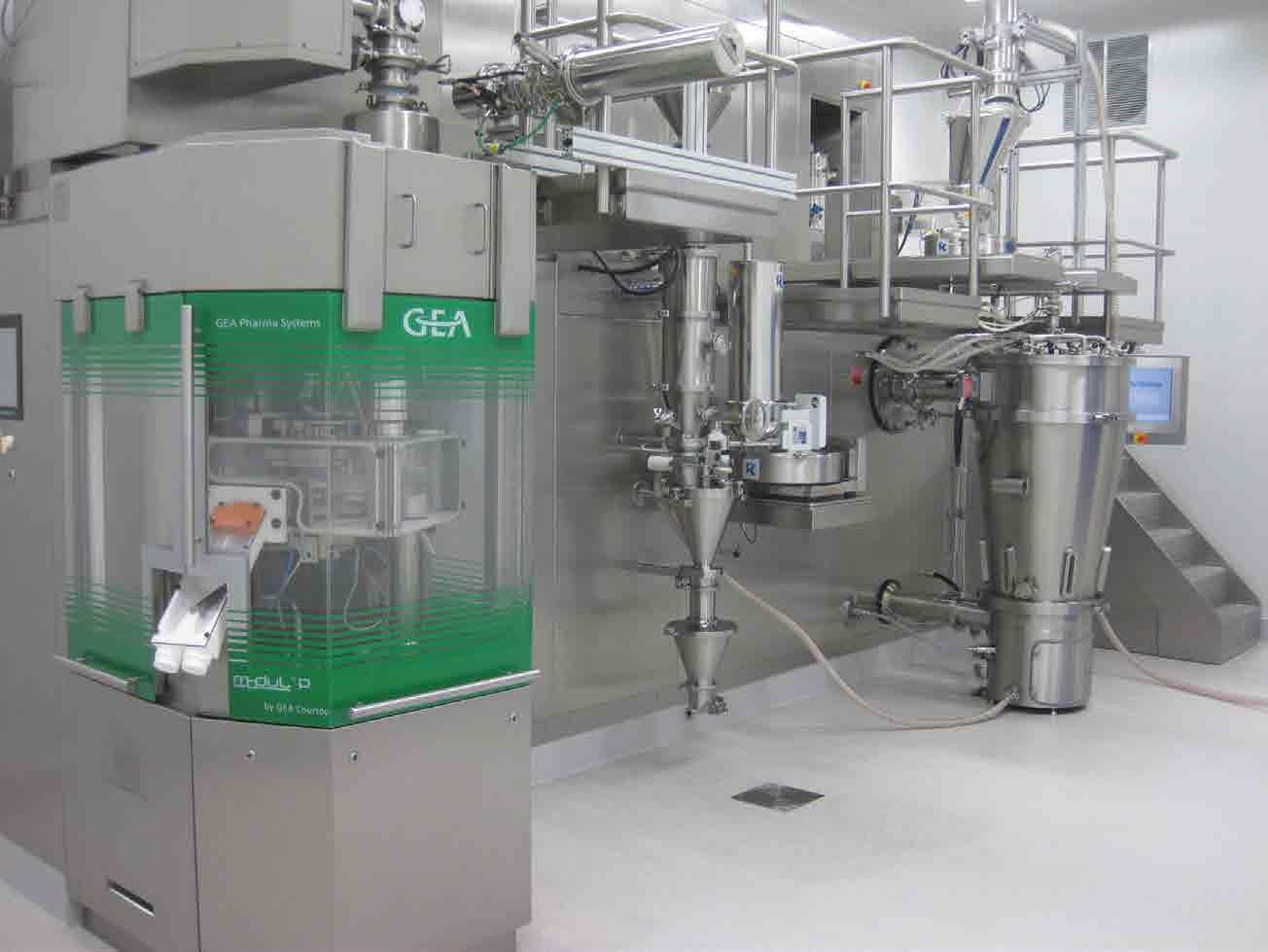
5 minute read
Leading the way GEA Group
ConsiGma™ Wet Granulation and Tableting Line Installed at GEA’s test centre in Belgium
LEADING THE WAY
GEA Group’s Pharma Systems division is leading the way in continuous processing technologies, backed up by the support of sister companies in other GEA Group divisions. Felicity Landon reports.
The pharmaceutical market is known for being highly regulated and therefor slow in adopting new technology – but technology leader GEA Group has been having some substantial success in introducing a radical new approach to the sector.
GEA’s Pharma Systems division has led the way in the development and implementation of continuous processing and it continues to move forward with innovative solutions for its customers. Its ConsiGma™ continuous manufacturing platform includes a high shear granulation and drying system with a modular design ensuring plug flow, first-in first-out, avoiding back mixing, providing a consistent quality and allowing for critical quality control in-line. The most recent addition to the platform is a fully integrated continuous direct compression line.
The system allows for building quality into the process, to measure in-line and to adjust parameters to meet high-quality target levels.
“Our achievements in continuous processing are getting a lot of attention – the pharmaceutical industry is usually slow in adopting radical new solutions, but it seems that we have developed something that, even in these times of slow growth, is attracting interest,” says Kris Schoeters, product manager con-
ConsiGma™ 1 Inspired lab-scale continuous processing for fast, easy R&D
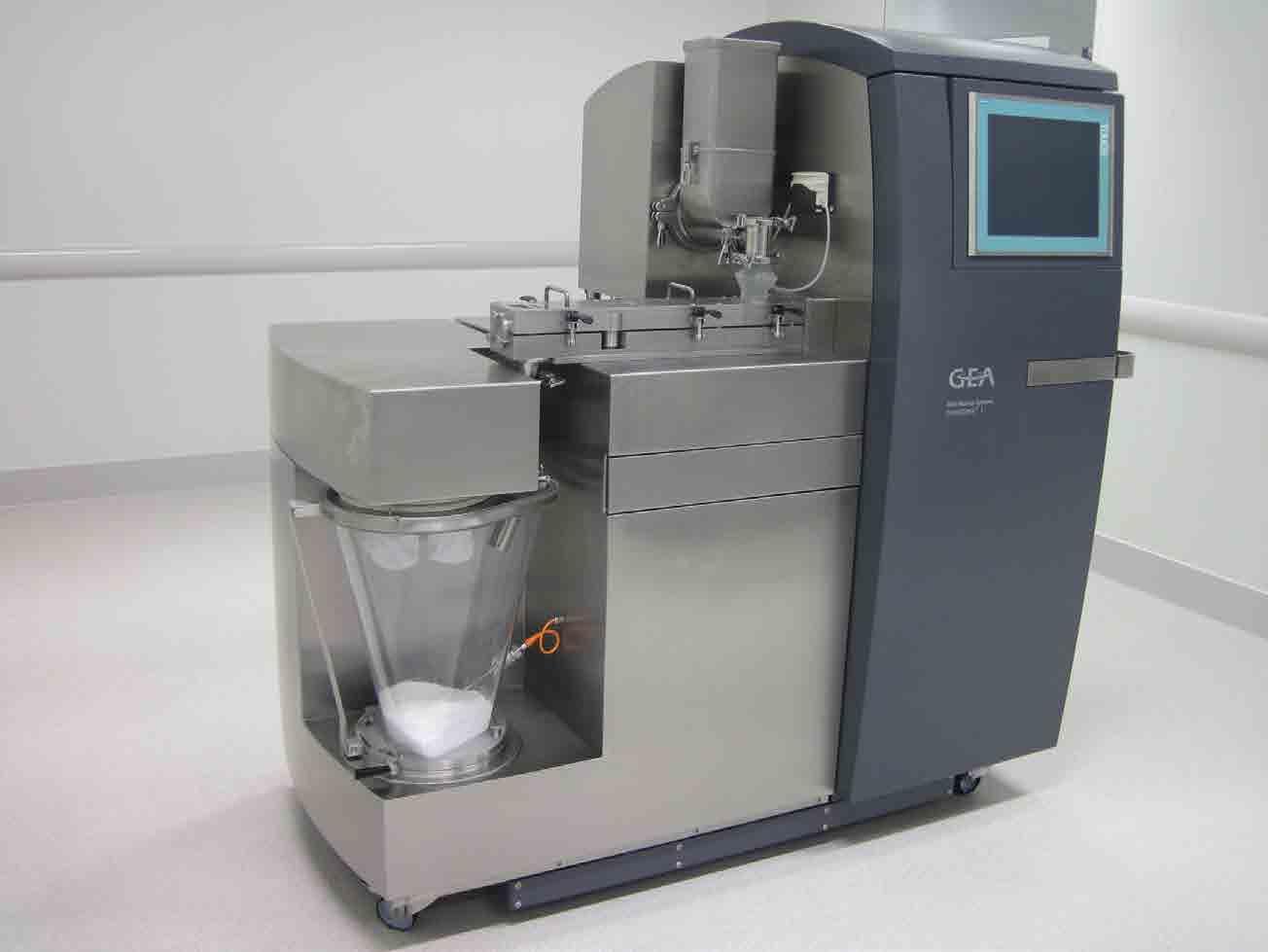
tinuous processing at GEA Pharma Systems. “The number of requests we are receiving is amazing,” he adds. “All kinds of pharma companies want to do tests with us or are buying equipment, and in just a few short years we have established ourselves in this area.”
Six divisions
Within the GEA Group, he points out, continuous processing is not such a new idea. The group, which reported revenue of €5.4 billion in 2011 and employs about 24,500 people worldwide, is divided into six divisions – food solutions, farm technologies, heat exchangers, mechanical equipment, refrigeration technologies and process engineering – the last of which includes the Pharma Systems business.
GEA Pharma Systems is a global specialist in solid and liquid dose technology. It has a range of manufacturing and technology sites and research facilities across the UK, Switzerland, Belgium, Germany, Denmark, India, China, Singapore and the United States, creating a global supply chain. Its central continuous processing test centre is in Belgium, where experienced engineers, technicians and industrial pharmacists can demonstrate the company’s continuous tableting line and explain about the pharmaceutical industry’s move towards this technology, to improve production quality in the most efficient way.
Central process development centre
GEA has invested heavily in its central process development centre in Wommelgem, Belgium; this facility has a clean room environment so that customers can view the kit in action and actually try it out with their own products. “We have a line with continuous processing through powder dispensing, granulation, drying, tableting etc, so they can really see what they are buying before they make the decision,” says Mr Schoeters. “This year we are expanding our clean room again, and new equipment will be coming in by June.”
GEA Pharma Systems also has a central R&D team in the UK which can do preliminary work, rapid prototype development, feasibility testwork etc.
Continuous processing is in use in many other industries which are served within GEA – particularly the food sector, says Mr Schoeters. “But it is relatively new in the pharma industry. A big benefit from our point of view is that we already have experience in other industries within GEA. We can learn a lot from our sister companies and have the experience in-house already. Some of our competitors are really focused on a certain product – and that may limit them.”
Authorities such as the FDA (US Food & Drug Administration) have made it clear that they want to see the industry move forward in technologies such as continuous processing, and that will be a key driver, he adds.
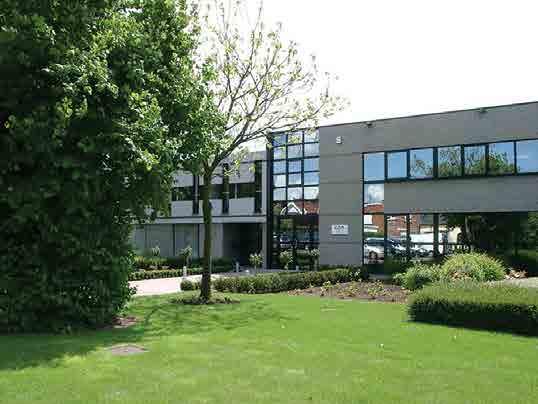
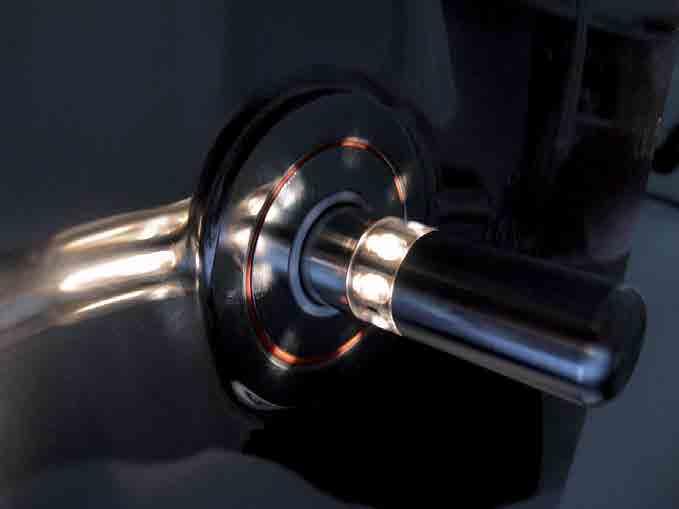
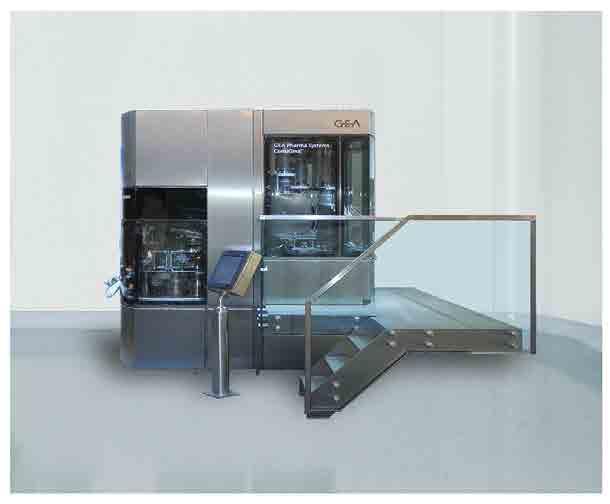
ConsiGma™ for Direct Compression
GEA Process Engineering Offices and test centre in Belgium
Lighthouse Probe™ technology: A compact and cleanable in-process optical probe for use in powder processing
In recent presentations the FDA has highlighted the potential economic and quality advantages both in development and manufacturing, and stressed that there are no regulatory hurdles to implement continuous manufacturing using a science and risk-based approach. Nevertheless, they recommend early and frequent discussion with the agency during the implementation as experience is still relatively limited.
While continuous processing is easy to apply, it also needs to be assessed on a caseby-case basis. “It might seem easy to move over to continuous processing for high-volume products but each time, you must bring up the business case and see what the benefits are. In some high-volume cases it may be better to leave it to existing technologies because it might cost more to change, while for smaller volume products – which at first sight may not seem likely candidates – continuous processing might offer significant benefits, both costwise and quality-wise.” Flexible and environmentally conscious
Continuous tablet manufacturing allows the pharmaceutical industry to bring products to the market faster, in a more flexible and environmentally conscious way, says Mr Schoeters. “There is no process scaleup, as time is the only relevant factor in a continuous process.
“Continuous processing can dramatically reduce development time and costs, and it offers a compact system – about one-third of the size of a classic granulation line. Development time and amount of product required can be reduced 10 times !”
Modular construction means the line can fit perfectly into any R&D department or existing solid dosage suite, including of a tablet press, and the concept fits with the Quality by Design philosophy, he adds.
“Continuous processing is becoming more and more important in the pharma industry. GEA Pharma Systems is taking the lead in introducing this innovative technology with our ConsiGma continuous tableting lines.”
The ConsiGma system handles flexible batch sizes, from 500g to many tonnes, and has been used for the testing of more than 100 formulations. According to Mr Schoeters, there is an increasing demand from the industry for complete solutions.
GEA Pharma Systems has recently been working with a US client, constructing a full production plant from dispensing powders through in-line blenders, full granulation line, roller compaction, tableting and coating. When it is complete, the line will be dismantled, shipped out to the customer from the Belgian test centre, and then reassembled and commissioned at the client’s plant, by a GEA team of technicians.
“We are doing projects all over the world and continue to invest in order to meet the demand – the expansion of our test facility in Belgium is of particular significance this year,” says Mr Schoeters. n
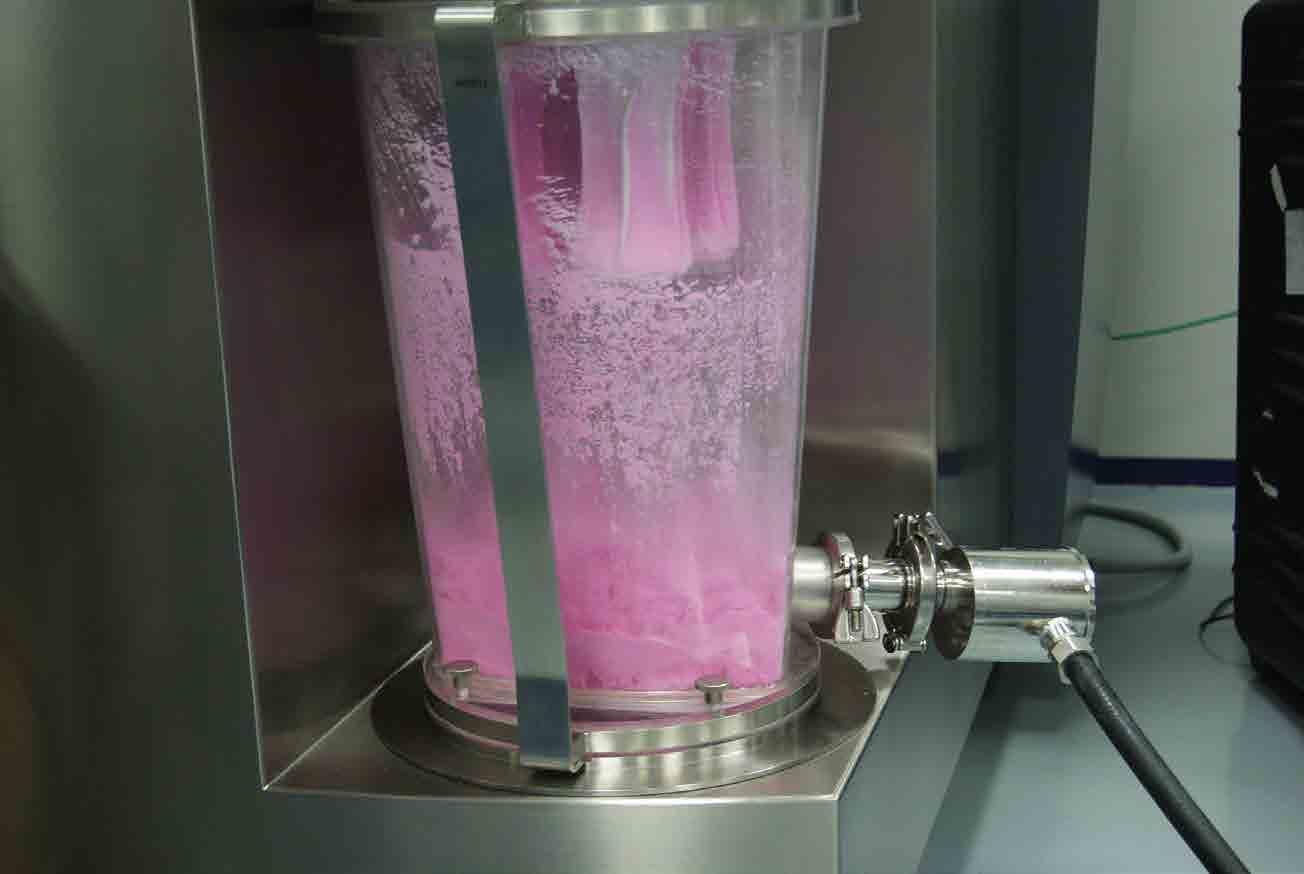