Industrial Automation
Risparmio energetico
La nostra guida sul risparmio energetico nei sistemi ad aria compressa
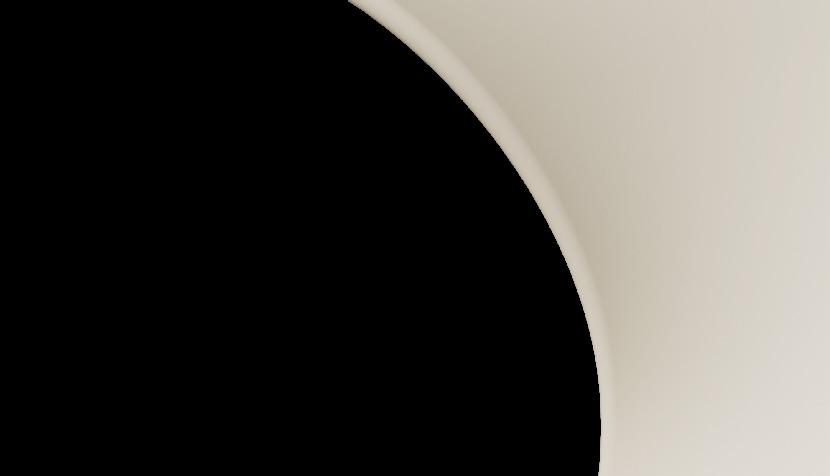
Breakthrough engineering for a better world

Risparmio energetico
La nostra guida sul risparmio energetico nei sistemi ad aria compressa
Breakthrough engineering for a better world
Progettiamo soluzioni innovative che rendono fabbriche e linee di produzione più sicure, produttive e sostenibili. I nostri sistemi di movimentazione pneumatica ed elettrica consentono a OEM ed end user in tutto il mondo di automatizzare e ottimizzare i processi produttivi.
Da oltre un secolo collaboriamo con clienti nel settore dell’automazione industriale.
Le nostre soluzioni sono utilizzate in un’ampia gamma di industrie: Automotive, Food and beverage, Farmaceutico e persino nel settore Aerospace.
Per la trasformazione digitale dell’industria offriamo soluzioni di prodotto ad alte prestazioni ed elevate connettività, innovando costantemente in stretta collaborazione con i nostri clienti.
I nostri prodotti migliorano efficienza e performance, riducono i tempi di fermo impianto e garantiscono un risparmio energetico.
Grazie all’aumento della produttività, dell’efficienza e della sicurezza, i nostri clienti possono servire meglio i loro clienti e risolvere le loro sfide di automazione più complesse, oggi e domani.
La gamma comprende rinomati brand quali IMI Norgren, IMI Bimba e IMI Bahr.
Soluzioni ingegneristiche innovative per un mondo migliore.
Si presume spesso che l’aria compressa sia una fonte energetica poco costosa o perfino gratuita. Non lo è.
Un normale sistema da 500 litri/sec avrà un consumo di circa 40 mila sterline di energia elettrica all’anno. Durante il suo ciclo di vita, l’energia rappresenta il 75% del costo totale di acquisto e funzionamento di un compressore. Numerosi studi indipendenti confermano che nel settore industriale si spreca circa il 30% dell’aria compressa prodotta, equivalente a circa 12.000,00 sterline in un comune sistema da 500 litri/ sec. L’obiettivo di questa guida è aiutare i clienti a ridurre al minimo lo spreco, migliorando i sistemi attuali. Saranno affrontate diverse aree chiave del risparmio, e verranno forniti consigli pratici su come agire.
Per quasi 100 anni la preparazione dell’aria è stata un ambito centrale per la nostra azienda. Questa guida presenta le opportunità principali di risparmio energetico, fornendo consigli pratici su come migliorare l’efficienza del proprio sito produttivo.
In tutta la guida sono presenti esempi dettagliati su come calcolare i possibili risparmi indicati.
Tali esempi sono basati su un modello di fabbrica chiamato “Fabbrica esempio”, che ha molti dei problemi tipici dei sistemi ad aria compressa.
• Dove individuare le possibilità di risparmio
• Cosa osservare o misurare
• I costi
• Quali sono le soluzioni?
• Come rispettare le procedure consigliate?
• Perdite
Le perdite sono la principale causa di perdita di energia dei sistemi ad aria compressa. Un normale impianto può perdere il 20% dell’aria compressa a causa dei collegamenti impropri di tubazioni, raccordi, accoppiamenti, ecc. Risolvere le perdite e introdurre una manutenzione pianificata può generare risparmi considerevoli.
• Uso improprio
La seconda causa di spreco principale di aria compressa è l’uso di una fonte di energia solo perché disponibile. Potrebbero essere disponibili delle alternative migliori per spostare, asciugare o pulire prodotti. Laddove si utilizza l’aria compressa, è fondamentale scegliere l’apparecchiatura corretta come ugelli e circuiti di controllo per ridurre al minimo gli sprechi.
• Pressurizzazione eccessiva
Un notevole risparmio sia di energia sia di usura dell’attrezzatura può essere raggiunto utilizzando dispositivi alla pressione minima necessaria per l’applicazione piuttosto che usare la pressione massima disponibile per la linea. Il semplice uso del regolatore di pressione offre un ritorno di investimento molto veloce.
• Caduta di pressione
La perdita di pressione, causata da elementi filtranti ostruiti e da tubazioni sottodimensionate, può causare una pressione insufficiente nella parte finale delle linee di aria compressa. La guida fornisce esempi su come scegliere ed eseguire la manutenzione dell’attrezzatura per ridurre al minimo i cali di pressione del sistema.
• Energia e sicurezza
I componenti con funzioni di sicurezza, come regolatori preimpostati e valvole di arresto, possono anch’essi essere utili ai fini del risparmio energetico. In questo paragrafo viene esaminata la norma BS EN 983 e altre norme riguardanti l’energia.
• Produzione
La scelta corretta dell’attrezzatura di controllo per configurazioni a più compressori, prestando attenzione al raffreddamento in l’ingresso e dopo il trattamento dell’aria compressa, può produrre un buon risparmio energetico. È di fondamentale importanza la manutenzione regolare e corretta di compressori, filtri e essiccatori.
• Piano d’azione e ulteriori informazioni
Una semplice lista di controllo con azioni e fonti di ulteriori informazioni.
La fabbrica nel nostro esempio possiede un compressore con una capacità di 750 litri/sec, è una richiesta media di 500 l/s. Funziona 24 ore al giorno, 7 giorni su 7, per 50 settimane all’anno. L’energia elettrica ha un costo di £0,10/kWh*.
Al 75% di utilizzo del compressore, il costo totale annuo è di circa £78.400
La base per la gran parte dei calcoli è la “formula dello spreco”.
Questo è il costo associato al flusso di energia:
0,4 x ore x flusso l/s per il costo energetico/kWh.
Nella Fabbrica di esempio, la perdita ordinaria è del 20% e corrisponde a 100 l/s, con il seguente costo:
0,4 x 8.400 x 100 x £0,10 = £33.596
I calcoli di esempio di questa guida sono basati su una sezione della fabbrica, l’area dell’officina.
L’officina è operativa 2500 ore all’anno, ma il circuito dell’aria compressa è sempre pressurizzato quando la fabbrica è aperta. Il risparmio totale individuato è del 30% dell’aria attualmente usata dall’officina.
*Sostituire questo valore con il costo dell’energia locale e con la valuta locale per ottenere un risultato che rispecchi la realtà del mercato locale.
Immagine 1
7 bar circuito aria compressa
Filtro rimozione olio 1”
• 2 torni + 2 pistole ad aria compressa
• 2 fresatrici + 2 pistole ad aria compressa
• Smerigliatrice da 15 litri/sec. A 4 bar
• Macchina da taglio laser da 10 litri/sec. A 4 bar Materiale pulizia ugelli -4 x 2 mm
Filtro/reg 1/4” impostato a 4 bar
Verifica prestazioni del banco di prova da 10 litri/sec. spurgo costante 1 mm a 4 bar
1”
4 macchine, ognuna con 4 valvole di sequenza
Trapani
10 trapani da 4 litri/ sec. A 4 bar
10 pistole ad aria compressa
Le perdite possono essere una fonte considerevole di spreco energetico in un sistema ad aria compressa industriale. Se l’aria compressa fosse un fluido idraulico, eventuali perdite sarebbero così visibili che ci assicureremmo di ripararle. Spesso si accetta la presenza di piccole perdite nel luogo di lavoro come condizione normale in qualche modo comparabile al gas in casa, ma questo comportamento comporta dei costi enormi in ambito industriale.
Oltre a rappresentare uno spreco, le perdite possono anche contribuire ad altre perdite operative. Le perdite possono causare riduzioni di pressione nei sistemi, che possono portare a pressione insufficiente per l’applicazione e a un aumento degli scarti di prodotto. Spesso si ricorre all’aumento della capacità produttiva per compensare le perdite piuttosto che ripararle.
Le perdite si verificano ovunque!
La fabbrica nel nostro esempio ha molti dei problemi comuni dei sistemi ad aria compressa.
• Tubazioni
L’usura dei tubi è una causa primaria di perdite. Sostituire eventuali sezioni corrose delle tubazioni ai fini della sicurezza e del risparmio energetico.
• Raccordi, flange e collettori
Le perdite più importanti si verificano spesso nei punti di collegamento, sia nel sistema di distribuzione principale che nelle diramazioni. Spesso, quando si utilizzano insieme numerosi connettori a scatto per formare dei collettori, possono verificarsi perdite a causa dell’usura dei connettori e dell’improprio collegamento delle tubazioni.
• Tubi flessibili e raccordi
Le perdite possono derivare da danni ai flessibili causati da abrasione da contatto con oggetti circostanti, da deterioramento del materiale del flessibile e dalla tensione sui giunti di flessibili troppo corti o troppo lunghi.
• Componenti vecchi
Controllare tutti i componenti pneumatici, per esempio i cilindri e i regolatori vecchi, verificandone l’usura delle guarnizioni pneumatiche che possono causare le perdite maggiori.
• Valvole di scarico della condensa
Grandi quantità di aria possono disperdersi quando le valvole di scarico rimangono bloccate aperte o perfino lasciate aperte intenzionalmente. Questo si può spesso verificare in zone remote del sistema dove si accumula il condensato.
Immagine 2
Valvola di arresto manuale
• Sistemi lasciati sotto pressione quando non utilizzati. Quando i sottosistemi hanno grandi perdite che non possono essere evitate, per esempio per le presse e i martelli a caduta, è necessario isolarli dall’alimentazione dell’aria quando non sono utilizzati. Delle semplici valvole di arresto (Figura 2), o valvole di avviamento dolce con scarico (Figura 3) offrono delle soluzioni efficaci per isolare i sistemi con perdite, o aree del sito produttivo quando non sono utilizzati.
È possibile misurare facilmente le perdite di base con metodi diversi.
• Installare un flussometro e un trasduttore di pressione nel circuito di alimentazione principale dell’aria compressa (dopo i serbatoi). Collegare l’uscita del flussometro e il trasduttore di pressione a un registratore grafico e controllare le letture di un periodo di tempo. Misurare il flusso dal compressore quando il sistema non è in funzione, per esempio nel fine settimana.
• Usare un compressore con una capacità nota per pompare il sistema ad una pressione di esercizio normale durante le ore non produttive. Il compressore smetterà di comprimere l’aria alla pressione di esercizio. Dato che la pressione di sistema diminuisce a causa della perdita, il compressore caricherà alla pressione di funzionamento minima. Quindi si potrà misurare la portata l’entità della perdita dalla media dei tempi di carica e scarica in un determinato periodo.
• Pompare il sistema alla pressione desiderata e misurare il tempo necessario affinché la pressione si riduca al limite inferiore. Se si conosce il volume totale della rete di tubi e dei serbatoi, si può calcolare il tasso di perdita. Usare un flussometro piccolo nelle diramazioni per individuare aree che presentano problemi.
Ne vale la pena?
Quanto mi costano realmente le perdite?
Immagine 3
Le valvole di avviamento dolce con scarico isoleranno anche l’apparecchiatura, prevenendo le perdite
Nella nostra fabbrica di esempio, una singola perdita da un foro del diametro di 2 mm può costare 600 sterline l’anno. Usare il diagramma di flusso relativo agli orifizi (Figura 26 nella sezione dei Grafici in appendice) per calcolare le perdite con diversi alesaggi e pressioni.
Riduzione delle perdite
Definire degli obiettivi di riduzione delle perdite Comunicare l’entità del costo delle perdite per l’organizzazione e le modalità con cui si intende ottenere dei risparmi. Implementare un programma di manutenzione regolare; utilizzare delle etichette per le perdite e promuoverne l’uso.
Condurre un’ispezione del sistema ad aria compressa Condurre l’ispezione durante le ore in cui c’è più silenzio. Esaminare con l’udito le perdite da tubazioni o strumenti ed esaminare i flessibili e i raccordi. Utilizzare uno spray per la rivelazione delle perdite e osservare l’eventuale presenza di bolle. La riparazione di una perdita comune richiede mezz’ora di lavoro di una persona, e offre un ritorno economico rapido.
La riparazione delle perdite fornisce un risparmio di denaro considerevole, ma come ci assicuriamo che le riparazioni siano durevoli. L’implementazione di un programma di consapevolezza in tutto il sito produttivo fornisce dei risparmi a lungo termine su larga scala.
La divisione del sito produttivo in aree, con l’installazione di misuratori del consumo d’aria e alimentando le aree in base all’utilizzo specifico indurrà presto gli utilizzatori dell’energia a prestare maggior attenzione. Si possono facilmente definire degli obiettivi di riduzione delle perdite d’energia causate dalle perdite dei sistemi ad aria compressa.
Dopo aver ispezionato l’area dell’officina, sono state rilevate alcune perdite:
Perdita 1 x 2 mm a 4 bar e perdita 11 x 1 mm a 7 bar
Utilizzando il diagramma di flusso relativo agli orifizi, che equivale a 4,8 l/s e 11 x 1,2 l/s
Totale delle perdite = 18 l/s
0,4 x 8.400* x 18 x £0,10 **= £6.048,00
* si presume che il sistema sia pressurizzato per 24 ore al giorno, 50 settimane all’anno.
Costo della soluzione
Stimare mezz’ora per la riparazione di ciascuna perdita
£20.00 all’ora = £120,00
Risparmio Risparmio netto
£6.048,00 £120,00 £5.928,00
**Sostituire questi valori con il costo dell’energia locale e con la valuta locale per ottenere un risultato che rispecchi la realtà del mercato locale.
Immagine 4
Tasso di perdita in base ai diversi diametri dei fori
Immagine 5
La perdita può provenire da un giunto e può essere rivelata per mezzo di rivelatore di perdite.
La portata di aria compressa, la pressione, il volume e la temperatura possono essere monitorati costantemente tramite sensori di flusso come il sensore di flusso in linea IMI Norgren M/80, dotato di funzioni di rilevamento multiplo. I sensori di flusso in linea monitorano costantemente il sistema ad aria compressa per rilevarne i cali di pressione e altri segnali di perdita del flusso d’aria. I modelli digitali, rispetto a quelli analogici, possono fornire dati in tempo reale accurati utili per gli addetti alla manutenzione. In questo modo è possibile individuare le perdite e risolverle rapidamente.
Sensori di flusso in linea
La tecnologia di rilevamento del flusso termico del sensore di flusso in linea si basa sull’effetto del raffreddamento dei fluidi in movimento. Una sonda in ceramica, che è il resistore di misurazione, viene riscaldato mentre l’altro, il resistore di riferimento, non viene riscaldato. Quando il flusso dissipa il calore, la differenza di tensione tra i due resistori determina la velocità del flusso.
Siccome ci sono meno collegamenti nelle tubazioni principali dell’aria, la gran parte delle perdite di grande entità non si trova nel lato di alimentazione. Tuttavia, operando secondo le indicazioni fornite si potrà creare una base di riferimento utile per l’utilizzo futuro. Con maggiori probabilità le perdite si trovano nella zona di utilizzo (monitoraggio della singola macchina) o in un diramazione a cui si collegano più macchine (monitoraggio dell’area).
È molto semplice installare un sensore di flusso in un’area, in una linea di produzione, o nella zona di collegamento con le macchine e misurare immediatamente i valori di consumo e di perdita. Senza uno strumento specifico, la misurazione di pressione integrata garantisce che gli attuatori funzionino nel modo più efficiente possibile.
Immagine 6
Sensore di flusso in linea M/80
Quando è presente un sensore di flusso in linea su una macchina o in un’area, esso può eseguire le seguenti attività:
• tracciare l’uso dell’aria compressa quando l’attrezzatura non è utilizzata;
• fornire dati di tendenza in modo da poter confrontare il consumo di macchine simili o tracciare le prestazioni della macchina nel tempo.
• Facilitare l’individuazione di perdite in modo che il personale della manutenzione possa dedicarsi alla manutenzione piuttosto che alla ricerca delle perdite.
Immagine 7
Sensori di flusso installato
Immagine 8
Primo piano del sensore di flusso
Apparecchiature datate e tubazioni con perdite causano un aumento inutile dell’uso di energia. Inoltre, le perdite d’aria costringono il sistema a un funzionamento più intenso al fine di fornire le prestazioni necessarie. Questi fattori causano una maggiore produzione di emissioni di anidride carbonica. Un altro problema dei sistemi ad aria compressa che utilizzano olio è la grande quantità di condensato contenente olio. Una corretta gestione dei rifiuti può fornire benefici alla vita acquatica, mantenere i corsi d’acqua puliti e proteggere la salute umana.
Ridurre l’impatto ambientale delle perdite di aria compressa
Verifica: una valutazione trimestrale o biennale del sistema d’aria compressa può rivelare la presenza di perdite che possono determinare un aumento dell’uso di energia e danni all’ambiente.
Manutenzione regolare: Il monitoraggio, la sostituzione dei filtri, e la manutenzione regolari forniscono una qualità ottimale dell’aria, minori cali di pressione, e minori perdite. Nello specifico, i sensori di flusso in linea IMI Norgren M/80 possono fornire dati in tempo reale utili per individuare rapidamente e riparare le perdite.
Aggiornamento dell’attrezzatura: Motori elettrici, rotori di compressori e altri componenti datati possono diventare pericoli per l’ambiente. Sostituendo o riparando i compressori con apparecchiatura ecosostenibile non solo si possono ridurre le emissioni ma si può migliorare l'efficienza energetica
Agenda 2030 per lo Sviluppo Sostenibile delle Nazioni Unite
Su scala mondiale, l’Agenda 2030 per lo Sviluppo Sostenibile delle Nazioni Unite definisce diversi obiettivi per aumentare la sostenibilità, ed anche altri elementi riguardanti i diritti umani e problemi globali. Gli impianti industriali che modificano le proprie operazioni nel rispetto dell’Agenda 2030 per lo Sviluppo Sostenibile delle Nazioni Unite possono giocare un ruolo fondamentale nel realizzare un futuro sostenibile e rispettoso dell’ambiente risparmiando al tempo stesso denaro.
Obiettivo 7
Garantire a tutti l’accesso all’energia moderna in modo conveniente, affidabile, sostenibile
Le industrie dovrebbero porre l’attenzione sull’efficienza energetica, promuovendo una transizione verso l’energia rinnovabile e migliorando la tecnologia a favore di un’energia più verde. Affrontando il problema delle perdite d’aria si agisce nella direzione degli obiettivi dell’ONU usando meno energia non rinnovabile.
Obiettivo 9
Costruire infrastrutture resilienti, promuovere un’industrializzazione inclusiva e sostenibile e favorire l’innovazione
L’importanza dello sviluppo di infrastrutture resilienti e sostenibili è evidenziata nell’obiettivo 9. Ciò si può applicare ai settori industriali che si occupano della modernizzazione, nello specifico di sistemi ad aria compressa, per renderli più ecosostenibili, efficienti e per ridurre le perdite.
Obiettivo 12
Assicurare modelli di consumo e produzione sostenibili Ponendo l’attenzione sulle perdite dei compressori d’aria, le aziende possono ridurre gli sprechi e promuovere una produzione ecosostenibile. Inoltre, l’obiettivo 12 spinge le aziende a implementare pratiche sostenibili e a divulgare le proprie iniziative per la sostenibilità. Ciò richiede responsabilità e apertura nei processi industriali.
Obiettivo 13
Agire per contrastare il cambiamento climatico e il suo impatto Le perdite dei compressori d’aria industriali possono causare maggiori emissioni di gas serra dovute all’utilizzo di energia elettrica; risolvendo queste perdite si può ridurre l’impatto ambientale.
Immagine 9
Infografica sulla sostenibilità dell’ONU
La seconda causa di spreco principale di aria compressa e l’uso di una fonte di energia solo perché disponibile.
Alcuni esempi di questo è la creazione inefficiente di vuoto, utilizzare l’aria compressa per espellere prodotti difettosi dalla linea di produzione, e la rimozione di acqua/sporco/polvere dai prodotti. Ci sono alternative migliori a queste applicazioni. Se si sceglie l’aria compressa, è necessario usare l’attrezzatura idonea e si deve effettuare un controllo appropriato per mantenere al minimo l’utilizzo.
In un impianto produttivo esistente si possono spesso individuare gli usi impropri attraverso l’aumento della richiesta d’aria e delle ore di funzionamento del compressori. Per individuare gli attuali usi impropri è necessario fare un controllo in tutte le aree dello stabilimento, ponendosi la seguente domanda: è questo un uso efficace dell’aria?
• Stima dei costi dell’uso improprio
Quando c’è un processo che prevede il passaggio d’aria in atmosfera, come l’espulsione di prodotti sottopeso, o prodotti difettosi in un processo di inscatolamento, si può installare un flussometro sulla linea per misurare l’utilizzo dell’aria. Quindi, usando la formula dello spreco, si può individuare il costo del processo.
• Procedure consigliate
Un altro modo per calcolare i costi è usare il diametro dell’orifizio o dell’ugello di uscita e la pressione applicata per calcolare il flusso (vedere la tabella, immagine 26 flusso dell’orifizio, sezione dei grafici in appendice). Quando si utilizzano gli ugelli per spruzzare farina sulle pagnotte (Immagine 10), è importante assicurare che la distanza tra l’ugello d’uscita e il prodotto sia la più breve possibile in modo da ridurre al minimo la pressione. L’ugello dovrebbe essere diretto solo nell’area necessaria formando un cono (area circolare) o per emettere un getto lungo e stretto, ecc. Per coprire aree lunghe e strette, usare ugelli in parallelo per produrre una cortina e ridurre la distanza con il punto più lontano. Assicurarsi che la linea di alimentazione principale di più ugelli abbia un diametro sufficiente affinché non limiti il flusso d’uscita.
Gli ugelli a risparmio d’aria intrappolano e accelerano l’aria nei loro meccanismi per produrre lo spruzzo desiderato con pressioni di alimentazione inferiori, con un 1/20 del consumo originale d’aria compressa (Immagine 11).
Per massimizzare l’efficienza, installare nel sistema valvole e sensori di controllo. In questo modo si assicura che il flusso sia presente solo quando il prodotto raggiunge il punto di applicazione, evitando flussi inutili negli spazi vuoti del nastro trasportatore o nelle pause di lavoro.
Tutte queste soluzioni possono essere calcolate e confrontate in relazione all’uso/spreco d’aria e quasi in tutti i casi è possibile ottenere un risparmio. Quando in uno stabilimento si individuano gli usi impropri, è importante assicurare che i nuovi processi vengano installati considerando la fonte di alimentazione e i controlli esistenti.
L’ugello deve stare vicino al pane e deve avere un circuito di controllo del risparmio d’aria A per interrompere l’aria quando il pane sotto l’ugello non è presente. Considerare l’uso locale di filtri e essiccatori a membrana per ottenere aria secca di alta qualità.
Il materiale viene pulito prima di essere tagliato dal laser usando 4 ugelli da 2 mm alla pressione della linea. 4 ugelli da 2 mm con parametri predefiniti
4 x 4,8 l/s a 7 bar
4 x 1,81 l/s a 2 bar
Usando il diagramma di flusso relativo agli orifizi, Immagine 26.
Quindi, una riduzione di pressione a 2 bar fornirà un risparmio di flusso di 11,96 l/s.
0,4 x 8.400* x 11,96 x £0,10 **= £4.017,00
* Si presume che nessuna valvola di isolamento e sistema siano costantemente pressurizzati.
Installare un regolatore di pressione = £18,00
Calcolare 30 minuti a £20,00 all’ora = £10,00
Totale = £28,00
Risparmio Risparmio netto £4.017, 00 £28,00 £ 3.989,00
**Sostituire questi valori con il costo dell’energia locale e con la valuta locale per ottenere un risultato che rispecchi la realtà del mercato locale.
Molti sistemi funzionano con una pressione di linea massima con il solo controllo fornito dall’interruttore di pressione del compressore.
Ogni componente pneumatico ha una pressione di esercizio e una portata ottimali. L’utilizzo al di fuori di queste condizioni riduce la vita utile dell’attrezzatura a causa di un carico e di un’usura maggiori, che fanno crescere anche i costi operativi. Un dispositivo che funziona a 7 bar consumerà una quantità d’aria doppia rispetto a una pressione di 3 bar.
L’assenza di regolatori di pressione in un sistema comporta un uso dell’attrezzatura a pressioni eccessive. I risparmi si possono ottenere in molte aree, negli strumenti pneumatici, nelle valvole di controllo, nei cilindri di bloccaggio, nella corsa di ritorno dei cilindri a doppia azione di grandi dimensioni.
Quando i regolatori di pressione sono presenti ma la pressione di uscita è uguale a quella d’ingresso, questo indica spesso una scarsa lubrificazione e una pressione eccessiva applicata per compensare la frizione che rallenta il processo. Queste condizioni producono costi in termini di usura e di energia.
Calcolo dei costi
• Tutti gli strumenti pneumatici sono classificati in base alla pressione e alla portata ottimale. Lo spreco d’aria può essere calcolato usando il rapporto di pressione (assoluto), e poi moltiplicandolo per la portata nominale, ad esempio il consumo a 3 bar è di 8 l/s, a 7 bar sarà (7 + 1) x 8 = 16 l/s (3 + 1)
Questo può poi essere sostituito nella formula per lo spreco annuale per calcolare i risparmi.
• Solitamente, i cilindri a doppia azione funzionano solo nella corsa di estensione (corsa di lavoro). Quando non si esegue un lavoro o sono possibili dei tempi di reimpostazione più lunghi, la corsa di ritorno può avvenire a pressioni più basse. In presenza di sistemi con diametro interno maggiore, corsa lunga o cilindri multipli, si può ottenere un notevole risparmio d'aria. L’utilizzo di un regolatore per ridurre la pressione della corsa di ritorno può essere una soluzione valida per un ritorno economico rapido.
Il consumo con una corsa di ritorno a pressione inferiore nel cilindro a doppia azione si può misurare usando la formula Risparmio d’aria = 0,7854 x d2 x L (P1 - P2) x 10-6 T x 60
d = diametro del cilindro (mm)
L = lunghezza della corsa (mm)
T = tempo di una corsa (sec)
P1 = pressione applicata (bar) - corsa di estensione
P2 = pressione applicata (bar) - corsa di ritorno
• Le valvole hanno una conduttanza nominale C in litri/ sec per bar assoluto. Qualsiasi risparmio di flusso si può calcolare riducendo semplicemente la pressione applicata. È importante annotare la durata di funzionamento della valvola (per esempio la durata del flusso) per garantire il corretto risparmio di flusso. Solitamente questo valore è piccolo ma per installazioni con numerose valvole e/o valvole a ciclo rapido con tubazioni lunghe il risparmio totale può essere considerevole.
Dopo aver individuato i casi di pressione eccessiva all’interno di uno stabilimento, assicurarsi di esaminare il nuovo impianto, i nuovi processi e la nuova attrezzatura per verificare le migliori condizioni operative e l’attrezzatura di controllo della pressione prima di eseguire l’installazione. Questo si traduce poi in una durata più lunga degli utensili e in costi energetici inferiori.
10 utensili pneumatici a 4 bar.
Questi trapani sono alimentati da una pressione di 7 bar, e ciascuno viene usato in media 1.000 ore all’anno.
Il consumo di ogni trapano a 4 bar è di 15 l/s.
Quindi a 7 bar ogni utensile consumerà*:
8 x 15 = 24 l/s
5
Quindi, usando una pressione inferiore, il potenziale risparmio è di 9 l/s per utensile.
Nel corso delle 2.500 ore di utilizzo annuale, il risparmio medio di flusso:
1.000 x 9 = 3,6 l/s
2.500
0,4 x 2.500 x 3,6 x £0,10** = £3.377,00 Per 10 utensili sarà = £33.770,00
Costo della soluzione
Installare un regolatore di pressione per utensile = £25,00 x 10 = £250,00 30 minuti per l’installazione a £20.00 all’ora** = £10,00 x10 = £100,00
Totale = £350,00
* i calcoli devono essere eseguiti con pressioni assolute: cioè 1 bar in più rispetto alla lettura
£3.377,00
**Sostituire questi valori con il costo dell’energia locale e con la valuta locale per ottenere un risultato che rispecchi la realtà del mercato locale. Risparmio Risparmio netto
Immagine 12
£350,00
£3.027,00
Regolare la pressione all’impostazione nominale dell’utensile pneumatico, non alla pressione della linea principale
La perdita di pressione può essere definita come una perdita di potenza in un sistema per eseguire il lavoro. In pratica si manifesta con una pressione più bassa in alcune parti del sistema. Spesso viene compensata aumentando la pressione di produzione o aumentando i regolatori. L’energia potenziale prodotta attraverso la compressione dell’aria viene dissipata tramite la frizione e la perdita di calore quando l’aria viene spinta attraverso tutti i componenti del sistema.
È necessario quindi progettare e gestire i sistemi per ridurre al minimo la quantità di caduta di pressione. Ogni singolo bar di caduta di pressione non necessaria causa un aumento del 7% dei costi di produzione. Questo significa £3.500,00 all’anno per la nostra Fabbrica di Esempio. Le due aree principali in cui si verificano i cali di pressione sono le tubazioni e il filtraggio.
• Non sovraccaricare le tubazioni. Mantenere la velocità al di sotto di 6 m/s nella linea principale.
• Semplificare le tubazioni. Evitare gomiti, per esempio un gomito a 90 gradi equivale a un tubo dritto di 1,6 metri.
• Installare valvole “a bassa resistenza”; una valvola a sfera a flusso completo equivale a un tubo di 0,4 m, ed offre una resistenza inferiore alla metà di quella offerta da una valvola a saracinesca. L’immagine 28 nella tabella mostra degli esempi.
Immagine 13
Esempio di tubazione inefficiente su un banco di prova per la produzione
La perdita di pressione nelle tubazioni si verifica soprattutto a causa della frizione delle molecole d’aria con la superficie dei tubi. Se il tubo è troppo stretto per il volume del flusso, la velocità dell’aria sarà molto alta, e la perdita di potenza sarà elevata.
L’energia si perde anche quando c’è un cambiamento di direzione del flusso causato da gomiti, giunzioni e valvole di arresto. Dei sistemi di tubazioni semplici riducono al minimo la perdita di pressione (Immagine 13).
Come calcolare la perdita di pressione nelle tubazioni
• Metodo 1
• Misurare la pressione di alimentazione.
• Misurare la pressione nel punto più lontano dall’alimentazione.
• La differenza è la perdita di pressione del sistema.
• Metodo 2
• Calcolare il consumo d’aria, cioè calcolare il volume spazzato dai cilindri di lavoro.
• Annotare la pressione di alimentazione e il diametro del tubo.
• Usare grafici normativi per calcolare la perdita di pressione.
• Metodo 3
• Utilizzare un flussometro in linea per misurare il flusso.
• Annotare la pressione di alimentazione e il diametro del tubo.
• Usare l’immagine 29 nella tabella per vedere se il flusso è nell’intervallo consigliato.
Immagine 14
È importante scegliere un filtro di dimensioni idonee
Dimensioni del filtro economico
Costo
Immagine 15
L’effetto del grado di finezza del filtro sulla caduta di pressione
Pressione della linea = 6,3 bar Flusso = 30 litri/sec.
Caduta di pressione iniziale (bar)
Il filtraggio è una parte essenziale del sistema ad aria compressa. Se non protette dall’acqua, dalle particelle e dagli oli degradati del compressore, le macchine possono danneggiarsi rapidamente. Per mantenere la perdita di pressione al livello minimo possibile:
Usare un filtro di dimensioni appropriate
Se il filtro è troppo piccolo per il flusso richiesto, allora si genererà una caduta di pressione troppo alta. Quando è nuovo, un filtro per uso generico dovrebbe fornire una caduta di pressione non superiore a 0,1 bar. Installando un filtro più piccolo non si ottiene un reale risparmio, perché esso causerà una caduta di pressione più alta e si bloccherà più facilmente a causa della minore area superficiale del filtro (Immagine 14).
Verificare il livello corretto di filtraggio
Un filtro molto fine offrirà una resistenza maggiore al flusso rispetto a un filtro a maglie più grandi. Gran parte dei componenti pneumatici richiede un filtraggio di circa 40 micron. Quindi in questa applicazione non è opportuno usare un filtro da 5 micron o perfino da 0,01 micron (Immagine 15).
Per applicazioni che richiedono un filtraggio elevato, i filtri con una maggiore capacità di filtrazione vanno messi il più vicino possibile all’applicazione. Questo assicura che le dimensioni del filtro determinate dal flusso siano le più piccole possibili. Non filtrare l’intera preparazione dell’aria o linea di derivazione secondo questo standard, perché ciò aumenterà la richiesta di flusso, aumentando la dimensione del filtro, il suo prezzo d’acquisto, il prezzo dell’elemento sostitutivo, e comporterà una caduta di pressione ulteriore per l’intero sistema a valle.
Verificare la presenza di elementi filtranti sporchi; controllare gli indicatori di caduta di pressione Dopo un certo tempo di utilizzo, all’interno dell’elemento filtrante si verifica un accumulo di particelle che causa l’ostruzione del filtro. Ciò comporta una caduta di pressione nell’applicazione. Spesso in queste condizioni la pressione viene aumentata tramite regolatore per compensare la caduta. L’aumento della pressione comporta un aumento dei costi. Un aumento di 0,35 bar della caduta di pressione in una linea può costare fino a £400,00 l’anno. Installare degli indicatori di caduta di pressione: di tipo pneumatico o elettrico (Immagine 17) in grado di indicare immediatamente un aumento della caduta di pressione. La sostituzione degli elementi in questa condizione produce un risparmio energetico. È buona prassi sostituire l’elemento filtrante ad intervalli regolari. Questo consente di mantenere al minimo lo spreco energetico e di fornire aria della giusta qualità (Immagine 16). Qualsiasi impianto dovrebbe essere concepito per fornire il grado di qualità dell’aria necessario per il sistema; tuttavia la qualità dell'aria adatta agli strumenti dovrebbe essere garantita solo dove effettivamente richiesta dall'applicazione. Fornire aria secca di alta qualità in tutte le aree dello stabilimento è costoso e quindi andrebbe evitato.
Immagine 16
Risparmio sui costi tramite il cambio regolare degli elementi
Nessuna sostituzione
Costi energetici annuali
Coalescenza
Aumento della Caduta di pressione
Un filtro da 2 pollici con portata di 400 l/s a 7 bar se nuovo, la caduta di pressione = 0,15 bar in 2 anni può aumentare fino a 0,4 bar
Questo 0,25 bar in più causa una richiesta di energia ulteriore di 1,8 Kwh
Per 2.500 ore totali di energia extra = 1,8 Kwh x 2.500 a £0,10 al Kwh* di costo extra = £450,00
Sostituire l’elemento filtrante = £70,00
30 minuti di lavoro a £20,00 all’ora = £10,00
Totale = £80,00
Risparmio
£450,00
Risparmio netto
£80,00 £370,00
*Sostituire questi valori con il costo dell’energia locale e con la valuta locale per ottenere un risultato che rispecchi la realtà del mercato locale.
Immagine 17
Filtri con indicatore di caduta di pressione integrato
Nei sistemi ad aria compressa, i componenti installati per motivi di sicurezza hanno un costo. Tuttavia alcuni sono vantaggiosi perché forniscono un risparmio energetico. Ci sono molti documenti sulla sicurezza dei sistemi ad aria compressa e sui componenti pneumatici. Alcuni sono norme internazionali mentre altri che non appartengono all’ambito legale forniscono linee guida elaborate da organizzazioni per la sicurezza e organizzazioni di primo piano nel settore della potenza fluida.
Le perdite (interne o esterne) non dovrebbero causare pericoli. Nei sistemi in cui la pressione dell’aria è impiegata per mantenere un carico, come in una pressa, in applicazioni di frenatura o bloccaggio, una perdita potrebbe costituire un pericolo.
Monitoraggio delle condizioni dei filtri. Se il decadimento delle prestazioni del filtro possono costituire una situazione di pericolo, allora è opportuno fornire istruzioni chiare a riguardo. Un filtro ostruito che causa una pressione ridotta a valle potrebbe avere un effetto simile a una perdita in sistemi in cui la pressione è utilizzata per mantenere i carichi. Gli indicatori di caduta di pressione indicheranno quando il filtro è ostruito e richiede la sostituzione. In questo modo si riducono al minimo i costi energetici mantenendo la caduta di pressione a un livello accettabile.
I dispositivi di controllo della pressione e del flusso o i loro involucri dovrebbero essere dotati di dispositivi antimanomissione in quanto una modifica non autorizzata della pressione o del flusso potrebbe costituire un pericolo. Spesso, la pressione di macchine o sistemi viene aumentata con la speranza di accelerare la velocità del processo. Solitamente ci sono altri fattori all’interno del sistema che possono limitare questa condizione mentre l’aumento della pressione può far crescere soltanto il consumo d’aria.
In alcuni casi, l’aumento della pressione può essere pericoloso, come nel caso dell'utilizzo di pinze pneumatiche. La forza prodotta viene calcolata per eseguire il serraggio dei componenti; qualsiasi aumento di tale forza potrebbe causare la rottura del componente che potrebbe frantumarsi o esplodere. Per garantire la sicurezza dei sistemi, sui regolatori è possibile montare delle custodie antimanomissione chiudibili con lucchetti. (Immagine 18). Le valvole d’arresto bloccabili impediscono a chiunque di spegnere accidentalmente l’aria di un sistema, o di accendere la macchina mentre riceve un intervento di manutenzione creando un possibile pericolo.
Immagine 18
Custodia antimanomissione
Le macchine dovrebbero essere progettate in modo tale che all’accensione qualsiasi componente in movimento raggiunga la posizione di lavoro in modo sicuro. Deve essere presente un modo sicuro e rapido di rilascio dell’aria dal sistema. Le valvole di avviamento dolce con scarico assolvono a queste funzioni e il loro segnale può essere collegato ad un’operazione di spegnimento automatico che isola la macchina quando non è utilizzata. Questo significa che qualsiasi perdita o dispositivo di spurgo costante non scaricherà il sistema principale.
Le pistole ad aria compressa possono essere poco sicure, se non dotate di un regolatore di pressione con antimanomissione che è regolato ad una pressione ridotta.
Spesso si ignorano i pericoli che comportano questi strumenti. Per esempio, la pressione di 0,4 bar può penetrare la pelle umana con risultati potenzialmente fatali se l’aria entra nel flusso sanguigno.
Inoltre, molte pistole ad aria possono essere anche artigianali, costruite con pezzi di tubi di rame di diametro fino a 6 mm, rendendole più pericolose.
Un altro aspetto da considerare è lo spreco d’aria. Sarebbe buona prassi utilizzare una pistola ad aria compressa con prese d’aria laterali che evitano l’accumulo di pressione in caso di blocco dell’ugello (Vedere l’immagine 19).
Se la pressione ridotta non è abbastanza per l’operazione, si può usare una pistola ad aria compressa con ugello efficiente in grado di convogliare una parte di aria atmosferica. Questa apparecchiatura può fornire una condizione di lavoro più e garantire una riduzione dell’utilizzo dell’aria.
Immagine 19
Regolatore preimpostato antimanomissione per pistole ad aria compressa
Il policarbonato è un materiale comunemente usato per serbatoi di filtri, regolatori di filtri e lubrificatori, offrendo una visibilità chiara del contenuto. Tuttavia, in un ambiente industriale deve essere trattato con una certa cura. Le norme prevedono quanto segue:
• A.4.1.2 ‘I serbatoi che a seguito di un’ispezione visiva mostrano segni di danno meccanico, rottura o appannamento, devono essere sostituiti’.
• A.4.1.3 ‘I serbatoi che sono stati contaminati da vernice devono anch’essi essere sostituiti; non devono essere puliti’.
• A.4.1.4 ‘Tutti i serbatoi utilizzati per 10 anni devono essere sostituiti, anche se a seguito di un’ispezione visiva appaiono in condizioni accettabili, come indicato nella norma A.4.1.2’ Sebbene la sostituzione dei serbatoi con uno dei problemi menzionati non fornisca direttamente un risparmio energetico, deve far parte di un piano di manutenzione che preveda anche il controllo delle condizioni degli elementi filtranti e degli scarichi per ridurre la caduta di pressione e le perdite. I filtri sono comunemente mantenuti in modo non corretto ed è importante sensibilizzare gli interessati sulle implicazioni per la sicurezza legate a una gestione trascurata di queste unità (Immagine 20).
Per poter effettuare degli interventi sulla preparazione dell’aria, la linea deve essere isolata dalla fonte di alimentazione e depressurizzata prima di eseguire qualsiasi intervento.
Sono disponibili diversi tipi di valvole che aiutano a soddisfare questo requisito:
• Valvole a sfera (Immagine 21)
• Valvole di arresto incluse in unità FRL (filtri, regolatori e lubrificatori)
• Valvole di controllo azionate elettricamente
• Valvole di controllo azionate pneumaticamente
L’utilizzo di queste valvole offre un vantaggio aggiuntivo per cui qualsiasi perdita del sistema a valle non sottrarrà costantemente aria dal sistema di alimentazione d’aria principale.
L’utilizzo di valvole di sicurezza pneumatiche può contribuire al risparmio energetico. Il dispositivo è progettato per impedire che i flessibili pneumatici si muovano in modo irregolare scaricando aria ad alta pressione in caso di rottura di un flessibile. Le valvole di sicurezza pneumatiche riducono il flusso in atmosfera, in modo che fuoriesca solo una piccola parte d’aria, rispetto al flusso totale di una linea guasta. In questo modo si elimina il rischio d’infortunio legato al tubo flessibile e si riduce al minimo lo spreco di energia.
In situazioni in cui le valvole di isolamento e le valvole di sicurezza pneumatiche sono assenti, sarebbe necessario effettuare lo sfiato del sistema a valle, facendo scaricare tutta l’aria compressa prima di riparare il guasto del flessibile.
18 pistole ad aria compressa con foro da 4 mm, alimentate da una pressione di linea di 7 bar.
Le pistole ad aria compressa devono essere regolate a una pressione più bassa usando il diagramma di flusso relativo agli orifizi.
Flusso 4 mm a 7 bar = 19 l/s
Flusso 4 mm a 2 bar = 7 l/s
Potenziale risparmio di flusso per pistola = 12 l/s
La pistola viene utilizzata per 300 ore l’anno (circa 10 minuti ogni ora)
Media di risparmio annuale = 300 x 12 = 1,4 l/s
2.500
Totale per 18 pistole ad aria compressa = 25 l/s
0,4 x 2.500 x 25 x 0,10£* = 2.500,00£
Costo della soluzione
18 regolatori preimpostati = £450,00
30 minuti* per singola installazione = £180,00
Totale = £630,00
Risparmio Risparmio netto £2.500,00 £630,00 £1.870,00
*Sostituire questi valori con il costo dell’energia locale e con la valuta locale per ottenere un risultato che rispecchi la realtà del mercato locale.
Gli attuatori vengono normalmente utilizzati per fornire movimento e forza in applicazioni di automazione industriale. Il corretto dimensionamento degli attuatori per soddisfare i requisiti dell’applicazione è un’operazione fondamentale per assicurare l’esecuzione ottimale del processo. Degli attuatori sovradimensionati possono avere un consumo d’aria superiore a quello necessario, riducendo l’efficienza complessiva del sistema, mentre degli attuatori sottodimensionati potrebbero non fornire la forza necessaria, comportando prestazioni insufficienti.
1. Stabilire i requisiti di carico:
Calcolare la spinta necessaria per spostare il carico. Per questa operazione è necessario considerare il peso del carico ed eventuali forze aggiuntive, come la frizione o la gravità.
2. Fattore di sicurezza:
Considerare quanto segue: l’applicazione è dinamica o statica? In base al tipo di applicazione, applicare il fattore di sicurezza appropriato: fattore di sicurezza del 50% per un’applicazione dinamica e fattore di sicurezza del 5% per un’applicazione statica.
3. Considerare la pressione di esercizio:
Considerare qual è la pressione disponibile per l’applicazione quando si sceglie il diametro interno corretto dell’attuatore. Le schede tecniche di IMI Norgren indicano dati teorici di spinta a 6 bar. Regolare la spinta necessaria in base alla pressione disponibile per l’applicazione.
Prendere in considerazione le condizioni operative, come temperatura e umidità, che possono incidere sulle prestazioni dell’attuatore. Assicurare che l’attuatore scelto possa funzionare in modo efficace in tali condizioni.
Considerare un’applicazione con una corsa di 80 mm, 10 volte al minuto, per 10 ore al giorno, 5 giorni a settimana, per 50 settimane.
*Costo previsto dell’aria di £0,02/m3
A 6 Bar (consumo d’aria) Ø63 mm Ø80 mm
Velocità in fase di uscita 0,218 l/cm 0,35 l/cm
Velocità in fase di entrata 0,195 l/cm 0,32 l/cm
ciclo 3,30 litri 5,36 litri
minuto (litri/min)
minuto (m3/min)
litri
Gli attuatori di dimensioni corrette possono ridurre notevolmente il consumo d’aria, con una conseguente riduzione dei costi energetici. Essi migliorano anche l’affidabilità e la durata del sistema, in quanto i componenti sono meno soggetti a usura eccessiva.
Immagine 22
Dimensionamento dell’attuatore
Nell’attuale situazione mondiale di costi energetici crescenti e di preoccupazioni per l’ambiente, siamo impegnati ad aiutare i nostri clienti a gestire efficacemente il consumo energetico. Oltre a numerose procedure consigliate presenti in questa guida, siamo impegnati a fornire prodotti innovativi pensati per raggiungere questi obiettivi.
Come abbiamo più volte detto in questa guida, una corretta pressione dell’aria è essenziale sia per ottimizzare le prestazioni dei processi sia per massimizzare le possibilità di risparmio energetico.
La serie IMI Norgren Excelon® Plus è un prodotto ideale che risponde a questa logica. Sia il regolatore sia il regolatore del filtro offrono una funzione di bloccaggio che consente di aggiungere un lucchetto per bloccare l’unità dopo averla configurata in modo ottimale. Le unità sono dotate di serie di un manometro integrato che mostra l’impostazione dell’aria compressa a valle. Come opzione, offriamo anche un interruttore di pressione elettronico intelligente, e sebbene esso possa essere usato come interruttore di pressione, offre anche la semplice lettura della pressione tramite schermo a colori a cristalli liquidi, per cui il verde - in tolleranza o il rosso - fuori tolleranza, possono essere visti facilmente e a distanza.
Regolatori di pressione
Il controllo proporzionale svolge un ruolo fondamentale nell’ottimizzare i processi regolando in modo preciso la pressione e il flusso secondo i requisiti specifici dell’applicazione.
I regolatori di pressione IMI Norgren VP50 e VP51 sono progettati per adattare la pressione d’uscita nei sistemi con carichi variabili, assicurando stabilità ed efficienza. In modo simile, le valvole di flusso VP60 sono perfette per applicazioni che richiedono il controllo della velocità variabile, come la regolazione precisa della velocità sugli attuatori, fornendo un funzionamento lineare con diverse velocità. Tramite l’utilizzo di queste valvole e regolatori avanzati è possibile gestire in modo efficiente le operazioni, ridurre lo spreco energetico al minimo ed evitare possibili danni ai componenti, assicurando che il proprio sistema funzioni in modo ottimale in condizioni variabili.
IMI Norgren IVAC è un attuatore pneumatico a risparmio energetico che soddisfa le regole dimensionali della norma ISO 15552. IVAC è dotato di una valvola integrata, di controlli di flusso e di interruttori azionati magneticamente per offrire un controllo totale dell’attuatore. Può essere aggiornato o integrato in nuovi sistemi e rispetto alla tradizionale valvola pneumatica e ai gruppi di attuatori, può aiutare a ridurre il consumo energetico fino al 50%.
25 IVAC
Nella condizione ottimale, solo il 5% dell’energia immessa in un compressore d’aria resta nell’aria dopo la compressione. Ciò è dovuto al calore emesso dal compressore nei suoi sistemi di raffreddamento.
Gran parte dei luoghi che ospitano i compressori contengono il compressore, il sistema di trattamento e il sistema di controllo. Ogni elemento della stazione del compressore, l’installazione e la sua manutenzione incide sull’efficienza energetica.
La dimensione e la configurazione del compressore è importante in termini di efficienza energetica. In base al modello di domanda, è normale affidare alla macchina più grande ed efficiente sulla linea la gestione del carico di base ed avere altre macchine che si attivano o disattivano in base ai picchi o ai cali di domanda. La maggior parte delle moderne installazioni usa compressori rotativi, a palette iniettate d'olio e a vite. Quando sono necessari volumi d’aria maggiori e di qualità superiore, si possono usare macchine a vite senza olio o centrifughe in quanto offrono prestazioni migliori. (Vedere l’immagine 27).
Sebbene non siano molto diffuse per le nuove applicazioni, a meno che non siano utilizzate per gas speciali o pressioni elevate, si utilizzano ancora le macchine a pistoni. Queste macchine, soprattutto quelle di grandi dimensioni, hanno un’efficienza e una capacità di adattarsi a situazioni di carico parziale eccellenti. Gli azionamenti a velocità variabile stanno diventando piuttosto diffusi in quanto sono macchine a iniezione d’olio a due stadi.
Il raffreddamento è un aspetto di grande importanza in tutti i compressori. L’aria immessa dovrebbe essere quanto più fredda possibile, idealmente presa da un luogo esterno all’ombra. In generale, una riduzione di 4°C della temperatura d’ingresso fornisce un miglioramento dell’1% in termini di efficienza. Un semplice controllo delle condizioni del compressore per misurare le differenze di temperatura tra mezzo di raffreddamento e aria di scarico dal post-refrigeratore. Per i compressori raffreddati ad aria questa differenza non deve superare i 15°C. Per i compressori raffreddati a liquido la differenza non deve superare i 10°C. Se invece si riscontrano differenze più ampie nelle macchine, l’efficienza sarà inferiore a quella prevista. I sistemi di raffreddamento dovrebbero essere migliorati.
Assicurarsi che tutte le linee di alimentazione principali siano progettate correttamente, con velocità di flusso non superiori a 6 metri al secondo. Usare raccordi a T curvi e gomiti a lungo raggio in tutte le giunzioni delle tubazioni. Usare scaricatori di condensa con sensore di livello in tutti i punti di accumulo del condensato e accertarsi che quest’ultimo sia recuperato nel rispetto delle relative norme.
Utilizzare il calore di scarto prodotto dalla compressione per il riscaldamento ambientale, il riscaldamento dell’acqua domestica o per l’acqua di processo. In questo modo si possono ottenere dei risparmi notevoli.
Il modo in cui si gestiscono i compressori sul campo incide in modo rilevante sull’efficienza produttiva. La manutenzione delle macchine dovrebbe essere sempre eseguita rispettando le indicazioni del manuale di istruzioni del produttore. Non è economicamente vantaggioso far funzionare compressori rotativi a palette e a vite oltre il ciclo di vita degli elementi compressori indicato dal produttore. Normalmente tale ciclo dura 24.000 ore per macchine a iniezione d’olio e 40.000 ore per macchine prive di olio.
Controllare regolarmente la pressione dell’intercooler dei compressori con pistone a due stadi e di quelli a vite. Essa dovrebbe essere compresa tra 2 e 2,5 bar quando la pressione di scarico finale è di 7 bar. Qualsiasi scostamento indica uno squilibrio di fase che causa una scarsa efficienza. In modo simile, controllare la caduta di pressione in tutto il sistema di separazione dell’olio. Se la manutenzione del compressore viene affidata a un’azienda terza, accertarsi che venga eseguita da un tecnico autorizzato dal produttore. Utilizzare solo pezzi di ricambio originali; gli articoli non originali o ricondizionati male possono compromettere gravemente l’efficienza energetica. Un piccolo risparmio apparente in queste aree può diventare nel lungo periodo un falso vantaggio economico.
Se si opera con più compressori di tipo e dimensioni diversi si dovrebbe utilizzare un sistema di controllo. Esso ottimizzerà il numero di compressori fornendo un controllo della pressione efficace dei gruppi di macchine di maggiore efficienza energetica.
Trattare l’aria solo secondo gli standard minimi richiesti. Gli essiccatori ad aria refrigerata che forniscono un punto di rugiada di +3°C e i filtri aumentano il costo dell’energia del 3%. Gli essiccatori ad adsorbimento e i filtri che forniscono un punto di rugiada di -40°C fanno crescere i costi di gestione dall’8 al 15%.
Per risparmiare energia, usare gli essiccatori a membrana nel punto d’uso finale. Con gli essiccatori ad adsorbimento, usare dispositivi di rilevamento del punto di rugiada. Mantenere la cadute di pressione del sistema di trattamento a 0,5 bar. Scegliere filtri con dimensioni adatte per il flusso massimo; non usare flange di dimensioni ridotte. Eseguire la manutenzione regolare dei filtri.
Stabilire la pressione minima accettabile del punto d’uso e accertarsi che la rete di tubazioni sia progettata in modo tale che la caduta di pressione con sistema a pieno carico non superi i 0,5 bar. Se possibile, ridurre la pressione di produzione: se ridotta di 1 bar, si avrà una riduzione del 7% sui costi di produzione. Una comune struttura con diversi compressori
Indagine sulla fabbrica in 3 settori
• Struttura per compressori
• rete di distribuzione ad anello
• aree di lavoro/punti di utilizzo
Attenzione in ogni area su
• Perdite
• Uso improprio
• Pressione eccessiva
• Caduta di pressione
• Problemi di sicurezza
poi misurare localmente l’utilizzo, se possibile
Individuazione delle aree di risparmio costo dell'azione correttiva e
• ritorno economico
• implementazione
• controllo/caduta di pressione per conferma
• misurazione
Usare i dati sul flusso per modificare il sistema di controllo per i compressori, ove necessario.
Implementare una manutenzione preventiva e verifiche periodiche (Le perdite sono ricorrenti).
ETSU, il ramo dell’efficienza energetica del Dipartimento per L’ambiente e i Trasporti e delle Regioni, offre una serie di pubblicazioni gratuite su tutti gli aspetti del risparmio energetico.
Per informazioni sull’aria compressa consultare:
Guide di buone pratiche
• 216 Il risparmio energetico nel filtraggio e nell’essiccamento dell'aria compressa.
• 238 Recupero del calore dai compressori d’aria
• 241 Risparmio energetico nella scelta, nel controllo e nella manutenzione dei compressori ad aria.
Casi di studio di buone pratiche
• Carbon Trust (Regno Unito) 0800 085 2005
Guide sul consumo energetico
• ECG040
Costi dell’aria compressa: Produzione
• ECG041
Costi dell’aria compressa: Perdite
• ECG042
Costi dell’aria compressa: Trattamento
• HSG 39 Sicurezza dell’aria compressa
• BS 6005 1997
Specifiche dei contenitori trasparenti stampati in policarbonato usati per filtri e lubrificatori per aria compressa
Perdita per attrito in raccordi per tubi in termini di metri equivalenti di tubo diritto
* Scarico automatico - totalmente aperta
Pressione manometrica applicata in bar
*Portata d’aria in dm3/s misurata come aria libera alla pressione atmosferica standard di 1,013 mbar.
Tramite tubo in acciaio di medie dimensioni conforme a ISO65.
Note generali
I valori di flusso si basano su una caduta di pressione, ( ΔP) nel modo seguente: 10% di pressione applicata per 30 metri di tubo, da 6 a 15 mm di diametro interno nominale inclusi gli estremi 5% di pressione applicata per 30 metri di tubo, da 20 a 80 mm di diametro interno nominale inclusi gli estremi
La nostra Divisione Automazione Industriale comprende quattro centri globali di supporto tecnico oltre a stabilimenti produttivi in Europa, America e Asia Pacifico. Inoltre il Gruppo dispone di una rete di vendita e assistenza in 50 paesi, supportata da distributori in tutto il mondo.
Per ulteriori informazioni, scansionare il codice QR o visitare il sito www.imiplc.com/industrial-automation
IMI Norgren
IMI Bimba
IMI Bahr
Le informazioni contenute in questo opuscolo sono fornite solo a scopo informativo e promozionale. Inoltre, sono fornite “così come sono” e senza garanzie di alcun tipo, espresse o implicite, comprese, ma non solo, le garanzie implicite di qualità soddisfacente, idoneità per uno scopo particolare e/o correttezza.
Tutte le specifiche, le caratteristiche e i prezzi contenuti in questa brochure sono soggetti a modifiche senza preavviso. IMI plc non dichiara né garantisce che le informazioni e/o le specifiche contenute nel presente opuscolo siano accurate, complete o aggiornate e pertanto non fornisce alcuna garanzia o dichiarazione in merito al loro utilizzo. IMI plc o una delle sue consociate è proprietaria di tutte le immagini, i loghi, i marchi dei prodotti e i marchi di fabbrica citati in questa brochure. È vietato l’uso, la riproduzione o la modifica non autorizzata di questi contenuti.
© Copyright IMI plc. Tutti i diritti riservati. z10280BR it/09/24
Le immagini utilizzate utilizzate sono sotto licenza di Shutterstock.com