
4 minute read
Turbocharged success BorgWarner Group
TURBOCHARGED SUCCESS
The BorgWarner Group is the world’s leading automotive supplier and its Turbo Systems division, with a European base in the small town of Oroszlány, Hungary (the second largest production site for the group as a whole) makes up two-thirds of its production output. Established in 2001, this subsidiary has seen continuous dynamic growth.
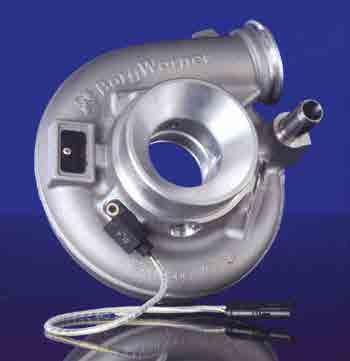
The American BorgWarner Group is a technology leader in the field of turbocharging and today has 59 locations in 19 countries. Two-thirds of its products are turbocharger systems that allow customers to meet current and future emission standards whilst achieving significant reductions in fuel consumption.
The company sets high standards in regards to performance, smooth running, reliability and durability. BorgWarner Turbo Systems has established sites in Mexico, China, South Korea, Poland and Germany in addition to the Hungarian site in Oroszlány. The German manufacturing site in Kirchheimbolanden is the European centre.
In 2012 BorgWarner’s turbocharger with low-pressure exhaust gas recirculation technology won an Automotive News PACE Award. Three BorgWarner technologies were also named finalists in the 2013 competition, including its regulated three-state turbocharging system, advanced compact brushless actuator and Visctronic highspeed reservoir system.
Dynamic growth
BorgWarner turbochargers are made for cars as well as for light trucks and commercial vehicles. The Hungarian production facility was built in 2001. The factory, located in Oroszlány, was initially built to
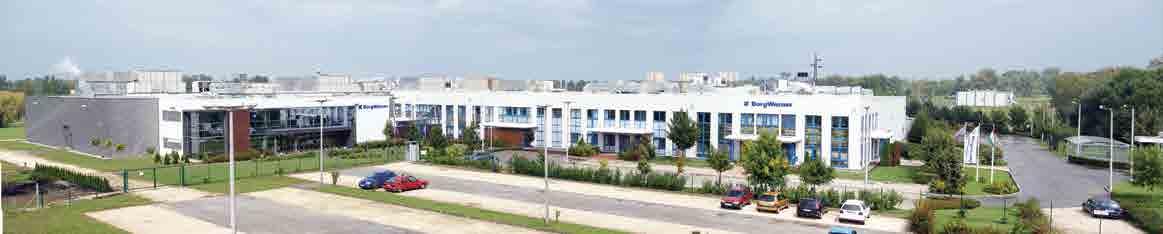
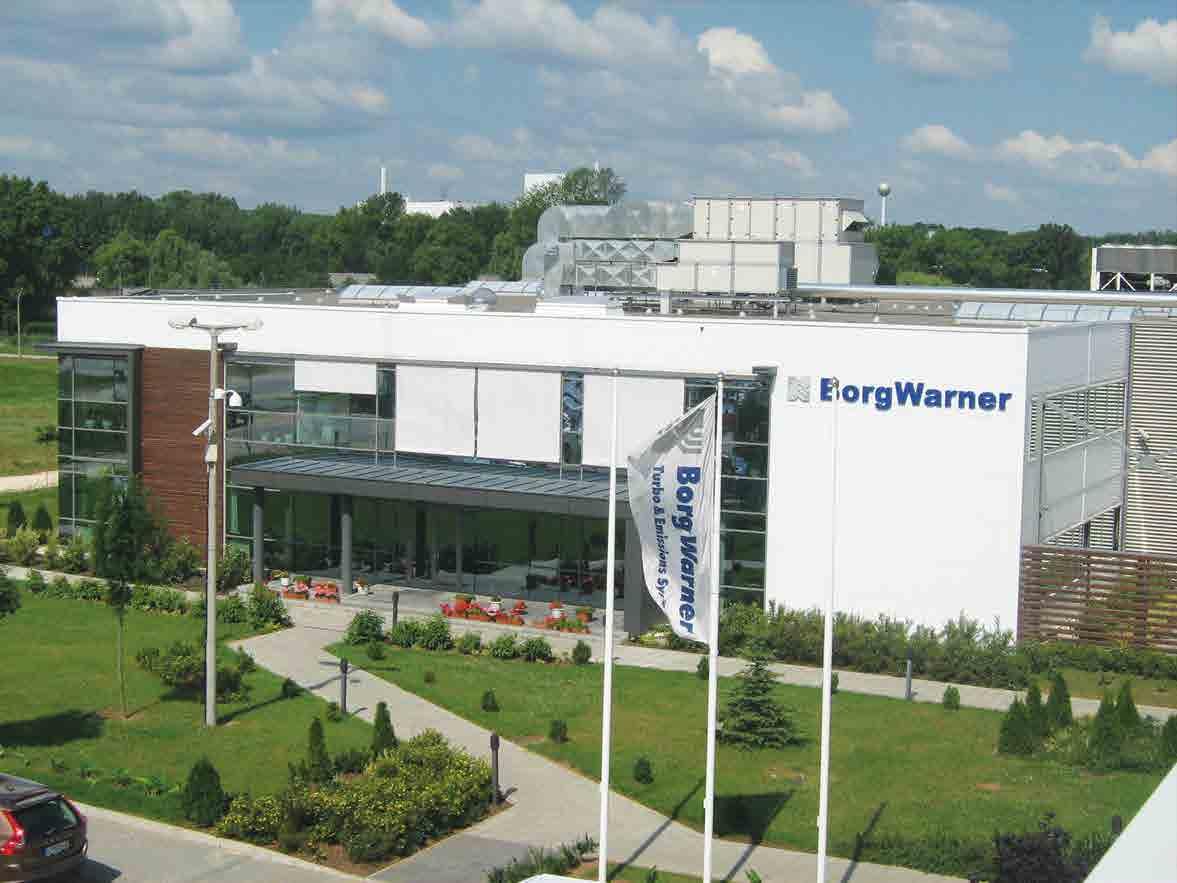
serve the Audi factory in Hungary. Initially it was only a site to assemble the turbochargers, but soon they began to manufacture and assemble the products. The company has seen dynamic development ever since, and has doubled its turnover every year. Parallel to its increasing turnover, the capacity of the production site has also continuously grown, requiring greater investment in infrastructure. Most recently was in November 2007 when a new 4000m2 production hall opened, increasing the company’s total area to 13.386m2 .
Initially BorgWarner only manufactured turbo systems for passenger cars in its Oroszlány plant. The company’s largest client is still Audi but its client base is expanding and now includes other prestigious car manufacturers including Renault, Fiat, VW, BMW, GM/Opel and Volvo.
The demand for cars with turbochargers is on the rise because of their reduced carbon-dioxide emission and increased performance. Therefore it is not surprising that whilst the growth of the global automotive sector was an average 3 per cent in the last decade, BorgWarner achieved five times greater growth in the same period.
The company will continuously improve its product range with newly developed, improved products whilst maintaining high quality.
In order to cope with the expected growth the company, which currently employs 700 people, plans to recruit more staff as well as investing in new equipment and the implementation of new production lines. “At the time of its foundation in 2001, BorgWarner Kft had one customer here; today we have 10 different clients. The complexities of the projects are getting higher, but our excellent team of professionals and existing capacities provide enough bases to fully meet the needs of our partners,” says a company spokesperson. Currently more
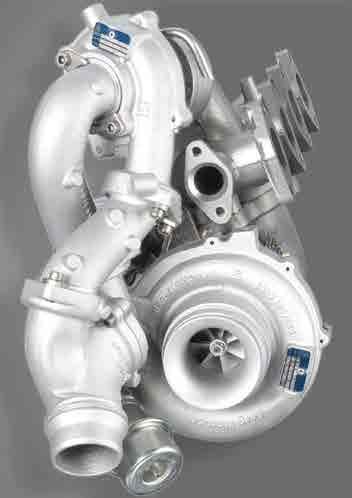
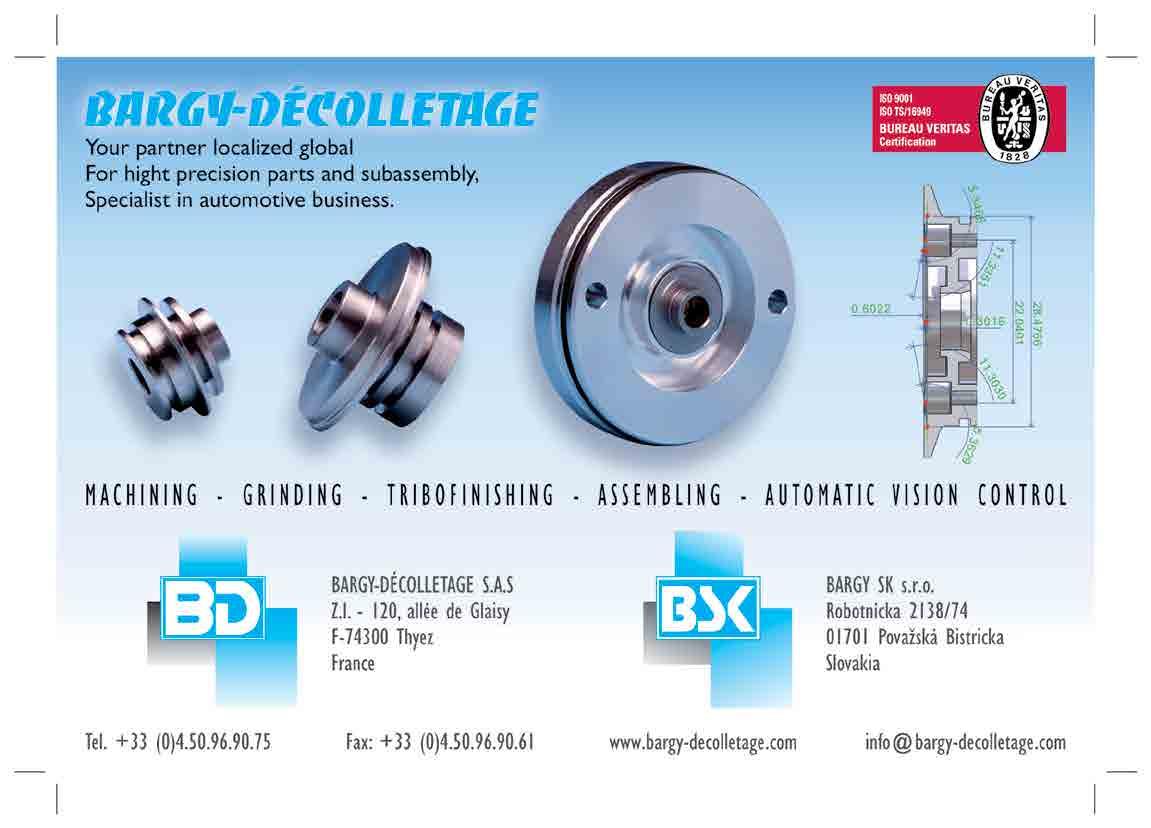
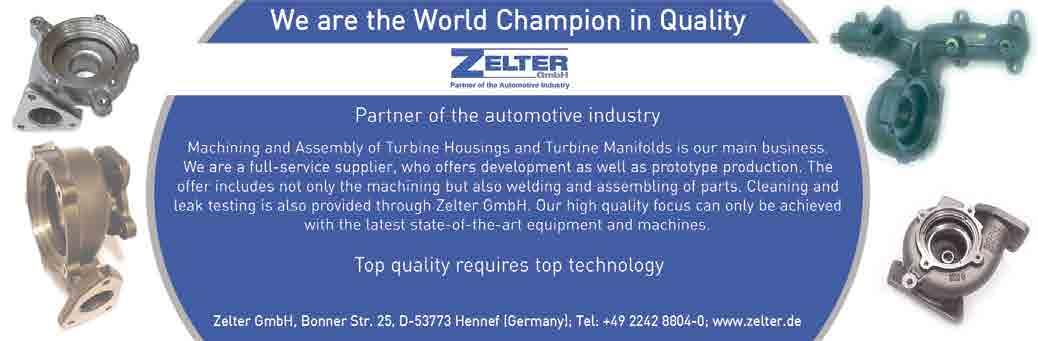
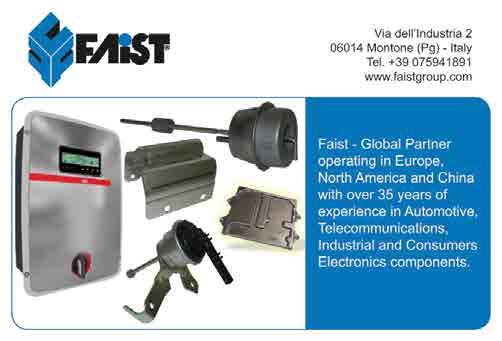
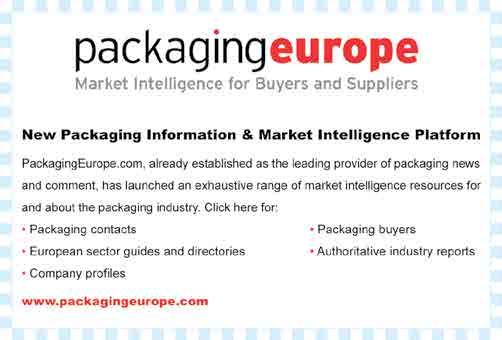
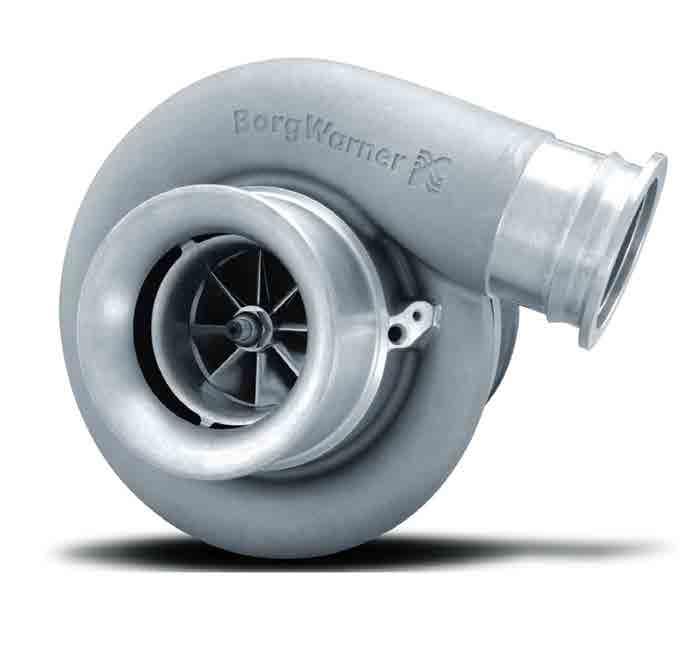
than 90 per cent of products are exported abroad, mostly in Europe, but the company’s turbo chargers are also distributed to North America and Asia. “Maintaining the relationships with our partners on a daily basis is fundamental. We only need to make small changes on our well-developed site to smoothly realise our planned growth.”
Lean management
Besides significant technological investments BorgWarner puts great emphasis on training its staff, using a new and unique training method. In order to maintain its competence it recognises the need to continue producing market-leading products and this requires excellent engineering staff who speak many foreign languages.
Predominantly the company is aiming to maintain its lean concept whilst developing its current site. For example the assembly equipment is being implemented in one direction, whilst the factory will aim to take full advantage of its existing equipment and bring in changes that will increase the efficiency of production.
“We would like to manage our operation based on a concept that decisions are made at the lowest possible levels, which will increase the quality of our products and improve our customer service,” reveals the spokesperson. “This is quite a serious investment, which is not put in to bricks and iron but to our human resources.”
Although there are no rivals in the domestic market, there are many competitors in the region especially in Germany and Slovakia. The managing director of the Hungarian subsidiary, however, has a clear view how to maintain the business for the long-term future: “In the long run we want to be the most effective turbocharger factory that also gains everybody’s support; most importantly we would like to gain the full satisfaction of our partners.” n
