
5 minute read
PASS YOUR NEXT CLEANLINESS INSPECTION WITH VAPOUR DEGREASING
Many finished metal parts are subject to high cleanliness standards and must pass black light inspection, particle count tests or water break analysis to ensure they meet the customer specified quality requirements. Also machined parts are getting smaller and more complex. Intricate geometries, awkward shapes, and internal blind holes, make them difficult to clean.
Adding to the cleaning difficulty are the ever-changing environmental regulations placed on metal fabricators today. The cleaning fluids must not only clean surfaces effectively, they must also meet strict regulatory requirements and environmental sustainability standards.
Contaminants Vary
Machined parts are exposed to a wide array of contaminants throughout manufacturing. This includes machining oil, grease, lubricants and polishing pastes. Also, adhesives, wax, marking inks, fingerprints or other production debris. To achieve a superior finish, it is important to clean and prep parts surfaces of these soils before any finishing work like plating, coating or anodising starts. One of the most efficient cleaning methods to achieve perfectly prepped parts is vapour degreasing.
Vapour Degreasing for Effective Cleaning
Vapour degreasers are effective, small, fast, economical and extremely flexible cleaning machines. Vapour degreasing, used in combination with modern cleaning fluids, makes parts cleaning consistent, repeatable and sustainable. It is also one of the most effective cleaning methods to achieve spotlessly clean parts and to help pass stringent cleanliness inspections.
How Vapour Degreasing Works
Vapour degreasing has a high throughput and is easily automated into standard production lines. A vapour degreasing machine is a closed-loop system. It uses a specialized low-boiling, non-flammable fluid as the cleaning agent. The vapour degreasing machine contains two chambers: the boil sump and the rinse sump. Soiled parts are immersed in the boil sump to dissolve or lift the soils from the parts surface. In some instances, ultrasonic agitation adds extra cleaning muscle. As the parts lift from the boil sump, they undergo a brief rinse in the rinse sump filled with pure, uncontaminated fluid or inside the rinsing fluid vapours. After a typical cycle of about 6-20 minutes, the parts come out clean, dry, spot-free and ready for finishing.
Modern Vapour Degreasing Fluids
Most modern vapour degreaser cleaning fluids are a mixture of ingredients. They can include hydrocarbons like mineral spirits, or alcohols like isopropanol and ethanol. How the ingredients combine determines the cleaning fluid’s effectiveness and its material compatibility. The vapour degreaser can use a single cleaning fluid or fluids can be mixed, blended or custom formulated to remove a specific soil from a specific substrate, maximising cleaning effectiveness. Modern vapour degreasing fluids are effective at trapping and removing soils from the most complex and intricate parts geometries. Their chemical properties help in the overall cleaning process. For example, modern cleaning fluids typically have a low surface tension and a very low viscosity. This allows them to penetrate and clean very tight spaces like inside blind holes or in the crevices between stacked parts. Most vapour degreasing fluids also are very heavy and dense, typically 20-40% heavier than water, which aids in dislodging particulate from the parts. And although they are powerful cleaners the cleaning fluids work without causing damage, even on delicate parts.
Sustainable Parts Cleaning & Surface Prep
Parts cleaning fluids now face increasing numbers of environmental regulations. It is not only the cleaning fluid itself that is under scrutiny, but also the disposal method. Vapour degreasing conveniently answers both of these concerns. Many modern parts cleaning fluids have improved environmental properties including a very low GWP (Global Warming Potential) to help reduce greenhouse gas effects. They also have zero ODP (Ozone Depleting Potential) and low VOC formula content. This allows them to meet strict regional air quality regulations and follow global environmental directives. Many are not considered a HAP (Hazardous Air Pollutant). The modern fluids are typically based on HFE (hydrofluoroethers) or HFO (hydrofluoroolefin) technology, making them excellent replacements for nPB (N-Propyl-bromide) or TCE (trichloroethylene) that cause air and groundwater quality concerns.
Recycling Helps Save Costs and the Planet
Another environmental benefit of vapour degreasing is its capacity for recycling. The fluid cleans inside the vapour degreaser for hundreds of cycles before it needs refreshing or replacing. Additionally, it concentrates the soils as it works. This reduces waste generation and lowers hazardous waste disposal costs. Vapour degreasing uses no water and little electricity to clean. Other cleaning processes like aqueous cleaning require massive amounts of energy for water heating, drying and wastewater prepping for disposal. In contrast, vapour degreasing helps conserve water and reduce fossil fuel consumption, resulting in lower total carbon emissions and less greenhouse gas output.
Vapour Degreaser Cost Savings
When you factor in all the benefits, vapour degreasing can reduce your operating costs while improving your facility throughput and productivity. It is low on energy consumption and can be re-used many times. It cleans quickly and effectively and parts come out of the vapour degreaser clean, dry, spot-free and ready for the next stage in the production process.
Finishing Up
Cleaning is a critical step to achieve a quality parts surface finish and pass stringent cleanliness tests. Using a vapour degreaser and modern, cleaning fluids is not only a cost-effective way to ensure parts are clean. It also addresses regulatory requirements and environmental concerns. It is a flexible process that readily adapts to impending changes. Whether it’s a change in cleaning requirements, a regulation change or new environmental concern. Vapour degreasing provides a meticulously clean part while addressing other issues like sustainability and cost-effectiveness.
For metal parts manufacturers looking for help in choosing a vapour degreasing fluid, work with a parts cleaning partner that has both cleaning fluid and vapour degreasing expertise. Based on specific parts make-up and the contamination encountered, they can suggest the fluids and metal cleaning and surface preparation methods that will work best and make passing cleanliness inspections easier.
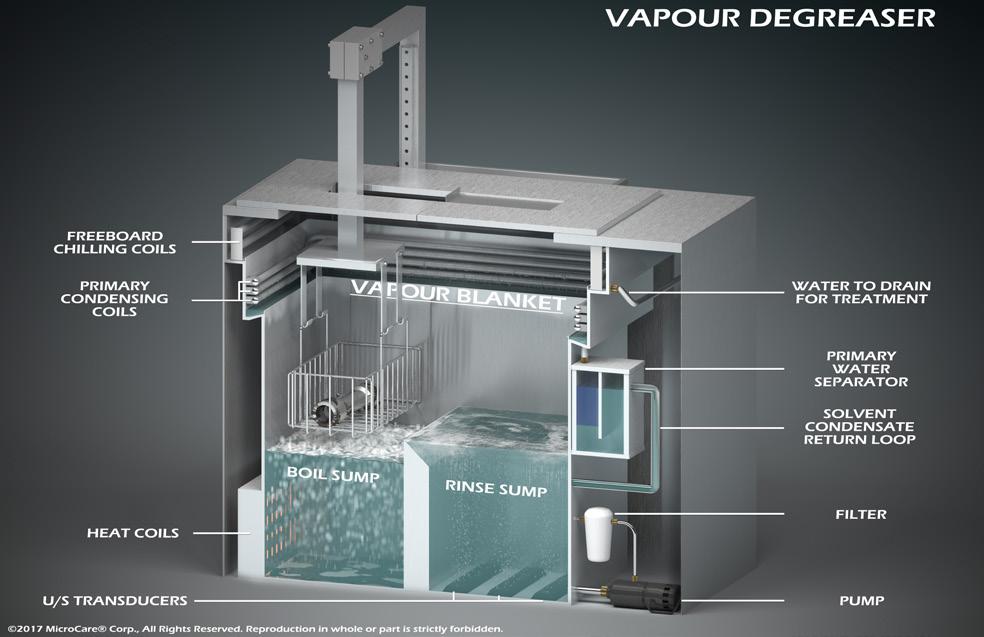
Vapour uses a specialised low-boiling, non-flammable fluid as the cleaning agent.
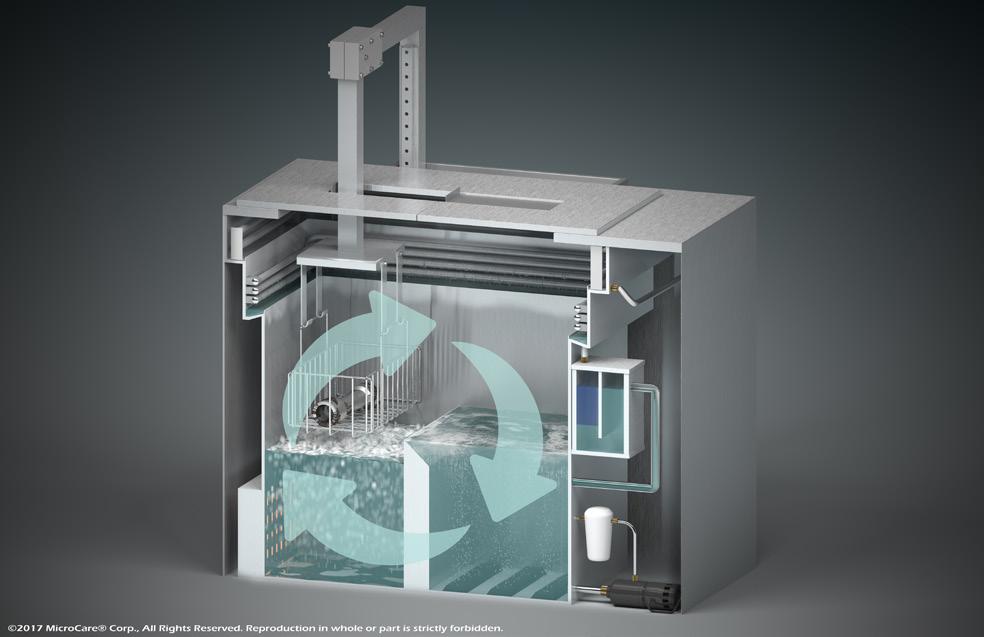
Vapour degreasing is low on energy consumption and re-uses the cleaning fluid many times before disposal.
Author information:
Elizabeth Norwood is a Senior Chemist at MicroCare, LLC, which offers precision cleaning solutions. She has been in the industry more than 25 years and holds a BS in Chemistry from the University of St. Joseph. Norwood researches, develops and tests cleaningrelated products. She currently has one patent issued and two pending for her work. For more information, visit www.microcare.com