NEXT STEPS WITH ALTÉA ( )
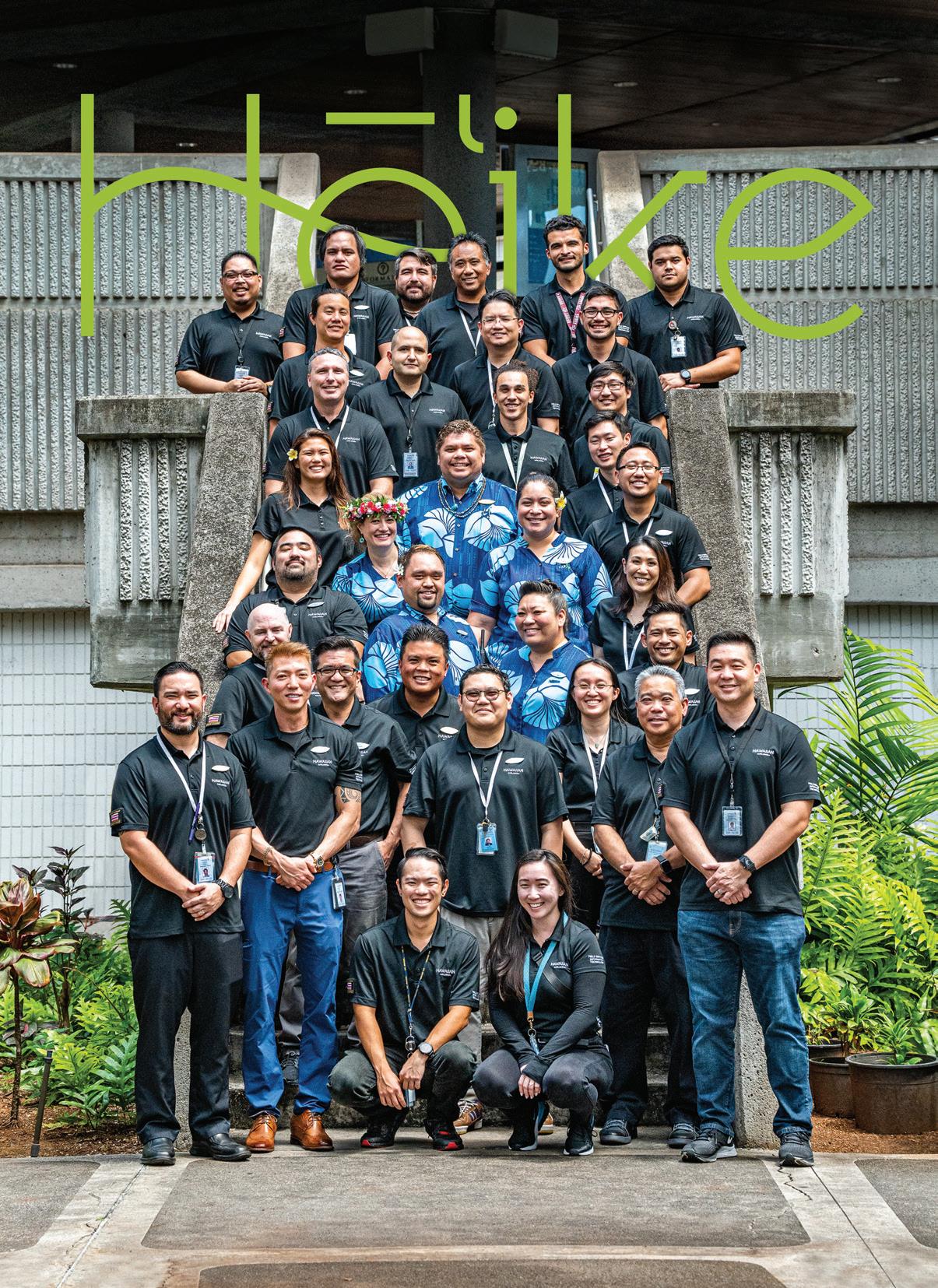
SO, IT’S NO SURPRISE that despite countless hours of testing and tweaking, the complex conversion of our passenger service system from Sabre to the Amadeus Altéa platform resulted in the temporary loss of some functionalities when we went live with the new system. Knowing cutover was not the endpoint of this momentous journey, our IT Field Services group deployed in full force to our airports to provide immediate support for our frontline teammates, backed up by a team of Amadeus representatives who provided expertise.
“While the first few days with Altéa did not meet our company’s service standards, our frontline teammates worked tirelessly in our airports to help as many of our guests as they could,” said Director of IT Field Services John Kim. “Everyone has been working together to identify the issues and implement appropriate resolutions.”
The PSS post-cutover period is now firmly in a Stabilization Phase, as demonstrated by the resolution of all Priority 1 (P1) incidents and the departure of most Amadeus on-site support personnel. Our new PSS vendor now classifies us as a “Tier U” carrier, which denotes a “business as usual” level of support.
“While the overall system is stable enough for us to maintain our business and operation, we continue to work with Amadeus on a number of important bug fixes,” noted Chief Information Officer (and PSS IT Lead) John Jacobi. “We recognize the challenges that our teammates are dealing with, and we remain committed to resolving outstanding issues and significantly reducing the current struggles they face.”
Meanwhile, we continue to support our Airport Operations teammates as they encounter bugs or glitches common to a complex system transition. They have been taking great care of our guests while climbing a steep learning curve amid our ongoing operational and infrastructure challenges.
“The airport environment can be difficult in the best of times, so a transition as complex as this has the potential to multiply this difficulty,” said Senior Director of Airport Operations Policies & Procedures (and PSS Operations Lead) Sarah
Any information technology transformation project brings challenges, not only as it relates to all the effort involved, but also ensuring that everything works as intended in a real-world environment.
Slay. “I appreciate the tenacity of our Guest Services team as they juggle their daily responsibilities while working with a new system and maintaining operational continuity. I know that we can all work together to resolve outstanding issues and stabilize our processes.”
The next chapter is known as the Restoration Phase where we work with Amadeus to bring back functionalities that we had to suspend in the interest of a smooth data migration. This phase also includes features that were in our contract but couldn’t immediately be delivered.
“We are working with Amadeus to address more than 60 Project Change Proposals that cover items that we had to defer,” explained Vice President of Marketing & E-Commerce (and PSS Business Lead) Rob Sorensen. “We are eager to restore these along with the enhancements we were hoping to incorporate into our business and operations.”
Following that is the Expansion Phase, where we can explore new capabilities to further improve the work environment for our teammates, the travel experience for our guests, and efficiencies for our business. This could include greater interoperability between our third-party platforms and expanded self-service opportunities for our guests.
“At the start of this project, I noted that it’s important we do the hard things to make us a better and more competitive airline,” recalled Rob. “The ability to do hard things means finishing well and finishing well means fine-tuning our systems and processes to where they need to be to deliver a quality product. Whether working on this project, adjusting to Altéa while serving our guests, or supporting our frontline teammates at our airports, it has been heartwarming to see how we all came together as a team to overcome challenges and come out stronger. I’m so proud of everyone’s dedication to this initiative, our company, and each other.” ■
Since October’s announcement, we have been preparing for the first of 10 Airbus A330300 freighters that we will fly and maintain for Amazon. The decision to develop a Freighter Line of Business dovetails with huge demand for air cargo shipments. According to an estimate by aviation analytics firm Cirium, passenger jet to freighter (P2F) conversion specialists are setting records with more than 170 airframe overhauls in 2022.
BEFORE THAT FIRST blue-tailed aircraft lands on our runways, it’s important to reflect on the extraordinary efforts happening behind the scenes. There are many elements that contribute to a successful launch. Here, we spotlight three — passenger-to-freighter (P2F) conversion, pilot training, and the creation of our Weight & Balance and Ground Operations manuals.
The P2F process typically happens when an aircraft reaches 30,000 – 40,000 flight hours, which translates to approximately 12-15 years of passenger service.
Senior Director of Fleet Introduction & Performance Marc Kup explains most cargo carriers acquire older passenger aircraft whenever airlines renew their fleets. “Usually, older airplanes have better ownership costs, as they are older and thus can be acquired cheaper,” he said. “They might not have the latest creature comforts and efficiencies, but boxes usually don’t care about that. That said, some operators with timecritical cargo needs and high utilization will indeed buy brand new production freighters.”
customer. Marc added, “Airbus usually sells those ‘white tails’ at an attractive discount, so Amazon gets the best of both worlds on those, with a new airplane and lower ownership costs (aka rent).” Whether old or new, Elbe Flugzeugwerke (EFW) is doing the conversion with each taking around six months.
The P2F process involves removing the interior down to the metal shell. The windows are plugged and the fuselage frame is reinforced to stabilize the addition of the large cargo door. Inside the aircraft, the frame and crossbeams are replaced and strengthened to support the extra load. Where passengers once sat, there will now be room for tons of freight.
1 2
In the case of this partnership, Amazon is actually acquiring both. The first four of the incoming A330-300 freighters are new passenger aircraft that were never delivered to their original
From a flight training perspective, this business arrived at a great time. We have already committed to a two-year process of modifying our Airbus operating procedures in line with the manufacturer’s recommendations. The freighter fleet will be the first to use these procedures. Nonetheless, freighter pilot training development is still a large endeavor.
“Development takes roughly four months for a new airplane. Since we already fly the A330s, we were able to shorten this development timeline. However, all testing and revision times remain the same,” said Senior Director of Flight Training Kele Fergerstrom. “Through a safety assurance process, our Training
and information provided by Airbus. We then develop all the courseware that goes along with the syllabus, test it among a small cadre of pilots, train our instructors/evaluators on how to teach the new material, then deliver it to Line Pilots.”
The seven-day freighter course will familiarize Pilots with all the relevant procedures, focusing on the differences between the passenger and freighter versions of A330 operations. Pilots currently flying the A330-200 will receive some training credit and experience on the -300.
“We are already seeing the excitement from our existing mainland pilot commuters and we expect to attract more experienced pilots from different regions who prefer flying freight over passengers,” said Kele.
Under our contract with Amazon, we’re responsible for all Operations Programs, including Weight and Balance. Amazon will handle day-to-day load planning via vendors or their employees; we manage program policy, procedures, training, compliance, and oversight. This requires significant additions to the Weight & Balance Manual and a new Freighter Ground Operations Manual. Our 94 years of airline experience, including 13 years of A330 operating expertise, coupled with Amazon’s institutional knowledge of operating warehouses and providing ground handling services, will form a solid foundation for both programs.
The process involves understanding Amazon’s policies and procedures, then merging them with our own – similar to a Joint Procedures Manual. “The Amazon manuals follow the same template as all of our HA passenger operations manuals,
but they adopt many policies and procedures that are unique to their operations,” said Senior Director of Policy and Procedures Ryan Thomas. “While the procedures may differ from HA’s typical operations, they still conform to IATA standards, and all policy and procedure differences undergo a safety risk assessment before acceptance.”
It’s more work than it sounds. Certain aspects of these new manuals must be overhauled to align with Amazon’s needs and operation. Amazon’s freighters operate on a different load planning software called SABLE, and given the rework of the A330 bodies themselves, weight, capacity, and procedures can differ significantly from our passenger A330s. But the team will be ready when operations begin this fall. ■
Our first two A330-300s are scheduled to begin service this fall, initially flying freight between Amazon’s main distribution hubs at Cincinnati/ Northern Kentucky International Airport (CVG), and San Bernardino (SBD), then eventually serving Honolulu (HNL) as well. Seven more aircraft will join the fleet in 2024, with the final airframe delivered the following year. Amazon has an option to increase the fleet count according to its business needs. ■
Publicly traded companies have increasingly demonstrated their commitment to the longterm greater good via annual ESG (Environmental, Social and Governance) reports. For us, this is kuleana — a responsibility to our teammates, stakeholders, and communities — and we embrace it. The data requirements for this reporting are rigorous and standardized to meet investor expectations, so the 80-page report is not “light reading,” but it’s a treasure trove of information. Here are four things you should know about this year’s report.
We’re setting closer-in emissions and efficiency targets than 2050. Our industry will need time, collaborative development, and technological advances to decarbonize. While we aim for 2050, we will make moves in the meantime:
■ By 2028: Conserve 3 million gallons of jet fuel through operational initiatives, improve fuel efficiency per average seat mile by 4%*, and reduce electricity consumption per square foot in core facilities by 20%*
■ By 2030: Replace 10% of conventional jet fuel with sustainable aviation fuel (SAF)
■ By 2035: Reduce life-cycle jet fuel emissions intensity per revenue ton mile by 45%
Energy efficient facilities make a difference. We’ve already lowered our energy use per square foot in our facilities by 10% over four years — we will cut that to 20% by 2030. Our improvement to this point is primarily driven by efficiency gains from the use of motion sensors, LED lighting, and automatic heating, ventilation, and air conditioning control valves. And, we work with building owners and airports that prioritize these actions. The photovoltaic solar array built at our Corporate Headquarters, for example, saved us $33,000 a year and reduced CO2 emissions by 682,000 pounds.
Single-use plastics are on the way out, slowly. Because we increased our volume of flying from 2021 to 2022, we didn’t see progress except with our transpacific flights, which are carrying about 7% less singleuse plastic per flight. Our partnership with Jason Momoa’s Mananalu aluminum can water diverted almost 360,000 plastic bottles from our cabins last year.
Our team grew by 20% last year, and we’re stretching our wings. As we accelerated out of the pandemic and prepared for new business (Amazon) and future new flying (787s), we welcomed 1,371 new teammates — our biggest year for hiring in recent history. We also:
■ inked new contracts with IAM, TWU, and ALPA, providing significant compensation increases
■ expanded our reach into the community via our Career Ambassadors team, which participated in over 80 school and college events and conferences
■ highlighted the school-to-career pipeline partnerships we’ve forged — from our mechanics teaching classes at Honolulu Community College’s AERO program, to joining the LeapStart IT program with the University of Hawai‘i and the SkillBridge program at Embry-Riddle Aeronautical University.
■ supported our community — more than 1,200 employees, retirees, and families donated 6,795 hours to 175 organizations in Hawai‘i and the destinations we serve, while providing more than $830,000 in donations to nonprofits via travel, HawaiianMiles, and cash. ■ [ Read the full report ]
1 2 3 4
Bennet Walsh, Managing Director of Safety & Security, is marking his two-year anniversary at our company. When he started, he faced the challenge of a depleted Safety team while working through a pandemic. Since then, he has grown the core team, worked to break down silos among operating groups, improved data collection and analysis, and infused the program with our Purpose and Values. We spoke with Bennet to learn more about a Safety Kuleana campaign launching next month.
What has changed with our safety program? First, we needed to lay the groundwork to fundamentally improve our safety organization. We are committed to partnering with and mentoring our operational divisions to build a positive safety culture via our people, processes, and data. President & CEO Peter Ingram led the recharting of our Safety and Security Policy, setting the expectation from the top that Hawaiian Airlines would align safety and security culture with our Purpose and Values.
Our policy also incorporated Just Culture, a system of shared accountability between the organization and the employees –used by many industries – that recognizes everyone has a role to play in reducing accidents and incidents. There are lingering perceptions of inequity across divisions regarding discipline and corrective actions. Just Culture is a shift: the focus is recognizing that errors happen, but a transparent and collective approach to root cause – versus blaming – reduces errors and increases safety. We are the first U.S. air carrier to commit to it at this level.
Also, we expanded the team to better respond to incidents and analyze data for trends or risk centers in all operating areas. We have positioned our Safety team to close the loop with the people who need the information the most. We clearly heard that there’s little incentive to engage and report hazards and incidents if the employees submitting them do not know what becomes of their reports. That is changing with the launch of the Intelex app, earlier this year. Intelex is an enterprise safety system that breaks down silos across operations with better reporting avenues, programs, workflows, and data connectivity. The old app was ineffective for submitting incidents, especially for those trying to extract data.
The timing is right for a campaign to bring awareness and understanding to this work. We’ve improved processes and data, now we need our people — all our people — to ensure our program is fully realized.
What is the objective of the Safety Kuleana campaign launching next month? The best way to mitigate operational risks is through our people using their training and common sense to promptly identify and rectify issues. The campaign will offer messaging and training for all levels to promote safety
ownership. Additionally, management training will center on identifying root causes by focusing on what rather than who.
It also brings our Purpose and Values front and center, where they belong. It is the great thing about our company, and you see it naturally reflected around the operation — people here care for one another. That comes from shared experiences and connections to the Islands and this community. So, to be intentional about Safety, it’s leaning into that feeling of mālama and elevating our shared responsibility to preserve that — for each other and our guests.
Our aim for this campaign and Just Culture training is to foster a team-based approach towards risk reduction, minimize the frequency, severity, and duration of accidents and incidents, and ultimately ensure the safety and well-being of our ‘ohana and guests. We can do the work to ensure we’re all contributing to our company’s safety legacy. Each of us owns that.
With our on-time performance focus, how do we ensure that safety is the top priority? Every movement we make must be safely on time. Our processes and procedures are designed to strike that balance. Sometimes conditions impacting the operation stretch procedures and personnel to a point where they feel they must compromise one or the other. Whether you are a manager or frontline, we all have the Safety Kuleana to recognize when it’s time to slow down. When we rush and compromise procedures, we increase risk. Additionally, our campaign aims to empower all employees to actively engage in safety reporting whenever procedures conflict with safe performance of their duties or when they discover a hazard.
How does this initiative change a typical frontline shift or day at the office? It encourages proactive risk and hazard mitigation. What that looks like can vary. It could involve employees speaking up if they notice something wrong, slowing down until the issue is resolved, or reporting incidents promptly to their supervisor or the Safety team. There will be more obvious signs that risk mitigation matters, and everyone should feel more empowered to take ownership of their safety as well as the safety of their colleagues. ■
I kīnohi o ka lā 1 o Mei ho‘i i ho‘omaka ai kā kākou ho‘olaule‘a ‘ana me ka ho‘āno hou ‘ia ‘ana o kekahi mele i kuluma iā kākou, na ‘elua mau pu‘ukani kaulana ‘o Auli‘i Cravalho lāua ‘o Paula Fuga. Ua hāmama maila ka Pahu A‘o o lalo o hale Koapaka i nā hoa hana i ‘i‘ini e hana i ka lei a hā‘awi paha i ka lei, a ua ho‘olako ‘ia he kui, he kaula, a me nā ‘okika. I ko kākou anamana‘o ‘ana i nā hoa hana, ua ho‘omaopopo kākou ‘o ka pua kenikeni ka pua helu ‘ekahi i waena o kākou. A ua pani ‘ia ka lā ma ka ‘Aha Mele Kū Makahiki ‘o Lā Mei na Ka Hui Wa‘alele ‘o Hawaiian, ma ke kahua o Kaiwi‘ula, me nā pu‘ukani ‘o Keauhou, ‘o Robert Cazimero, a me nā hoa ‘ē a‘e. Mana‘olana kākou ua pumehana ‘oukou i ke aloha ma ka Lā Mei – a me nā lā a pau!
We kicked off Lei Day with a tribute to the classic mele, remixed with a twist by two of Hawai‘i’s brightest stars, Auli‘i Cravalho and Paula Fuga. We opened our pop-up room at Corporate Headquarters to teammates who wanted to make a lei and give a lei — supplying them with needles, string, and loose orchids. A poll of our employees found that pua kenikeni are your preferred flowers for lei. And, we finished the day with our annual Hawaiian Airlines May Day Program at Bishop Museum, featuring performances by Keauhou, Robert Cazimero, and special guests. We hope you felt the warm embrace of aloha on May Day — and continue to do so every day! ■