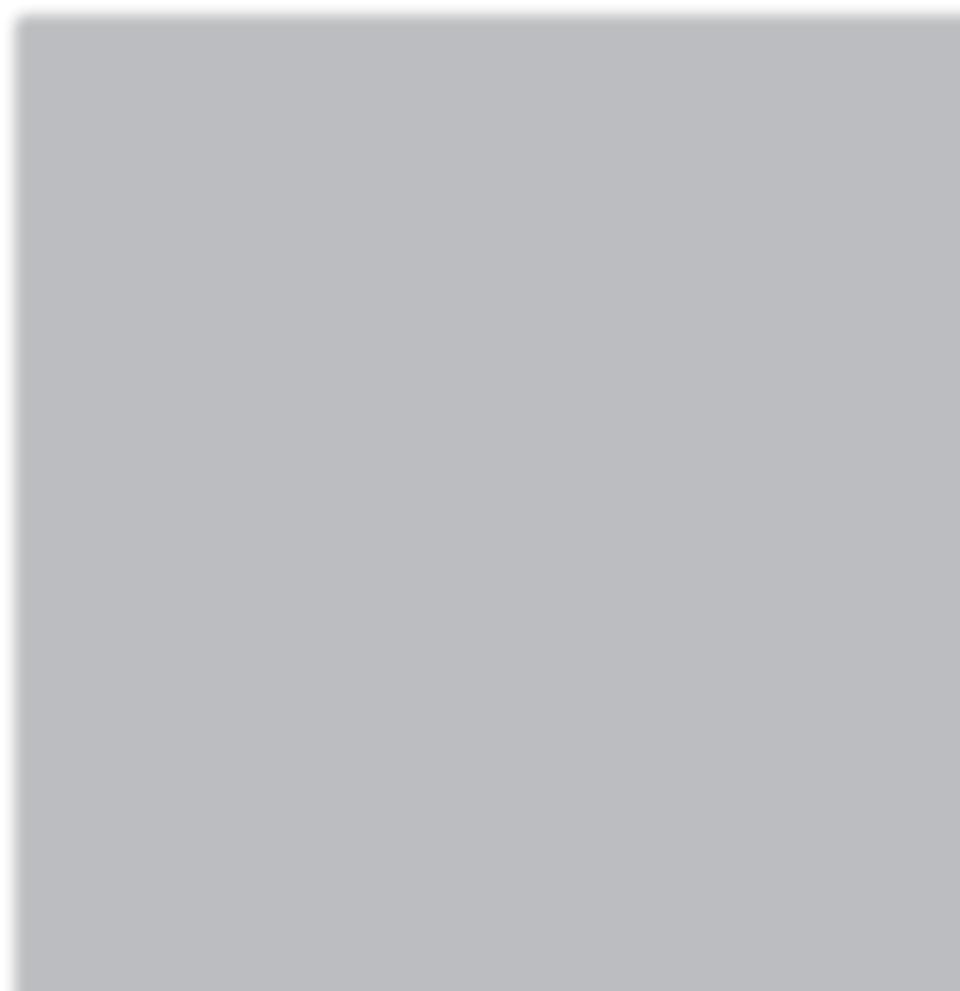
5 minute read
PLASTRATUM DIFFERENTIAL VOLUMETRIC FUME EXTRACTION
Plastratum Diff erential Volumetric Fume Extraction
Effi cient fume extraction is essential in safety critical chemical processing and complimentary to the extensive Plastratum range of fully automatic plant and ancillary equipment for the Metal Finishing industry and our numerous aerospace applications.
It is an application of technology that significantly reduces the volume of fume extraction exhausted from the plant and much reduces the loss of expensive heated factory air. In conjunction with ducting and scrubber systems designed and installed to DW154, this produces a safe, environmentally friendly and efficient fume extraction process. The process tank sequence and systems have integrated lids fitted that generally operate in the closed position and are only opened during the short time of loading or unloading the work piece flight bars. This enables the fume extraction volume on each process to be significantly reduced and is only converted to full volumetric flow when the process tanks lids are in the open position. The riser tubes, as shown in the accompanied photograph, are fitted with automatic dampers as well as manual dampers enabling the volume flow to be adjusted in line with the type of chemistry and process operating temperature. Tank lids, of which there are usually two per process, are moved from their rest horizontal position through 90 degrees by rotational shaft actuators. Each operation is controlled through the plant PLC controller, such that the opening of the lids and the opening of the riser damper allows the transporter to interface with the process and access the work for movement to the next sequential process. Following this operation, the lids and the automatic damper are returned to their original positions. These operations, which only allow full open tank fume volume to be operational, give the benefit of at much reduced fume extraction to atmosphere and has been measured to reduce the output volume as much as 70%. This in turn reduces the fume scrubber and ducting requirements, with significant installation, capital and operational cost reductions. Overall, the increase in cost of the lid technology is more than offset by the reduction in cost of the fume ducting, fume scrubber, fan and discharge stack to atmosphere. This technology allows operation of the scrubber at a constant volumetric flow, allowing automatic dampers, with operate in conjunction with the lids, to allow air flow from outside to balance the changing fume flow from the chemical plant. The use of unheated, external air for balancing reduces the operational cost still further The constant volume fume flow can also be balanced by integration of the fume fan under inverter control. For further information please telephone: 0121 314 1191 or visit www.plastratum.com
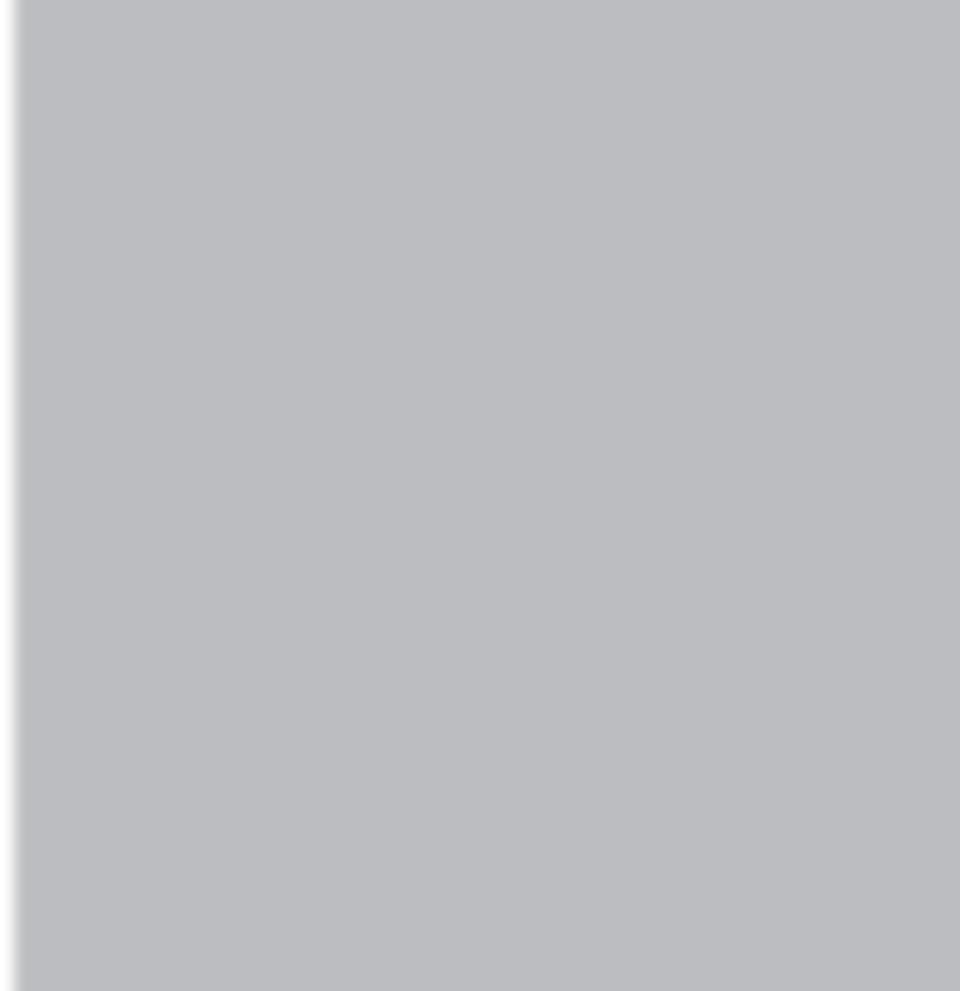
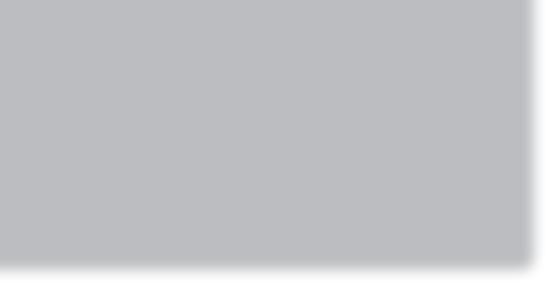

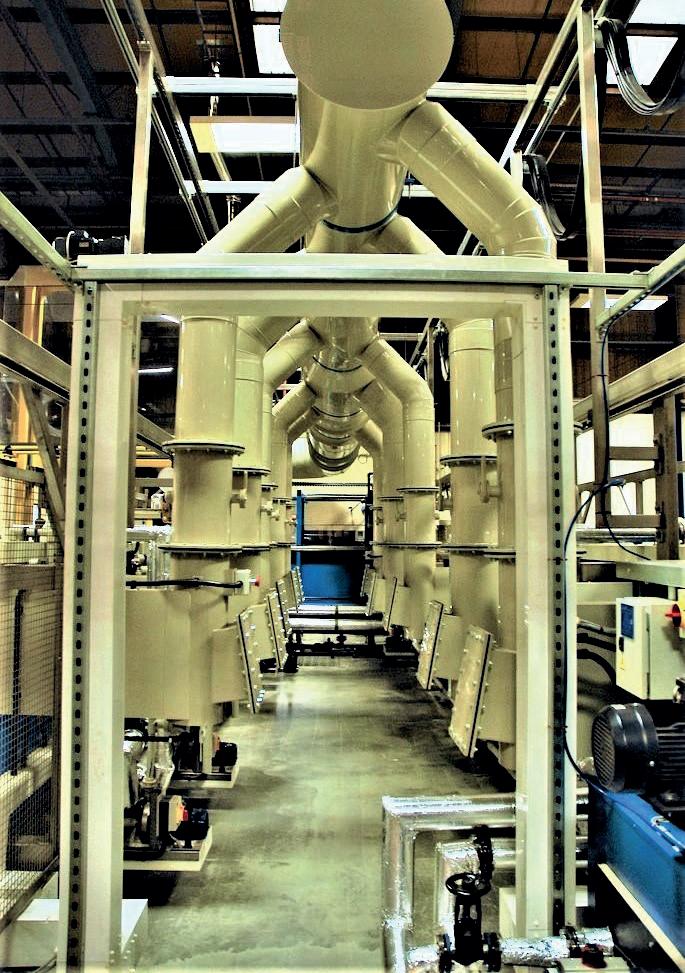
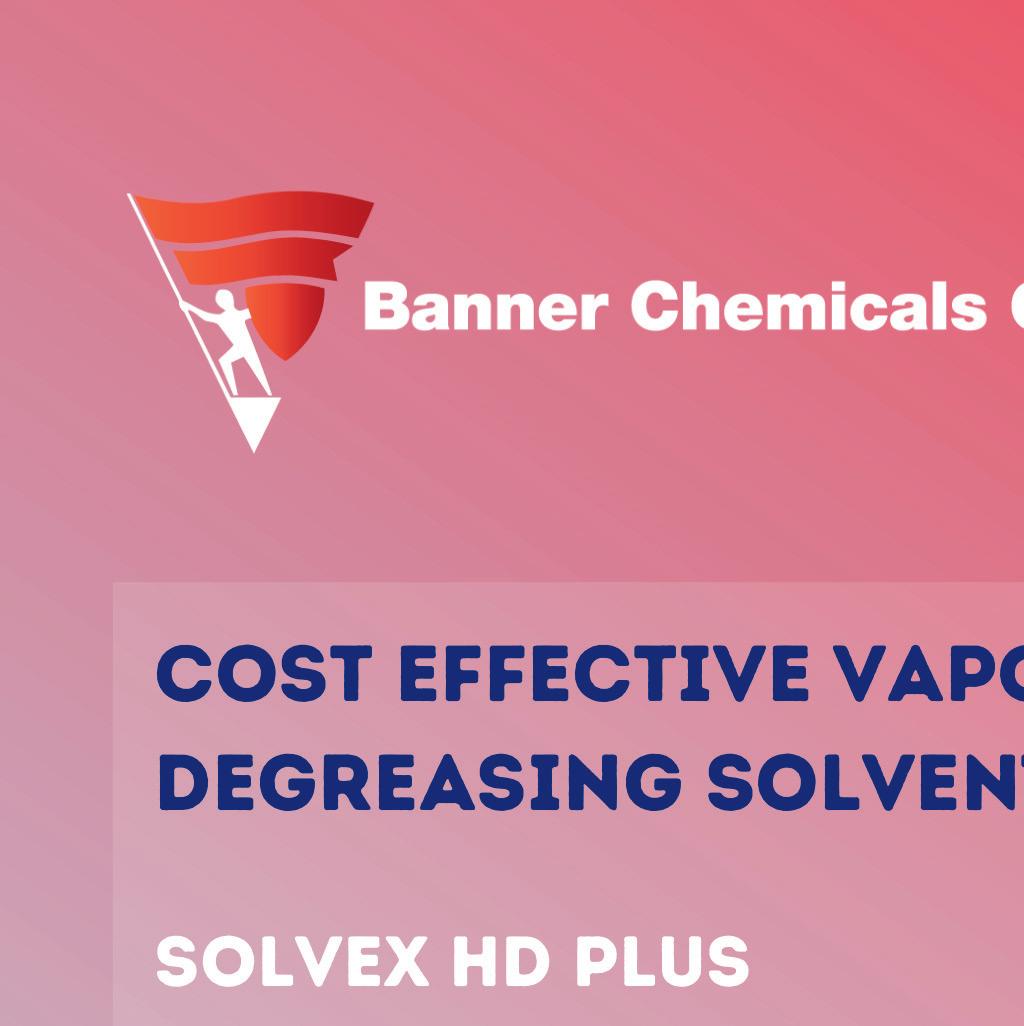
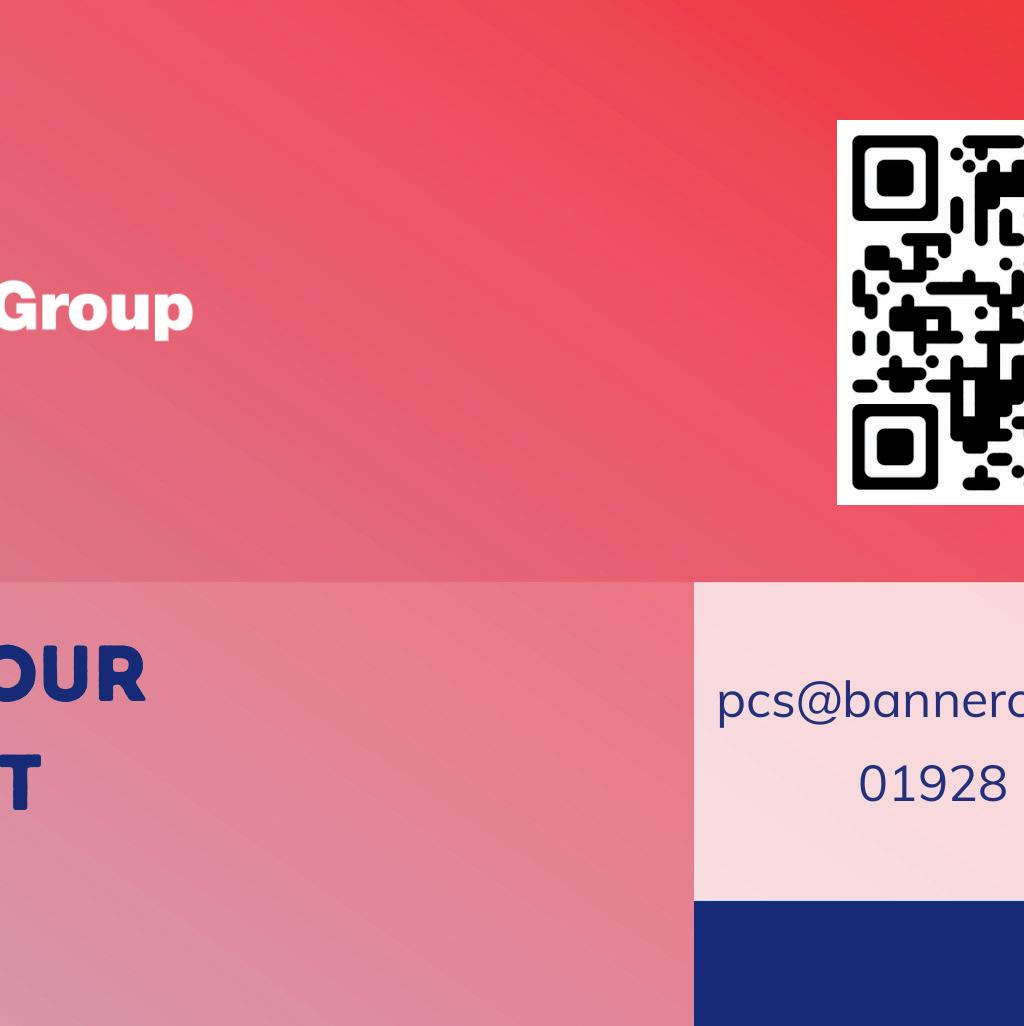
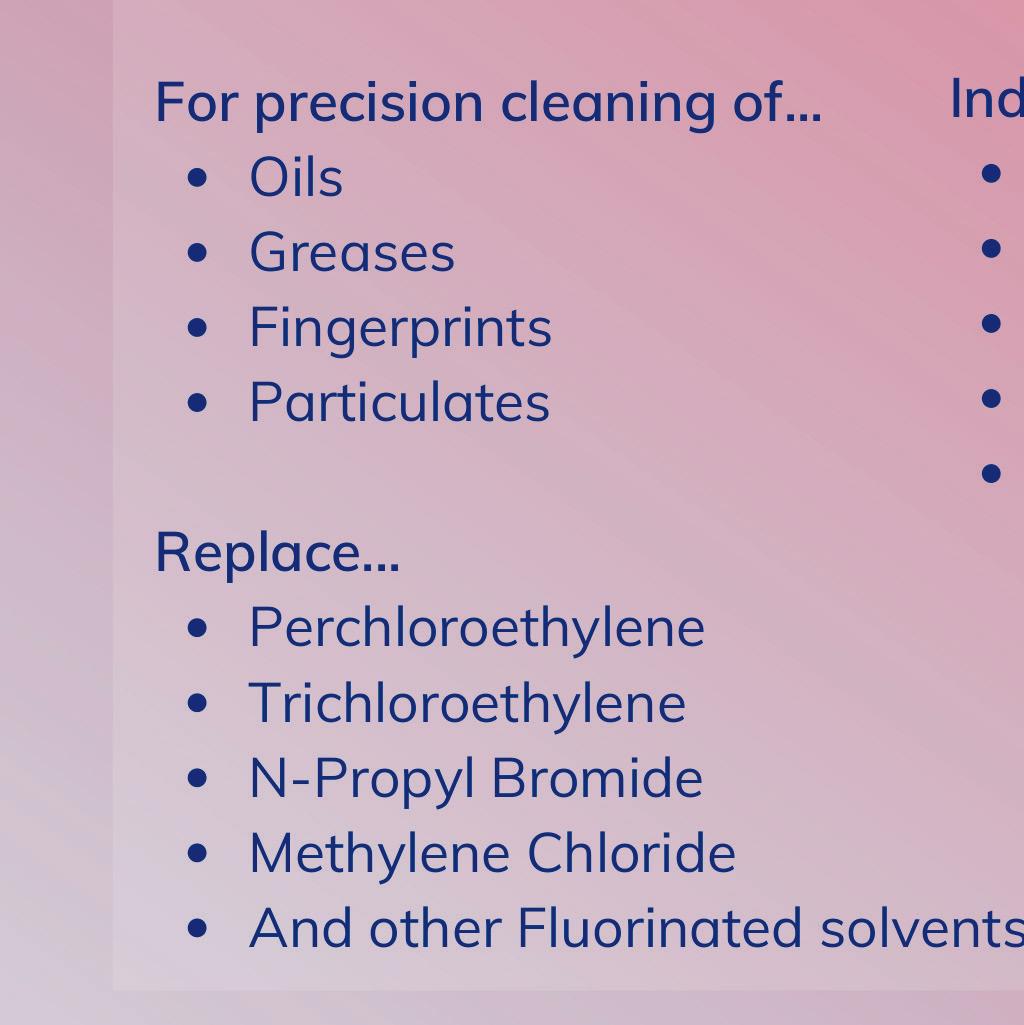
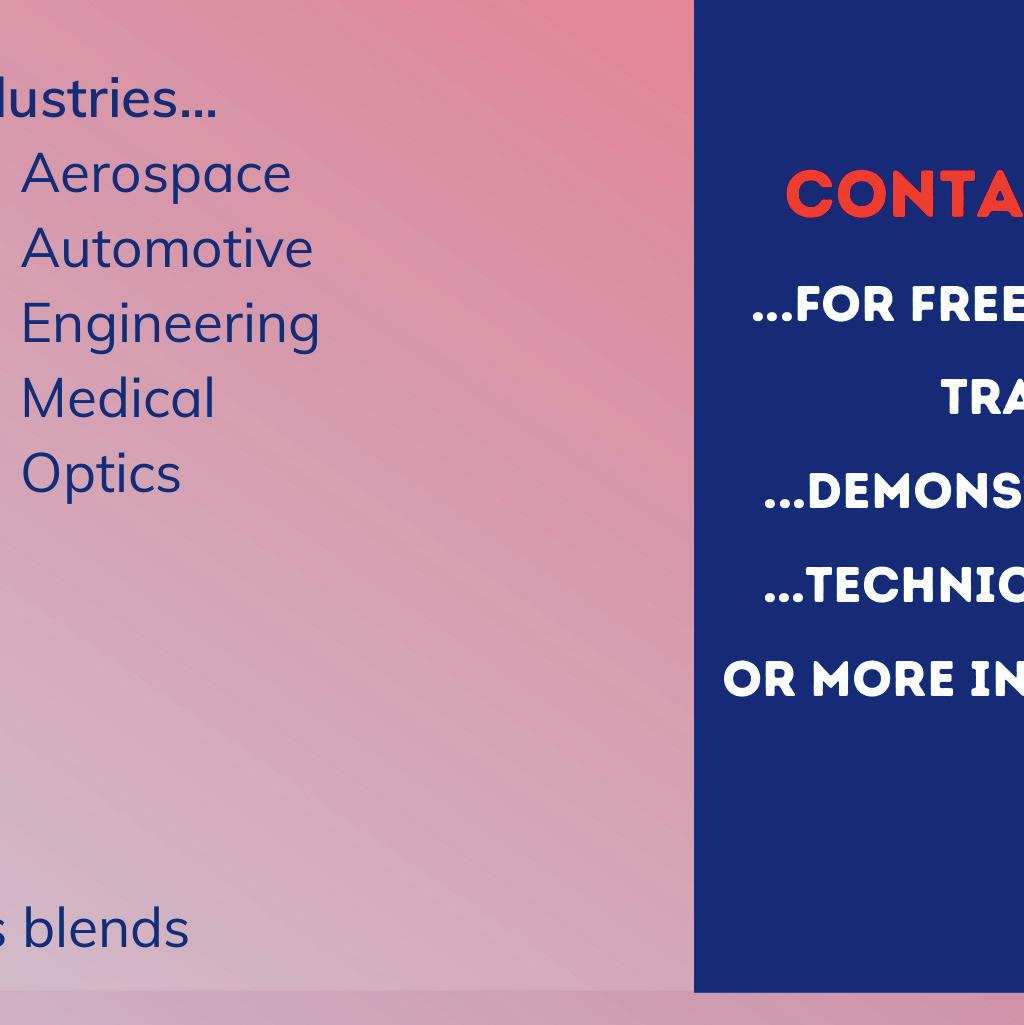
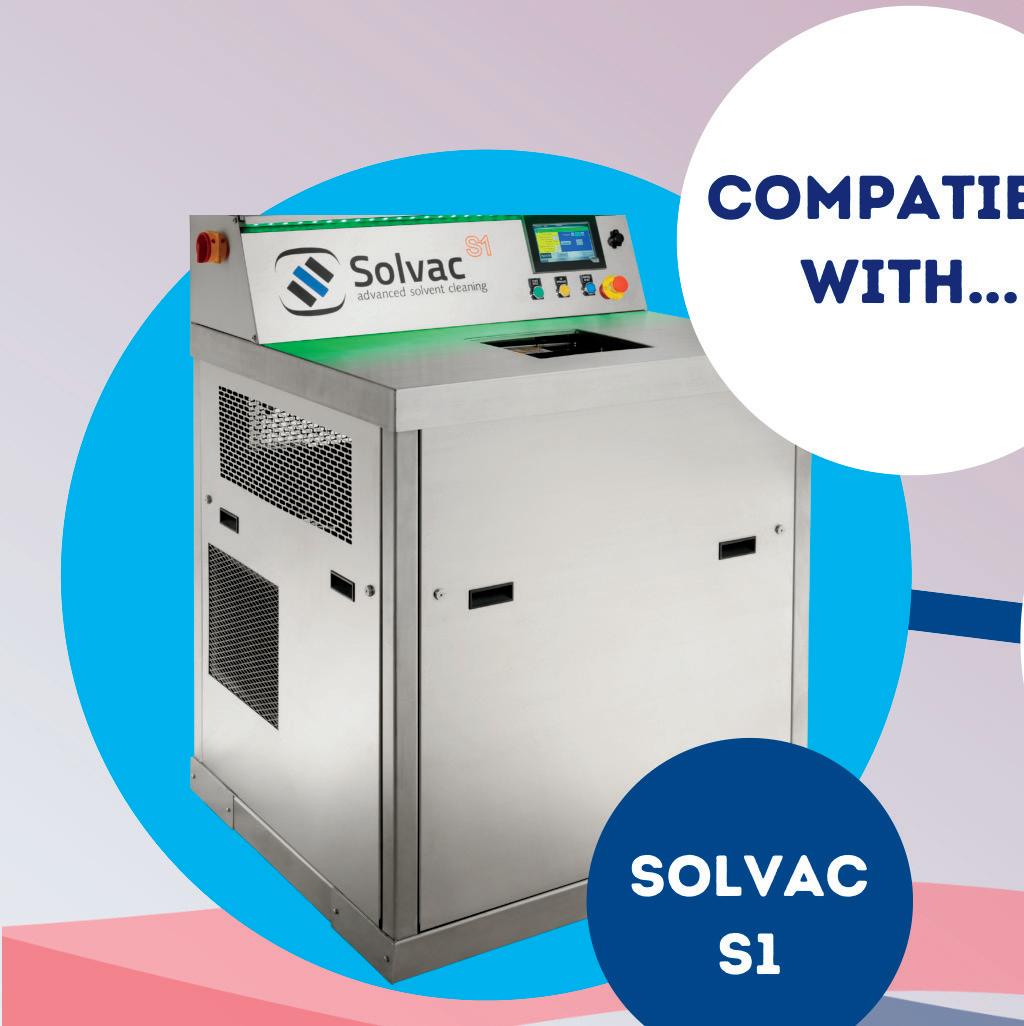
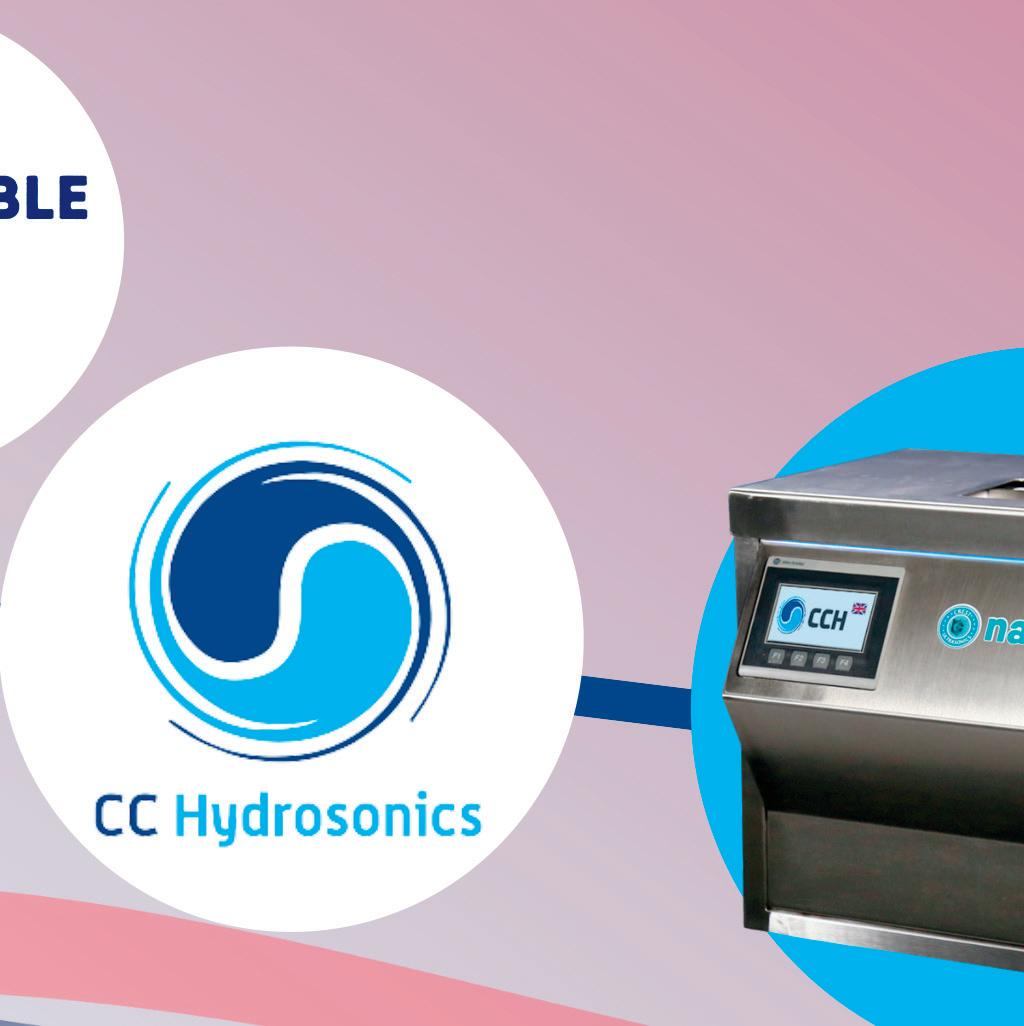
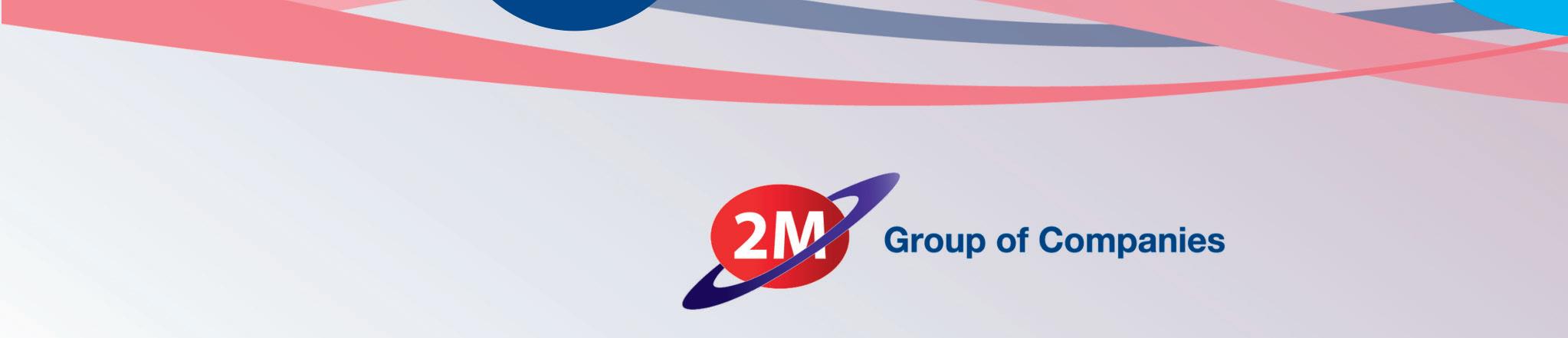
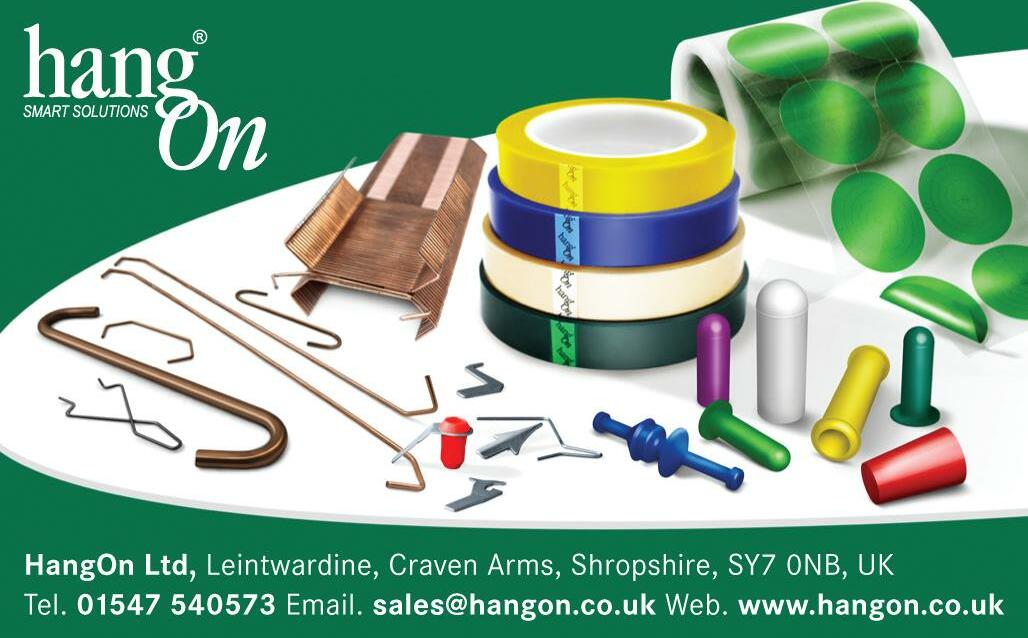
MASKING
Over 40 years of effective solutions!
We are your natural partner when selecting hanging and masking technology. Don’t hesitate to get in touch if you have questions about any of our products or our work!
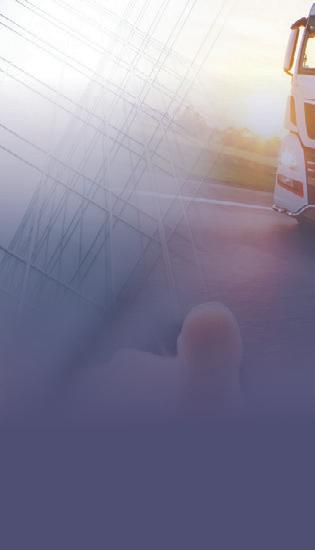
Jason Hardeman, jason@epifatech.uk Phone: +44 7500 938 950
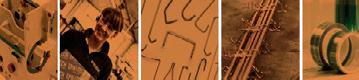
www.epifatech.com
LACQUERS
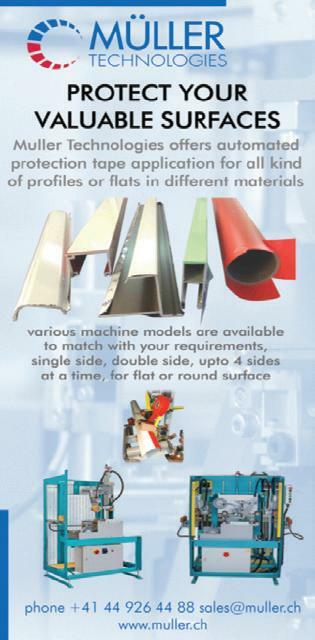
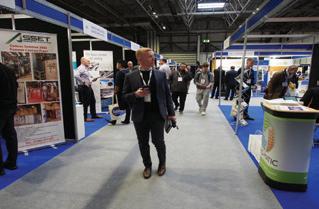
4th & 5th October 2023
NEC, Birmingham

NYLON COATING POWDERS


OVERHEAD CONVEYORS

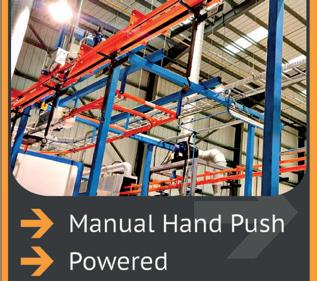
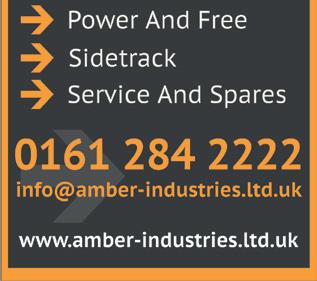
RDM Industrial Services Ltd
Parkfield Industrial Estate Kemp Street Middleton Manchester M24 4AA Tel: 0161 643 9333 Fax: 0161 655 3467 www.rdm.u-net.com.
Contact: Robert Horwich or Geoff Ball
Spraybooths, rooms, ovens, conveyors, pretreatment, powder plant and air replacement units.

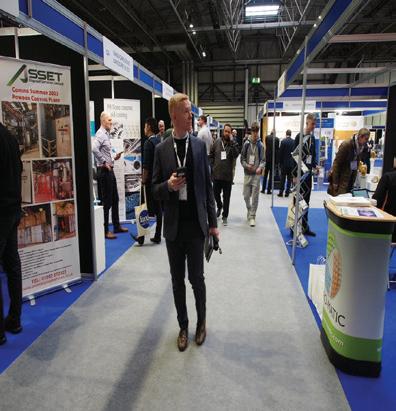
Straaltechniek UK Limited
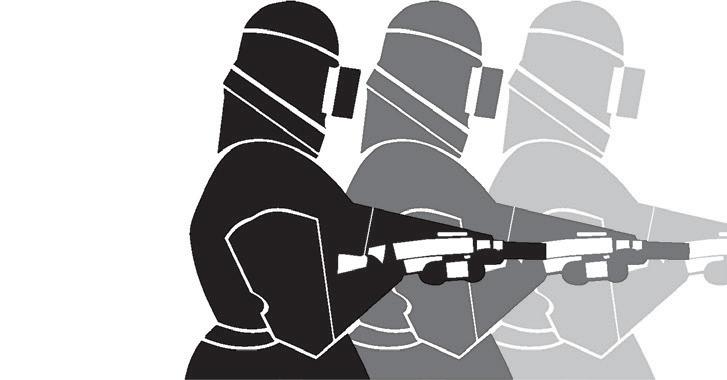
8 Valley Works, Grange Lane, Sheffield, S5 0DQ, United Kingdom

Table Wheel Blasting Machines
• Work zone mm; 1803 Dia x 1500 H • Work zone mm; 1803 Dia x 1200 H • Work zone mm; 2743 Dia x 400 H • Work zone mm; 1500 Dia x 1000 H • Work zone mm; 1000 Dia x 400 H • Work zone mm; 1200 Dia x 1200 H
Tumblast Wheel Machines
• Type; Rubber Belt Volume Litre; 420 Litre • Type; Steel Belt Volume Litre; 425 Litre • Type; Rubber Belt Volume Litre; 50 Litr • Type; Rubber Belt Volume Litre; 150 Litre
Hook Wheel Machines
• Type; I Track Work Zone mm; 1800 Dia x 1800L • Type; Y Track Work Zone mm; 1500 Dia x 1700L • Type; Y Track Work Zone mm; 800 Dia x 1200L
Roller Conveyor Wheel Machines
• Type; Roller Conveyor Work Zone mm; 1000 x 500 Wheel No; 4 • Type; Roller Conveyor Work Zone mm; 1000 x 500 Wheel No; 4
Air Blast Hand Cabinets
• Type; Pressure Work Zone mm; 900W x 600D x 350H • Type; Pressure Work Zone mm; 900W x 700D x 500H • Type; Pressure Work Zone mm; 900W x 700D x 500H • Type; Pressure Work Zone mm; 900W x 700D x 500H • Type; Suction Work Zone mm; 700W x 500D x 400H • Type; Pressure Work Zone mm; 800 Dia Turntable • Type; Pressure Work Zone mm; 500 Dia Basket • Type; Pressure Work Zone mm; 1200 x 750 x400 • Type; Suction Work Zone mm; 700W x600D x300H • Type; Pressure Work Zone mm; 600W x 500D x 400H • Type; Pressure Work Zone mm; 1400W x 700D x 600H
Blast Rooms
• Work Zone mm; 4000L x 2000W x 2000H Type; Room Abrasive Recovery; Waffle Floor • Work Zone mm; 4000L x 2000W x 2000H Type; Room Abrasive Recovery; Waffle Floor • Work Zone mm; 20ft x 8ft x 8ft Type; Container Abrasive Recovery; Sweep Up
Dust Filters
• Various Types & Sizes