
6 minute read
Sensing the difference with amazing skills


Sensonor AS is a leading manufacturer of gyro, inertia and pressure products. Abigail Saltmarsh looks at the company’s recent success.
Sensonor AS has always emphasised innovation but with SAR500 products currently under development, the company is looking ahead for significant growth through an ever-broadening portfolio of ground-breaking technologies.
Hans Richard Petersen, vice-president of marketing and strategic sales at Sensonor AS, says new products such as the STIM300 and STIM210, are already making a name for themselves in the world of precision MEMS technology solutions. Sensonor AS plans to remain ahead of the industry.
“Most of our future growth will be organic,” he explains, “and this will be achieved by widening our product portfolio. We will focus on our unique development projects. We compete with the biggest industry players around the world and our customers realise we have a great deal to offer.” High precision
For more than 25 years, Sensonor AS, a leading manufacturer of gyro and pressure products for high precision applications, played a significant role in the global MEMS industry. Today, its gyro modules and inertial measurement units (IMUs) are the smallest and highest-performing commercially available products in this category worldwide. Sensonor AS’s products are used in a wide
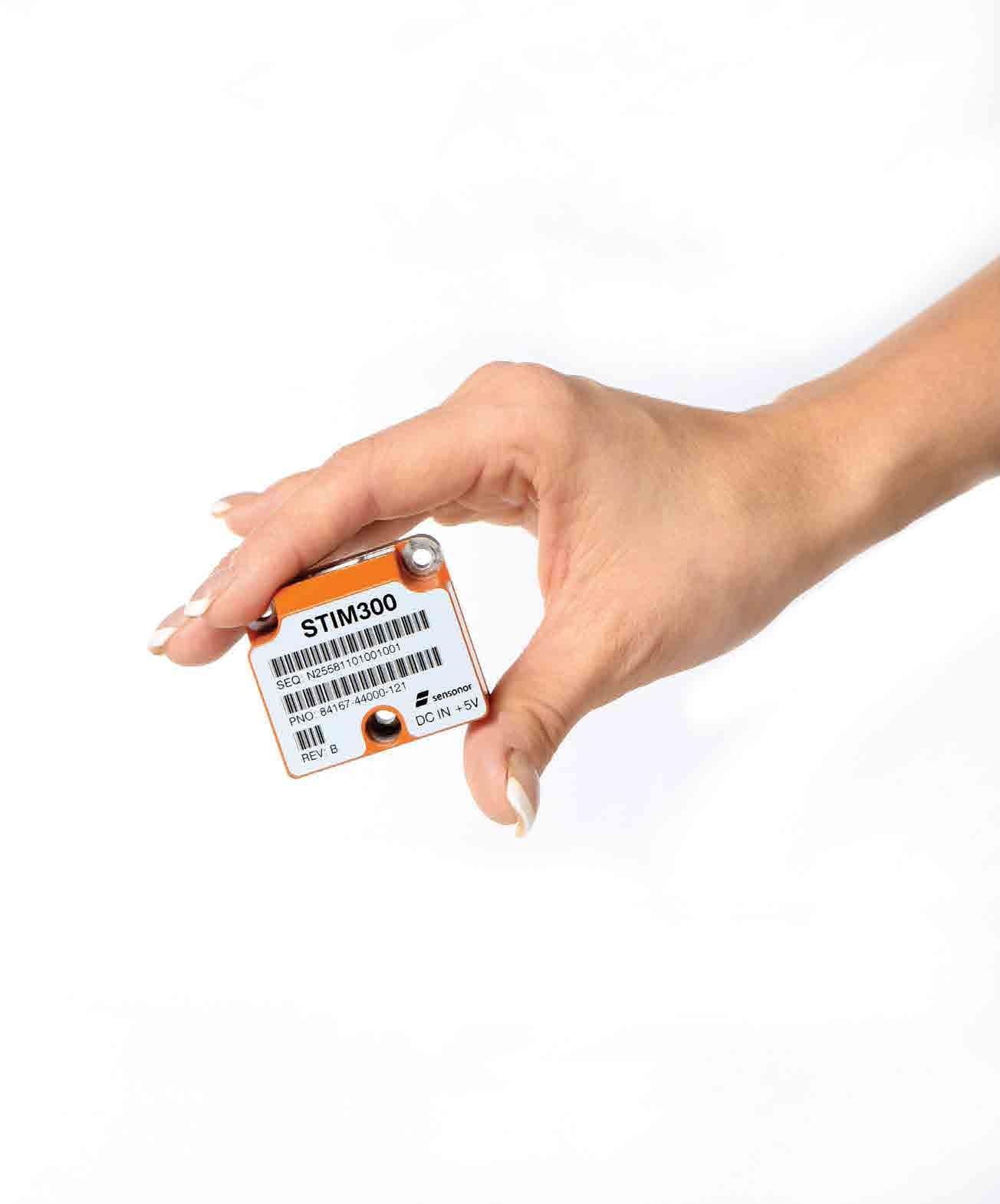

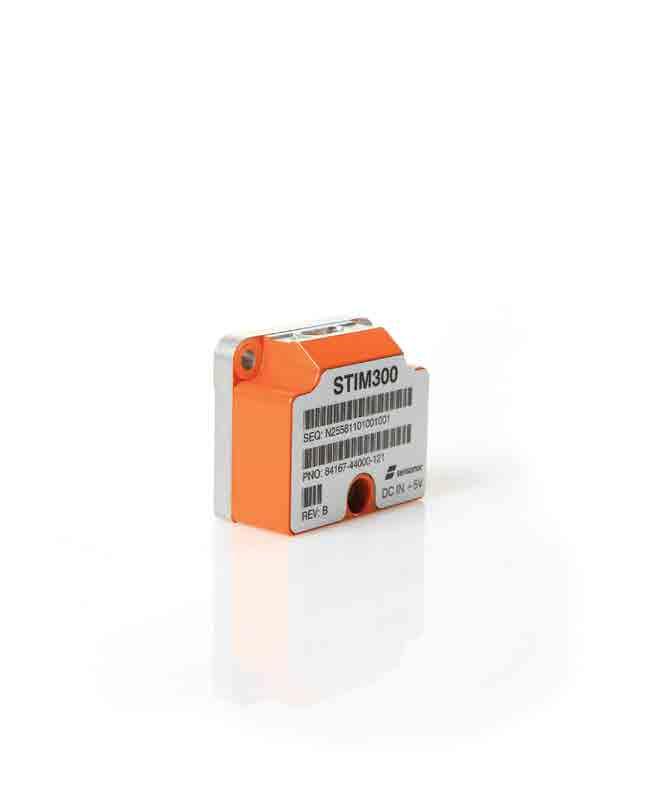

range of applications for the defence, energy and aerospace industries and are used for navigation, guidance and stabilisation.
Sensonor AS has produced more than 250 million pressure sensors, 250 million accelerometers, and more than two million gyros that have been shipped to customers for use in a wide array of applications. Over the years, it has also achieved a catalogue of achievements including launching the first MEMS pressure sensor for aircraft engine control, the first MEMS accelerometer for air bag systems, the first optical pressure sensor for down hole well monitoring and the first low-cost automotive gyro.
“We started off with our core business in defence and aerospace before moving into automotive and consumer applications, where we have had a presence for the last 10 years or so,” says Mr Petersen. “However, we recently decided to increase our concentration on high precision products to gain increasing focus on this part of the market in the future.
“It was a challenge for us and we followed a potentially risky strategy of aggressive pricing while customers realised what Sensonor AS was capable of. But, our strategy has proven success and we are seeing increasing levels of demand.”
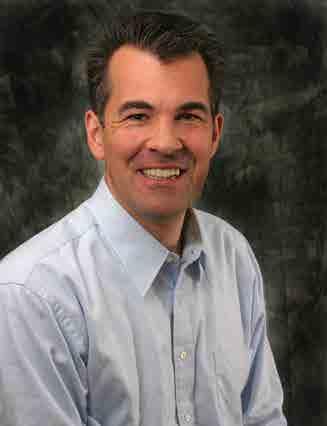
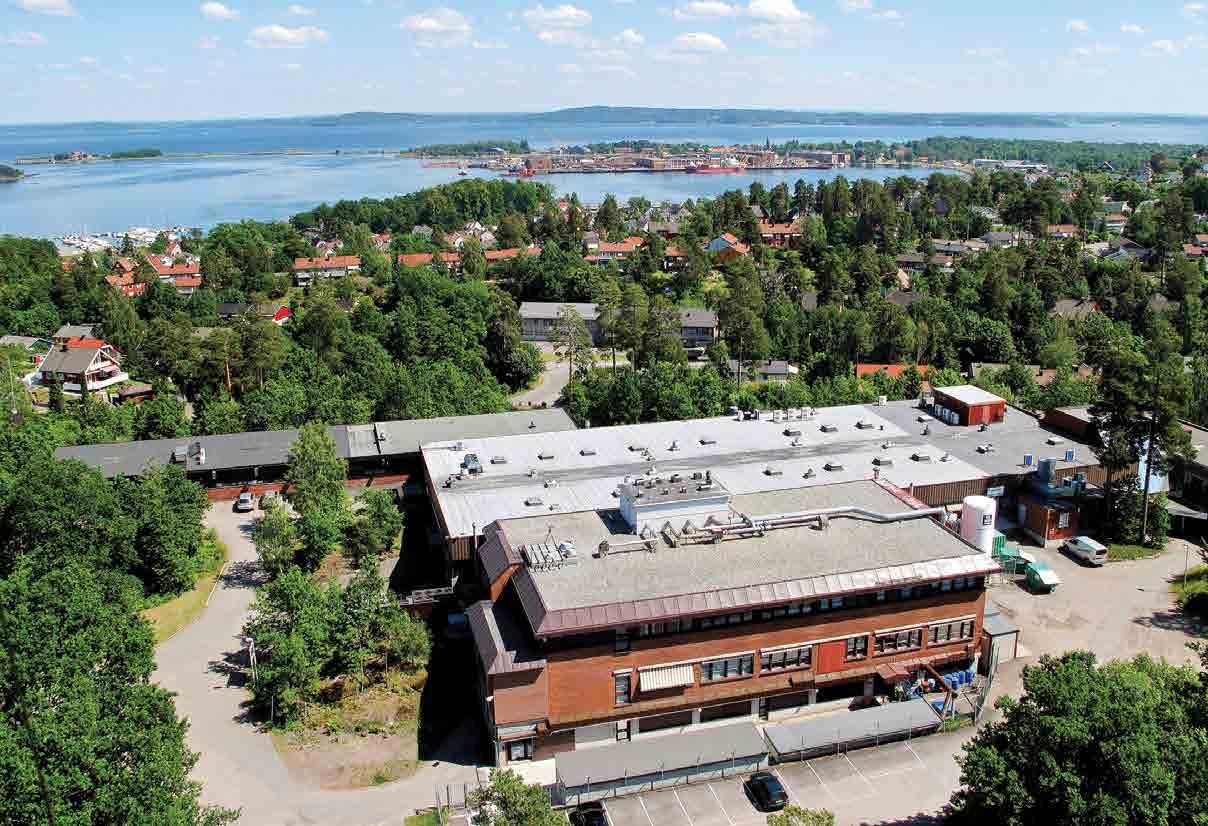
Lower cost and more robust
Historically, Sensonor AS has been known for the development of a triple stack hermetic wafer bonding technology, which has extremely good long-term properties. The technology is based on a combination of micro-machined single crystalline silicon and micro-machined glass wafers. These wafers are then bonded together using anodic bonding and a controlled gas pressure, creating electrical connections into the bonded cavity by utilising semiconductor diffusions buried under a layer of epitaxial silicon.
These stable, long-term properties have been explored within high precision applications by customers using pressure sensors as well as by those using Sensonor’s ButterflyGyroTM sensors. From this platform, the company has gone on to launch new products aiming to replace traditional high precision technology by offering lower cost and better robustness in smaller housings, using less power at equal performance.
Realising the vision
The STIM202, consists of one, two or three ultra high accuracy gyros in a miniature package with an RS422 interface. The module function is based on an integrated 32-bit microcontroller that provides flexibility in the configuration.
“We started several projects with these back in 2008 that will go into regular volume production in 2013. This targets applications that have high levels of shocks,” Mr Petersen explains. “Then we have the STIM210, which does not have that capability, but the STIM210 has better navigation capabilities.”
The STIM210 represents the world’s highest performance silicon MEMS gyro module and also presents a breakthrough for system designers who are under constant pressure to provide smaller, better and lower-cost solutions.
“The STIM210 is another step in our ongoing success in realising our vision of providing more stable, robust and affordable high performance gyros to the market place. MEMS gyros continue to advance in performance. With STIM210 in our portfolio we will better address more applications in the navigation and guidance segment.”
An important addition
Towards the end of 2012, Sensonor AS also launched its tactical grade miniature IMU, STIM300. This is a small, lightweight and low power International Traffic in Arms Regulations-free, high-performance product.
As well as being non-GPS aided and insensitive to magnetic fields, it offers 12 times less weight, 10 times less volume and five times less power consumption over existing solutions with similar performance.
“The STIM300 is an important addition to our inertia portfolio and another step in our strategy to increase our reach in the high-performance inertia market. The new IMU has great advantages to applications, where size, weight and power consumption is critical. We see a robust interest from segments where system payload must be maximised,” Mr Petersen states. “The performance of the sensor cluster in STIM300 allows navigation tasks that earlier had to be addressed by FOG (fibre optic gyro) solutions.”
Change on the horizon
Sensonor AS is currently developing SAR500, Mr Petersen said. This is a novel high-precision, low-noise, high-stability, calibrated and compensated digital oscillatory gyroscope with SPI interface housed in a custom-made ceramic package.
The SAR500 contains a Butterfly MEMS die and an analogue ASIC, housed in a rigid custom-made ceramic package. It is factorycalibrated and compensated for temperature effects to provide high-accuracy digital output over a broad temperature range.
“This is very exciting for us as the gyro will be between 10 and 100 times higher performance than anything else we are doing at the moment and if it comes on line as we plan, there will be a big change in the market as a whole,” he says.
“We hope to start sampling it toward the end of this year. The plan is to make it available, giving our customers the ability to compete much more within the market.” n
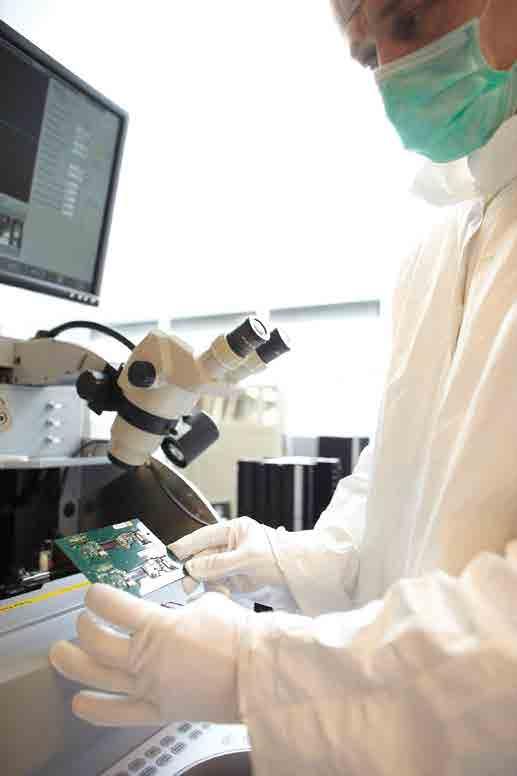
LEADING IN PATTERNED PACKAGING WAFERS
We produce reliable packaging wafers when it comes to technology. Billions of MEMS with successfully implemented wafers from Plan Optik in automotive, aerospace, chemistry, pharmaceuticals and bio technology applications tell its own tale.
Ueber der Bitz 3 56479 Elsoff • Germany T +49 2664 5068 0 F +49 2664 5068 91 info@planoptik.com www.planoptik.com
PLAN OPTIK AG
PLAN OPTIK AG produces wafers from glass, quartz and glass-siliconcompounds up to 300 mm diameter. In particular wafers for MEMS wafer-level-packaging and process carriers from glass. They are machined to a very tight thickness tolerance and total thickness variation (ttv). Sub-nanometer roughness and virtually defect free surfaces make them suitable for high end applications such as requested by the automotive industry. Customized cavities, vias and holes are manufactured by mechanical and lithographical processes. Miicro lens- and conductive via wafers (through-glass-vias) are available. Plan Optik has set the standard in respect to high end substrates for the MEMS and semiconductor industry.