
5 minute read
The complete value chain Lech-Stahlwerke
THE COMPLETE VALUE CHAIN
The Lech-Stahlwerke GmbH is a steel plant and a recycling company at the same time, having already transformed over 26 mio tons of steel scrap into high-quality engeneering steel bars and rebars. Julia Snow spoke to the two management directors to hear more about the company’s expanding value chain.
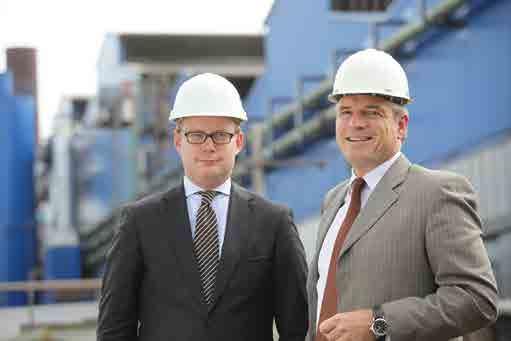
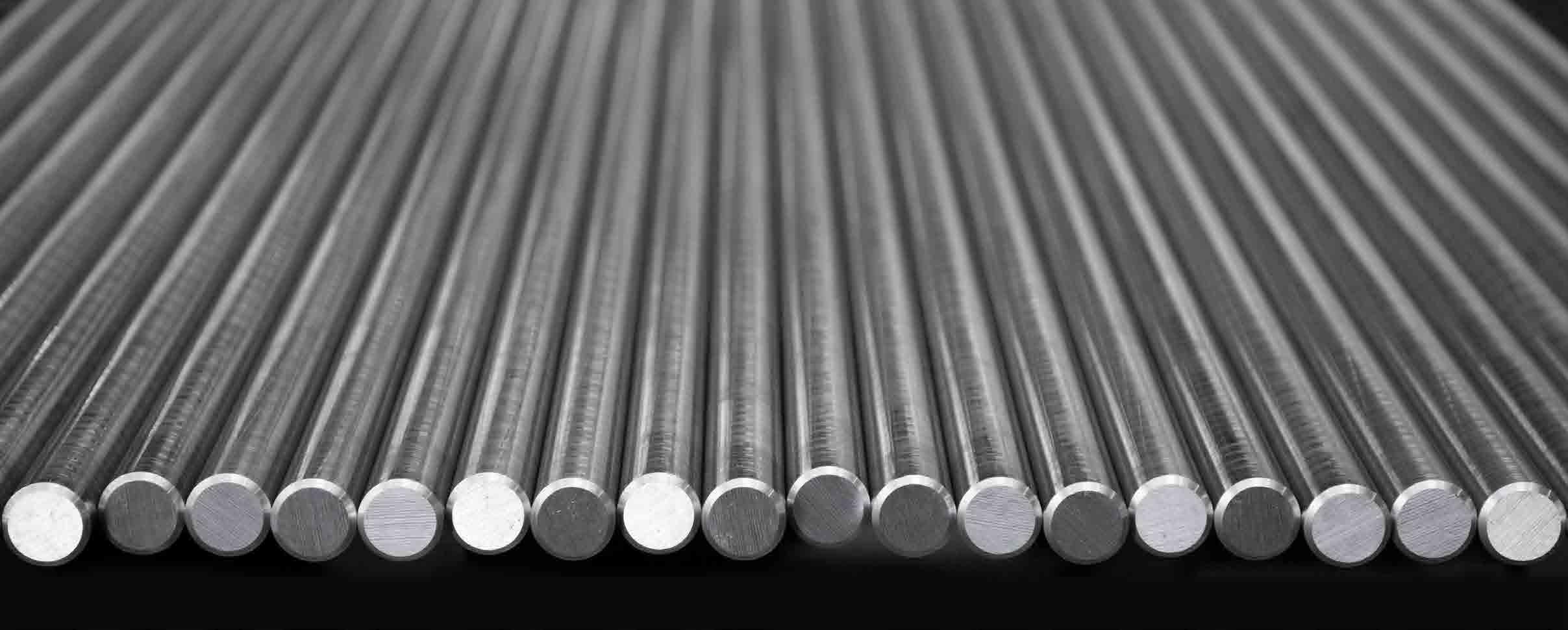
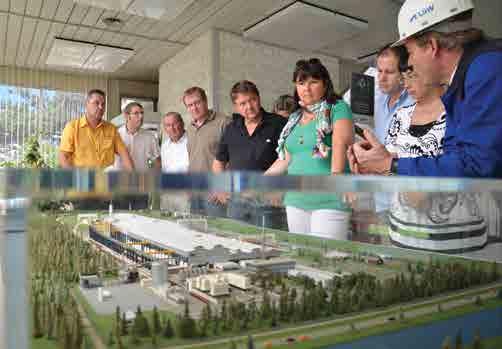
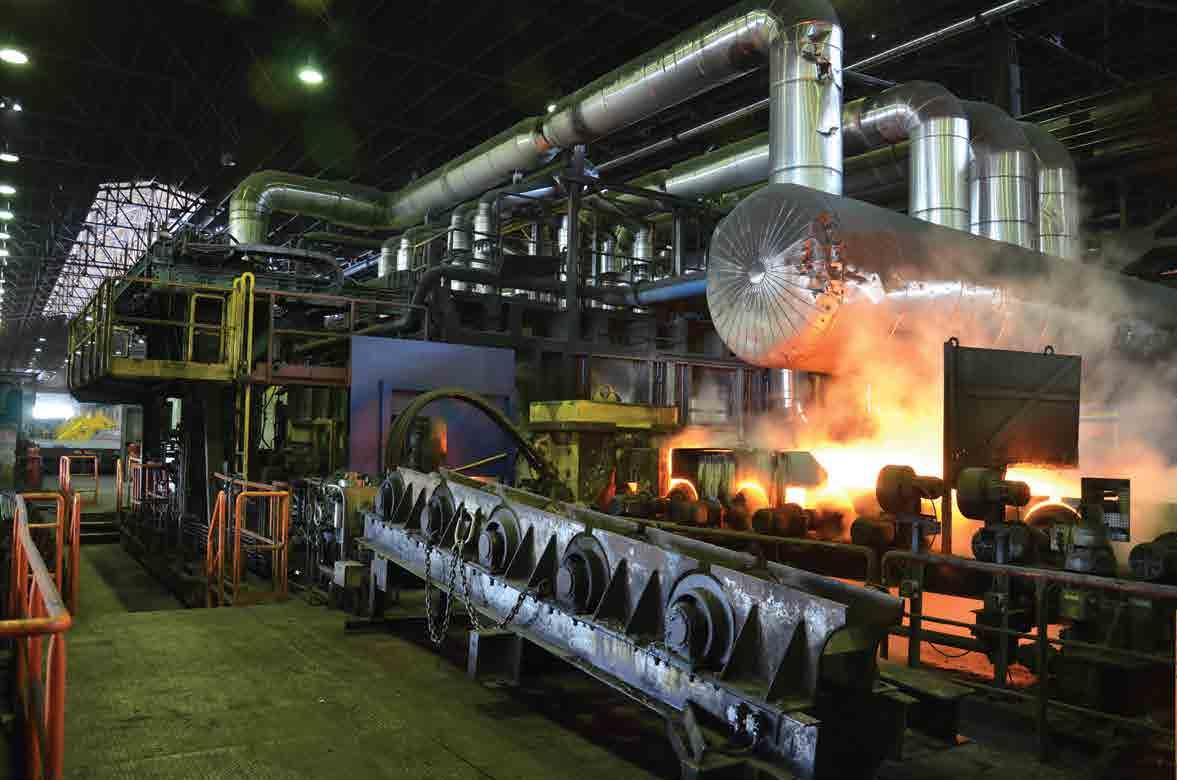
AS the only steel producer in Bavaria, Germany, Lech-Stahlwerke GmbH (LSW) turns out over 1 million tons each year, both as high-grade as well as rebars from its sites in Meitingen, Landsberg and Oberndorf. Right at the beginning of the interview management director Mr Bardosch draws attention to the company’s crucial strategic decision to extend the value chain: “It is most important that through our various subsidies we can now offer the whole steel value chain, from scrap metal recycling to production and distribution, including all the steps in between like logistics, processing and finishing.”
Over 40 years of steel history
The company’s operations began in 1970, with the foundation of the Bayerische Elektrostahlwerke by Luigi Giussani, who wanted to exploit the output of car scrap in Bavaria. Four years later the name changed to Lech-Stahlwerke GmbH, and Aicher KG began its involvement in the company which was gradually increased to the majority shareholding of 80 per cent in 1992. In 2002 the company celebrated an annual production of over 1 million tons of raw steel for the first time. Between 2004 and 2008 a range of investments boosted the technological capacities of LSW, including the introduction of the ultrasound testing in immersion, the purchase of a fully automatic spectrographic line and the installation of the first vacuum-degassing facility. Since 2008 the company has also used a modern scanning electron microscope.
Special bar quality steel – straight to the end customers
LSW started out by producing rebars, and until recently the major business was the sale of special bar quality steel directly to oem and also to automotive suppliers, who would in turn re-forge and process the material before selling it on. Management director Dr Heussen explains: “To grow over all LSW-GroupCompanies the strategic decision was taken to grow over the whole supply chain. We are investing to extend our offering at both ends, in the recycling of scrap and in the finishing processes with the specific focus on peeled bars. Today it´s obvious that this strategic development was completely right: in 2011 we had one of the best years in company history!”
In addition to the capacities in Landsberg, LSW is supporting this move with a major investment in the Oberndorf plant, where a new 3000m2 hall is going to house precision saws and modern induction heat treatment systems, which can produce exactly the type of finished steel bars needed by automotive customers.
Around two thirds of LSW’s business is in quality and special steel in thicknesses of 30-120 mm, says Dr Heussen: “Other major parts of our production capacity are send to the bavarian construction industry, but also to companies in Switzerland, Austria or Italy. Further more LSW-steel is provided in form of billets for our partner companies, Rohrwerk Maxhütte or the Stahlwerk Annahütte.” LSW has proudly announced that threaded Lech steel from Annahütte will be used for the reconstruction of the new World Trade Centre in New York.
“We have a ‘hidden export quota’, because we supply all the German automo-
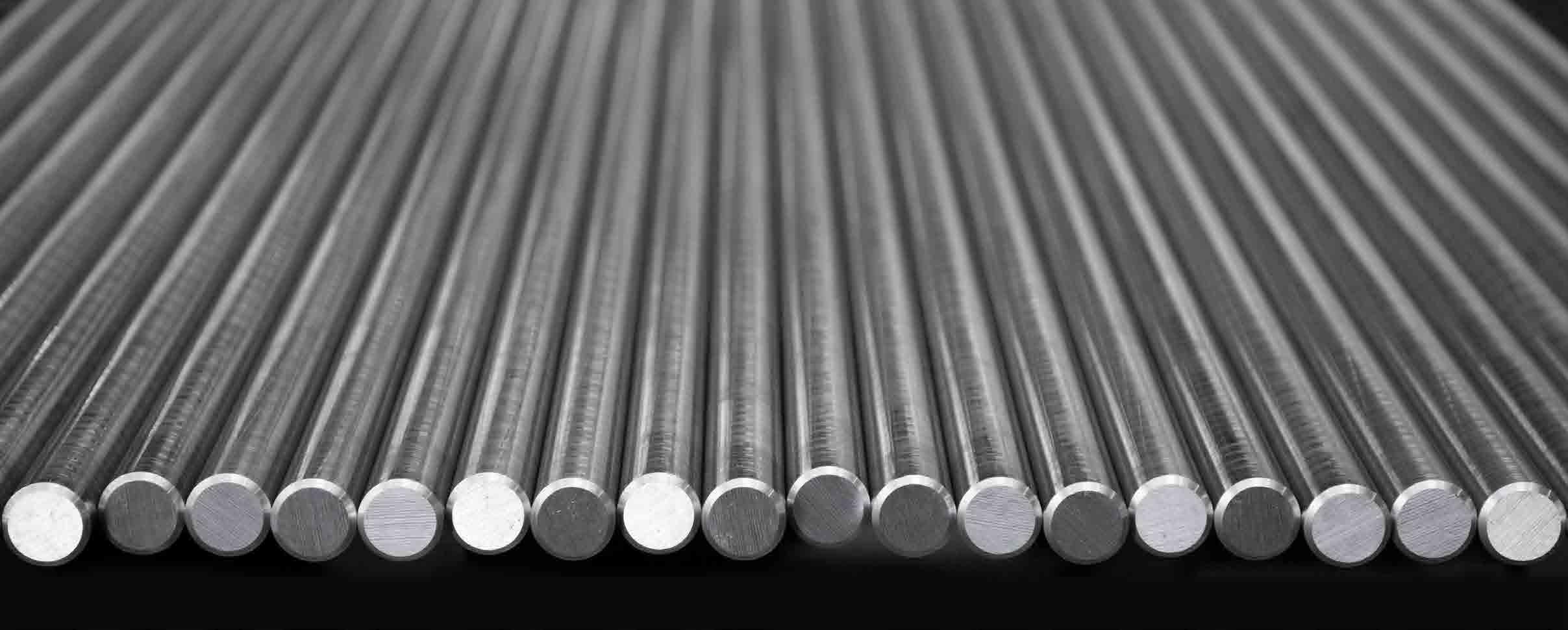
tive manufacturers, who in turn export 3 out of 4 of their cars - so while our customers may be in Germany, our products end up worldwide.” adds Mr Bardosch.
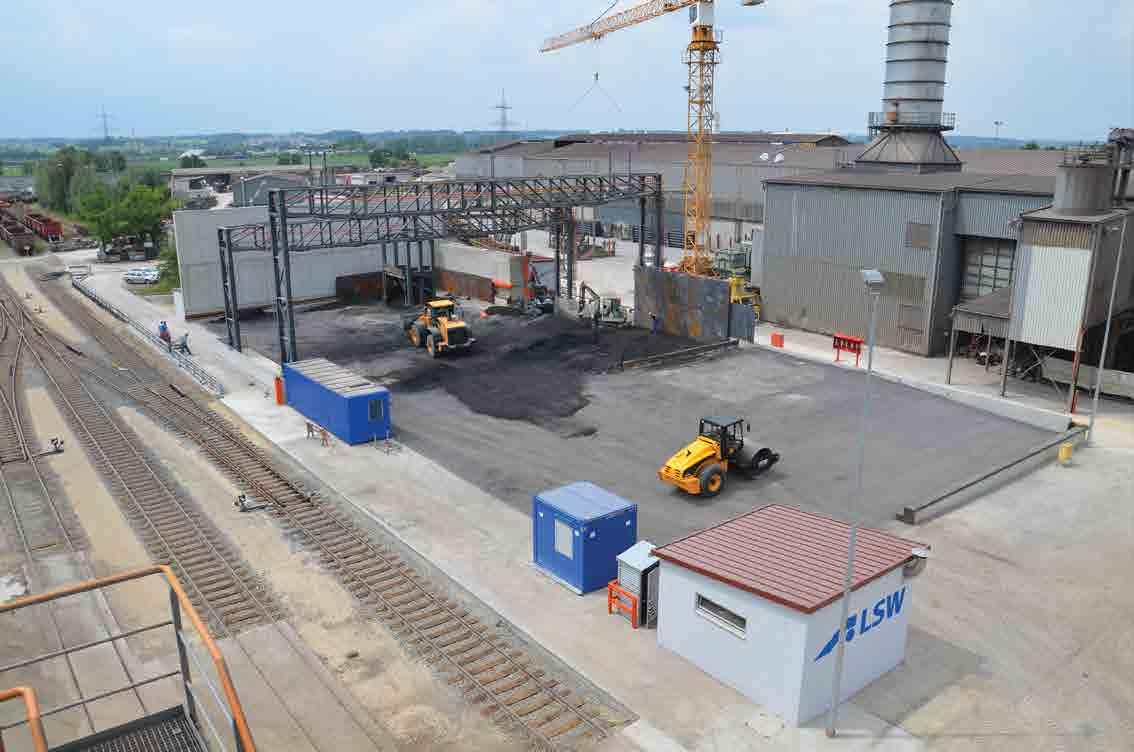
Sustainability at the top of the agenda
In the past years many investments in environmental technology were made, the installation of a filter with a suction performance of 1,000,000m3 per hour and a cooling system with a heat exchanger saving about 80,000m3 deep spring water are examples. Noise reduction measures alone have totalled €1.2 mio: with the installation of a silencer on the roof, sound-insulating scrap bucket equipment and noise protecting walls.
“Our investments in measures to reduce noise, emissions and the use of resources are substantial. “We are very involved in the local community; for example we have a mentoring programme where our staff helps students from a local university, and we are active in charity work and sponsorship of local sports clubs and cultural events. Safety and sustainability are a priority for us and for our neighbours, as shown by our achievement with the new slag facility.” says Dr Heussen.
World’s first in slag treatment
“We started operating a new slag facility in June, which is worldwide the first and only facility that actually satisfies 100 per cent of environmental requirements.” reports Dr Heussen. The facility has a 1cm thick steel base and features an 80cm open maintenance area underneath the base, to allow access for regular controls, as well as an innovative sprinkler system that cools the slag and reduces the production of dust. “Because slag is increasingly important as a source of raw material we are sharing our knowledge and experience with others at an annual symposium. In October we are again inviting experts from academia, business and government who will explain how we can address the challenge of treating slag for recycling – a process that is still very cost intensive but that will become essential in the future.”
The strategic focus on the new business field of high quality finished steel products along with the commitment to keep improving the recycling process places the company right on track for the intended ‘growth by value chain extension’. n
M.T. LEGIERUNGEN GMBH - Feldstr. 22-40667 Meerbusch / Germany Phone: +49 2132 938910 - Fax: +49 2132 938915 - E-mail: mtl@mtl-legierungen.de
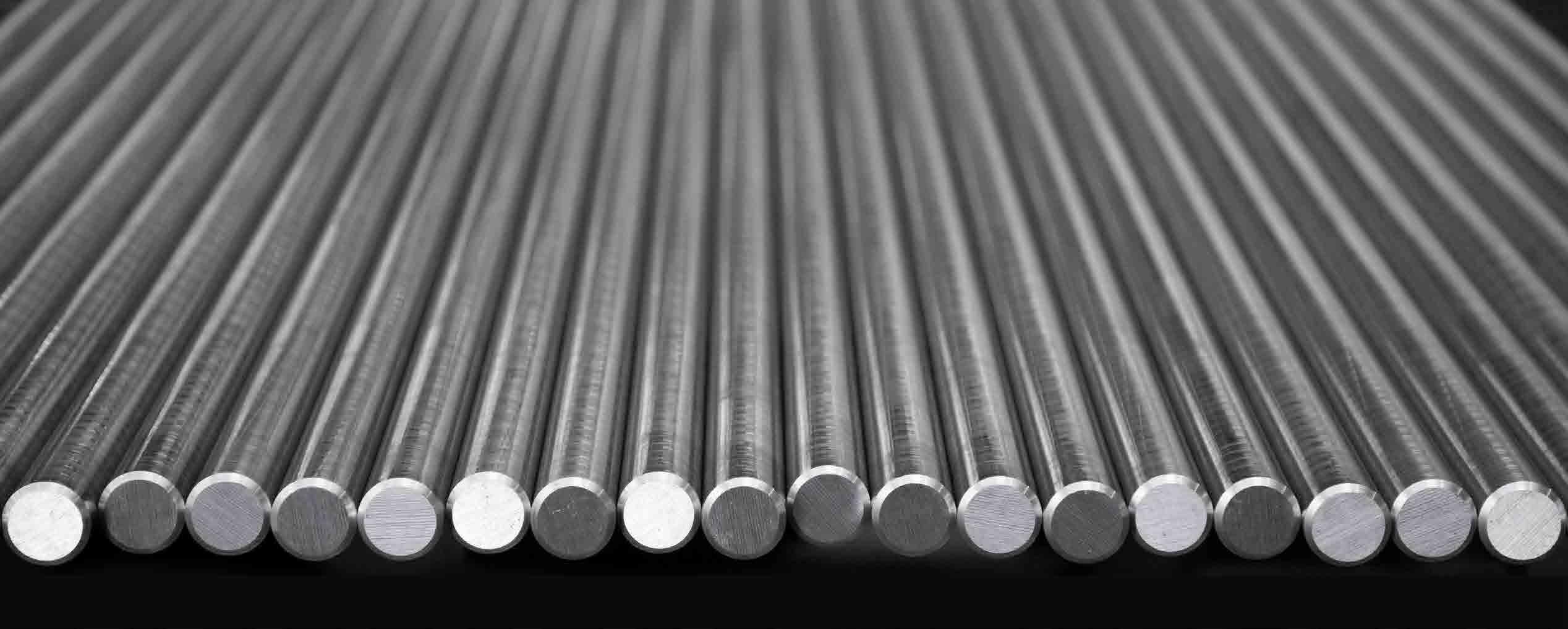
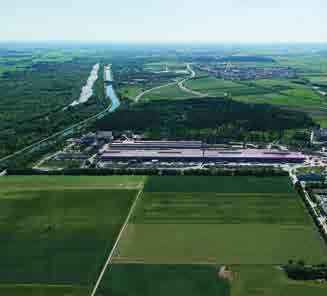
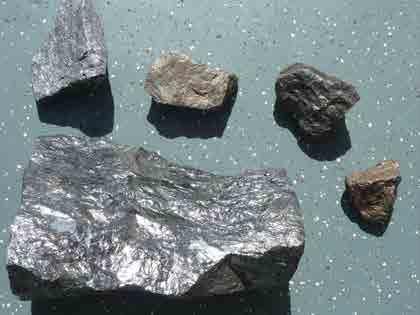
