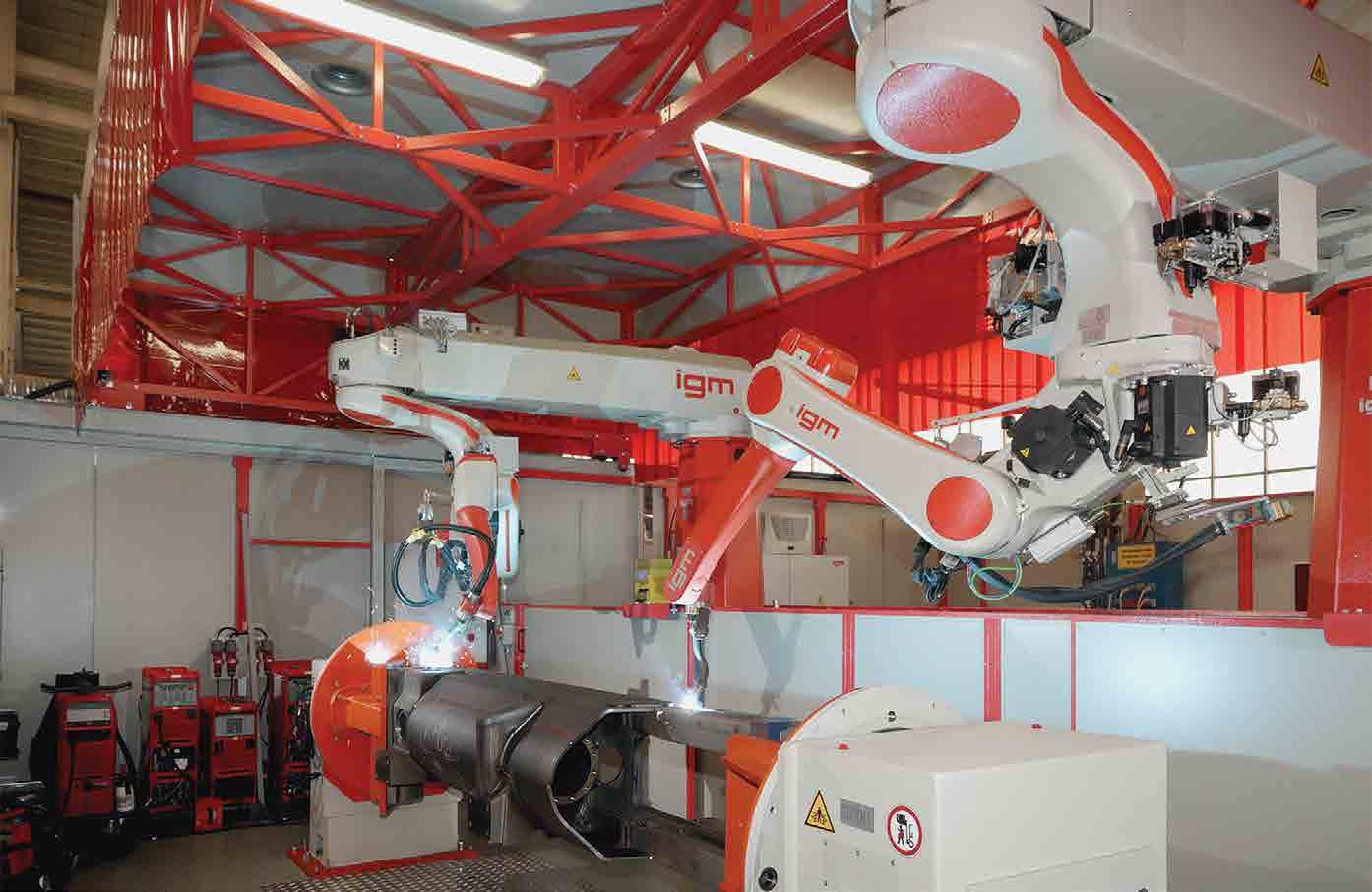
4 minute read
Unique track record for heavy engineering
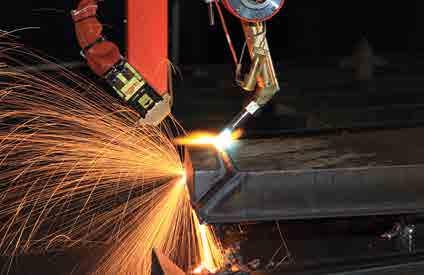
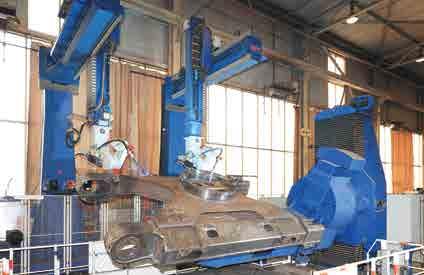
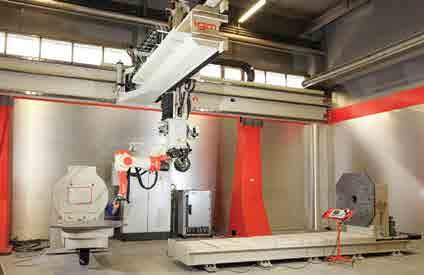

IGM Robotersysteme AG is a global leader in the production of customised, tracked and automated robotised welding systems for heavy industry. Philip Yorke talked to Martin Wihsbeck, the company’s marketing manager about its latest innovative robotic products and move into the development of complete, flexible manufacturing systems.
IN 1967 two innovative industrial engineers, Günther Kloimüller and Franz Vokurka established a trading house for marketing welding machines in Austria. Their combined creative technical expertise led them to develop welding robots in the late 1970s. One of these, the Limat 2000, was awarded the Austrian prize for innovation in 1981.
By 1992, IGM had set up a global network of sales and service centres with representation in more than 20 countries worldwide. Another landmark was reached when the company opened its new, purpose-built, assembly centre in the industrial park of Győr in Hungary.
The company’s reputation throughout heavy industry for innovative, high-quality, welding robot systems has resulted in it becoming the company of choice in almost every area of industrial welding and cutting operations. This reputation as a specialist for large-scale projects is based upon its steady stream of major contracts from heavy engineering companies since the early 1980s. In fact the company’s special floor track systems of up to 100 metres in length and work piece manipulators with a payload of 25t and more were developed to meet the precise requirements of this sector of industry.
Components with larger than usual dimensions such as those found in bridge construction and ship building are manufactured by IGM systems using robotised portal welding units, which are capable of taking components of up to 25 metres in width. IGM’s advanced robotic systems are also used in many other industrial applications, such as in the manufacture of excavators, railway wagons and locomotives, as well as for boiler making and the construction of truck and fork lift components.
Flexible solutions for complex applications
Today IGM offers tailor-made, flexible manufacturing systems which provide much more than simply advanced welding technology. These customised constructions involve loading, conveying, stretching, bending and cutting facilities, as well as measuring, manipulating, editing, storing and controlling. For additional production requirements IGM provides handling devices and can develop special-purpose machines. IGM takes care of an entire project from the placing of the order to the final commissioning as a main contractor.
Today, the whole fabrication line including the robotic cells is controlled by a single host computer, with graphic information displays making the monitoring and operation of the production line simple and straightforward. Mr Wihsbeck said, “When clients come to us with their drawings they know that they will be getting added value throughout the entire value-chain. Unlike other robot manufacturers, who choose only to sell the robotic heads, we are capable of supplying complete tailor-made systems. Another key differentiator is the fact that we are a global operating company that is always in close proximity to our customers.
“Furthermore, when we arrive in a new market we stay there in order to support and grow with our clients. Yet another bonus for us is the fact that we are headquartered in Austria and this can be a particular advantage in terms of the quality of engineering that our country represents. This is especially true in markets such as Asia and the Far East.
“Currently our main growth markets are in earth moving and heat exchanger equipment; however, we are still seeing strong demand in our traditional markets, such as in railways and general construction. Earth moving is certainly the main business driver for us in China, the USA, Russia, India and Brazil. We have also developed a new laser camera system to track robots which means that we will be reducing still further our reliance on outsourcing. In fact we are now in a position to be able to develop and supply absolutely everything in-house, from original designs to the software, assembly, testing, installation and commissioning.” Synchronised laser scanning technology
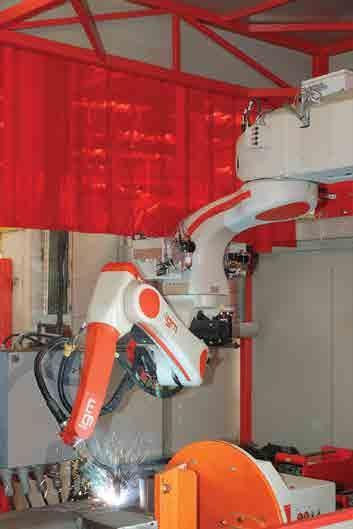
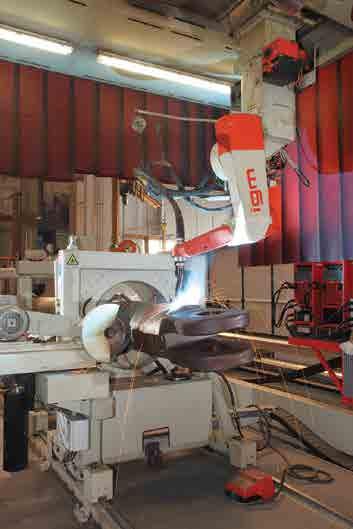
Recently, IGM launched the world’s most compact and efficient laser-scan camera iCAM designed to track different welding seam types for identifying and measuring detected gaps and for compensating volume deviation. This ground-breaking

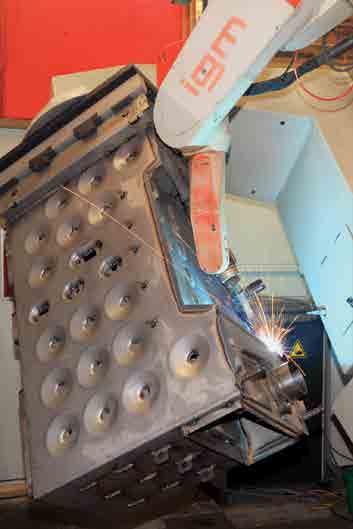
device is based on the latest synchronised laser-scan technology and features high speed stability, large and programmable work spaces. This is in addition to offering a deep visual range and a special robustness regarding ambient light and reflections. Impassivity against high frequencies and magnetic fields also makes it an ideal choice for arc welding processes, especially as they are carried out in rough environmental conditions.
This latest IGM innovative product offers many outstanding features as well as complete integration into the robotic controls. The user also benefits from the wide range of European and Asian languages available in the software package.
Following on the heels of the launch of this unique product, IGM recently announced its latest RTi 400 Series of arc-welding robots. This new development was prompted by the demands from customers for a bigger work zone, which initiated the planning for a modular series of welding robots, leading to 6, 7, 8 or even 9 axes-robots comprising several different modules. The new product’s optimal set-up of all system components permits a reduction in transfer time by up to 30 per cent for all construction sizes as well as numerous other advantages. n
For further information about IGM’s advanced technology products and services visit: www.igm.at