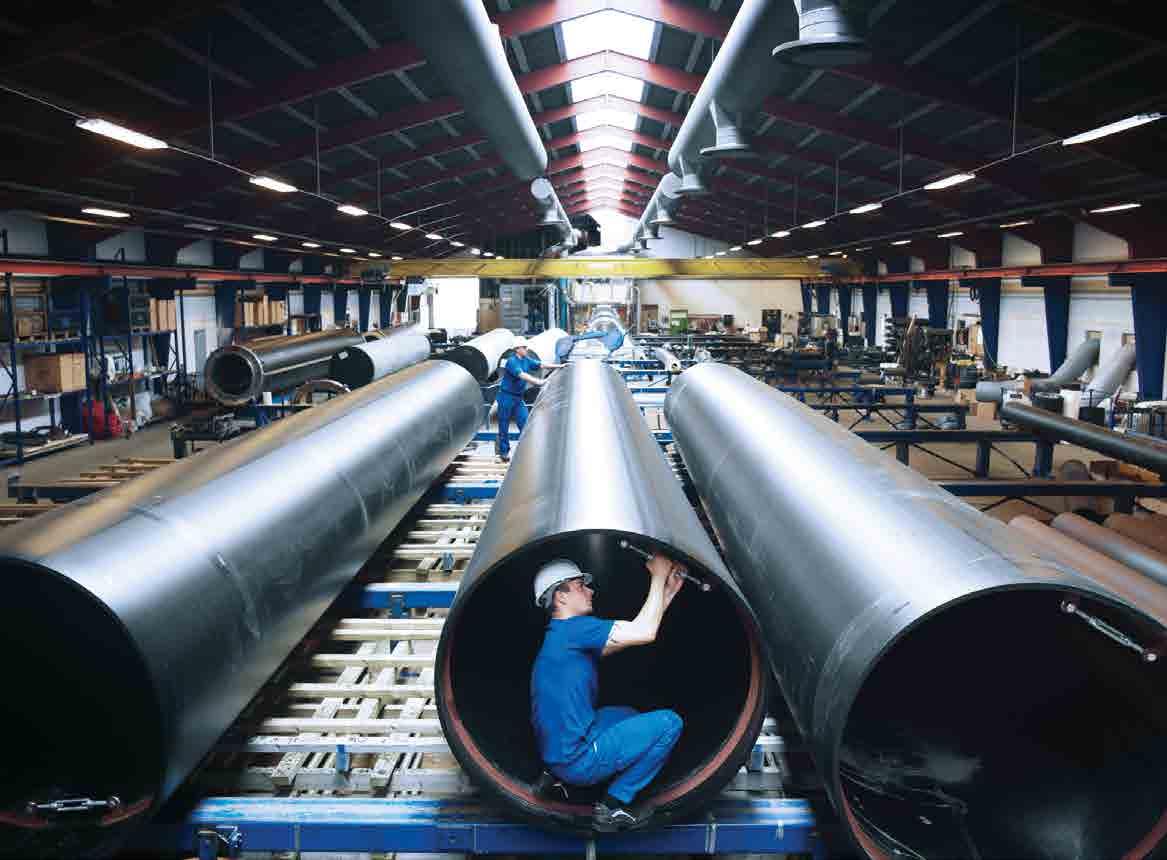
5 minute read
Fast-flowing technology Logstor
FAST-FLOWING TECHNOLOGY
Logstor is a Danish company and a global leader in the field of pre-insulated pipe systems for both the private and public sectors. Increasing global demand for liquefied natural gas (LNG) has led to new, innovative pipe systems being developed by the company.
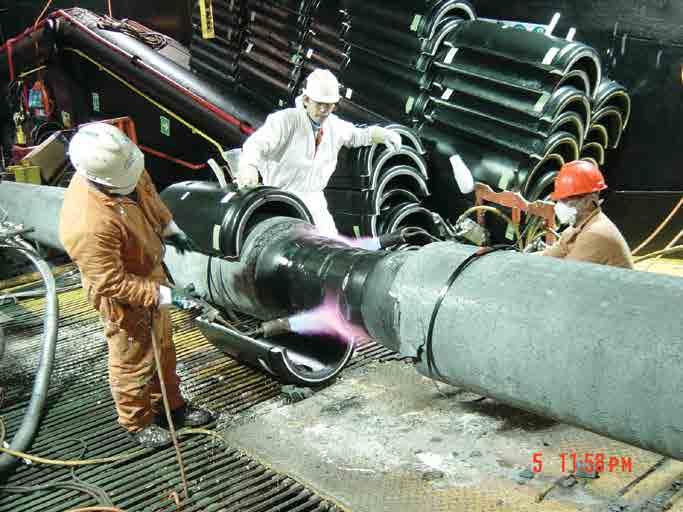
IN August 2005 Logstor Ror merged with Alstom Power Flow Systems to form Logstor A/S, and overnight the company became the world’s leading manufacturer of pre-insulated pipe systems for the transportation of oil and gas, and for district heating and cooling, as well as for marine and industrial purposes.
Logstor AS has its headquarters located in Logstor, Denmark, and production facilities throughout Europe. In addition, the company has dedicated distributors in 30 countries, as well as having dedicated joint-venture companies in Korea and China. The private equity company Montagu Private Equity owns the majority of Logstor AS.
Global focus
During the past few years, the oil and gas industries have seen major changes in levels of demand and their pricing structures. These evolving market forces have created new growth opportunities for Logstor, as a company representative explained: “Until just a few years ago, our main focus was on the growing demand for district heating and cooling systems in northern Europe, as well as the design and installation of pre-insulated pipe systems for marine applications. Today it is a very different story. We have developed our core competences in pre-insulated pipe systems to take advantage of the global opportunities in the transportation of oil and gas.
“In particular, we have overcome the problems of transportation of liquefied natural gas, which presents major challenges to producers due to the very low temperatures involved of around -180 degrees Celsius, encountered in the transportation process. After many years of research and rigorous testing procedures we are now able to safely transport LNG from both on and offshore sites to anywhere in the world. As a result of this breakthrough in pipe system technology, we have moved from a pan-European focus to a global one and have already established facilities in the Middle East, the Far East and South America.
“In a separate business sector, we are also moving ahead with strong interest being shown in our district cooling systems. This interest is from markets in hot countries, such as the Far East and the Middle East and we will also be marketing these energy-saving systems in the USA eventually. Our current challenge is to control our production capability and the risks associated with moving volatile oils and gases over long distances. We are recruiting skilled pipe-layers and fitters internationally, and will only employ people who can prove that they can meet the same high standards that we demand from our existing employees.
“As the price of crude oil and LNG continues to rise due to increased global demand, transportation from existing and new fields also increases, and so we see this as a long-term opportunity for us. For example, in Canada they have discovered the second largest reservoir of oil in the world, known as the Suncor oil field. In the years to come, the USA will source its oil from Canada and not the Middle East. In the future, crude oil from the Suncor field will rely on its international transportation from pre-insulated pipelines developed by Logstor.
“Yet another Logstor R&D breakthrough has opened up the solar energy industry to us. At Logstor we have developed the world’s first integrated solar pipeline systems, and these new systems are currently being introduced into Spain, where solar heating and piping systems are leading the way forward in reducing global warming there.”
District heating gaining ground
District heating and cooling have been operating in the Nordic countries for many years. However, it is only since pressure has been building to move towards more environ-
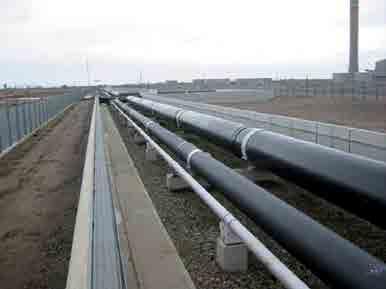

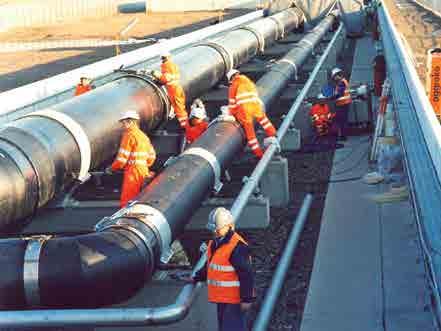
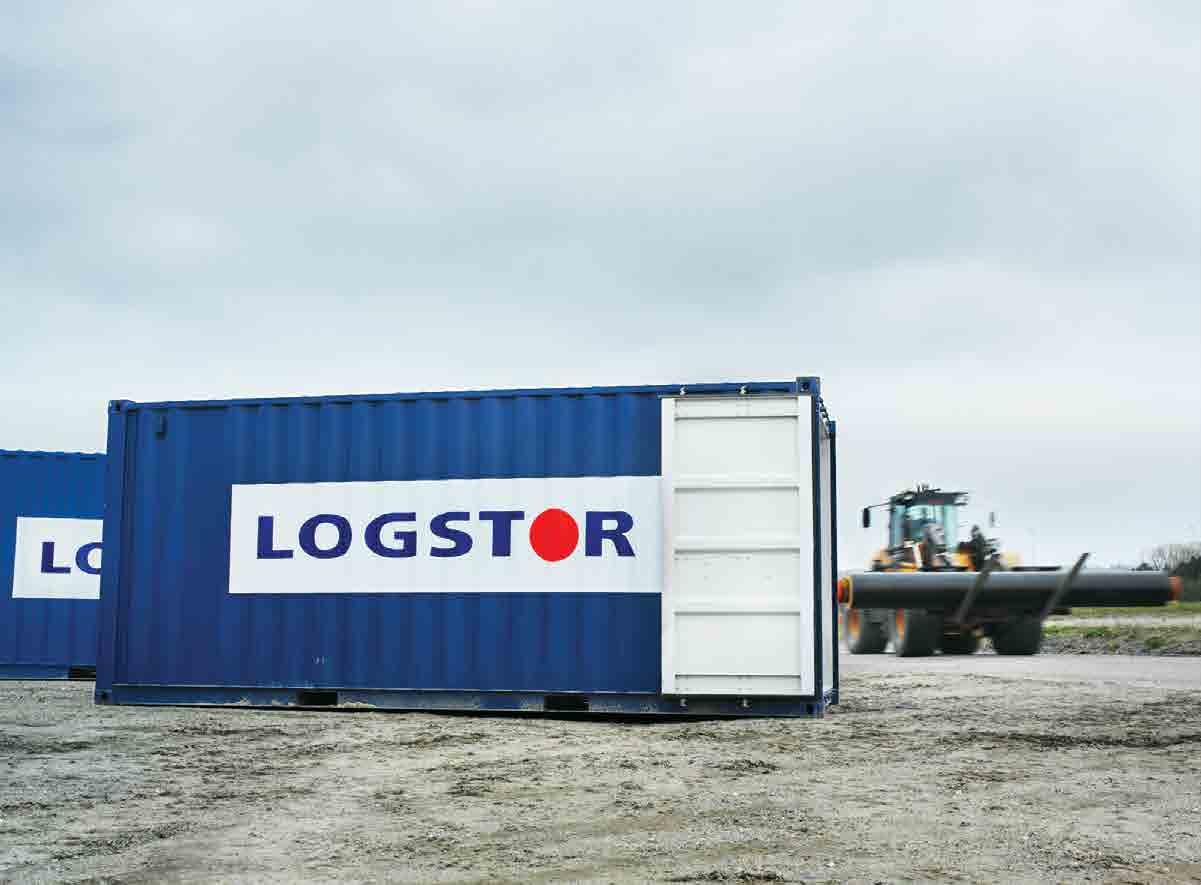
mentally friendly systems that the rest of the world has taken an interest in district heating and cooling.
District heating systems use media at temperatures of between 0°C and 140°C with typical media transported being heating water and steam. This system can also be used for other types of media, and carriers consist of polyurethane pipes with unique insulation properties, which in turn guarantee low operational costs.
District cooling systems are also gaining ground as the planet warms up and summer temperatures rise. The traditional use of air conditioning systems is now being replaced by district cooling systems, as AC installations do not offer such environmentally friendly solutions. The Middle Eastern countries and South America are showing particular interest in Logstor’s district cooling systems.
Continuous improvement
Logstor has developed a pre-insulated pipe manufacturing system known as the ‘continuous production system’. In the traditional production method, lengths of pipe are manufactured individually. The carrier pipe is fitted with spacers and then inserted in the polyethylene (HDPE) jacket pipe. The foaming liquid is then injected into the cavities between the carrier pipe and the outer pipe, where the foam expands. However, this method is highly demanding with respect to the viscosity of the foaming liquid, since expansion is required along the entire length of the pipe from one end to another.
In the advanced ‘continuous production’ process, the pipes are manufactured continuously in an unbroken length instead of being produced individually. The carrier pipes enter the production units horizontally and are joined to form a long, unbroken line. The continuous method uses less foam to give insulation that offers significantly improved characteristics and handling properties, when compared to traditional production methods.
Logstor has also perfected the ‘axial process’ for manufacturing pre-insulated piping, where pipes are insulated continuously in a travelling mould, and where the PUR material flows around the pipe. The moulded foam-insulated carrier pipe then continues through an extruder, where the HDPE jacket is applied. In the spiral process, the PUR foam is sprayed directly onto the pipes while the pipes rotate around their own axis when passing through the production units.
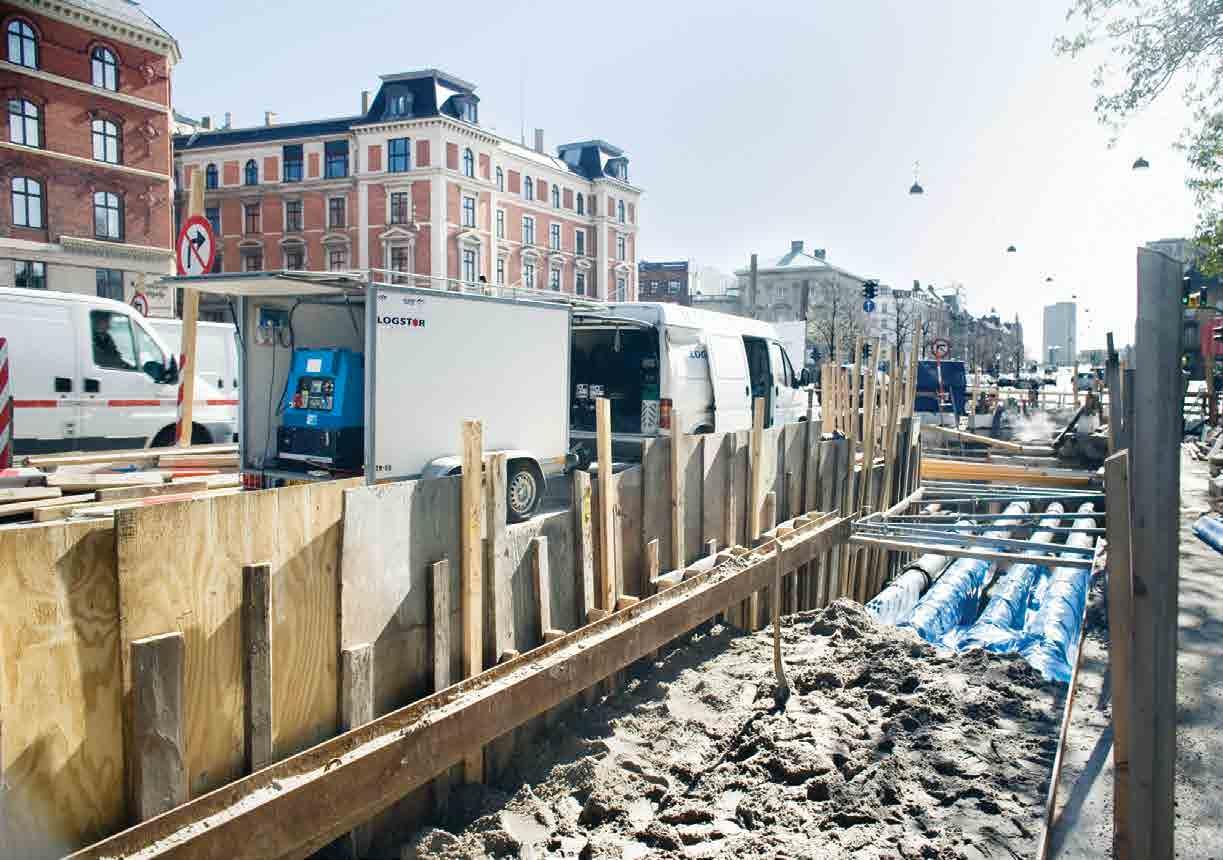
Growing demand for marine applications
Logstor’s diverse range of pre-insulated pipes includes systems for marine applications. The company has developed a unique approach to the design and installation of pre-insulated pipe systems for marine applications. This approach can be applied to new-build shipping as well as to retrofitting on existing vessels. The advantages of its pre-insulated pipe systems are even more apparent for above-deck piping systems. The combination of salt-water-wave impact, high winds, driving rain, heat, extreme cold and human traffic across the pipes, makes Logstor’s preinsulated pipes the ideal solution, as they are impervious to all extreme elements. n
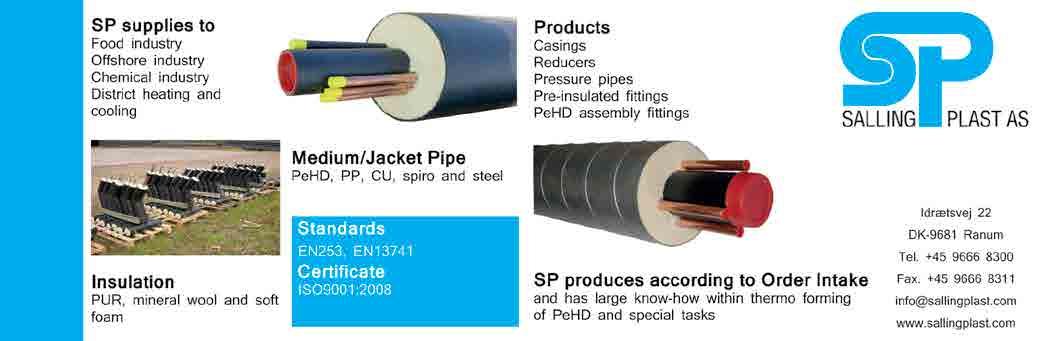