimized by the addition of additives.
The coatings, inks, and plastics industries are among the main consumers of BYK additives. Yet with the production of oil and gas, the manufacture of care products, the production of adhesives and sealants, and construction chemistry, too, BYK additives improve the product characteristics and production processes. Testing and measuring instruments from BYK can effectively evaluate the quality of color, gloss, and appearance as well as the physical properties of paint, plastic, and paper products and are an important part of quality control.
As a globally operating specialty chemicals company, BYK has production sites in Germany (Wesel, Kempen, Moosburg, Schkopau and Geretsried), in the Netherlands (Deventer, Nijverdal, and Denekamp), in Great Britain (Widnes), in the US (Wallingford, Chester, Gonzales, Louisville, and Earth City) and in China (Tongling).
Today the company employs around 2,300 people worldwide and forms part of the ALTANA Group.
L SERIES | Medium flow rate filter
P SERIES | Ultra-high flow rate filter
A SERIES | Mechanical seals pump
M SERIES | Magnetic drive pump
T SERIES | Vertical pump [...]
L-TECH | Pleated cartridge
BAGTECH | Filtration bag
QUALITHERM | Extruded cartridge
QUALIBOB | Wound cartridge
ANODTECH | Anode bag [...]
SPECIAL SYSTEMS
ACIDPURE | Acid recycling
EASYPURE | Fluid recycling
IONPURE | Ionic filtration
ACIDVAC | Acid draining vacuum
EDUCTORS | Bath agitation [...]
The PosiTector series, developed by DeFelsko, the leading US manufacturer of paint inspection equipment, offers a versatile and cost-effective solution for coating applicators and inspectors. The system allows users to easily swap interchangeable probes with a single PosiTector gauge body, streamlining multiple inspection tasks with one device.
The PosiTector gauge body is available in two models: Standard and Advanced. Both feature a large touchscreen display, user-friendly navigation, internal memory, and an IP65-rated enclosure. The Advanced model adds Wi-Fi, Bluetooth, additional memory, onscreen graphing, and advanced probe features, such as the ability to take over 180 readings per minute in scan mode (PosiTector 6000) or measure up to three layers on non-metal substrates between 13-7800um with the 200 series probe.
The latest PosiTector gauge body is fully compatible with all PosiTector probes manufactured since 2012. This backward compatibility allows the gauge body to easily convert into various inspection tools, such as a dew point meter, surface profile meter, soluble salt tester, hardness tester, gloss meter, or ultrasonic wall thickness gauge, making it highly adaptable to different needs.
Changing probes on the PosiTector system is simple. There is no need to turn off the device—just slide the probe out, following the arrows on the back, and insert another probe. The gauge body automatically recognizes the new probe and retains all settings, including calibration, language preferences, and measurement units. This seamless probe switching eliminates the need to relearn menu functions, saving time during inspections.
The system also helps reduce costs and space by allowing users to consolidate all inspection equipment into one compact case. You can start with a single probe and expand your collection over time or opt for a standard or custom kit to suit your specific needs.
The PosiTector Advanced gauge body offers additional features that enhance inspection efficiency. When connected to the PosiTector 6000, users can access specialized modes like PA2, 90/10, and 19840, along with Smartbatch functionality for the PosiTector SPG. The dew point meter includes trend charts and live graphing, providing deeper insights during inspections.
PosiTector’s integration with the PosiSoft Software Suite makes it easy to compile professional reports. You can download readings from multiple probes and generate
multi-batch PDF reports, simplifying data analysis and presentation. Bluetooth and Wi-Fi connectivity allow for easy report generation in the field or remote data transfer to a computer.
The PosiTector 6000, 200, and UTG gauges feature a “Prompted Batch Mode,” which simplifies inspections by providing on-screen prompts for each measurement. This is particularly useful for repetitive jobs or when specific measurement locations are required. Multiple templates can be stored, allowing for consistent and efficient inspections.
For companies with multiple probes, the PosiTector system reduces downtime by allowing only the probes to be sent for recertification, not the entire gauge body. This means the gauge body remains in service, eliminating the need for recalibration.
The PosiTector range offers significant cost savings by allowing multiple probes to share a single gauge body. Kits are available in medium, large, and heavy-duty Pelican cases with customizable interiors, saving space and reducing the number of cases needed.
For more information contact Mark Conlon at DFT
Instruments UK Ltd, the official UK and Ireland distributor for DeFelsko.
Telephone: 01442 879494
Email: sales@dftinstruments.co.uk
Visit: www.dftinstruments.co.uk 6 K-type thermocouple ports
High
or export to .CSV
Download, view, and analyze data using PosiSoft Desktop
The Chinese electric vehicle manufacturer BYD Auto Company Limited is building its first European passenger car plant. To equip it with painting technology, BYD selected Dürr. Over the coming months, the German mechanical and plant engineering company will send more than 120 robots to Hungary for various painting lines. These robots, fitted with EcoBell3 atomisers, deliver outstanding quality and support sustainable painting.
BYD Auto Company Limited, one of China’s largest vehicle manufacturers and ranks among the market leaders in electric vehicle sales. Now, the company is becoming one of the first Chinese car manufacturers to build a European car factory, located in Szeged, Hungary, . For painting its “New Energy Vehicles” (NEV), BYD has partnered with Dürr, one of the world's leading mechanical and plant engineering firms to supply and install more than 120 painting and handling robots.
“As a world market leader in automotive painting, Dürr is the right partner to implement projects of this size successfully and on schedule. It was not just our outstanding technology that won over BYD, but also our experience in Hungary, where we have already completed a number
of projects,” explains Dr. Lars Friedrich, Head of the Application Technology division at Dürr. This is the first order the company has received from the Chinese carmaker in the passenger car segment after Dürr Systems AG was successfully audited by BYD before being considered as a supplier.
The painting lines will use Dürr’s latest EcoRP series painting robot, available in both six- and seven-axis variants for interior and exterior painting. The seven-axis robot offers high precision and flexibility for interior painting, reaching even the most difficult to access areas. Six-axis robots will handle exterior painting. The scope of supply also includes the corresponding door, lid, and flap openers as additional aids for the painting process.
SurTec 650 - Tri-chrome Passivation for Aluminium
Best-in-class bare metal corrosion protection and excellent paint adhesion
Outstanding filiform corrosion resistance
QPL-listed; Meets MIL-DTL-81706-B and MIL-DTL 5541-F
Specifically designed for the application in the architectural industry
Leading-edge performance in filiform corrosion resistance
Easy handling without additives as make-up/replenisher system
Corrosion resistance almost on the level of ZnPhos
Very high flash-rust stability
No mapping effect when E-coated
SurTec 609 EC - Phosphate Replacement for Multi-Metal Pre-Treatment
SurTec 643 - High-Performance Chrome-free Aluminium Conversion Coating SurTec
EcoBell3 high-speed rotary atomisers ensure flawless painting quality with uniform shade, flow, and layer thickness. When combined with the associated cleaning equipment and colour change technology, the atomiser family minimises paint and solvent consumption and enables fast colour changes within the cycle time. In future, BYD will also be able to sustainably implement customers' special colour requests using Dürr's standardised, modular EcoSupply P paint supply system with pigging technology. The ”pigs” –fitting bodies matched exactly to the internal diameter of the hoses– push paint to the colour changer and return any leftover paint back into the paint container, leaving absolutely no trace of residue and eliminating the need for cleaning. This process reduces paint and the rinsing agent consumption, benefiting both budget and the environment.
The supply scope also includes cleaning robots that remove dust and dirt particles from the bodies before painting. Flexible-action feather rollers clean different body shapes efficiently and independently of each other in nearly any combination and order – ideal for BYD’s various NEV types.
For more information about Dürr and its innovations, visit www.durr.com
Product Overview
Manual Monorail Systems
Unit loads up to 3000kg
Monorail Chain Conveyors
Unit loads up to 300kg
Power & Free Conveyors
Unit loads up to 7000kg
Floor Conveyors
Unit loads up to 500kg
Stewart Gill Conveyors Ltd have been supplying overhead conveyors into all sectors of industry for over 70 years.
As a long time member of the Railtechniek van Herwijnen BV Group based in the Netherlands, Stewart Gill Conveyors can offer a comprehensive range of overhead conveyor products which are capable of handling unit loads up to 7000kg.
Stewart Gill Conveyors Ltd offer complete manufacture, installation and commissioning, coupled with fully documented instruction, operation and maintenance manuals.
We do:
In-House 3D CAD engineering
In-House manufactoring in the UK and EU
In-House design of PLC/PC control systems
Industry 4.0
Worldwide installation and commissioning
Remote support, service & inspection Stewart
Part of the
Models:
ELECTRON Powder Coating Booths are vital for powder applications in production processes. The aim is to protect human health and maximize powder savings.
Ergonomic designs and demountable structures provide easy installation and maintenance.
Automatic Powder Coating Booths:
Fast and high-quality coating with uninterrupted powder supply.
Filtered or monocyclone system options.
Production specific to the customer's needs.
In order to minimize time and productivity loss during color change, we develop cabins that can be cleaned quickly and have high recycling efficiency. Thanks to plastic structures, rapid color changes are possible.
Cyclone or Filter Type:
Designed for effective powder retention and easy maintenance.
Metal Body Type: Durable and long-lasting use.
Plastic Body, Floor Blown Quick Color Change Booth:
Easy to clean and ideal for quick color changes.
Conveyor Pass or Closed Type: It is designed to be suitable for continuous production lines.
Movable Platform or Fixed Type: Flexible for different coating processes.
Features:
Maximum Energy Saving: Advanced technology insulation and energy efficient designs.
Emission Amounts Compliant with CE Standards: Environmentally friendly operations.
Fast Color Change: Flexibility and time savings in production processes.
High Powder Retention Percentage: Minimum powder loss and high quality coating.
Sound Insulation Compliant with CE Standards: Increases the comfort of the working environment
Each powder coating booth model is designed to increase efficiency and quality in industrial coating processes, ensuring excellent results in your production processes.
Visit: www.electron.com.tr
Surface energy plays a crucial role in determining the wetting behaviour of liquids on solid surfaces. Generally, surfaces with higher surface energy tend to be more easily wetted by liquids, resulting in better spreading, while surfaces with lower surface energy are more likely to repel liquids. A prerequisite to any adhesion and bonding is wettability, and so understanding surface energy is critical to the success in the application of adhesives, coatings, inks and more. Surface energy can be measured in different ways, both before and during the manufacturing process. Here, Kevin Brownsill (KB), Head of Technical and Learning at adhesives and sealant supplier Intertronics, and Alison Fox (AF), Brand Manager of Dyne Testing, an Intertronics brand, answer some of the important questions about why manufacturers should measure surface energy.
AF: Different solids have different surface energy depending on their molecular makeup. For example, polytetrafluoroethylene (PTFE) has a very low surface energy, and metals typically have a high surface energy. The surface energy of a substrate can also be affected by roughness and contamination. Surface energy will affect liquid flow across the substrate and can influence, for example, the formation of homogenous thin coatings and the way that fluids react with objects placed in the human body in biomedical applications.
KB: The successful application of adhesives, coatings, inks and other materials where adhesion is important is highly dependent on the wettability
of these materials to the target substrate. If the liquid behaves like water on a greasy plate, forming discrete balls rather than a film, then it is easy to see adhesion problems ahead.
KB: Wettability is a prerequisite of adhesion. For bonding or printing to be a success, the surface energy of the substrate must be higher than that of the liquid so that wetting can occur –the liquid forms a contiguous film on the surface, rather than the liquid beading up or retracting from the surface. So, we need to understand the relationship between the surface energy of the substrate and the surface energy (or surface tension) of the liquid. Many modern plastics have low surface energies that make bonding a challenge, because they are lower in value than the adhesive or ink. Another issue may be surface contamination, like oils, greases or release agents, which can influence surface energy and inhibit wetting.
AF: Surface measurement technologies help identify the cause of poor wettability, so that manufacturers can optimise material choice or the surface preparation process to eliminate adhesion issues. We can measure physical properties of the substrate and the surface tension of the liquid; understanding those is important for that bonding mechanism.
KB: That depends on the situation. For qualitative and fast testing, dyne inks are a cost-effective method that can be used for on- or off-the-line testing. The inks have specific surface tension, measured in mN/m, or dyne/ cm, often known as “Dynes”. When a dyne ink is applied to a substrate, the ink will either form a continuous film on the surface or pull back into small droplets. If you apply a 38 dyne ink to a substrate, and the ink stays as a film for three seconds, the substrate has a surface energy of at least 38 dyne/cm.
Dyne inks are predominantly supplied in a special pen (hence, Dyne Pen), which makes them very convenient
and portable. A manufacturer can take a component/material off the production line and test it quickly for its surface energy – so for example, confirming that a polyethylene film has been surface treated prior to printing. By using a range of Dyne Pens of various dyne levels, the surface energy of a substrate can be determined to a narrow range.
AF: At the other end of the scale are measuring instruments like tensiometers. A tensiometer is an instrument used to measure the surface tension of liquids. It can also measure other properties, like contact angle. The wetting behaviour of a liquid on a solid surface is directly related to the contact angle and surface energy, where a lower contact angle indicates higher surface energy and better wetting, while a higher contact angle suggests lower surface energy and poorer wetting. A good example of this kind of instrument is the Biolin Scientific Theta range of optical tensiometers. A drop of liquid is dispensed onto a substate, and viewed from the side with a high resolution camera. This is analysed with sophisticated, user-friendly software. These instruments are predominantly used off-line to give accurate and repeatable quantitative measures of contact angle, and therefore wetting.
Optical tensiometers like the Theta range are used in production quality control centres, product development and research laboratories and test
houses. With contact angle measurement you can compare a range of solids and liquids with surface treatments to ascertain the most effective.
AF: First, manufacturers should understand what surface properties are needed to obtain the ideal conditions for adhesion. If you’ve got a clean, dry, dust-free and non-porous surface, you’ve got the first step to good wettability. For some applications, the surface can be cleaned with an isopropyl alcohol wipe to ensure there are no oils or greases. For more critical applications, understanding the cleanliness of the substrate is beneficial. For example, on metal substrates, the SITA CleanoSpector is a popular and easy-to-use handheld non-destructive metal cleanliness test instrument used for measuring organic contamination such as oil, grease, coolants, release agents and cleaning fluid. This can indicate the need for a more effective cleaning process or highlight a poorly functioning cleaning process.
Even if you have a clean substrate, you will still have wetting and bonding problems if that substrate has a low surface energy or is a non-polar surface. Many common plastics, such as polyethylene and polypropylene, have non-polar surfaces and low surface energy.
Elcometer’s CONTRACTOR and PERFORMANCE abrasive blast equipment is engineered to last longer, work harder & perform better.
dry abrasive blast machines | precision media valves blast hose | blast nozzles | personal protection equipment
Surface World - Changed background CB.indd 1
This year, marks five decades as an independent powder coating specialist. We are proud to have one of the largest ranges of stock powder coatings in the UK, available for next day delivery. We have thousands of satisfied customers across diverse markets including construction, agriculture, leisure and retail as well as renowned architects and design houses.
Some form of additional surface treatment can help; this includes flame treatment, corona or plasma.
KB: Application of plasma to a surface can clean at a molecular level and increase surface energy – activating the surface ready for bonding. For example, at Intertronics, we have used atmospheric plasma on a polyethene surface. Untreated it had a surface energy in the low 30s mN/m, but treated it had a surface energy of ~55 mN/m, therefore making it bondable with an adhesive with a surface tension in the 40/45 mN/m range.
Plasma can modify and functionalise surfaces to prepare them for adhesive bonding, varnishing or printing without altering the bulk properties, or marking or discolouring the treated part. In a process known as surface functionalisation, plasma treatment
causes the generation of polar oxygen groups on the substrate’s surface, which can act as bonding anchors by forming covalent bonds with molecules in an adhesive to increase bond strength.
Atmospheric pressure plasma treatment is a versatile and efficient method for surface modification, widely used in industries ranging from automotive to biomedical for improving surface properties without altering bulk material characteristics. These devices can often use compressed air, or sometimes specific gas mixtures for special applications. For larger scale fast production, manufacturers can opt for technology such as the Relyon plasmabrush PB3, which can be integrated into automated, continuous production processes.
In addition, there are a range of cold atmospheric plasma devices on the market. The Relyon piezobrush PZ3 handheld device is a good choice
for R&D, pre-production or medium volume work due to its small size and manoeuvrability, while a variant, the PZ2-i can be mounted onto a robot for automated or semi-automated applications.
In summary, the wettability of a surface is a complex interplay between the surface energy of the solid, the surface tension of the liquid, and their interactions. The contact angle serves as a measurable indicator of these underlying forces, providing valuable information about the wetting behaviour of liquids on different surfaces. Understanding wetting behaviour is a prerequisite to achieving good adhesion for your adhesive, coating, ink, or paint.
For assistance in measuring surface energy and to find out which application is most suited to your production needs, visit Dyne Testing’s website https://dynetesting.com/
By Jorrit van Rijn, Global Segment Manager for Industrial, AkzoNobel Powder Coatings
Corrosion is more than just an unsightly nuisance. It can cost businesses, governments, and indeed entire countries billions of dollars every year.
According to a study by The National Association of Corrosion Engineers (now AMPP), the global cost of corrosion is now estimated to be greater than $3 trillion.
Corrosion can lead to major disruptions in productivity and a significant hike in operating and maintenance costs. And it is not just about the bottom line. It is also the impact that corrosion has on safety, and the risks associated with product failure.
Experts from the AMPP warn that the issue is only going to get worse, driven by climate change. Heavier rainfall and
more intense storms at one end of the extreme and hotter, longer heatwaves at the other place huge pressure on the designers to find ways of protecting their creations over the long term, whether that’s a simple piece of playground equipment in a school or a park through to a major piece of essential infrastructure.
Different metal surfaces also present different challenges and require different approaches to corrosion protection. Location, application, and use are all important factors in determining what protective coatings are most suitable.
Powder coatings have been used to address corrosion for decades and new products are constantly being innovated. Powder coatings not only give originators and operators solutions that enhance performance but also support brand integrity, eliminating the presence of ‘red dust’ on a
product which potentially destroys consumer confidence, ensuring the visual appearance is maintained.
So why are powder coatings so popular? And why can they prove so effective at protecting surfaces against corrosion?
Protecting a pre-treated surface by using a powder coating brings a number of benefits, notably around the two key themes of performance and sustainability.
In terms of performance, powder coatings are available that provide especially excellent edge coverage. This makes them ideal for coating the sharp edges and more difficult shapes that might typically be encountered, for example, in the manufacture of Agricultural and Construction Equipment (ACE). The risk of corrosion is most often greatest at the edges of a surface where there is less of a coating barrier to protect the base metal.
Pre-Treatment Solutions Group Ltd supply unique chemistries for an array of metal processes.
Our Phos-Prep® range of chemicals are chrome free, eco-friendly and cost effective all while maintaining quality and performance.
With over 50 years experience within the industry we pride ourselves on finding the right solution for your metal treatment. Whether that be degreasing, etching, phosphating, paint stripping and more!
“We have been a customer of PTS for over 20 years and during our time we have relocated our business, changed our pretreatment process with the full support and expert advice to implement changes from the PTS team. A great company who always go the extra mile to support their customers.”
P.Allen, West Midlands.
“We have been fortunate to have partnered with PTS for over ten years now. They are consummate professionals and always exceed expectations in terms of delivery of service, knowledge and customer care.”
E.Smith, Hampshire.
, ten a
“We have had the great pleasure in working with PTS for over 5 years. No matter how big or small our queries are, PTS always come up trumps and in rapid time. The team are always willing to visit our site to help out with any issues we have or just for a general catch up with our staff. We have a very good relationship with the whole team at PTS and long may this continue.”
R.Glasbey, West Yorkshire.
Powder coatings also have significant sustainability benefits, being free from solvents and Volatile Organic Compounds (VOCs) and offering different levels of durability. Surfaces that are powder coated are much easier to clean and maintain. They also offer greater resistance to scratching or marring, both during production and in transit, therefore helping to prevent the process of corrosion from taking place.
They are also more sustainable in terms of the material you use, and the process you follow. A powder coating delivers the same and usually a better chemical, mechanical and weathering performance than a liquid, but in fewer coats or even a single layer. They are easy to apply and very forgiving in their application, being less sensitive to runs, sags or bumps.
In the application process, a powder coating creates significantly less waste, since any overspray powder coating can be collected, recycled and re-used. There is also the benefit of having no hazardous waste to dispose of, nor the expense or inconvenience of doing so.
But with so many powder coating products out there to choose from, and multiple manufacturers, how do you go about selecting the right product for the job?
How one specific manufacturer’s product performs versus another is complicated since it involves many different variables. You need to ensure you are making like-for-like comparisons. That means comparing a product’s performance using the same substrates (e.g. steel and aluminum), the same testing conditions and equipment (e.g. the same corrosion cabinet and scribing tool) and the same type of pre-treatment (i.e. chemical or mechanical) prior to the powder coating being applied.
It is particularly important to compare products based on their adherence to international standards. Given the extreme environments to which many steel structures are exposed, for example, protective paint systems are governed by international industry standards. One is Qualisteelcoat, a quality label organization that requires the performance of a coating to be measured against defined technical specifications. The organization also undertakes ongoing compliance through the licensing of plants around the world, thus ensuring the product quality is maintained. The second is the recognized International Organization for Standardization (ISO) 12944.
ISO12944 is officially a liquid paint corrosion standard that powder coating manufacturers also reference in their own testing as regards a
powder’s performance against corrosion. While not a powder coating standard in its own right, it can, by agreement, also be applied to do those cases which are not covered by ISO12944. Indeed, Qualisteelcoat and GSB ST 663 take as references several parts of ISO 12944 (i.e. for specifications, requirements and assessment).
ISO12944 prescribes test and related performance requirements of the powder coatings, either through the Neutral Salt Spray (NSS) test conducted in accordance with ISO9227 or Cyclic testing (for very high corrosion requirements) according to ISO20340. The performance of these tests is not only influenced by the quality level of the powder corrosion protection primers, but also – as previously stated – by type of substrate (aluminum, steel, etc.) and by its preparation (i.e. the cleaning and pre-treatment of the metal surface). It is also important to recognize and measure ‘creep’, and to what extent creep occurs over an extended time.
The product range that performs consistently well, whatever comparisons are made, is Interpon Redox. The range comprises a variety of primers proven to provide the highest levels of long-lasting protection in the most challenging conditions (i.e. up to one of the most demanding environments known as ‘C5’ to protect surfaces for 25 years or more in accordance with ISO 12944).
Among the latest innovations in EMEA for preventing corrosion is Interpon Redox One Coat. It protects surfaces up to C4M (i.e. for between 15 – 25 years) and does so in a single coat. It also has the advantage of being free of Bisphenol A (BPA) and zinc.
Trestles, a Czech-based global manufacturer of gates and fences, is a good case in point. It has recently started using Interpon Redox One Coat on the recommendation of AkzoNobel’s Technical Services team and only after Trestles tested its performance against samples from other powder coatings manufacturers:
“In salt spray tests, Interpon Redox One Coat performed the best in protecting our products against corrosion,” says Daniel Molnár, Procurement Manager at Trestles.
“We also tested it on different steel surfaces, as well as some Beta products we currently have on trial, with excellent results. We wanted to be sure the product would perform, even in rain or snow, and since using Redox One Coat there have been no complaints.”
While powder coatings traditionally require a primer layer for corrosion protection, followed by a topcoat for gloss and UV protection, Interpon
Redox One Coat enables Trestles to reach corrosion protection up to C4M and high UV durability in a single coat which requires only a base chemical pre-treatment.
CEMER, a global manufacturer of playground equipment and urban furniture, is another example of a business using a powder coating system to deliver exceptional levels of anti-corrosion performance.
Burak Eroglu, Chief Production Officer at CEMER, says that the system, comprising an Interpon primer and topcoat, is helping the business to
compete on the international stage: “The durability of the powder coatings helps to guarantee that our products will last in extremes of hot and cold and all climates, in any of the 75 countries in the world where our products are used,” he says.
Using Interpon Redox in preference to hot dip galvanizing (HDG) reduces costs and waste, while still meeting the market requirement for corrosion protection. HDG also requires the steel substrate to be pre-treated prior to a topcoat being applied, an additional process layer that is now removed.
Powder coatings are proven products in tackling corrosion. The product itself, however, is only one half of the equation, and the need for professional guidance and support to maximise its effectiveness is essential.
AkzoNobel can help customers directly with the most challenging applications through its technical support team and provides R&D support with extensive testing services to help businesses arrive at the right decision.
For more info: https://www.interpon. com/gb/en/products/industrial/ interpon-redox
For contact details: https://www. interpon.com/gb/en/contact
Large OEM automotive paint lines are all closely monitored and controlled by sophisticated monitoring systems. Such systems are generally based on monitoring of control thermocouples within zones of the various ovens. Although giving 24/7 monitoring capability obviously such data does not give actual product temperature. For years process engineers have been striving to achieve continuous live product temperature monitoring through the process.
Radio telemetry as a technology allows in theory direct data transfer from a data logger out of an oven to a monitoring PC providing such live monitoring. Although well known the technology has rarely been applied to temperature profiling in the automotive paint market. The reasons for this are generally down to the distance over which the signal needs to be transmitted (Oven to QA Office), number of receivers needed to detect a signal out of the oven and the costs associated with configuring receiver units hard linked by cable and needing external power to operate. Even with
expensive RF configuration any data gaps in the process, due to large ovens, faraday gage effects and transient RF interferences can make comprehensive monitoring difficult and non-conclusive.
To overcome the inherent technical limitations of existing RF system on the market PhoenixTM has developed its own unique RF telemetry system. The system has been designed in such a way as to overcome the inherent challenges of the automotive paint line. The two-way RF system not only monitors temperature data recorded by the data logger but allows direct control of the data logger itself. The data logger can be reset or downloaded direct from the oven
without any need to access the data logger inside the thermal barrier. The RF signal transmitted out of the oven is passed along a series of repeater units back to the main coordinator connected to the monitoring PC. The repeater units are powered by battery and are not physically linked by any cable. As such they can be positioned where needed and moved with ease (No expensive infrastructure installation costs). For a paint line it is possible therefore that each oven has its own allocated repeater(s). A very valuable feature of the system is a unique ‘catch up feature’. Any missed data from RF black spots is automatically re-transmitted as soon as the RF signal is re-established ensuring that profile data is complete.
PhoenixTM RF telemetry temperature monitoring system key components: (i) Multi-channel data logger and customized paint thermocouples (ii) TS04-135 Thermal Barrier (iii) Remote repeater(s) used to transfer data logger RF data signal back from Ovens to monitoring PC
• Data Logger and Thermal Barrier choice (6 to 20 Thermocouples)
• Extensive Thermocouple range
• ATEX approved options
• Real Time RF Telemetry options
• Full UK service and calibration support
• Thermal View or enhanced Thermal View Finishing software
- Match Analysis Tools to suit.
• CQI-12 Temperature Uniformity Survey solution options
Innovative Video Capture Thru the operating oven
• Detect paint runs, chips and defects
• Spot transport problems
• Identify oven damage
• Locate dust and inclusion risk areas
Combining RF telemetry with the performance of the profiling system it is possible to monitor the complete paint process in one continuous run. This approach eliminates a lot of the intensive labour required for traditional manual profiling of each oven. System set-up installation and retrieval for each oven is tedious, time consuming, not forgetting the travel time from oven back to the QA office to download the profile data.
The Thermal barrier (TS04-135) provides up to 5 hours protection @ 200 °C. So, with the delays between ovens (cooling period) it has enough thermal protection to allow all coating ovens to be run in one profile pass. With RF operation the data is collected automatically, and process issues can be detected immediately. With a battery life of up to 1000 hours and 3.8 M data point memory in theory the system could run continuously in RF mode for a complete manufacturing week (6.5 days).
It is potentially feasible that a car test body, fitted with a RF system and thermocouples permanently fixed in place could run continuously around automated paint cure loop, performing a daily profile of all cure ovens without any operator intervention, other than programming the insertion of the test body into the product stream.
PhoenixTM Thermal View Software allowing live monitoring of the RF transmitted temperature profile run and post run analysis and full reporting using key analysis features such as the Phoenix Factor Paint Cure Index.
Why not consider RF technology as a means of automating your thru-process product temperature monitoring making it easier, quicker, less labour intensive and live!
For more information: Contact Dr Steve Offley - Product Marketing Manager
Telephone: +44(0)1353223100
Email: Steve.Offley@phoenixtm.com Visit: www.phoenixtm.com
Automated Water & Effluent Ltd have been supplying process control equipment to the metal finishing and surface finishing industry.
We have an in-house team of qualified engineers able to design and build control panels and process equipment specifically to fit your requirements.
A wide range of our control instrumentation, dosing pumps and chemical process equipment is available on short delivery.
• Custom Designed & Built Control Panels
• pH & Redox Controllers & Electrodes
• Conductivity Controllers
• Liquid Level Controllers
• Open Chanel & Magnetic Flow Meters
• Data Loggers
• Dosing Pumps & Tanks
Call today for a quote or to inquire.
Measure the adhesion of coatings to metal, wood, concrete and more
n Impact and scratch resistant color Touch Screen display with keypad
n Wirelessly connect the PosiTest AT-A to your smart device using our free app
n Record the results as pass/fail and the nature of fracture cohesive, adhesive and glue failures
The right paint and finish can play a surprisingly important role in protecting your fleet from extreme weather conditions. Dan Szczepanik, Global Marketing Director for the Automotive Finishes division at Sherwin-Williams, explains why.
As the worst of the winter weather starts to bite, fleet managers around the country want to know that their vehicles are winter-ready for the months ahead.
Mechanical maintenance plays a big role in ensuring that fleets are able to withstand frost, snow and ice, as well as the salts and chemicals used to de-ice roads. But, surprisingly, the right paints and finishes can also make a significant difference.
Our advice to fleet managers is to look for any dents, imperfections or cracks in the bodywork of their vehicles. Salt and chemicals can get into these cracks, attack the surface and cause corrosion.
Fortunately, in the U.K., sodium chloride (salt grit) is the most commonly used chemical de-icer because it’s suitable for most U.K. winter conditions, is relatively
low-cost and is readily available. Traditional rock salt only causes corrosion when it’s wet and doesn’t absorb a lot of moisture. This means it causes less damage than the chemical slurries used in countries where winter weather conditions are more severe. These slurries stay wet a lot longer and absorb moisture from the air, causing corrosion over a longer period of time.
Even though salt doesn’t cause as much corrosion as chemical slurries, it still poses a risk to your fleet.
To minimise this risk, it’s important to repair any damage now, choosing quality paint and finishes that will give you the processing speed and durability that will save you money over the long term. Bear in mind that the cost of paint only accounts for about 5-10% of the total cost of bodywork repairs. The rest of the cost lies in labour, energy and time.
Inexpensive paint may seem like a good choice but it will take longer to apply and process, costing you more in labour and keeping the vehicle is out of action for longer. It also won’t offer the durability of a quality paint.
Taken together, these two factors mean that you could end up spending 33-40% more over the lifetime of a vehicle than if you had used a quality coating in the first place.
Sun damage may not be top of your list of worries this season, but snow and ice are not the only weather that can take the shine off your fleet. UV rays can cause colours to fade and even change, causing your bright-red van to turn pink or purple.
Again, a quality paint will give you the colour retention you need if you want your fleet to stay true to brand. Avoid paints that use industrial-grade pigments and instead look for finishes using automotive-grade finishes. In addition to pigments, look at the overall chemistry of the coating. Acrylic urethane topcoats mixed with automotive-grade pigments will give you a lasting glossy finish, come rain, snow or shine.
Finally, if you’re keen to fine-tune your body shop and maintenance operations, a professional body shop audit by a trusted paint supplier can help you optimise every step of the process from cleaning to curing. You may think you’ve already reduced downtime and operational costs as much as possible, but in our experience, however good your processes are for maintaining fleet exterior integrity, there’s always room for improvement.
Remember, your fleet is the rolling billboard for your business, and first impressions count – with vehicles as well as people.
To find out more about Sherwin Williams premium paints and finishes that keep fleet vehicles looking their best, visit https:// industrial.sherwin-williams.com
Alongside the high-quality of design and product, a large part of the Junair ethos have always been the pursuit of process efficiency, energy saving and reduction of cost for our customers. With the recent push for carbon reduction, Junair are leading the way within the industry in providing fully electric paint finishing plant.
Junair have recently installed a number of electric process ovens, spray booths and early next year will be delivering the UK’s firsts fully-electric powder coating line, including spray pretreatment, drying and curing ovens.
The client has set a global target for carbon emissions across all of its operations of net zero by the year 2030.
In order to achieve this, the client reviewed all energy usage across the site, with a view to reducing power consumption, eliminating gas consumption, and installing renewables as a local source of energy for the plant.
The existing paint line is currently responsible for over 80% of total gas usage and nearly 60% of the overall energy consumption for the site. It is therefore the key focus for energy reduction and ultimately achieving the global goal of net zero carbon emissions by 2030.
Junairs flagship spray booths and spray booth ovens, including the 1 series, 3 series, 5 series and commercial booths are now all available with electrically heated air handling systems. These booths are all available with all our standard energy saving features, which, when combined mean we can supply a combination spray booth with power supply as low as 63A. Our standard energy saving features include:
The original auxiliary air movement assisted drying system, which can reduce drying times by up to 40%. In turn reducing running costs and increasing product throughput. Designed to minimise dust contamination QADs also provides excellent temperature uniformity and allows product to come to temperature faster than with rival systems.
Junair are the UK’s number one supplier of paint finishing equipment, offering the most energy efficient and lowest full life cost of any system on the market.
Experts in the design, manufacture and supply of:
• Paint and powder coating systems
• Dip and spray pre-treatment
• Drying and curing ovens
• Overhead and floor mounted conveyors
Contact us today for more information or to discuss your requirements.
During periods of inactivity, between spraying or baking cycles, Junair booths automatically enter a reduced power mode which prevents unintentional energy use. This feature has exceptional energy saving over the 20 years life expectancy of a booth. This feature allows Junair to supply a booth with one of the lowest whole life costs of any booth on the market.
On resuming spraying the booth will automatically revert to 100% exhaust.
Junair booths have automatic recirculation of 90% of air volume during Flash Off (QADs), BAKE and ECO modes, dramatically reducing energy consumption for most of the booth operation.
Junair booths are fitted as standard with LED lighting for reduced energy use and extended life. Working with industry leading component manufacturers, Junair have developed a class leading LED light solution with optimised light levels at the point of painting, excellent colour rendition, with a suitably diffused light to reduce dazzle, and located to minimise effects on cabin airflow. These are a booth
specific, highly optimised flat LED solution, not an off the shelf LED tube replacement
Lighting is automatically controlled and is turned off when not required
An advanced PLC and HMI based control system which allows recipe based bake cycle control to ensure
each bake profile is optimised for temperature and time according to paint systems being used. Air speeds are automatically varied throughout the process to meet the process requirements
High visibility LED lights on the front of the booth clearly show the booth mode operation for ECO, SPRAY, QADs, BAKE to allow the painter and paint shop manager to have excellent visibility for all operations
Junair Ovens and booths, are fitted with variable speed fan controllers (Inverters), which allow the fan speeds to be set on commissioning for optimum performance and the lower energy usage.
Variable speed drives also allow ECO-ACTIVE automatic airflow control for the thermal process within the iSystem control package.
The option is available to add heat recovery to Junairs electric spraybooths and ovens
Cross plate heat exchangers allow recovery of energy from waste exhaust air and transfer of that energy to pre-heat the clean replacement input air prior to it getting to the heating system. The system includes additional air filters to remove any particulate which has passed the booth extraction system to allow the system to maintain efficiency over the system life.
The system works on Fuel Saver/ bake/spray modes. Expected energy saving to heat the booth are in the region of 60%.
specialised frame and panel design, which allows us to maintain a cool exterior, whilst achieving a working internal temperature of 425°C
Heat recovery systems when fitted to our ovens can be used to assist the pre-treatment heated tanks among other processes.
Junair have recently supported several customers with the supply of electric spray booths and ovens to the advanced AMS2750 specification for aerospace furnace applications. This specification relates to the control functions and for the recording and temperature uniformity for industrial thermal processing equipment.
Three recently supplied AMS2750 ovens (pictured) were supplied to one of our aerospace customers based in Scotland. These ovens are supplied as electrically heated, and with a comprehensive air distribution ductwork system. These ovens have a
When mapping the ovens, Junair carry out a detailed multi-point temperature uniformity survey, with a minimum of 9-thermocouple positions. This allows us to correctly balance airflows and heat distribution to ensure any thermal process requirements are met within the whole area of the booth or oven.
Where a conveyor has been supplied the equipment will then have a full through-process temperature profile carried out.
Temperature uniformity is a critical factor in all heated paint and powder coating processes, and it plays a crucial role in determining the quality and consistency of the final product.
AMS2750 provides a good guide by utilising the furnace classes which
range from class 1-6 (±3°C to ±28°C). Whilst Junair equipment as standard can achieve some of the highest uniformity standards, to achieve the most stringent standards equipment is typically supplied with electric heating with P&ID control. Electric heating not only delivers the benefit of a sustainable green process, but it also allows for a more accurate control of temperature.
If you are in need of high quality, efficient paint finishing or heat process equipment for your operations, Junair are here to assist. Our extensive range of reliable and efficient machinery is designed to meet the demands of your business. Whether you're looking for specific equipment, need a custom solution, or simply want to learn more about our offerings, we're just a call or click away. Contact us today, and let's find the right equipment to power your success!
Telephone: +44 1706 363 555
Email: sales@junair.co.uk
Visit: www.junair-spraybooths.co.uk
Cyclomix® Evo, the industry-leading solution for 2K & 3K mixing and dosing, is now available for OnSite Demonstration as a portable unit with cart, delivering precision, flexibility, and enhanced productivity directly to your production line
The Cyclomix® Evo ensures perfect mixing and dosing with an accuracy of +/- 1%, thanks to its patented injection system. It supports a wide range of materials, including waterborne, solvent-based, acid, epoxy, and polyurethane paints, making it a versatile solution for various production needs.
This system maximizes productivity with its dual circuits that allow rinsing and priming during production. Its intuitive interface requires only two minutes of training, enabling quick onboarding for operators and seamless integration into your workflow.
The Cyclomix® Evo can reduce your operating costs and mixed paint waste, thanks to the «Paint Optimization» function, and allows monitoring of Production and Maintenance Data through a smartphone. The system has the capability to retrieve and download production and maintenance data to optimize your production monitoring and is perfectly adapted for use with acid catalysts, solvent based and water based materials.
405 seconds was 170°C, a temperature which could fail to achieve full curing of the powder.
A retrofitted, infra-red booster oven from Excelitas Noblelight (formerly Heraeus Noblelight) has allowed South Staffs Industries Ltd (SSI)to increase throughput and improve quality on the powder-coating line at their Tipton LPG gas cylinder re-qualification factory.
SSI repairs, refurbishes and requalifies low pressure propane and butane cylinders and ammonia, nitrogen and refrigerant gas cylinders to British Standards, with facilities to requalify cylinders up to 50 Bar. Refurbishment of LPG cylinders, which typically takes place after 15 years in service, includes making cylinders gas-safe before processing, hydraulic testing, removal of old paint, shotblasting, zinc coating, powder coating and curing. screen printing, valve fitting and testing and weighing cylinders for tare weight.
Powder coating is carried out to restore the colour scheme of the original cylinder manufacturer and, historically, the coating has been gelled and cured in a gas-radiant oven, which emits long wave infra-red. However, this oven could prove inefficient and SSI decided to investigate ways to improve the overall efficiency of the process and increase the powder-coating line speed.
On the advice of powder-coating specialists NDK Finishing Systems, SSI contacted leading infra-red experts Excelitas, who carried out preliminary investigations on the existing gas radiant system, using a Datapaq oven tracker. These established that the maximum temperature achieved after
After carrying out tests on a range of cylinders at its Neston Applications centre, Excelitas proposed that an electric, 156kW medium wave infra-red booster oven should be retrofitted in front of the existing gas radiant oven. This has four zones to cater for the different size of cylinder. Subsequent Datapaq readings have shown that the booster oven very quickly raises the body temperature of the coated cylinders so that dwell time in the gas radiant oven is substantially reduced, allowing line speeds to be increased by 19%. In addition, optimum curing temperatures can be achieved consistently, leading to quality improvements.
As Ryan Cummings, operations director at SSI, comments, “The booster oven has allowed us to significantly increase our powder coating efficiency, with potential for further benefits once other parts of the process are improved.”
Excelitas Technologies® is a leading industrial technology manufacturer focused on delivering innovative, marketdriven solutions to meet the critical sensing, detection, imaging and illumination needs of our OEM and end-user customers. Serving a vast array of applications across medical, life science, industrial, semiconductor, smart building, aerospace and defense sectors, Excelitas stands committed to enabling its customers’ success in their many various end-markets. The Excelitas team consists of more than 7,500 professionals working across North America, Europe and Asia to serve customers worldwide.
Noblelight® counts itself among the market and technology leaders worldwide for specialty light sources with wavelengths from ultraviolet to infrared for industrial, scientific, and medical applications. With operations located across Europe, Asia and the United States, Noblelight designs and manufactures infrared, flash and ultraviolet emitters, systems and solutions for applications in industrial manufacturing, environmental protection, medicine and cosmetics, research, development and analytical measurement techniques with a high level of vertical integration.
Telephone: 0151 353 2710
Email: ian.bartley@excelitas.com
Visit: www.excelitas.com
Streamline Your Manufacturing: Simplify processes and boost productivity
Sustainability at the Core: Reduce energy consumption and water usage without compromising on quality
Cutting-Edge Chemicals: Ensure superior protection and unmatched longevity for your metal products
Efficiency Meets Excellence: Transform your Powder-coating Process with Metavate!
SYNOTHERM® heat exchangers allow for use in heat exchange loop systems through which a hot liquid (such as hot water, steam, hot oil) is passed through the panel. Heat energy from the hot liquid then transfers through the internal surface of the panel into the process solution tank. The spotwelded, perforated design creates turbulence through the channels, ensuring heated liquid molecules all touch with the internal surfaces of the panel therefore increasing heat exchange efficiency. Heat losses during the production process are compensated. A process generated heat input (e.g., from ambient heat, rectifier, or an exothermic reaction), can be compensated with the aid of heat exchangers by passing a cold liquid (e.g. cold water, glycol) through the panel.
SYNOTHERM® PFA-coated plate heat exchangers exhibit a metallic base build. The compact, lightweight and pressure-resistant design of the metallic base enables a long service life and high operational reliability of the heat exchanger.
In a multi-stage coating process, a fluoropolymer coating is applied to the metallic base build.
Zero porosity of the coating is verified by conducting a 100% high voltage test.
Thanks to the PFA-coating, SYNOTHERM® PFA-coated plate heat exchangers feature excellent chemical resistance and anti-adhesion properties, thus fulfilling two key requirements for use in chemical apparatus engineering. They are suitable for tempering highly acidic process liquids.
The anti-adhesive fluoropolymer coating ensures homogeneous heat transfer in conditions where incrustations, build-ups and deposits restrict the heat transfer capacity of heat exchangers. Fluoropolymers have significantly better heat transfer properties than other coating materials and plastic heat exchanger.
• low space requirement
• high thermal and mechanical stability
• easy to clean
• custom-made dimensions
+44 / 1509 673 656
• for process liquids with strong acids
• anti-adhesive coating made of thermal conductive fluorpolymer
significant reduction in encrustations
• different dimensions
• highest chemical resistance
• several planar layers of tube coils made of PFA large heat transfer surface to volume ratio high temperature- and pressure resistance
The incrustation tendency from media that cause heavy incrustation, such as zinc phosphates, is reduced considerably.
Easy cleaning and extended maintenance intervals reduce maintenance costs and ensure the availability of your plant in the long term. Falling parts or sediments cannot deposit on or get caught in the heat exchanger body.
The coated plate heat exchangers have a high surface density. This means that a large heat exchanger surface area (in m2)
can be provided in relation to the required construction volume (in m3).
The total installation depth (see image) is 61 mm (11 mm heat exchanger body + 50 mm spacer to tank wall). The space saving reduces the size and cost requirement for tanks. More space is available for other components in the tank or plant (pumps, rectifiers, barrels etc.).
Telephone 01509/673656
Email: sales@gmfequipment.co.uk
Visit: www.gmfequipment.co.uk
FD Series Packaged Oven/Dryer Burners
•Speci cally designed for process air heating applications in convection ovens and dryers
•High turndown/short ame lengths providing accurate process temperature control
•High ef ciency gas + air modulation, gas only modulation and simple high/low control options
•Heat Input Range: 9 kW – 1550 kW
TX Series Gas Fired Process Tank Heating Systems
•High ef ciency (80%+) heating of all types of spray and dip process tanks
•Compact high ef ciency small diameter immersion tube heat exchangers occupying minimum tank space
•Accurate performance modelling using Lanemark TxCalc design software
•Heat Input Range: 15 kW (1½") – 1150 kW (8")
Midco HMA Series Air Replacement or “Make-Up” Air Heating Burners
•Direct red, high ef ciency burner systems, for high volume air heating applications such as paint spray booths, ovens and dryers.
•Supplied either as Midco burner heads for OEM system integration or as Lanemark DB or FDB complete packaged systems including modulating gas valve trains and controls
•Wide range of ring rates to suit alternative temperature rise and air velocity system requirements
•DbCalc system design software
EnviroTech Europe supply approved vapour degreasing solvents, solvent cleaners and corrosion protection products. We offer a range of formulations tailored to your industry, which are cost effective, energy efficient, safe for operators and the environment.
We are pleased to introduce our range of products in our 2025 products brochure: https://www.envirotecheurope.com/brochure
Our products are used in the following industries:
Avionics and Aerospace
Electronics and Electrical
Environmental
General Cleaning
Industrial and Manufacturing
Marine and Maritime
Mechanical Engineering
Medical Device Manufacturing
Military
Motorsport
Oxygen Cleaning
Power Generation
Railways and Automotive
In December 2022, 3M™ announced their plans to stop producing per- and polyfluoroalkyl substances (PFAS) in its product line. Final order dates have now
been set for March 31st 2025, and the supply of these products will end on December 31st 2025. This phase-out affects the following 3M™ product lines:
3M™ Novec™ Engineered Fluids
3M™ Fluorinert™ Electronic Liquids
EnviroTech Europe offer drop-in replacements for all 3M™ Novec™ cleaning and degreasing products and provide free on-site visits, technical support and cleaning trials when required. We can provide a full assessment of your current precision cleaning process to put in a plan to help ensure a seamless transition. We have already successfully transitioned many Novec™ users globally to our ProSolv® Direct Replacements range.
All products are manufactured in the United Kingdom and available on short delivery times through our dedicated team of qualified distributors worldwide. We can help with productuse and offer advise on legislative changes, ensuring your metal cleaning and corrosion protection solutions stay within regulatory boundaries.
We can supply Material Safety Data Sheets, independent laboratory reports, product samples and further assistance. EnviroTech Europe is accredited to ISO 9001:2015 for marketing and distribution of specialist metal cleaning and corrosion protection products.
Visit www.envirotech-europe.com/ applications-and-case-studies for information about uses and applications for all EnviroTech Europe products.
For more advice, please telephone us on +44 (0) 20 8281 6370 or use our website contact form. All products are supplied and supported by EnviroTech Europe Ltd. Manufactured in the United Kingdom and available on short delivery times through our dedicated team of distributors worldwide.
After purchasing a MWX400 system in 2020, Vixen CNC experienced such an improvement in cleaning efficiency that the team ordered another system for their factory in Snowdonia. Vixen CNC has seen a significant increase in demand for their services over recent years and needed the additional machine due their use of both ferrous and non-ferrous metals and the different process requirements of the two applications.
Repeat business is key to the global success of MecWash Systems over the past three decades. Designing and building the highest standard of component washing systems is the initial part of the customer experience, but providing long term support is just as important in cementing the
relationship and keep the customer happy with their purchase and ongoing use.
Jake Wood, managing director of Vixen CNC, commented: “The MWX400 systems have transformed the washing capability and overall productivity at the factory. The communication and servicing from MecWash have been excellent, which combined with the effectiveness of the cleaning, made the decision of investing in a second machine a simple one.
“We replaced a tunnel wash system with two MecWash MWX400 machines. Each machine uses a specific cleaning process, one for ferrous metal and the other for non-ferrous metals. The initial MecWash MWX400 system in 2020 considerably decreased the amount of manual drying that had been both costly and time consuming. Overall, the MecWash systems have provided superior cleaning results, in faster time, all with reduced manpower,” said Jake.
The MWX400 system is a state-of-theart industrial parts washer, manufactured at the MecWash factory and lab in Tewkesbury, Gloucestershire. The systems created by MecWash are popular with machining companies due to the incredibly high standards in surface finish and cleanliness.
Alan Atkinson, sales manager, said: “Having recently revisited Jake and his team, I fully understood the situation and the requirements at Vixen CNC. After deep discussions, we knew Vixen CNC would benefit from another MWX400 system. The initial MWX400 system was specifically designed for cleaning ferrous parts, using an inhibited rinse. The second MWX400
was designed specifically for nonferrous parts, with a clean water rinse.
“The process starts with powerful ultrasonics, which are essential to carefully clean the intricate shapes and blind holes, contaminated by oil, swarf and fine particles. The MWX systems boasts four ultrasonic rod transducers with single or mixed frequency (25kHz and 40kHz). The ultrasonics create large amounts of localised cleaning energy, dislodging any contamination.
“The rigorous wash stage of the MWX400 includes ultrasonic, flood and spray processes. After the wash stage, the components are rinsed, firstly with an ultrasonics stage, followed by the flood and spray rinses, resulting in a polished finish,” said Alan.
John Pattison, managing director of MecWash, said: “We were delighted to receive the follow up MWX400 order from Vixen CNC. The MWX series represents the pinnacle of the parts washing and degreasing systems available. The original system had a sizable effect on the component cleaning capacity. This second order in such a relatively short period of time shows how confident Vixen CNC are with MecWash.
“The machines purchased by Vixen CNC will last for many, many years and we will support them throughout. We believe the ‘MecWash Approach’, our commitment to our customers over the entire lifecycle of the system, is greatly valued and is a key factor in winning repeat business,” said John. Telephone: +44 (0) 1684 271600 Email: enquire@MecWash.co.uk Visit: www.mecwash.co.uk
At Fraser Technologies, with our long history of providing both cleaning equipment and fluids, we recognised a gap in the cleaning machine market. Where traditional solvent systems like Perc or Hydrocarbons often fell short, either due to limited applications or high maintenance costs.
In response, we’ve taken a bold step to introduce not just another machine, but a revolutionary solution: The Newborn.
This cutting-edge, solvent-based cleaning system delivers a fully sealed design with *near-zero emissions, offering the ultimate combination of adaptability, efficiency, and sustainability. Engineered with advanced, patented cooling technology, the Newborn brings a modern twist to traditional component cleaning processes, making it ideal for industrial component cleaning. It is a futureproof, environmentally conscious solution that redefines the standards of degreasing systems while significantly reducing the environmental impact.
With the Newborn, Fraser Technologies is pushing the boundaries of what’s possible in industrial cleaning. The Newborn machine stands out in the market, offering a superior cleaning solution that meets the needs of today’s industries while anticipating the demands of tomorrow. When considering older technologies requiring retrofit to change a chemical, it is worth considering that the costs to retrofit old systems could be close to the cost of new “Next Gen” Newborn system.
* PCE – 28 g/hr fugitive emissions
For Engineers and Operators:
Ease of Use: Automated processes minimise manual intervention.
Reduced Maintenance: Runs 24/7 with minimal downtime.
Safety: Sealed system reduces operator exposure to harmful chemicals.
Versatility: Quick solvent switching without additional retrofitting.
For Purchasing Managers and Decision Makers:
Cost Efficiency: Lower total cost of ownership due to reduced chemical use and waste.
Investment Protection: Future-proofed to adapt to regulatory changes, avoiding costly upgrades.
Competitive Pricing: New technology has significantly lowered capital costs, making high-spec systems more affordable.
For Environmental and Safety Officers:
Low Emissions: Sealed design and patented cooling system minimise environmental impact and comply with safety regulations.
Sustainability: Uses modified alcohol, a non-carcinogenic solvent that supports green initiatives.
Minimal Waste: Continuous solvent recycling reduces hazardous waste output.
Newborn Applications:
High-Volume Cleaning: Handles high oil loads, complex geometries, and blind holes.
Industries Served: Aerospace, automotive, precision engineering, and other high-standard industries.
Component Types: Screws, fasteners, machined parts, and complex components.
Additional Services Offered:
Comprehensive Support: Waste management, servicing, and chemical supply managed in the UK for rapid response.
Training & Technical Support: On-site training ensures optimal performance and safety compliance.
Customisation: Tailored solutions for industry-specific needs.
With over 55 years of expertise, Fraser Technologies offers more than just equipment. Understanding that each client’s needs are unique, the company provides a comprehensive suite of support services designed to ensure optimal cleaning performance and customer satisfaction.
Our Services Include: Evaluation & Cleanliness Testing: Assessing customer needs through rigorous analysis.
Process Audits & Optimisation: Identifying efficiency improvements to reduce costs.
In-House Trials & Demonstrations: Hands-on testing before investment decisions.
Just-in-Time Delivery & Service Plans: Ensuring timely product availability and tailored maintenance support.
Fraser Technologies provides a full spectrum of services that ensure optimal results for our clients.
Find out more about The Newborn and contact us today.
https://www.frasertech.co.uk
Innovation Oxsilan®: high-performing and suited for multi-metal applications
Technological turning point in metal pretreatment: The eco-friendly Oxsilan® technology offers long-term corrosion protection and excellent paint adhesion – and at the same time more safety, economics, flexibility and sustainability. The thin-film technology is free of heavy metals, suited for multi-metal applications and allows an unlimited throughput of common metal substrates. Expect more from Chemetall: innovative technologies, environmentally-sound processes, comprehensive technical support, a global network and dedicated people – inspired for your success.
www.chemetall.com/oxsilan · oxsilan@chemetall.com
www.chemetall.com
The surface of painted profiles, which may be scratched when manipulated during processing, should already be provided with protective film before initial processing. Customer claims due to damaged surfaces are reduced to a minimum as a result. Before foiling the surface is checked and, as a result of the film, the quality is maintained up to the delivery of the finished product. The film remains on the surface during all machining processes and is usually only removed after the installation of a window.
The profile, which is inserted manually or via powered roller conveyors into the filming machine, is conveyed with a drive up to the knurling machine. Usually only one side is foiled in the process, but two-sided foiling is also possible. The beginning of the profile is detected by the control system, the film is pressed on fully automatically and cut off automatically at the end. The machine itself communicates with the downstream machine to synchronise and optimise speeds. This film wrapping can also be supplied for autonomous applications.
For autonomous applications, different versions are available for one-sided up to four-sided wrapping. The machines can easily be adapted to very different profile shapes.
The profiles are manually inserted or via roller conveyor fed into the wrapping machine. The film (a maximum of 4 pages at a time) is continually being pressed on and cut off automatically at the end of a profile.
In addition to a good throughput speed, high demands are made on the performance of the machine with regard to blistering and the placement of the film on the profile. The film itself also has an impact on its clean attachment. The adhesive power of the self-adhesive, as well as the ultimate elongation of the film, plays an important role in this. Good results can be achieved with an adhesive strength of 260cN / 20 mm and a thickness of 80-100 my. Thinner films are often used as well. In the case of structured colours, films with a significantly higher adhesive strength need to be used. After foiling, it must be borne in mind that the profiles or finished windows are not exposed to direct sunlight, as residues of the film may form in the surface coating as a result.
Telephone: +41 44 926 44 88
Email: sales@muller.ch
Visit: www.muller.ch
Steel Shot (High & Low Carbon)
Steel Grit
Stainless Steel Shot and Stainless Steel Grit (Cr & Cr/Ni)
Chilled Iron Grit
Glass Bead
Ceramic Bead
Fused Alumina Cut Wire
www.ampereabrasives.com sales.uk@ampereabrasives.com
Tel : 0121 244 1809
17 School road, Hall Green Birmingham B28 8JG
High Carbon Steel shot and Grit.
Low Carbon Steel Shot and metal Bead
Stainless Steel Cr and Cr/Ni.
No 5, Queensway Link Industrial Estate
Stafford Park 17, Telford, Shropshire TF3 3DN
Tel: 01952 299777
Fax: 01952 299008
E-mail: sales@pometon.co.uk
Fax: +44(0)1469 571644 e-mail: sales@scangrit.co.uk www.scangrit.co.uk Scangrit
•
• PLANT CONTROL SYSTEMS • DATA MANAGEMENT SYSTEMS
• BARRELS - PROGALVANO ROTOR
• BARREL AUTO LOADING SYSTEMS
• PROGALVANO FILTERS
• SEMI/AUTOMATIC FILTER SYSTEMS
• CENTRIFUGAL DRYERS La ge Range)
• AUTOMATIC DRYING SYSTEMS
• ROTARY PAINTING/LAQUERING
• TOP COATING/SEALING SYSTEMS
• VIBRATORY POLISHING EQUIPMENT
• LUBRICATION EQUIPMENT
• RECTIFIERS Conventional & Pulse
• A/HOUR METERS & DOSING PUMPS
Hot dip galvanizing provides you with long-term protection against rust and corrosion of steel products.
✔ 14 plants across the UK
✔ 1.5mm washer to a 29m beam
✔ 24hr turnaround on request
Scan to find your nearest plant
info@wggltd.co.uk 01902 601944
telephone: 0044(0)1509 237415 fax: 0044(0)1509 264455
•
•
•
•
•
•
RDM Industrial Services Ltd
Parkfield Industrial Estate
Kemp Street
Middleton
Manchester M24 4AA
Tel: 0161 643 9333
Fax: 0161 655 3467
www.rdm.u-net.com.
Contact: Robert Horwich or Geoff Ball
Spraybooths, rooms, ovens, conveyors, pretreatment, powder plant and air replacement units.
Final Cleaning • Spray Wash
In-process Cleaning
Aqueous Ultrasonics
Precision Cleaning • FPI Lines
Degreasing • Anodising
Chemical Cleaning for MRO
Chemical Etching/Milling
E sales@turbex.co.uk
T 01420 544 909
F 01420 542 264 turbex.co.uk
NO PRICE INCREASES FOR 2025
• Ideal for frequent & fast color changes
• High degree of automation for optimum efficiency
• Double-designed fresh powder station for increased productivity