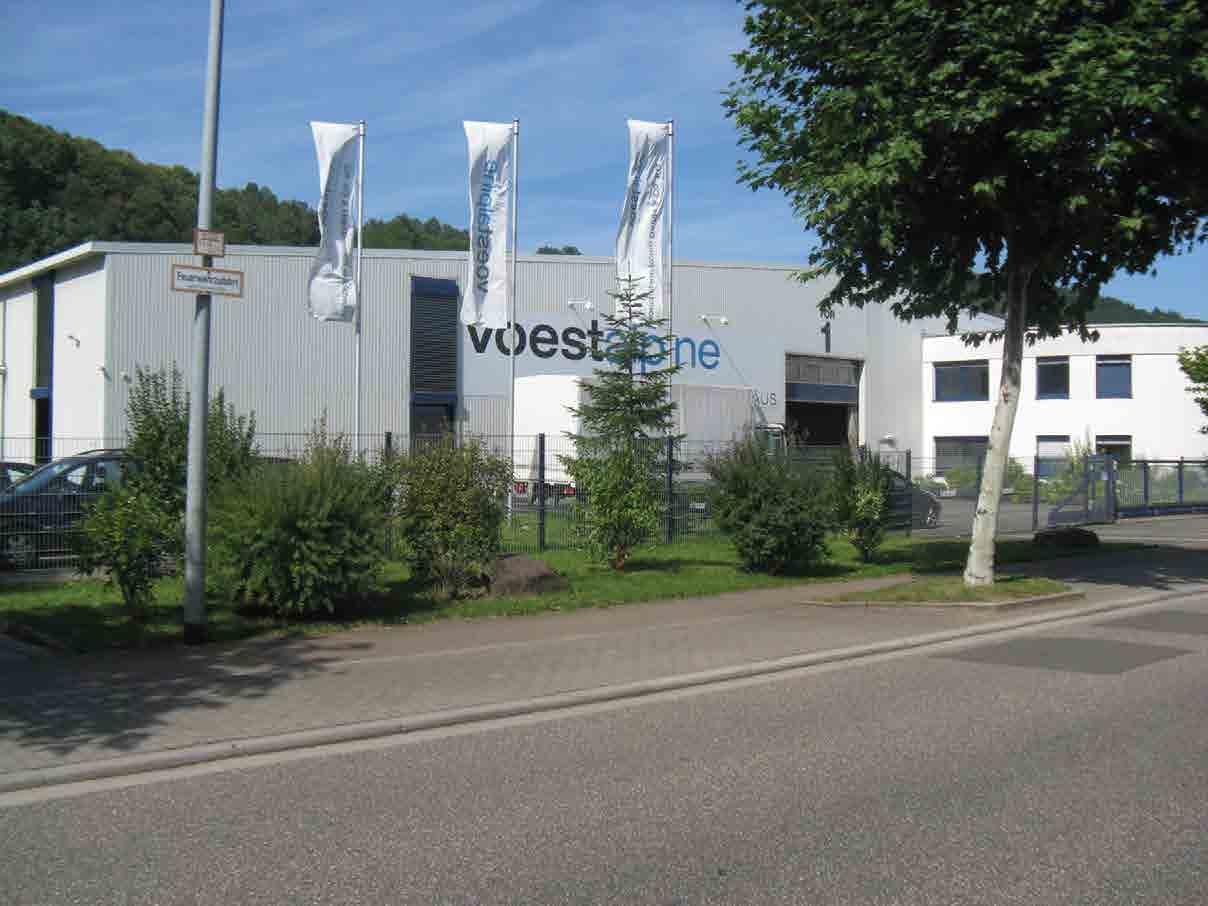
5 minute read
Leaders in tube forming Voestalpine
Production site in Annweiler/Rheinland-Pfalz
LEADERS IN TUBE FORMING
Voestalpine Rotec GmbH & Co. KG specialises in the production, further processing and sales of precision steel tubes. Abigail Saltmarsh looks at its operations.

IN his time at Voestalpine Rotec GmbH & Co KG , Dr Rolf Weiel, director of research and development at the group, has seen it leap from an annual turnover of €6 million to one of almost €32 million. Now, he says, the operation, which specialises in tube forming and machining technologies, has ambitions of reaching €50 million by 2020.
“We have seen an average growth of 14 per cent every year and, although it will be a challenge, I believe we can reach our target by that time,” he says.
“We always follow the options of both organic growth and acquisition – and will definitely be looking for acquisitions that fit our portfolio. However, in the past we have been much more successful with organic growth and we see good opportunities for that in the future.
“This may be achieved by strong growth in our main business field, but we also plan to implement further services for our customers.”
High-precision operation
Voestalpine Rotec is part of Voestalpine, a steelmaking, processing, and technology group that operates worldwide and manufactures, processes and develops high-quality steel products. With 500 production and sales companies in more than 50 countries on five continents, the mother group is one of the leading partners to the automotive and domestic-appliance industries in Europe and to the oil and gas industries worldwide.
Voestalpine Rotec itself specialises in the production, further processing and sales of precision steel tubes. It has a focus on the automotive industry and on segments
of mechanical engineering and hydraulic or pneumatic applications.
The group supports its customers in the development of products and production solutions with cutting-edge technologies, expertise in materials and perfected logistic concepts.
Industry leading technologies
“Our main specialities are temperature supported metal forming, such as hot spinning, round forging or hot radial press forming,” explains Dr Weiel. “We have transfer line based processes for the highest productivity and robot-equipped cells for high-level process integration.
“We concentrate on the development of highly efficient and productive integrated tube forming and machining processes in house and have our own design and engineering of complex production lines for high volume production.”
For the automotive sector, which accounts for 70 per cent of production, the group produces airbag cylinders and combustion chambers. It also manufactures components for air suspension systems, including aluminium pressure vessels, spin formed pistons and bellow support housings, silencer and seat frame tubes.
In non-automotive, it supplies housings for electromotors, such as blind shutter drives, as well as stainless steel pressure vessels, construction struts for electrical power plants and high pressure gas transport bottles for special applications, for example, avalanche airbag systems.
Automated line for aluminium pistons Developing new products
Proud of its technologies, Voestalpine Rotec is also at the forefront when it comes to developing new products. Working closely with its customers, it is able to design, build and deliver equipment from under one roof.
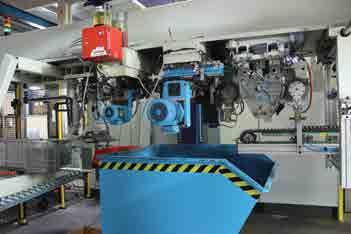
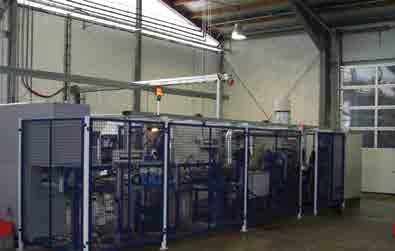
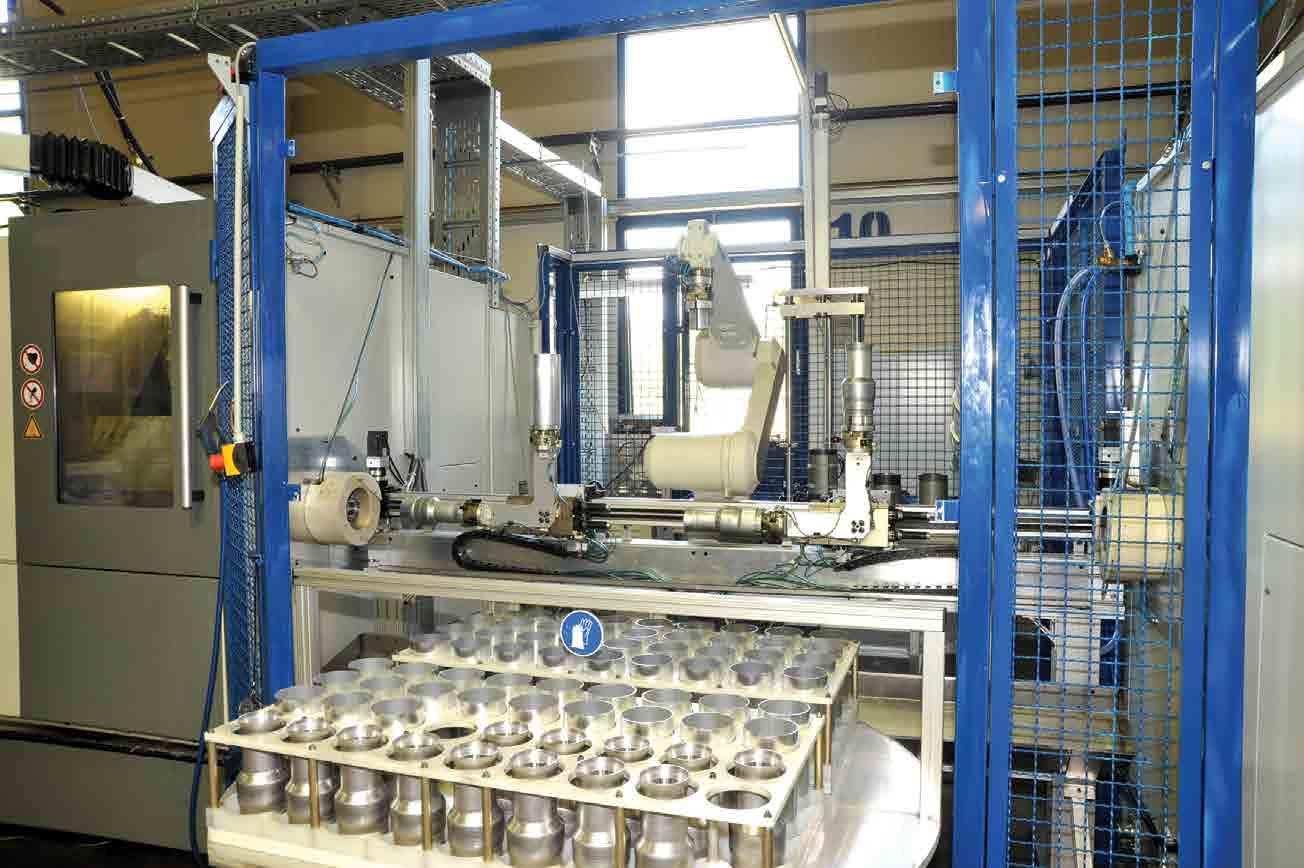


14 stage transfer lines for airbag components
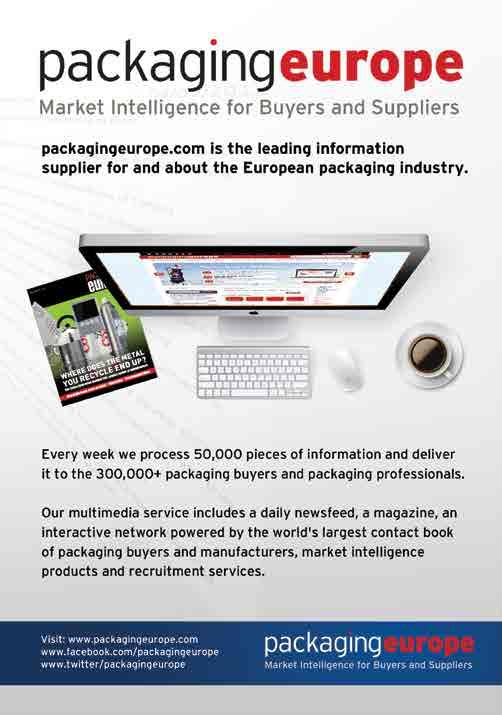
Dutch company Kinkelder was founded in 1945 and grew into one of the most important manufacturers of circular saws worldwide.
The blades are being exported to more than 70 countries. One of the main markets is Germany. Kinkelder is working in close cooperation with their German distributor “Werner Thelen OHG” for more than 40 years already.
Key users of Kinkelder saw blades are manufacturers and suppliers of tubes and profiles that are applied in the automotive industry, the Oil & Gas sector and the world of construction.
Kinkelder saw blades are typically used on fully automated sawing lines, where very high standards are set regarding speed, quality and sustainability.
Flying cut off Besides cutting tubes on off-line machines, Kinkelder is specialised in demanding Flying cut off applications. This includes single-, twin and orbital saws, with or without ID scarf.
These Flying Masters series are dedicated to perform on in-line sawing applications for ERW tube and pipe manufacturing, in order to address the specifics of this market.
The Kinkelder Flying Master series help you to: • Reduce downtime • Increase line speed • Improve blade life • Cut through a heavy ID scarf • Produce a bur free cut • Remove X80 and P110 from your problem list
“One recent product has been a pressure reservoir for Land Rover, where also the automated production line was engineered inhouse,” he says. “In parallel, we are developing new approaches for a further integration of additional functions in the aluminium pistons for automotive air-spring systems.”
He adds: “Air-spring components for cars have been a niche area to date but we do see this growing, especially in midrange vehicles.” Bringing added value
In total, Voestalpine Rotec has eight companies – seven of these are in Europe and one is in the USA. There are two manufacturing sites in Germany: at Annweiler, there is production, as well as management, administration and research and development, while at Sülzfeld, the company has an airbag pressure vessel facility.
While central Europe, Poland and the USA will remain key markets for the group, Dr Weiel is in no doubt that Voestalpine Rotec will be following its customers to Asia, specifically China.
“We have to move to these markets while also focusing on bringing added value here in Europe,” he says. “In order to achieve the organic growth we are looking for, we will have to move away from just making single components, to concentrate more on areas such as the assembly of more complex sub-units.” n
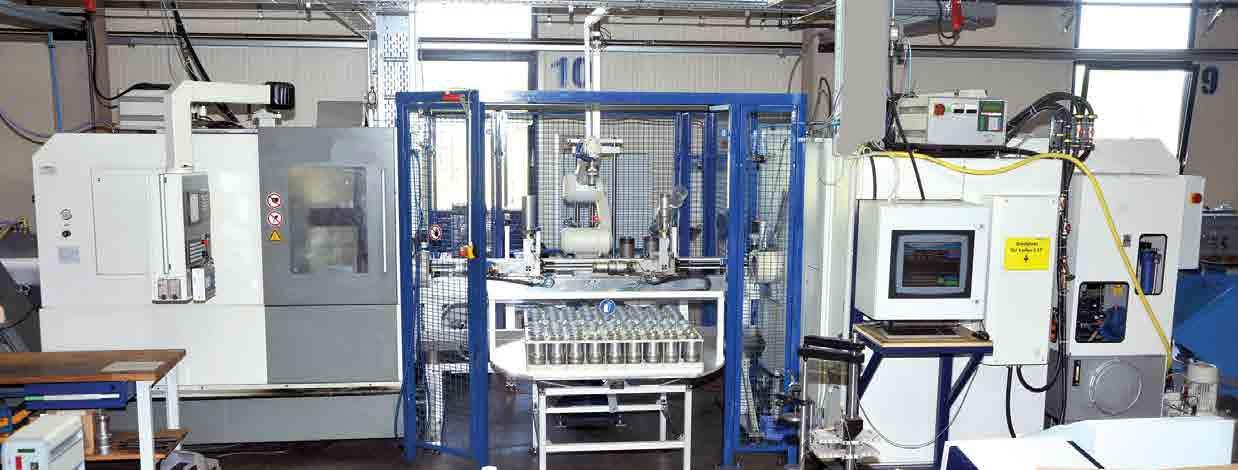