
5 minute read
Extreme precision Bruno Presezzi
EXTREME PRECISION
Since its establishment in 1954, Bruno Presezzi SpA has grown to being a high-profile engineering, mechanical processing and construction company. Barbara Rossi finds out a little more about the company from its MD, Mr Alberto Presezzi.

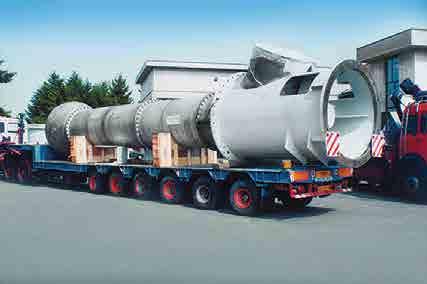
Despite now being listed on the stock market, the company is still firmly in the hands of the founding family (Mr Alberto Presezzi is the son of Bruno Presezzi, founder of the company). It can count on a staff of 200 people and for 2013 predicts a total production value of €77,000,000. Bruno Presezzi SpA operates from its main site in Burago Molgora (Milan), as well as from two nearby sites in Colnago. The Burago Molgora plant occupies an area of 36,000m2, 9000 of which is covered, while Colnago 1 has an area of 3000m2 and Colnago 2 also covers an area of the same size. As Mr Presezzi tells Industry Europe, “We had a new office building constructed in recent years, which has been designed following innovative concepts to give staff the ability to work together and interact with each other in a different way, thus increasing efficiency. The project has been carried out using quality materials, following a ‘green philosophy’, in accordance with the beliefs of the company.”
The company mainly carries out projects commissioned by clients and its core business covers three areas, namely aluminium, power and oil and gas. In fact, Bruno Presezzi SpA manufactures its own patented continuous aluminium casting line for aluminium coil production, which it sells to aluminium coil manufacturers all over the world, as well as producing spare parts for the same line in the form of the shells to be mounted on the rolls. The coils produced with the continuous casting line are then laminated and reduced and thus employed in a variety of sectors, ranging from automotive to foil or air-conditioner production. A wide range of products
In terms of the power sector, the company is active in this field by manufacturing components supplied to gas and steam turbine producers, as well as by producing large exhaust casing and turbine rotors.
The third core business sector that the company serves, that of oil and gas, is a more recent venture. In fact, as Mr Presezzi explains, “We launched our products for this sector, valves which we have engineered, in June 2011 with a group of highly skilled new staff. We are now fully operational and we supply our valves to both oil companies and contractors which employ them in their extraction, production and transportation processes. In fact, our valves are installed in pipelines, refineries and extraction centres. We also supply equipment for other sectors,
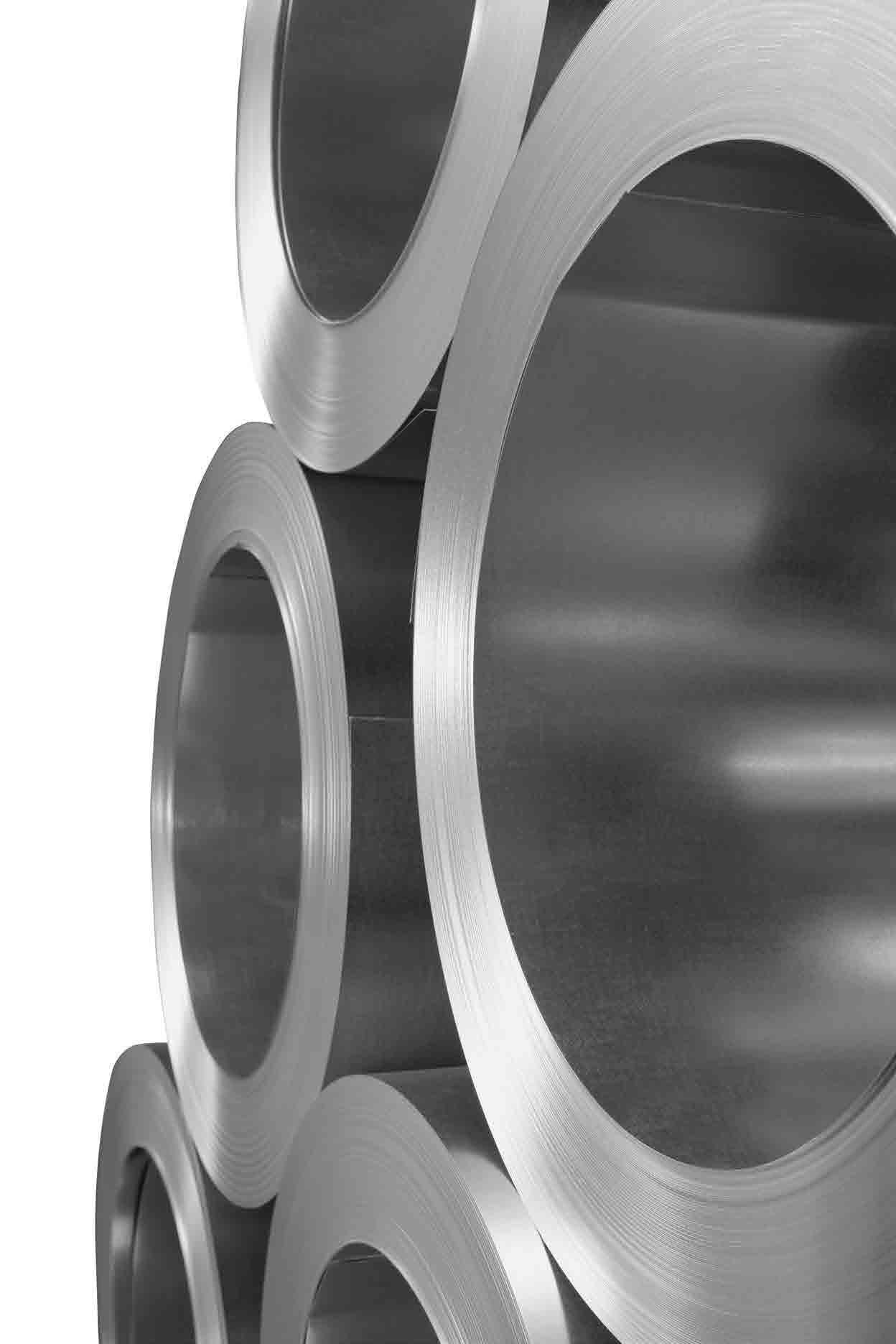

Via G. Vittorio, 23 20060 Vignate (Italy) P.IVA 11569960153 T: +39 02.9566025 F: +3902.9567227 E: marco@tecnomecvignate.it
www.tecnomecvignate.it
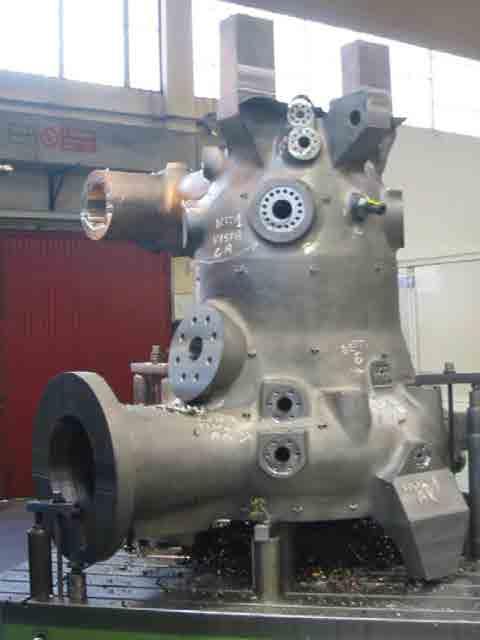

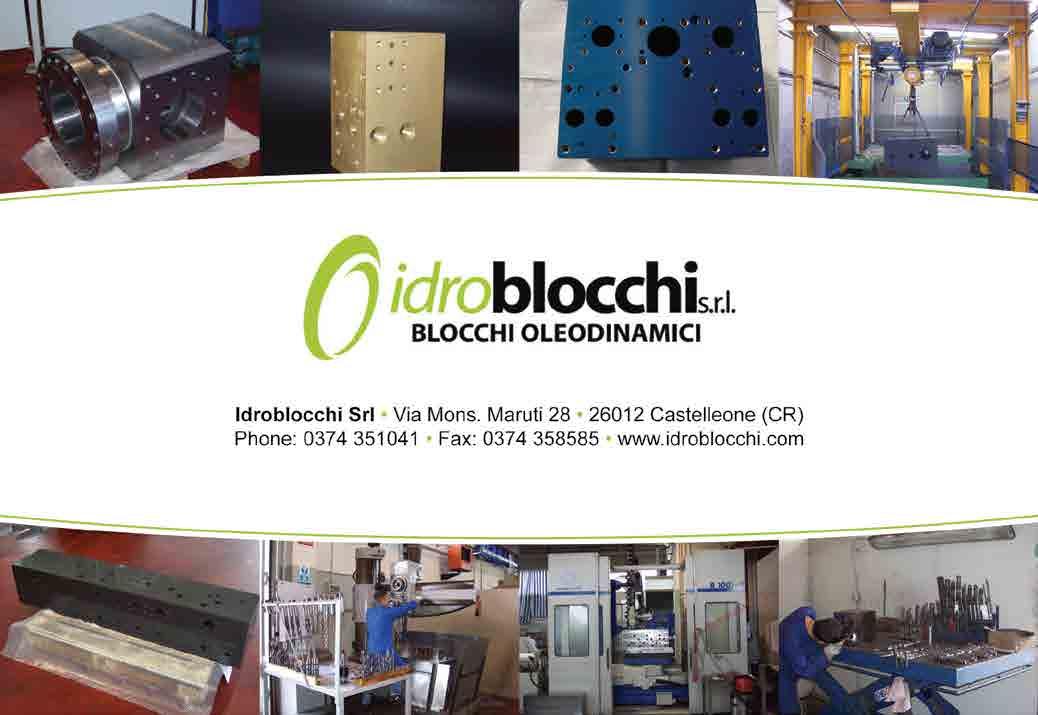
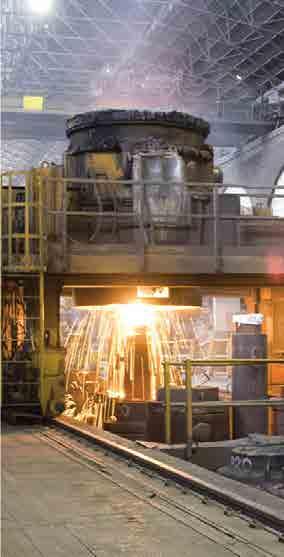
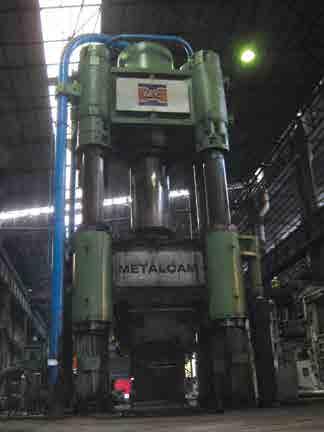
Metalcam is one of the most important Italian manufacturers of open die forging on high-quality steels.
Metalcam has an integrated end to end production cycle that combines in a single site:
Metalcam offers a wide range of fi nished products for the following industrial sectors:
• Oil & Gas and Petrochemical • Mechanical and Extrusion • Power Generation and Shipbuilding
• Product and process engineering • Steel production according to specifi c customer needs • Forging • Heat treatment • Machining • Quality control
Metalcam S.p.A. I-25043 Breno (BS), via Leonardo da Vinci 3 Phone: +39 0364 238 1 Fax: +39 0364 320 768 Email: forging@metalcam.it www.metalcam.it
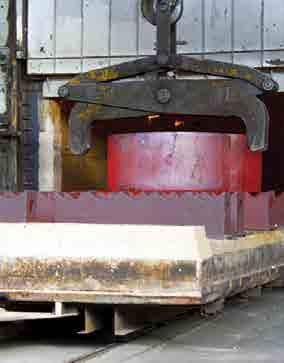
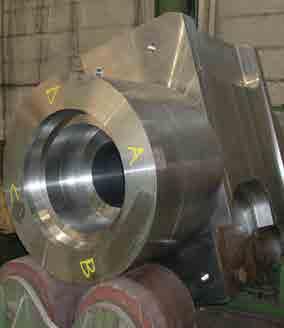
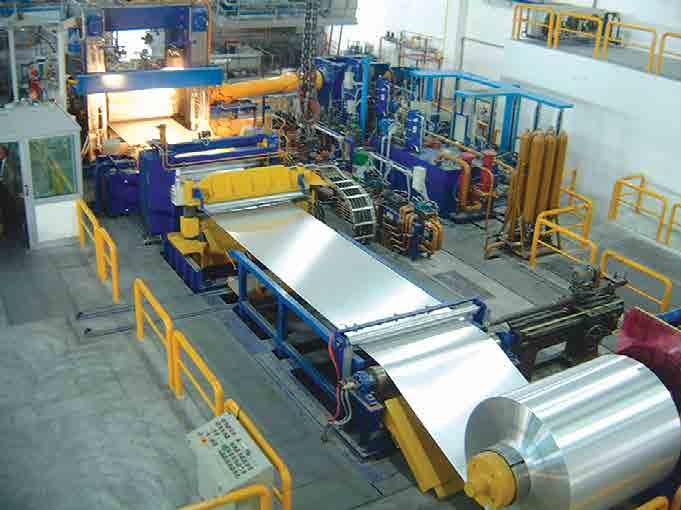
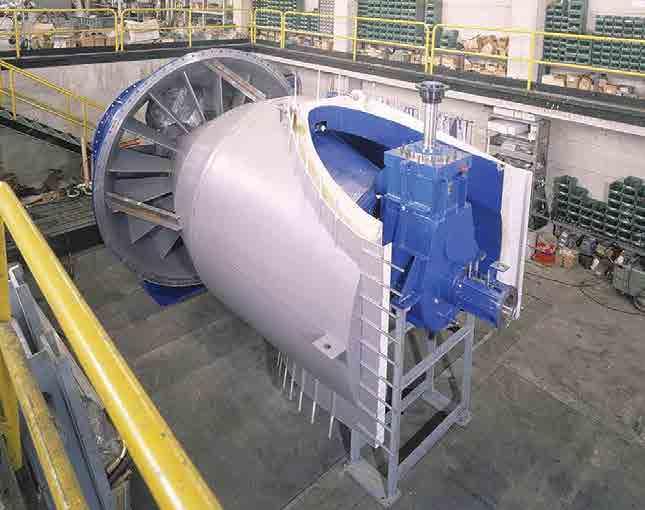
apart from the three core areas previously mentioned, that we are able to offer thanks to the fact that we have a very strong technical department. Alongside our speciality machines we offer a strong after-sales service, including a spare parts programme and client training.”
As mentioned, the company offers machines and complete units, as well as components, and examples of its products include, as well as the previously mentioned complete continuous casting line, presses, turbine casing, shafts, hot rolls, nozzles, marine pumps, hydraulic valves, steel structures, internal and external cladding, reactors and super alloy constructions. The company is proud of its stock of CNC machines, as well as of its testing department and of the quality guarantee it is able to offer. Recently it has invested in electron beam welding technology. Thanks to this large high-tech machine it will be possible to carry out welding in large dimensions. Supplying our products all over the world
“The power sector is currently our main market, however oil and gas is the fastestgrowing area in terms of the forecast for next year. Geographically we cover different markets, ranging from western Europe, North, Central and South America (Brazil, Argentina and Mexico come to mind in particular), to the Middle East, Russia, Kazakhstan, Serbia, Romania, Turkey, Japan, Nigeria and India. Export accounts for over 90 per cent of turnover, further increasing if some of our Italian clients will then export the products for which they use our components is taken into account.
“While western Europe and the Middle East are our main geographical markets today, in terms of growth in the near future the markets offering the best forecast are still in the Middle East, but this time alongside Russia. We expect a positive trend in both 2013 and 2014, which I think is an impressive result in itself in the current economic situation. We’ll carry on investing in quality in terms of staff, as well as in terms of acquiring strategic and latest generation machinery. R&D is important to us and in the last year we have channelled 3 per cent of our turnover into this. The new electron beam technology that we have acquired will have an important role to play in our development, as it opens up possibilities in welding work of larger dimensions. ” n
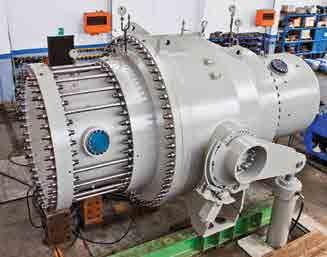
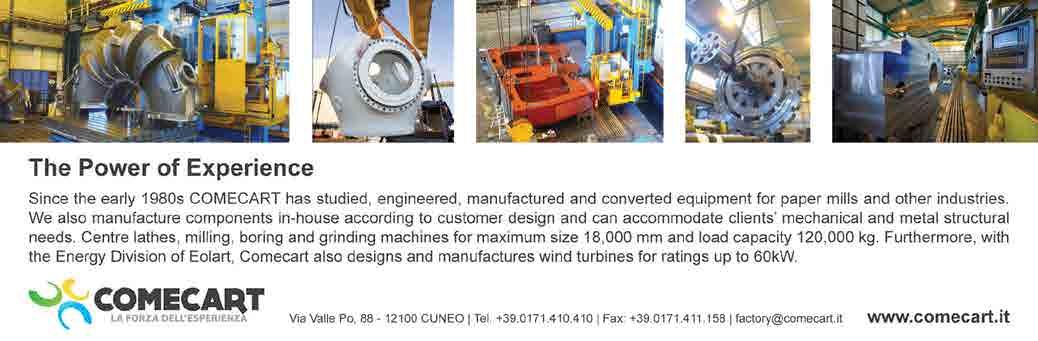