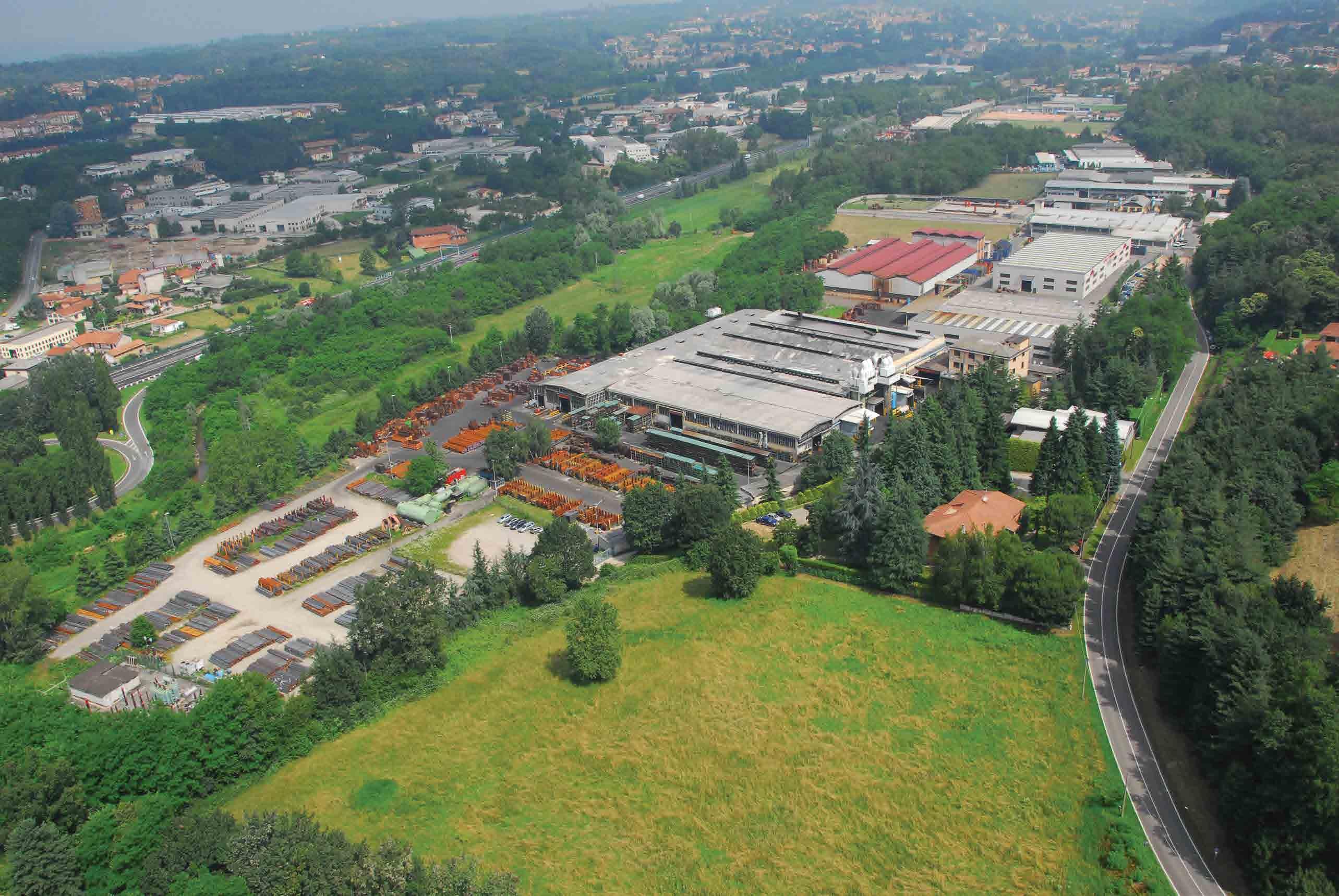
4 minute read
Steel forgings for global markets ACSA Steel Forgings
STEEL FORGINGS FOR GLOBAL MARKETS
Specialised in high-quality hot steel forgings, available in a wide range of weights, and with a focus on total quality, ACSA Steel Forgings SpA is already equipped for volume growth, as Industry Europe discovers when talking to Sabrina Colombo, one of the two partners leading the company. Barbara Rossi reports.
ACSA Steel Forgings was set up in 1935 by Mr Antonio Colombo, near the northern Italian town of Varese. Specifically its first site was in Solbiate Arno and this is reflected in the acronym naming the company: ACSA stands for Antonio Colombo Solbiate Arno, but the last two letters of the acronym can also mean ‘stampaggio a caldo’ (hot forging), thus describing the activity of the company. The company developed when the two sons of Mr Colombo, Rino and Evaldo, joined the operation. In the 1960s ACSA was already exporting to Germany and the USA, offering clients a fast service, thanks to the employment of staff based at local level. Today, the company is managed by the third generation of the founding family, in particular by Mr Colombo’s grandchildren, Arturo and Sabrina.
The company has moved its location, although it is still based in the Varese area (Oggiona Santo Stefano). Here it operates from a 250,000m2 site, which includes 50,000m2 of covered area. ACSA also has a production unit situated 15 km away, where it carries out thermal treatment of some of the forged components that it produces.
ACSA employs the latest technology, thanks to which it has an annual output capacity of 70,000 tons of high-quality hot steel forgings in carbon alloy, micro-alloy and stainless steels, among others, with a wide variety of weights ranging from 0.5 kg to 250 kg. Production starts with the design provided by the client, further supported and developed by the ACSA engineering department, which being equipped with upto-date technology (CAE), is able to support customers in the design phase, by means of forging simulation to optimise the forging process and the product. ACSA works in partnership with its customers, choosing the best materials and processes to use in order to optimise resistance, obtain homogeneous mechanical features, etc. The moulds necessary for the production of the required component are then manufactured. The needs of clients determine the development of new products, as ACSA customises its offer in order to fulfil their requirements, with 10 people dedicated
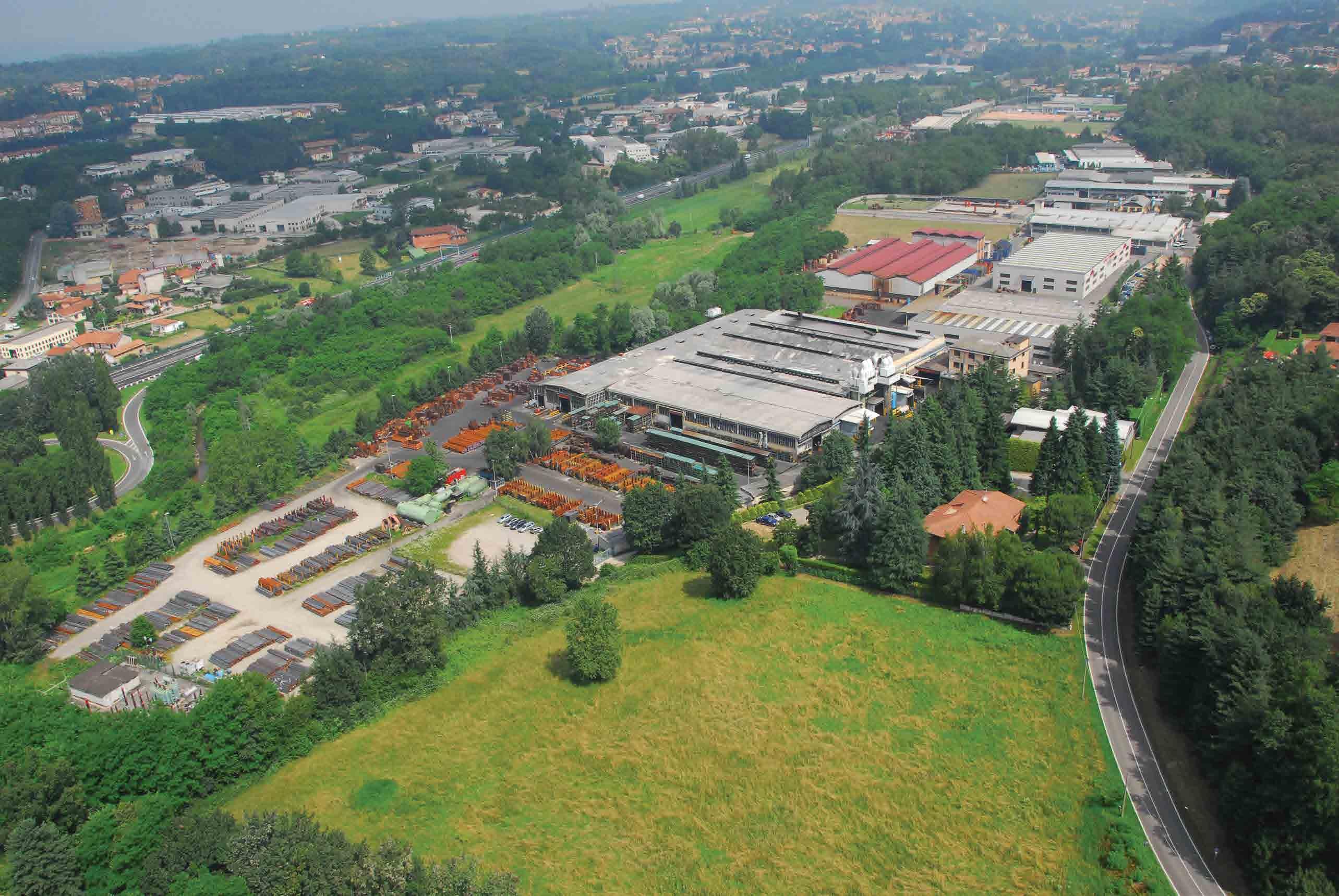
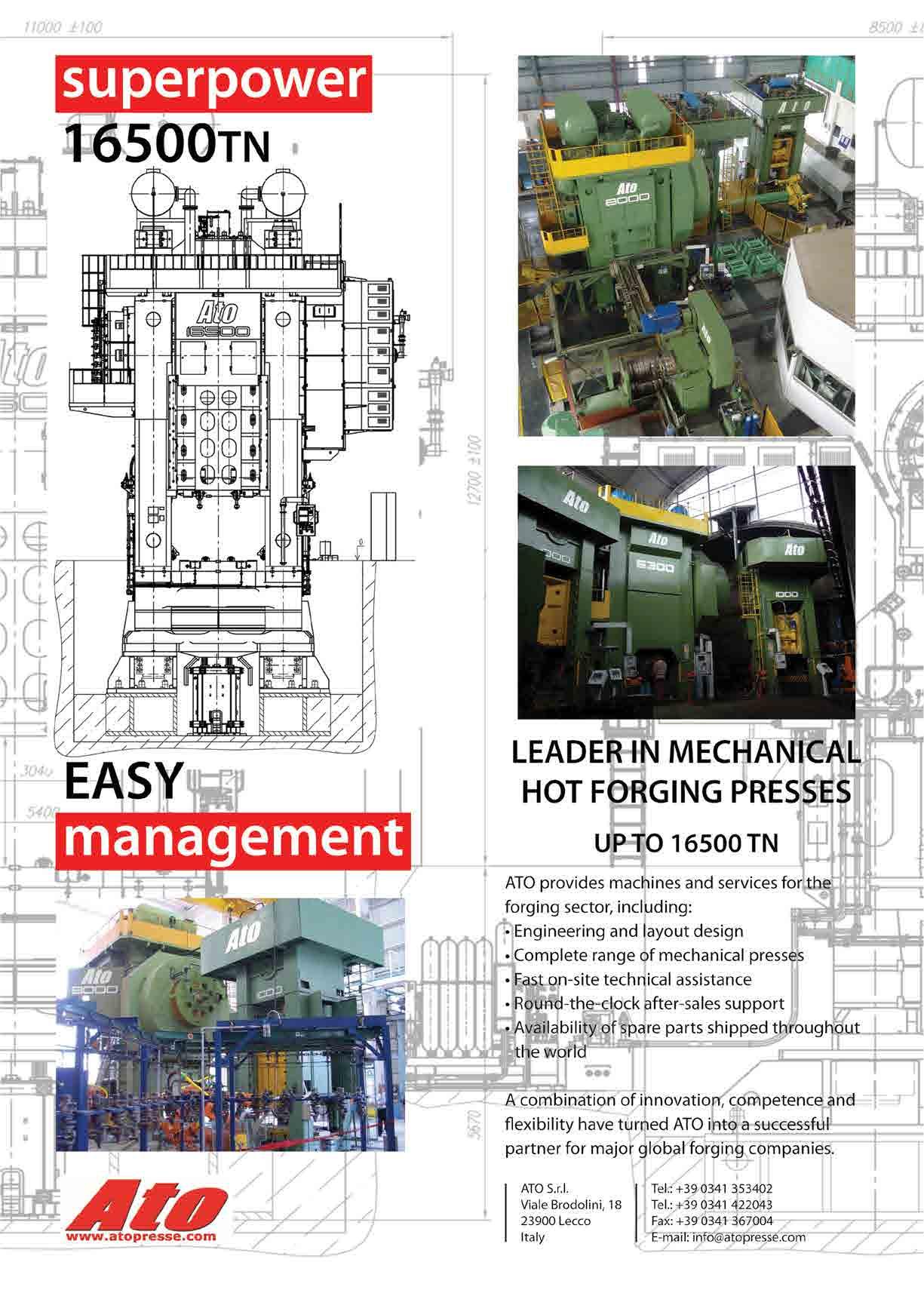
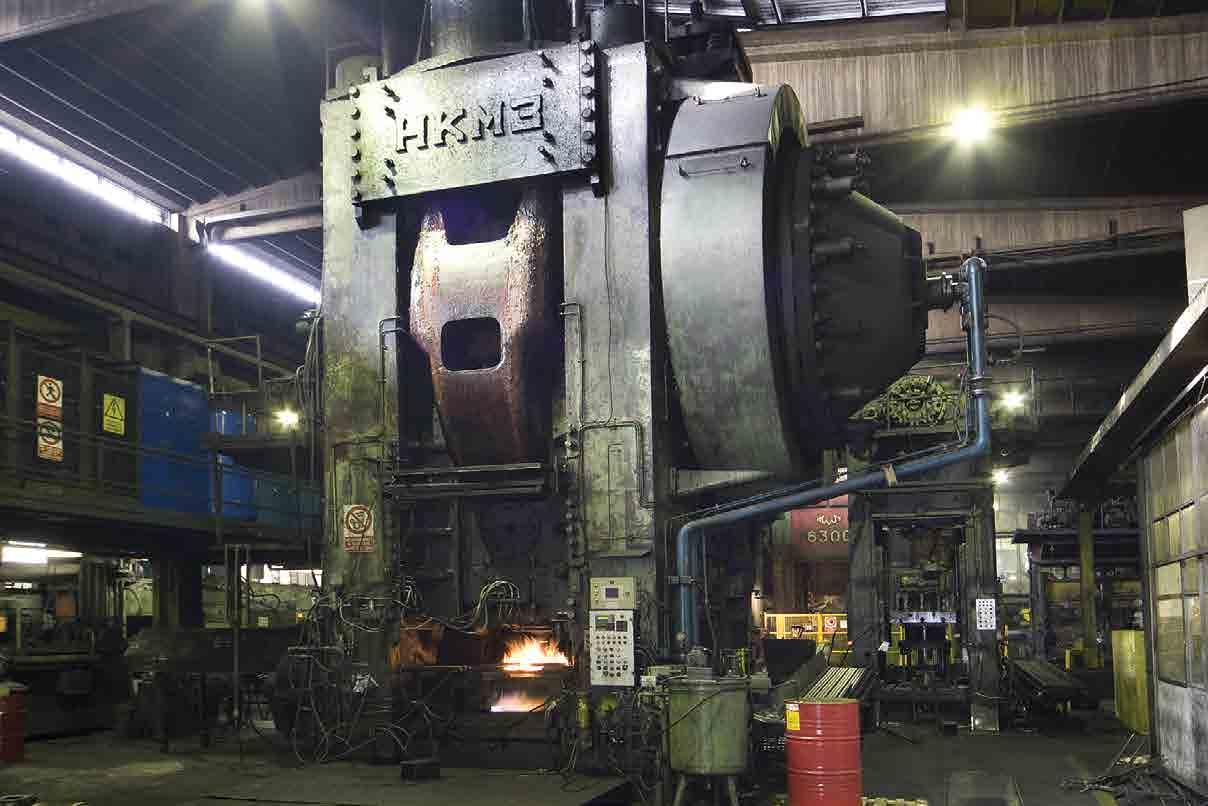
to R&D. ACSA also manufactures all the moulds and machinery that it needs for its production, thereby only depending on external suppliers in terms of the raw materials employed in its industrial processes. The result is a tooling department which is completely autonomous and equipped with the latest generation of CNC-machines fully controlled by CAD/CAM.
The range of products currently manufactured includes components for wind power and earth-moving equipment, cylinders and crankshafts for small planes, parts for pressure accumulators, crankshafts for motor vehicles and internal combustion engines, steering knuckles for truck and car axles, oil filters for industrial machinery, flywheels for the earth-moving sector and gears for agricultural machines and lorries; alongside these there are also parts for lorry transmissions, components for diesel, locomotive and marine engines, rod supports for diggers, adaptors for the energy sector, and camshafts, flywheels and rods for the textile industry.
Production is guaranteed by the fact that for each different production range there are at least two production lines available. ACSA has of 10 lines of presses of 1600, 2500, 4000 and 6300 tons; two hammer lines of 9000 and 25,000 kg; and three extrusion lines of 400, 1000 and 1250 tons.
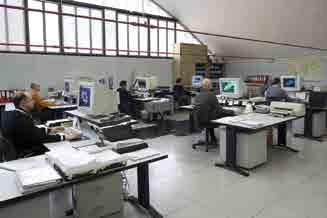
Total quality
ACSA has total quality control at each stage of the production process, constantly checking materials, suppliers, production (statistical controls) and shipment. A 3D optical scanner is employed to carry out further quality checks of the production phase. ACSA, which holds certifications such as ISO 9001, ISO/TS 16949, Lloyd’s and TUV, also has an internal laboratory which is ISO IEC 17025 certified. Tests carried out by this internal laboratory are microstructure and macrostructure checks, chemical analyses, impact, tensile and hardness tests and crack detection.
The sectors served by the company are commercial vehicles and automotive, petrochemical, railway and locomotives, aerospace, wind power, agriculture, earth-moving and industrial machinery. Ms Colombo explains, “We have no problems in exporting our production. Already 70 per cent of our output is for export, and we serve markets all over the world. Currently our main geographical markets are Europe, North America, Japan and South Africa, while the main market segment is the automotive industry (including lorries and motorcycles). Our size and organisation have developed over the years, but we have maintained the decision making speed of a familyled company, offering quick response times. We are able to support our clients in periods of production ramp-ups, often encountered in current markets, as we already have at least two production lines for every production range, meaning that we are equipped to accommodate sudden increases in production volumes. However, in order to further increase our production capacity, as well as to make thermal treatment more efficient and increase its output, we are planning to expand our production site in terms of covered area, so as to enter important new markets. Geographically we will focus our future growth on expanding our presence in North African markets, as well as in the Middle East and Gulf States, while in terms of market segments served we intend to extend our offer to products for the oil and gas sector.” n

