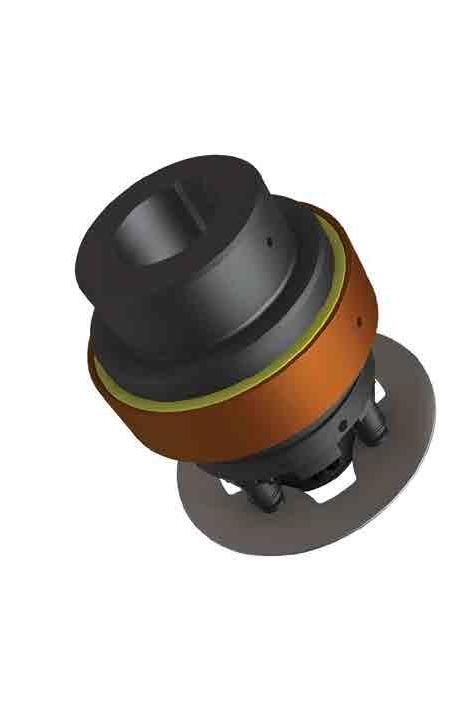
6 minute read
Driving powertrain technology forward
DRIVING POWERTRAIN
TECHNOLOGY FORWARD
Autogard is part of Rexnord and a global leader in the development and manufacture of torque management products and solutions. Philip Yorke talked to Eric Blickley, the company’s European marketing director about its latest Monitorq® systems and move into the world’s emerging markets.
Autogard was founded in England in 1930 and is a world leader in torque limiter and coupling engineering technology. Based in Cirencester, UK, it houses a comprehensive innovation, research and development facility that has kept it at the forefront of powertrain technology. Today Autogard products are at work across a wide range of industrial applications, such as power generation, mineral production, printing, packaging, extrusion and conveying. The company is recognised worldwide for its advanced overload-protection devices and its flexible couplings that are used in a diverse range of power transmission systems.
The company’s team of engineering experts use innovative processes and stateof-the-art equipment to research, design, prototype and test, new, energy-efficient powertrain products.
Autogard is part of Rexnord, which is listed on the New York stock exchange and is recognised as a diverse, multinational manufacturing company. Rexnord is comprised of two strategic business platforms: Process & Motion Control and Water Management. In 2012 Rexnord employed over 7000 people.
Unparalleled overload protection
Autogard’s torque limiters are available in a wide range of configurations and capabilities, from the simple, cost-effective Series 200 to the Series 600 model, which is pneumatically controlled and has a torque range of up to 20,000Nm and shaft sizes up to 95mm. The Autogard 400 Series is available in reverse to reset as well as automatic reset versions. The 820 Series modular torque limiter can be used in applications up
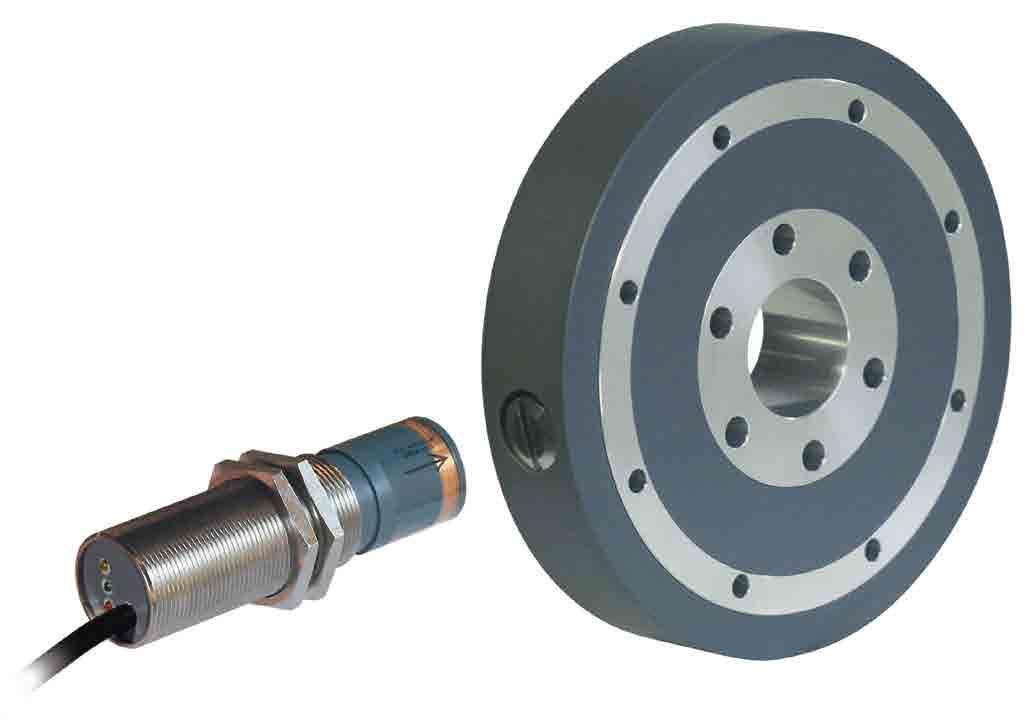
to 500,000Nm. Autogard’s Monitorq® torque monitoring system provides a highly accurate measurement of torque from any location in a drive train. It offers proven straingauge technology used in conjunction with a short range telemetry system to measure and transmit real-time torque data. These unique, patented systems enhance equipment performance by providing a variety of functions from simple overload protection to production and process control monitoring.
Mr Blickley said, “As part of Rexnord we have the benefit of multiple facilities in Europe with a major presence in Germany, the Netherlands, Italy, the UK and Belgium. We also have manufacturing plants and Rexnord sales, service and logistic offices strategically located in Brazil, India, China and the USA. While Rexnord has global manufacturing plants, Autogard’s core manufacturing plant and global centre of excellence is based in Cirencester, UK. We also have significant manufacturing capabilities in the USA and have recently expanded our capabilities in China. With the recent acquisition of the company by Rexnord, we are able to extend our global reach, especially in the world’s developing economies.
“When it comes to power transmission technology Rexnord is clearly a market leader. Our focus in Europe is on the development and manufacture of torque limiters and flexible couplings, clutches and brakes. We are also expanding our capabilities to support the Falk branded enclosed gear drives. Our products span many industries including automotive, petro-chemical, mining, paper, agriculture and cement. Our fastest-growing business segments at the present time are the petro-chem, energy and mining industries. We have been growing our market share across all our product ranges over the last ten years as part of an overall strategy to provide products globally and services locally.”
Mr Blickley added, “We believe that our latest product development initiatives will position us yet further ahead of the field, particularly in the area of flexible disc coupling technology, where our couplings can accommodate the difference in alignment of almost any manufacturing machinery. We are also delivering other high-tech industrial solutions with our Monitorq® system. With the ever-changing powertrain challenges of today, we develop new technology to meet the needs of our customers, whether this is for compressors, conveyors, generators or transport.
“We also provide focused training programmes for our customers who require
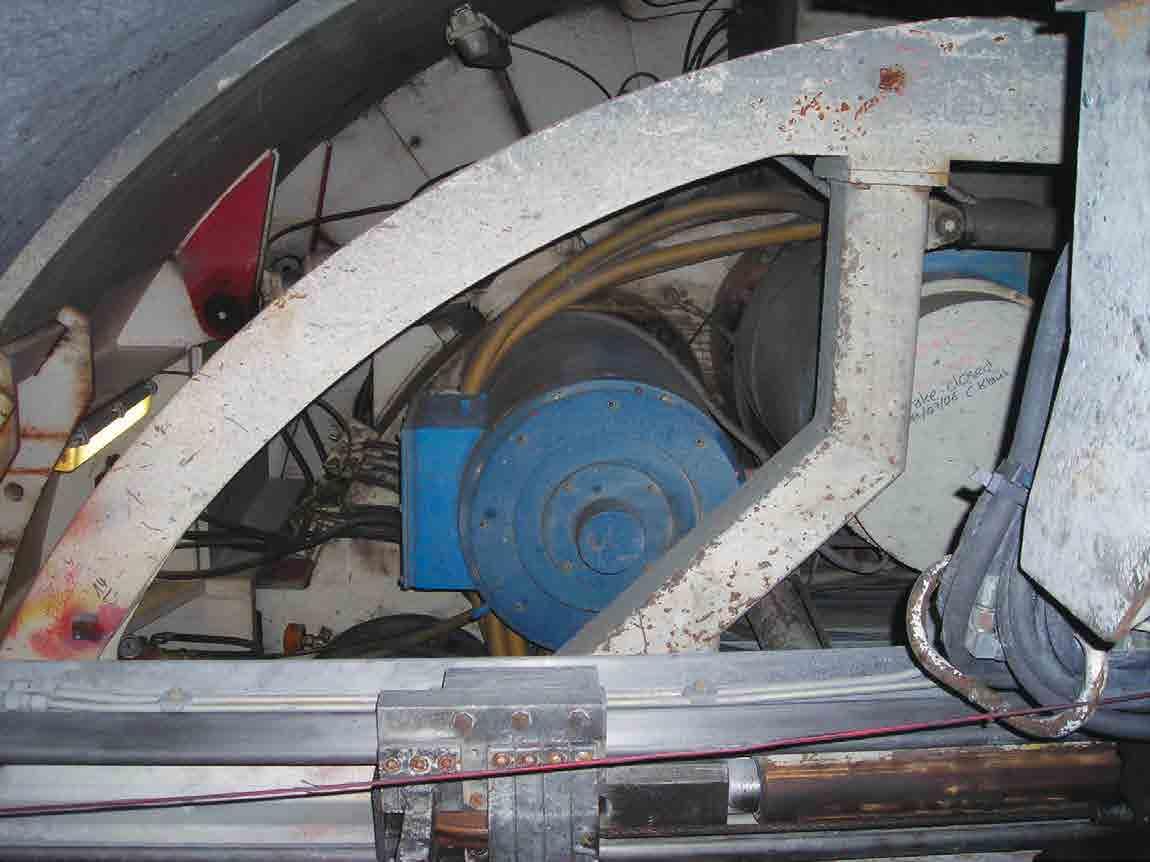
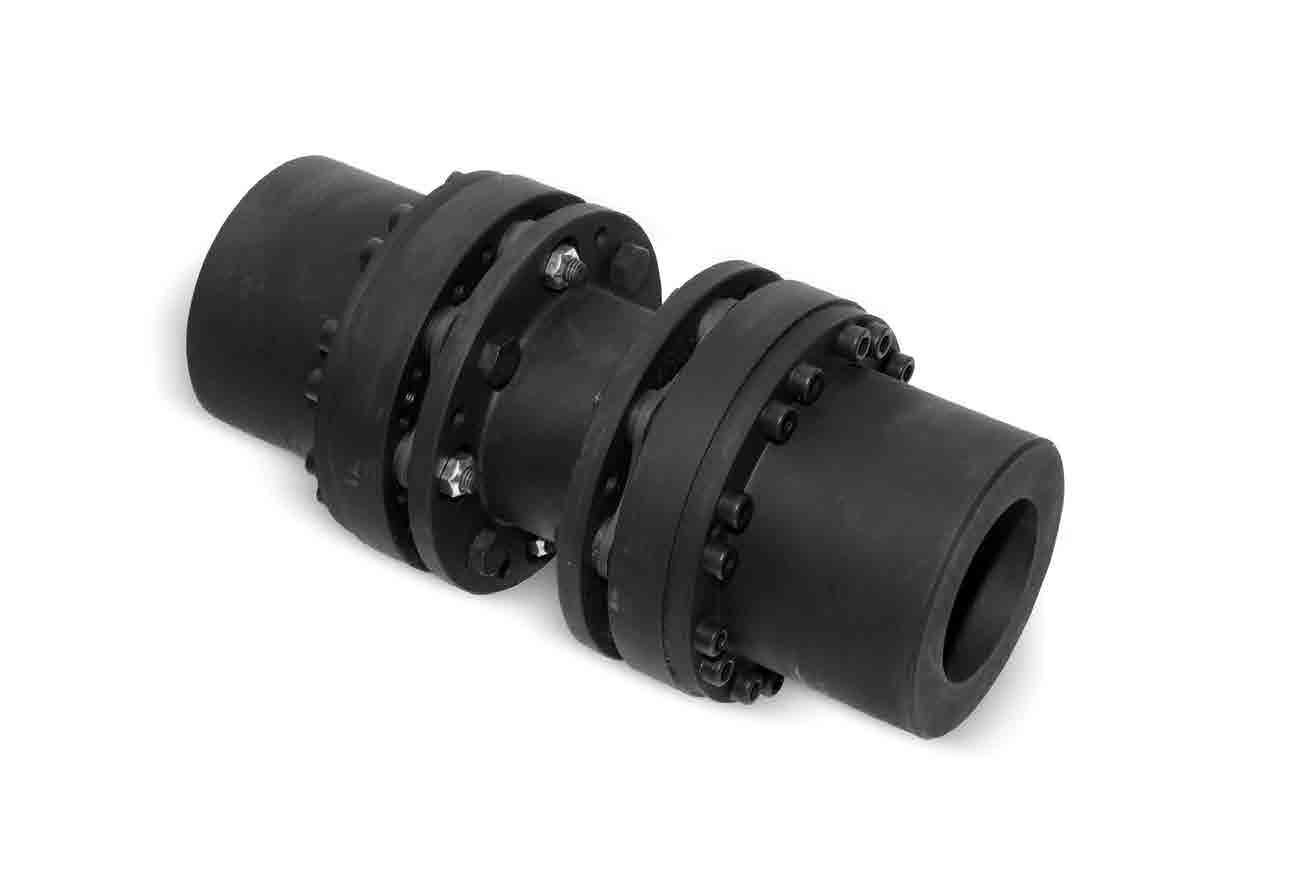
Grillet & Partners: your partner for turning and milling

Grillet & Partners from Vilvoorde is a specialist in turning and milling. The company consists of a team of five professionals with extensive experience.
Manager Michel Grillet and his team can certainly help when it comes to mechanical parts. The company has over 80 years experience in industrial sectors such as the chemical, food and aerospace industries.
Grillet & Partners makes customised mechanical parts such as gears, shafts and clutches for machines, pumps, gearboxes etc. Whether the material is metal, plastic or non-ferrous, we can provide the solution. Moreover, we also repair parts for pumps, lifts etc.
Owing to our decades of experience we are able to use both old and new techniques. This means we can choose the best method to ensure optimum quality. One of our strengths is our ability to deliver large pieces.
www.grillet-partners.be an increased level of expertise in order to understand the changes in the global industry specifications and materials available for use. We are also involved in much of the cuttingedge technology of the future. For example, we are involved in the development of alternative energy whether that is wind, clean coal or wave energy. In fact, we are able to contribute to any projects that involve ‘rotating’ equipment. I believe that the next new challenge for the world’s manufacturing industries beyond improving the efficiency and reliability of material processing is the storage and distribution of energy, possibly through its conversion to liquefied gas or other technologies currently under development.”
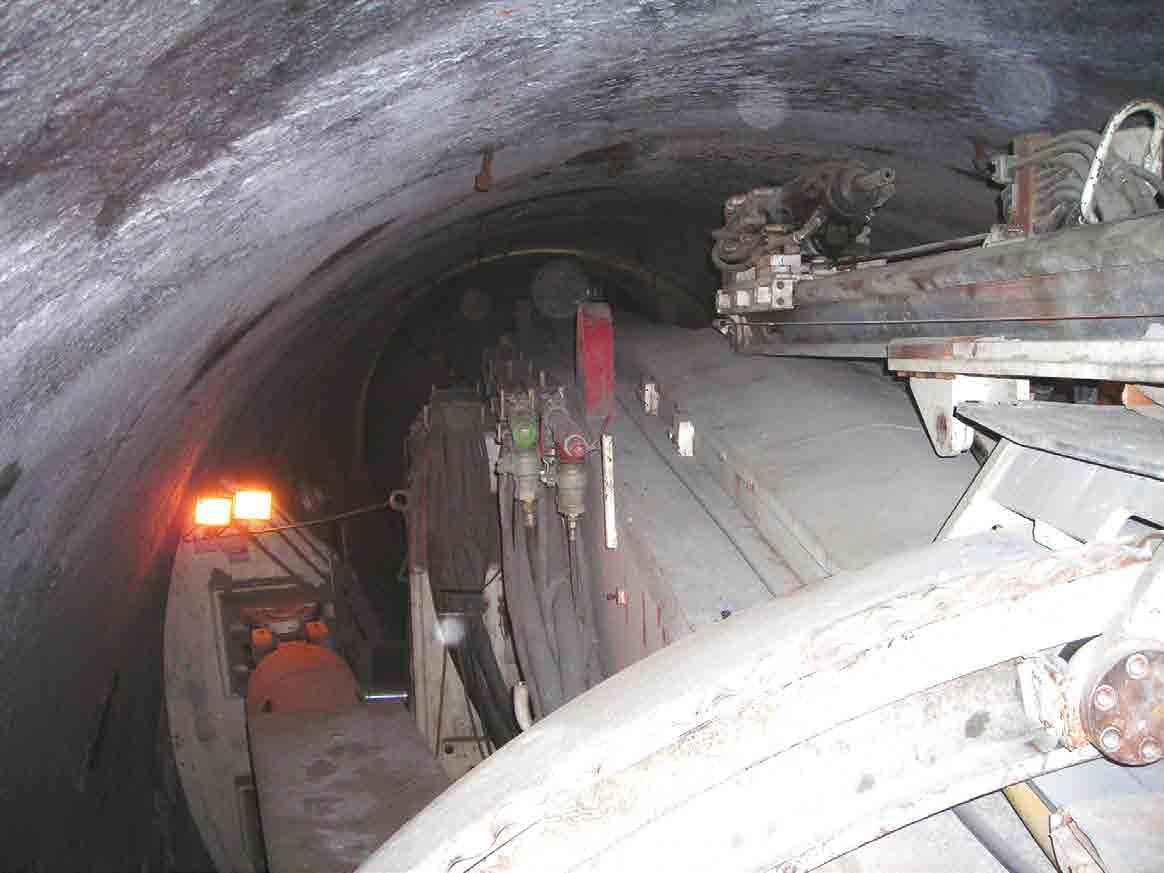
Solutions and savings in action
There are countless examples of how Autogard products have enhanced a company’s productivity and at the same time save it large sums of money. One such case involves one of the world’s largest producers of absorbent pads used for cleaning up oil spills. Thanks to Autogard, this company was able to increase its production efficiency by more than 50 per cent, thus resulting in savings of almost €100,000 in the first year. This particular situation involved a rotary cutter wheel that trimmed the material being processed and was being driven by a timing belt and sheave. The problem occurred when the material built up on the blades, eventually causing the cutter to jam and break the belt.
At the height of a recent oil spill disaster, the company was required to work 24 hours a day and 7 days a week, in order to meet the demand for its oil-absorbent products. However, the heavy volumes required, caused the conveyor belts to break on a regular basis and when they did, the material continued to pile up on the floor of the factory. This resulted in the material having to be either reprocessed or scrapped altogether. Autogard provided the solution in the form of its Series 400 torque limiter, which was attached to the company’s existing sheave and provided precise disengagement at the required torque before the jam could occur.
Since installing the Autogard torque limiter, the customer has experienced huge savings in downtime with a record two years running without a single belt breakage. At the same time, the oil pad manufacturing company enjoyed major savings in production with 50 per cent less scrap being produced. This was in addition to making big savings in labour costs and the replacement of broken belts. n

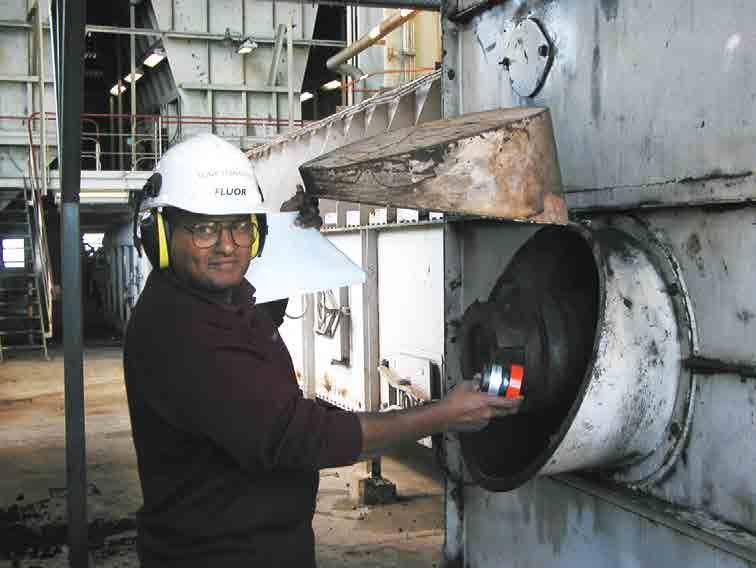
For further information about Autogard’s advanced products and protection systems visit: www.autogard.com