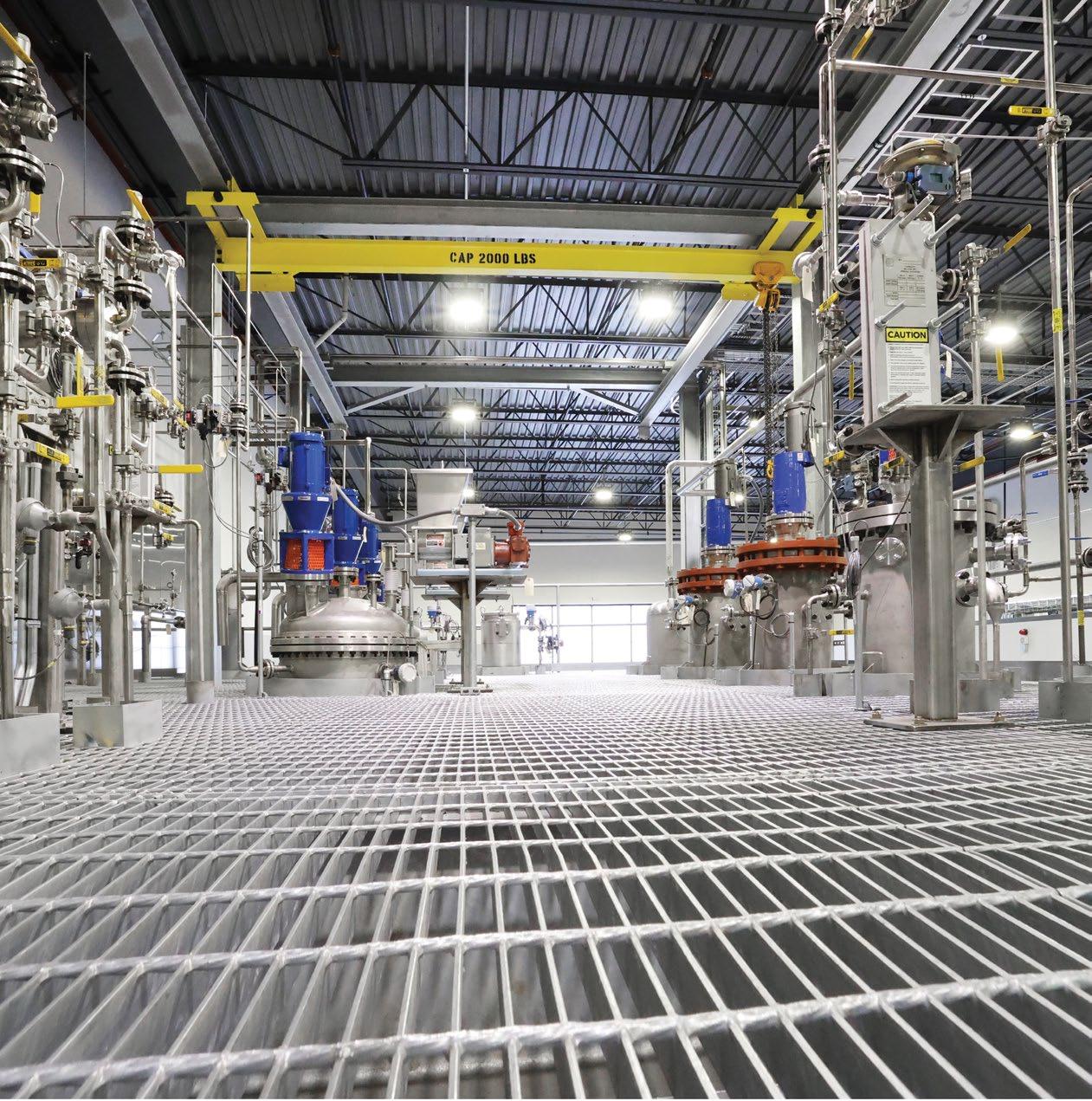

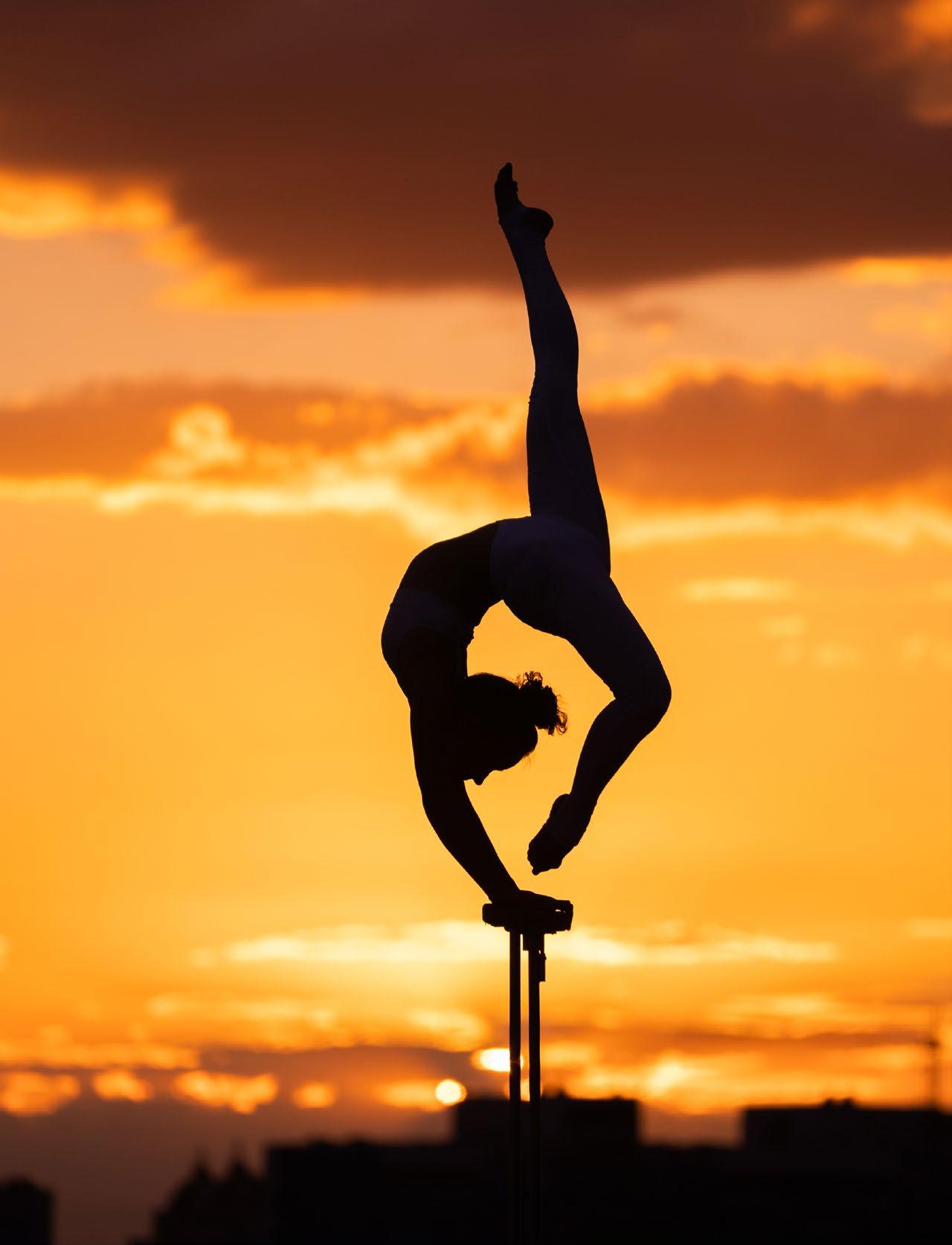
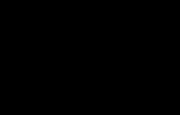
With the current global supply chain issues it isn’t always easy to keep production running while managing complex streams of raw materials and finished products.
Evonik is helping the North American Biodiesel industry by offering the highest quality Sodium Methylate directly from our recently expanded production site in Theodore, Alabama, including rail to truck transloading terminals located in Kansas City, East Chicago, Baltimore, Arizona and Alberta.
At the same time Evonik offers global supply of Sodium Methylate from our other production facilities in Germany, Argentina and, coming soon, South East Asia.
Looking for readily available Sodium Methylate for your biodiesel production? Ask our biodiesel experts!
biodiesel-nam@evonik.com
https://catalysts.evonik.com/en/markets
After covering the biobased diesel industry for more than 18 years, 14 of which I have spent as an editor, I find myself typically avoiding using this page—the editor’s note—to highlight articles or columnists featured in the ensuing pages of the magazine.
Usually, I find this space as a great opportunity to share my opinion on issues of the day that otherwise wouldn’t be included in the edition, or for late-breaking news that developed after the articles were completed and ready for print.
In many cases, the editor’s note is the last piece to be written before publishing, either because editors have been too busy preparing the magazine for print or because, at least in some instances, they really have nothing to say.
I find editor’s notes that shy away from real opinion or interesting industry developments and instead point out articles the reader would otherwise find on their own by simply thumbing through the pages quite pedestrian, actually.
Having said this, the collection of experts gathered in this 56page book—the largest yet since I launched Biobased Diesel™ two years ago—is nothing short of impressive and noteworthy, in my humble opinion. In fact, I challenge any editor in this sector to assemble a better group of industry leaders.
Kelly King, co-founder of one of America’s oldest biodieselproducing companies—Pacific Biodiesel—put pen to paper in an exclusive article for Biobased Diesel™ on page 46, “Community-Based Biodiesel is the Circular Economy,” in a great piece whose name says it all.
John Campbell, another true pioneer in biodiesel, authors “Signs Flash Positive, but Questions Remain,” on page 18, in which he discusses remarkable developments in these industries but notes lingering policy uncertainties that, when answered, will certainly have profound impacts on producers and markets.
Paul Nazzaro, who developed the Bioheat® fuel concept more than two decades ago, takes a rare break from writing about his Bioheat® brainchild to share a behind-the-scenes look at the company he founded 30 years ago—Advanced Fuel Solutions— in “Is Your Fuel Advanced?” on page 30.
Tom Slunecka, CEO of Minnesota Soybean and the biodiesel technology company Plasma Blue, has worked in biofuels and commodities for as long as I can remember. When he joined Minnesota Soybean in 2012 as CEO after many years in the corn and ethanol space, I knew he would be a good fit for the biobased diesel sector. On page 32, Slunecka gives us “Plasma Blue: Lower Carbon Score, Higher Savings.”
Scott Fenwick, technical director for Clean Fuels Alliance America, takes the opportunity on page 26 to discuss Optimus Technologies’ recent capital raise and what it means for neat biodiesel use in “Optimus Technologies and the Era of B100.”
Milica Folic with Topsoe provides us with quite an interesting piece on where the process-technology company sees the SAF market going in years to come in “SAF Production Needs 3rdGeneration Feedstocks to Take Flight” on page 20. Be sure to read this one.
Chatty Sakhalkar with Teikoku USA astutely tells us about why canned-motor pumps are the environmentally friendly and intelligent choice for biorefineries in “Green—and Smart—By Design” on page 22.
Kristof Reiter with Reiter Companies, who I’ve known for many years, gives his expert opinion on the sharing of confidential business data as EPA finalizes its UCO-reporting requirements in “There’s a New Variable in UCO Trading” on page 24.
Dani Charles, co-founder of Veriflux, explains why technology is the only solution to the issue of “Feedstock Traceability” on page 34.
For our cover story, “Crown’s Next Step in Biofuel Innovation” on page 38, Bill Morphew with Crown talks about the company’s recently completed Liquids Pilot Plant, which is now open and fully operational at its Global Innovation Center in Blaine, Minnesota.
Finally, I author four stories in this issue, including “Feedstock Theft & Fraud” on page 36, “After More Than 15 Years, BDI’s RepCat Technology Comes of Age” on page 52, “Missouri’s Claim to FAME” on page 42, and “Automation Integration: Do It Right the 1st Time,” a profile of Helle Engineering, on page 28.
I sincerely hope you enjoy reading this issue as much as I enjoyed putting it together. I am grateful to all the editorial contributors and advertisers for making this very special edition of Biobased Diesel™ possible. Thank you.
Ron Kotrba Editor and PublisherIn May, Montana Renewables—currently North America’s largest sustainable aviation fuel (SAF) producer—celebrated its first commercial production and initial shipments of SAF under a multiyear agreement with Shell Trading (US) Co. The Great Falls plant can produce 135 million gallons per year (mgy) of renewable diesel, 30 mgy of SAF and 15 mgy of green naphtha. In April, Delta announced an agreement to purchase 10 million gallons of neat SAF from Shell at Los Angeles International Airport (LAX) [BBD]
Darling Ingredients and Valero Energy made a final investment decision on a $315 million project to manufacture SAF at their Diamond Green Diesel joint-venture facility in Port Arthur, Texas Upon completion in 2025, half of the plant’s 470 mgy capacity will be capable of producing SAF. [BBD]
Par Pacific Holdings is investing $90 million to produce approximately 61 mgy of renewable diesel, SAF, naphtha and LPG in Hawaii at its Kapolei refinery by 2025. The unit will be able to produce up to 60 percent SAF. [BBD]
LanzaJet is collaborating with Jet Zero Australia to start project development of an alcohol-to-jet (ATJ) SAF plant in Queensland Construction on the 26.4 mgy project is expected to begin in 2024. LanzaJet is also exploring SAF project development in India with Indian Oil [BBD]
Axens and Praj signed an agreement to work jointly on projects in India for SAF production based on Axens’ Jetanol™ ATJ technology. [BBD]
Sichuan Jinshang Environmental Protection Technology (JSRE) will use Honeywell Ecofining™ technology to produce nearly 100 mgy of SAF at its newly planned facility in Suining, Sichuan Province, China. Once completed, the facility is expected to be one of the largest SAF plants in China. [BBD]
Wizz Air is investing $6.2 million in Firefly Green Fuels. The partnership will allow the airline to supply more than 170 million gallons (mg) of SAF to its U.K. operations from 2028. [BBD]
JGC Japan and Toyo Engineering signed an alliance agreement to pursue and execute orders for FEED and EPC services for SAF plants in Japan, where domestic SAF demand is expected to grow from almost 80 mg in 2025 to nearly 452 mg in 2030. [BBD]
Cepsa and Bio-Oils, Apical’s biofuels entity, have created a joint venture to build a $1.1 billion, 165 mgy renewable diesel and SAF plant. The facility, to be located at Cepsa’s La Rábida Energy Park in Huelva, Spain, will include two pretreatment units. The plant is scheduled to begin operating in 2026. Most of the waste feedstock will come from Apical. [BBD]
The four-year expansion of Neste’s Singapore biorefinery is complete. Neste doubled total capacity to 880 mgy and significantly expanded SAF capacity to 340 mgy, making it the largest operating SAF facility in the world. Neste’s global SAF capacity will grow to 515 mgy by the end of this year, and to 750 mgy in 2026. As a result, Neste has been shoring up supply deals, including 12 mg to Wizz Air beginning in 2025; 5.6 mg to Boeing; 2.5 mg to Air Canada at
San Francisco International Airport (SFO); 1.5 mg to United at SFO; and 264,000 gallons to Viva Aerobus for certain flights from LAX to Mexico [BBD]
Repsol signed an agreement with Ryanair to supply up to 52 mg of SAF at airports across Spain and Portugal between 2025 and 2030. [BBD]
Several big-name companies such as Bank of America, Meta and JPMorgan Chase are joining together through the Sustainable Aviation Buyers Alliance to purchase SAF certificates at scale. The 850,000 gallons of SAF involved in the SABA transaction is produced by World Energy and is being used to fuel JetBlue flights this year. [BBD]
European legislators agreed this spring to increase SAF uptake, setting the minimum share of SAF at 2 percent in 2025, increasing to 6 percent in 2030, 20 percent in 2035, 34 percent in 2040, 42 percent in 2045 and 70 percent in 2050. At least 35 percent of the SAF share must be synthetic eFuels made from renewable electricity and CO2 by 2050. [BBD]
Washington Gov. Jay Inslee signed a bill providing a $1-pergallon tax credit for SAF with at least 50 percent less CO2 emissions than conventional jet fuel, and a 2-cent increase for every additional 1 percent CO2 reduction beyond 50 percent, not to exceed $2 per gallon. The credit may not be claimed until in-state production reaches 20 mgy. Coprocessed SAF is eligible for the credit. [BBD]
In Illinois, Gov. J.B. Pritzker also signed a bill providing SAF purchase credits for 10 years. Beginning June 1 through Jan. 1, 2033, the new law gives a $1.50-per-gallon tax credit for SAF sold to or used by an air carrier in Illinois. To qualify for the credit after June 1, 2028, the SAF must be derived from domestic biomass resources. [BBD]
A federal grand jury in Washington, D.C., indicted Bryan Sherbacow, founder and former CEO of SAF company Alder Fuels, for allegedly embezzling at least $5.9 million from the company. Sherbacow was terminated from his position as CEO by the board of directors in December due to “questionable financial transactions.” [BBD]
Several projects in the U.S. and Canada near the finish line while others in Brazil get started.
Following Vertex Energy’s ribbon-cutting ceremony for the company’s renewable diesel unit at its Mobile, Alabama, refinery, held April 28, the facility’s feedstock-pumping system suffered a critical equipment failure. Vertex Energy reached mechanical completion March 31 and the ribbon-cutting a month later marked a transition from commissioning to start-up. Once running at full rate, renewable diesel volumes of 114 million gallons to 143 million gallons per year (mgy) are anticipated, with expansion to 200 mgy upon installation of additional required infrastructure. Soybean oil is serving as the primary feedstock initially. The feedstock-pumping failure occurred during unit start-up sequencing before any hydrotreated fuel was actually produced. Repairs were expected to be complete by the end of May. [BBD]
Construction on PBF Energy’s 306 mgy renewable diesel production unit co-located with its Chalmette refinery in Louisiana reached mechanical completion this spring, followed by commissioning. Feedstock (virgin oils, technical tallow and distillers corn oil) was introduced in May. Once its pretreatment unit is complete, the company expects to introduce lower carbon-intensity feedstocks. Project costs are estimated at $650 million to $700 million. In February, PBF Energy and the Italian refining company Eni announced a 50/50 joint venture, St. Bernard Renewables, which will own the Chalmette renewable diesel project. Upon closing, which is expected later this year, Eni will contribute $835 million in capital, excluding working capital, plus up to an additional $50 million subject to achieving project milestones. PBF Energy will continue to manage project execution and will serve as operator. [BBD]
The joint-venture project between Marathon Petroleum and Neste to convert a petroleum refinery in Martinez, California, for manufacturing renewable diesel began Phase I commissioning and start-up activities early this year. Phase I capacity is 260 mgy. Pretreatment capabilities are expected to come online later this year, and once Phase II is completed by the end of 2023, the site will be capable of producing 730 mgy. [BBD]
Braya Renewable Fuels secured a $300 million preferredequity investment from Energy Capital Partners, which completes financing for the conversion of Braya’s Come By Chance refinery in Newfoundland and Labrador, Canada, to manufacture renewable diesel and SAF. The project, scaled at nearly 260 mgy, includes production of green hydrogen for biorefining processes and export as green ammonia. [BBD]
Tidewater Renewables began initial unit commissioning of the 45 mgy renewable diesel complex at its Prince George Refinery in British Columbia, Canada, this spring. Start-up of the $255.8 million project is expected in June. [BBD]
Imperial, Canada’s largest petroleum refiner, is investing $560 million to construct what it says will be “the largest renewable diesel facility in the country.” The project at Imperial’s Strathcona refinery near Edmonton, Alberta, is expected to produce more than 264 mgy of renewable diesel beginning in 2025. [BBD]
Parkland has decided to scrap plans to build a standalone renewable diesel complex at its Burnaby Refinery in British Columbia, Canada. The company cited several reasons for the decision, including rising project costs, a lack of market certainty and the Inflation Reduction Act, which advantages U.S. producers. The company will, however, expand renewable diesel coprocessing at the refinery. [BBD]
Brazil’s state-owned petroleum company Petrobras is conducting new project studies to expand the production of coprocessed renewable diesel as part of its biorefining program. Petrobras is coprocessing vegetable oil with petroleum diesel to produce end fuels with varying concentrations ranging from 5 percent to 10 percent. Adjustments are being studied for coprocessing at its Gabriel Passos (REGAP) and Abreu e Lima (RNEST) refineries. New plants dedicated to the production of 100 percent renewable diesel made in standalone units will also be assessed at RNEST and the Gaslub Pole [BBD]
Mubadala Capital’s Acelen, owner of the Mataripe Refinery in Bahia, Brazil, has signed a memorandum of understanding with the state government of Bahia for renewable diesel and SAF production. The manufacturing of up to 264 mgy is slated to begin in 2026. Acelen expects to invest more than $2.4 billion over the next 10 years in renewable fuel production. [BBD]
Oleo-X recently opened its renewable diesel and SAF feedstock merchant pretreatment facility in Pascagoula, Mississippi. The new facility has the potential capacity to produce up to 300 mgy of premium feedstock. [BBD]
Kinder Morgan has begun service of its renewable feedstock storage and logistics hub project in Harvey, Louisiana, in a longterm contract with Neste, which collects used cooking oil from more than 80,000 U.S. restaurants for renewable diesel and SAF production in Finland, the Netherlands, Singapore and California. The storage and logistics project was first announced in 2021. Kinder Morgan’s Southern and Northern California renewable diesel hub projects are also now in service. The initial phases of both California hubs are fully subscribed with customer commitments. [BBD]
Astomos Energy and Inpex have agreed to supply B24 marine biofuel to a Very Large Gas Carrier chartered by Astomos in the United Arab Emirates—a first for the Middle East Neutral Fuels will produce the biodiesel from used cooking oil (UCO) and Monjasa will supply the blended bunker fuel. [BBD]
Toyota Tsusho and group company Toyotsu Energy have launched Japan’s first continuous supply of biodiesel-blended fuel on a commercial basis to ships operated by Toyofuji Shipping at the Port of Nagoya. [BBD]
VT Group and FinCo Group concluded a nine-month pilot using 100 percent biodiesel as marine biofuel on the MTS Vlissingen. Conditioning of the ship’s fuel-supply system was adjusted for the pilot. Some biodiesel used was made by Argent Energy. VT Group plans to use B100 on other ships in its fleet. [BBD]
Total Energies Marine Fuels completed its first B30 marine biofuel bunkering trials in France, one on the Minerva Tychi at the Port of Le Havre and the other on the ro-ro/passenger ship Mega Express Two in the Port of Toulon, in cooperation with Corsica Ferries [BBD]
Fratelli Cosulich, in partnership with Iplom, has begun producing and supplying its own marine biofuel blend in Genoa, Italy. The fuel, first tested on a Hapag-Lloyd ship, is bunker fuel
sourced from Iplom blended with 10 percent biofuel from an ISCCcertified Italian biorefinery. [BBD]
In South Korea, HMM has signed an agreement with GS Caltex to secure marine biofuel with 30 percent biodiesel, which HMM plans to use for three containerships later this year. [BBD]
Marine-fuel supplier Peninsula has begun providing marine biofuel at its hub ports in the Strait of Gibraltar. Peninsula has received ISCC certification for its supply operations in Gibraltar, Algeciras, Spain, and nearby ports. [BBD]
The Global Centre for Maritime Decarbonisation completed two supply-chain trials of biofuel blends sourced from different origins. The trials encompassed tracing biofuels from their production sites outside Singapore, to Singapore where the fuels were blended and bunkered. Five vessels bunkered 4,700 metric tons of blended marine biofuels. UCO was used in B20 and B24 blends. Companies involved include Chevron, CMA CGM, MOL, ONE, NYK, Asotomos Energy, Angelicoussis Group, Maran Tankers Shipmanagement and VPS [BBD]
DB Schenker has secured an arrangement to use 12,000 metric tons of biofuel component from MSC Mediterranean Shipping, representing one of the largest carbon-insetting biofuel deals between a freight forwarder and shipping company. The UCO-based marine biofuel will consist of 20 percent to 30 percent blends. [BBD]
Portugal-based biodiesel producer Prio has formed a partnership with World Fuel Services to provide B30 marine biofuel to Norwegian Cruise Line Holdings. Prio provides B30 at any Portuguese port and plans to extend service to other locations in Europe [BBD]
CLINTON, IA
WASHINGTON, IA
VISIT
CONTAC T: Shawn Triscuit, Director
HERO BX has been innovating and expanding for over 10 years. Each location offers biodiesel products and logistics expertise to meet regional demand. HEROBX.COM
NORTH HAMPTON, NH MOUNDVILLE, AL
ERIE, PA
ofSales striscuit@herobx.com
1 Singapore: 258,300,000 gallons
2 Netherlands: 3,948,000 gallons
3 UAE: 420,000 gallons
Total U.S. biobased diesel imports down 14%
Total U.S. renewable diesel imports down 33%
U.S. received first shipment of renewable diesel from UAE
Total U.S. biodiesel imports up 23%
U.S. imports of Italian biodiesel soared 265%
U.S. imports of German biodiesel up 185%
U.S. imports of South Korean biodiesel down 48%
Total U.S. biodiesel exports up almost 65%
U.S. exported more to Canada in 2022 than all 2021 exports combined
U.S. biodiesel exports to Canada up 34%
U.S. exported more biodiesel to Singapore in 2022 than ever before, securing second-top destination for first time
1 Canada: 189,630,000 gallons
2 Singapore: 76,104,000 gallons
3 Peru: 22,722,000 gallons
4 The Netherlands: 8,610,000 gallons
5 Norway: 1,890,000 gallons
6 Germany: 1,092,000 gallons
7 Mexico: 126,000 gallons
8 Chile: 42,000 gallons
9 Taiwan: 42,000 gallons
1 Canada: 123,354,000 gallons
2 Germany: 76,860,000 gallons
3 Spain: 20,580,000 gallons
4 South Korea: 12,516,000 gallons
5 Italy: 12,432,000 gallons
6 Belgium: 4,158,000 gallons
Various federal and state policies continue advancing biobased diesel production forward, but the finalization of important details lingers.
By John CampbellThe U.S. biofuels industry got a powerful shot in the arm Aug. 16, 2022, when the Inflation Reduction Act was signed by President Joe Biden. A pared-down version of the Green New Deal, long been given up for dead, was narrowly approved by Congress as the IRA. The U.S. Department of the Treasury is still writing rules to implement IRA, but already it’s directed nearly $400 billion toward clean-energy programs. Notably, the tax code will—for the first time—reward biomass-based diesel carbon reduction in a way similar to California’s Low Carbon Fuel Standard. The biodiesel and renewable diesel blenders’ tax credit will morph into a new technology-neutral clean fuel production tax credit and include incentives for alternative jet fuel. Importantly, the details around modeling greenhouse-gas (GHG) reductions and carbon-intensity (CI) scores will invite the treasury department and tax code into key debates about the appropriate lifecycle-impact assumptions behind various versions of the all-important GREET model.
In parallel, the U.S. EPA has been undertaking the most important rule changes for the Renewable Fuel Standard since 2007. Congress gave EPA broad authority to reset the RFS in 2023 and beyond, thus leading to the EPA’s proposed RFS “set” rules that were released for comment Dec. 1. The proposed RFS “set” rules would modestly increase the renewable volume obligation (RVO) for biomass-based diesel by nearly 200 million gallons (7 percent) and the advanced biofuel RVO by 1.1 billion gallons (more than 30 percent) by 2025, as well as potentially adjust the ethanol-equivalent renewable identification number (RIN) values for both biodiesel and renewable diesel.
The IRA and the RFS “set” rules promise the greatest stimulus for the biobased diesel industry over the next decade. While not as robust as advocates would have liked, they have breathed new optimism into investors and markets.
In addition, the California Air Resources Board is considering a more aggressive decarbonization plan under the state’s LCFS by considering a 48 percent reduction of GHG emissions
below 1990 levels by 2030, surpassing the minimum statutory emissions goal of 40 percent. With 83 percent of the renewable diesel used in the U.S. already consumed in California and other West Coast incentivized markets, these potential changes to the LCFS could impact biobased diesel destinations as well as feedstock mixes.
In 2023 alone, Ocean Park estimates that approximately 900 million gallons of renewable diesel capacity will come online in the U.S. This will push total biodiesel and renewable diesel capacity to 5.5 billion gallons, exceeding the proposed RFS biomass-based diesel mandate by approximately 2.7 billion gallons and the nested advanced biofuel mandate by approximately 1.8 to 2.1 billion gallons. In 2024 and beyond, the scheduled biobased diesel capacity of approximately 7.1 billion gallons will exceed the proposed RFS mandates by more than 50 percent. It is important to keep in mind that both the RFS advanced biofuel mandate and the California LCFS credit market allow competing fuels such as renewable natural gas (RNG) and new electrification eRINs to compete with biobased diesel for compliance purposes. RNG and other fuels comprised 18 percent of the advanced fuel category in 2022.
The proposed RFS “set” rule essentially establishes a cap on biobased diesel production significantly below estimated capacity, which would only grow modestly over the next few years. Industry advocates have responded to this disconnect by requesting increases to the proposed RFS mandates in the final “set” rules as well as a carve out specifically for methyl ester biodiesel production. Essentially setting the biobased diesel market, the advanced biofuel RVO is growing modestly to the equivalent of 4.4 billion to 4.7 billion gallons.
While EPA may respond positively to these requests, it is unlikely that it will agree to mandate increases that would boost feedstock prices or disrupt feedstock trade flows. The prospect of significant excess biobased diesel capacity is increasingly apparent in renewable diesel project distress as well as reductions in traditional biodiesel production as more renewable diesel capacity comes online.
As producers of a “policy-made” fuel, the biobased diesel industry depends on what happens in Washington, D.C., and state capitals. All the signs are flashing positive, but questions remain on final rulemaking for the IRA, RFS and LCFS policies.
Ocean Park is active in mergers and acquisitions, as well as the credit and financing markets. For sellers seeking to cash in on this brave, new biofuels world and buyers nervous about regulatory risk, the trick is negotiating valuations that depend on the policies of this and future administrations.
Author: John Campbell Managing Director, Ocean Park 402-680-7111 jcampbell@oceanpk.comAlthough their solid nature provides more processing complexity, a watershed moment is expected in the next decade.
By Milica Folic´The aviation sector contributes 2 percent to 3 percent of global CO2 emissions and is under pressure to address this number. The industry must face the challenge of increasing sustainable aviation fuel (SAF) production to meet demand projected to reach 15 million metric tons (approximately 5 billion gallons) in 2030 and 200 million tons (66 billion gallons) by 2050.
For over 15 years, airlines have been exploring SAF’s potential, but adoption is still low. Significant changes have been seen in the past year though. The International Air Transport Association estimated SAF production increased 200 percent in 2022 from 2021’s level, and over 12 times the amount produced in 2019. But SAF use in 2022 was still only roughly 0.15 percent of global jet fuel.
For SAF adoption to truly take off, two significant and interconnected obstacles must be overcome: The supply capacity of SAF producers and the cost competitiveness of SAF compared to petroleum-based jet fuel. Increased investment, legislation, incentivization and standardization are key to making this happen.
Current specifications ensure existing aircraft and engines need not be redesigned to run on SAF, making the transition even more attainable. The primary focus today is on SAF as a drop-in replacement for conventional jet fuel, with ASTM standards excluding use of neat SAF. The International Civil Aviation Organization currently lists 59 airports worldwide distributing SAF. Seven technology pathways have been approved for producing drop-in SAF, as well as two coprocessing pathways.
The focus at Topsoe has been to develop a deep feedstock library, innovate solutions for a range of pathways and help accelerate the more mature routes for SAF, such as hydroprocessed esters and fatty acids (HEFA). HydroFlex, which provides great feedstock flexibility, enables processing of a wide range of raw materials. HydroFlex also provides product flexibility between renewable diesel and SAF. It is a dynamic technology that allows for full feedstock flexibility, including virgin oils, waste oils and fats, and yet-to-be-approved liquified waste biomass and plastic waste/tires. It utilizes Topsoe’s hydroprocessing expertise to produce HEFA-based SAF with minimal carbon intensity (CI) compared to traditional jet fuel. Topsoe also offers a comprehensive range of proprietary catalysts and hardware, and a versatile process design for HydroFlex.
Another potential source of alternative feedstock is gasified waste. The gas-to-liquid (G2L) route uses Sasol’s low-temperature Fischer-Tropsch technology and Topsoe’s hydroprocessing technologies to produce Fischer-Tropsch
synthetic paraffinic kerosene (FT-SPK). Meanwhile, G2L eFuels allows fuels to be produced from green hydrogen—derived from renewable electricity via electrolysis—and captured CO2. This technology combines synthesis gas, Fischer-Tropsch and hydroprocessing technologies to produce FT-SPK/eSAF and green naphtha. The overall carbon efficiency of this technology is 95 percent or more.
To tap into some of the same feedstocks of gasified biomass or captured CO2 and green hydrogen, the methanolto-jet technology is also being developed, but it will take time before this pathway is approved, scaled and commercialized. The MTJet™ technology is under development as a fasttrack project, and catalysts, process, business and ASTMcertification developments are all progressing in parallel.
As SAF demand grows, the availability of feedstocks and pathways is becoming increasingly crucial. SAF can be produced from a variety of renewable sources but competition for these feedstocks from other sectors for on-road and marine fuels is a challenge.
Though some on-road fuel producers are expected to switch to SAF production, first-generation feedstocks as a whole have likely reached saturation, while second-generation feedstocks, such as waste oils and fats, are expected to experience some growth, with more projects announced and realized until around 2030-’35, when growth will likely plateau. The focus will then shift to enabling third-generation feedstocks, which provide new opportunities but must be liquefied and come with extra costs and complexity.
Currently, the cost of producing HEFA and fatty acid methyl ester (FAME) biodiesel from first- and second-generation feedstocks is considered attractive. But as advanced feedstocks like third-generation waste require extra steps in the process due to their solid nature, prices are expected to rise because of this extra production complexity. EU policy, mandates and legislation, and the Inflation Reduction Act in the U.S., for instance, are incentivizing novel technologies and encourage industry to develop solutions for new feedstocks so these cost barriers can be reduced.
So, while hydroprocessing technology is mature and straightforward for liquid first- and second-generation feedstocks, third-generation feedstocks are more complex. Nevertheless, the industry and Topsoe are optimistic, and we expect to make third-generation feedstocks gamechangers. In terms of timelines, sooner is obviously better and we anticipate there will be a watershed moment between 2030 and 2035 when third-generation feedstock projects take off and dominate SAF production.
Author: Milica Folic´ Product Line Director, Clean Fuels & Chemicals-TechnologyThe journey to cleaner skies starts now. Sustainable aviation fuel is no longer an experiment but a prerequisite for low-carbon air transport. Industry players, passengers, and the planet will benefit. And our range of proven green-energy technologies is ready to help you produce more in-demand, renewable SAF.
Turn your sustainable ambitions into a sustainable business.
True secondary containment and onboard bearing-wear monitoring make canned-motor pumps the preferred choice where sealless pumps are required.
By Chaitanya “Chatty” SakhalkarWith the goal to combat climate change through feedstock selection and process technologies that would eliminate greenhouse-gas (GHG) emissions, the renewable bioeconomy— which includes sustainable aviation fuel (SAF), renewable diesel, green crude, biodiesel, ethanol, and finished biobased chemicals—is using carbon intensity (CI) as a metric to measure its operations.
While the big focus continues to be the feedstock, plant personnel are being challenged to identify more ways to contribute to lowering the CI of plant operations. Consistent with this effort, essential process centrifugal pumps are at the forefront of these low-carbon initiatives.
Given the emissions and possible leaks associated with mechanical shaft seals, bioeconomy industry leaders are pursuing sealless pump technology. By design, sealless pumps eliminate any potential of operating emissions and liquid leaks, making the technology an ideal choice for sustainable and environmentally conscious companies.
Within the realm of sealless pumps, canned-motor pumps are often preferred over magnetically coupled solutions due to standard advantages of true secondary containment as well onboard bearing-wear monitoring. Magnetically coupled pumps are equipped with a single containment shell that eliminates operating emissions and leaks normally associated with mechanical seals.
However, in specifying canned-motor pumps, where true secondary containment is provided as standard design, plant operators can rest assured that process fluid cannot leak into the atmosphere—even under upset scenarios.
Further, with technology to monitor bearing wear, cannedmotor pump technology offers the only pumping solution that provides real-time measurement of the actual condition of pump-wear components, as opposed to symptoms of wear, which can be inferred from fluctuating power or rises in circulated liquid temperature.
These two features—true secondary containment and onboard bearing-wear monitoring—allow the plants to manage risk and trend wear patterns to establish preventative maintenance schedules with the longest mean time between maintenance (MTBM) intervals, as well as avoid unplanned shutdowns due to pump failures.
In biorefining services, canned-motor pumps are being used in various inside battery limit (ISBL) and outside battery limit (OSBL) applications. Traditional refinery and chemical processing industry operators have invoked ASME B73 for OSBL services and API 685 for ISBL services. Bioeconomy projects follow a similar approach. The application of canned-
motor pumps, however, has been broadened within the biobased industry, and they are now being used on highly critical services such as hydrodeoxygenation as well as simpler services in water-treatment facilities.
A variety of features and enhancements are available that provide the opportunity to monitor critical operating parameters required for the handling of volatile, toxic and environmentally sensitive liquids and minimize maintenance exposure. These include:
• Rotating element position and bearing-wear monitors with control outputs
• Variable frequency drive (VFD) speed-control capability for enhanced process control
• Secondary-containment leak monitors
• Elimination of alignment
• Underwriters certification for hazardous-area classifications
• Versatile and space-saving mounting arrangements with small footprints
• Full compliance to industry design standards such as API, ISO and ASME/ANSI
• High-temperature motor-insulation systems that eliminate cooling-water needs
• API 685 Annex D and ASME/ANSI B73.3 circulation systems to meet all fluid characteristics
The global Teikoku Group is the world’s largest manufacturer of sealless, emission-free, canned motor process centrifugal pumps. With manufacturing and design capability in the U.S., China, India and Japan, and subsidiary offices and service centers located in major markets worldwide, Teikoku is positioned to exceed user expectations in both production and support of its pumping technology.
Author: Chaitanya “Chatty” Sakhalkar National Sales ManagerTeikoku USA Inc.
281-846-2857
csakhalkar@teikokupumps.com
As U.S. EPA finalizes its UCO-reporting requirements, collectors and buyers now have to agree on how much confidential business data to share.
A used cooking oil (UCO) collector considers a variety of factors when deciding where and to whom to sell their oil. Price, length of contract, logistics and the reputation of the counterparty have historically been primary decision drivers. But now, as the U.S. EPA is finalizing its UCO-reporting requirements, they have an additional variable to consider. Collectors and buyers now have to agree on just how much confidential business data (client lists and oil-volume sources) to share, when and with whom. Both sellers and buyers now have new concerns and liabilities.
Throughout 2022 and 2023, EPA has been drafting and reworking the Renewable Fuel Standard for the 2023-’25 term. A key part of that effort has revolved around clarifying the rules about reporting where biofuel producers get the UCO they use in their production. While debate has gone back and forth on who should be responsible for the data—for example, whether a producer or third-party company should hold the records—EPA has made clear that it wants detailed records of where each gallon of oil originated, down to the address or GPS coordinate of the source, the date of collection, and the number of gallons or pounds collected.
In recent years, some leading biofuel producers have sought to become more vertically integrated by entering into collection of restaurant waste themselves or by expanding their accounts. Think of this as analogous to a petroleum refiner also wanting to own and operate the wellheads. Understandably, most grease collectors who have traditionally serviced these UCO “wellheads” will not want their lists of clients and the volumes of oil they produce to be publicly available to their potential competitors.
Conversely, if a seller (UCO recycler) is known to have hand-written records decomposing on the floor of their truck, or worse yet, the records don’t exist at all, the buyer probably would not want to assume the risk of failing an audit, replacing invalidated renewable identification number (RIN) and Low Carbon Fuel Standard credits, and facing steep penalties.
EPA has the right to regulate entities generating RIN credits and hold these producers liable for replacing invalidated RINs. To limit their own liability, the producer can create a scenario in which they are indemnified, such as with Q-RINs—RINs verified by a third-party auditor under the Quality Assurance Plan protocol. In turn, RIN producers are given the choice to incur the costs associated with third-party QAP services or handle the risk and liability internally. Each option has its pros and cons for the producer.
As a trading firm representing independent, U.S.-based recyclers in the UCO space for over a decade, Reiter Trading and sister company Reiter Software have sought to take an active
role in shaping the current discussion regarding recordkeeping. We have worked to develop software that makes handling the ever-changing compliance landscape effortless for our clients. And we have fought to ensure the privacy concerns of our suppliers and liability concerns of our customers are fully understood by each party and the regulatory authorities.
To those of you who have engaged with us over the past several months in this effort—both suppliers and oil users—thank you. We appreciate your engagement and support. Whether you are a competitor, client or something in between, it is the existence of all of us that creates a competitive and efficient marketplace of products and services that, in the end, benefits the entire supply chain—all the way back to the restaurant.
At present, Reiter Trading will continue to transparently communicate all the recordkeeping obligations to our vendors, letting them decide the price/privacy balance that is right for them on a contract-by-contract basis. Conversely, we will continue to supply all our customers with one of the most traceable UCO supply chains on earth.
If you are a collector hoping to sell into the renewable fuel industry, consider first getting organized using software tools such as those offered by Reiter Software. Not only will our software offerings, such as Route Simplified, improve operations, but it will allow our trading firm and others like us to purchase from your organization with confidence that you are on top of the recordkeeping situation.
For a limited time, Reiter Software is offering free trials of its Route Simplified UCO collection and recordkeeping platform. Route Simplified removes the pain points in the UCO collection business and makes compliance a value-added byproduct of your further-optimized operation.
To learn more about all of the trading, software and consulting services available to UCO collectors from Reiter, visit ReiterUSA.com.
Author: Kristof Reiter CEO, Reiter Companies 888-428-5617kristof@reiterscientific.com
Clean Fuels Alliance America uses the slogan “Better. Cleaner. Now!” because there is urgency in the mission. Removing a pound of carbon from the atmosphere today is worth more than removing a pound of carbon from the atmosphere a year from now—and certainly 10 or 20 years from now. Carbon emissions in the atmosphere are cumulative, and time is a multiplier for many of the problems created by greenhouse gases, whether global warming or, on a more personal level, health problems such as increased instances of severe asthma.
Recently, Optimus Technologies raised $17.8 million to decarbonize the transportation industry through a Series A funding round led by Mitsui & Co. out of Tokyo, Japan. The round included participation from one of North America’s largest commercial fleets, along with Chevron Renewable Energy Group and several regional investors. This funding may help kickstart a new era for biodiesel and carbon reduction by improving options for fleets that are serious about reducing their carbon footprints now instead of waiting for developing technologies that are years or decades away from deployment.
The capital raised will fund the further development and deployment of Optimus’ Vector System, an advanced fuel-system technology that enables heavy-duty diesel engines to operate on 100 percent biodiesel (B100), a biogenic near zero-carbon fuel. The Vector System seamlessly integrates into existing engines in operation or can be built into new engines as they are manufactured, leveraging the foundational diesel engine for the transition to a low-carbon future.
“This strategic investment allows us to accelerate our mission to decarbonize the transportation sector,” said Colin Huwyler, founder and CEO of Optimus Technologies. “More importantly, this funding enables Optimus to immediately scale the delivery of carbon reductions at
a time when eliminating emissions can’t come soon enough.”
Heavy-duty transportation sectors are extremely challenging and costly to deploy with electric or hydrogen solutions, which require total replacement of existing assets, buildout of completely new infrastructure, and a fundamental shift in global energy production to renewables.
Biodiesel is an immediate solution and the fastest, easiest and cheapest way to meet scopes 1 and 3 emissions goals set by corporations and governments. The vast majority of diesel vehicles already support the use of B20, a blend of 20 percent biodiesel and 80 percent petroleum diesel, without any modifications required to make a meaningful reduction in emissions. However, the Optimus Vector System essentially multiplies that reduction by five by allowing vehicles to switch from B20 to B100.
The city fleet of Madison, Wisconsin, which in a February report made its case as the top fleet in North America, was an early adopter of Optimus’ Vector System. The city has seen substantial environmental benefits from using biodiesel without increasing the maintenance or downtime of vehicles, despite the cold environment. The fleet is approaching 8 million pounds of total carbon-dioxide reduction since 2018, and biodiesel is responsible for about 90 percent of that reduction, according to Mahanth Joishy, fleet superintendent.
“To convert the entire fleet to electric is going to take decades,” Joishy said. “Trucks are not going away. Construction equipment is not going away. These are here to stay, but we can operate them in a better way, in a cleaner way.”
Since 2018, Optimus has accumulated millions of miles of successful operation of its technology in numerous public fleets such as Madison and Washington, D.C., as well as in major commercial fleets, including that of Archer Daniels Midland.
Optimus’ unique approach to reducing carbon emissions is applicable across a wide range of industries from long-haul trucking to maritime and rail. The Vector System enables customers to reduce their carbon emissions today by more than 90 percent with a cost-effective solution that leverages existing assets and infrastructure. With this funding, Optimus will expand its team in Pittsburgh, Pennsylvania, and ramp up production of the Vector System to help meet the ever-increasing global decarbonization demands of fleets and governments.
The biodiesel industry is a mature industry now, having provided reliable, high-quality fuel for decades, but it’s still an industry capable of tremendous breakthroughs. The new round of funding for Optimus Technologies has the potential to dramatically increase the adoption of B100 and make the dream of a low-carbon future for fleets across the world a reality.
Author: Scott Fenwick Technical Director Clean Fuels Alliance America 573-635-3893 sfenwick@cleanfuels.orgAfter raising nearly $18 million in funding, the company is prepared to accelerate its mission to decarbonize heavy-duty transportation.
The last situation a project developer wants to encounter is monthslong delays in starting up a new plant due to inadequate integration of their automation systems. But that is precisely what can happen when International Society of Automation standards are not followed, says Matthew Helle, owner of Helle Engineering. Shortcuts and cheap fixes often lead to long, expensive delays.
“One company fought us tooth and nail on the ISA standards,” Helle says. “They questioned me on how long it would take to commission their plant. I told them, ‘First, we need to do loop checks.’ The project manager said, ‘What’s a loop check?’”
The shocking truth, according to Helle, is that many vendors and producers don’t know—or don’t care—ISA standards exist. “We have to let them know there’s a standard for this,” he says. “Reliability is a key thing.”
A loop check is required to test instrumentation end to end, making sure the transmitter’s calibrated range matches the range in the controller and human-machine interface (HMI).
“This particular customer didn’t want to follow ISA standards because of the money it would cost them,” Helle says. “Based on the IO count, I told them it would take us 12 to 14 weeks working 12-hour days. They chose not to perform loop checks and wanted it done in two weeks. It ended up taking them 18 months to get their plant running. This was only after the customer conceded and loop checks were completed. If you do it right the first time and follow standards, then, first and foremost, people don’t get hurt, second, you don’t harm the environment, and third, you can run your plant reliably and profitably. If you don’t follow ISA standards, you can have a very bad day—a very bad year, in fact.”
Helle has been providing automation-integration services for a quarter century. “I have a passion for this,” he says. “We try to do our job the best we can as engineers to ensure we don’t harm people and the environment. That’s our duty.” He’s worked for big-name companies over the years too. “I know what goes on in the biofuels industry and it can hurt and kill people,” he says.
What Helle Engineering provides may sound simple—a common user interface for plant operators—but it is anything but that. “In a manufacturers’ environment, they are buying different process skids from different vendors, and those skids do different things—whether its stripping CO, O2, H2S or distillation,” Helle says. “They buy separate pieces and put them together. That’s how they develop their plants. Along with that comes different controllers from every vendor they choose. They all have different HMIs, different programmable logic controllers (PLCs), and when operators try to run the plant with different user interfaces, that’s a problem. Normally they’re not following ISA standards. When we go to implementation, we follow the standards for loop checks,
Matthew Helle, owner of Helle Engineeringgraphics and automation controls. We write the logic based on process-control narratives and develop a common user interface. For the operator, it looks the same— uniform—at his or any another plant. This way, they know the alarm philosophy and what the difference is between critical and general alarms. We also provide first-out logic from each vendor skid so they know what tripped the plant.”
When Helle Engineering programs PID controllers, it utilizes current process values to identify problems in the process. “It’s all about throughput, how much you can push through the process to make finished product,” Helle says. “We call it loop tuning. We fine-tune temperature, pressure and flow controllers—we tune them properly and make the process more efficient to where a control valve is not oscillating as much. If the valve output is showing a sawtooth pattern, it’s not tuned properly. What you want is the valve making small moves—just millimeters. That means PID control logic is controlling the process and it’s in tune and working properly. When you optimize, you get more throughput. And constant throughput means reliability and profitability.”
Helle Engineering offers 24/7 support for everything it does. The company even supports systems provided by other integrators. “We have a customer in one state at whose plant the controls were developed by someone else, and we provide system support,” Helle says. “Their support costs are astronomical. But we wrote the controls for the same customer in a different state, and their support costs are 10 times less. We are not afraid to support what we write because we’re not going to put out a bad product.”
When it comes to automation integration, the Spanish saying, “lo barato sale caro,” which translates to English as “the cheap turns out expensive,” is so very true. “If you want reliability, if you want profitability, and if you want it done right, come talk with us,” Helle says. “If you don’t, then you can shop the world for the cheapest programmer, and they may get your interface up and running—but let’s see how you do over a year or two and what your profitability looks like when your system is crashing every day or week, or when you can’t maintain good flow because they didn’t tune your valves properly.”
Author: Ron Kotrba Editor, Biobased Diesel™ 218-745-8347If you don’t, then prolonged delays in start-up, as well as poor reliability and profitability in operations, will likely follow.
The word “advanced” conveys the ideas of modernity, something recently developed or ahead of its time in development or progress, as well as a high level of skill or knowledge. As the founder and president of Advanced Fuel Solutions, I have committed to living up to my company’s name by, first, being a disruptor. This is a moniker I carry for which I will never apologize. In fact, I encourage my team, clients and strategic partners to adopt disruptive behavior as well—constructive disruption, of course.
Sticking our heads in the sand hoping legislative pressures go away is not the solution. Identifying the threats before they are existential is the key. Being acutely aware of your space and your company’s position within it starts with maintaining an open mind. This means discarding what Daniel Burrus, someone who I believe is a notable American futurist, calls “rearview mirror thinking.” In other words, don’t milk the moment, because it’s easier to lead than to try catching up when others have already responded and are enjoying the benefits associated with being proactive.
With the liquid-fuels landscape being threatened by other energy sources that are still not practical for broad-based integration, strategic collaboration is more important today than ever before. Beyond being recognized as anything but an out-of-the-box additive supplier, AFS has succeeded in seeing what many others do not.
“Other’s Look, We See” was a proper phrase describing AFS three decades ago while we were building premium diesel formulations supported by intelligent, effective marketing campaigns. This helped differentiate market leaders like us from the laggards. Early adoption to improve baseline diesel quality presented market differentiation and growth for both buyers and sellers of these next-generation fuels.
Early on, I recognized the value of biodiesel as being a future blendstock designed to complement conventional diesel fuel and heating oil. Today that foresight pays dividends as a more expansive portfolio of low-carbon products like biodiesel, renewable diesel and sustainable aviation fuel (SAF) are no longer tethered to the question of “what if?” but rather now evoke a “bring-it-on” decarbonization strategy across the nation.
AFS is a consultative additive supplier navigating between fuel buyers and sellers to improve clients’ market positions. No shelf additive package will accomplish that. We differentiate ourselves by offering an unmatched consultative approach to additive use. Our clientele is a diverse group that includes heating-oil jobbers, diesel distributors, terminal operators, traders, renewable fuel producers, marketers, fleets and government agencies.
We can introduce custom AFS formulas anywhere in the supply chain. We search for and challenge our partners to develop innovative technologies that help us help our customers differentiate and prosper. How the additive will be stored, handled and blended on site also makes a difference in success. Those of you who know me also know that I have long been a vocal proponent of good housekeeping as an integral component to the quality management of fuelstorage systems.
Throughout the years, AFS’s services and products have evolved to meet changing fuel slates, hardware and regulatory demands. As low-carbon liquid fuels continue to make their way into the national supply chain, we will continue to work collaboratively with companies that have the capability to research and develop products we can rely on to serve those downstream.
For three decades, I have worked to understand the challenges and opportunities surrounding fuel quality and lowcarbon fuels. The expertise I have gained as a result of this focused 30-plus years can be leveraged by companies still deliberating or resisting the move toward low-carbon products that progressive fuel users across the country demand.
I never use low-carbon fuels as a scare tactic to sell more additives because additives were necessary long before lowcarbon fuels were available. And additives will continue to be required for many years as fuels and the quality, technical and regulatory environments in which they operate continue to evolve. Naysayers become adopters when they find out lowcarbon fuels do, in fact, deliver on their promise.
The expertise I have gained over the past three decades has been integrated with the entire AFS team. This is an insurance policy, so to speak, that my longtime practice of disrupting the business-as-usual mentality—a mindset that hinders progress—will carry on to the next generation.
Author: Paul Nazzaro President Advanced Fuel Solutions 978-258-8360Now more than ever, the biofuels industry seeks a solution that balances fiscal and environmental conservation. Look no further.
By Tom Slunecka By Tom SluneckaPlasma Blue is a revolutionary technology that creates biodiesel at a dramatically lower production cost while easily integrating into current renewable fuel facilities, including both existing plants and new greenfield projects. This combination is almost assured to drive profitability to higher levels, while giving you flexibility in your operation.
Rather than time-consuming traditional bioreactors, which use natural gas and mixing, our Plasma Blue technology applies electricity that excites the molecules as they pass through the reactor. In turn, this causes an improved intimate contact between the molecules. This technology drives the reaction faster than any other form of transesterification. In doing so, it delivers a more complete conversion and decreases bottleneck issues during this stage. Using Plasma Blue technology as a means for performing transesterification offers dramatic advantages, including a potential 10-cent-per-gallon savings to your plant due to lower energy and catalyst costs.
Beyond the operational savings, Plasma Blue technology is also environmentally friendly.
With changes to California’s Low Carbon Fuel Standard in 2024 coming from the Air Resources Board, reducing your carbon score is imperative. And by using electricity instead of natural gas, Plasma Blue requires significantly less energy because it doesn’t require preheating and creates flexibility in operations. Imagine the possibilities—biofuel plants lowering energy costs while enhancing facility carbon-intensity (CI) scores, allowing plants to take advantage of government incentives for clean, renewable energy. For example, an additional 35 cents per gallon may be attributed to the pergallon value of your plant based on a reduced carbon score.
Plasma Blue technology can be powered through wind or solar energy because our power requirement is amazingly low. Our 1.5-million-gallon-per-year (mgy) reactor only requires the equivalent of electricity used to run two 60-watt light bulbs. This technology can use renewable farm-grown oil, and by adding ethanol (another farm-grown renewable) instead of methanol and renewable energy such as solar electricity to power the process, the ultimate renewable liquid fuel is created. This is the true trifecta of liquid renewable fuels. On top of this perfect blend of renewables, Plasma Blue uses a less-intensive catalyst that is significantly more affordable than traditional ones. This may also further improve your facility’s carbon score and dramatically reduce production costs.
But often, production facilities are afraid of new technologies because they can be unproven, expensive to install and difficult to operate. This transformative technology, however, is none of these. Don’t let the fear of expensive downtimes or expansion needs stop you from integrating Plasma Blue in your facility.
When compared to installing traditional transesterification equipment, a Plasma Blue reactor will save you an estimated $1.5 million when installed in a 10 mgy plant. The unit has a very small physical footprint and modular design. This allows existing plants to increase production without expensive downtime or expansion of plant footprints. Furthermore, our technology easily fits into almost all existing plants without exterior expansion.
But actions speak louder than words.
Through years of rigorous testing, this design, which has received a certificate of analysis, has been scaled from a simple benchtop design to our current 5 mgy capacity unit. Scaling the technology is easy and, no matter the plant size you’re interested in, the plasma unit can be custom built for you.
Plants that have operated our technology have received consistent ASTM-spec biodiesel, and because of the plasma unit’s ability to complete reactions, the products have achieved much higher specs, including cold flow properties, equal to far more expensive distilled biodiesel.
As an additional advantage, plants outfitted with a pretreatment plasma reactor will be able to purchase far less expensive oils containing high levels of free fatty acids (FFA). Most plants benefit from the ability to purchase less-refined soybean oil and take advantage of the other benefits of this technology. This is because the plasma reaction works equally well for acid esterification as it does for transesterification.
To accomplish this effectively, we have developed a selfcontained mobile testing unit. This unit will allow plants to see the technology firsthand in the comfort of their own facility. The mobile testing unit exists in an enclosed trailer, allowing multiple feedstock product samples to be run on site and tested in the plant’s laboratory for comparison.
The future of biodiesel is here, and it’s time to invest in today’s technology. Our confidence is high that Plasma Blue technology expands possibilities and will be a game changer for the biofuels industry. In an ever-changing industry where each penny matters, this technology will help your facility increase profitability through growth and cost reduction.
Author: Tom Slunecka CEO, Plasma Blue 507-720-4052 tom@plasma-blue.comThe biofuel industry’s ability to trace feedstock has long been hampered by complex supply chains, data-collection challenges, and feedstock suppliers’ reluctance to share confidential business information (CBI) with producers downstream. Yet now more than ever traceability is critical, not just for compliance but also to demonstrate the lifecycle benefits of biofuels within a competitive marketplace. Technology isn’t just a part of the solution for end-to-end feedstock traceability—it’s the only solution.
Our technology, Veriflux, traces separated food waste and other biogenic fats, oils and greases such as used cooking oil (UCO) from collection to the producer, across domestic and international supply chains. It captures real-time data on greenhouse-gas (GHG) emissions while navigating complex supply chains, overcoming data-collection challenges and maintaining data entitlements and integrity.
We achieve this by leveraging the power of technology to solve challenges inherent in feedstock traceability. If your supplier workflows aren’t digitized, our intuitive web portal, easy-to-use mobile application and supplier-centric functionality help incentivize adoption. Our anonymization approach enables data sharing while protecting CBI, ensuring records are made available to regulators and auditors without
compromising competition. Our data-sharing framework prevents duplicate assignment and reuse of records, giving biofuel producers confidence in record authenticity. With realtime data sharing, Veriflux allows producers to access present and historical feedstock-recordkeeping data, minimizing timebased audit uncertainties.
Our technology not only enables traceability but also enhances business operations and advances sustainability objectives. For example, Veriflux’s collection-route optimization feature leverages Veriflux data with state-of-the-art machine learning to recommend the most efficient UCO collection routes, resulting in reduced mileage and fuel consumption, cost savings, lower GHG emissions and better carbon-intensity scores.
Technology is the only solution to the feedstock-traceability challenge, and that solution—Veriflux—is feasible and used globally today.
Author: Dani Charles Co-founder, Veriflux 720-838-7233 dani@veriflux.ioUsed cooking oil (UCO) theft is nothing new. Ever since the material, which at one time restaurants paid to get rid of, became sought after as low carbon-intensity (CI) feedstock to produce biodiesel and, more recently, renewable diesel and sustainable aviation fuel (SAF), there have been unsavory characters stealing in the dark of night what isn’t theirs to make a fast, illegal buck. But a recent case of UCO theft in New York implicating a highly respected biodiesel producer in Pennsylvania, along with salacious allegations of fraudulent UCO exports and doubtfully innocently “mislabeled” wastebased biodiesel produced from contentious palm oil instead of byproducts, have once again brought the high-profile specter of shame on these otherwise noble sectors.
collectors we know or historically from aggregators or brokers with strong reputations.”
Peterson says the company unknowingly bought two 46,000-pound truckloads of this stolen oil. This sounds like a lot, but on any given day Hero BX can process an average of 45 truckloads of oil.
“As far as I know, both we and the aggregator are in the clear,” says Peterson when asked whether Hero BX will be in any trouble for innocently purchasing stolen UCO. “We had an initial interview with Homeland Security, and we walked through our process with them. They asked, ‘How would you ever know?’ and we agreed.”
According to companies like Veriflux and Reiter Software, which offer feedstock-traceability platforms, there are new ways to know.
“Our software addresses this a few different ways,” says Dani Charles, co-founder of Veriflux. “One is traceability start to finish, not just for UCO collection but all the way down the supply chain to the producer.”
Using the Veriflux system, a producer can log in and see where their product is coming from and how much. “When you have that visibility from the database side, we can reconcile irregularities,” he says. “Also, there’s higher fidelity data like GPS, determining a collector was where they said they were and when, and whether they are the validated collector for that particular restaurant.”
This April, six individuals were arrested and charged with conspiracy and the transportation and sale of stolen UCO in interstate commerce. According to the complaint, the defendants conspired to commit a series of UCO thefts from numerous restaurants in and around Monroe County, New York.
A year ago, in April 2022, police encountered several of the defendants pumping UCO in the middle of the night out of privately-owned holding tanks and into box trucks equipped with storage tanks. The deputies followed the box trucks to warehouses in Rochester, New York, where they observed the defendants offloading the oil.
During the execution of search warrants, deputies found more than 12,000 gallons of UCO worth over $73,000. Discovered records showed that the stolen oil was sold and shipped to a biodiesel refinery in Erie, Pennsylvania. Investigators traced two specific oil shipments of 95,320 pounds from the defendants’ warehouse in Rochester to the Pennsylvania plant. The defendants were paid $60,051 for these two shipments, or roughly $4.70 a gallon.
Chris Peterson, president of Hero BX, confirmed with Biobased Diesel™ that this plant in Erie, Pennsylvania, was in fact his facility. “We had no idea that the oil was stolen,” Peterson says. “It was purchased through one of our largescale aggregators. It is our policy that we only buy directly from
Kristoff Reiter, CEO of Reiter Companies, says there are a few different technology offerings this year. “The problem is that when oil’s worth $3.50 to $5 a gallon, it’s worth thieves’ time to make up records,” he says. In that case, what becomes important is analysis of the associated metadata to gauge the record’s authenticity. “How far apart were the data-entry intervals, were devices GPS-confirmed at those locations, does this data fall in line with standard data?” Reiter says. “Those are things we look at to rate a record’s quality and legitimacy. It’s the analysis that creates more security.”
It’s well known that organized crime is embedded in the UCO trade. Sources say the business model of these syndicates is simple: They build large oil-processing plants in major cities through which “every Tom, Dick and Harry” can offload hundreds or thousands of gallons of stolen (“dirty”) UCO, and the plant turns around and sells it as legitimate (“clean”) feedstock. It’s a UCO-laundering scheme, basically. As a cover, some players have a few legitimate accounts, but it’s never close to the volume they’re selling. “Everyone knows the game, but their oil keeps moving with enough plausible deniability,” one source says.
In February, the International Council on Clean Transportation issued a whitepaper on potential fraudulent UCO exports from Asia to the U.S. due to demand for low-CI feedstock created in American low-carbon fuel policies.
“It is important to remember that the physical and chemical nature of waste oil and drop-in hydrotreated fuels makes it possible to disguise virgin vegetable oil as waste oil,” ICCT stated. “Indeed, there have been documented cases of wasteoil fraud in the United States [and Europe] already … UCO is nearly indistinguishable from virgin vegetable oil and it is difficult for auditors to detect fraud using chemical fuel testing.”
The ICCT report notes that Asian countries export most of the world’s UCO. “While import volumes fluctuate annually, the UN Comtrade Database shows that approximately 15 percent of the UCO imported by the United States comes from Asia.”
Future import demand from the U.S. and other locations such as Europe will likely exceed the potential for genuine UCO exports from Asia, the report states. “We estimate that U.S. policy incentives could promote the import of 8.9 million metric tons of UCO into the United States in 2030 due to the [3-billion-gallon by 2030] SAF [Grand Challenge] mandate alone. That is a sizeable amount compared to the UCO that we estimate is currently collected in [China, India, Indonesia, Japan, Malaysia and South Korea], which is in the range of 3.7 million to 5 million tons.”
It should be noted that ICCT advocates for the capping of how much UCO and animal fats should be allowed under certain biofuel policies, a move that many in the industry do not support, but which the organization believes will help curtail fraud.
Reiter says there’s a lot of “UCO” containers entering the U.S. from China that aren’t actually UCO. “Everyone I know in this business gets calls offering these containerloads,” he says. “The quality on them is way too good to be UCO, with 2 percent free fatty acids and an iodine value that is exactly that of palm oil.”
In April, the International Sustainability and Carbon Certification system issued a notification about communications from stakeholders expressing concerns over a surge of “advanced biodiesel”—or biodiesel made from EU-approved waste feedstocks—imported from China “and produced from waste and residue materials that are at least partly supplied from Indonesia and Malaysia.”
This sharp increase began late last year and peaked this February, ISCC noted, “with serious implications for the European biofuels market and indications pointing to a potentially dubious or fraudulent origin of these trade flows.”
While biofuels made from virgin palm oil are not allowed under U.S. and EU biofuel programs due to sustainability issues and deforestation perceived to be linked with palm-oil plantations, byproducts from palm processing, such as palm oil mill effluent (POME), may qualify as waste under some policies. But what ISCC points out is that some of this “waste-based biodiesel” coming to the EU from China is labeled as having been manufactured in part from POME originating in Indonesia or Malaysia but instead may be made from palm oil.
“ISCC has already intensified its work on mitigation measures,” the organization stated. “As a result, ISCC’s integrity program has focused on Asia since last year and additional integrity assessments have been conducted at points of origin.”
Part of the fortified requirements include a designated selfdeclaration for POME oil, a mandatory 100 percent audit for
respective points of origin and guidelines for plausible yields. The idea behind this is a palm-oil mill processing X tons of palm should only theoretically be capable of producing Y tons of POME. If POME yields exceed plausible limits, then this is a red flag.
“Implausible quantities of material … that cannot be verified by the auditor will be considered as a critical nonconformity and will result in withdrawal of the certificate,” ISCC stated. “False declaration of materials on sustainability declarations will be regarded as a critical nonconformity subject to certificate withdrawal, and further measures regarding points of origin will be implemented.”
The organization added that, “Since [March], after being alerted to certain players suspected of committing fraudulent activity, we immediately carried out unannounced integrity audits at the companies concerned,” ISCC stated. “In a second step, we are conducting a further 70 unannounced integrity audits at processing units in China and Singapore.”
Charles says, “What makes this so tough is how complex the supply chain is, which also makes designing software difficult. In some cases, supply chains are linear while others involve aggregators, multiple processors, and multiple collectors rolling under those processors. If there’s a bad actor upstream, even a small one, then you’re running the risk of this rolling down to the producer.”
Optimists can see the good in these unfortunate incidents. “It’s bad that it’s happening, but it’s good because there’s more market awareness,” Charles says. “What makes it so challenging is there’s just so much feedstock and collection points—20,000 or 30,000 tons of UCO alone can reflect 50,000 to 60,000 points of origin. That’s a lot of data. That’s why it’s hard to facilitate endto-end traceability. The only way to do it is with software. It isn’t a solution, it’s the solution.”
In general, some feedstock records might look imperfect because they’re occasionally missing some metadata, but should they be excluded flat out? “No,” Reiter says, “because there are also in-betweens. There’s good, imperfect and in-between data. So, our system (Reiter Software’s Cooking Oil Service Tier, or COST) will work more like a credit market with triple As, single As, double Bs. Records will have a rating. I plan to define and publish the criteria by which we will score them, to be transparent.”
Other than criminal actors, most stakeholders in this space are well-intentioned, Charles says. “They understand [these incentives and credits come from] taxpayer dollars, so collectively we need to move the industry forward with more transparency around this, and more data sharing,” he says. “But actual implementation is the challenge. You need to have buy-in from industry and government. With better traceability, however, theft and fraud will ultimately be eliminated by market dynamics and enforcement. But it’ll take time to get there. We just need to have the patience to work collectively.”
Author: Ron Kotrba Editor, Biobased Diesel™ 218-745-8347Crown’s recently completed Liquids Pilot Plant offers customers access to a state-of-the-art continuous-process environment.
As the world decarbonizes transportation fuels, the role of liquid biofuels will expand. The production of renewable diesel within the U.S. has risen dramatically in the past few years, and that growth is expected to continue. The latest announcements of new investments in biobased diesel and sustainable aviation fuel (SAF) have one thing in common: They are all focused on innovation. Many of these ventures are describing new technologies or processes, while others are keying in on new feedstock choices. The biofuels industry is turbocharging the need for novel oilseed crops and new ways to create value from waste oils. The importance of innovation in biofuels is clear.
Crown has been innovating in the oilseed-processing industry for over half a century. And, in the past several
years, we have invested significantly in our commitment to innovation. In 2019, Crown moved its headquarters to a new purpose-built office in Blaine, Minnesota, with a 15,000-square-foot Global Innovation Center.
earlier trials produced crude vegetable oil from oilseeds, Crown can now pretreat those oils and fats to make them RD Ready™ to produce SAF, renewable diesel (also known as HVO) or any other biofuel. The pretreatment portion of the pilot
Shortly after moving into the new space, Crown commissioned and began processing a variety of oilseeds and other materials in the Global Innovation Center. The new pilot plant operates much like a full industrial-scale plant, where the seeds are received, cleaned and prepared before moving to the solvent-extraction building. Then, the desolventized meal can return to the preparation building for further processing. This new piloting capability has been essential for Crown’s clients who work with plant-based proteins and other specialty-extraction processes. For the renewable fuels market, Crown is working with clients to extract vegetable oils for use as feedstocks in renewable diesel and SAF.
Our Global Innovation Center has been and continues to be critical for clients who want to try new things, to process traditional oilseeds in new ways, or to step outside oilseeds altogether. Their reasons for choosing to pilot with us are varied. In some cases, it’s all about process development. In other cases, it simply creates enough product volume to aid in identifying and developing a market.
Crown’s most recent addition to the Global Innovation Center focuses on renewable fuels pretreatment. While
plant performs the same operations as a full-scale Crown pretreatment plant. The system is fully automated and operated from workstations within the control room. During operation, we collect and analyze samples in our fully equipped and staffed laboratory. In many cases, the laboratory analysis helps us adjust parameters as we optimize a pilot-plant run to achieve specific objectives.
Perhaps the aspect most relevant for the renewable fuels space is risk mitigation. As renewable fuel producers look to incorporate feedstocks with lower carbon intensity, the quality of the pretreated feedstock must be preserved. Commodities such as waste cooking
oil and other nontraditional streams have a wide variety of contaminants depending on their origin and path to the pretreatment plant. Strategies for removing these contaminants can be tested, validated and documented with the pretreatment pilot plant. This type of risk mitigation is invaluable for the success of a project.
Crown’s pilot plant also provides excellent opportunities for training. It’s possible to see and interact hands-on with equipment like that in full-scale plants. The pilot-plant experience can be further enhanced with classroom education and access to our seasoned engineers and technicians.
Crown’s Global Innovation Center and renewable fuels pretreatment pilot plant is fully operational, and we are adding even more capabilities. We are finishing installation of a tower that includes a full deodorizing column to complete our edibleoil piloting capabilities. The tower includes a fat-splitting column and a distillation column for fatty acids or methyl esters. These unit operations give us several tools to choose from as we
look to maximize contaminant removal from raw materials. We expect to commission these columns later this summer.
These processes and equipment are already generating new knowledge and discussions, but there is more to do. As Crown continues along the path of innovation, we will create additional tools. Our R&D team already has plans and the space to add yet more equipment and processes. New feedstocks, novel oilseeds and creative startups in the industry will push all of us to advance.
Lead the oils and fats processing industry with total con dence in your investment.
Had Kenlon Johannes never had his “feathers ruffled” by a research paper more than 30 years ago, the biodiesel industry of today may have never materialized. So claims Alan Weber, an agricultural economist and M4 Consulting Inc. co-founder and partner, who jokes that the former Missouri Soybeans executive director reading a research paper about developing canola biodiesel was all it took to start “this whole thing.”
The use of vegetable-oil fuel in compression-ignition engines goes all the way back to the late 1800s and Rudolf Diesel himself. However, the U.S. crudeoil boom in the early 20th century led to cheap and abundant distillates, sidelining the development of vegetable oil for fuel.
Not until the energy crisis of the 1970s would curiosity in fuel alternatives be reinvigorated in America and abroad. Thanks to Martin Mittelbach at the University of Graz in Austria, who thought the molecules of vegetable oils were too bulky, esterified rapeseed and, later, used fryer oils, were showing much promise as a better pathway to new diesel-fuel alternatives. In the U.S., researchers including Chuck Peterson at the University of Idaho and Carroll Goering at the University of Illinois also began to better understand how vegetable oils could be used as fuels.
The central problem with vegetable oil was that it gummed up engines after prolonged use. Transesterification with alcohol and a catalyst produced fatty acid methyl esters (FAME) or fatty acid ethyl esters (FAEE). This eliminated the problem of gunked-up engines while providing lubricity, an attribute that would greatly benefit the movement in years to come.
By Ron KotrbaWhat Johannes started, of course, was the U.S. biodiesel industry. It provided soybean farmers with a high-volume, value-added use for the mounting stocks of soybean oil accumulating across Missouri and the broader Midwest in the late 1980s and early 1990s. Voluminous oil surpluses were a drag on the whole soybean market, depressing farmgate prices. Food uses for soybean oil—mayonnaise, salad dressing, deepfrying oil and the like—only consumed so much. Something had to be done. And Missouri Soybeans, with Johannes’ leadership, did it.
Research persisted throughout the 1980s. In 1991, when Johannes heard
this new canola-based “biodiesel fuel,” he had a vision of what could be
fatty acid
(FAME), better known today as “biodiesel,” owes its storied existence to forward-thinking Missouri soybean farmer-leaders.With a $22,000 investment, Missouri Soybeans funded a research project by Leon Schumacher at the University of Missouri. The researcher would test and demonstrate this esterified soybean oil as a dieselfuel replacement in a new Dodge pickup. Schumacher is pictured with that truck, “Old Goldie.” PHOTO: MISSOURI SOYBEANS Kenlon Johannes, left, is credited for starting the U.S. biodiesel industry when he was executive director of Missouri Soybeans. In October 1991, he welcomed Tom Verry, right, to the Missouri Soybeans team as the organization’s new field services director. The two are pictured here in 1992 at a St. Louis alternative-fuel promotion in front of the old Busch Stadium with “Old Brownie,” a famed 1992 Ford F250 that ran on biodiesel. PHOTO: MISSOURI SOYBEANS about
possible for his constituents and their soybeans: soy diesel. With a $22,000 investment, Missouri Soybeans funded a research project by Leon Schumacher at the University of Missouri. The researcher would test and demonstrate this new esterified soybean oil as a diesel-fuel replacement in a new Dodge pickup. Although Goering in Illinois had been testing esterified soybean oil, the fuel hadn’t been tested in real-world conditions.
Next, Johannes approached serial entrepreneur Bill Ayres, who had been tinkering with biodiesel in Kansas City, and his longtime friend and partner Doug Pickering to see if they’d be interested in making fuel for the project. Ayres ultimately agreed, and the seeds of an American biodiesel industry took root in a trash-can reactor, sump pump and cone-bottom drums.
In 1992, with funding from members of Qualified State Soybean Boards, Missouri Soybeans formed the National Soy Fuels Advisory Committee to further investigate what was needed to get a U.S. soy-diesel industry off the ground. Information Resources Inc. was contracted to provide a plan to develop markets and the technical proof, specifications and education needed to build an industry. An important takeaway from this report was that a trade association must be formed to establish the soy-diesel sector in America.
In less than a year, the National Soy Fuels Advisory Committee was disbanded to form the National SoyDiesel Development Board. The NSDB was organized with more than a half-dozen states as charter members, each contributing $10,000. Johannes stepped down from Missouri Soybeans to chart the course for the new association, which was tasked with creating a new fuel industry, markets, technical specifications, policy support, and all the testing and demonstrations to buttress these developments.
The new NSDB, which formed in late 1992, didn’t spread its wings and fly the nest, though. Rather, it occupied office space in the basement of Missouri Soybeans and was co-located with its “parent” organization for many years in Jefferson City. Johannes continued to secure funding, a major portion of which came from the United Soybean Board.
Interest in soy diesel was growing at a fast clip. Ayres and Pickering secured demonstrations with the St. Louis Lambert International Airport, cooperatives, city bus fleets, boaters and even the Sunrider expedition that circumnavigated the globe. Ayres and his company, Interchem, had plans to build a production facility in Kansas City. Scaled at 2.1 million gallons per year, it would have been the nation’s first dedicated soydiesel plant. However, when Ayres learned a nearby Proctor & Gamble plant was already making methyl esters, plans for the new facility were scrapped. P&G began providing FAME for testing and the growing list of demonstrations.
It was around this time that a great nexus took place as those who would become major players in biodiesel would connect. Gary Haer—who would later become a superstar with Renewable Energy Group (REG), renowned for door-to-door sales of 5-gallon pails of biodiesel—was hired by Interchem. John Campbell of Ag Processing (AGP), who greatly influenced biodiesel policy, attended Ayres’ plant kick-off ceremony for the facility that never came to be. Interchem and what became Midwest Bio-Fuels eventually struck deals with both AGP and West Central Cooperative, the roots of REG, to build what are considered the first dedicated U.S. soy-diesel plants in Iowa.
Another important person in the biodiesel community also intersected with Ayres and Interchem early on: Missourian Steve Howell. Working for Stratco at the time, Howell became immersed in biodiesel. He shared ideas, engineering plans and a FAME pilot plant with Interchem and Ayres. Eventually, Howell and Weber formed MARC-IV (now M4), which stands for “market analysis, research and consulting.” Howell worked to secure a fuel specification, a yearslong battle that eventually culminated in ASTM D6751 in the early 2000s.
Ayres also did business in the mid- to late 1990s with Gene Gebolys, founder of World Energy, which, years later, became one of the largest pureplay biobased diesel producers in North America. Gebolys, who many considered tenacious and relentless, was a young up-and-comer in the biodiesel world. He respected what soybean farmers brought to the biodiesel table. According to Ayres, he was selling Gebolys biodiesel and fronted the young go-getter volumes when he was struggling.
The pieces of the puzzle of what would become a uniquely American biodiesel industry were being put into place.
In 1994, just two years after its formation, the NSDB made the difficult decision to change its name to the National Biodiesel Board. It did not come without a fight or the possibility of major backlash from soybean farmers, some of whom were skeptical about becoming a feedstock-neutral organization. Those who approved the move realized that if biodiesel took off, they would need everyone and every feedstock onboard to provide the membership funding, political influence, marketing and, of course, the raw materials to see it through.
Johannes eventually stepped down from NBB leadership. Jeff Horvath led the organization for a few years until another Missourian, Joe Jobe, NBB’s chief financial officer, took the helm and guided the organization for 15 years.
It was about this time that the all-important health-effects testing was underway, a necessary step toward biodiesel becoming a legitimate fuel in the U.S. per EPA requirements. After rigorous testing and millions of dollars, biodiesel obtained its legitimacy. Biodiesel producers could either go through the time and expense of doing the same, or join NBB and be given access to the data. This began a period of expansive growth for the Missouri-born national trade association and the industry it represented.
In the late 1990s, the USDA, in cooperation with the National Renewable Energy Laboratory, performed a lifecycle analysis (LCA) on biodiesel that turned out to be one of the most comprehensive LCAs ever performed. The study cemented biodiesel’s position as a sustainable, “green” fuel that significantly reduces greenhouse gases, criteria pollutants such as particulate matter and provides a positive energy balance.
This was an important milestone. When soybean farmers set out to develop biodiesel, carbon reduction wasn’t even on the
radar. Now, the most comprehensive LCA in existence showed biodiesel significantly reduced carbon emissions compared to petroleum diesel.
Still, the industry of biodiesel production was largely undeveloped. After nearly a decade of lobbying, a $1-per-gallon tax credit was implemented in 2005, and everything changed. In 2007, the second installment of the federal Renewable Fuel Standard was signed into law. It included categories for advanced biofuels and biomass-based diesel. Although it took a few years to go into effect, the policy provided domestic demand after Europe imposed hefty tariffs on U.S. biodiesel, which was the major market for American biodiesel at the time. Since then, the biodiesel industry has grown to a national capacity of more than 2 billion gallons annually. Missourians including Johannes, Weber, Jobe, Howell and others helped fulfill a vision that soybean leaders had to develop, grow and
“The pieces of the puzzle of what would become a uniquely American biodiesel industry were being put into place.”
sustain a high-volume, high-value commercial industry to provide an outlet for soybean oil.
Interestingly, when biodiesel was being developed in Missouri, increasing energy independence and bolstering rural economies and farmgate prices were definite goals. When the fuel’s ability to reduce criteria emissions such as carcinogenic particulate matter was discovered, it was seen as a tremendous benefit to urban communities in fleets like transit buses.
Once the comprehensive LCA was completed in the late 1990s, another important societal attribute was added to biodiesel’s repertoire. Its ability to cut greenhouse-gas emissions from the hard-to-decarbonize heavy-duty sectors was recognized. Today, whole sectors, such as the heatingoil industry, are relying on biodiesel to sustain existence in a carbon-constrained world.
In 2022, the National Biodiesel Board celebrated its 30th anniversary. With the milestone came a new name and an expanded vision. As Clean Fuels Alliance America, the association will further grow its reach into Canada and now include biodiesel, renewable diesel and sustainable aviation fuel (SAF).
Virtually all growth and interest in the biobased diesel sector during the past few years has been in renewable
Missouri is the leading soy-based biodiesel producer in the nation. Biodiesel is a renewable, energy-efficient, clean-burning fuel made from Missouri’s top agricultural commodity- soybeans. Ask for it where you buy fuel.
diesel and SAF. The U.S. Energy Information Administration forecasts that the U.S. renewable diesel sector alone will hit more than 5 billion gallons of productive capacity by next year. That doubles what the biodiesel industry took 30 years to build—and only in just a small fraction of the time. Meanwhile, through its SAF Grand Challenge, the federal government is pushing for domestic SAF production of 3 billion gallons a year by 2030 and 35 billion gallons a year by 2050.
The ability of renewable diesel and SAF to grow would not have been possible without the three decades of groundwork laid by biodiesel, NBB and the vision of Missouri soybean farmers. Where the next 30 years will take the Missouribased association and the industry it built is unknown. However, the future appears to be one that will leverage the significant environmental, health, economic, agricultural and energy-security benefits of biodiesel, renewable diesel and SAF for the betterment of society and the climate.
Author: Ron Kotrba Editor, Biobased Diesel™ 218-745-8347 editor@biobased-diesel.comThere is a lot of talk about what the circular economy is, but there is much less understanding of how community-scale biodiesel production is the concept’s poster child.
By Kelly KingI’ve had the honor of being a delegate to and presenting at the past two United Nations Conference of the Parties—COP26 and COP27—representing at these global climate-change conferences as a local elected official specifically from the island state of Hawaii, the most isolated population on the planet and a glaring example of vulnerable island communities feeling the heat on the front lines of the climate crisis.
On this world stage where local and international leaders converged to discuss climate action, there was not a lot of talk—and sadly even less action—when it comes to supporting biodiesel’s role in climate solutions. There was a virtual void of voices about community-based biodiesel and its abundant benefits as part of the circular economy.
The circular economy is not a new concept. Rooted in the mantra of “think globally, act locally,” it is the essence of true sustainability. The circular economy is about finding unique resources in your own community, using those resources to provide local jobs creating local products and services, and maintaining the economic and environmental benefits such as taxable revenue, environmental protection, energy and food security. The circular economy brings climate action into the local equation alongside basic needs like farming, food production, clean water and housing.
Since COP26, there seems to be more buzz around the circulareconomy concept, but clearly not much understanding about what it means—especially when you see world leaders singularly focused on wind, solar and batteries as the only solutions to fighting the catastrophic consequences of greenhouse-gas (GHG) emissions. There is not a “one size fits all” silver bullet. Batteries, for example, rely on an extractive manufacturing process by global corporations—raw materials are mined in one country while batteries are produced in another and shipped for manufacturing of vehicles to yet another country. It seems easy to confuse with the global economy, but just because the world is round doesn’t mean it’s a circular economy.
Extractive renewables leave us vulnerable to catastrophic world events, natural disasters and other supply-chain disruptions that can sever our energy and food supply. It is shortsighted and dangerous to ignore locally produced biodiesel and other biofuels. We must have a balanced, diversified portfolio of renewable energies to face whatever the future brings.
I currently serve as a board member of ICLEI-Local Governments for Sustainability, a global network of more than 2,500 local and regional governments committed to sustainable urban development. At the recent ICLEI “Cities Summit of the Americas” in Denver, Colorado, the focus was on “promoting regional cooperation and uniting subnational leaders from
government, civil society, business, academia, youth, culture and the arts, and indigenous and underrepresented groups.” I met with mayors from our country and other nations including Ukraine. The common thread was a focus on basic needs— fighting climate change while focusing on local food production, clean water, housing and jobs.
The brightest glimmers of hope in the fight against climate change are at the local level. Collaboration among cities and counties around the world is where sustained climate action is taking place. While national leaders play politics with renewable energy policies, local leaders are rolling up their sleeves, learning from each other and taking action. Maui County has recently passed ordinances regulating plastic and chemical pollution, mandating net-zero energy home construction as well as benchmarking county facilities to reduce water and energy use. Moving far faster than the state of Hawaii in our environmental goals, our previous council also took action in reducing harmful outdoor lighting and restoring wetlands that are our first defense against flooding.
This is where community-based biodiesel and its role in the circular economy becomes crystal clear.
Community-based biodiesel is the poster child for the circular economy. My husband Bob King and I founded Pacific Biodiesel with this model in 1995 on Maui, where we created the first retail biodiesel pump in America. We first produced biodiesel by recycling used cooking oil from local restaurants—and still do. Today we’re expanding our local feedstock through agriculture, using regenerative-farming practices to grow crops like sunflowers to produce culinary oils for local restaurants and consumers, which also supports food security in Hawaii. Coming full circle, we then recycle the used cooking oil for production of our premium distilled biodiesel sold entirely in Hawaii, creating local jobs, revenue and energy security for our island state.
In the very early days of Pacific Biodiesel, we were small and grassroots, attracting values-driven people excited to support locally produced biodiesel. Supporters and celebrity friends, including Woody Harrelson, Willie Nelson, Darryl Hannah, Jack Johnson and Paul Mitchell founder John Paul DeJoria made biodiesel sexy and have been eager to highlight our communitybased model, which brings benefits directly to our communities. They believed in us because our local biodiesel story was pure and real. It made a tangible local impact. It touched local lives and cleaned up our local environment. We were real people making this innovative, clean fuel for our local community. Farmers and conscientious consumers like to say it’s important to know who’s growing your food. With Pacific Biodiesel, our customers know their local fuel producer. I can’t count all the times I’ve been thanked by customers for providing them with a cleaner, more-environmental alternative to fossil diesel.
Today, Bob and I are also farmers. Our Maui sunflower farm has become a symbol for our circular-economy story here in Hawaii—attracting a new wave of supporters. This Earth Day, we hosted our Sunflower Farm Music Fest at our farm—an all-day live-music event focused on raising funds and awareness for Hawaii’s food hubs that are supporting local farmers to increase local food production. The event’s good intention to support this important, local cause caught the eye of multiplatinum music producer and owner of Licorice Pizza Records, Kerry Brown, who owns a home on Maui and immediately understood the urgency of the food-security issue here in Hawaii. A drummer who once performed with The Smashing Pumpkins, Kerry enthusiastically joined our concert lineup as headliner to help us expand our impact—and announced he’d produce a vinyl record of the day’s live music and donate one to every ticket purchaser.
This example reinforces the power of the circular economy— local farming, local food, local biodiesel, local jobs. Local keeps it real. People can participate and benefit directly. Because it also motivates folks to stand up and get involved, local is what we need to fight climate change.
In the biodiesel sector, we can overcome the greed that feeds the “bigger is better” corporate instincts. We need to be consistently beating our drum about the multitude of benefits community-based biodiesel brings in the race to reverse the impacts of the climate crisis. In 2007, Willie Nelson, his
wife Annie, Darryl Hannah and I created the Sustainable Biodiesel Alliance to help the small, local producers struggling to remain viable in a world where venture capitalism seeks to conquer and centralize all promising new industries. We were focused on realizing the intended beauty of communitybased biodiesel—that we can create clean energy in our own hometowns for our own people and do our part to reduce fossil-fuel emissions.
Local biodiesel is integral to the circular economy. So many are struggling these days to make ends meet—it’s hard to even contemplate climate mitigation when you can’t find housing and don’t know how you’ll feed your kids next month. Community-based biodiesel gives power to local communities, literally and figuratively, and it connects with the basic needs that folks must consider in their daily lives. Whether or not you believe in the science of climate change, the benefits are increasingly clear: You can change your fuel even if you can’t afford to change your car, and you can support local, green jobs as well as energy and food security. Collectively, we can leave a sustainable, cleaner environment for the next generation to enjoy.
At Pacific Biodiesel, we have been steadfast in our community-based mission for nearly three decades. And now, as farmers on Maui, Bob and I are beginning to realize our vision of full-circle sustainability. We hope our country’s state and federal governments continue to support our grassroots intentions, even as President Biden pours billions of dollars into hydrogen and electric vehicles. As our government continues to explore and fund new technologies, remember the strongest renewable energy portfolio is as diverse as the people of America.
Author: Kelly King Co-Founder, Pacific Biodiesel ktk@biodiesel.comThe commissioning of three new plants in less than a handful of months marks a milestone for the decade-and-a-half-old “new” biodiesel technology.
By Ron KotrbaBDI-BioEnergy International, the Austrian biodiesel processtechnology provider and plant builder whose pioneering achievements in waste to fuels supercharged the global industry after its inception in 1996, is still going strong after all these years.
In fact, 2022 was a banner year for the nearly 27-year-old company—and its RepCat technology.
RepCat is short for “repeatable catalyst,” meaning the catalyst used to esterify and transesterify fatty acids and triglycerides can be used over and over again, unlike
homogeneous catalysts such as sodium or potassium methylate. Recycling the catalyst significantly reduces operating costs for biodiesel producers.
BDI developed its RepCat technology for processing raw materials with a high proportion of free fatty acids (FFA). This innovative process can effectively handle raw materials containing up to 99 percent FFA.
The RepCat process has been positively evaluated for the use of high-risk fats (definition according to EU Regulation No. 1069/2009) by the European Food Safety Authority.
An additional advantage of RepCat compared to other industrial processes is the production of absolutely salt-free glycerin of distilled quality.
Adoption of new technologies is often slow in the beginning, as companies that could benefit from them remain satisfied with existing processes and the status quo. Market conditions at the time the technology was developed also may not warrant adoption. But over time these customer attitudes and market conditions change.
For instance, BDI first patented its RepCat technology in 2006. A year later, the company oversaw commissioning of the first industrial RepCat biodiesel plant in Arnoldstein, Austria.
This time period was at the height of the biodiesel boom in the U.S. and many projects were focusing on using virgin crop oils such as soybean oil or, in Europe, rapeseed oil as feedstock. These clean feedstocks feature very little FFA, and distillation of the resulting biodiesel fuel was seldom thought to be necessary then.
But having been engrossed in the market at that point for 10 years and operating its business around the motto “from waste to value,” BDI could gauge where the market was eventually going.
“2022 was the most successful year for this prevailing technology, with three RepCat plants having been commissioned,” says Hermann Stockinger, BDI’s chief sales officer.
Last March, BDI announced the opening of a RepCat plant commercially scaled at 15 million gallons per year (mgy) in Komárom, Hungary, operated by Rossi Biofuel, a subsidiary of Envien Group. The Envien Group is one of the largest groups of companies in biofuels production in Central and Eastern Europe and is also one of the most important agricultural groups in Central Europe.
One month later, in April, BDI shared that its first RepCat biodiesel project in the U.S. came online at the Crimson Renewable Energy plant in Bakersfield, California. The new RepCat production line added 13 million gallons of annual production capacity to Crimson’s existing biodiesel plant, which combined can now manufacture more than 37 mgy.
Then in June, BDI revealed Cargill’s new RepCat plant in Ghent, Belgium—the biggest RepCat facility to date scaled at 35 mgy—started operations. The Cargill project itself was a major milestone for BDI considering it is one of the largest waste-to-biofuel facilities in Europe. The project is also BDI’s largest assignment in the company’s long history. Also, while Cargill has several biodiesel manufacturing facilities around the world, this new one in Ghent, Belgium, is its first making biodiesel from waste materials and is co-located at an existing oilseed-crush and biodiesel complex.
“I had the pleasure of being present at each of the three commissionings and was thus able to get to know the technology better in its ingenuity and simplicity,” says Christine Riedl, BDI’s technical sales manager. “Raw-material sourcing will become a big issue in the future because different industries use waste oils and fats. With our RepCat process, various types of raw materials—even those with up to 100 percent free fatty acids—can be processed, providing high flexibility for our customers.”
More than 15 years later, the renewable diesel boom is contributing to a run on virgin vegetable oils, animal fats and used cooking oil, all of which have traded at record or nearrecord highs in the past two years—leaving some biodiesel producers to consider low-grade materials they once thought untouchable, such as trap and sewer greases and high-risk animal fats, for instance.
The market conditions were ripe for technological change in the biodiesel sector. Well-known, established plant owners saw this and became convinced there could be a better way.
The spring of 2022 was a milestone period for BDI in terms of commercial deployment of its RepCat technology, with three official RepCat biodiesel plant start-ups on two continents in four months.
Building on BDI’s history of more than 25 years in development of biodiesel, multifeedstock and retrofit technologies, the RepCat process has indeed finally come of age.
As Stockinger notes, 2022 was the most successful year so far for the RepCat technology. “But 2023 looks to be equally promising,” he says, “so stay tuned!”
Author: Ron Kotrba Editor, Biobased Diesel™ 218-745-8347 editor@biobased-diesel.com>70 international biodiesel reference projects
for highest yield
measurable solutions for
customized perfection CO2 reduction