
5 minute read
Global leader in welding and cutting ESAB
GLOBAL LEADER IN
WELDING AND CUTTING
ESAB is one of the world’s largest and most experienced manufacturers of welding and cutting equipment and welding filler metals, with a history dating back to 1904. Recognized as the technological leader in the industry, ESAB is committed to providing cost effective solutions for its customers.
Following his invention of the covered welding electrode back in 1904, Oscar Kjellberg founded ESAB in Sweden. Since then, the company has constantly improved on existing methods and materials. At the same time, ESAB has developed new methods to meet the challenge presented by technological progress.
More than 100 years of continuous research, development and manufacture have made ESAB a world leader in welding, cutting and also an international supplier of products, know-how and services that none can match. Today the company produces consumables and equipment for virtually every welding and cutting process and application in countries across the world.
ESAB serves a global market. The group is organised in the regions Europe, North America, South America, Asia/Pacific and India. It is represented in almost every country by subsidiaries or agents. Sales and support is established in 80 countries and there are 26 manufacturing plants across four continents.
The ESAB brand is synonymous with world leading expertise in the following key areas: manual welding and cutting equipment, welding consumables, welding automation and mechanized cutting systems.
For each discipline, continuous development of methods, materials and know-how is being directed to meet the challenges posed by a diversity of industry sectors. ESAB serves global customers in industries such as automotive, general fabrication & civil construction, pipelines, pipe mills, power generation, process industry, repair & maintenance, shipbuilding & offshore, transport & mobile machinery.
Global expansion
Throughout the last decade ESAB has continued to expand its global operations. In 2005 it acquired the majority of the shares in the South American joint venture Conarco and opened a new cutting factory in China. In the following year it opened a consumables factory in Zhangjiagang, China, and, as the first global company in the steel and welding industries, it implemented and achieved global ISO 14001 certification of a global Environmental Management System.
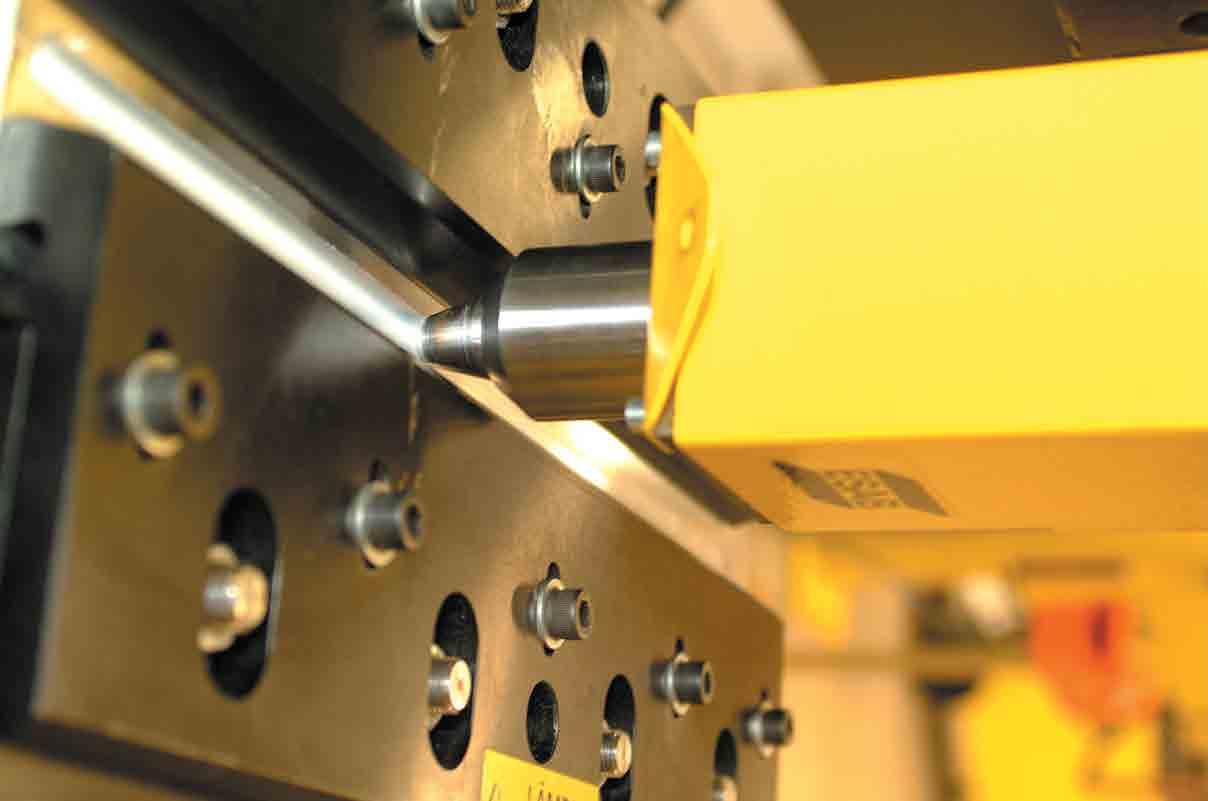
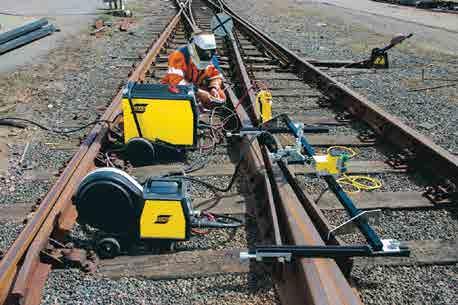
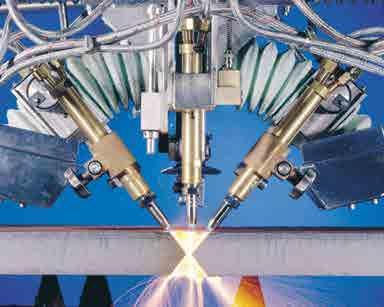

In 2007 a new sales company was opened in Romania and ESAB acquired ATAS GmbH, a German software solution company. It also acquired the welding & cutting division of Air Liquide Argentina S.A. (stick electrode products) and the Bulgarian stick electrodes manufacturer Electrodes JSC. A new agglomerated flux production facility was also completed at ESAB’s SVEL factory in St. Petersburg, Russia. Then, in 2008, ESAB Holdings Ltd acquired Romar Positioning Equipment Pte Limited, an automation positioning and workpiece handling manufacturer in Asia. In the same year ESAB won the top Frost and Sullivan industry award, the “2008 Global Welding Consumables Customer Service Excellence”.
In January 2012 ESAB’s parent company Charter International plc was acquired by Colfax Corporation. Colfax Corporation, based in Fulton MD, USA, is a diversified industrial manufacturing company listed on the New York Stock Exchange. Charter International plc resided in Ireland and was the parent of both ESAB and Howden, a premier manufacturer of heavy-duty air and gas handling equipment.
“We are very excited by the future potential and enhanced opportunities that this acquisition will bring to ESAB,” said Clay Kiefaber, Colfax CEO. “Colfax Corporation is a leading manufacturing company with a proven operating system – the Colfax Business System – and is solidly focused on customer needs and the development of strong brands. This is a perfect fit for ESAB, which is a global leader in the welding industry – a position it has attained by building strong partnerships with its customers and by creating a brand that is trusted worldwide.”
Wind energy order
Last year ESAB won a major order from Denmark for automation solutions for welding on wind turbine towers. ESAB has been involved in wind generation since its inception. The company’s automation solutions, welding equipment and consumables (welding wire) have been used in the production of more than half the world’s wind turbines.
Steel construction company Bladt Industries A/S, fabricates, amongst other things, steel structures for the offshore wind energy sector, the oil and gas industry and the construction business. ESAB had already delivered eight new Tandem column and booms for multiwire welding, twenty sets of 300 and 400 tons conventional roller beds, five pieces of ESAB A6 powder tractors and retrofit of eight existing Tandem column and booms. The new orders for Bladt Industries included another four sets of ESAB Tandem column and booms.
“The order is the single largest in the Nordic region for ESAB automation products and it is exciting to participate in such a large scale project,” said Magnus Andersson, Automation Sales Manager at ESAB in the Nordic region.
New products
Continuous improvement and innovation define the future for ESAB, driving breakthrough ideas for technology, products, solutions, and processes. Already in 2013 it has introduced two new high tech cutting machines. The Hydrocut™ LX Waterjet Shape Cutting Machine is the latest version of ESAB’s popular Low-Rail Hydrocut machine. This new Hydrocut LX includes all of the recent

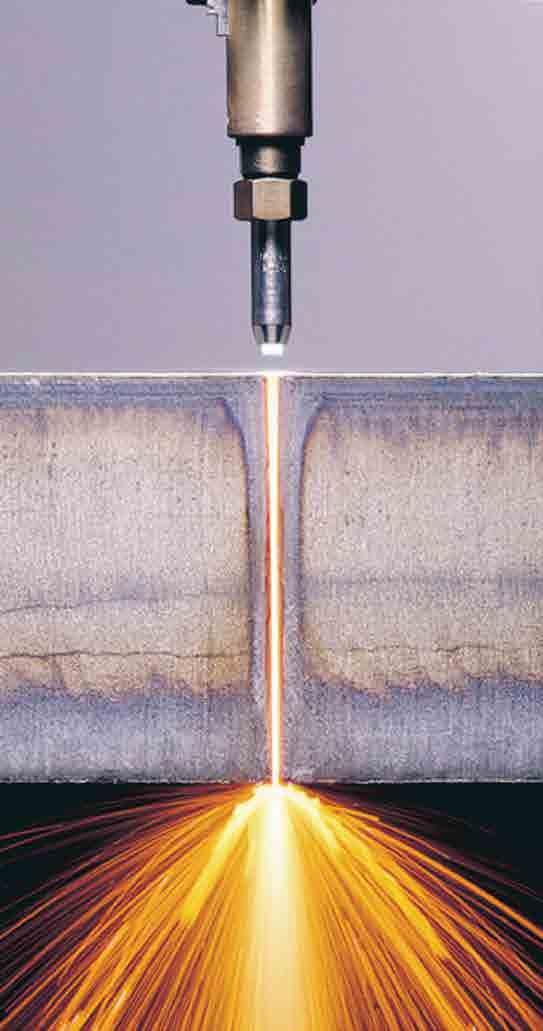
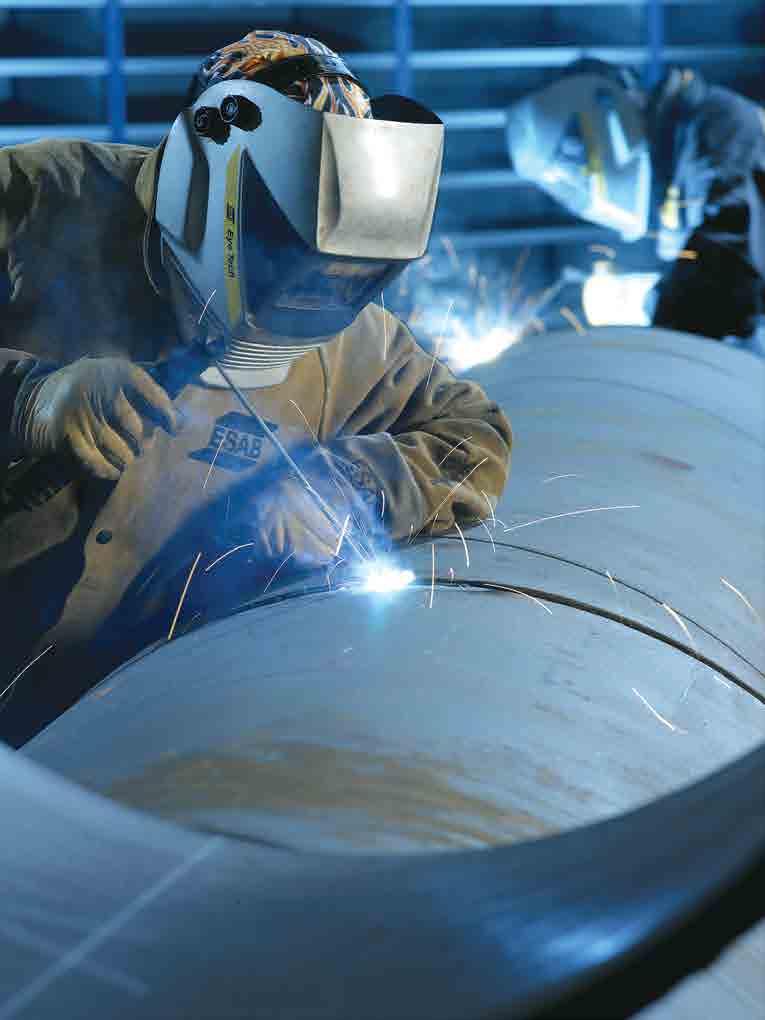
advancements in gantry design and modular assembly that have been used on ESAB’s X series gantry, making it an enhanced replacement for the Hydrocut LR gantry.
The Hydrocut LX is a large gantry with a high-stiffness beam design featuring dual precision linear rails and precision rack & pinion drives. The size and strength of this gantry make it ideal for accurate waterjet cutting over large working areas with multiple process tools. It is widely used throughout heavy manufacturing and fabrication industries when waterjet cutting is required on large plates in harsh environments.
The company has also launched the PowerCutTM 700 portable plasma cutting package that is suitable for use on all electrically conductive materials in production, assembly, repair and maintenance applications. Well balanced and with a convenient, comfortable carrying handle, the PowerCut 700 can be carried easily from one work site to the next, or to exactly where it is needed in the workshop. However, the machine can also be fitted with a CNC interface so that it can be connected directly to a cutting table. n
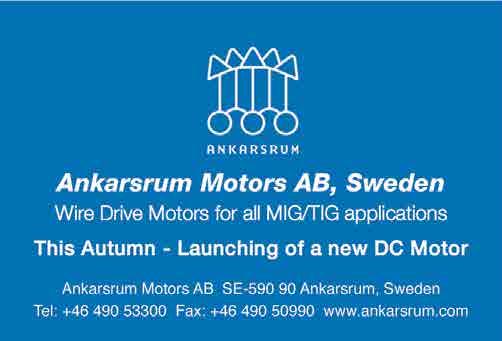