
4 minute read
HOW ARE FUNCTIONAL COATINGS IMPACTING THE AUTOMOTIVE INDUSTRY?
Advancements around functional coatings are disrupting many industries. Each industry has its own set of circumstances that lead to unique opportunities and challenges brought about by these developments.
And the automotive space in particular has faced significant disruption across many different areas. Industrial Physics is a global packaging, product, and material test and inspection partner that is home to numerous specialist testing brands, including TQC Sheen and C&W Equipment. One of the areas this document explores in detail is the issue of functional coatings within the automotive space…
The impact on interiors
Tests associated with the finish of a car, such as gloss testing, appearance testing, or abrasion testing, are likely going to be some of the biggest factors that will jump to the minds of those thinking about coatings testing for the automotive space. And they’re incredibly important. But functional tests associated with the interior of a car and all of the different components and parts that have to be inspected are equally as critical and highly affected by developments in the space. Good performance for visible and nonvisible functions is critical for all automotive manufacturers – and engineers and manufacturers at all stages of the supply chain have to protect product integrity.
How are non-visible functions affected?
Acoustics, friction, safety, and comfort all contribute to non-visible functions – and many tests are needed to verify these areas. From coatings tests that ensure seats are comfortable and stain resistant, to tests that ensure dashboards will avoid the scratching or discoloration that come with day to day use, having the right tools in place is critical to verifying the quality of coatings. As your test and inspection partner, Industrial Physics offers a broad stroke of testing applications to help ensure the integrity of your automotive coatings. You can find out more about how Industrial Physics can support your needs at www.industrialphysics.com
Barriers to development
While developments are inspiring change within the world of coatings and helping to improve processes relating to quality control, there are many different barriers that are somewhat stalling progress. From regulations that limit new scopes for development, to electronics issues that stall innovation surrounding testing machines, there are numerous obstacles at play. Industrial Physics’ exclusive report, ‘2022 Global Outlook of Sustainable Packaging’, exposed insights surrounding testing standards in relation to new materials – with coatings, labelling, and printing being revealed as the biggest area for challenges associated with testing in sustainable packaging. If you’d like to get in touch with the team at Industrial Physics, it couldn’t be easier! Just visit https://industrialphysics.com/contact/ to connect with our team of experts – they’ll be able to outline the relevant solution for your unique circumstance.
Gas Process Burners
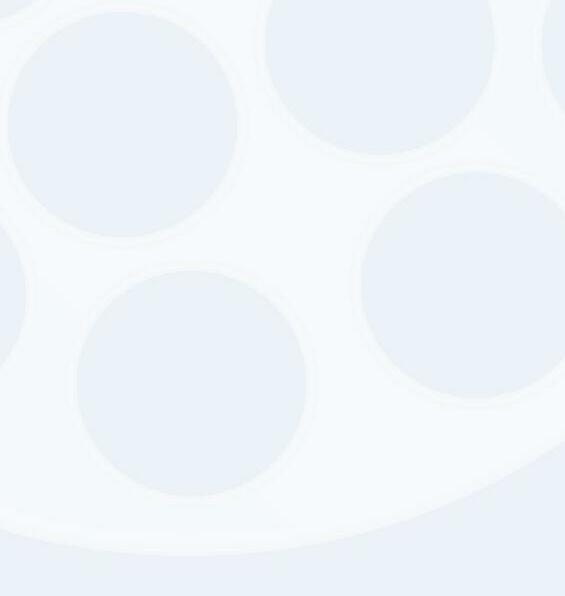
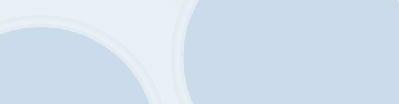
FD-C high turndown oven/ dryer air heating burners.

Midco HMA high efficiency, high turndown, air replacement or “make-up” air heating burners. FD-GA modulating gas + air process air heating burners. FD-E low cost high turndown oven/dryer air heating burners.
TX high efficiency small diameter immersion tube tank heating systems.
Lanemark Combustion Engineering Limited Lanemark House, Whitacre Road, Nuneaton, Warwickshire CV11 6BW United Kingdom Tel: +44 (0) 24 7635 2000 Fax: +44 (0) 24 7634 1166 E-mail: info@lanemark.com www.lanemark.com

Lanemark gas burner systems offer users reliable, high effi ciency, process heating solutions. FD Series Packaged Oven/Dryer Burners • Speci cally designed for process air heating applications in convection ovens and dryers • High turndown/short ame lengths providing accurate process temperature control • High ef ciency gas + air modulation, gas only modulation and simple high/low control options • Heat Input Range: 9 kW – 1550 kW TX Series Gas Fired Process Tank Heating Systems • High ef ciency (80%+) heating of all types of spray and dip process tanks • Compact high ef ciency small diameter immersion tube heat exchangers occupying minimum tank space • Accurate performance modelling using Lanemark TxCalc design software • Heat Input Range: 15 kW (1½") – 1150 kW (8") Midco HMA Series Air Replacement or “Make-Up” Air Heating Burners • Direct red, high ef ciency burner systems, for high volume air heating applications such as paint spray booths, ovens and dryers. • Supplied either as Midco burner heads for OEM system integration or as Lanemark DB or FDB complete packaged systems including modulating gas valve trains and controls • Wide range of ring rates to suit alternative temperature rise and air velocity system requirements • DbCalc system design software
COMBUSTION ENGINEERING
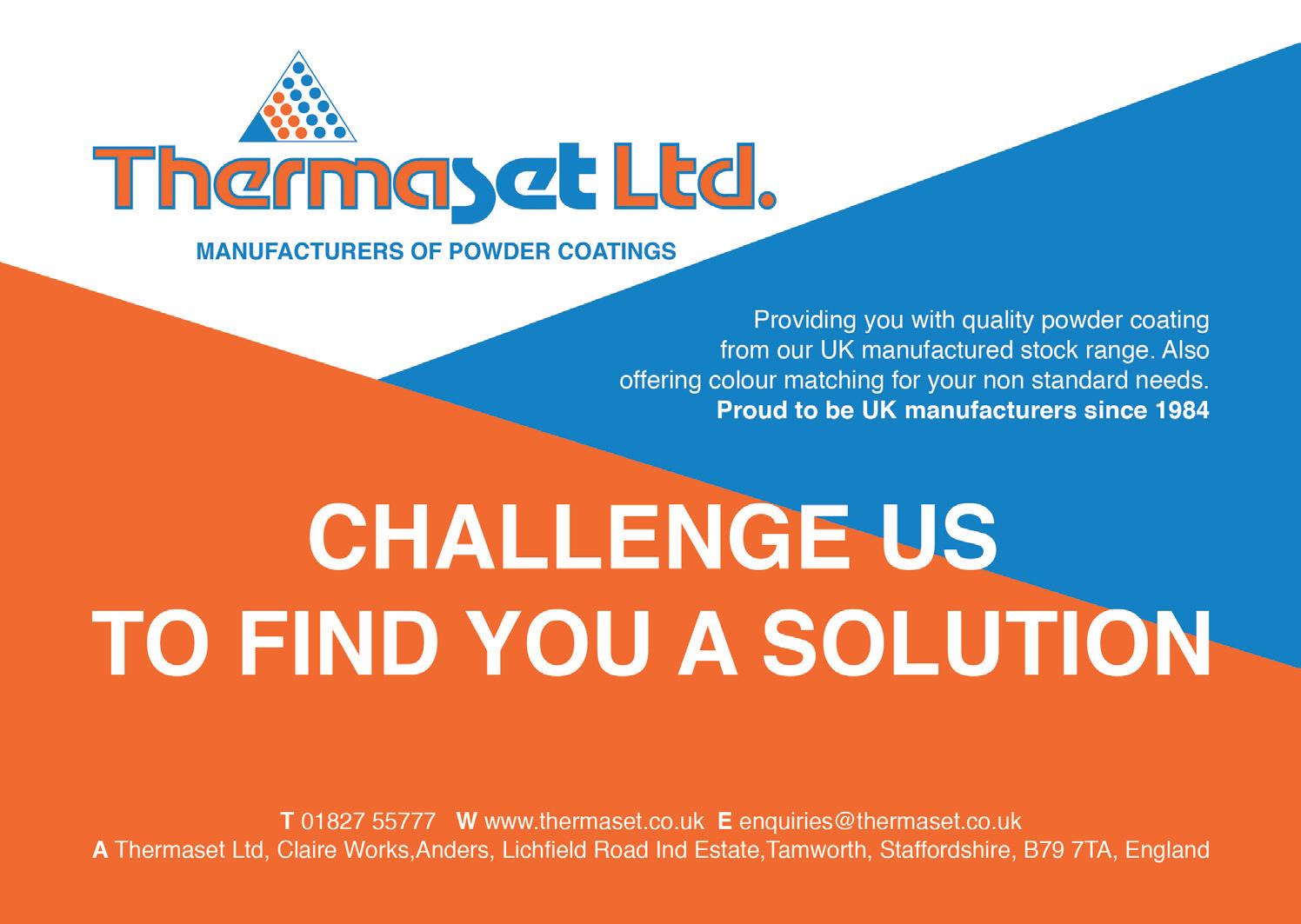