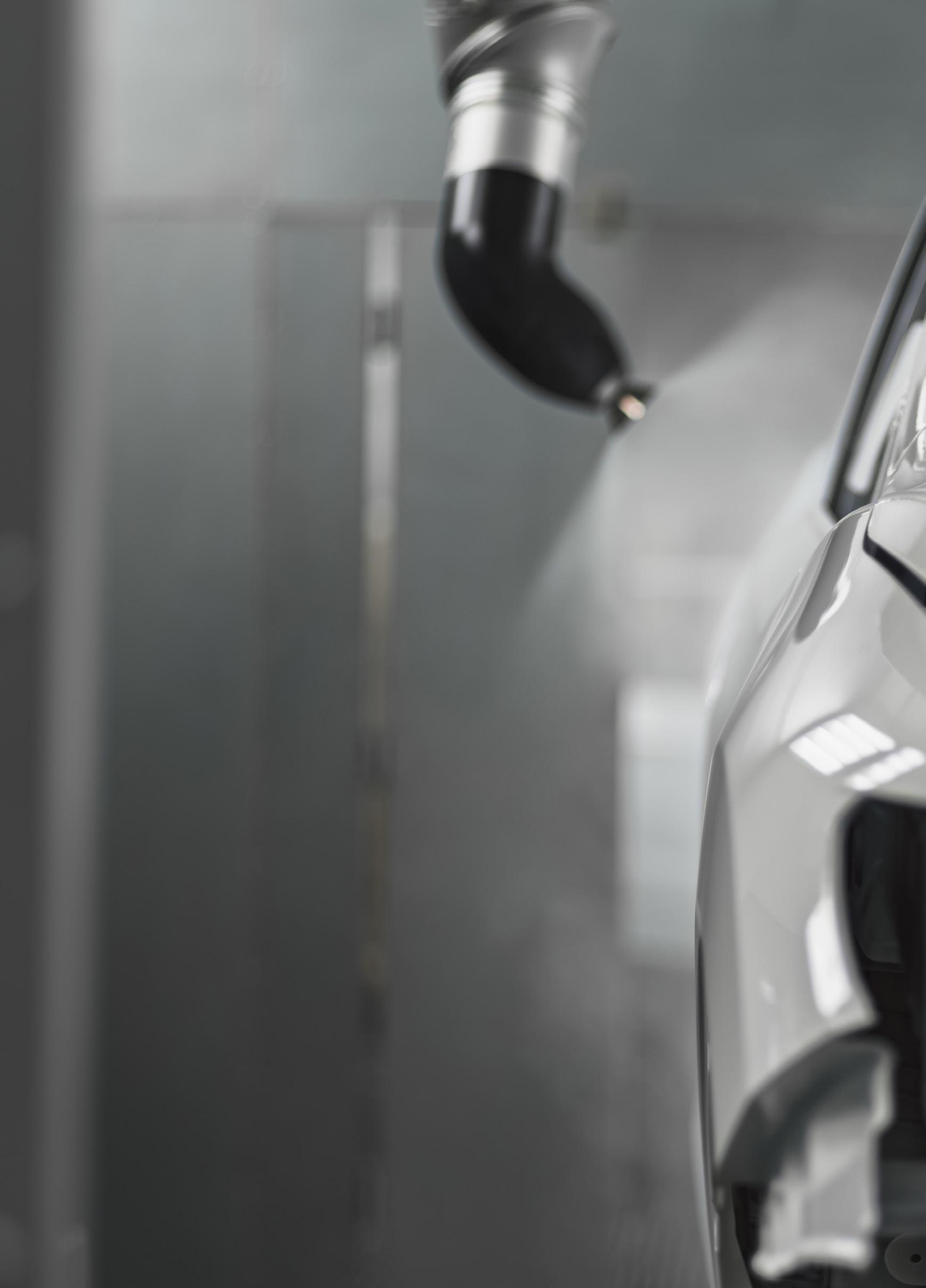
3 minute read
Galvanizing Steel as the Sustainable Choice
As the world’s most recycled material, steel is at the core of a more sustainable economy. Much is being done industry-wide to ensure the manufacturing, treatment, and use of steel is kinder to our planet. And as the main material used in delivering renewable energy (solar, tidal, geothermal, and wind), it’s a real front-runner in achieving a sustainable future.
With an ever-increasing focus and awareness on sustainability – for businesses, communities, and individuals – it’s important that the finish can also keep pace with everchanging demands, offering the same sustainability claims, and that it doesn’t undo all of the progress that the industry has been striving to achieve to date. Since the introduction of galvanizing in the mid-1700s, it’s long become the finish of choice for many due to its ability to offer long-term protection against rust and corrosion, as well as its green properties and process.
Andy Harrison, Sales and Marketing Director at Wedge Group Galvanizing Ltd, the UK’s largest hot dip galvanizing organisation, explains what galvanizing is, why it continues to be one of the greenest protective steel coatings, and the industry advancements that are ensuring it progresses with the times.
“Used across a diverse range of industries, including agriculture, construction, and automotive, as well as by many artists, architects, and sculptors, hot dip galvanizing essentially protects steel objects from rust. The steel object – anything from large-scale steel infrastructure components through to small nuts and bolts – is completely immersed in a bath of molten zinc at temperatures of around 450°C, allowing a metallurgic bonded coating to be formed.
“Galvanizing is inherently sustainable thanks to its process, the resources used, and also the longevity it provides to the steel. And together, it allows for a low-maintenance, long-lasting, low whole-of-life costing material that is strong, durable and can be utilised for a variety of purposes.
Longevity
Galvanizing offers long-term protection of up to 70 years – longer if in the right conditions. Over the years, the coating will continue to remain effective, and unlike other finishes, reduces the requirement for ongoing maintenance, meaning it’s also a cost-effective option.
Coating Toughness
Galvanizing is unique. The hot dip process produces a coating which is bonded metallurgically to the steel. No other coating process has this feature and, as a result, galvanized steel has by far the greatest resistance to mechanical damage during handling, storage, transport and construction – an important factor where steelwork is to be shipped around the world.
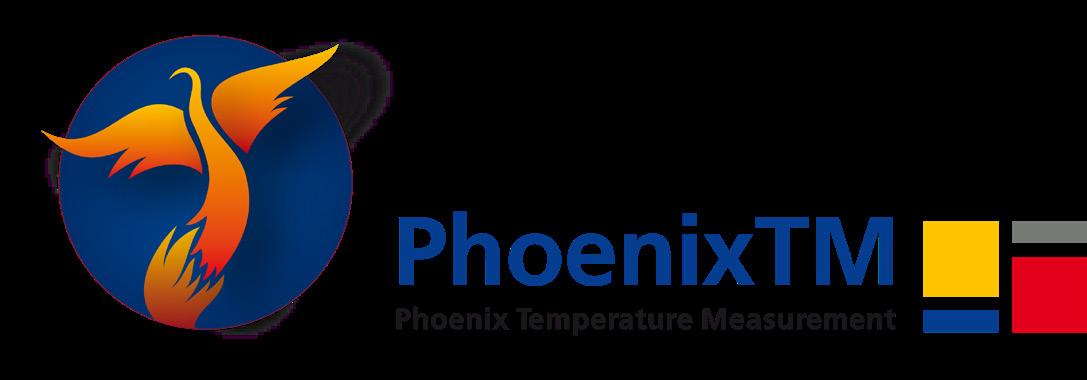

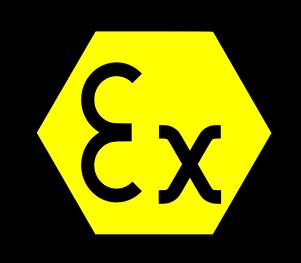
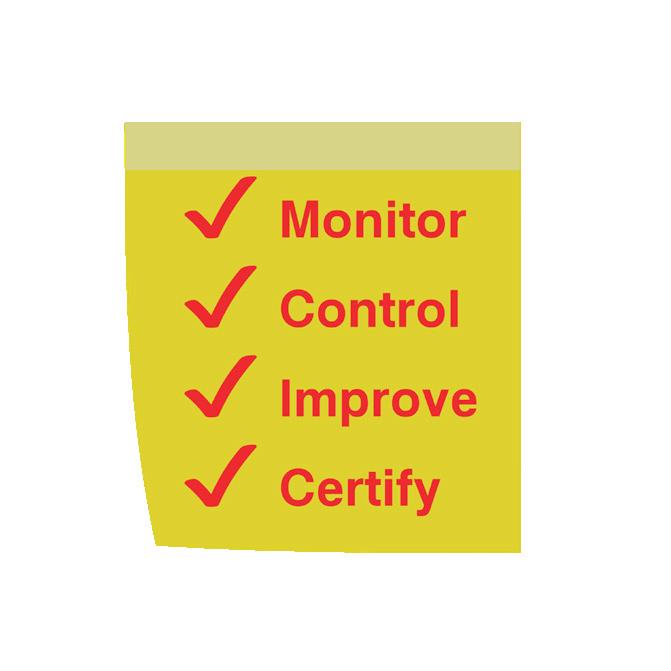

Reduced Waste
Zinc is non-ferrous, which means that any leftover in the galvanizing bath can be used again, without any impact to its physical or chemical properties. Not only does this reduce the amount of wasted resources, but it also ensures that plant productivity and efficiency is high.
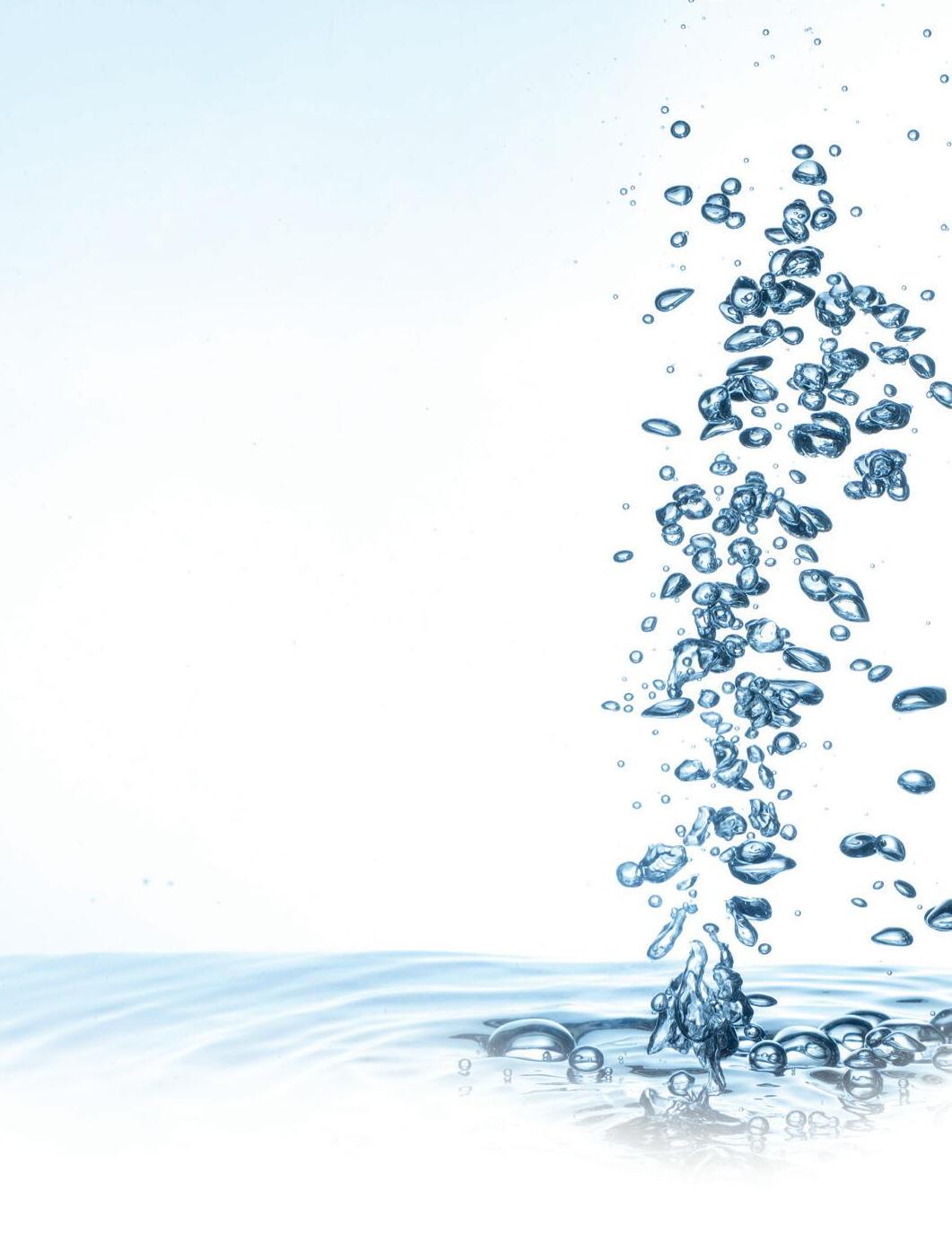
Recyclable
Once galvanized, the life cycle of the steel isn’t harmed or broken, instead it can still be recycled. Or, it can be cleaned down and used again.
“The UK Environmental Act includes provisions that require manufacturers to pay the full net cost of managing specified products and materials at its end of life, to incentivise more sustainable use of resources. But otherwise, there’s little legislation or industry standards regarding sustainability.”
That said, Wedge Group Galvanizing is continually and proactively making improvements to enhance the overall running of the business and implement practices to ensure they’re as sustainable as possible. They’ve continued to innovate and invest across the board to ensure that they continue to meet customer requirements and demands for both sustainability and quality.
Over the past 12 months alone, two of its 14 nationwide plants have received significant investment to upgrade equipment and ensure they’re fit for the future. The renovations have seen major improvements to processing lines, a new de-grease tank, acid tanks and water rinse system, all of which will help to speed up production, improve the efficiency of the plants, as well as increase their sustainability credentials.
In efforts to further reduce waste and promote better use of resources, a bespoke rainwater collection and harvesting system has been implemented across a majority of Wedge’s plants. The rainwater is stored on-site through gutters and tanks, before being recycled back into the galvanizing process. Another example is the re-use of ‘waste’ heat created by the furnaces – to combat this, all plants have installed heat exchanger units to transfer the heat for use in pre-flux and de-grease tanks to improve their overall fuel efficiency and performance.
About Wedge Group Galvanizing Ltd
Wedge Group Galvanizing Ltd is one of the largest hot dip galvanizing organisations in the UK with a history dating back over 150 years. With 14 plants strategically placed across the country, they offer a truly national galvanizing service.
For further information please contact Wedge Group
Galvanizing on 01902 630311 or visit www.wedge-galv.co.uk.
References: www.worldsteel.org/about-steel/ steel-industry-facts www.local.gov.uk/publications/ get-act-environment-act-2021
Our high quality, advanced range of equipment provides the best way to clean paint spray guns or industrial parts. With numerous options, you can be sure that there is a model in our extensive range that meets your cleaning requirements using either solvents or water.
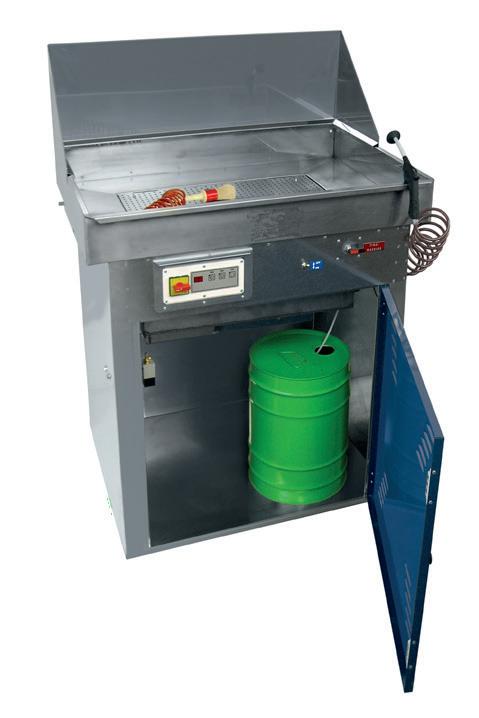
Hot dip galvanizing provides you with long-term protection against rust and corrosion of steel products.
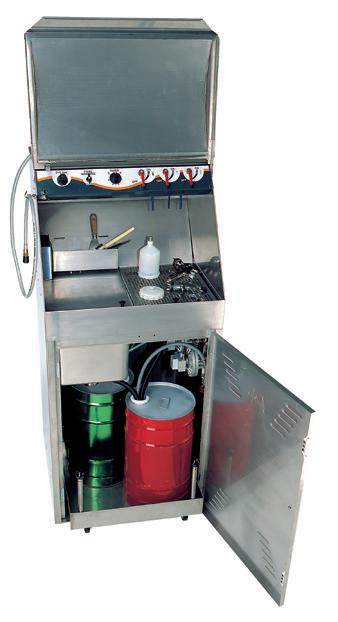
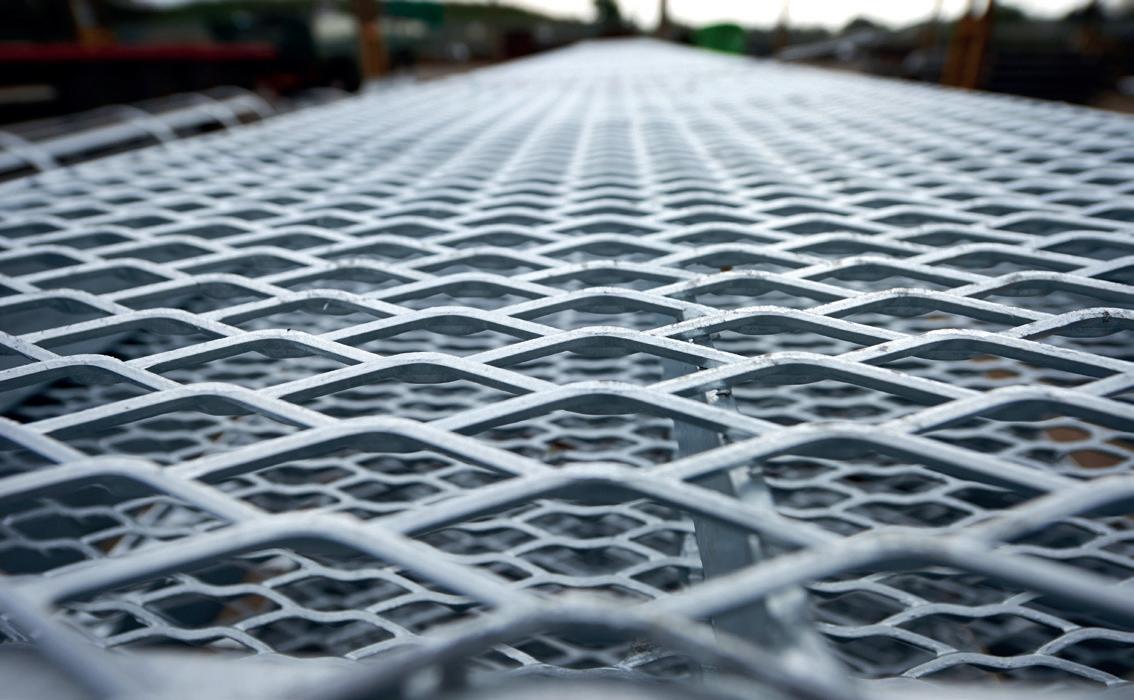
With 14 plants across the UK, Wedge Group
Galvanizing is the UK’s largest hot dip galvanizing organisation offering a national service, collection and delivery and 24hr turnaround on request. The group can process anything from small components to 29m structural beams.
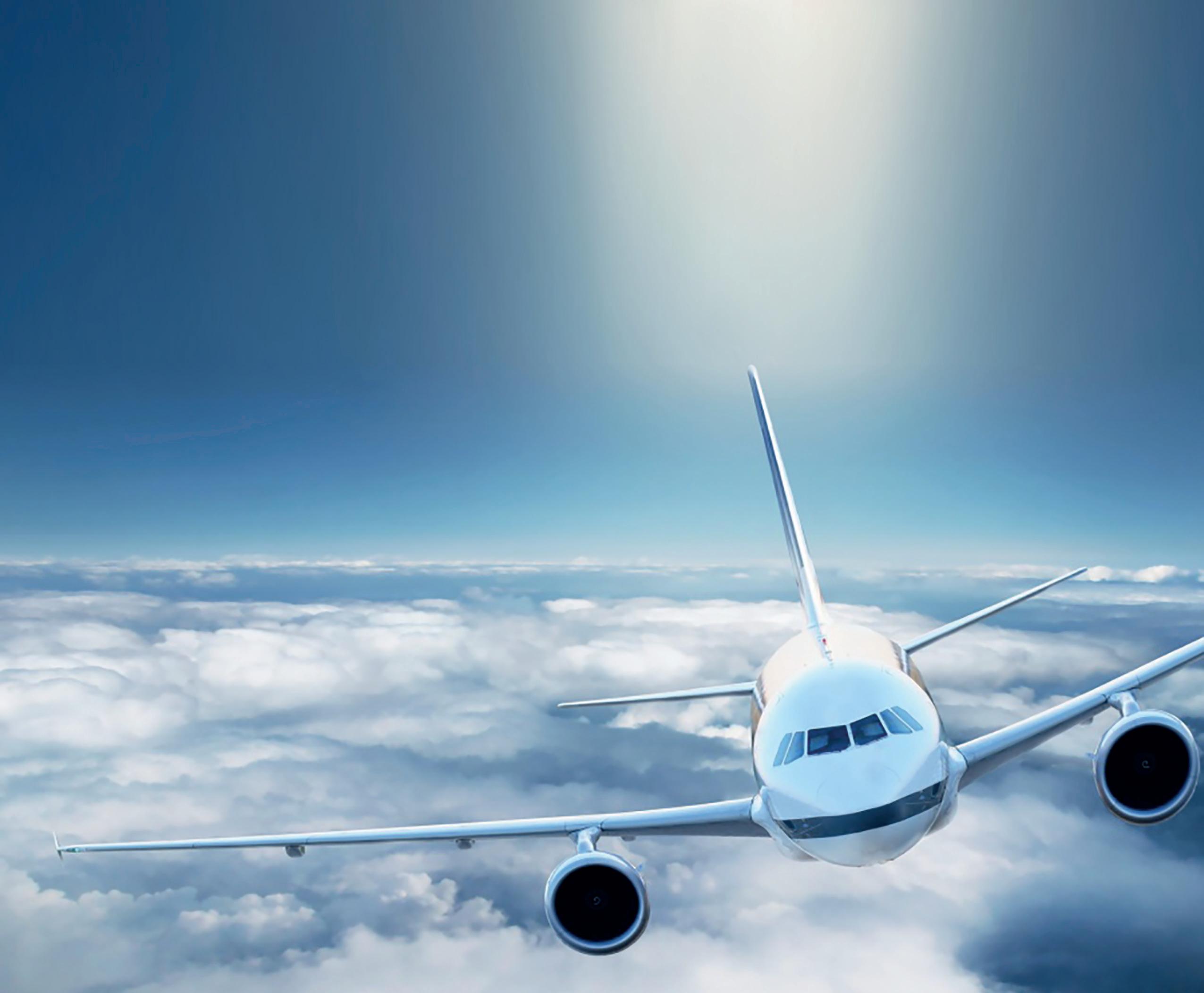
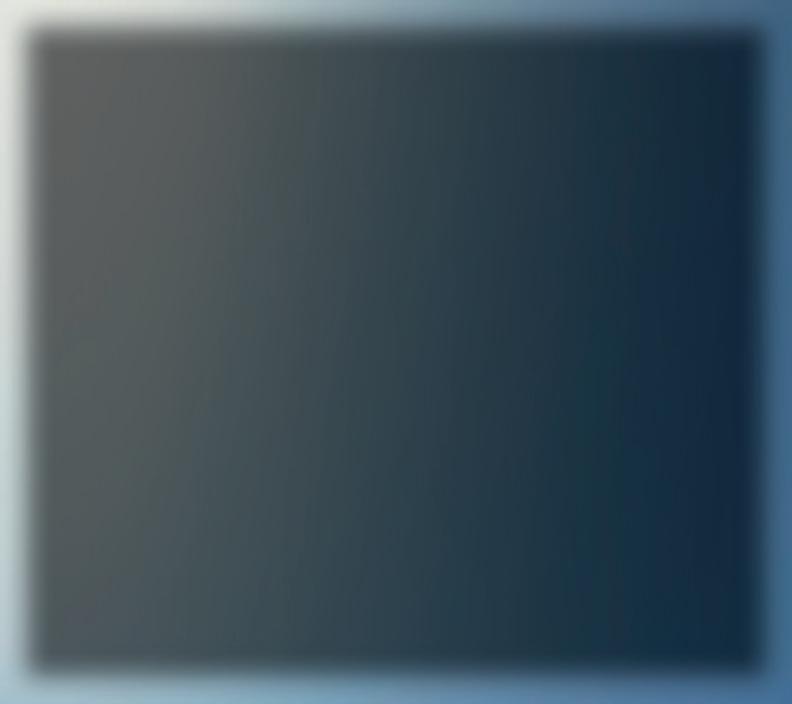

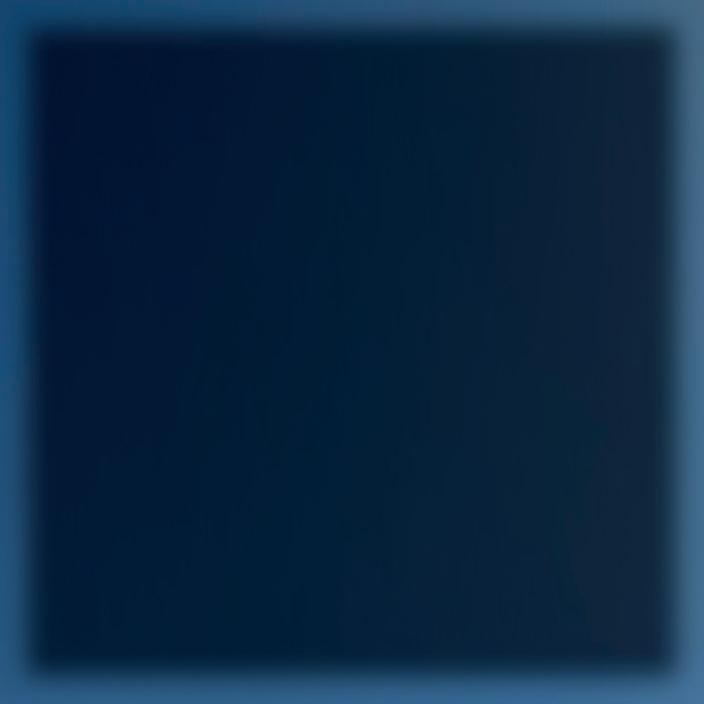
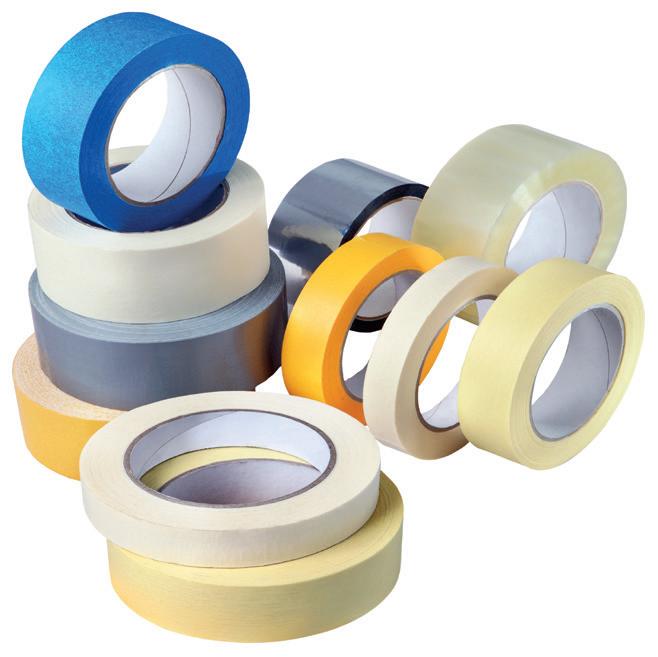
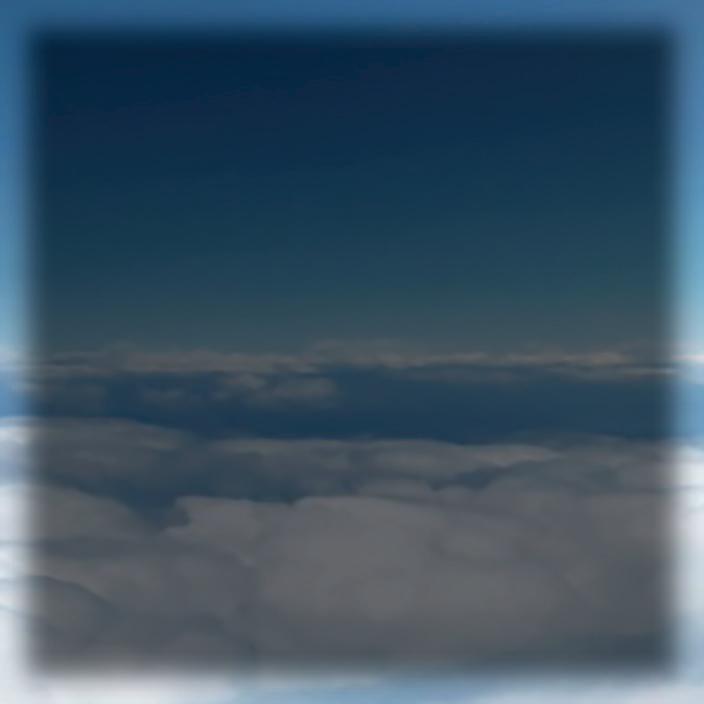
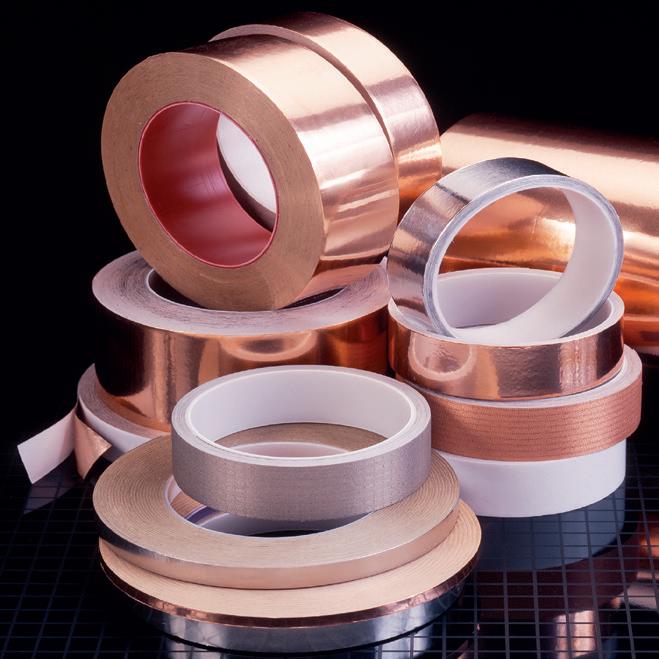
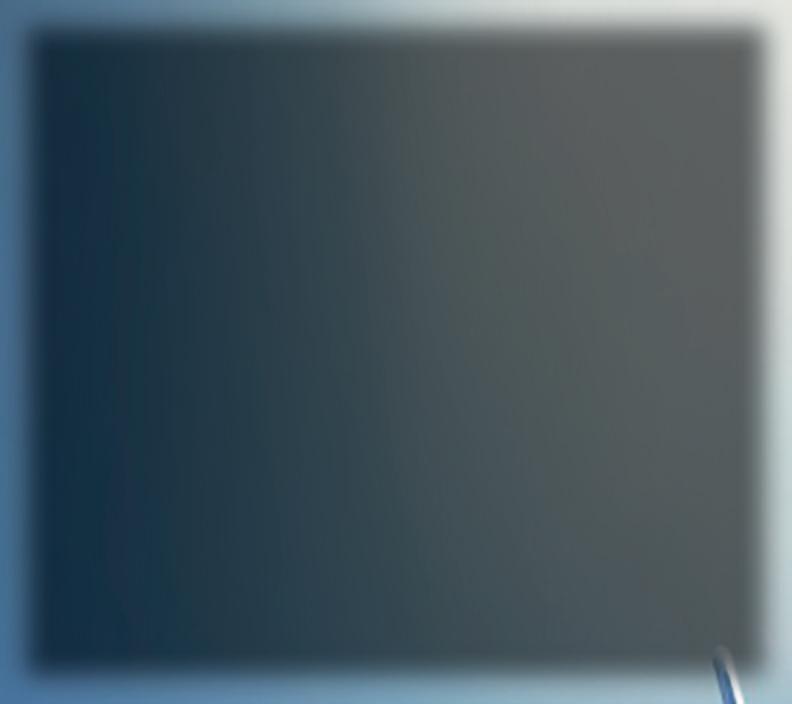
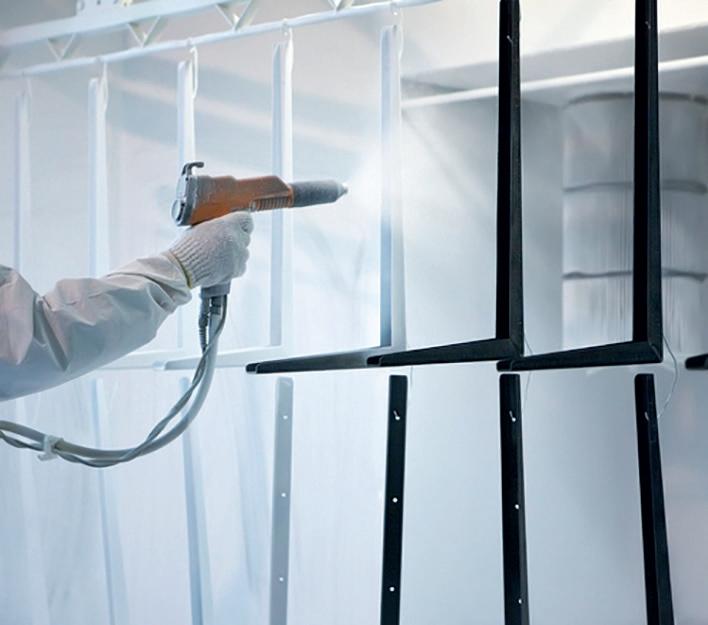

