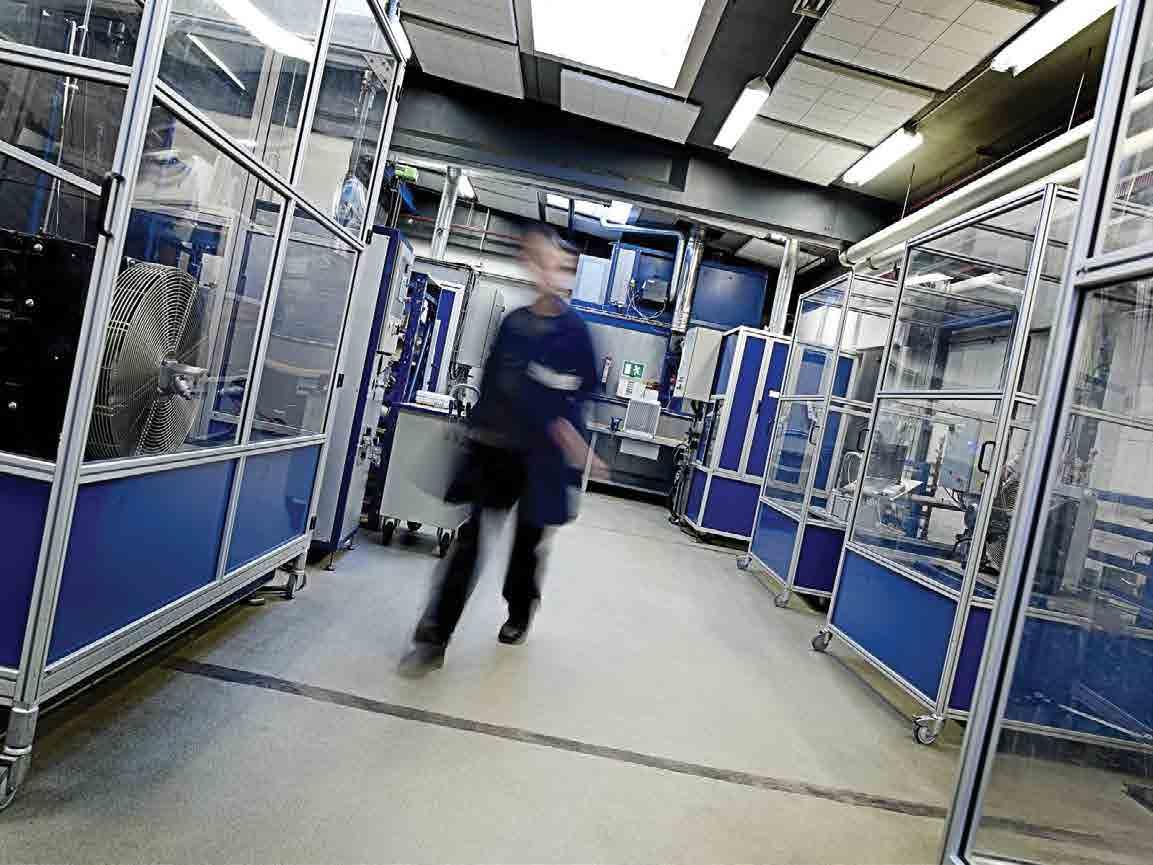
5 minute read
Specialists in cooling technology Nissens
SPECIALISTS IN COOLING TECHNOLOGY
The Danish company Nissens AS manufactures radiators, oil coolers, heat exchangers, charge air coolers and condensers for the automotive sector and produces complete cooling solutions for various industrial applications such as excavators, generator sets and mining and forestry equipment. Nissens is also a major supplier of cooling solutions for the wind turbine industry.
Alan Nissen is the CEO of a company that was founded by his great-grandfather, Julius Nissen, in 1921. Nissens began by making car radiators and is now one of Europe’s largest manufacturers of engine cooling products. From the 1980s, under Alan Nissen’s direction, the business diversified and began to produce cooling solutions for a broader range of machines. Nissens today has two divisions, one for automotive spare parts and another, the OEM division, which makes cooling solutions for manufacturers of wind turbine generators, buses, earth moving machines and other on- and off-road machines.
“We started as a local company in Denmark, but over the last decades we have developed into a global company with production plants in Slovakia and China,” stated Mr Nissens. “We decided to build our factory in Slovakia in 2003, and it was ready by 2005. We need the factory in China because our biggest customers are expanding into China and want us to serve them in the region from the region.”
Offshore wind
Denmark is famous for its pioneering role in the renewable energy industry. The Nissens OEM division moved into wind power as long ago as 1988 and produces cooling systems for wind turbine generators. As a wind turbine generates electricity it also produces heat.
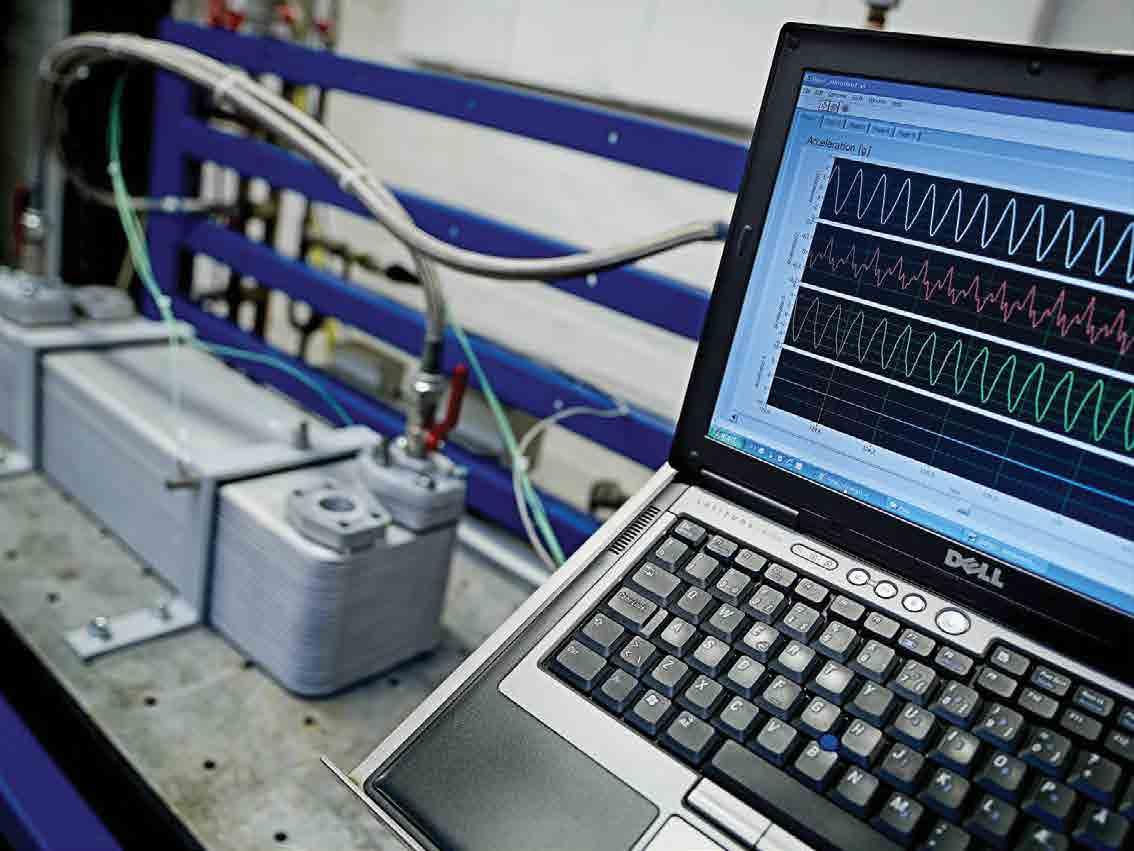
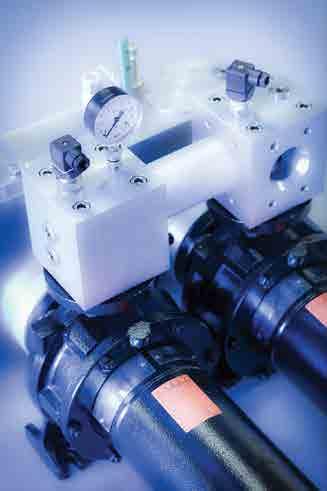
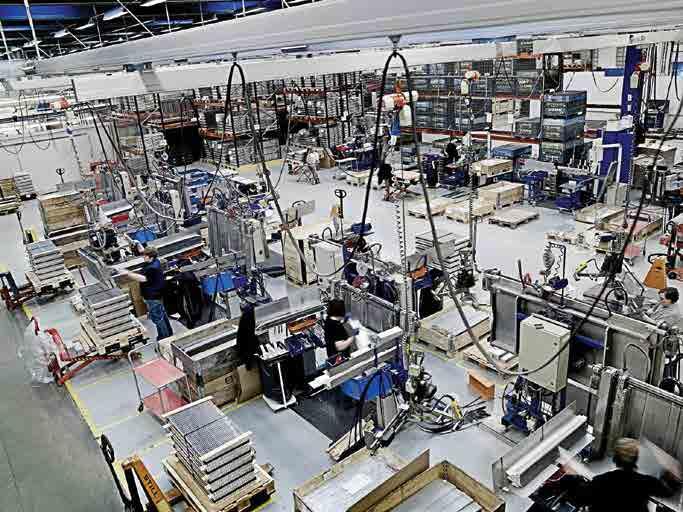
A wind turbine therefore needs a cooling system to cool the generator, along with the gearbox, converter, transformer and hydraulics. Customers include leading wind turbine manufacturers like the Danish firm Vestas Wind Systems and Siemens Wind Power.
Cooling systems from Nissens can be found in nearly all offshore wind farms like Horns Rev, off the coast of Denmark, and the Thanet Offshore Wind Farm, which is located off the Kent coast. Customised cooling modules and cooling systems
Nissens offers customised cooling modules and indirect cooling systems for on- and off-road applications. “Most of our on- and off-road customers buy a complete cooling module including steel parts, fans, motors, etc., and we see an increasing interest for our indirect cooling systems combined with our water cooled charge air cooler,” says Thomas Juul Eilersen, the company’s vice-president for sales and projects. The indirect cooling systems consists of a low and a high temperature radiator which cool part of the machine indirectly through a water cooled charge air cooler (WCAC) and aluminium heat exchangers. The indirect cooling system has several benefits such as reduced complexity in the front end cooling module, optimised dimensioning through sharing of a pooled cooling capacity, faster response from the charge air cooler and up to 5 per cent lower fuel consumption.

Nissens also offers complete cooling systems including pump stations, heat exchangers, hoses, valves, etc. that cover all the cooling requirements of a modern wind turbine. “We aim to provide an integrated cooling system rather than just individual cooling components,” says Anders Allesø, research and development manager at Nissens. A wind turbine may look simple from the outside, but the technology inside the nacelle (the housing at the top) is complex and has to function in demanding conditions. It is often difficult to reach an offshore wind turbine to carry out maintenance work, so the cooling systems from Nissens must be extremely reliable and are designed to have a lifetime of at least 20 years.
Nissens sees a trend towards passive cooling in the wind industry where the coolers are mounted on top of the nacelle without any forced ventilation. Passive cooling takes advance of the speed of the wind and thereby decreases the power consumption from the fan to zero. Intelligent and smart cooling is about looking at the total cost of ownership i.e. all the end user’s costs including operation and maintenance cost. With passive cooling and the correct control of the cooling systems pumps and valves Nissens ensures the optimum cooling set-up for its customers.
In the last couple of years, Nissens has launched a new aluminium plate heat exchanger, a water-cooled aluminium charge air cooler and a new water pump station concept. In early 2012, Nissens brought out its new AluXstream cooler which is an improved cooling system that employs a special design of aluminum coolers, rather than the traditional ‘plate and bar’ type. The AluXstream enables a significant reduction in weight.
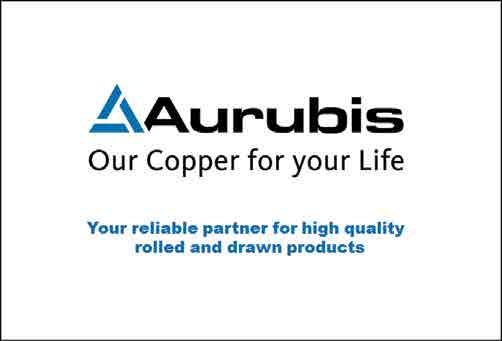
Markets
Nissens exports over 90 per cent of its output. Within Europe, the company’s main markets include Sweden, France, Germany, the Netherlands and Spain. “Our cooling systems tend to be highly customised,” stated Thomas Juul Eilersen. “Customers will involve us during the design of a new product and ask us to develop a prototype
of the cooling system. The OEM division focuses on a special segment of the market. Typically we develop coolers for the kind of machine of which no more than 5000 units will be produced every year.”
The Nissens factory in China began production in 2012. The result of some €10 million of investment, the factory at Tianjin is capable of developing cooling systems for the company’s customers in China. In renewable energy, the market in China is growing fast, as Mr Nissen explained. Nissens sells to the majority of leading wind OEMs and is seeing increasing interest from the large Chinese wind OEMs like Dong Fang and Goldwind. “We are a major suppliers of cooling systems for the wind power industry and expect a lot from the Chinese market. In wind power, China has become the biggest market for new capacity.” n
Aurubis
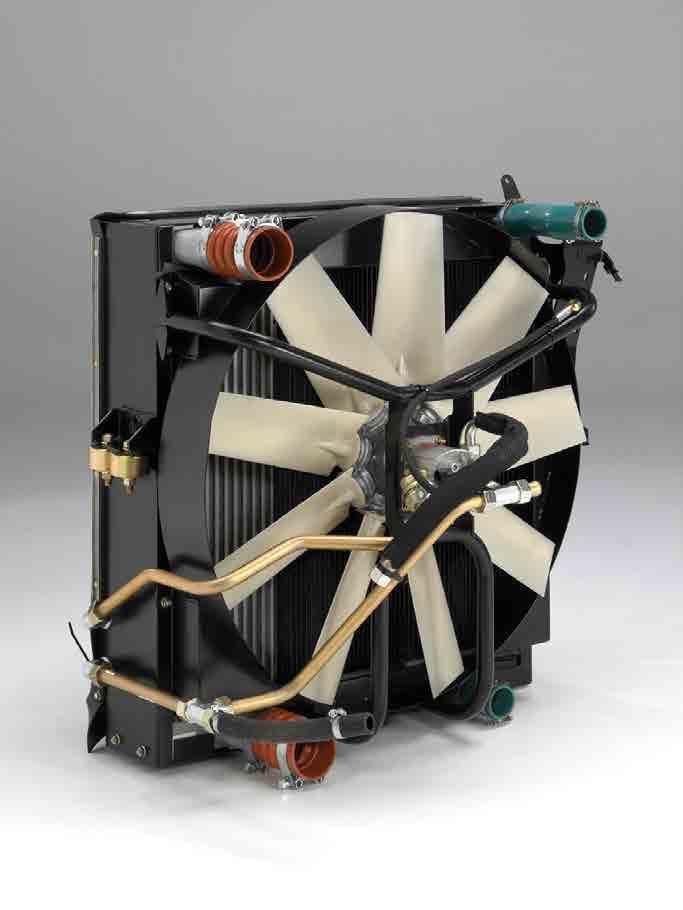
Aurubis is the market leader in copper and brass strip for engine cooling applications utilizing soft solders and CuproBraze® technology. Aurubis uses the most efficient technology and offers innovative assistance in Research & Development as well as technical cooperation for our customers. Aurubis produce an extensive range of copper and copper alloys, which include alloyed brasses, copper tin alloys and our special alloy CuproBraze® as well as alloys such as DHP, OF, OFE, ETP, XLP, HPC and PHC for almost any application.
Aurubis is the leading integrated copper group and the world’s largest copper recycler. Visit Aurubis at www.aurubis.com for further information.
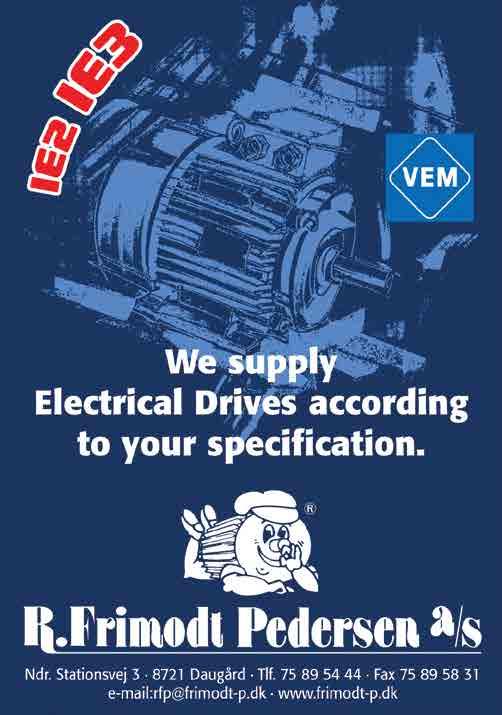