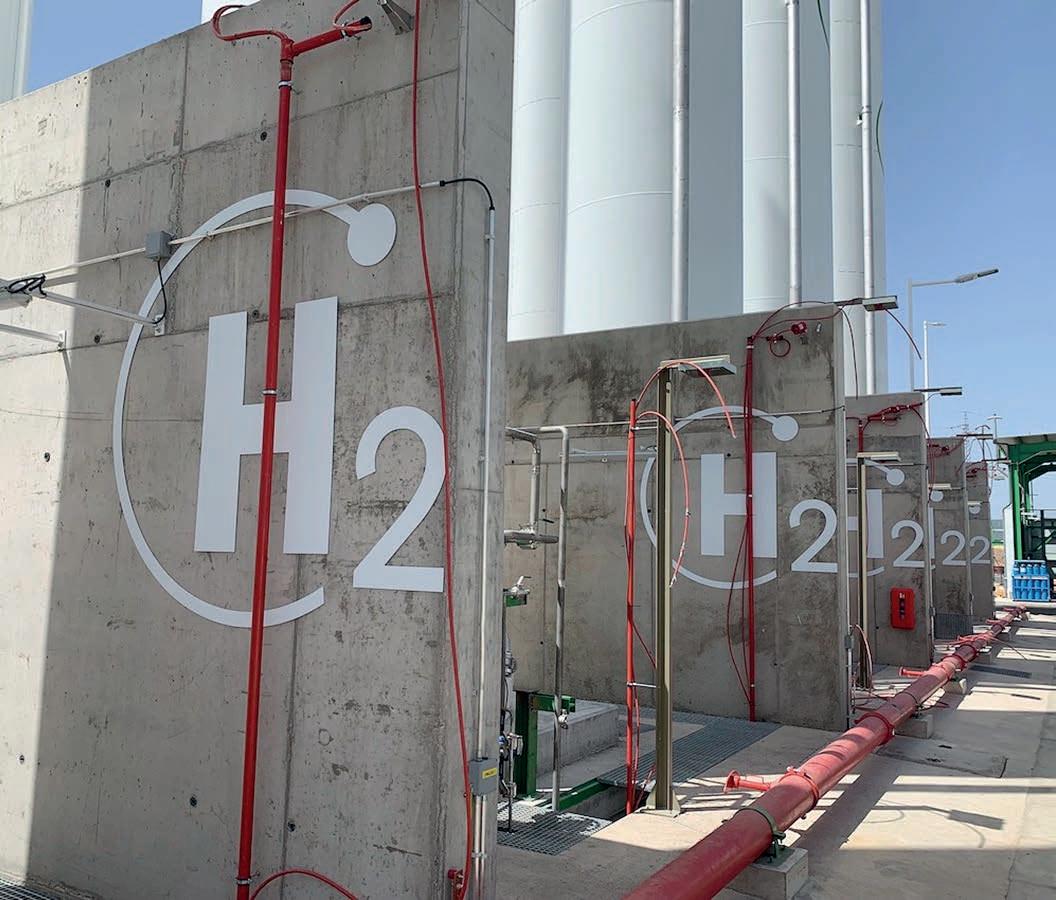
9 minute read
EXTRA MOMENTUM VOOR INDUSTRY 4.0
from Petrochem 4, 2022
Transitie geeft momentum voor Industry 4.0
Sinds afgelopen zomer lijkt het spel definitief op de wagen. Shell is inmiddels bezig met de bouw van een groene waterstoffabriek van 200 megawatt op de Maasvlakte en heeft grote plannen voor de transformatie van zowel Pernis als Moerdijk. En ook andere industriële bedrijven namen investeringsbeslissingen of werken daar met rasse schreden naartoe. Denk aan RWE, HyCC, Neste, Air Liquide, Uniper en BP. Een momentum om volgende stappen te zetten op het gebied van industry 4.0?
Advertisement
Wim Raaijen In hun berichtgeving zijn waterstofproducent HyCC en gasttransportbedrijf Gasunie er duidelijk over. Vanaf de eerste investering in Djewels 1, een nieuwe waterelektrolysefabriek op Chemie Park Delfzijl, willen ze zoveel mogelijk gebruikmaken van de voordelen die Industry 4.0 biedt. Dit betekent onder meer dat er niet continu personeel bij de fabriek zal zijn, dat de fabriek van afstand kan worden bestuurd. Ook zullen er slimme sensoren worden ingezet die tijdig waarschuwen wanneer een onderdeel van de fabriek moet worden vervangen. En het flexibel opereren van de fabriek zal niet gebeuren door een operator, maar door een slim algoritme dat reageert op de condities in de elektriciteitsmarkt. Al deze zaken lijken haalbaar voor de fabriek met een capaciteit van 20 MW. En het is de bedoeling om deze allemaal door te trekken naar de grotere vervolgprojecten van HyCC. Denk aan Djewels 2 (extra 40 megawatt in Delfzijl) en nog grotere plannen in de Rotterdamse en Amsterdamse haven.
Waterstofhub
Ook bij nieuwe installaties die RWE de komende jaren wil bouwen, zal de rol van slimme digitale techniek groot zijn. En de ambities van het energiebedrijf in Nederland zijn immens. Zo wil het concern miljarden euro’s investeren in en rond de Eemshaven. Dat RWE zoveel geld in deze locatie investeert, heeft alles te maken met de overtuiging dat het gebied dé energie- en waterstofhub van Noordwest-Europa wordt. Niet alleen heeft RWE plannen om de Eemshavencentrale te verduurzamen door kolen te vervangen door biomassa en de CO2 af te vangen en als grondstof aan de chemische industrie te leveren. Het concern wil ook de gasgestookte Magnumcentrale, die RWE later dit jaar vrijwel zeker van Vattenfall overneemt, vrij van CO2-uitstoot maken. En ook komt er een waterstoffabriek van in eerste instantie 50 megawatt die groene stroom krijgt van RWE’s windmolenpark Westereems. Het plan is om de waterstoffabriek niet veel later uit te bouwen tot de grootste van Nederland. Dat hangt nog wel af van de vraag of het concern toestemming krijgt om het nieuwe offshore windpark Hollandse Kust (west) te bouwen en te exploiteren.
Minder mensen nodig
‘Dat we de mogelijkheden van industry 4.0 bij nieuw te bouwen installaties zo veel mogelijk gaan benutten, is een no brainer’, stelt Marinus Tabak, directeur central asset management van RWE. Bij nieuwe installaties, zoals een groene waterstoffabriek of een offshore-windpark is het relatief eenvoudig om nieuwe technologische mogelijkheden mee te ontwerpen. Dan is het volgens hem gemakkelijker om all the way te gaan. ‘We zullen ook wel moeten’, benadrukt Tabak. ‘De druk op de technische arbeidsmarkt is nu al zeer voelbaar en die zal alleen maar toenemen. Digitalisering kan er sowieso al voor zorgen dat we minder mensen nodig hebben.’ En de mogelijkheden worden steeds uitgebreider. ‘Vergeet niet dat de OEM’ers, de
bouwers van de installaties, ook niet stil hebben gezeten. Zij komen met steeds geavanceerdere oplossingen.’
Op afstand
Tabak heeft al de nodige ervaring met slimme industriële technologie. De Eemshavencentrale, waarvan hij tot vorig jaar plantmanager was, behoort tot de nieuwste en dus meest moderne energiecentrales van Nederland. Daarin zijn al relatief veel snufjes ingebouwd. Maar ook bij oudere installaties heeft RWE op dit vlak niet stil gezeten. ‘De energiecentrale in Moerdijk wordt bijvoorbeeld grotendeels bestuurd vanuit Geertruidenberg.’ Het helpt natuurlijk wel dat er door de transitie meer momentum ontstaat om de mogelijkheden die er al zijn te benutten. Zoals ook Covid een versnelling bracht op dat gebied. De hele samenleving zat in een mum van tijd in Teams, Zoom of iets soortgelijks en energie-en chemiebedrijven zetten versneld stappen in het op afstand opereren van de installaties. Zo ook RWE.
Belangrijkste uitdaging
Toch zijn de ideeën daarover niet alleen van de laatste paar jaren. Tabak: ‘Drie of vier jaar geleden hebben we intern al eens het gedachte-experiment gedaan met een nieuw te bouwen gasgestookte centrale. We hebben die helemaal uitgedacht tot en met inspectiedrones aan toe. Alles erop en eraan.’ Volgens de RWE-directeur is het eigenlijk niet zo heel erg ingewikkeld om veel data te verzamelen. ‘De belangrijkste uitdaging is om uit al die gegevens ook waardevolle informatie te halen waarmee we onze installaties kunnen verbeteren en beter kunnen opereren. Dat zal bij nieuw te bouwen installaties ook de belangrijkste uitdaging zijn.’ ■
Selectie en inbedrijfname van sensoren wordt simpeler
We raken eraan gewend om bij het kopen van een product zelf online een eerste selectie te doen. Ook bestellen we steeds meer online. Bij de aankoop van sensoren doen we dit nog nauwelijks. Daarvoor is veel kennis nodig. Door te streven naar eenvoud, bij de selectie van de sensor én bij de inbedrijfname, brengt VEGA dit concept ook naar de instrumentatiewereld.
Wat doe je als je koelkast kapot is? Je surft eerst op het internet om te onderzoeken wat het aanbod is. Je vergelijkt de mogelijkheden en prijzen en maakt uiteindelijk je keuze op basis van de informatie die je hebt verzameld. Bedrijven als Coolblue spelen daar perfect op in. Ze presenteren eerst hun complete aanbod. Via een aantal vragen over bijvoorbeeld het gewenste merk, het energielabel en de maten blijven er nog maar een paar mogelijkheden over. Ze maken het voor hun klanten heel gemakkelijk om tot een keuze te komen die precies aansluit bij hun behoefte. Dit concept ontwikkelt VEGA nu ook voor haar klanten. ‘We willen dat iedereen, met of zonder verregaande kennis van zaken, via onze site de juiste sensor kan kiezen’, vertelt business development manager Rob Smulders. VEGA is leverancier van niveau- en drukmeters. Het bedrijf heeft ervoor gekozen zich te specialiseren in deze
Productieprocessen worden steeds complexer. Daarom is het belangrijk dat de meettechnieken die worden gebruikt om deze processen te monitoren steeds intuïtiever worden. VEGA ontwikkelt daarom meettechniek die gemakkelijk te installeren en bedienen is en die maximale veiligheid en betrouwbaarheid biedt. Het bedrijf is onder andere actief in de chemische, farmaceutische en voedingsmiddelenindustrie. De procesinstrumentatie van VEGA wordt vrijwel overal ingezet, denk aan drinkwatersystemen, zuiveringsinstallaties, stortplaatsen, mijnbouw, energie-opwekking, olieplatforms, schepen en vliegtuigen. twee werkgebieden en daarbinnen ‘de best available technology’ te leveren.
Kennis
Smulders ziet dat steeds meer klanten de selecties voor sensoren zelf gaan doen en online beginnen te bestellen. ‘Ik verwacht dat het aandeel van online aankopen alsmaar groter wordt. Zeker de jongere generatie is het Coolblue-systeem gewend. Die zijn gewend te chatten of te mailen in plaats van te bellen. Het liefst willen die ook zelf online een instrument kunnen bestellen.’ Voor het kiezen van een niveau- of drukmeter is echter wel degelijk kennis nodig. ‘Je moet best veel weten om het juiste instrument te kiezen. Die kennis verdwijnt langzaamaan met de al wat oudere generatie. De zestigers van nu zijn opgegroeid met de pneumatiek, doorgegroeid naar analoge instrumenten en vervolgens naar digitale instrumenten. Ze weten waar ze op moeten letten en waar hun kennis eventueel tekortschiet. Ze vragen ons regelmatig om hun keuze nog even te checken.’ Volgens Smulders kan een foute keuze serieuze gevolgen hebben. ‘Dus hoe zorgen we ervoor dat iedereen een goeie selectie kan doen? Door het verhaal simpeler te maken. Ik zal niet zeggen dat je niets meer hoeft te weten, maar we zijn het wel heel erg gemakkelijk aan het maken.’ VEGA biedt nu een basic-pakket voor de minder veeleisende applicaties. ‘Dit is een eenvoudig opgebouwd kunststoffen instrument met altijd dezelfde procesaansluiting. Voor een heleboel applicaties is dit instrument goed, maar wil je bijvoorbeeld meten bij temperaturen hoger dan 80 graden Celsius, dan heb je de pro-variant nodig. Deze lijkt op de kunststoffen variant, maar is van rvs. Je kunt er grote flenzen op krijgen en zo’n vijfhon-
derd verschillende procesaansluitingen. Dan wordt het kiezen van je instrument al een stuk complexer.’
Altijd juist
De eerste selectie voor basic of pro is erg belangrijk. Smulders: ‘Vroeger kon het bij die eerste keuze al fout gaan en kwam je nooit meer bij het juiste instrument uit. Dat was een groot risico. Een voorbeeld daarvan is als je een instrument zoekt voor een medium als ammoniak. Hiervoor is een bepaalde frequentieband radarsensor nodig, andere doen het niet goed voor dit medium. Maar als je daar niet op wordt gewezen, kun je mooi de mist in gaan. Binnen ons nieuwe concept hoef je deze kennis niet te hebben, want je krijgt gewoon de vraag: zit er ammoniak in het proces?’ Door een aantal eenvoudige vragen in te vullen, komen klanten altijd bij het juiste instrument uit. ‘Kun je kiezen voor een standaard toepassing, dan kom je automatisch uit bij 80 GHz radartechnologie. Dat is voor jou de beste optie. Heb je echter een medium met aceton, ammoniak of vinylchloride, dan kom je bij een andere selectie van
mogelijkheden terecht. Daarna kun je via een keuzemenu de procesaansluiting kiezen. Hetzelfde geldt voor bijvoorbeeld de vorm, de maat en het materiaal. De vragen beperken het aantal mogelijkheden die aansluiten bij je behoefte. Zo kun je heel simpel en snel, zonder dat je een fout kunt maken, een sensor selecteren die altijd juist is voor jouw applicatie.’
Eigen chip
Het grootste deel van de oorspronkelijke modellen is hetzelfde gebleven. ‘We zijn wel bezig alle instrumenten een upgrade te geven, dat doen we telkens na een aantal jaren. De twee meest gebruikte sensoren hebben deze upgrade al gekregen. Er is een nieuwe, eigen chip in gekomen die we zelf hebben laten ontwikkelen. We zijn daarin dus niet meer afhankelijk van derde partijen en kunnen altijd voor voldoende voorraad zorgen.’ Ook is VEGA naar de laatste standaarden toe gegaan. ‘Alle instrumenten voldoen aan de IEC 62443-4-2-norm voor IT-veiligheid en de nieuwste SIL by design. De veiligheid van de instrumentatie is dus heel erg hoog geworden. Verder zijn we bezig ons pakket te comprimeren. Vroeger hadden we een sensor voor vaste stoffen en een sensor voor vloeistoffen. Dat is samengevoegd. Je kunt nu vaste stof en vloeistof met één type sensor meten.’ Ook aan het gemakkelijk in bedrijf nemen van instrumenten besteedt VEGA veel aandacht. ‘We zien namelijk dat ook die kennis afneemt. We willen er naartoe dat we een instrument toesturen, de klant hem inbouwt en hem daarna met drie of vier aanpassingen in bedrijf kan nemen. We streven naar eenvoud, in de selectie en bij de inbedrijfname. We schrappen daarom een hoop vragen die de klant vroeger moest doorlopen. Natuurlijk kun je nog finetunen, maar alleen de belangrijkste vragen voor een inbedrijfname worden gesteld. Alles wat nice to have is, daar kun je via de speciale parameters nog bij.’ Daarnaast gaat ook de ontwikkeling van de technologie verder, stelt Smulders. ‘De volgende stap zal zijn om ook 80 GHz radartechnologie in te zetten bij hoge temperaturen, tot 450 graden Celsius. En hogere drukken. Er zitten nog een heleboel innovaties aan te komen.’ ■
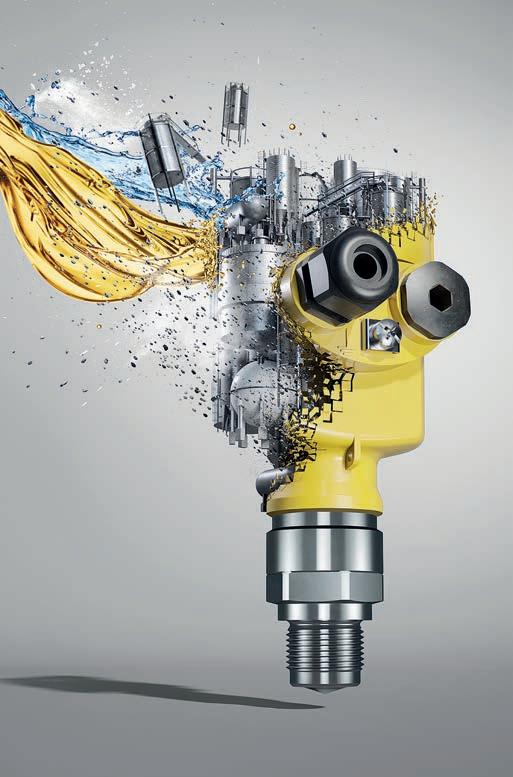