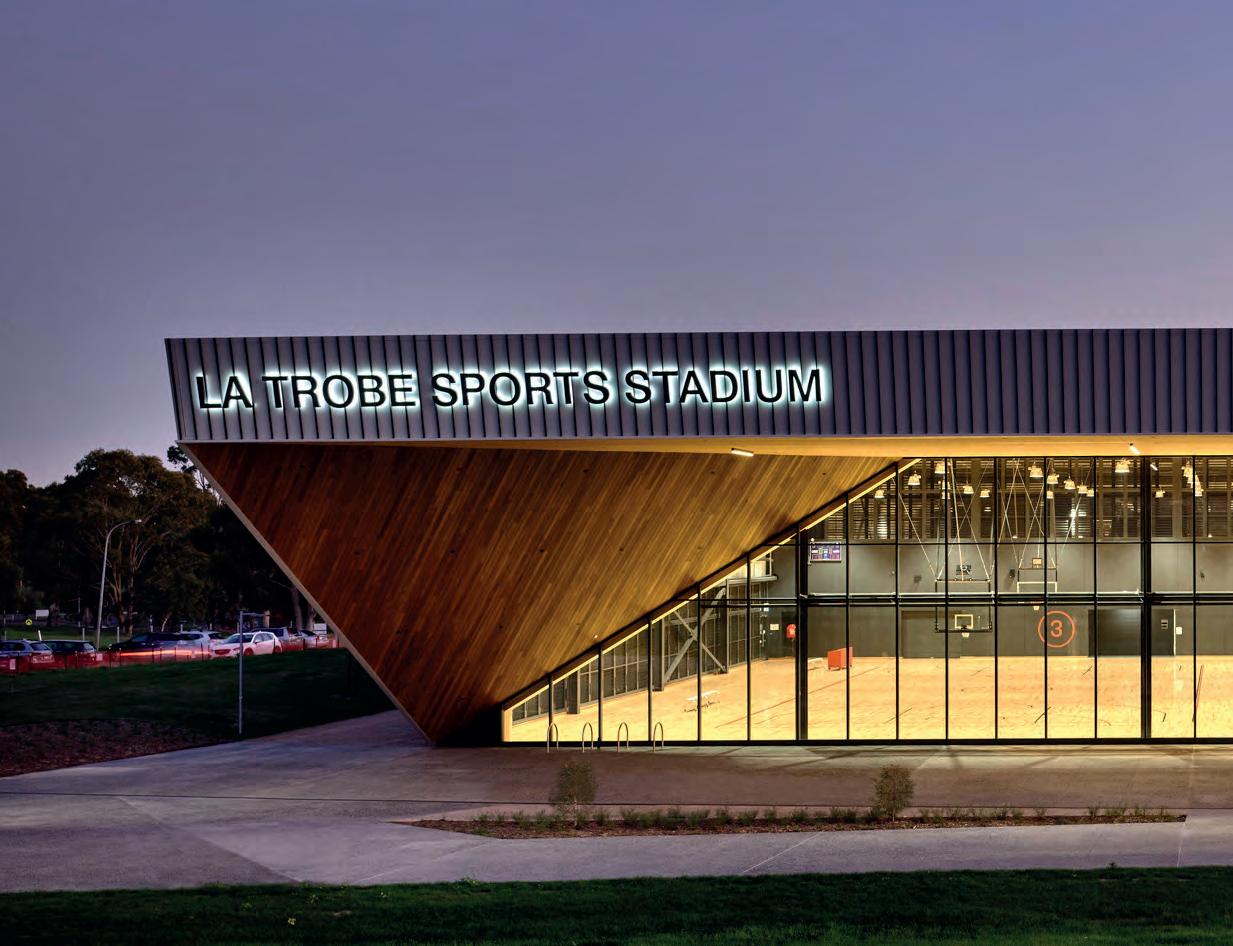
7 minute read
La Trobe University Sports Stadium
from sb 5/2022 (english)
by IAKS
Location Melbourne, Australia Client / operator La Trobe University Architects Warren and Mahoney AU – 3000 Melbourne www.warrenandmahoney.com MJMA CA – M5V 3C1 Toronto www.mjma.ca Author Warren and Mahoney Photos Derek Swalwell
Official opening January 2020 Construction costs EUR 33.7 million
AUSTRALIA’S FIRST HIGHEST RATED SPORTS BUILDING IN DESIGN AND SUSTAINABILITY
LA TROBE UNIVERSITY SPORTS STADIUM IN MELBOURNE
The La Trobe University Sports Stadium has been designed by Warren and Mahoney in association with MJMA Toronto and is an Australian-first. Generating more energy on site than it uses – making it net positive – it is the first sports building in Australia to be awarded the highest rating for both the design and build by the Green Building Council of Australia. This was achieved through an integrated strategy covering building material performance, natural ventilation, sustainable energy generation, water storage and reuse, and building management and operational strategies.
As a centralised facility, the Sports Park offers high ball sports courts, high performance assessment and testing laboratories, teaching spaces and sports management tenancies. Breaking down barriers between industry and the student experience, the stadium provides facilities for grass root community sport and in return creates a pathway to connect the community and university life. The Sports Park Stadium project allows student sport and sport related clubs to increase student participation; actively engaging the local community and schools through the use of enhanced sporting facilities and sport services at LaTrobe; leveraging sports facilities to encourage all members of the university to improve their health and fitness; securing long-term, meaningful institu-

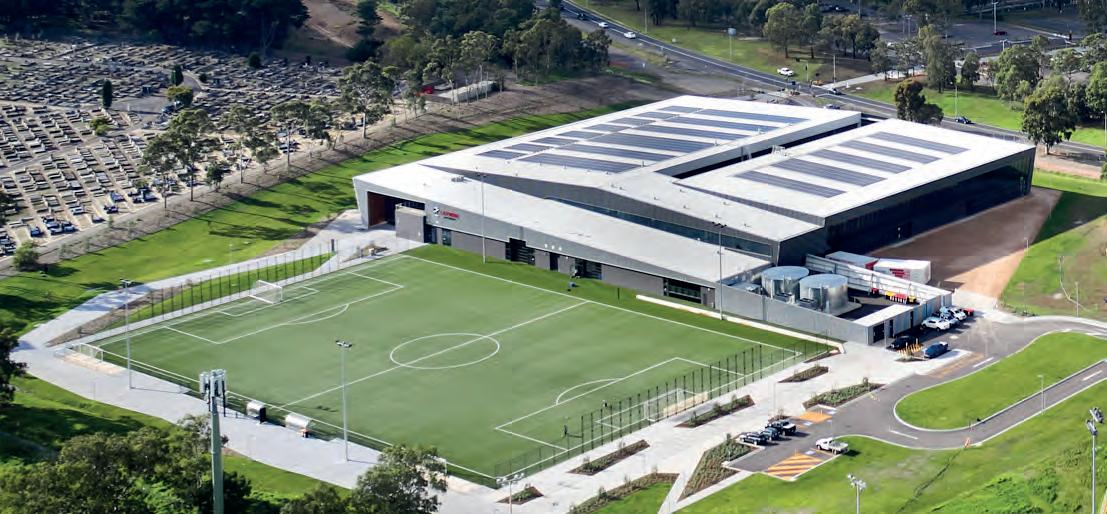
tional influence within the sport industry in Victoria and Australia; and developing links between high performance sport and the teaching and research capacity of the university.
Passive design and a photovoltaic roof The facility was designed as a Net Zero emissions building. This was achieved through application of the energy hierarchy-optimised passive design which includes natural and mixed mode ventilation, a highly efficient facade well over BCA minimums, highly efficient all-electric building systems and maximisation of PV on the extensive roof. The mixed mode provided challenges in terms of thermal separation and performance between the naturally ventilated and conditioned spaces. The stadium is equipped with a vast high-spec photovoltaic array on the roof that amounts to over 519 kW and generates around 724,000 kWh per year. This is more than enough to meet the stadium’s electrical demand, so surplus renewable energy is fed back into the rest of the campus. The first major piece of La Trobe’s bold “University City of the Future” plan, the stadium and surrounding park will help it achieve its Net Zero strategy for a net positive operation.
The building makes use of the stack effect to enable an effective natural ventilation to the sports courts. High level windows also facilitate this, providing daylight into all spaces in line with best practice levels. The building has considered
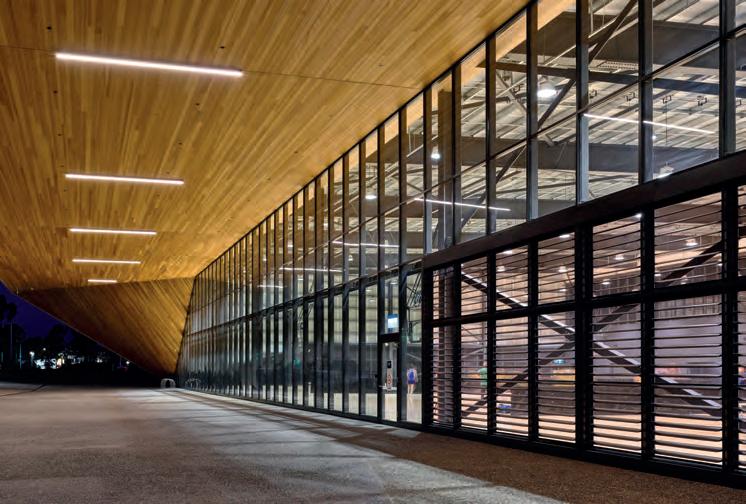

PHASE 2 PHASE 1
The project was designed to accommodate a third fieldhouse expansion. Each fieldhouse uses natural ventilation with base louver walls allowing fresh air to enter low and exhaust high through banks of upper clerestory louvers located
The project was designed to accommodate a third fieldhouse expansion. Each fieldhouse uses natural ventilation with base louver walls allowing fresh air to enter low and exhaust high throubetween each fieldhouse. The rooftop houses a full PV array with interspersed linear skylights to power the building banks of upper clerestory louvers located between each field house. The rooftop houses a full PV array with interspersed liand provide daylight autonomy to the fieldhouses throughout the day. near skylights to power the building and provide daylight auto to the fieldhouses throughout the day.
climate change adaptation and resilience – future climate change scenarios were assessed and building design responses implemented to address identified risks. These include the provision of plant space for additional services and others.
Procurement, cost allocations and environmental performance Operable louvres were implemented with the wall construction and structural systems to achieve a high level of natural ventilation to the 3-court event hall and community halls. There were some challenges experienced, including the setting of pre-set modes responding to the building weather station and overrides for the operational staff to control air movement on high wind days.
Naturally ventilated cells (courts) were created to separate the naturally ventilated courts from the high thermal insulation education, commercial and front of house areas. The wall separating the conditioned space from the naturally ventilated space was treated thermally as an external wall.
The skylight design was modified using a combination of off the shelf products to ensure that the skylights perform thermally similar to the adjacent roof insulated panels, incorporating a top material to match the roof profile of the selected roof and a bottom layer to create an air gap and internal appearance to match the perforated acoustic metal lining to the interior.
The structural design of the long span roof drew from architectural elements, such as the striking cantilevered canopy over the main entrance and the trussed columns in the southern hall, to find an efficient form. By using these features as key structural elements, a reduction in the overall amount of structural steel – a highly carbon intensive material. Reduced by 21.1 tonnes, it resulted in a 5 % decrease across the whole building.
7
1
2
4 2
21
7
9 5
10
13
4
611
12 7
18 15
7 3
4
7
20 22 21
21 10
4
4
20
920
19
22 11
4
21 10
920
20
920
er walls allowing fresh air to enter low and exhaust high through near skylights to power the building and provide daylight autonomy
819 Level 1Level 1
1. Main Entrance 1 2. LobbyLobby 2 3. Reception 4. WC / Changerooms WC / changerooms 3 5. Cafe 6. Sta RoomTeaching lab 4 Level 1 7. Teaching LabRunning track 8. Running Track 5 1.Main Entrance 9. Biomechanics LabBiomechanics lab 6 2.Lobby 3.Reception 4.WC / Changerooms 10. Environmental Chamber 11. Strength & ConditioningStrength & conditioning 7 5.CafeWeights & cardio 6.Sta Room 8 F 7.Teaching Lab uture Phase courts 9 8.Running Track 9.Biomechanics LabCommunity courts 10 S 10.Environmental Chamber 11.Strength & Conditioninghow courts 11 2,500 seat show court
12. Weights & Cardio 13. Research Lab 14. Service 15. Pedestrian Entrance 16. Field Entrance 17. Fire Water Tanks 18. Loading 19. Future Phase Courts 12.Weights & Cardio 20. Community Courts 13.Research Lab21. Show Courts 14.Service 15.Pedestrian Entrance 22. 2500 Seat Show Court 16.Field Entrance 17.Fire Water Tanks 18.Loading 19.Future Phase Courts 20.Community Courts 21.Show Courts 22.2500 Seat Show Court
Sustainable performance over entire lifespan Provision has been made for the modification of the Event Stadium and Show Court, so that it transitions from a ventilated three court sports hall to being a thermally sealed conditioned space to address patron comfort for the 2,500 patrons that will be accommodated by retractable seats on both sides of the main show court.
There is also provision in the design to accommodate more teaching spaces and an additional three courts to the south of the site to increase the capacity of the facility to meet the requirements of the local community and add to the university campus experience. Consideration of future expansion and provision for that expansion is a critical piece of addressing the sustainable performance of the building.
Exceeding the Green Building Council of Australia’s criteria The stadium achieved innovation points for sustainable sourcing, use and disposal of materials, material reduction and efficient material use, with 16 % of the building area fit out with locally procured sustainable products.
The contractor, client, and design team conducted a whole of building Life Cycle Assessment using eToolLCD software, comparing the building to a “Business as Usual (BAU)” reference case. This frame of reference was important to position the project in terms of its sustainable outcomes. The structurally efficient design achieved a reduction of 15 % in embodied carbon (the greenhouse gas emissions generated upfront to construct the building) compared to the “BAU” level.
The support of the client team and the operators was critical to the successful six star “As Built” rating but was principally credited to the post construction phase of the project and the client’s initiatives to support the design data with an operational response.