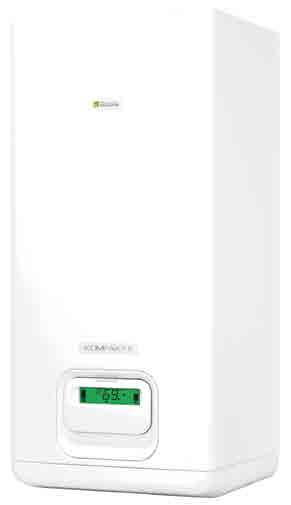
9 minute read
Advanced heating technology
Riello Urzadzenia Grzewcze SA of Torun, Poland, is one of the most important manufacturing plants in the Riello group. The group, of Italian origin, is a leading European producer of heating systems and technologies. Beretta boilers, manufactured in Torun, are one of Riello’s best known brands. Dariusz Balcerzyk reports.
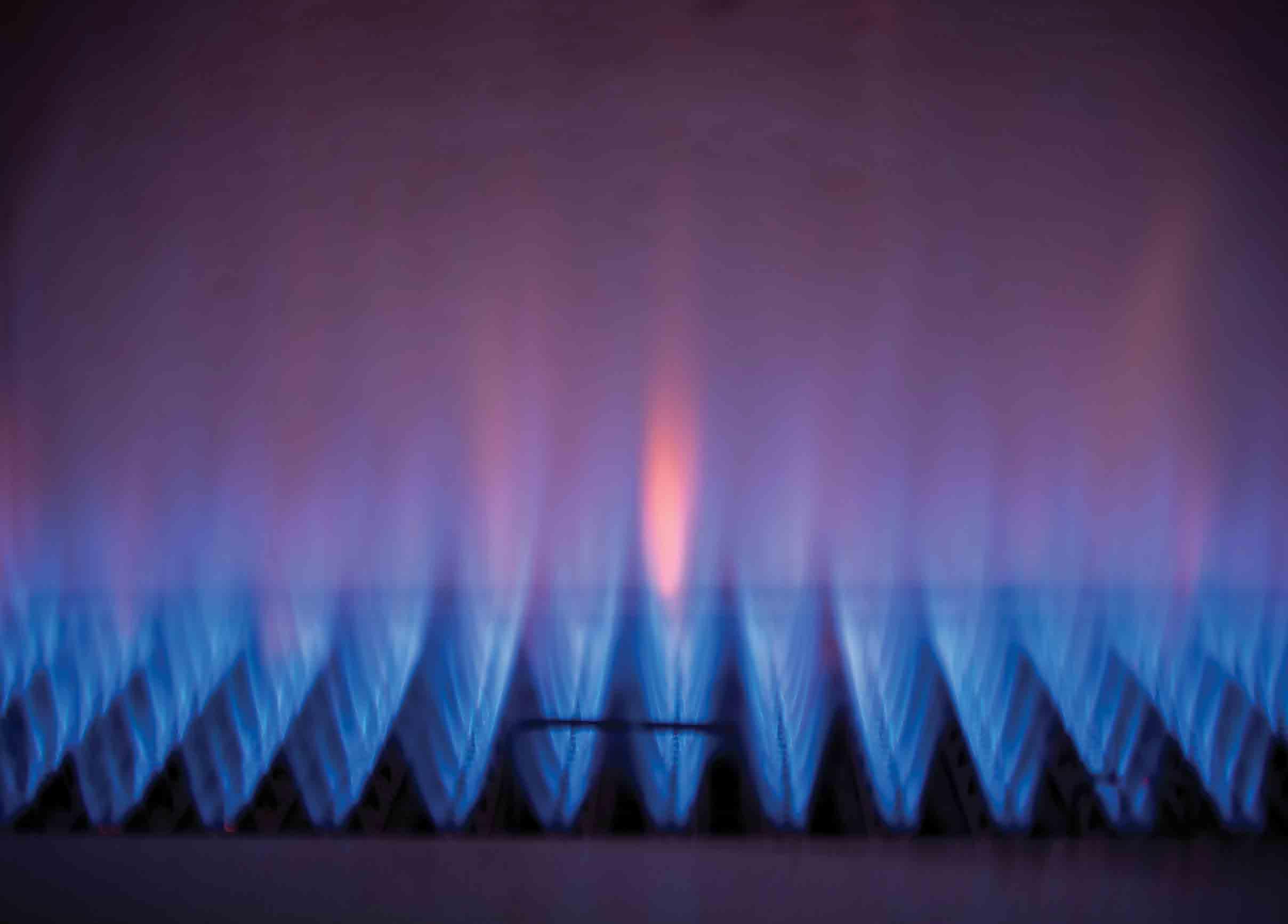
Riello Group is the world-wide leader in the production of burners and one of the major European players offering products and services in the heating and air-conditioning market. The company mission is to optimize comfort where people live and work, by proposing projects and solutions able to create the perfect harmony of climate, thanks to the integrated systems and services which are always focused on the impact on the environment.
The group takes pride in its nine production sites, provides employment for 2,200 people, owns four operations abroad, has a commercial network comprising 13 international companies and has customers in more than 60 countries. Riello owns two modern research and development centres, too.
Annual demand in the European boiler market is estimated as 5 million pieces. The Riello Group’s average share in each European country is about 10 per cent. As the numberone manufacturer in the global market, Riello produces around 500,000 burners, 450,000 wall-hung boilers, 150,000 water heaters and 70,000 floor-standing boilers per year. Wall hung boilers and water heaters make up around 50 per cent of the whole production: burners and units 23 per cent, floor standing boilers 9 per cent, air conditioners 6 per cent, and other products 13 per cent.
Focus on boilers
The vast range of Beretta products includes: gas-fired boilers, condensing boilers, boiler auxiliary equipment, air conditioning systems, under floor-heating systems, and solar systems. The factory in Torun is mainly focused on producing wall-hung boilers, and water heaters.
Condensing boilers are by far the most efficient and economical boilers in the market. The term ‘condensing’ is derived from the creation of condensation within the boiler. The advantage of such boilers over non-condensing boilers is a reduction in fuel costs. It has an efficiency of around 100 per cent compared to about 91 per cent for a non-condensing boiler. This also reduces emissions of both carbon dioxide and nitrous oxide to extremely low levels.
However, offering a good condensing boiler is not enough in the modern world, because there is a growing demand to develop other kinds of energy, such as solar or wind energy. Today the company offers state-of-the-art technologies for the most sophisticated heating and air-conditioning systems, where it is working to set new standards in terms of efficiency, reduction of energy consumption and protection of the environment.
Beretta intends to remain one of the most important players in the market. This involves further development. The key idea is to adapt to changing conditions, and to anticipate future trends, such as a devel-
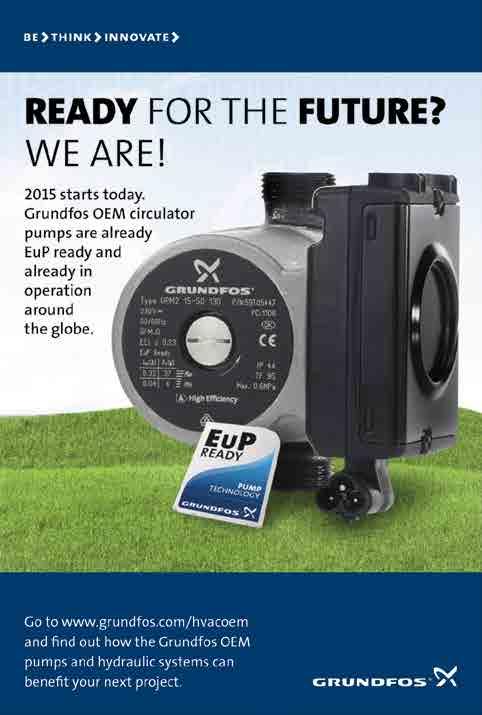
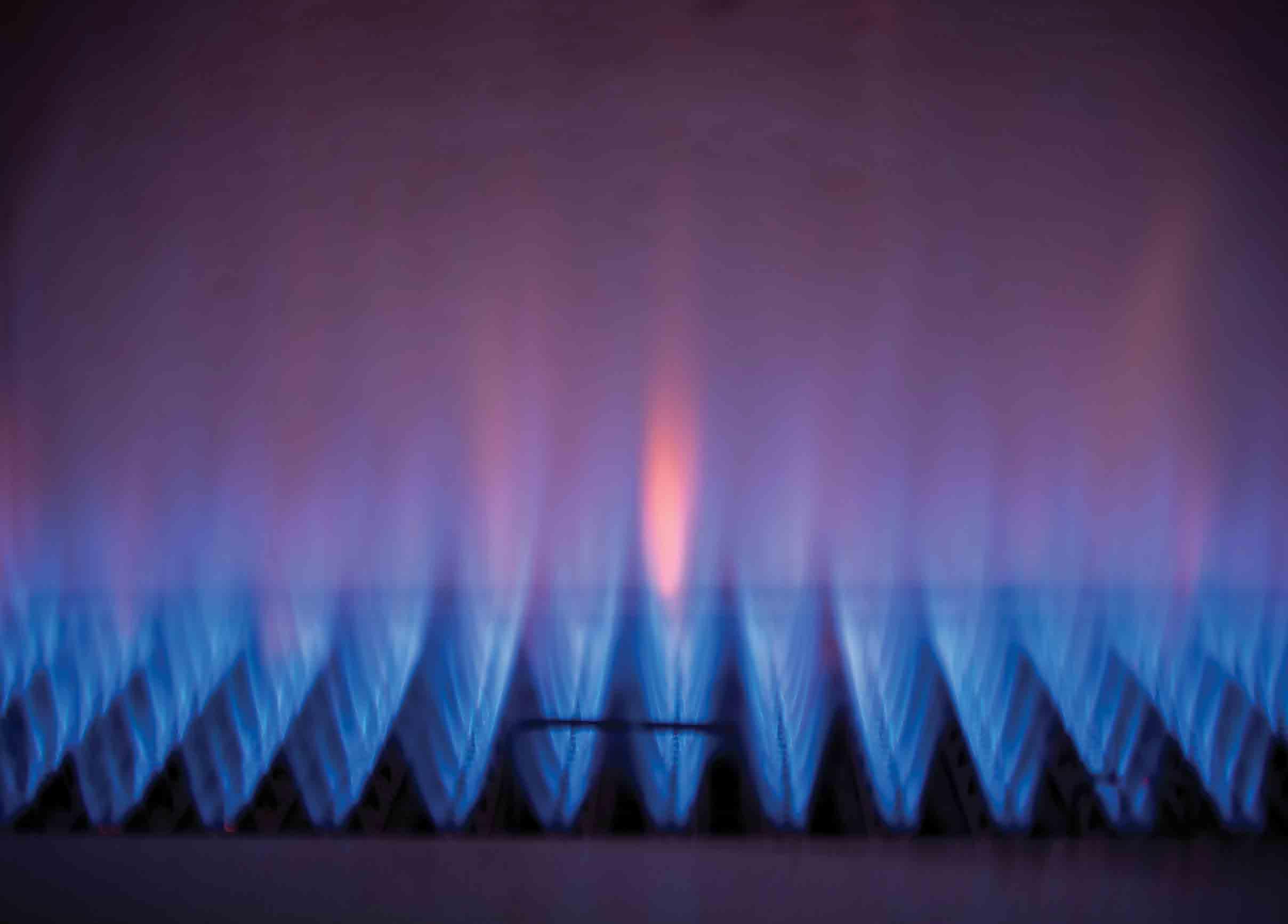
For over 30 years we are on the market with our production of ball valves and brass fi ttings for water and gas.
We are also qualifi ed suppliers to large groups such as tinkers Gruppo Riello, Ferroli Spa, Fonderie Sime Spa, Ariston Thermo Spa, Bitron Spa and so on and we have studied and developed various types of valves and taps according to the specifi c needs.
We are available for the construction of new studies and customers need with great fl exibility and speed of orders.
If you have any questions, please e-mail: Andrea: uff.tec@ruval.it Simone: uff.comm@ruval.it
RUVAL INTERNATIONAL SRL Via Sale, 123 Casella Postale N. 77 - 25064 Gussago (Brescia) - Italy Tel. +39 030 277 22 61 - 2 ◦ Fax: +39 030 277 22 63 ◦ www.ruval.it
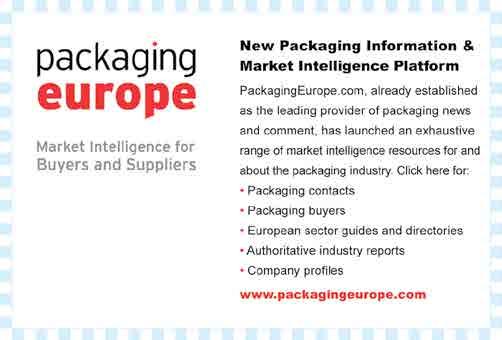
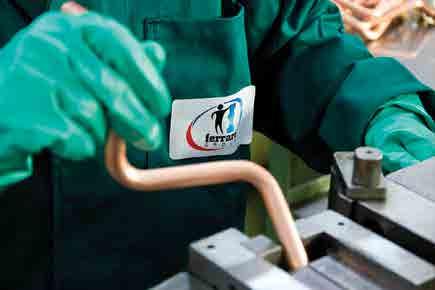
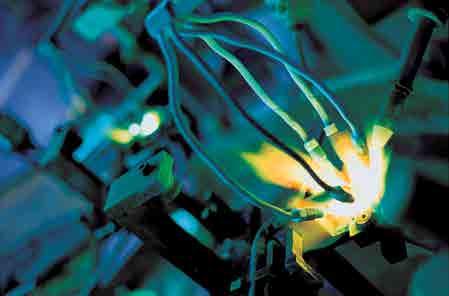
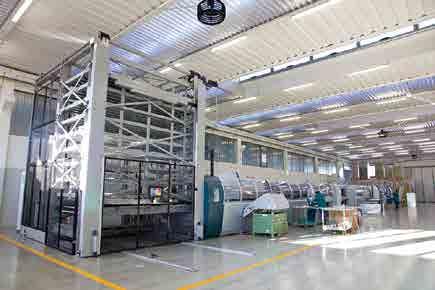
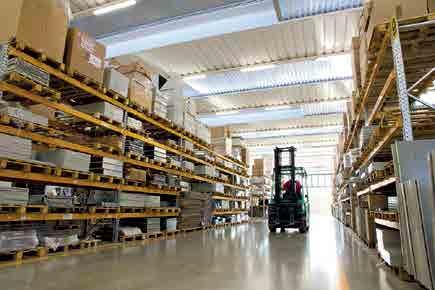
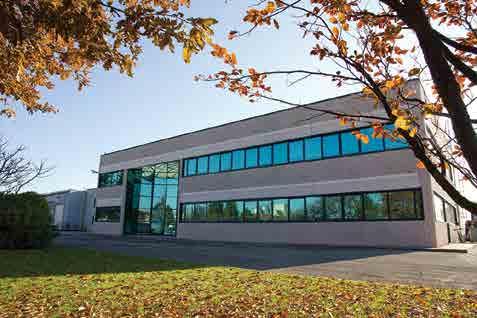
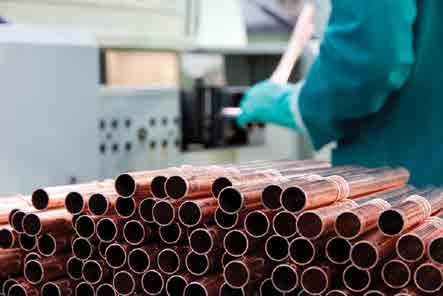
FERRARO GROUP The Ferraro group, for over thirty years, with its technology amongst the most advanced in the conduction of liquid and gas, manufacture components for use in numerous fields: heating, air conditioning, refrigeration and automation. For the past number of years the group has invested substantial amounts of capital in its air treatment department, and also for natural energy heating applications (Solar systems: vessels, refrigeration tubes). Our philosophy is not to be solely a supplier, but a partner capable of proposals and collaboration. This is carried out and applied also within the new departments within the group.
LMF LMF S.p.A represents the birth of the Ferraro Group and within its 4000 m2 the carries out the production of light metal-work operations, components for Central Heating Units and the new department dedicated to air treatment applications. Furthermore, Water to Water and accumulation exchangers are also constructed, using the necessary machinery and equipment. It also has press machinery equipment for moulding, forming and cutting of sheet metal. To complete the vast array of its product range, one can also count 3 Amada punching presses, CNC deformation machinery and punches of various capacities.
LMF Clima LMF Clima designs and manufactures, equipment and units for air-conditioning, heating and air-treatment systems. The company operates on a shop-floor of approx. 6200 sq. metres, using state of the art machineries. It supplies a wide range of products, developed to guarantee maximum comfort for ones surrounding environment. Unlimited possible solutions, which are ideal for many different situations. Whether used in the home, in commercial locations (offices, shops, bars or hotels) or on industrial sites, our products are particularly ideal for any task. The skill and professionalism of our technical staff, plus the perfect balance between quality and price, make LMF Clima an important reference point for thermo-technical studies and installers within the sector. Inside the Downloads section you can find the catalogs and all the material on our range of products.
INDUSTRIE FERRARO Industrie Ferraro S.p.A occupies itself with all forms of copper and steel tube forming to be utilised in domestic and industrial central heating units. Articles that have undergone a welding process, and by washing the pieces in this manner, may be zinc or nickelplated. The end result giving a visible aspect of extremely high quality. Its main strength that distinguishes the company from others is the quality found in its products: major attention to detail is placed high up in its priorities, and is rigorously checked in every phase of the material production process. A seemingly continuous arrangement of CNC machines, are used for the bending of copper, steel and aluminium tubes. Diameters utilized range from 4 mm until 32 mm. These machines, with the deformation of the tube possible with or without an internal punch, allow the realisation of articles from drawing repeatable many months later, with a simple recall and insertion of the coded program used, placed into the machines computer database. For those articles with high production turnover, the use of automated welding accelerates production is a possibility, whilst maintaining a constant and elevated level of quality. Complex pieces are welded by professional and qualified staff, and facilitated with braze-welding. Pressure testing (tested are carried out between 6 and 10 bar) is effectuated on tubing that the client requires, to be able to have the certainty of 100% leak-proof products. The internal quality control department oversees the verification and the acceptance of material from sub-suppliers, production drawings, and revealed measurements, assuring that the finished product exactly respects client requirements.
RAME CZ The RAME CZ s.r.o. company is in a possession of a comprehensive range of various pieces of equipment used for forming of pipes. Bending and pipe end forming is performed by powerful CNC bending machines including classic mechanical benders and special automatic presses. Technological processes utilized in the production of the pipes are as follows: cutting, notching, shaping of pipe ends by pressing, brazing, etc. The necessary pre- requisite of the production process as a whole involves control facilities where pipe dimensional checks and soldered joint tightness checks are per- formed. Based on the customer’s requirement it is also possible to carry out surface finishing of pipes using nickel plating, chrome plating, passivating, etc.

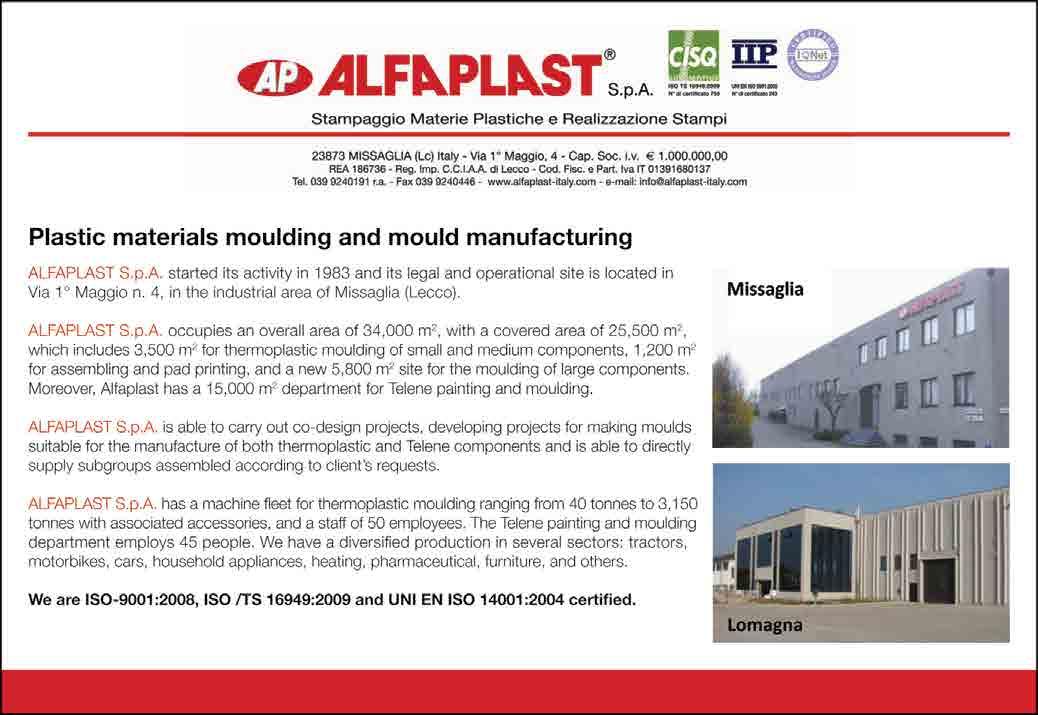
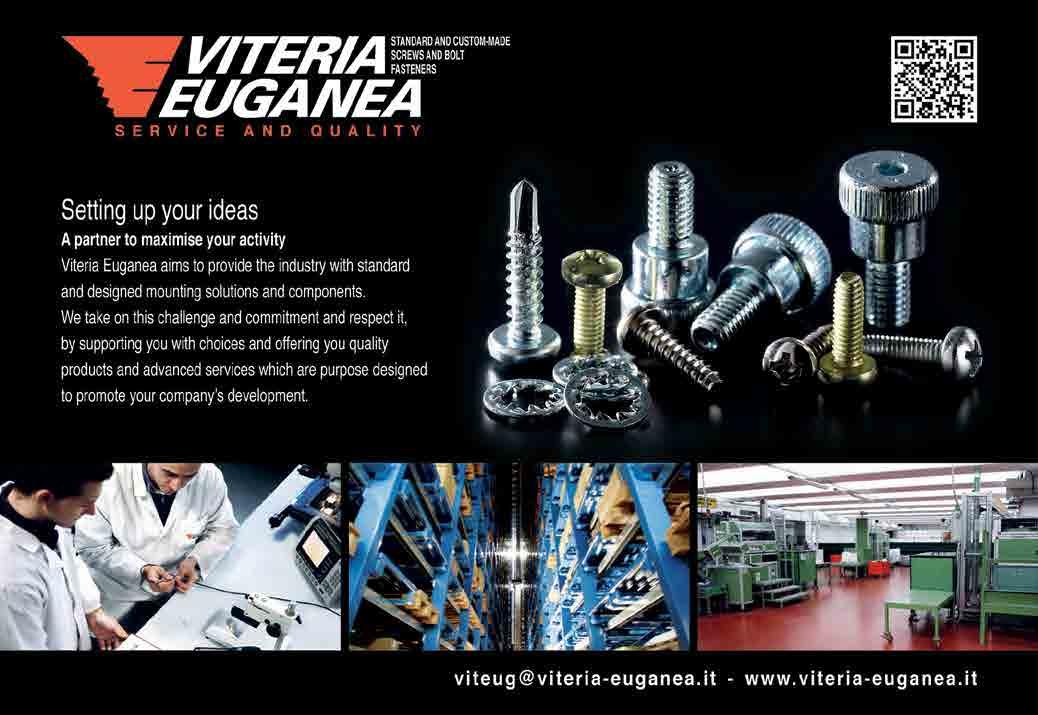


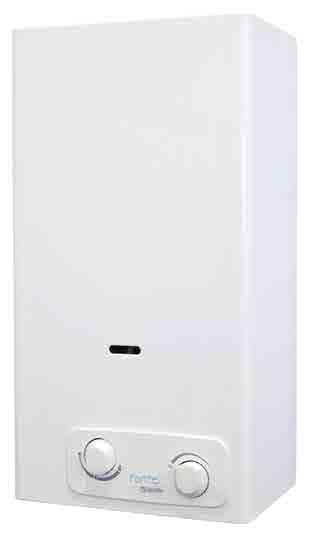
opment of the different kinds of energy production systems. The company’s objective is to be a leader in innovative integrated systems and applications for intelligent climate control.
Twenty years in Poland
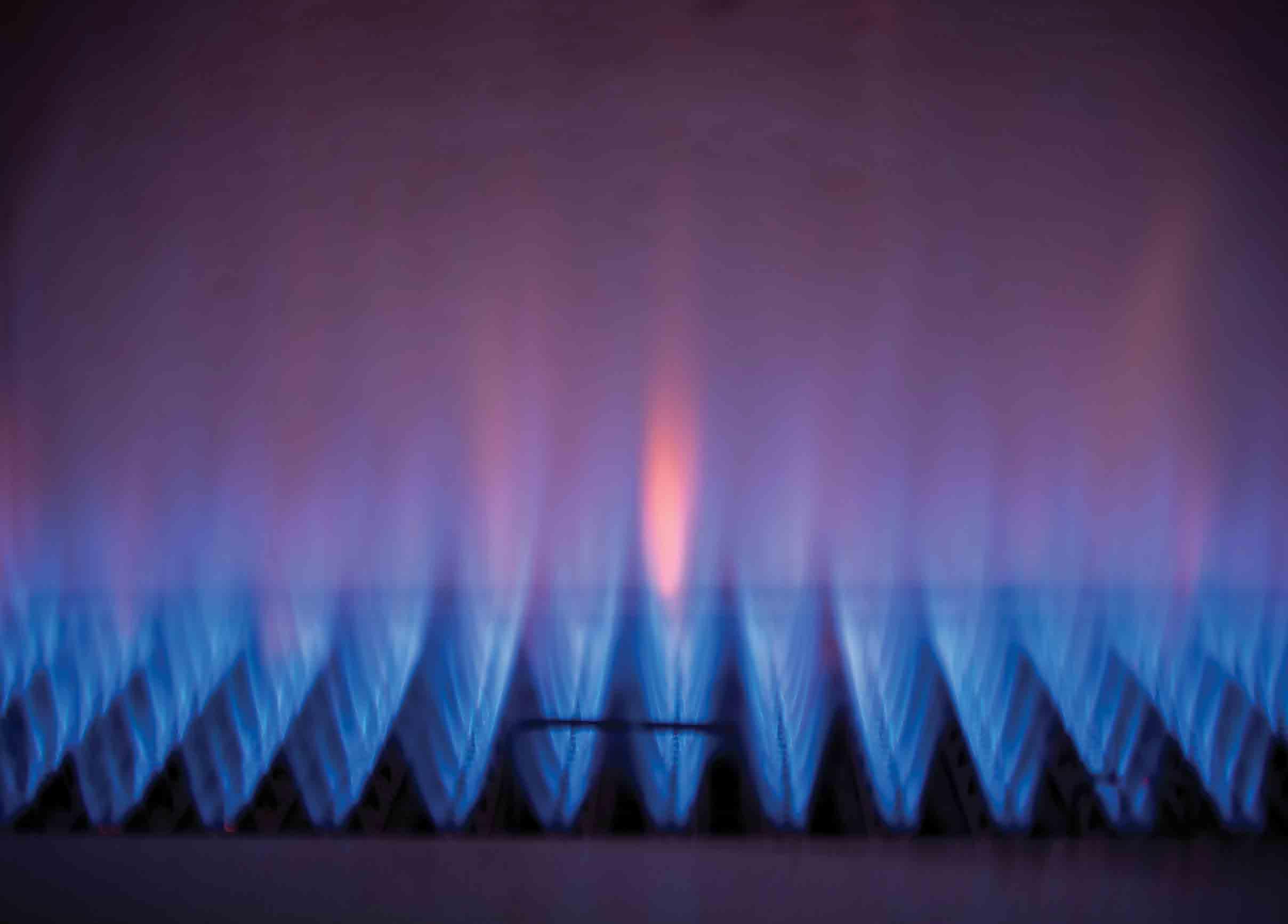
Both Riello Urzadzenia Grzewcze SA and Beretta brand have been well known in Poland for years. RUG was founded in 2001 while Beretta entered the Polish market nine years earlier.
At the beginning, it was a presence only in terms of sales. In those days inefficient central heating systems and old power stations made Polish customers keen on looking for modern heating solutions. So, that was the right moment to enter the Polish market. After some years Riello faced production problems in Italy as the costs of production appeared to be too high. The company started to look for the possibility of opening a factory abroad. It decided to build a plant in Poland because this was a reliable country, especially compared with other eastern European countries. At the end of the 1990s Riello was looking for the best place for the investment in the north part of Poland. Finally, such a place was founded in Torun. Twelve years later the company is still very satisfied with the decision to establish the Beretta plant there. The boilers from Torun have gained a significant position in Poland’s market of heating devices. Currently, there are more than 100,000 of these boilers in the homes of Polish customers.
Burners from Wroclaw
At the same time when Beretta was entering the Polish market, Boren Jan Borkowski Company started to operate as the official importer of Riello burners. Two years later, the Office of Technical Inspection performed the factory certification. This way Riello obtained approval for production in Poland and Riello Burners in Wroclaw was created.
The company is fully owned by the Italian company Riello SA and is the number 1 producer of burners sold in Poland. Knowledge, skills and experience allowed it to offer burners for boiler solutions, as well as for many specialized devices where the technological process is based on the heat generated by the combustion of gas or oil. Every year, the Riello Burners training centre in Wroclaw conducts more than 30 training sessions for about 300 technicians. Moreover, Riello Burners also manages the distribution of burners to Slovakia, the Czech Republic, Hungary, Lithuania, Latvia and Estonia. n
Visit: www.rugriello.pl