
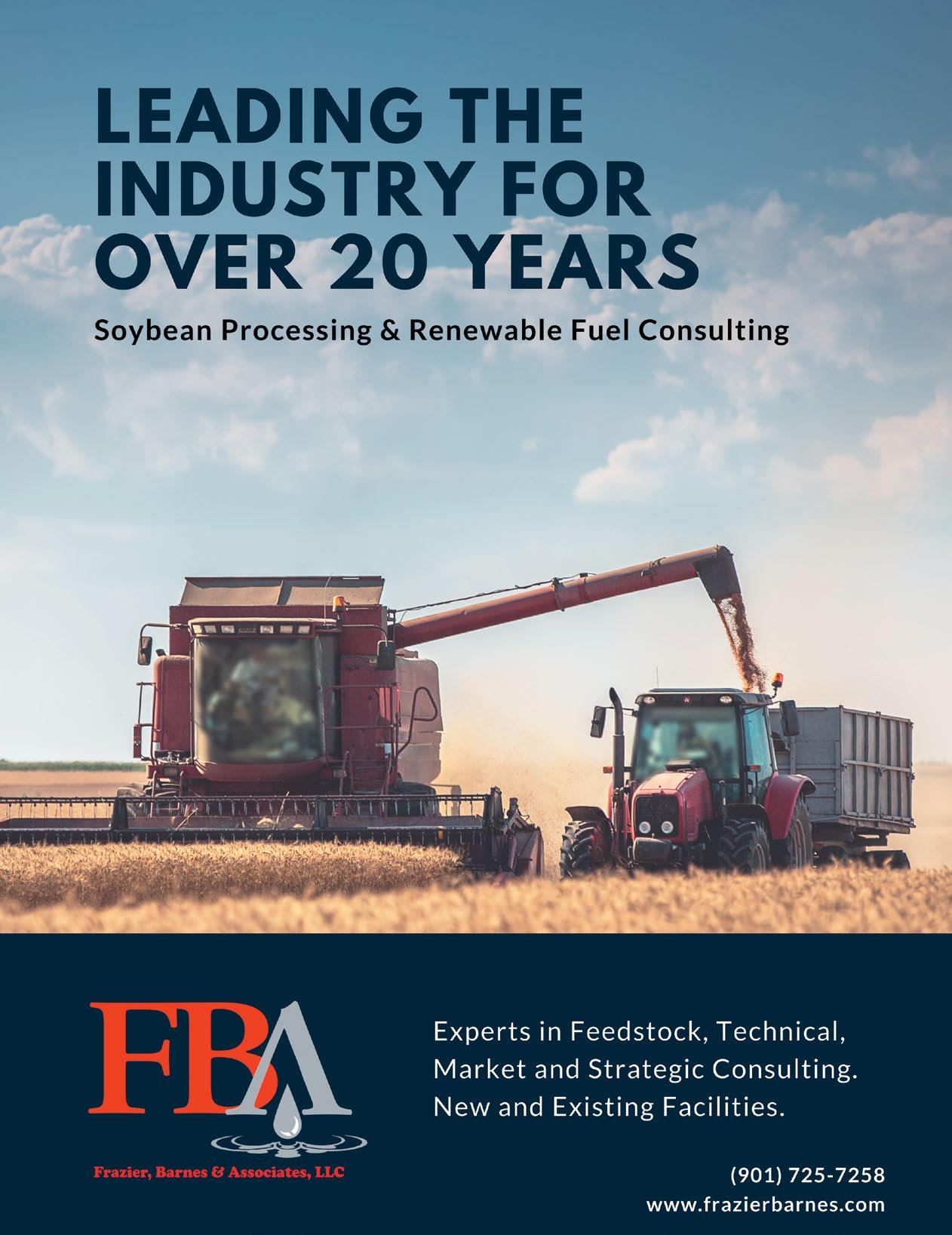
The journey to cleaner skies starts now. Sustainable aviation fuel is no longer an experiment but a prerequisite for low-carbon air transport. Industry players, passengers, and the planet will benefit. And our range of proven green-energy technologies is ready to help you produce more in-demand, renewable SAF.
Turn your sustainable ambitions into a sustainable business.
Join Flight Plan Green. Find out how: topsoe.com/saf
From
With the current global supply chain issues it isn’t always easy to keep production running while managing complex streams of raw materials and finished products.
Evonik is helping the North American Biodiesel industry by offering the highest quality Sodium Methylate directly from our recently expanded production site in Theodore, Alabama, including rail to truck transloading terminals located in Kansas City, East Chicago, Baltimore, Arizona and Alberta.
At the same time Evonik offers global supply of Sodium Methylate from our other production facilities in Germany, Argentina and, coming soon, South East Asia.
Looking for readily available Sodium Methylate for your biodiesel production? Ask our biodiesel experts! biodiesel-nam@evonik.com
ADVERTISERS:
For advertising sales please call 218-745-8347, email editor@biobased-diesel.com or visit our website at www.biobased-diesel.com.
Biobased DieselTM is published by RonKo Media Productions LLC. Subscriptions are free of charge to those in the United States and Canada. To subscribe, visit biobased-diesel.com and fill out the contact form in the website footer. For subscribers outside the United States and Canada, a digital version of the magazine will be emailed. For those located outside the United States and Canada who wish to have a print version of Biobased DieselTM mailed, please email editor@ biobased-diesel.com with the request. A nominal postage fee may be required. For mail correspondence, write to: RonKo Media Productions PO Box 86 Warren, MN 56762 All rights reserved. No part of this publication may be transmitted or reproduced in any form without written permission from the publishers. The information contained within has been obtained from sources believed to be reliable. Neither the publisher nor any other party assumes liability for loss or damage as a result of reliance on this material. Appropriate professional advice should be sought before making personal,
The legendary boxer Mike Tyson famously said, “Everybody has a plan until they get punched in the mouth.” The biobased diesel industry took that punch Dec. 1 when U.S. EPA finally released its “set” proposal for the Renewable Fuel Standard. When Congress passed the second iteration of RFS as part of the Energy Independence and Security Act of 2007, it included statutory volumes for conventional, advanced and cellulosic biofuels through 2022, but left biomass-based diesel volumes up to EPA’s discretion with certain guidance. From 2023 onward, EPA has much more latitude in administering all aspects of the program.
Heading into the RFS set process, hopes were high. Many U.S. renewable diesel projects came online in 2022, proving the buildout of this industry wasn’t mere conjecture—it was actually happening. Check out some of the news on page 11 and the story on Montana Renewables on page 30.
Then the punch came—punches really, as it was a vicious combination. For biobased diesel, EPA suggests moving from 2.76 billion gallons in 2022 to 2.82 billion gallons in 2023, 2.89 billion gallons in 2024 and 2.95 billion gallons in 2025. For advanced biofuels, the agency proposes moving from 5.63 billion ethanol-equivalent gallons (3.75 billion biodiesel-equivalent gallons) in 2022 to 5.82 billion gallons in 2023, 6.62 billion gallons in 2024 and 7.43 billion gallons in 2025.
While 7.43 billion gallons sounds like a lot, it’s not—for two reasons. One, remember, that’s ethanol-equivalent gallons, so in biodiesel-equivalent gallons, that’s 4.95 billion. Two, for 2025, EPA proposes to drastically increase the cellulosic biofuel subcategory within the advanced biofuels category to 2.13 billion ethanol-equivalent gallons. Although appreciable volumes of wood-based diesel that might qualify for this subcategory may come online by 2025, that’s not why EPA wants to spike cellulosic biofuel volumes. The agency is doing this to accommodate socalled eRINs for electric vehicles (EVs), manifesting the Biden administration’s clear and obvious bias toward EVs. When the proposed 2025 cellulosic volumes are subtracted from the proposed 2025 advanced biofuel volumes, and the remainder is converted to biodiesel-equivalent gallons, we are talking a little over 3.5 billion gallons—more than half a billion gallons less than the U.S.’s installed operable biodiesel and renewable diesel production capacity in 2022, not to mention hundreds of millions of gallons of qualifying imports and the billions of gallons of additional capacity that will be online in three years. To visualize how grossly undersized EPA’s volume proposals are, check out the simple but effective graphic on page 16 in the information section.
To put this all in perspective, just think about four large-scale projects by oil refiners or oil-refiner partnerships that are either online now or soon will be: Diamond Green Diesel’s facilities in Louisiana (690 mgy) and Texas (470 mgy), both of which are now operating; Phillips 66’s Rodeo, California, refinery conversion (800 mgy), scheduled for start-up in 2024; and the Marathon/ Neste joint venture (730 mgy) in Martinez, California, planned for operations in 2023. Together, these four sites alone represent 2.69 billion gallons of annual capacity. If EPA’s proposal for the 2025
biomass-based diesel volumes becomes final, these four plants— if operated at capacity—could satisfy 91 percent of that year’s D4 RIN obligations, leaving dozens and dozens of other large- and small-scale renewable diesel and biodiesel producers across the country in the lurch to vie for the remaining 260 million gallons’ worth of crumbs in the RFS subcategory.
While ethanol stakeholders seemed pleased with the proposal, and virtually everyone appreciates the idea of rolling out volume obligations for multiple years to provide stability, biobased diesel advocates described the proposed volume requirements for 2023-’25 as “woeful,” “lackluster,” and “a missed opportunity.” Some even pointed out the obvious: The agency and its proposal are not keeping up with the rapid growth in renewable diesel production—let alone acting as a market-moving mechanism. Others went further. The American Soybean Association said, “These very insignificant volume increases for 2023-’25 realistically could not only stifle growth but also jeopardize the existing biofuels industry.”
The one-two punch of low biobased diesel volumes and soaring cellulosic biofuel volumes to accommodate Biden’s EV agenda is an astounding wakeup call for those who thought this industry’s troubles were over once the new administration took office. The electrification agenda is so ubiquitous it is even infiltrating what was clearly established 15 years ago as a liquidfuels program. In the words of Geoff Moody, the senior vice president of government relations and policy for the American Fuel & Petrochemical Manufacturers organization, “[EPA] must also hold true to the legacy of RFS as a liquid-fuels program—not an electric-vehicle program—by rejecting yet another massive regulatory subsidy for electric-vehicle manufacturers.”
I have been a boxing fan even longer than I’ve been covering these industries, which is one reason why I used the Tyson quote to lead off this column. The biodiesel industry and its U.S. trade association Clean Fuels Alliance America (formerly the National Biodiesel Board) have long been said to punch above their weight class in terms of getting things done in Washington, D.C. Year after year, over decades, the association and its members have been able to surmount the insurmountable, forever the underdog to rise, not without surprise, to the occasion again and again.
The time to do this once again is here. Submit well-reasoned, informed, data-backed and impassioned comments to EPA during the open-comment period. The time is now.
Less famously but just as astute, Tyson also said about his growing up, “My disadvantage was my advantage.” This seems just as true for the biobased diesel sector. Let’s convert these obstacles into opportunities and, yet again, turn this around.
Ron KotrbaCrown technology delivers maximum contaminant removal to extend hydrotreater catalyst life. Get the cleanest possible feedstock delivered to your hydrotreater and achieve up to double catalyst life with Crown technology. Our rugged, robust RD Ready ™ Pretreatment System is guaranteed to meet product specs for all common contaminants and drastically improve plant uptime by reducing the need for catalyst changeovers. Backed by the construction of 50+ biodiesel plants, design of 10+renewable diesel pretreatment plants, and a propriety database of feedstock specs and results, Crown RD Ready ™ Pretreatment System protects your investment now, and in the future. Protect your hydrotreater and your Renewable Diesel operation with CPM and Crown. Edible Oils | Biodiesel | Renewable Diesel | Oleochemical Contact CPM and Crown today 1-651-639-8900 or visit our website at www.crowniron.com
When it comes to Plasma Blue technology and its benefits to new and existing biodiesel and ethanol plants, seeing is believing.
Join Plasma Blue at this year’s Clean Fuels Conference on Jan. 23-26, 2023 in Tampa, FL as we bring the technology to life.
Stop by booths 16 & 17 to view a technology demonstration, ask questions and learn how Plasma Blue can positively impact your plant’s profitability.
Demonstration times
January 24 10:30 a.m. 3:00 p.m.
January 25
10:30 a.m. 1:30 p.m.
To learn more, visit plasma-blue.com or email info@plasma-blue.com to schedule a private demonstration.
Policy achievements in the U.S. and Europe spur continued investment, project development and supply agreements.
The European Parliament adopted its position on new draft European Union rules to increase the uptake of sustainable aviation fuel (SAF) by EU planes and airports to ensure Europe becomes climate neutral by 2050. From 2025, this share will be 2 percent, increasing to 37 percent in 2040 and 85 percent by 2050, up from the European Commission’s original proposal of 32 percent for 2040 and 63 percent for 2050. [BBD]
In the U.S., President Joe Biden signed the Inflation Reduction Act into law Aug. 16. Among the myriad climate-change provisions in the law are key biofuel incentives, including a new SAF tax credit ranging in value from $1.25 to $1.75 per gallon based on greenhouse-gas (GHG) reductions, through 2024, and a clean fuel production tax credit from 2025-’27. The legislation, combined with the SAF Grand Challenge introduced in 2021, is expected to significantly incentivize SAF production and use in the U.S. The U.S. DOE subsequently released the SAF Grand Challenge Roadmap, a collaboration between DOE, USDA, U.S. EPA, the Federal Aviation Administration and Department of Transportation. The roadmap is intended to help achieve the goals of the SAF Grand Challenge, which are for industry to produce 3 billion gallons per year (bgy) of SAF by 2030 and 35 bgy by 2050—enough to meet 100 percent of domestic demand. [BBD]
Member states of the International Civil Aviation Organization adopted a collective long-term global aspirational goal (LTAG) of net-zero carbon emissions by 2050 at the 41st ICAO Assembly this fall in Montréal, where 2,500 delegates from 184 states and 57 organizations convened. The LTAG will rely on numerous measures, including increased production and use of SAF. [BBD]
In one of the world’s largest SAF-supply deals, Neste Corp. signed an agreement with Air France-KLM Group to provide more than 330 million gallons of SAF over eight years. The new agreement builds on a relationship that began in 2019. Air FranceKLM also recently signed an MOU with Total Energies for more than 265 million gallons of SAF over 10 years. Total aims to produce half a billion gallons of SAF by 2030. [BBD]
Aemetis Inc. has signed $7 billion worth SAF and renewable diesel supply agreements with 10 airlines for a total of 916 million gallons of blended SAF, to be produced at its future Carbon Zero biorefineries in California. Airline customers include Delta, JetBlue, American Airlines, Alaska Airlines, British Airways, Cathay Pacific, Finnair, Iberia, Japan Airlines and Qantas [BBD]
Vienna-based oil refiner OMV signed an MOU with Lufthansa Group for the supply of more than 270 million gallons of SAF through 2030. OMV plans to scale up SAF coprocessing to approximately 240 mgy in 2030. The company also signed an MOU with Wizz Air for 62 million gallons and with Europe’s largest airline, Ryanair, to supply up to 53 million gallons. Meanwhile, Ryanair signed an MOU with Shell for access to 120 million gallons of SAF between 2025 and 2030. Shell, in turn, has signed a five-year MOU with Korean
Air to supply SAF at major airports in Asia Pacific and the Middle East beginning in 2026. [BBD]
Breakthrough Energy Catalyst is providing LanzaJet a $50 million grant to complete construction of its 9 mgy alcohol-to-jet SAF plant, Freedom Pines Fuels, in Soperton, Georgia. [BBD]
United Airlines Ventures has made a strategic investment of up to $37.5 million in Next Renewable Fuels, a 750 mgy SAF and renewable diesel project in Oregon. Next received a crucial air permit from the state recently, as well. Next plans to go public via a merger with a special purpose acquisition company (SPAC) wherein a newly formed subsidiary of Industrial Tech Acquisitions II will merge with Next, with Next surviving as a wholly owned subsidiary. [BBD]
Brasil BioFuels plans to build a new SAF plant in Manaus, Brazil, scaled at approximately 165 mgy using Topsoe’s Hydroflex™ and H2bridge™ technologies. Production is expected to start in 2025. [BBD]
Gevo Inc. broke ground on its first commercial-scale SAF facility, Net-Zero 1, in Lake Preston, South Dakota. Net-Zero 1 is expected to produce 55 mgy of SAF. Gevo expects to close financing in 2023 and begin construction. The company plans to begin delivery of initial SAF volumes in 2025. Gevo recently signed new supply deals with Alaska Airlines, America Airlines, Aer Lingus, Qatar Airways, Iberia Airlines, and Virgin Atlantic [BBD]
World Energy plans to convert its large biodiesel-plant site in Houston, Texas, to manufacture 250 mgy of SAF by 2025. The company is also expanding its California facility to make 250 mgy of SAF by 2024. World Energy recently launched its QuestZero program to help companies meet their net-zero goals, signing Etihad Airways as its first commercial airline to participate. [BBD]
RMI and Energy Web Foundation plan to build a digital registry for SAF certificates (SAFc) that will bring more transparency to emissions-reduction claims. SAFc will enable companies by mid-2023 to pay for environmental benefits of SAF, even if the physical fuel is not yet available for their flights. Decoupling SAF’s environmental attributes from the physical fuel will democratize access to SAF’s benefits and catalyze SAF supply at scale. [BBD]
The Royal Air Force, Airbus and other industry partners recently carried out the world’s first 100 percent SAF flight using an in-service military aircraft. In November, both engines of an RAF Voyager flew entirely on 100 percent SAF. [BBD]
Several U.S. plants come online as major Canadian and European projects move forward.
On Dec. 1, the U.S. EPA finalized approval of canola/rapeseed oil for use as renewable diesel and sustainable aviation fuel (SAF) feedstock under the Renewable Fuel Standard, allowing hydrotreated fuels made from canola and rapeseed oils to qualify for the program and generate renewable identification number (RIN) credits. Similar to other RFS fuel pathways, hydrotreated biofuels produced from canola or rapeseed oil are eligible for D4 biomass-based diesel RINs if they are not coprocessed with petroleum. Coprocessed canola or rapeseed oils are eligible for D5 advanced biofuel RINs. Canola- or rapeseed-based naphtha and LPG produced via hydrotreating also qualify to generate D5 RINs. In addition, the agency finalized its definition of “canola/ rapeseed oil.” [BBD]
Diamond Green Diesel, a joint venture between Valero Energy Corp. and Darling Ingredients Inc., came online in November with its 470-million-gallon-per-year (mgy) renewable diesel facility in Port Arthur, Texas, six months ahead of schedule. With plants in Texas and Louisiana, DGD now has the capacity to manufacture nearly 1.2 billion gallons per year (bgy). [BBD]
BP has completed expansion of renewable diesel coprocessing capacity at its Cherry Point refinery in Washington state. The refinery doubled its renewable diesel capacity and is now able to coprocess nearly 110 mgy from waste vegetable oil and animal fats. BP first announced the expansion plans in fall 2021. [BBD]
HF Sinclair Corp. has begun renewable diesel production at its Navajo Refinery in Artesia, New Mexico. The unit is scaled to produce approximately 125 mgy. The site is also equipped with a new feedstock-pretreatment unit. The company’s 90 mgy renewable diesel unit in Cheyenne, Wyoming, is also operational. In addition, HF Sinclair has a 117 mgy renewable diesel refinery in Sinclair, Wyoming [BBD]
Seaboard Energy, a division of Seaboard Foods, cut the ribbon in October on its new 85 mgy renewable diesel facility in Hugoton, Kansas, marking start-up of production. An onsite feedstock-pretreatment plant has also been completed. Topsoe provided its renewable diesel and hydrogen production
technologies, HydroFlex™ and H2bridge™, respectively, for the project. Seaboard Energy has also begun operations at its renewable fuels distribution terminal in Madera, California. The company welcomed its first unit train of 110 railcars in late October. Seaboard is railing in renewable diesel produced in Kansas along with biodiesel manufactured at its Missouri and Oklahoma plants and blending the two biofuels together in Madera for distribution in California. [BBD]
Heartwell Renewables, a joint venture between Love’s and Cargill, broke ground in November on its new 80 mgy renewable diesel processing facility in Hastings, Nebraska. The plant will use tallow provided by Cargill, as well as vegetable oil feedstock. Heartwell Renewables expects operations to start in summer 2024. [BBD]
Construction is underway on the Green Bison Soy Processing complex, a $350 million joint venture between Archer Daniels Midland Co. and Marathon Petroleum Corp., in Spiritwood, North Dakota. By harvest 2023, the plant is expected to be producing 600 million pounds of refined vegetable oil annually, which will be supplied exclusively to Marathon as feedstock for renewable diesel. [BBD]
Fluor Corp. has been awarded a reimbursable front-end engineering and detailed design, engineering and procurement services contract for Imperial, which is developing a renewable diesel complex at its Strathcona refinery near Edmonton, Alberta, Canada. The new complex is expected to produce about 285 mgy. Fluor will design and integrate a new renewable diesel unit into the existing Strathcona refinery. The integration will include a series of utility tie-ins, electrical and control-systems integration as well as commodity storage, loading and unloading capabilities. [BBD]
Topsoe has been selected by Federated Co-operatives Ltd. to provide its HydroFlex™ process technology for renewable diesel production in Regina, Saskatchewan, Canada. Once fully operational, the FCL renewable diesel plant will have the potential to produce approximately 215 mgy. The complex includes a canola-crushing plant. FCL expects to be producing renewable diesel in 2027. [BBD]
Italian petroleum refiner Eni S.p.A. is investigating the opportunity to build a new biorefinery at its industrial site in Livorno, Italy. The feasibility study involves building a feedstockpretreatment unit, an Ecofining™ facility scaled at approximately 165 mgy, and a plant for hydrogen production from methane gas. The design will be completed in 2023 and construction could take place by 2025. This would be Eni’s third converted refinery in Italy to produce renewable diesel after Venice and Gela. The company recently completed construction of a 15,000-ton oilseed collection and pressing plant in Makueni, Kenya, which is processing castor, croton and cottonseeds. In October, the first shipment of oil left the port of Mombasa on its way to Eni’s Gela biorefinery. [BBD]
Neste Corp. is spending $2 billion to nearly double capacity at its renewable diesel plant in Rotterdam, the Netherlands. The plant is expanding from nearly 475 mgy to close to 915 mgy. Roughly 44 percent of its total, expanded capacity in Rotterdam will be capable of refining SAF. Technip Energies was awarded the engineering, procurement services and construction management contract. Neste plans to complete the project in 2026. Once its expansion projects in Rotterdam and Singapore, plus its joint venture with Marathon in California, are complete, Neste expects to have a total production capacity of 2.3 bgy. [BBD]
Calgary, Alberta, Canada-based Canary Biofuels has acquired the assets of Community Fuels, including its 10-milliongallon-per-year (mgy) biodiesel facility in Stockton, California, and a dedicated fuel terminal. The Stockton plant is not currently producing biodiesel fuel. Canary is evaluating engineering and retrofit options to increase efficiency, throughput and capacity. Meanwhile, Canary’s plant in Lethbridge, Alberta, has begun biodiesel production after retooling the 20 mgy facility with multifeedstock technology and a distillation unit. Canary is also constructing a 60,000-ton canola-crush facility at the site. [BBD]
Neste Corp. is acquiring the used cooking oil collection and aggregation business and related U.S. assets of Crimson Renewable Energy Holdings LLC. The transaction does not include Crimson’s biodiesel plant in Bakersfield, California. [BBD]
Northeast Biodiesel has begun manufacturing biodiesel in Greenfield, Massachusetts, after years of development and funding issues. The plant is scaled at 1.75 mgy and Northeast Biodiesel plans to double capacity in the future. [BBD]
Pacific Biodiesel opened two off-grid biodiesel-fueling stations so far in Hawaii on Maui and Hawaii Island, with a third planned in late 2022 and eventually six total. Each station holds 8,000 gallons of distilled B100 produced at the company’s refinery on Hawaii Island, which celebrated a decade of operations in 2022. [BBD]
Missouri Gov. Mike Parson signed legislation creating a 2-cent-per-gallon (cpg) tax credit for B5 to B10 blends and a 5 cpg incentive for blends greater than B10 but less than B20. The law also establishes a 2 cpg tax credit for biodiesel produced in Missouri. [BBD]
Cargill Inc. is acquiring Owensboro Grain Company LLC, including its soy-processing complex and biodiesel facility in Owensboro, Kentucky. Terms were not disclosed, and the transaction is expected to be complete in early 2023. [BBD]
Across the pond, Cargill’s new 35 mgy waste-to-biodiesel production facility in Ghent, Belgium, is now operating. Under construction since late 2020, the $150 million project was designed and built by BDI-BioEnergy International utilizing its patented RepCat process. [BBD]
Argent Energy is significantly expanding its biodiesel plant in the Port of Amsterdam, the Netherlands, from 30 mgy to 162 mgy. The U.K.-based company plans for project completion by mid- to late 2023. [BBD]
The U.K. government has decided to keep tariffs on biodiesel imports from the U.S. and Canada through Jan. 30, 2026, but to remove duties on renewable diesel. The government’s reason was the U.K. has an established biodiesel industry to protect “but no domestic [renewable diesel] production,” even though Phillips 66 produces hydrotreated biofuel at its Humber refinery. [BBD]
JBS Biodiesel opened a new biodiesel plant in the city of Mafra in Santa Catarina, Brazil. At 98 mgy, JBS’s total biodiesel
Acquisitions and plant start-ups dominate recent biodiesel headlines.
A regulatory hurdle regarding NOx emissions and compliance with regulation 18.3 MARPOL Annex VI and the NOx Technical Code was cleared recently thanks to a new unified interpretation approved by the International Maritime Organization. Marine biofuel blends up to 30 percent will now be treated the same as regular oil-based fuels. It also allows use of B30 to B100 biofuels provided certain NOx conditions are met. The news is expected to facilitate much greater use of marine biofuel and comes as a relief to shipowners who want to use biofuels without having to undertake onboard NOx measurements, deemed a complex and onerous exercise. [BBD]
The Maritime and Port Authority of Singapore, a global bunkering hotspot, has established a provisional national quality standard for marine biofuel in concert with industry, academia, and relevant government organizations under the national standardization program overseen by Enterprise Singapore. There is no international quality standard for biofuel as marine fuel yet. According to MPA, approximately 21 million to 24 million gallons of biofuel have been supplied in Singapore to ocean-going vessels across more than 40 biofuel-bunkering operations. Interestingly, the U.S. exported more than 76 million gallons of biodiesel to Singapore
in the first nine months of 2022. Aside from a few shipments in late 2021 totaling nearly 7 million gallons, U.S. biodiesel exports to Singapore have been relatively nonexistent. [BBD]
RBF Renewable Biofuels recently supplied Central Boat-owned diesel-powered push boat MV Captain Raphael with 20 percent biodiesel (B20) for a trip to the New Orleans area from its plant in Port Neches, Texas, and back with two barges filled with soybean oil. RBF will use the soybean oil as biodiesel feedstock. [BBD]
Virgin Voyages is partnering with the Roundtable on Sustainable Biomaterials, Twelve, Argent Energy and GoodFuels for sustainable marine biofuel supply. Virgin plans for net-zero carbon emissions by 2050. [BBD]
Total Energies completed the first refueling of a COSCO Shipping Lines containership—COSCO Houston—with B20 biodiesel, marking the oil company’s first biofuel-bunkering operation for a containership in Singapore. This followed Total’s biofuel-bunkering trials in Singapore with a vehicle carrier operated by Mitsui O.S.K. Lines Ltd. and a bulk carrier chartered by NYK Line in 2022. [BBD]
DHL Global Forwarding and GoodShipping expanded their five-year partnership with the purchase of 16 million gallons of marine biofuel, enough for 10 container vessels to journey from Asia to Europe. [BBD]
Royal Caribbean Group said it became the first major cruiseline operator to sail a cruise ship from a U.S. port while using renewable diesel to meet part of the ship’s fuel needs when Navigator of the Seas set sail from the Port of Los Angeles to Mexico this fall. [BBD]
Important regulatory news, partnerships and several trials continue fostering growth in the sector.
Top: EPA is not keeping up with growth in the renewable diesel sector through its administration of RFS, even with its proposed RVOs through 2025. Left: According to EIA data, U.S. renewable diesel capacity is on a sharp rise while biodiesel capacity is falling. Some suggest unintended policy consequences from the federal RFS and California LCFS are causing cannibalization.
Right: Global SAF output must grow 1,000 times the most optimistic 2022 estimates in order to hit airline targets.
Biodiesel producer W2Fuel joined the newly formed Michigan Advanced Biofuels Coalition to help advocate for blending incentives and encourage in-state use of its clean-burning fuel.
By Karen PotratzLike a cat with nine lives, a biodiesel production plant in Adrian, Michigan, faced down multiple business and economic challenges over the years. Thanks to W2Fuel, it’s now a thriving operation that brings sustainable, renewable biodiesel fuel to Midwest customers.
“W2Fuel believes in alternatives to fossil fuels,” says Roy Strom, the company’s president and CEO. “Our mission in producing biodiesel is to achieve energy independence, clean air and environmental responsibility.”
W2Fuel has the capacity to produce 15 million gallons of biodiesel per year (mgy) in Adrian. Another W2Fuel plant in Crawfordsville, Iowa, has a 10 mgy capacity.
Previous owners built the Adrian facility in 2007, during an era Strom calls the “Wild West” of biodiesel production. At that time, the industry specifications and standards were not as stringent as they are today to ensure biodiesel quality and consistent performance.
“Back then, biodiesel got a bad reputation due to the lack of quality controls,” Strom says. “There were reports of biodiesel clogging fuel filters and causing trucks to shut down.” An economic downturn didn’t help. The Adrian plant operated for only a year before closing in 2008.
With improved economics and higher quality standards, the biodiesel industry rebounded in 2011, stimulating new investment. A private-equity investor with interest in alternative fuels saw opportunity in the Adrian plant.
The investor breathed new life into the facility, purchasing the distressed assets and retooling operations to meet industry standards. W2Fuel is now BQ-9000-certified for biodiesel-quality assurance.
“We replaced old equipment to prevent breakdowns and reduce downtime, installed better separation and filtration systems for product consistency and made process improvements for faster and more efficient production needed for us to remain competitive,” Strom says.
Strom joined W2Fuel as controller in 2014 and was promoted to CEO when the previous company leader left in 2016. He’s a self-described “finance guy” with no prior experience in the fuel industry or the chemical engineering required to produce biodiesel. “I flunked chemistry in college,” he admits wryly.
What Strom did bring was the ability to keep the business viable by applying manufacturing and quality-control processes that he learned from past experiences in the automotive industry.
And he understood problem solving and how to hire and manage the right team of technical experts to operate the plant.
Despite the owner’s investments and Strom’s business acumen, W2Fuel was forced to shut down for nine months in 2019, due to uncertain federal policies related to renewable fuels.
“We had no biodiesel tax credits for two years,” Strom says. “On top of that, a record number of small-refinery exemptions were handed out under the Renewable Fuel Standard. The combination killed biodiesel demand and we couldn’t run profitability with those disruptions. After Congress renewed the biodiesel tax credit, the market became more viable again.”
Today the W2Fuel plant in Adrian runs at 100 percent capacity, producing biodiesel primarily for customers just across the state line in Toledo, Ohio. The company’s Crawfordsville plant serves customers in Iowa, Illinois and Minnesota. “There is a lot of demand for biodiesel in Minnesota because there is a B20 mandate there in the summer,” Strom notes. “Many states offer incentives to use biodiesel, but Michigan currently has no incentives for fuel suppliers to blend biodiesel. So, even though we are producing biodiesel in Michigan, there is not much used here.”
Strom would like to change that dynamic, which is why W2Fuel joined the Michigan Advanced Biofuels Coalition (MiABC). The organization, established in 2022, aims to promote biodiesel use through education, networking and technical expertise.
Strom sees many benefits from using biodiesel in Michigan, including maintaining the state’s valuable tourism industry. “Our clean lakes and beautiful forests drive people to Michigan as tourists,” he says. “We need to protect the environment so people can continue to enjoy our natural beauty.”
Decarbonization is another benefit. “Biodiesel can reduce carbon emissions now, while we are waiting for electric vehicles to become viable alternatives to petroleum diesel,” Strom says. “There are lots of soybeans grown in Michigan. Let’s use a fuel product manufactured here versus using oil from other parts of the world.”
While weathering the ups and downs of biodiesel markets and policies, W2Fuel remains steadfast in its mission to provide sustainable, renewable biodiesel fuel.
“Biodiesel can be a volatile business but it’s a mission we believe in,” Strom says. “Although W2Fuel is in business to make money, the investment also pays off socially, globally and environmentally. Biodiesel is a fuel we should support.”
Author: Karen Potratz Marketing and Communications Advisor Michigan Advanced Biofuels Coalition contact@miadvancedbiofuels.comBiodiesel producers who are using plant-based feedstock, or those who are willing to switch, can get certified kosher and capture more value from their glycerin coproduct.
By Rabbi Mordechai StareshefskyAbout 350,000 tons of glycerin are produced in the United States each year. Kosher glycerin is harder to come by today than it was previously, in part because of decreased government subsidies and certain other economic factors. Along with using plant-based feedstock, certifying biodiesel refineries kosher under rabbinic supervision makes it possible to manufacture kosher glycerin and meet a growing demand.
One of the most exciting and innovative processes spawned by relatively recent technology advancements is that of biodiesel. Simply put, biodiesel is a replacement fuel for diesel engines. One fascinating and exciting use of biodiesel is in marine fuel. Many commercial shipping liners and other maritime companies have committed themselves to using marine biofuel, of which biodiesel fills a prominent role. While standard diesel fuel is made from petroleum, biodiesel, which is nontoxic and biodegradable, is made from what are known as biomass oils.
These biomass oils can be derived from plant oils, such as soybean, canola and corn oil, but this industry is so versatile that refineries can take waste products such as used cooking oil (UCO) and animal fats and turn them into biodiesel. Even algae is being investigated as a potential source of biodiesel feedstock.
Of particular relevance to the food world is the fact that a coproduct of biodiesel production is glycerin, an indispensable ingredient in a variety of foods, such as dried and canned vegetables or fruits, precooked vegetables, precooked pasta, rolled oats, breakfast cereals, rice or tapioca pudding, breading or batters, precooked rice products and baked goods. Glycerin helps to retain moisture, prevent sugar crystallization, and add bulk, smoothness, softness, sweetness and texture.
Many biodiesel refineries are now looking to attain kosher certification. This is for two reasons:
• Biodiesel is not cost-effective to manufacture without heavy government subsidies. Congress has proven to be parsimonious and inconsistent with these subsidies, and producers are scrambling to develop ways to add value to their products, such as making the glycerin kosher by using kosher feedstock, for example.
• Animal feedstock, which includes animal fats, is becoming increasingly expensive. While it is highly in demand because it meets various California environmental standards for renewable sources, it can’t be used to make a kosher product. In order to produce kosher glycerin, then, the biodiesel process must use strictly plant-based feedstock.
Biodiesel is produced by a process called transesterification, which converts fats and oils into biodiesel and glycerin, a coproduct commonly used in the manufacture of pharmaceuticals and cosmetics as well as many foods. The process of making biodiesel starts with feedstock being delivered to the facility by boat or by tanker truck and stored in terminals until it is treated. About 100 pounds of oil or fat are mixed with 10 pounds of methanol and a catalyst to form 100 pounds of biodiesel and 10 pounds of glycerin (or glycerol).
Orthodox Union Kosher rabbis not only thoroughly understand how to apply Jewish law to the products they supervise, but they also make it their business to learn exactly how these products are manufactured. This often includes mastering technical intricacies that require special advanced education and training. It also means the rabbis are skilled at pinpointing the best processes and adaptations to help a company take advantage of the value-added benefit of being able to market a product as kosher.
In addition, OU Kosher has, of course, vast experience in helping refineries transition from nonkosher to kosher. Although each refinery is unique, the basic plan takes two steps: the cleaning of the equipment and its kosherization. Although kosherization of tanks is typically done with boiling water, this is not feasible in a biodiesel refinery for two reasons:
• Many tanks are not jacketed, that is, they don’t have the ability to heat themselves, and the water therefore will not reach a boil.
• The amount of water necessary to effect kosherization will wreak havoc with the plant’s utilities—boiling and disposing of up to 5 million gallons of water is quite a challenge.
Accordingly, kosherization of refineries is done with steam. The plant will blow in live steam through the top of the tank, and the rabbi supervising the kosherization will measure the condensate exiting below. Once the condensate displays consistent readings of 200 degrees Fahrenheit and above, the tank has been effectively kosherized.
Author: Rabbi Mordechai Stareshefsky Rabbinic Coordinator, Orthodox Union 212-613-8375 stareshefskym@ou.org
When considering process centrifugal pump options for production of renewable biofuels such as sustainable aviation fuel (SAF), renewable diesel, green crude, biodiesel, ethanol and bio-finished chemicals, plant owners and operators are increasingly specifying sealless centrifugal pumps to transfer, circulate and boost process refining and feedstock production liquids. Sealless centrifugal pumps offer a unique combination of operating-risk mitigation and process-safety management (PSM) benefits to users.
Because sealless centrifugal pumps, by design, simply cannot leak or generate emissions into the environment, use of this technology provides baseline process-equipment selection and operation that immediately meets manufacturing-company goals and standards for ongoing sustainability, corporate social responsibility (CSR) and combating climate change.
With global goals for production of clean, renewable fuels by 2030 and beyond far exceeding industry production capacity, sealless centrifugal process pumps will play an instrumental role in every new production and feedstock technology to be employed by providing emission-free operation.
Of the two types of sealless process centrifugal pumps, canned-motor and magnetically coupled canned-motor pumps offer the ultimate in best-practice sustainability, environmental performance, long-term reliability, containment control and regulatory compliance. Standard production includes secondary containment and control, which assures that no process liquid can escape into the environment—even in the event of a catastrophic mechanical or electrical failure. These currently manufactured and available pumps offer the industry a wide range of hydraulic and double-containment solutions that enable users to minimize risk and enhance plant safety. At the same time, they provide a lower long-term cost of operation through increased reliability. Products are available up to 600 kilowatts (805 horsepower) with capacities to 2,400 cubic meters per hour (10,000 gallons per minute), heads to 1,000 meters (3,300 feet) and containment pressures up to 35 megapascals (5,000 pounds per square inch). These limits far exceed current industry requirements.
A variety of features and enhancements are available that provide the opportunity to monitor critical operating parameters required for the handing of volatile, toxic and environmentally sensitive liquids and minimize maintenance exposure. These include:
• Rotating element position and bearing-wear monitors with control outputs
• Variable frequency drive (VFD) capability for enhanced process control
• Secondary containment leak monitors
• Elimination of alignment
• Underwriters certification for hazardous-area classifications
• Versatile and space-saving mounting arrangements with small footprints
• Full compliance to industry design standards such as API, ISO and ASME/ANSI
• High-temperature motor-insulation systems that eliminate cooling-water needs
• API 685 Annex D and ASME/ANSI B73.3 circulation systems to meet all fluid characteristics
For biorefiners and clean, renewable fuel producers, canned-motor pump designs that meet the rigorous standards of API 685 are available to assure safe, reliable and documented operation in critical services. API enhancements to standard designs are offered to the level required by users or governed by plant-operating standards. All API solutions are available with manufacturer field support and considerable expertise in canned-motor pump operation. With 60-plus years of design and successful field experience, canned-motor pump manufacturers can assist plant-operating personnel and process-design engineers in applying canned-motor pump technology for increased plant safety, operating reliability and return on investment.
The global Teikoku Group is the world’s largest manufacturer of sealless, emission-free, canned motor process centrifugal pumps. With manufacturing and design capability in the U.S., China and Japan, and subsidiary offices and service centers located in major markets worldwide, Teikoku is positioned to exceed user expectations in both production and support of its pumping technology.
Author: Chaitanya “Chatty” Sakhalkar National Sales Manager, Teikoku USA Inc. 281-846-2857
csakhalkar@teikokupumps.com
Sealless process centrifugal pumps featuring canned-motor technology will play a pivotal role in building out the biobased diesel sector and beyond.
The U.S. government’s aggressive SAF goals will present challenges to tracking and verifying feedstock sustainability, demanding new solutions to ensure compliance.
By Kristof ReiterThe U.S. government has set major goals to ramp up production of sustainable aviation fuel (SAF). According to the plan, by 2050, 100 percent of jet fuel should be sustainable.
In 2021, the federal government announced the Sustainable Aviation Fuel Grand Challenge, a project through which it hopes to produce 3 billion gallons of SAF per year by 2030. To put this in perspective, the entire lipid-based biofuel production complex produced roughly 3 billion gallons in 2022, meaning that the SAF ramp up would double demand for low carbonintensity (CI) lipids over the next decade. To achieve such an ambitious goal, it outlines investments in innovative solutions, but it also suggests beefing up infrastructure and creating policies to make better use of existing sustainable feedstocks.
In short, between continued growth of on-road renewable diesel and emerging SAF markets, demand for low-CI feedstocks is projected to continue growing rapidly. As the market grows, so will the challenges of ensuring untraceable and unsustainable feedstocks do not work their way into the U.S. biofuel market, robbing consumers and taxpayers of the intended benefits.
Aircraft have unique fuel energy-density needs, which render electricity and hydrogen unviable options to replace fossil fuels in aviation today. As an alternate path to reducing petroleum dependence, SAF can be created from renewable biomass and waste sources.
To reach 3 billion gallons of SAF per year by 2030, SAF production must grow 122 percent each year between now and then. Starting in 2023, one of the first steps outlined by the SAF Grand Challenge Roadmap is to maximize the supply of SAF derived primarily from fats, oils and greases (FOG).
For years, the federal and state governments have been working to incentivize the production and use of biofuels. The federal government offers tax credits based on the volume of biofuel that a producer blends with petroleum. Other incentives include the U.S. EPA’s renewable identification number (RIN) credits and California’s Low Carbon Fuel Standard credits.
To qualify for tax credits and other petroleum-reduction incentives, it’s likely companies will need to produce detailed records to prove the fuel they produce and feedstocks they’re using really are produced along the pathway they claim. Since the collector who sells their oil to a buyer does not determine the final destination of the fuel they sell, it’s in their best interest to comply with all recordkeeping regulations—even those of other states and, sometimes, countries. Failing to do so limits sellers’ ability to access top-product bids. Compliance
pays, and at Reiter Software we are building—and constantly adapting—the tools to make it easy.
In the past, industry leaders had understood EPA regulations as requiring companies to share the approximate areas from which they collected oil, rather than exact business addresses. More recently, however, regulators clarified that they are looking for these granular details.
Clean Fuels Alliance America is fighting EPA in court because, under current language, the biofuel producer is responsible for verifying the supply chain, while used cooking oil (UCO) collectors say this is tantamount to giving confidential business data to a competitor (many biofuel producers also have an arm that collects UCO) and are thus resistant to handing over these records.
To address the “need for traceability” dilemma, California Air Resources Board allows records to be provided to thirdparty auditors rather than counterparties themselves.
In some regards, EPA has allowed biofuel producers to use intermediaries such as third-party auditors to absolve themselves of RIN fraud culpability—a notable example being RIN Quality Assurance Plans.
A QAP-like program for UCO using a combination of Reiter Software data analytics and on-the-ground data validation could provide the defense against fraud the industry is looking for.
Another solution discussed within industry and regulatory circles is the creation of a central-records database protected from private interests but available to law enforcement for fraud detection. Enforcement actions and removal from the supply chain could be collaborative between government and industry.
Reiter Software is dedicated to being part of the solution regardless of how EPA decides to handle this issue and is determined to protect the needs of both UCO collectors and their biofuel-producer counterparties.
Reiter Software’s first-generation Cooking Oil Service Tier software platform has been successful in helping collectors build more efficient routes, easily train and deploy drivers, and maintain the detailed compliance records necessary to comply with data audits since 2018. Throughout this time, we received consistent, ongoing feature-development feedback from 10 growing collectors of various sizes. With their insights and experience, Reiter Software is launching Route Simplified, the next generation in UCO productivity and value-creation software. We recommend getting on the schedule to onboard now, as there is limited availability.
Author: Kristof Reiter CEO, Reiter Companies 888-428-5617 kristof@reiterscientific.com
A: Sepigel® has been a reference bleaching-earths brand in the oils- and fatsrefining industry for the past 35 years. We strive to continue developing technological solutions to purify and refine oils and fats across five continents, working hand in hand with large groups and world-leading refineries.
Our extensive know-how and cutting-edge technology enable us to offer a whole range of solutions based on specialty minerals, from naturally active clays to highly activated clays.
Besides conventional bleaching earths, in Sepigel®’s portfolio we have solutions developed to meet the specific requirements and properties of renewable diesel, sometimes referred to as hydrotreated vegetable oil (HVO), and biodiesel production.
Q: What relevant products are in the Sepigel® portfolio?
A: Sepigel®’s portfolio encompasses a complete set of products for the wide spectrum of feedstocks and biofuels used in the market: Sepigel® Extra, a selection of chemically activated clays specially designed for the treatment and purification of the wide variety of feedstocks used in renewable diesel production; and Sepigel® Natural and Active, a range of specialty-clay solutions for treatment and purification of vegetable oils and animal fats used for conventional biodiesel production and polishing.
At Sepigel®, we are very proud to work with the largest HVO and biodiesel producers, coprocessing refineries, and oil- and fatprocessing plants. We are committed to the success of our customers. We continue helping them look for technological solutions to reach the desired results with assistance from our Sepigel® adsorbents. Since the first HVO developments in the market a decade ago, at Sepigel® we were convinced that, given our experience in oils and fats purification, we can continue helping our customers with at least one of their main challenges—achieving flexibility and efficiency in pretreatment of new feedstocks with very different qualities.
Q: How are Sepigel®’s filtering agents different than others on the market?
A: A careful mineral selection, our cuttingedge technology and our passionate, highly skilled R&D team enable us to develop a portfolio that combines an effective removal of impurities and metals with high filterability and therefore high throughput.
Depending on what our client’s production characteristics and challenges are, the expertise of our technical department allows us to recommend the right solution to aid solving their pretreatment problems.
Q: What biofuel-market trends or developments has Sepigel® noticed in recent years?
A: We have detected three major trends. 1) The need to have at least two high-performing adsorbent suppliers to secure supply and hence business continuity. Due to growing adsorbent demand from renewable fuels, the guarantee of a regular and constant supply becomes crucial, and we must be prepared to face it. 2) A growing concern about the quality and availability of feedstocks. Even if there are important projects developing new feedstock sources, we acknowledge how hard it is for HVO producers to secure them, and it’s hard to think there will be enough for all the biofuels projects announced. 3) To close the circular-economy concept of renewable fuels, the industry is pursuing innovative ways to reduce and recycle all waste. This includes spent adsorbents. Sepigel® is actively investigating and collaborating with refineries and international research institutions to find innovative solutions to this challenge.
Q: How has the market for filtration agents changed over the years?
A: We have seen a tremendous growth in demand and efficiency in the biofuels industry over the past decade. In turn, this has put pressure on the availability of adsorbents for the traditional oils and fats industry, from mining to manufacturing the finished product. The supply chain now faces additional stress exacerbated by the pandemic. There has been global capacity expansion by filtrationagents players to meet such growth, and Sepigel® has certainly contributed to this expansion at our European and American production sites.
Q: How has Sepigel® adapted to change with the market and provide customers with what they need?
A: First, in addition to our existing
Sepigel® plants in Europe, we expanded our minerals sourcing, R&D and production capacity by investing in state-of-the-art facilities in America. The strategic location in Querétaro, Mexico, allows Sepigel® to have an important platform in the Americas, guaranteeing an agile and efficient service and constant supply to our customers in America and abroad. The new R&D center in Mexico is part of the brand’s commitment to innovation and constant development of new technological solutions adapted to the needs of every customer and any type of oil and fat. Second, to be close to our clients, we built an international network of logistics hubs, keeping constant security stocks for our clients, optimizing our supply-chain strategy and drastically reducing lead times.
Q: How does Sepigel® plan to capitalize on HVO growth in North America, Europe and, to a lesser extent, South America and Asia?
A: Over the past few years, we put our efforts into developing better-performing adsorbents and increasing our production and logistics capacity worldwide to be able to face this huge demand growth. As previously mentioned, we’ve worked hard in securing our clients’ supplies by building an important logistics-hub network, considering conventional and unconventional delivery formats, depending on our client’s needs, whether bulk bags, trucks or railcars.
All these actions allow us to be fully prepared to deliver our biofuels clients the right product in the right place at the right time.
Q: What might Sepigel® be researching or developing to satisfy future market demands in this industry?
A: We work continuously to innovate and develop new solutions adapted to new challenges posed by the new feedstocks used. We strive to continue developing adsorbent solutions effective on a wide variety of feedstocks, which combine effective removal of impurities, metals and soaps with very good filterability. Increasing production efficiency and throughput of biorefineries is our main goal.
Q: Any last words?
A: At Sepigel®, tradition is good, and innovation is better. We are totally ready to accompany our clients on their path toward the transition from fossil fuels to renewables.
For more information, email javier.aznar@puremin.com.
Q: For those who may not know, what is Sepigel®?
A Q&A with Javier Aznar, the business development manager at Minersa Group, about Sepigel®-branded
The U.S. market for biodiesel and renewable diesel reached 3.1 billion gallons in 2021, generating $23.2 billion in economic activity and supporting 75,200 jobs, according to a new report released by Clean Fuels Alliance America. The study, “Economic Impact of Biodiesel on the U.S. Economy 2022,” was conducted for Clean Fuels by LMC International, and it evaluates direct, indirect and induced economic impacts and jobs across the entire value chain, from raw-material production, collection and processing to fuel production and distribution. The 75,200 jobs paid $3.6 billion in annual wages in the United States.
The study finds that biodiesel and renewable diesel production generate the largest economic and employment benefits in the sectors of farming, oilseed processing and fuel production. The farm sector benefits from 30 percent of the overall economic activity, or $7.41 billion. It also supports 28,236 U.S. jobs earning $1.36 billion in wages. The oilseed-processing industry benefits from more than 21 percent of the economic activity, or $4.97 billion. The biodiesel and renewable diesel market supports 6,024 U.S. jobs earning $380 million in wages in the sector. It also supports 14,661 jobs earning $560 million in wages in the waste-grease recycling and animal-fat rendering sectors.
Clean-fuel production supports $9.57 billion in economic activity—equal to 41 percent of the overall economic impact— and 17,120 U.S. jobs, earning $880 million in wages. For every 100-million-gallon increase in domestic clean-fuel production, the direct, indirect and induced economic activity increases by $1.09 billion and U.S. jobs grow by 3,185.
The data also demonstrates a substantial increase in overall economic activity associated with market growth for biodiesel, renewable diesel and sustainable aviation fuel (SAF) compared to a prior study in August 2019. That study calculated an overall economic impact of $17 billion and 65,600 jobs based on a U.S. market of 2.5 billion gallons. The 2019 study demonstrated an increase in economic activity of $780 million for every additional 100 million gallons in the market.
The biodiesel and renewable diesel industry is already growing steadily to meet demand for heavy-duty transportation and work vehicles as well as new markets like rail, marine and aviation fuels. According to data from U.S. EPA’s Renewable Fuel Standard program, the U.S. market for biodiesel and renewable diesel grew by 200 million gallons in both 2020 and 2021. That growth occurred during the pandemic, as other U.S. fuel manufacturers cut production. For the first half of 2022, the U.S. market for biodiesel and renewable diesel was already 400 million gallons larger than during the same period in 2021, according to EPA data.
Clean Fuels Alliance America envisions the industry doubling
in size by 2030, with domestic production reaching 6 billion gallons annually. That growth can generate additional jobs and increasing economic opportunities for growers, fuel producers and other economic sectors.
The study calculates that producing 6 billion gallons of clean fuels in the United States would increase overall economic activity from the current $23.2 billion to $61.6 billion and support 187,003 jobs earning $8.8 billion in wages. The construction of additional capacity would increase economic activity by an added $4.3 billion and support an additional 144,500 related temporary jobs earning $5.8 billion in wages.
The envisioned growth is aggressive but achievable, based on existing investments in oilseed processing, fuel production and infrastructure.
The crushing industry has existing operable capacity to process nearly 2.2 billion bushels of soybeans annually, according to the American Soybean Association. Overall, the industry is investing more than $4 billion in additional oilseed-processing capacity. The existing facilities are scheduled to expand capacity by an additional 255 million bushels. An additional 494 million bushels of new capacity is planned over the next several years. Combined, the expansions and new capacity could support growth of an additional billion gallons of biodiesel and renewable diesel.
Infrastructure to provide clean fuels to consumers is also attracting new investment. The USDA’s Higher Blends Infrastructure Incentive Program provided more than $25 million in matching grants to infrastructure projects for storage and dispensing that will support 1 billion gallons of biodiesel, making it more accessible to consumers. USDA is taking proposals on another round of grants for next year. And the agency is planning a follow-on grant program—the Biofuel Infrastructure and Agricultural Market Expansion Program— with funding authorized by Congress through 2030.
The industry’s vision for rapid growth through this decade is within reach. It has the potential to bring economic opportunities to many states and rural communities across the country, where the industry has strong roots.
Author: Paul Winters
Director of Public Affairs and Federal Communications
Clean Fuels Alliance America 202-737-8803 pwinters@cleanfuels.org
A new report details the important economic impacts biodiesel and renewable diesel have on the U.S. economy, particularly for farming, oilseed processing and fuel production.
As of 2021, the Clean Fuels Industry:
• Contributes a total U.S. economic impact (direct, indirect, induced) of $23.2 billion
• Supports 75,200 U.S. jobs throughout the economy/country
• Pays $3.6 billion in wages
Supported by United Soybean Board, soybean farmers and their checkoff.
CLEANFUELS.ORGWhen Calumet Specialty Products Partners announced in early 2021 it was exploring renewable diesel manufacturing at the company’s Great Falls, Montana, refinery, the relatively obscure oil refiner joined a crowded field stacked with bigname petroleum companies with even bigger projects. While Calumet executives were confident in their plan, some people were skeptical whether the project would ever get off its feet, let alone reach commissioning a year and a half later.
“The cognitive dissidence, maybe, was that we had a bunch of conventional thinking from the analyst community,” says Bruce Fleming, executive vice president of Montana Renewables. He says coverage of Calumet’s plans, mostly from Wall Street types using conventional wisdom, came perhaps from a misunderstanding by analysts about this new market in which refinery assets are being repurposed. “We didn’t agree with it,” Fleming says. “We felt like a contrarian.”
Despite cynics’ early doubts, Calumet’s Montana Renewables has begun manufacturing renewable diesel and sustainable aviation fuel (SAF) in Great Falls— and it soon plans to be the largest SAF producer in North America.
What most of these critics didn’t know is that Calumet spent nearly two years studying the move prior to announcing its plans. One of the biggest questions facing Calumet was of feedstock—what will it use and where will the company get it?
“Energy commodities do not provide a springboard to become ag-commodities observers,” Fleming tells Biobased Diesel™. “People say, ‘There’s not enough feedstocks to go around.’ There are enormous quantities traded globally every day. A few refineries converting to produce renewable diesel are just a blip on the radar. The market is elastic. More acres can be planted, technologies can be deployed, farmers can obtain cash for cover crops. Camelina is going to be a poster child in our latitude, something farmers want to do— that’s a whole new factor. Conventional analysts missed all the responses. When there’s a shortage, prices rise and unexpected responses show up, and prices go back down.”
Ag commodities “think” and “behave” differently, Fleming says. “We did not claim to know anything about it,” he admits. “So, we went out and got people who did understand it.”
Calumet hired VEOS and StoneX Group. “They’ve been doing this for a really long time,” Fleming says. “We subsequently added a really qualified tallow trader too.”
Despite the critics, Calumet continued referencing in its earnings calls quarter after quarter the location advantage its refinery in Great Falls, Montana, had over other market players—for both feedstock and final product distribution. “We have 10 times more feedstock than we need flowing past us,” he says. “It’s an accident of geography.” Canola from Canada and the upper Midwestern and Western U.S. “ships right past us to get anywhere,” Fleming says, adding that hydrotreated canola oil wasn’t approved by U.S. EPA under the Renewable Fuel Standard when Calumet began this journey—but it is now.
For the refinery conversion itself, Fleming says Calumet had additional advantages over its competitors. Most of the refineries converting to renewable diesel were not performing well in the petroleum market and had either shut down or soon would, he points out. “We were not on that road,” Fleming says. “But through an accident of history, our hydrocracker was much larger than we were able to take advantage of.”
Before Calumet ever considered renewable diesel production, its oversized hydrocracker was retrofitted with 317L stainless steel, which the company says is needed to process highly acidic renewable feedstock.
Plans for the catalyst changeout were originally set for spring 2022 during a scheduled refinery turnaround. These turnarounds typically happen in the spring or fall, never winter or summer. A third of what Calumet produces in Great Falls is high-quality asphalt, a high-demand product that ships all over the U.S. After talking with the board of directors, the turnaround and catalyst changeout was put off until fall, to take advantage of one more summer of asphalt sales.
Even with the planned delay, the project came to fruition quickly. “The metric we’re judged by is speed,” Fleming says. “When we told people how fast we’d do it, they said, ‘No you won’t.’” He adds no one bothered to ask what’s been done
already—like the 317L stainless steel—to expedite the process. “It wasn’t our job to convince doubters,” Fleming says. When large, expensive projects are undertaken, they are typically done as carefully and efficiently as possible. “That’s one reason why large projects in the hands of conventional EPC activity take a long time,” Fleming says. “We wanted to speed to the prize, be fast and sacrifice certainty on spending for certainty on time. With investors it’s dates, not dollars. In commodities, if you overinvest, you can have trouble recovering. We felt good about where we stacked up.”
Calumet found no shortage of investments in the project, which became known as Montana Renewables, a wholly owned subsidy of Calumet. Oaktree, Stonebriar and Warburg Pincus saw the vision and were convinced of the possibilities.
As the company was starting production, it announced two transactions that together fund the plant’s workingcapital needs, including a supply and offtake agreement with Macquarie Commodities and Global Markets, which provide inventory monetization for feedstocks and products, as well as intermediation services connected with feedstock purchases, the company stated. Simultaneously, a $90 million assetbacked loan revolving-credit facility was executed with Wells Fargo Bank, secured by accounts receivables and open blenders tax credit refunds.
The company also surrounded itself with qualified technology, equipment, and service companies. Burns & McDonnell was chosen as EPC contractor. Matrix Service was awarded the contract to build seven new storage tanks. Topsoe provided its well-known HydroFlex™ process technology. Technip Energies was retained to build a new green-hydrogen plant. And Applied Research Associates is providing the pretreatment unit.
Montana Renewables began processing renewable diesel this fall. “After a year of investing in the conversion of our facility, today (Nov. 30) we are sending out our first railcars of renewable diesel fuel,” said Ron Colwell, general manager.
In November, the company had $50 million in feedstock inventory on site. “Our feedstock strategy is to gather locally, and we have soy, canola, distillers corn oil and tallow inventoried,” Fleming says. He notes that while Montana produces these crops, the state does not crush the seeds nor render or recycle animal byproducts. “Our long-term vision is that agribusiness will connect the farm, ranch and us, by building crusher or meat packing in Montana,” he adds. “Camelina is not commercially available in large quantities, but it will be.” Montana Renewables has reserved land on its site in Great Falls to accommodate a crush plant, if a deal can be struck with the right co-op or company.
Also in November, the board of commissioners for Cascade County, where Great Falls is the county seat, approved a proposal to issue its solid waste disposal and sewage facility revenue bonds, up to $275 million, to Montana Renewables.
The company has been successful in raising equity but raising debt has been more challenging. According to Fleming, it had been running a conventional debt process in early 2022, but once Russia invaded Ukraine, the markets became uneasy. “So that didn’t get done,” he says. The municipal bonds approved for issuance by Cascade County are essentially a loan—the debt financing Montana Renewables had been seeking. While the approval by the county board of commissioners is a positive development, it isn’t the actual issuing of the bonds, but rather a step toward their issuance. Fleming anticipates the bonds to be issued this spring.
The new hydrogen plant, the flowsheet for which Montana Renewables has filed for patent protection, will use ample offgas supplies from renewable diesel processing to completely provide enough hydrogen for its needs and is targeted for completion in December. The pretreatment system is expected to come online after that, sometime late this winter.
Refinery assets have been completely separated into a 12,000-barrel-per-day (bpd) crude-oil refinery and 12,000 bpd of renewables. For renewables, this breaks down to approximately 135 million gallons per year (mgy) of renewable diesel capacity, 30 mgy of sustainable aviation fuel (SAF) capacity and 15 mgy of renewable naphtha capacity.
Selling its renewable products won’t be a problem either. “We have three blue-chip customers,” Fleming says. “Phillips 66, Chevron, and the third is bigger than them. All three have
contracted for as much renewable diesel as we can get them.”
The company has secured an SAF agreement with a bluechip offtaker for 30 mgy and is pivoting its production plans to manufacture greater volumes of SAF. By the first quarter of 2023, Montana Renewables will be the largest SAF producer in North America, according to the company. SAF production for 2023-’24 is expected to expand to 60 mgy, with the potential to produce a maximum of up to 230 mgy of SAF by 2024.
In the end, Montana Renewables defied the odds—or at least the opinions of the odds-makers and analysts—and pulled all the disparate elements together to successfully bring its biobased diesel project to fruition in Great Falls. The work is far from over but producing 230 mgy of SAF by 2024 would double even the most optimistic global SAF output estimates for 2022, according to recent data from the International Air Transport Association. And despite the boardapproved six-month delay in commissioning, Calumet and Montana Renewables still succeeded in its goal, which, as Fleming describes it, was “speed to market, speed to prize.”
Author: Ron Kotrba
Editor, Biobased Diesel™ 218-745-8347 editor@biobased-diesel.com
Buy-Side Advisor
Acquisition of Elkhorn Valley Ethanol Plant from Louis Dreyfus
Buy-Side Advisor
Global Renewable Energy Company
Acquisition of Midwest Ethanol Facility
Financial Advisor Strategic Investment by ExxonMobil
Sell-Side Advisor
Sale of High Quality Alcohol Distillery to CC Industries
Sell-Side Advisor
Sale of Ord, NE and Hereford, TX Ethanol Plants
Lenders’ Financial Advisor
Restructuring of $105M Secured Debt for Alto Ingredients
Sell-Side Advisor
Sell-Side Advisor
Sale to VERBIO Diesel Canada
Sale of Cellulosic Ethanol Facility to VERBIO North America
For a complete list of transactions and to learn more, find us at www.oceanpk.com
In the most relevant market newsletters, feedstock like used cooking oil (UCO) or animal fats are specified by the free fatty acid (FFA) content, moisture, insoluble impurities and unsaponifiable matter (MIU), and sometimes sulfur. But is this information sufficient?
FFA content varies depending on the kind of feedstock. Refined vegetable oil usually has an FFA content of 0.1 mass percent (mass%) but can be as high as 0.5 mass%. In “good” UCO, the FFA content is at most 5 mass%, but there are qualities on the market where the FFA content is up to 15 mass%. In animal fats, FFA can range from 1 mass% up to 30 mass%. Even higher FFA content can be found in waste material like acid oils, which are generated, for example, in the soapstocksplitting process. The soapstock is obtained as a byproduct of the chemical neutralization of oils and fats. This soapstock can be split into fatty acids and water through acidification with a strong acid, such as the sulfuric variety. Other examples of high-FFA feedstock are brown grease, black grease and palm oil mill effluent (POME). These waste oils have an FFA content higher than 30 mass% and up to 90 mass%.
All of the feedstocks described above can be used for biofuels production, but depending on the technology installed, feedstock with the right FFA content must be chosen. The rule of thumb for using waste oils, however, is the higher the FFA content, the worse the rest of the feedstock quality parameters will be.
For example, UCO is a complex mixture of different substances formed during the deep-frying process. Water, introduced by the food during frying, leads to hydrolysis of the triglycerides to form mono- and diglycerides, as well as FFA as products of decomposition. As a weak nucleophile, water attacks the ester linkage of triacylglycerols. In addition, oxidation processes—preferably taking place at double bonds of the fatty-acid chains—lead to the formation of peroxides (primary oxidation products) by singlet oxygen oxidation in the first step. These peroxides will further react with fatty material to form all kinds of secondary oxidation products.
The complexity of oil degradation is increased furthermore by the fact that different types of oils behave differently regarding the rate of formation of polar components. In one study, a total of 220 compounds were identified as volatile composition products that formed during deep-fat frying, where a significant portion remains in the frying oil. These products show strong polar characteristics and can act as a surfactant, building a stable bond for free glycerol in biodiesel, which cannot be washed out during biodiesel purification. Thus, problems with too high a content of free glycerol and water can occur during UCO processing. Nevertheless, the UCO can be still used for biodiesel production, but there has to be the right pretreatment technology in place to ensure a stable operation.
Remember to follow the rule of thumb: The higher the FFA content, the worse the rest of the feedstock quality parameters will be. So, it becomes necessary to look in greater detail at which other parameters are crucial to know in order to select the right feedstock.
The complexity of oil degradation is increased furthermore by the fact that different types of oils behave differently regarding the rate of formation of polar components.
With more than 25 years exploring waste oils and fats, BDI personnel have established a great deal of knowledge in feedstock quality.
PHOTO: BDI-BIOENERGY INTERNATIONALThe next parameter specified in market newsletters is MIU. The acronym stands for three of the principal qualitycontrol tests used to determine common contaminants in waste oils: moisture and volatiles, insoluble impurities, and unsaponifiable matter. For “good” UCO, the typical maximum value is 3 mass%. The more interesting part, however, is the ratio between these three components. Whether the water portion is 0.2 mass% or 2 mass%, for example, can determine if the raw material is suitable as feedstock for biodiesel or renewable diesel production. Therefore, this parameter also must be scrutinized more closely.
In general, higher water content is preferable as this means the amount of impurities and unsaponifiable matter is low. These are much more difficult to treat and have a greater influence on the production process. The water content can be reduced or handled by installing a drying unit, which typically can be designed for water content up to 5 mass%. But nevertheless, using a feedstock with higher water content will block the esterification and transesterification reactions and leads to greater consumption of chemicals and the creation of soaps, which ultimately leads to a lower yield. The other two parameters, however, are of more interest.
Some examples of insoluble impurities are solid-food residues in UCO and bone-meal residues in animal fats. When using feedstock with a high insoluble-impurities content to manufacture biofuels, there will be a significant risk of blockage in heat exchangers, pipes and other important equipment, which will lead to undesirable production interruptions. Therefore, these impurities must be pretreated up front before biofuel processing. This can be realized by means of filtration or centrifugation.
Unsaponifiable substances are compounds that cannot be converted into soaps by means of aqueous sodium-hydroxide solution and cannot be converted to biodiesel. Examples of these are sterols (e.g., cholesterol), fatty alcohols and mineral oils. For
biodiesel producers, a high unsaponifiable content in feedstock will unavoidably lead to yield losses, production decreases, lower ester content in the final product and poor-quality glycerin—the byproduct of biodiesel production. So, in this small acronym there is a lot to know in order to make the right raw-material choice.
The next parameter to investigate is sulfur. In vegetable oil, sulfur is organically bound and therefore is also a component of UCO. For UCO, this parameter is not that critical unless the vegetable oil’s origin is from old rapeseed varieties, which have a high content of glucosinolates and means rapeseed rich in erucic acid. There are qualities on the market up to 30 parts per million (ppm) sulfur.
For animal fats, the rule of thumb is, the higher the sulfur content, the worse the rest of the feedstock quality parameters will be. Sulfur is an indicator for the degree of decomposition and can reach values up to or greater than 200 ppm. By using high sulfur-contaminated feedstock for biodiesel production, fat pretreatment is a necessary first step to reduce the watersoluble sulfur components. Other sulfur components can be reduced by means of biodiesel distillation to achieve the strict parameters of ASTM D6751 and EN14214.
Furthermore, sulfur poisons catalysts, which means highsulfur feedstock is detrimental to the renewable diesel industry. And phosphorus is even worse than sulfur. Catalyst poisons are bound by the catalyst instead of the substance whose reaction it is supposed to accelerate. Thus, they block the adsorption capacity of the large surface area of the catalyst particles.
Coming back to the first question, “Is this information sufficient?”, here the answer is a clear “no.” There are many more parameters to know in order to avoid off-spec product on one hand and yield loss, production issues, and high costs for chemicals or catalysts on the other.
One of these parameters, for example, is polyethylene-type plastics. Polyethylene in UCO is mainly in a solid state and exists in big particles, which means it is part of the insoluble impurities and can be reduced by filtration or centrifugation. In animal fats, the polyethylene is finely shredded or in molten form and, therefore, due to its similar density to the oil, elimination cannot be easily done by a simple filtration or centrifugation. If feedstock with a high polyethylene content is used in biofuel production, the producer can expect fouling issues in relevant process equipment, which ends up as decreased output capacity due to greater cleaning effort.
Being in the business of exploring waste oils and fats for more than 25 years, a high degree of know-how has been established and, thus, a number of additional parameters like alkalinity, phosphorous, polymerized triglycerides and many more have been detected. To ensure that the right feedstock is used with the appropriate technology, these parameters must be identified, established and understood. New frontend pretreatment technologies can be employed to render the feedstock suitable for the limits of a given biofuel production process, while backend quality-improvement units can help the final product meet the relevant industry specification. Contact us to learn more about feedstock parameters and their influence on different biofuel processes.
Christine Riedl Technical Sales Manager, BDI-BioEnergy International +43 316 4009100 christine.riedl@bdi-bioenergy.com
For animal fats, the rule of thumb is, the higher the sulfur content, the worse the rest of the feedstock quality parameters will be.
Hydrotreated vegetable oil can reduce the use of fossil fuels and recycle waste streams, but its production requires efficient, flexible, safe, reliable and sustainable pretreatment of feedstocks.
By Veronique Gibon, Wim De Greyt, Jan De Kock and Marc KellensTo address global-warming challenges, it is essential to reduce fossil-fuel use, which is the objective of the European Commission’s “Fit for 55” and Renewable Energy Directive (RED) II policies. The EU aims to reduce net greenhouse-gas (GHG) emissions by at least 55 percent by 2030 compared to 1990 levels, and to define a common framework for the promotion of renewable energies. Hydrotreated vegetable oil (HVO), or hydroprocessed esters and fatty acids (HEFA), is a renewable diesel that can reduce use of fossil fuels and recycle waste streams. European demand for drop-in biofuels— HVO and sustainable aviation fuel (SAF)— will significantly increase in coming years, supported by higher blending targets
and the introduction of new mandates for the aviation sector. It is projected that the HVO/HEFA share in European oilbased biofuel demand will increase to 35 percent by 2030.
Conventional (first-generation) biodiesel consists of long-chain fatty acid methyl esters (FAME) typically made by transesterification of vegetable oils or animal fats. Biodiesel has to meet international quality standards such as ASTM D6751 or EN14214 and is approved for blending with petroleum diesel.
Renewable diesel is a biomass-derived fuel suitable for use in diesel engines and meets the ASTM D975 diesel-fuel
standard or EN15940 for synthetic diesel. It consists of hydrocarbons and is mostly produced through a hydrotreating process but may also be obtained via gasification, pyrolysis or other technologies. The term HVO is used for renewable diesel manufactured in a hydrotreating process (hydrogenation and hydrocracking) from different feedstocks, such as vegetable oils, waste cooking oils, animal fats, acid oils and fatty acid distillates.
HVO, also called green diesel, has properties similar to fossil diesel but with some differences such as a lower density and higher energy content. It typically has a low sulfur content, is free from oxygen and aromatic hydrocarbons, and has a high cetane number.
HVO offers benefits over FAME, such as reduced nitrogen oxide (NOx) and particulate emissions, better storage stability and better cold-flow properties. It can be used in existing diesel engines without blending limitations.
SAF is the commonly used term for nonpetroleum synthesized jet fuel components produced in accordance with ASTM D7566 specifications. It is derived from renewable resources that enable a reduction in net lifecycle carbon-dioxide emissions compared to conventional jet fuels. SAF can be produced from waste and plant-based raw materials using essentially the same technology as HVO production. When SAF is blended with conventional jet fuel, it meets ASTM D1655 specifications. All major European and U.S. airlines have recently announced they will start using increasing volumes of SAF voluntarily in anticipation of a future compulsory SAF proportion.
The EU’s RED II promotes the use of biofuels, favoring next-generation biofuels that are obtained from nonfood waste feedstocks. Today, the only commercial alternative to FAME that can be obtained from waste feedstocks is HVO, while we await larger quantities of biofuels from lignocellulosic and algal biomass.
HVO production uses hydrogen instead of methanol, like conventional biodiesel processes, and biopropane is the major byproduct. There is no low-
value glycerol production like with biodiesel. HVO can also be blended with fossil fuel in higher ratios than 7 percent used nowadays for biodiesel in Europe.
The same feedstocks can be used for HVO and biodiesel production, but the technology and final products, as well as producers’ core activities, are all different. While biodiesel is mainly produced by food-oil refiners, HVO production is mostly carried out by petrochemical companies because they are familiar with the hydrotreatment process, which typically operates in two stages. The double bonds of the hydrocarbon chains are first saturated with hydrogen. This is followed by the elimination of oxygen atoms through three parallel mechanisms: hydrodeoxygenation, decarboxylation and decarbonylation. An extra step is mandatory for SAF production. Catalytic hydrotreatment occurs at high temperatures, from 300 degrees to 400 degrees Celsius, and hydrogen pressure between 3 megapascals (MPa) and 20 MPa. Sulfide nickel-molybdenum (Ni-Mo) and cobaltmolybdenum (Co-Mo) supported on alumina are the most common catalysts used, along with sulfur-free noble metals such as platinum (Pt) and palladium (Pd) or zeolite-supported Pt catalysts. Along with the process temperature and pressure, the catalyst type has an important impact on the final HVO product quality (compositional distribution).
Today’s main HVO markets are in Europe and the U.S., but new markets are developing fast elsewhere throughout the world. While biodiesel is still the most common biofuel in Southeast Asia, HVO production is also taking off in that region. Global HVO production capacity is expected to exceed 20 million metric tons per year (mtpy), or approximately 6.5 billion gallons, in the coming years. A number of companies have developed in-house HVO production processes but, in most cases, the HVO technology is offered by licensors.
The Finnish company Neste Corp., a pioneer in HVO technology, is a leading renewable diesel and jet fuel producer worldwide. Its NEXBTL technology can turn a wide range of renewable feedstocks into premium biofuels and other products. Neste’s first commercial-scale HVO plant was set up in 2007 at Porvoo, Finland. Today, it also has large capacity plants in Singapore and the Netherlands. When the scheduled expansion of these plants is realized by the end of 2023, Neste will have a global HVO production capacity close to 4.5 mtpy, including 1.5 mtpy of SAF.
HydroFlex™ is the technology supplied under license by Denmark-based Topsoe, which was developed in 2004 in anticipation of new market trends. HydroFlex™ units run alongside conventional petrochemical units all over the world with full flexibility, allowing the transformation of any renewable feedstock into drop-in, ultra-low sulfur gasoline, jet fuel or diesel.
Italy-based Eni has developed the Ecofining™ system in collaboration with Honeywell UOP and, in 2013, started up a green refinery project based on the conversion of two existing hydro-desulfurization units in Venice and Gela into
hydrotreatment processes. Several other plants using the technology are in operation in the U.S. and Europe.
The Vegan® HVO technology developed and licensed by France’s Axens Group is a flexible solution for hydrotreating a wide range of lipids and producing low-density, high-cetane renewable diesel as well as renewable sulfur-free jet fuel. This technology was originally developed by IFP Energies Nouvelles in the mid-2000s and is the result of Axens’ wide experience in conventional hydroprocessing technologies and catalysts, with more than 200 units licensed in the world.
A wide variety of products containing triglycerides and/ or fatty acids can be used in HVO production. These include vegetable oils, beef tallow and waste or used cooking oil (UCO). There is also increasing use of wastes or residues such as nonfood-grade vegetable oils, low-quality animal fats, sludge palm oil mill effluent (POME), distillers corn oil, or refining byproducts such as acid oils from soapstock, oil recovered from bleaching earths, fatty-acid distillates, distillation pitches and even nonglyceride feedstocks.
For sustainability, economic and political reasons, producers are increasingly looking for alternative, lower-quality waste and nonfood feedstocks. The quality parameters of some raw materials used for HVO are presented in Table 1.
Table 1: Quality Parameters of Different HVO Feedstock
Raw Material FFA P Metals N S Cl (total) Polyethylene % ppm ppm ppm ppm ppm ppm
Edible Vegetable Oils
< 3 50-250 100-300 30200 2-20 < 5Crude Palm Oils < 6 15-30 20-60 10-20 < 10 < 15 -
Used Cooking Oils 1-10 < 20 < 50 5-15 10-100 20-100 0-200
SOURCE: DESMET BALLESTRA
Table 2:
The HVO process requires efficient, flexible, safe, reliable and sustainable pretreatment of feedstocks. In general, pretreatment is necessary to remove impurities such as phosphorous, metals, polyethylene, nitrogen, sulfur and chlorine-containing components that are naturally present in some raw materials.
Pretreatment is a critical step in protecting HVO catalysts and increasing their life span, and to avoid operational problems in the industrial installation.
> 85 < 5 < 10 < 10 < 10 < 10100 250 30 100 Chlorine (total) ppm EN 14077 ASTM D7359 10 50 5 50 Polyethylene ppm AOCS Ca 16-75 50 50 50 50 NS: Not Specified *Ca, Mg, Fe, Na, K, B, Si, Zn, Al
The quality requirements for feedstocks at the inlet of the HVO unit are mostly set by the HVO technology providers and are generally quite stringent (see Table 2). An efficient and flexible pretreatment process will determine if, or to what extent, a low-quality feedstock can be used. This will directly impact the viability of the HVO plant. Pretreatment of good-quality raw materials (vegetable oils, UCO and high-grade animal fats) is quite straightforward and can be
Moisture
Unsaponifiable
Phosphorus
Metals (Total*) ppm AOCS Ca 17-01 ASTM D5185 10 5 5 10
Nitrogen ppm ASTM D4629 50 350 100 350
Sulfur ppm ASTM D2622 ASTM D4294 ASTM D5453
100 250 30 100
Chlorine (total) ppm EN 14077 ASTM D7359 10 50 5 50
Polyethylene ppm AOCS Ca 16-75 50 50 50 50 NS: Not Specified *Ca, Mg, Fe, Na, K, B, Si, Zn, Al SOURCE: DESMET BALLESTRA
accomplished by a series of processes that are already known within the edible-oil refining sector.
The basic configuration of a standard HVO pretreatment plant (see Figure 1a) normally has two cleaning sections: an acid-degumming section followed by a dry pretreatment/ bleaching section. Acid degumming with washing efficiently removes most impurities such as phospholipids, metals and mineral salts. Dry pretreatment/bleaching, with activated bleaching earth or silica, achieves the required low levels of contaminants. Animal fats and some UCOs may nevertheless require an additional second bleaching step to remove polyethylene and plastics residues that can be present in these raw materials (see Figure 1b).
For other low-quality feedstocks, some additional steps may be required prior to the standard pretreatment process. This includes a prefiltration step to remove high levels of solid impurities, polyethylene and some nitrogen components (for example, from protein) and/or a specific heat pretreatment step to remove phosphor-containing components and metals from very low-quality animal fats (EU category 1 and 2 animal byproducts) and acid oils, as the basic pretreatment-plant configuration fails to remove these contaminants to lowenough levels.
Finally, an alternative pretreatment process has been developed for very poor-quality feedstocks like some acid oils, distillation pitches and trap grease. This process mostly consists of fat splitting followed by fatty-acid distillation. The process is very efficient at treating feedstocks with extremely high loads of contaminants, but often has lower yields then a classic pretreatment process and has much higher capex and opex costs. Its application has, until now, been limited to lowcapacity plants with difficult feedstocks.
Providers of pretreatment processes for HVO mostly originate from the vegetable-oils and fats industries since the technologies are very similar to vegetable-oil refining for food applications. The companies generally have an extensive portfolio of similar technologies. However, since HVO producers are increasingly focusing on low-quality feedstocks, existing processes need to be adapted and optimized to clean these feedstocks. In addition, as more pretreatment plants come online, greater operational experience is gained, and this allows a continuous improvement in pretreatment-plant configurations to enhance efficiency, reliability and safety.
Desmet Ballestra is one of the companies that supplies pretreatment technology for HVO producers. The objective is to guarantee the quality requirements set out by different HVO technology providers and to meet the high-capacity ranges, up to 5,000 tons per day inlet capacity, required by this industry.
Authors: Veronique Gibon Science Manager, Desmet Ballestra vgibon@desmetballestra.com
Wim De Greyt
R&D Manager, Desmet Ballestra wdegreyt@desmetballestra.com
Jan De Kock
Key Account Manager, Desmet Ballestra jdekock@desmetballestra.com
Marc Kellens
Group Technical Director, Desmet Ballestra mkellens@desmetballestra.com
Demand for renewable energy is surging, and biofuel companies are meeting this need by rapidly investing in new renewable diesel and sustainable aviation fuel (SAF) capacity. To supply these plants and hit carbon-intensity targets, producers are drawn towards a variety of feedstocks that contain more impurities than virgin oils. Consequently, the refining process typically requires significant solids removal, and improved filtration techniques mean even the most heavily contaminated fats, oils or greases can be used to run engines. Whatever the source, the feedstock needs to be refined, either filtered or water-washed with a centrifuge. The latter process effectively scrubs away the contaminants but has a few drawbacks, namely heavy water demand and highly contaminated wastewater. For that reason, more biofuel suppliers are moving towards filtration.
The filtration process for wastebased biofuels needs to work with different feedstocks from different sources that contain different types of contamination. Mineral filter aids have this flexibility due to the wide range of permeability available. Although diatomaceous earth (DE) filter aids are more widely known, perlite filter aids are used in almost every industry that separates solids from liquids. Expanded perlite particles are precisely milled to desired particle-size distribution to make various grades, able to filter a wide array of liquids. The high solidsholding capacity of perlite filter cakes is a function of the maze of microscopic pathways formed in the cake. Perlite filter aids can be used in both the precoat and bodyfeed in pressurefilter applications or on rotary vacuum filters, matching the performance of diatomite. Yet, when converting from a DE filter aid, it is important to note that these are two different minerals with different physical properties. Producers considering switching from a DE to a perlite filter aid should work with a filtration technical expert to understand all of the conversion considerations and to find the best filter aid for their filtration system.
An abundant and reliable perlite product can assure quick and uninterrupted supply. This is not always the case with comparable minerals that have longer lead times and require significant inventories to supply variations in demand. Perlite filter aids are produced at numerous, small expansion plants located across North America. This national footprint places perlite filter-aid production within close vicinity of nearly every biofuel producer. In contrast, other filter aids rely on a supply chain to customers that may be long and vulnerable to logistic complications. Due to its distribution of production locations, perlite capacity is less constrained. At Imerys, our network of six expansion plants can readily manufacture any filter-aid grade to minimize order backlogs. With operations close to customers and serving only the domestic market, perlite is the most readily available filter aid for biofuel producers.
Figure 1
SOURCE: IMERYS
The unique structure of perlite makes for a very light weight with 30 percent to 50 percent less bulk density compared to other filter aids. Therefore, users typically require 30 percent to 50 percent less additive. The high void volume and porosity of perlite form a thick, permeable filter cake improving permeability and flux rates.
“The main consideration when making a conversion to perlite is the impact of density,” explains Mike Boerner, manager of filtration technical services at Imerys. “Dosage is based on filter area, so producers switching to perlite are typically using the same volume at nearly half the mass.”
Experience in a variety of applications has shown that most filter-aid users can economically switch to perlite from other filter aids without sacrificing efficacy or efficiency.
“We have successfully converted a variety of producers to perlite while maintaining excellent filtration performance,” Boerner confirms. “Qualifying an alternative filter aid gives our customers options.”
Figure 2
Figure 3: Perlite yields a lower pressure rise than DE with comparable filtrate clarity (NTU).
SOURCE: IMERYS
Figure 3 Previous Process SOP
Savings
Perlite filter aids also provide significant savings due to density and supply advantages. The value proposition shown in Figure 4 was modeled using data from a successful customer conversion. Due to the lower density of perlite, the customer realized a 44 percent reduction in filter-aid usage by mass. The closer proximity to the customer also provided substantial shipping savings. In total, the savings are about $78,000 per year by switching to perlite filter aid for precoat.
Authors:
Neal Williams Research Engineer, Imerys neal.williams@imerys.com
Jacob Misuraca Research Engineer, Imerys jacob.misuraca@imerys.com
With more than a century of production experience and technical expertise, Imerys has developed a portfolio of filter aids and filterable absorbents that offers unparalleled flexibility and cost-effectiveness in a wide range of feedstock.
Harborlite 900 RE is our perlite filter aid formulated and quality-tested to meet the specifications required by the biofuel market. We work closely with plant operators and their engineering support teams to help identify new solutions to problems that have yet to happen. Imerys’ proven track record and commitment to sustainable innovation are core to our reputation. Producers looking to optimize their filtrationsystem performance should reach out to the Imerys filtration team.