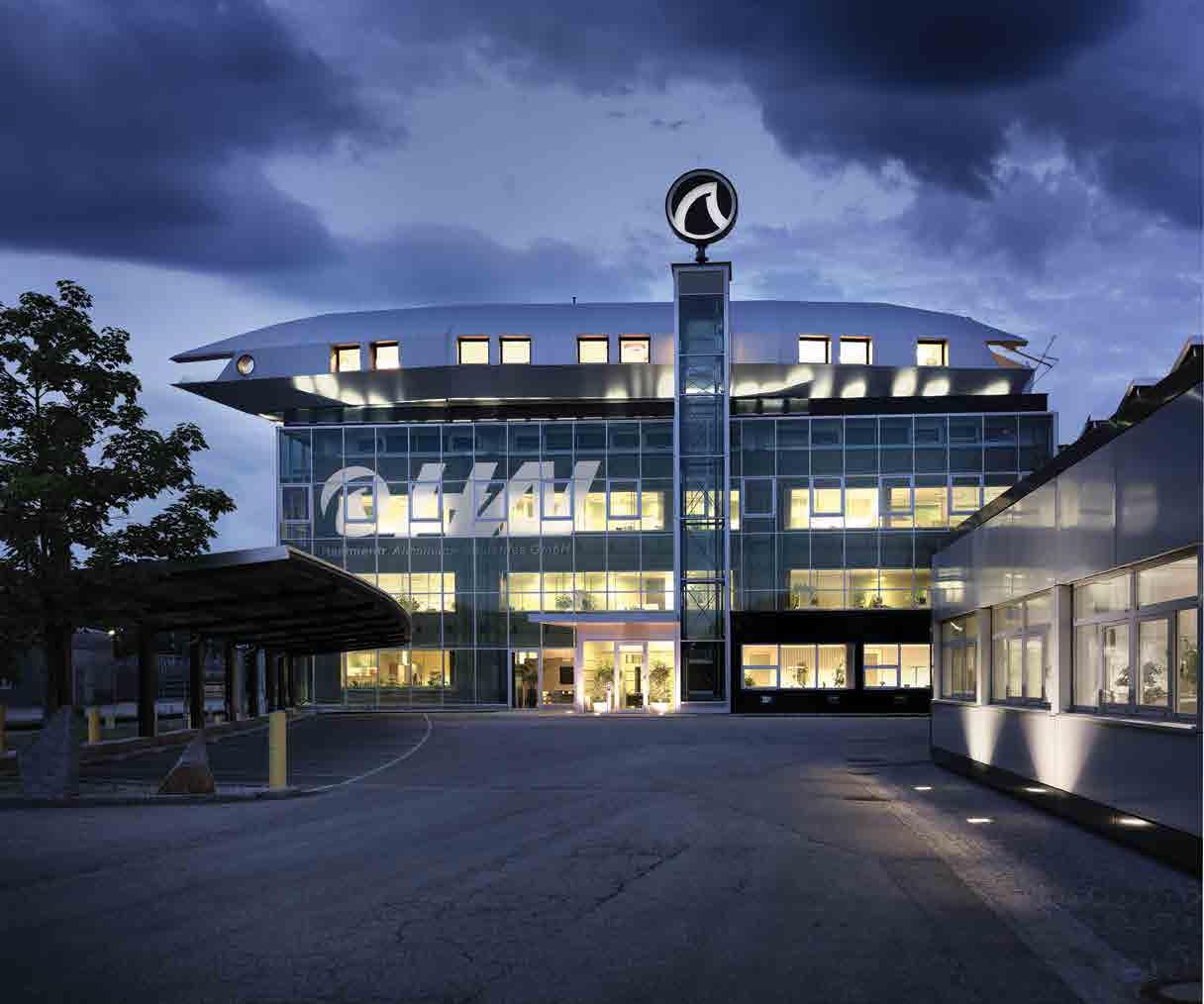
6 minute read
Extruding greater value HAI Group
EXTRUDING GREATER VALUE
The HAI Group is a market leader in the manufacture of advanced and complex aluminium components for niche markets. Philip Yorke talked to Rob van Gils, the general manager of the HAI Group, about its ambitious plans for growth and its latest casting, extrusion and welding technology.
The HAI Group (Hammerer Aluminium Industries) was created as the result of the Hammerer family taking over the casting and extrusion product divisions of AMAG in 2007, while in turn the Hammerer family yielded its interest in AMAG to Constantia Packaging AG. This strategic decision to produce extrusions in an autonomous company heralded the founding of the HAI Group and formed the springboard for its success.
Over the past five years the company has seen strong growth as a result of its strategy of combining its long-standing experience with young dynamics. The company has ample capacity for cooperation on large projects, which have been merged together with lean structures and rapid decisionmaking procedures.
The HAI Group headquarters are at Ranshofen, Austria, where aluminium has been manufactured since 1939. The company operates the most advanced casting furnaces and homogenisation plants in Europe and is continuing to invest heavily in new technology. Furthermore, the company operates four extrusion presses enabling them to produce profiles from 80g/m up to more than 20kg/m. A brand new machine park for customised additional fabrication is completing the range of products
It is not possible to make the kind of progress that the HAI Group has made in the last few years without offering something special. The company attributes its ongoing success to
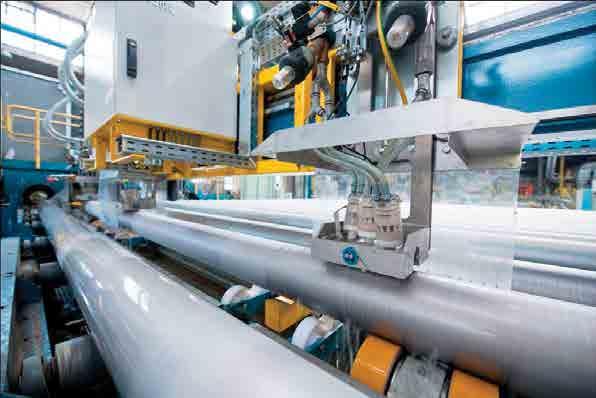
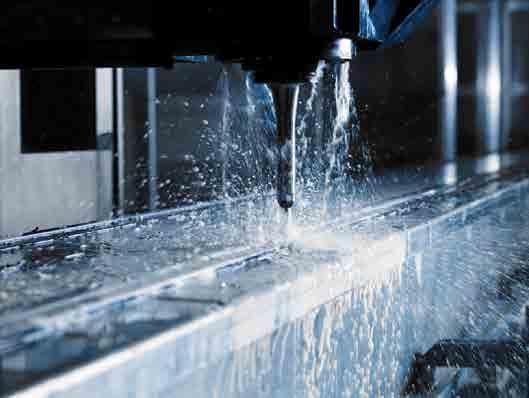
a number of business principles. The main driving force for success is considered to be its ‘Alu-plus principle’ which forms an integral part of the company’s business model. This principle (CIP = continuous improvement process) is based upon its commitment to optimising every stage of its manufacturing processes and to offer greater value, quality and efficiency to its customers. With its comprehensive experience and competence in extrusion design, its advanced welding technology and all its other aspects of processing, HAI is able to deliver product-orientated optimisation of any basic concept. In addition, the company offers a special consultancy service which reduces development costs in the process of extruding design and geometrical optimisation.
Mr van Gils said, “We are above all a dynamic and efficient company that operates two distinct business units. We have the casting division, which is involved in aluminium recycling where we buy raw materials in from all over Europe and produce billets and slabs for the extrusion and rolling industry. Currently this amounts to more than 150,000 tons per year.
“The second part of our operations is all about value-added services in which we take billets and extrude them into high quality aluminium profiles and complex components for a diverse range of industries. We are also able to offer ‘friction stir welding’ and there is only one other company in
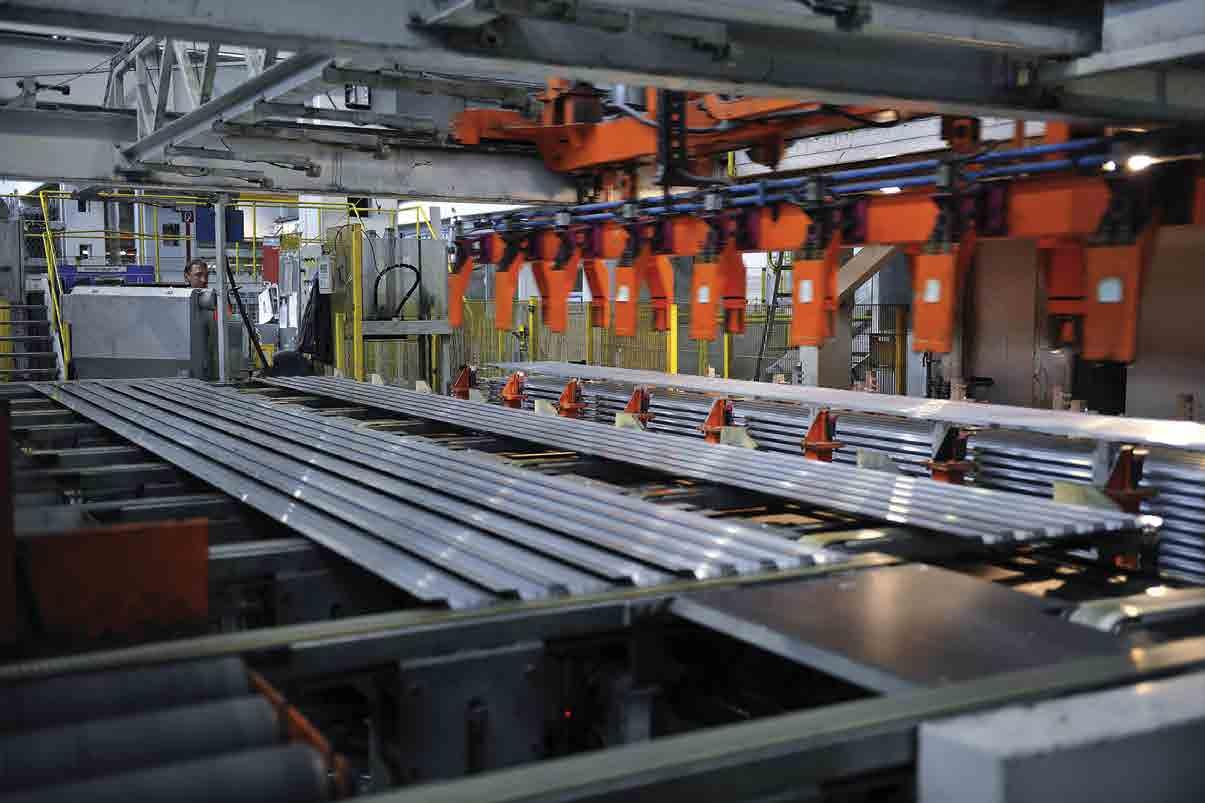
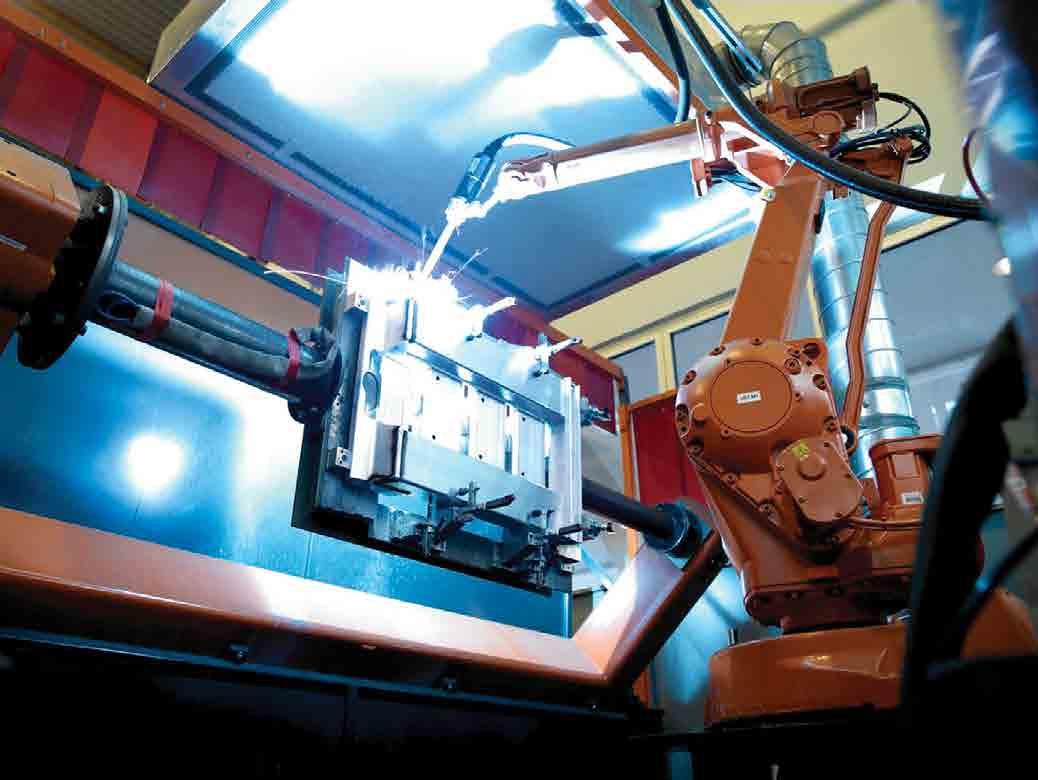
Hammerer Aluminium Industries (HAI) is one of Hertwich’s most important customers since many years. To date Hertwich has supplied the following equipment to HAI:
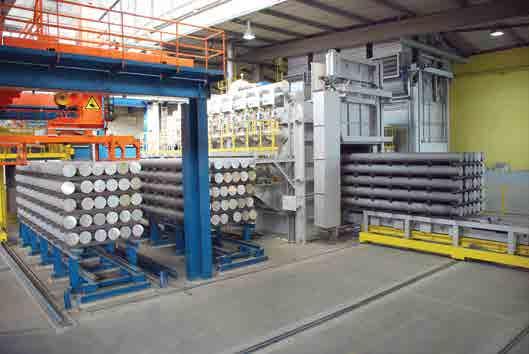
HAI Austria: HAI Romania:
Melting and Casting Furnace VCD Casting Machine Continuous and Batch Type Homogenizers Helical Ultrasonic Inspection Long and Short Billet Saw Complete remelt production line for 90.000 tpy comprising: 2 Melting Furnaces 2 Casting Furnaces VDC Casting Machine and Water Treatment Ultrasonic Inspection Long Billet Saw Universal Rotary Tilting Furnace (URTF)
Both HAI casthouses operate upon latest technology supplied by Hertwich. With close cooperation and permanent improvement efforts HAI is set to maintain their lead as most advanced and efficient remelters and billet producers.
Hertwich Engineering GmbH Weinbergerstr. 6, 5280 Braunau – Austria Phone: +43 7722 806-0 Fax: +43 7722 806-122 E-mail: info@hertwich.com www.hertwich.com Europe than can compete with us in this area. This precision process is ideal for extrusion components for the automotive industry, the rail industry and the transportation industries in general.”
Mr van Gils added, “The whole procedure of friction stir welding was invented in a Cambridge University laboratory in the UK. Our company identified its value early on and invested in the technology, which has resulted in this process being one of our main drivers for growth. Today we are supplying all the well-known European car and railway manufacturers with components and offer complete solutions in friction stir welding technology. Currently we are in a phase where we are consolidating our dynamic growth over the last few years, and have more than doubled our capacity and our turnover.
We are also in the process of upgrading still further our extrusion plants to offer optimal value to our customers and in the process we are adding to our value chain across the board.
“We have also moved into a higher-value end of the market. Our state-of-the-art milling centre can produce aluminium components up to 20 metres long and to the highest standards in the industry. I believe that the main difference is that we are a family
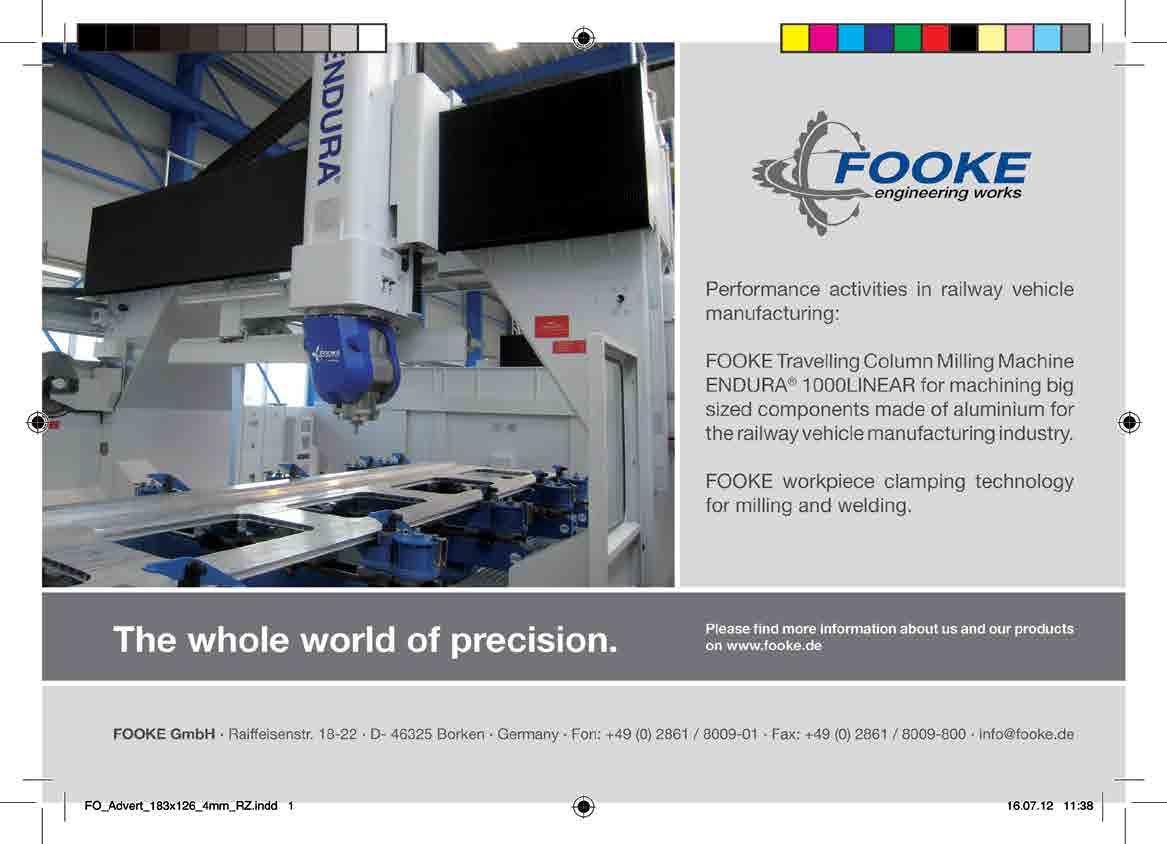
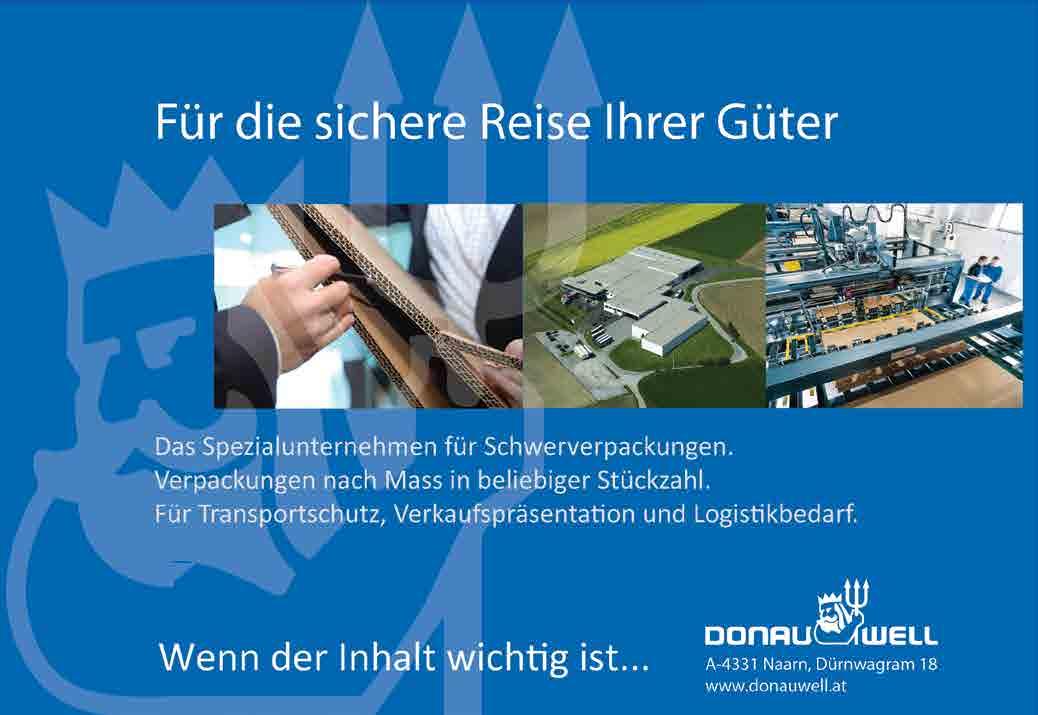

run business and can offer greater flexibility as well as making investment decisions in days rather than months as with many other companies. We are also committed to caring for the environment and work with specially designed furnaces to minimise our carbon footprint using the most efficient filters and energy efficient processes, which in most cases are fully automated operations.”
Investing in the future of SBU casting
The HAI Group has been making significant investments to ensure that it retains its premier position in the industry in the future. In 2009 the company invested in a new plant in Santana, Romania, with a total investment of more than €30 million and added another €10 million to this with its expansion of its processing plant at Ranshofen in Austria. The company’s main objective is to modernise its existing facilities still further to achieve higher value-added products and services for its customers.
During the past five years HAI has more than doubled its capacity within SBU casting, where extrusion has been the main focus and additional machining and welding technologies have been implemented. These ongoing investments have positioned HAI in the market as a reliable partner that is able to offer comprehensive solutions to the aluminium industry. During the next five years the company expects to see similar growth in its key markets and where special solutions and value-added services can be optimised. The strongest growth is likely to come from the automotive, rail and transport industries. Today the HAI Group is one of Europe’s biggest recyclers of aluminium and offers its customers exceptional value-added services along with high quality extruded profiles and complex components. n
