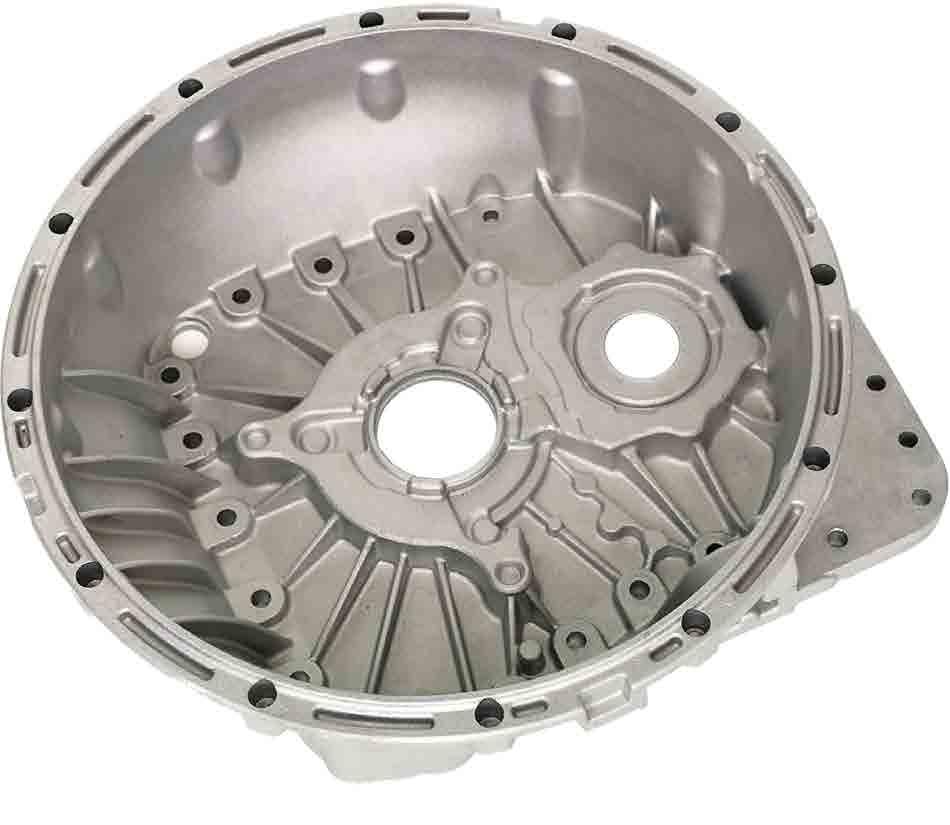
7 minute read
Bouncing back Metallfabriken Ljunghäll
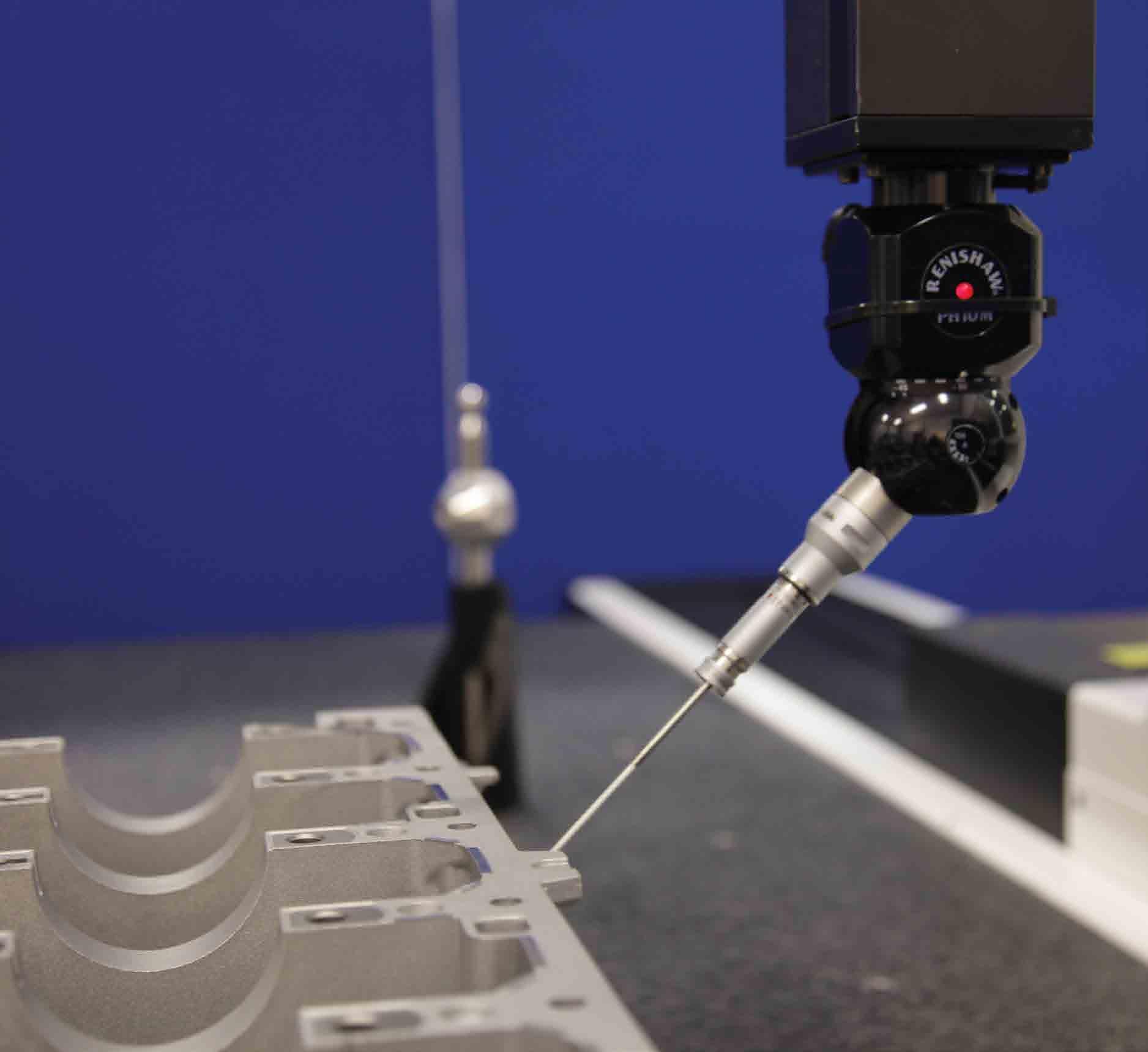
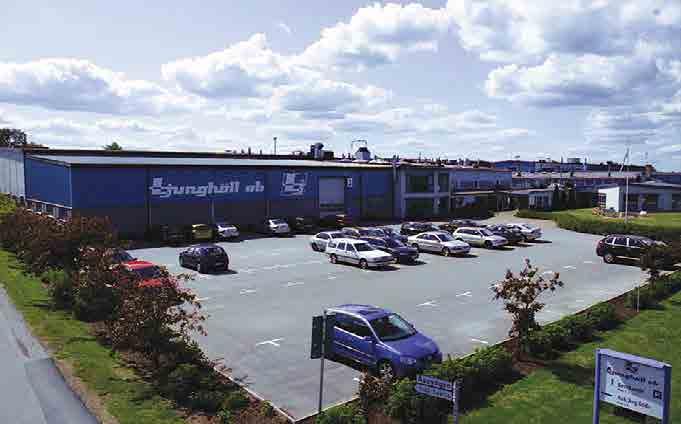
BOUNCING BACK
The Swedish firm Metallfabriken Ljunghäll AB manufactures high pressure die cast aluminium components for the automotive and telecom industries. Ljunghäll was hit by the recession, like much of the automotive sector, but demand is now recovering. Joseph Altham spoke to Ljunghäll’s CEO, Hans Linner, to find out why the company is well-positioned for future growth.
From its base in the village of Södra Vi, Ljunghäll supplies aluminium components to many of Europe’s leading car and truck manufacturers. The company makes aluminium parts using high pressure die casting, and specialises in powertrain and chassis components. The factory in Södra Vi is the largest high pressure die casting plant in Scandinavia, employing around 500 people and with a production floor space of 40,000 m2 .
Ljunghäll only makes components for other businesses, and its main customers, such as Volvo Cars, Volvo Powertrain and Scania, are located within Scandinavia. However, Ljunghäll wants to build up its business elsewhere in Europe as well. The firm already manufactures components for Audi, Jaguar and Daimler, and aims to increase its sales outside the Nordic countries. “One of our strategies is to grow further in the premium car segment,” said Mr Linner, “and to specialise in complex and difficult parts.”
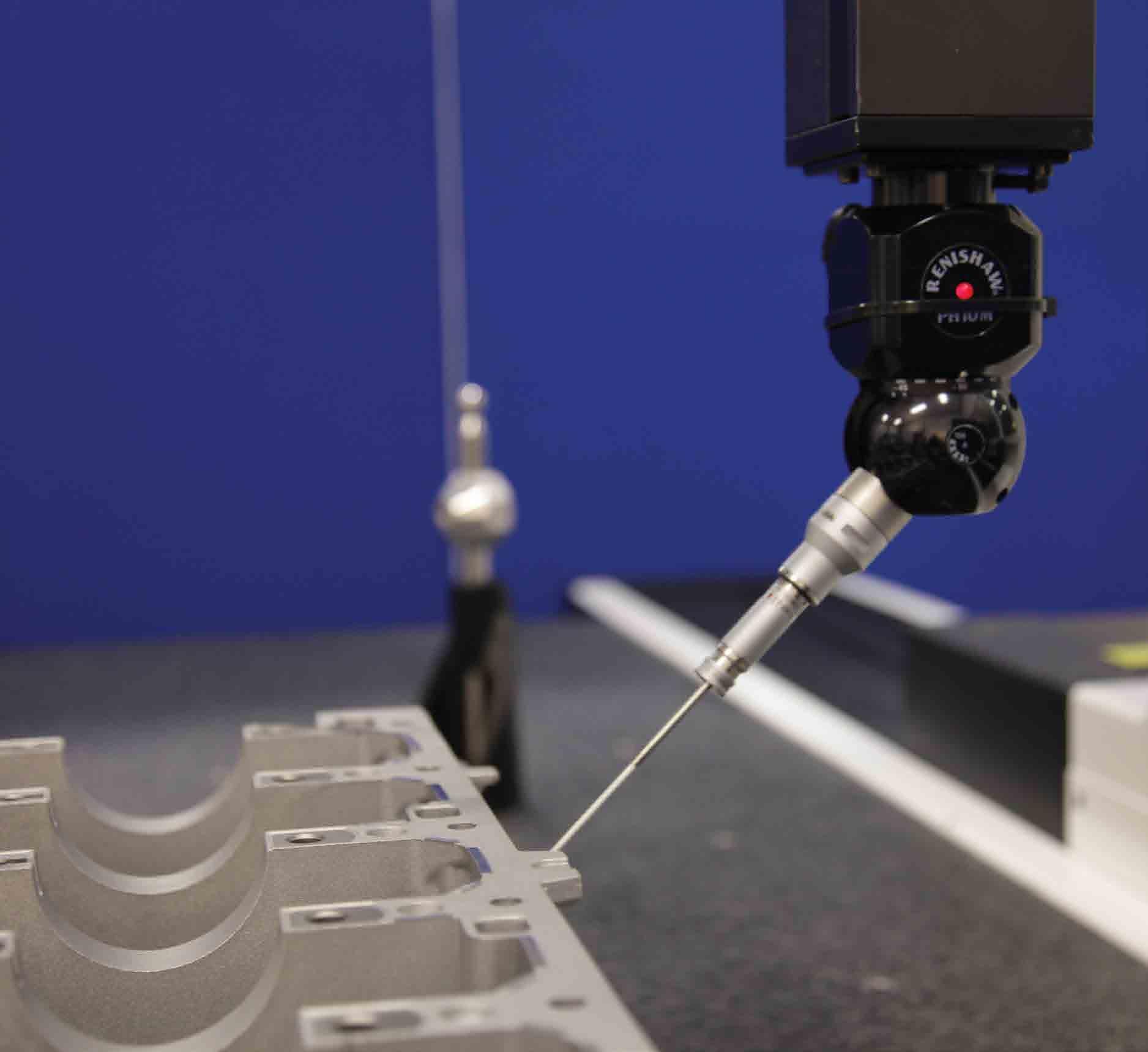
Quality
In the automotive sector, maintaining the highest standards of quality and reliability is vital. Ljunghäll’s quality management system is certified to ISO/TS 16949 ISO 9001, while its environmental management system is certified to ISO 14001. Working for the best names in the industry means that Ljunghäll has to be capable of delivering the best in terms of design. Customers require strong and durable components that at the same time will be as light as possible and make the most efficient possible use of raw materials. The factory at Södra Vi is equipped to satisfy these demands, with 40 die casting machines, 55 machining units for machining the cast pieces, as well as 100 robots whose job is to load the cast pieces onto the machines. The human factor also counts, and the company’s skilled engineers often work with customers to bring about improvements in the design of specific parts.
Mr Linner stated that the Södra Vi plant has built up special expertise in manufacturing thin-wall components. “We focus on thin-wall components with very low porosity. These parts have complex geometry and are trickier to manufacture. The process is not easy, but we have the advantages of long experience and a good knowledge base.”
Telecoms
Mr Linner stated that 15 per cent of Ljunghäll’s sales are to the telecoms industry. Ljunghäll makes aluminium parts for the wireless network, and one of the company’s main customers is Ericsson. These aluminium components, such as frames, covers and filters, are designed for radio base stations. Aluminium filters are needed to enable the base stations to transmit and receive the mobile phone signal. Ljunghäll
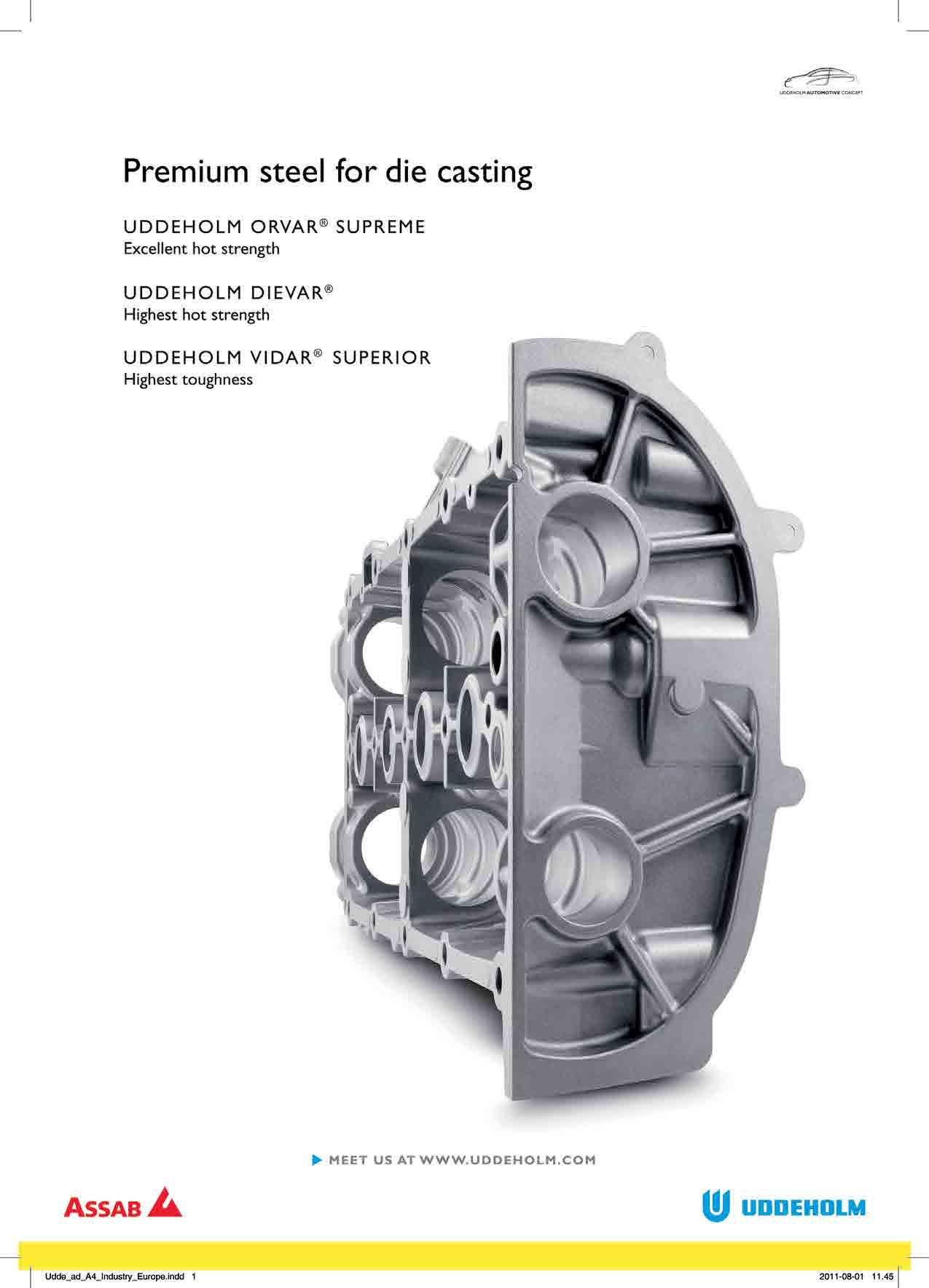

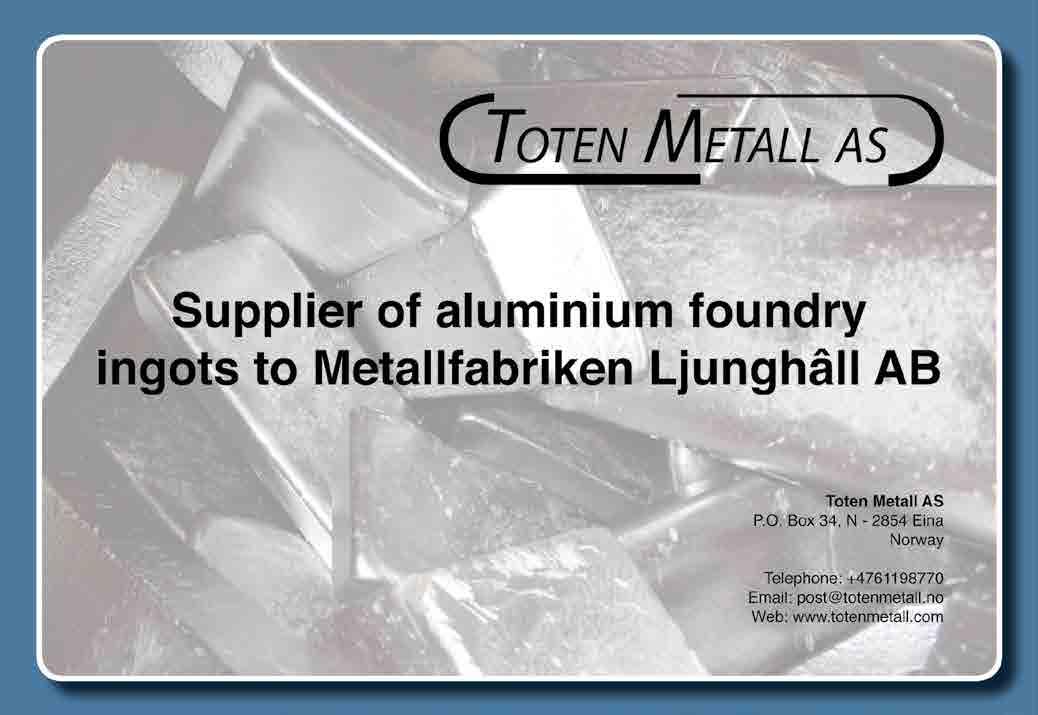
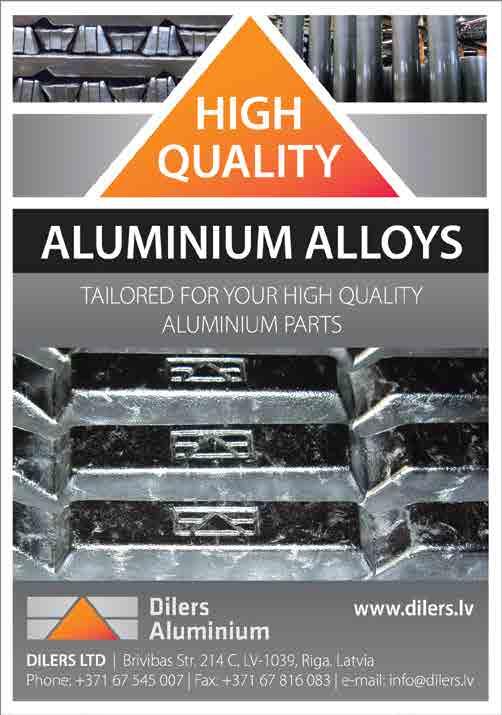
Swedish high quality tool steel improves your daily life
Cars, computers, medical equipment and millions of other products developed to improve and simplify our daily life are produced in a mould or die manufactured of Uddeholm tool steel.
Uddeholm is the world’s leading supplier of tooling materials, and related services. We produce and deliver high quality tool steel to more than 100.000 customers in almost 100 countries worldwide. The growing Asian Pacific market, are served by ASSAB Pacific, our wholly owned and exclusive sales channel.
Frontline of innovation
Uddeholm is constantly developing new products and we are known for delivering first class tooling materials with excellent machinability and a complete dimension program.
Our drive for development is improved tooling economy. As the tooling cost is, for example in die casting, 10% of the total cost of the finished aluminium die cast product, the validity of paying for high performance die steel quality, resulting in increased tool life, is obvious.
During the last years Uddeholm has focused on long run die casting production and the importance of a good property profile for the dies. The continued growth depends on a large extent on the greater use of die castings in the automotive industry where weight reductions are important.
Tradition of global thinking
Throughout our history, working closely with research and development together with our customers, has been a vital part of our business. Since 1668, Uddeholm has been associated with knowledge, innovative spirit and the special quality of Swedish steel. Generations of skilled craftsmen and professionals have laid the foundation of our present day products.
Early on, we established contacts with overseas customers. Our global thinking means that we will always be there wherever or whenever you need us. Our presence on every continent guarantees the same high quality wherever you have your business.
It is a challenging process, but the goal is clear – to be your number one partner and tool steel provider.
Richardssons Verktygsservice AB
Richardssons Verktygsservice AB is Sweden’s biggest manufacturer of pressure die casting tools. We have reached this position by focusing on the most important task of all: living up to the trust given to us by our customers during the 50 years we´ve been in business. Richardssons’ overall goal is to be a reliable supplier with the highest level of quality and expertise.
Richardssons make pressure die casting tools in all sizes and levels of difficulty, and we have the resources and skills for even the biggest and most complex tools. This means that we can manufacture tools that weigh from 500 kg up to a maximum total weight of 25 tons. Thanks to our machinery and personnel resources (with our 40 employees) and also to our business partners, we can also work on a large number of tools simultaneously. We can thereby offer our customers the maximum possible level of service and help to reduce the number of their subcontractors.
Toten Metall
Toten Metall, headquartered in Eina, Norway, was founded in 1992 and bought by the Norwegian group AS Oppland Metall in 2001.
Today we are the only producer of secondary aluminium alloys in Norway. All our alloys are manufactured on the basis of aluminium recovered from recycling all kinds of aluminium-scrap.
We produce around 13,000 tonnes of foundry alloys each year, all in the form of ingots. Our production takes place in two gas-fired furnaces with a capacity of 15 tonnes each. The majority of our customers are in Norway, Sweden and Denmark.
Our largest customer is Metallfabriken Ljunghäll.

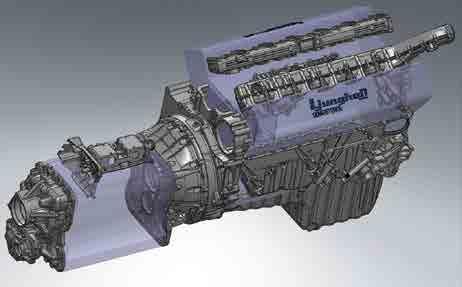
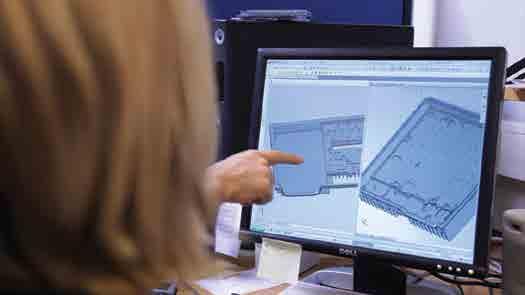
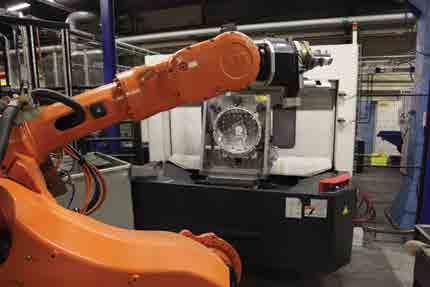
makes aluminium components for the 3G (third generation) network. More and more people are using smartphones to access data while on the move, and mobile phone networks have to be continuously upgraded. Ljunghäll therefore anticipates growing demand for its telecoms components in the future.
Čáslav
In 2007, Ljunghäll acquired a factory in the Czech Republic in order to obtain a foothold in central Europe. The factory in Čáslav employs 250 people and has 11 die casting machines. The Czechs have a long tradition of car manufacturing and a skilled workforce. At the same time, labour costs are significantly lower than in Sweden. To enable its customers to reduce their costs, Ljunghäll offers them the option of having aluminium components developed and perfected at Södra Vi for subsequent manufacture at the Čáslav site.
The Čáslav factory is helping Ljunghäll to enlarge its European customer base. “To support this strategy, we have decided to extend our Czech plant and to add new die casting machines and additional machining cells,” said Mr Linner. As part of a €15 million programme of investment, Ljunghäll plans to extend its factory in Čáslav by building a foundry with a total area of 6000 m2 .
Costs
In order to be able to offer a competitive price to Ljunghäll’s customers, Mr Linner has to keep a tight control over costs. Indeed, initially Ljunghäll transferred machines from Sweden to Čáslav rather than buying new equipment for the Czech facility. As Mr Linner explained, it took more than just money to integrate the Čáslav site with the rest of Ljunghäll’s operations. After the acquisition, the company worked hard to improve systems and processes at the Čáslav site and to introduce a logical way of working where responsibilities were clearly defined. Getting the factory in good shape, he says, was the key to achieving high quality of output. Even though Ljunghäll has emerged from the recession, the cautious approach Mr Linner has taken to his company’s finances is unlikely to change.
Overall, the outlook for Ljunghäll is positive, with interesting opportunities in the pipeline from the emerging market economies. “Our main goal is to support our customers in Europe,” said Mr Linner. “In the future, we will see if we can follow them within a global perspective. We are currently looking into how we can support their requirements in China and Brazil.” n