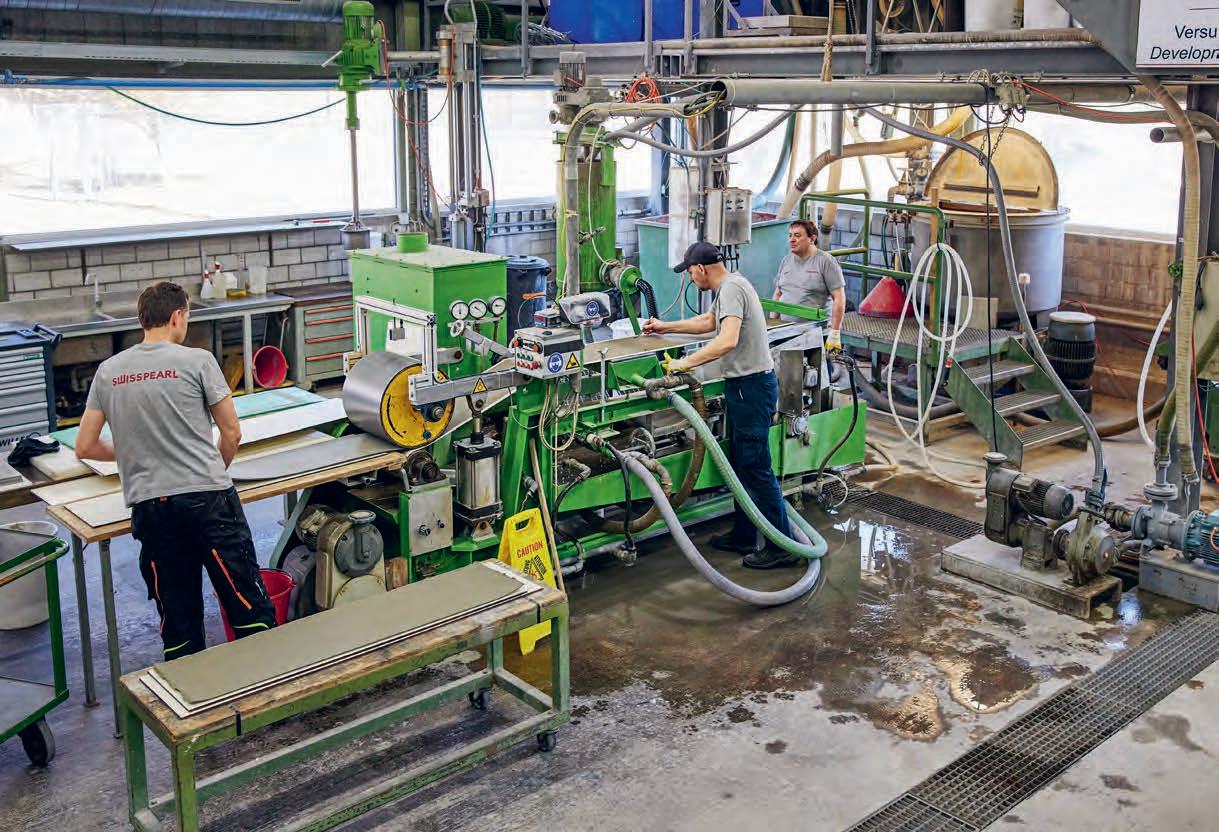
7 minute read
Les enjeux du ciment
Polyvalent et d’une grande longévité, le fibres-ciment reste entaché d’un gros point noir: le ciment. Les recherches vont bon train pour trouver des alternatives adaptées aux enjeux climatiques actuels.
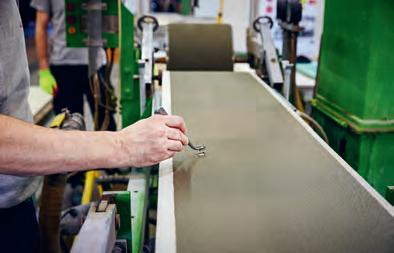
Advertisement
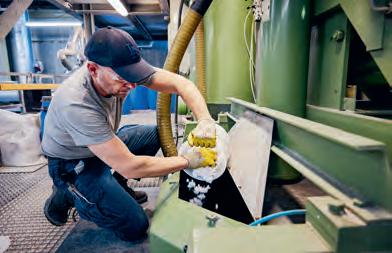
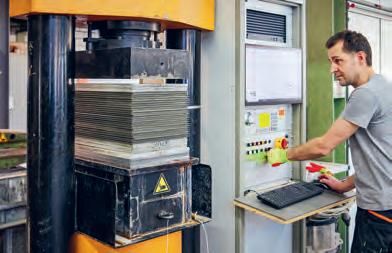
À Niederurnen, dans le canton de Glaris, est fabriqué un matériau de construction quasi parfait: d’une grande longévité, résistant aux intempéries, facile à transformer, de couleurs et formats variés, testé depuis des décennies, adapté aux façades comme aux toitures et, qui plus est, relativement bon marché. Non, ce n’est pas le matériau miracle d’une start-up mais un produit qui est connu depuis bien longtemps. Ce matériau de construction fut inventé en 1894 à Vöcklabruck, en Autriche, par Ludwig Hatschek qui le baptisa Eternit. En plus de le produire lui-même, il se mit à céder, à travers le monde, des licences tant pour le matériau que pour la marque, notamment à la Schweizerische Eternit-Werke AG, en 1903. Simple marque à l’origine, Eternit devint, au fil des ans, synonyme, voire hyperonyme, des plaques en fibrociment, si répandues en dépit du « re vers de l’amiante » dans les anné es 1970. Ce fut au prix de gros efforts en recherche et développement que les spécialistes d’Eternit réussirent finalement à remplacer les fibres d’amiante cancérigènes par des fibres de cellu lose et de polymères. Mais les voilà aujourd’hui à nouveau confrontés à un problème majeur: le ciment, qui constitue les plaques. Ses répercussions sur le climat sont mis en cause. C’est donc le tout pour le tout.
Comme leur nom l’indique, les plaques en fibres-ciment sont et ont toujours été essentiellement constituées de ciment. Leur production s’apparente à la fabrication du papier voir ‹ D’abord liquide puis solide ›. Les plaques en fibres-ciment produites à Niederurnen sont composées d’environ 51 % de ciment, d’une part, et d’autre part d’air et de beaucoup d’eau, de même que de quelques pourcents de fibres de polymères et de cellulose, et également de colorants. En fonction de l’aspect voulu suit un revêtement soit organique, soit appliqué manuellement ou par un robot pulvérisateur. Les fibres renforcent la matrice cimentaire friable, améliorant ainsi la résistance à la rupture, à la flexion et à la traction des plaques minces. Légère, bon marché et ignifuge de surcroît, la fibre d’amiante fut longtemps la candidate idéale. Mais si elle est inhalée, cette fibre risque de provoquer une asbestose, maladie pulmonaire incurable et mortelle. Au début des années 1990, la gamme des produits de l’entreprise Eternit SA fut totalement débarrassée d’amiante et le problème a été réglé, du moins pour les nouveaux produits. Aujourd’hui, le risque ne concerne plus la santé mais le climat.
Émissions de catégorie 3
La fabrication du clinker, déjà vorace en énergie, nécessite, de surcroît, une réduction du carbonate de calcium en oxyde de calcium, responsable de grosses émissions de dioxyde de carbone. Climatiquement parlant, la production de plaques en fibres-ciment continue donc, en dépit de leur longévité, à poser problème au secteur du bâtiment. Tandis que sur ses sites, Swisspearl optimise ses processus, investit dans le photovoltaïque, réduit autant que possible ses besoins énergétiques et achemine ses matières premières par le rail, le véritable enjeu tient aux émissions de catégorie 3 imputables au ciment. Cela d’autant plus que le ciment à forte résistance nécessaire aux plaques de fibres-ciment génère beaucoup d’émissions. Selon Carsten Zanders, responsable recherche et développement chez Swisspearl Suisse « tout indique que les producteurs de ciment vont décarboner leurs gammes de produits dans les meilleurs délais et que certains types de ciment ne vont plus être disponibles ». L es neuf usines Swisspearl vont donc passer à des variétés de ciment décarbonées d’ici 2024, toujours selon Zanders. C’est facile à dire mais complexe à réaliser, car la substitution de l’agent liant ne doit en aucun cas altérer les proprié - tés des produits fibres-ciments. Le ciment n’est pas le seul chantier en cours. « Nous travaillons aussi sur d’autres questions de développement durable, toutes aussi exi geantes et captivantes à la fois », poursuit C. Zanders. Swisspearl s’est fixé l’objectif à l’horizon 2030. L’entreprise entend franchir d’ici là des étapes décisives en termes d’efficacité environnementale, de recyclage, d’optimisation des cycles et processus. Les objectifs sont actuellement redéfinis au niveau du groupe. Les sociétés danoises Cembrit qui ont rejoint Swisspearl en 2022 jouent un rôle moteur dans ce processus.
D’abord liquide, puis solide À Niederurnen, le personnel de Swisspearl fait tourner deux grosses machines, parfois en 24 h sur 24 selon le carnet de commandes, pour fabriquer des plaques en fibres-ciment. Au départ, le produit est une suspension aqueuse de ciment, fibres et additifs. Un tapis de feutre sans fin est plongé dans ce bain. Les matières solides se déposent sur celui-ci en couches minces que récupère ensuite un rouleau. Quand la plaque a l’épaisseur voulue, les couches superposées sont détachées du rouleau, déposées sur un plan de travail sous forme de plaques souples brutes, puis découpées grossièrement. La pile qui se forme au fur et à mesure passe ensuite dans une presse qui permet d’extraire l’essentiel de l’eau encore présente. Un contrôle est alors effectué, puis les plaques brutes sont envoyées au séchoir. Si nécessaire, un revêtement y est alors appliqué, le séchage se poursuit et les plaques arrivent enfin au conditionnement, où elles sont découpées aux différents formats. La production des plaques ondulées et des produits pour toiture suit le même procédé.
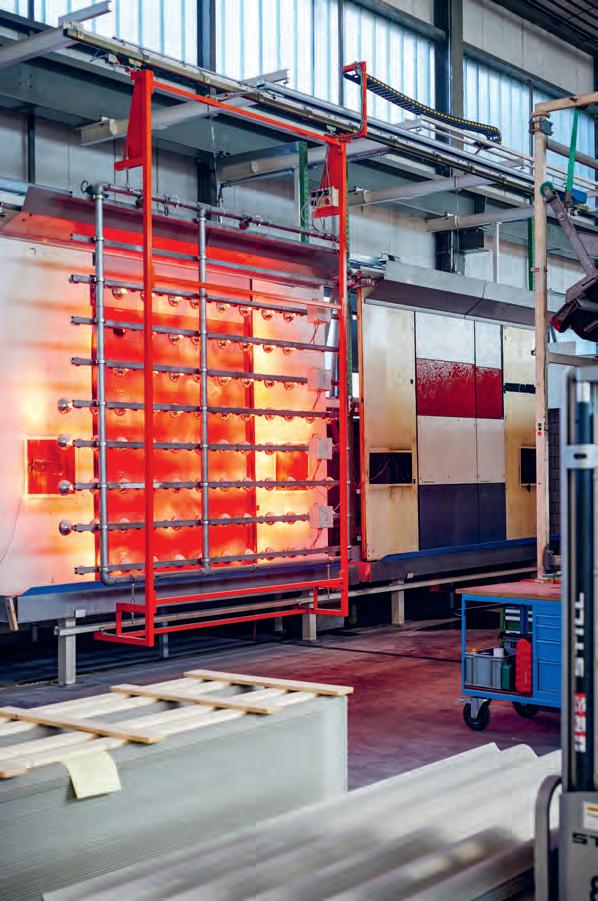
Recherche et développement à l’international Swisspearl emploie au total 53 p ersonnes dans le domaine recherche et développement, réparties entre la Suisse, l’Autriche, la Slovénie, la Tchéquie et le Danemark. Jusqu’ici structuré par sites, il s’articulera désormais par compétences autour d’équipes transfrontalières. Sous la direction de Carsten Zanders, le centre de compétence Matrix-Technology se consacrera essentiellement à la question du ciment, Surface-Technology se concentrera sur les nouvelles propriétés des surfaces, New Product Development développera de nouveaux produits. Ces trois départements emploient 21 personnes en tout, les laboratoires 32 p ersonnes. Ces dernières assistent aussi bien leurs collègues de la recherche que ceux de la production, elles vérifient et testent, certifient et secondent la gestion de produit. Cette structure vise à mieux exploiter le potentiel d’innovation, à éviter les développements en parallèle et à faciliter la transmission des concepts au sein du groupe. Ainsi un procédé de recyclage des déchets de chantier est-il actuellement suivi au Danemark et en Scandinavie. Les possibilités de revalorisation de matière du composite commencent à peine à se profiler. « Nous p arvenons à traiter des déchets issus de la production mais, en l’état actuel, pas à les réintroduire à 100 % dans le cycle , dit Carsten Zanders. Réactiver les déchets de notre production ou de nos clients pourrait être une solution. Le s essais à petite échelle ont l’air pas mal. » Zanders n’en dira pas plus pour l’instant vu les procédures de dépôts de brevet en cours. « Nous avons l’objectif de substituer de grosses parties, l’intégralité dans l’idéal, de l’agent liant qu’est le ciment. » L’équipe de Zanders collabore étroitement avec les fournisseurs de matière première et, sur certains projets, avec des chercheurs externes. Dans le cadre d’une coopération avec l’Institut de technologie de Karlsruhe ( KIT ), p. ex., l’utilisation d’agents liants sans ciment est étudiée en théorie.
Et les fibres ? Tandis qu’au fil du temps, la fibre de cellulose de la plaque se décompose, la part à 2 % de fibre synthétique d’armature reste intacte. Le remplacement par des fibres biosourcées serait-il envisageable ? « Nos matrices cimentaires alcalines de pH inférieur à 9 ne constituant pas un milieu stable pour de telles fibres, c’est un enjeu de portée globale, explique C. Zanders. Mais si nous modifions et les fibres et la matrice cimentaire, cela pourrait changer la donne. Nous avons adopté la technologie sans amiante il y a 40 ans et depuis la situation, tant technique que chimique, a continué d’évoluer et offre de nouvelles possibilités intéressantes. » Dans le domaine du surfaçage, on a déjà avancé. Il y a des alternatives aux liants polymères des revêtements colorés dans la fabrication desquelles intervient de la biomasse, réduisant ainsi la part pétrochimique. S’il y avait un compte à rebours jusqu’à l’horizon 2030, nous nous situerions actuellement « quelque part entre 9 et 4 », dit C. Zanders. En termes de décarbonation des émissions de catégorie 3, on en serait à 8 – normal car c’est sans doute la tâche la plus complexe.
Au croisement du photovoltaïque et du fibres-ciment Tandis que l’on s’évertue à améliorer les perspectives écologiques des fibres-ciments, ailleurs dans l’entreprise, on travaille sur de nouveaux systèmes énergétiquement actifs pour toits et façades. Et cela ne date pas d’hier. Swisspearl s’est intéressée au photovoltaïque dès les années 1990, forte de l’énorme expérience acquise avec les systèmes VHF et de toiture. En 2010, leurs premières installations pilotes ont été réalisées au moment de la redéfinition des règles sur la rétribution de l’injection d’électricité solaire. Avec la croissance du marché, le solaire est devenu en quelque sorte une entreprise dans l’entreprise Comme l’équipe de développement autour de Rolf Hefti, responsable de la branche solaire, s’est vite aperçue que les panneaux sur toiture d’Extrême-Orient défiaient toute concurrence, la décision fut prise en 2014 de se concentrer uniquement sur le développement du photovoltaïque intégré au bâtiment avec des modules bi-verre de qualité et autres systèmes de construction complexe.
Depuis, Swisspearl est présent en Suisse et en Autriche avec ses systèmes photovoltaïques, fournit des plans de pose et de câblage en soutien aux professionnels, se charge des détails tant électriques que sur la technique du bâtiment. Rendant la couverture classique superflue, les systèmes intégrés sont tout indiqués pour la construction ou la rénovation de toitures inclinées.
Et les façades ? Architecte s et maîtres d’ouvrage seraient encore frileux en la matière, selon Hefti. Même chez Swisspearl, on en est encore à optimiser les systèmes afin que tous les projets individuels de façade soient rendus possibles avec un nombre fini de modules standards, ce qui serait un sérieux plus pour la rentabilité. Et c’est là que la plaque en fibres-ciment revient en piste: là où trames de façades et photovoltaïques ne coïncident pas parfaitement, elle est toujours en mesure de prendre le relai. Cela demande toutefois qu’il y ait une meilleure harmonisation visuelle entre les modules photovoltaïques et les plaques en fibres-ciment, surtout au niveau des coloris. Les modules colorés ont toutefois de moins bonnes performances que les cellules standards; tous les procédés et technologies ne se valent pas. Mais « cela n’empêche pas le courant de passer, même avec l’impact hivernal ».
Fibres-ciment d’un côté, photovoltaïque de l’autre –symbiose de deux technologies à fort potentiel mais soumises à des rythmes différents: face aux fortes poussées d’innovation du solaire, le développement du fibres-ciment est généralement considéré comme arrivé à terme. Mais les choses sont en train de changer. ●
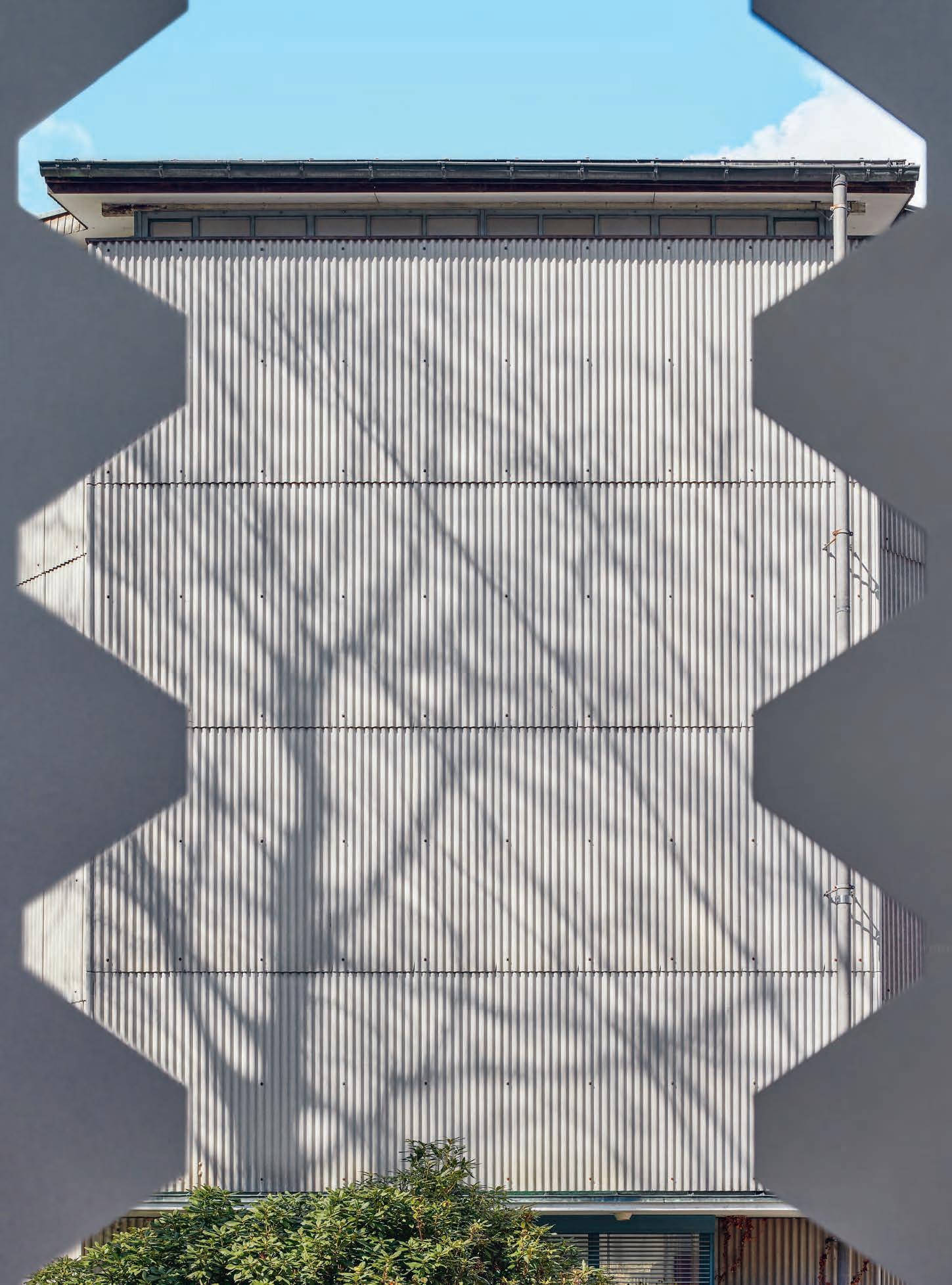