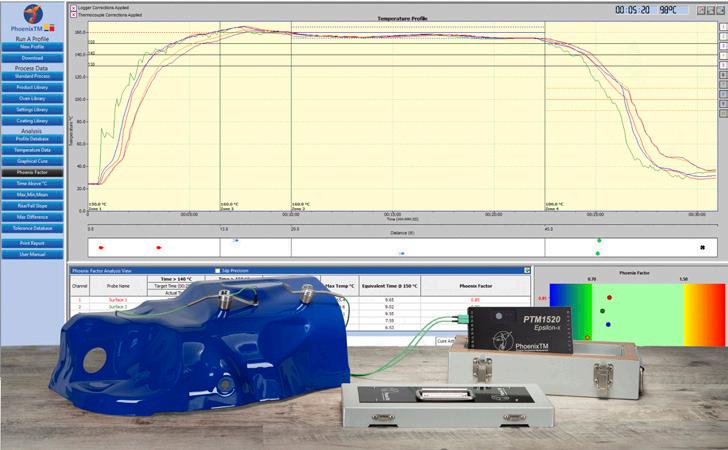
3 minute read
PAINT CURE MONITORING
Paint Cure Monitoring – PhoenixTM Helping drive Quality and Coating Oven Economy
Monitoring what is happening inside your cure oven is critical to understand how your paint or powder coating operation is working. PhoenixTM understands the challenges you face running your operation, to not only get the coating cure quality you need but keep your oven technology up and running as economically as physically possible. With energy costs and ever increasing labour costs you need to make your operation run efficiently and make those costs savings wherever possible. To help you get the best out of your oven PhoenixTM offer a monitoring toolbox to suit your specific needs.
Comprehensive Product Temperature Profiling
The PhoenixTM Thru-process temperature profiling systems provide you with an accurate record of what temperature your product experienced in the cure oven. Thermal View Finishing software provided with the system converts the raw temperature profile data into meaningful information. The software is designed with all the analysis and process documentation tools to fully interpret and communicate paint cure performance. To provide an accurate method to quantify cure PhoenixTM have developed its own mathematical index of cure calculation referred to as the Phoenix Factor. The Phoenix Factor gives the paint technician a perfect numerical tool to easily and accurately confirm that the cure process is working to the coating supplier specification, guaranteeing quality of cure and eliminating rejects or need for rework and corresponding cost. Irrespective of the profile shape, as all profile data is utilised, it’s as simple checking for a correct consistent Phoenix Factor. A value close to 1.00 equals perfect theoretical cure with < 1.00 potential under cure >1.00 potential over cure. With the current energy crisis, the tool provides a further benefit in that is allows operational characteristics of the oven (zone set temperatures / line speeds) to be optimised with confidence and with no risk to the cure quality. Consider what effect potentially dropping your set-point temperatures by 10 °C could make to the operating cost of the oven over a month or year! When setting up new processes or changing energy / heating sources you can monitor your process to permit quick effective optimisation. As they say look after the pennies and the pounds will look after themselves. Even in coating every little counts!
Oven Temperature Uniformity Surveying (TUS)
Complementing its range of thruprocess temperature profiling systems PhoenixTM has recently launched the new PTM4220 “Delta” stand alone data logger. The data logger is a 20-channel system designed for monitoring static batch ovens for either product temperature measurement or temperature uniformity survey (TUS) work. The data logger operates externally to the oven and allows live real time monitoring of temperature linking back to the monitoring computer either by cable, Bluetooth®, or RF telemetry. The system is perfect for performing temperature uniformity surveys (TUS) of batch ovens to comply with CQI-12, when combined with the purpose designed Thermal View Survey analysis and reporting software.
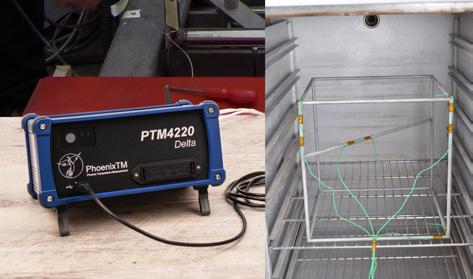
Oven Optical Profiling
Thru-process temperature profiling provides a great understanding of what temperatures the product sees travelling through the cure oven. In terms of paint quality though, in particular cosmetic finish and paint defects, this is not the complete story. During the journey through the oven the painted part can experience many problems that are not temperature related that can affect the quality of the cured paint. Problems such as paint runs, drips, or paint inclusions from dust or particulates can only be detected post process without any specific knowledge of the root cause / location in the oven of the problem. The Optic system developed by PhoenixTM travels through the paint cure oven with the product capturing a live video of exactly what the product sees on its journey. The technology is perfect to detect the source / root cause of paint inclusions. Dust contamination in the oven can be detected as streaks of light passing across the torch illuminated video image, just like a shooting star across the night sky. The same system can detect damage to the inner oven walls / insulation which may be the cause of heat losses resulting in inefficient operation and wasted energy. To understand, control and optimise your coating operation why not PhoenixTM your finishing oven today! Email: sales@phoenixtm.com Viisit: www.phoenixtm.com
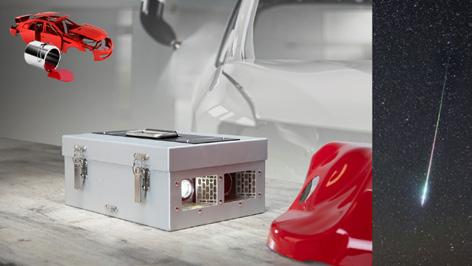