
4 minute read
Specialists in hydraulic valve blocks
SPECIALISTS IN
HYDRAULIC VALVE BLOCKS
Brinks Metaalbewerking BV is a technology leader in complex machining operations as well as in thermal deburring and cleaning. The company continues to expand and enter new markets thanks to its innovative production expertise and high-precision technology. Philip Yorke reports.
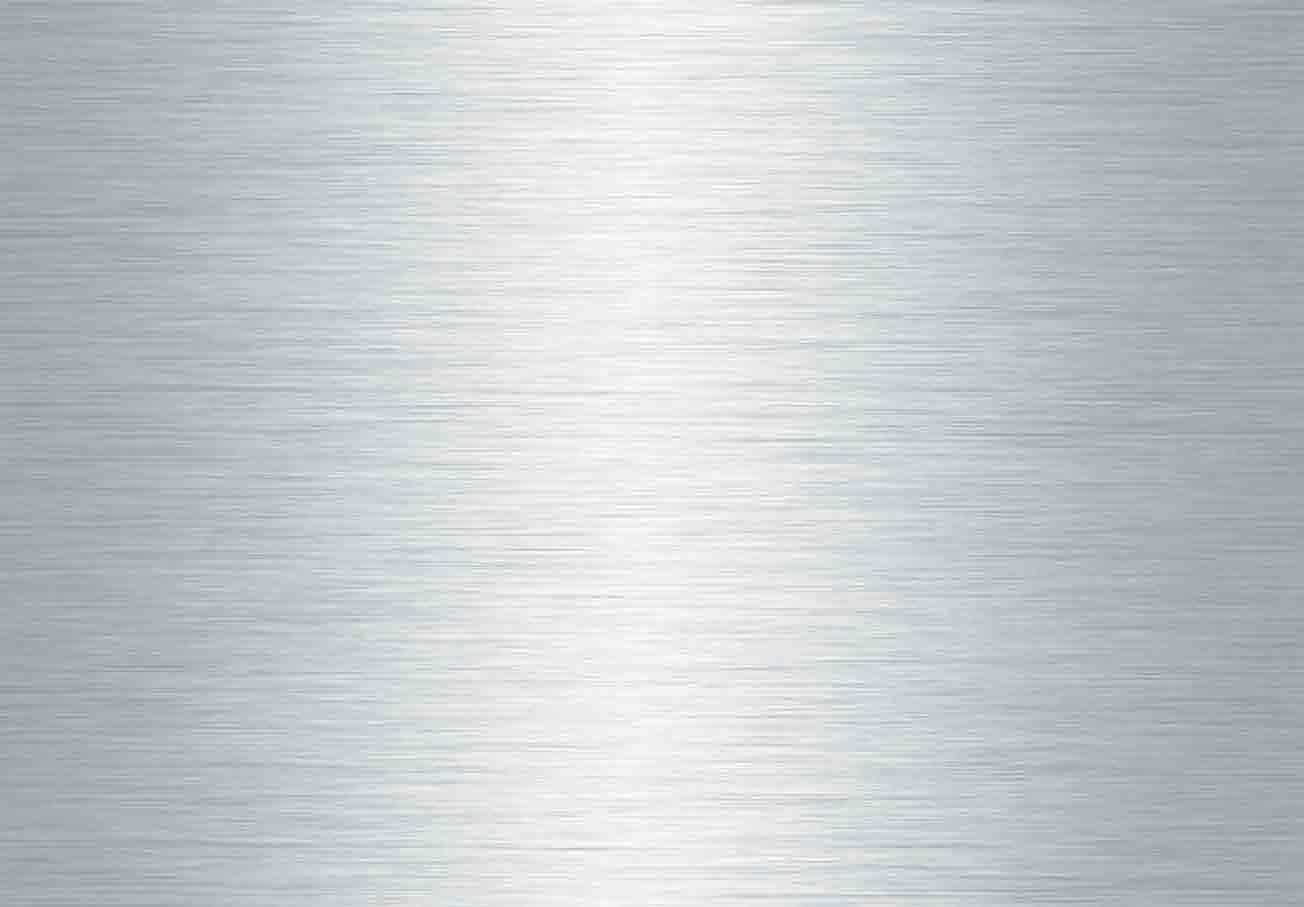
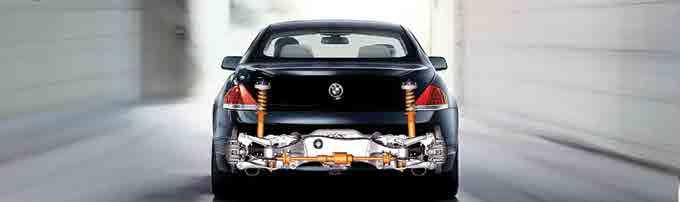
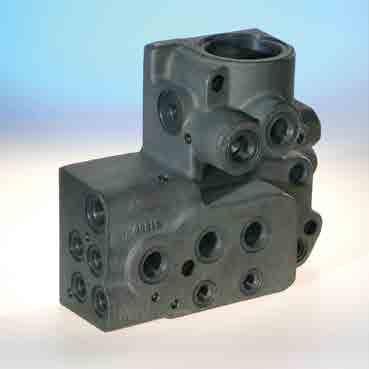
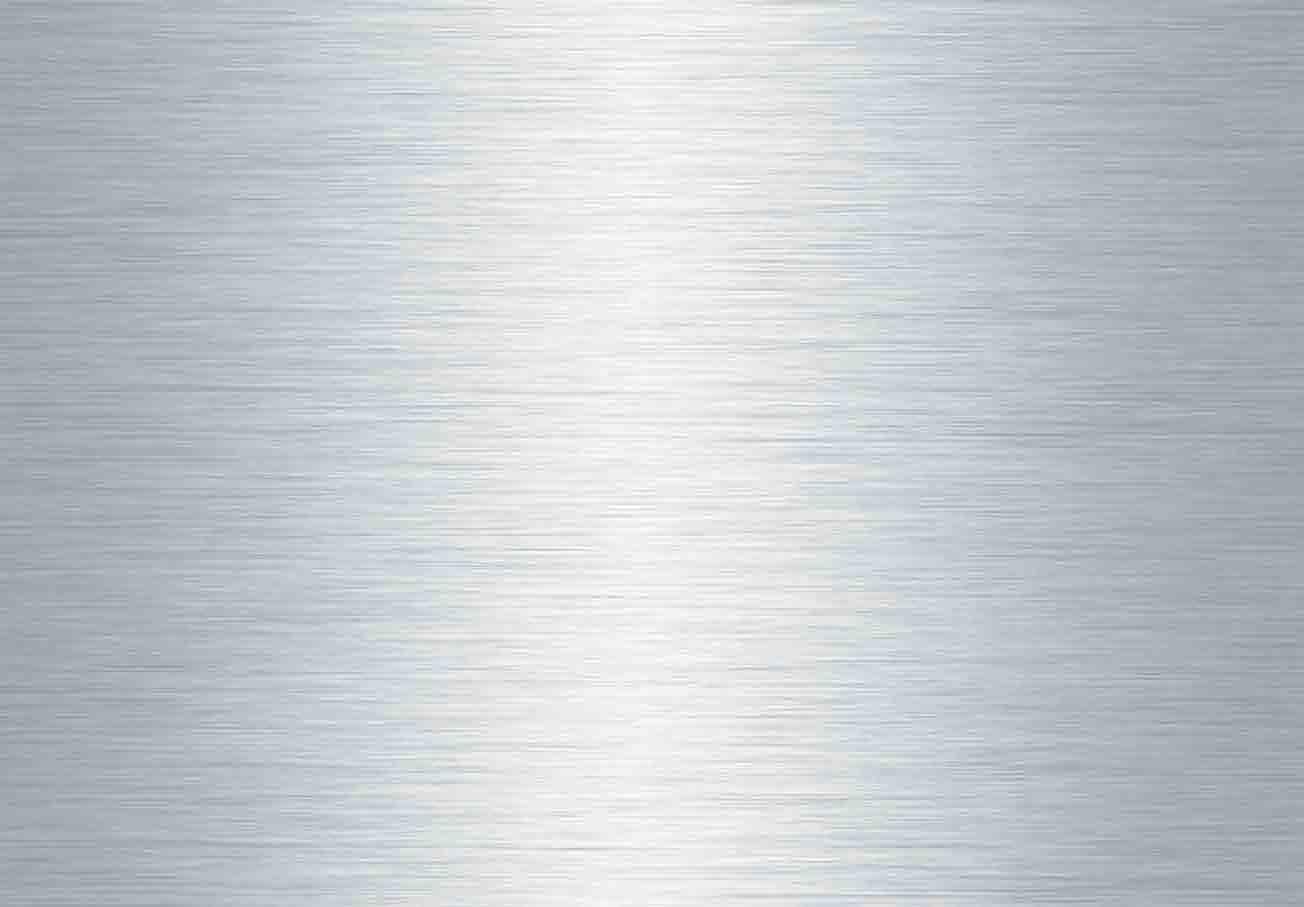


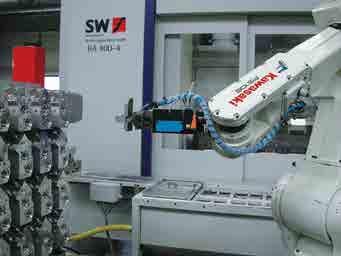
Brinks Metaalbewerking was founded in 1964. In 1983 the company was acquired by a young entrepreneur by the name of De Bruine who increased its product portfolio and broadened its range of customer services. Today, Brinks Metaalbewerking is one of Europe’s leading suppliers of hydraulic valve blocks and components which are produced to meet the needs of a diverse range of industries, from renewable energy and construction, to agriculture and automotive. Brinks Metaalbewerking specialises in drilling, milling, thermal deburring and cleaning, in serial batches that range from a few hundred pieces to more than two hundred thousand, with an individual weight limit of 40kgs.
Diverse high-quality processes
Brinks Metaal’s core business involves machining, deburring and the cleaning of hydraulic parts. The company has a comprehensive range of equipment and processes in house that enables it to meet any challenge and to guarantee the highest standards at all stages of production. It is able to supply its parts ready to be assembled. Brinks Metaalbewerking machines its components from cast iron or forged parts, aluminium profiles or aluminium forged parts and its customers include many of the world’s best-known hydraulics system manufacturers. The company’s hydraulic components are produced for use in a wide range of industrial applications, including trucks, agriculture, construction equipment and forklifts.
Another important sector for Brinks Metaalbewerking is the automotive market where the company is a supplier to manufacturers of convertible roof systems. It is a fact that most of convertible cars worldwide benefit from Brinks Metaal’s valve bodies, pump bodies and cylinder tubes, and its
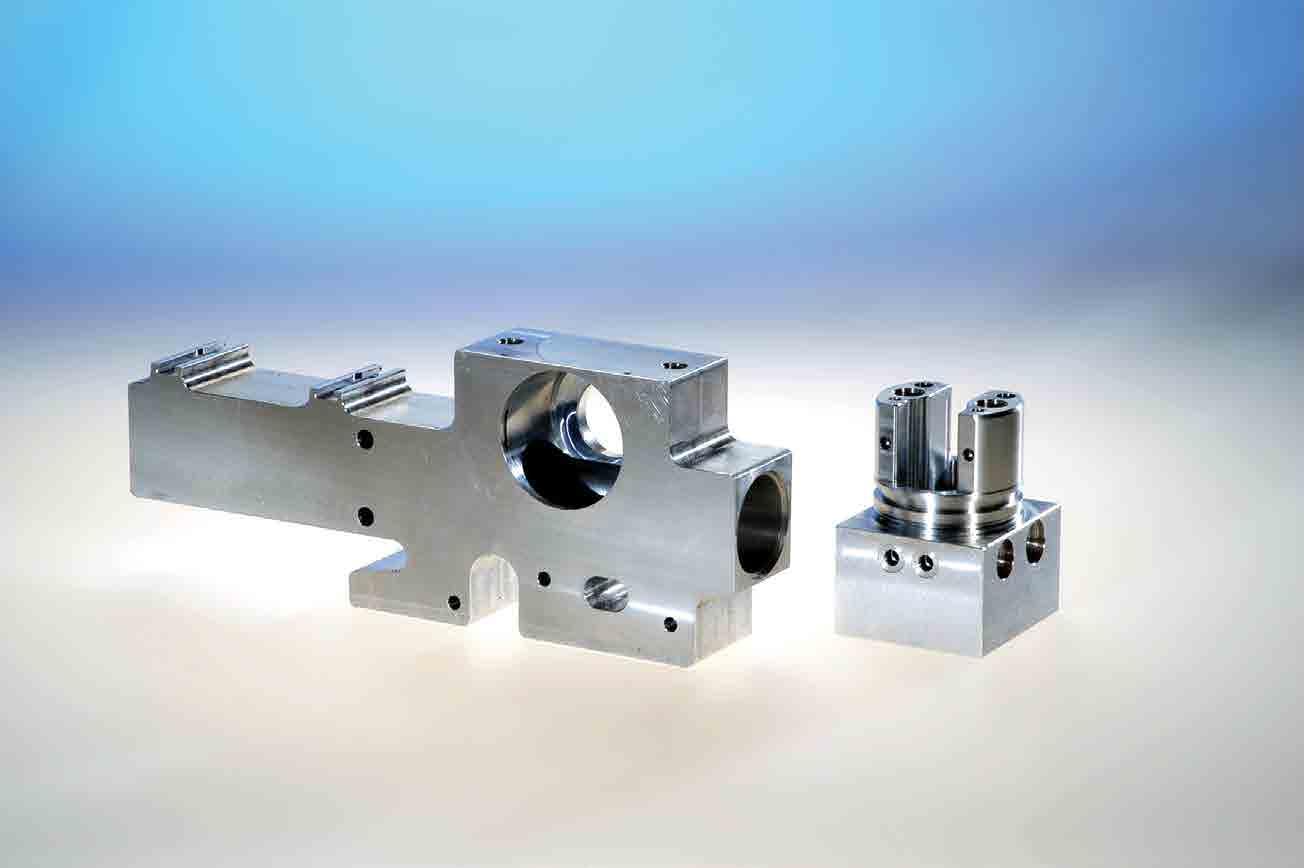
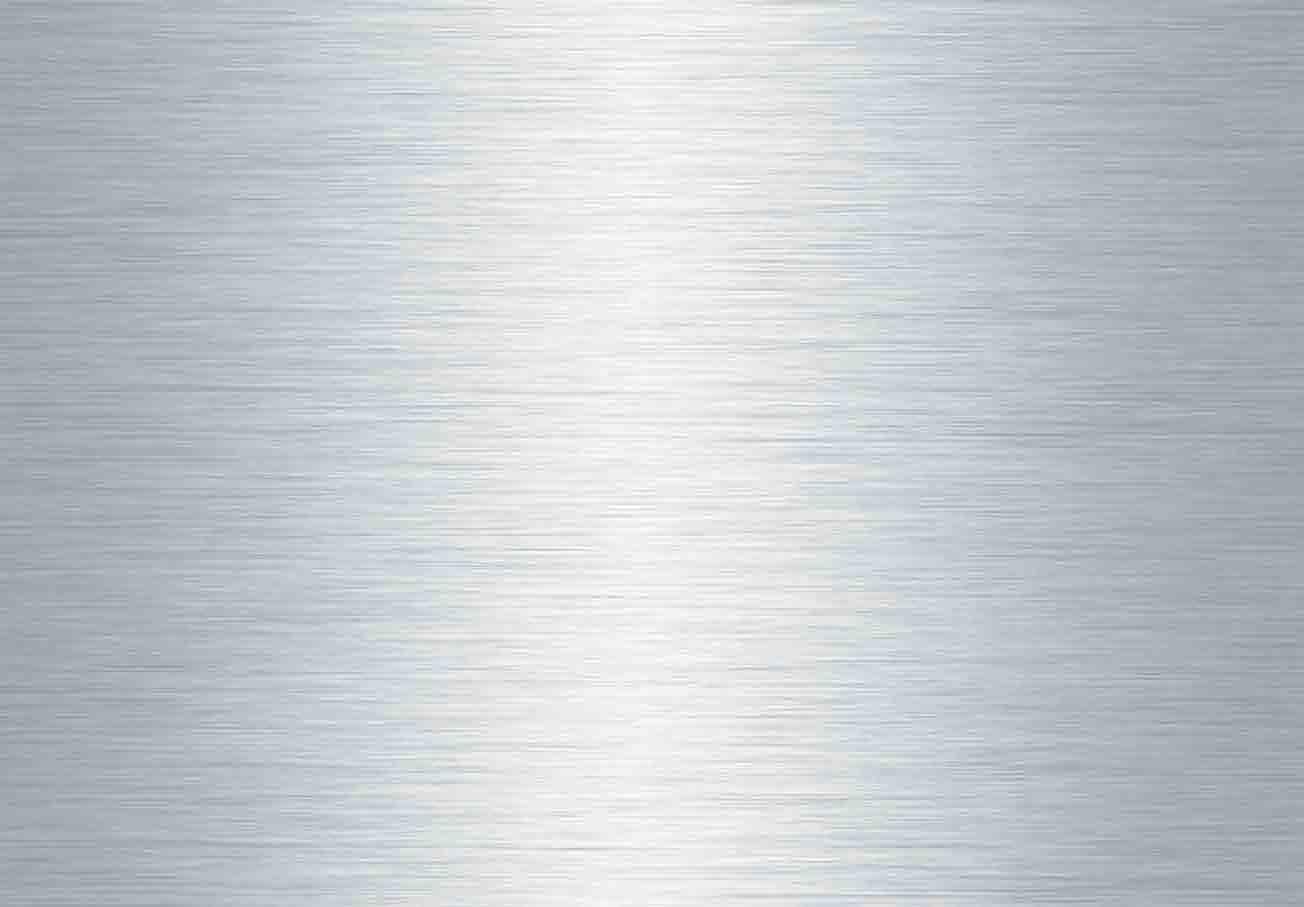
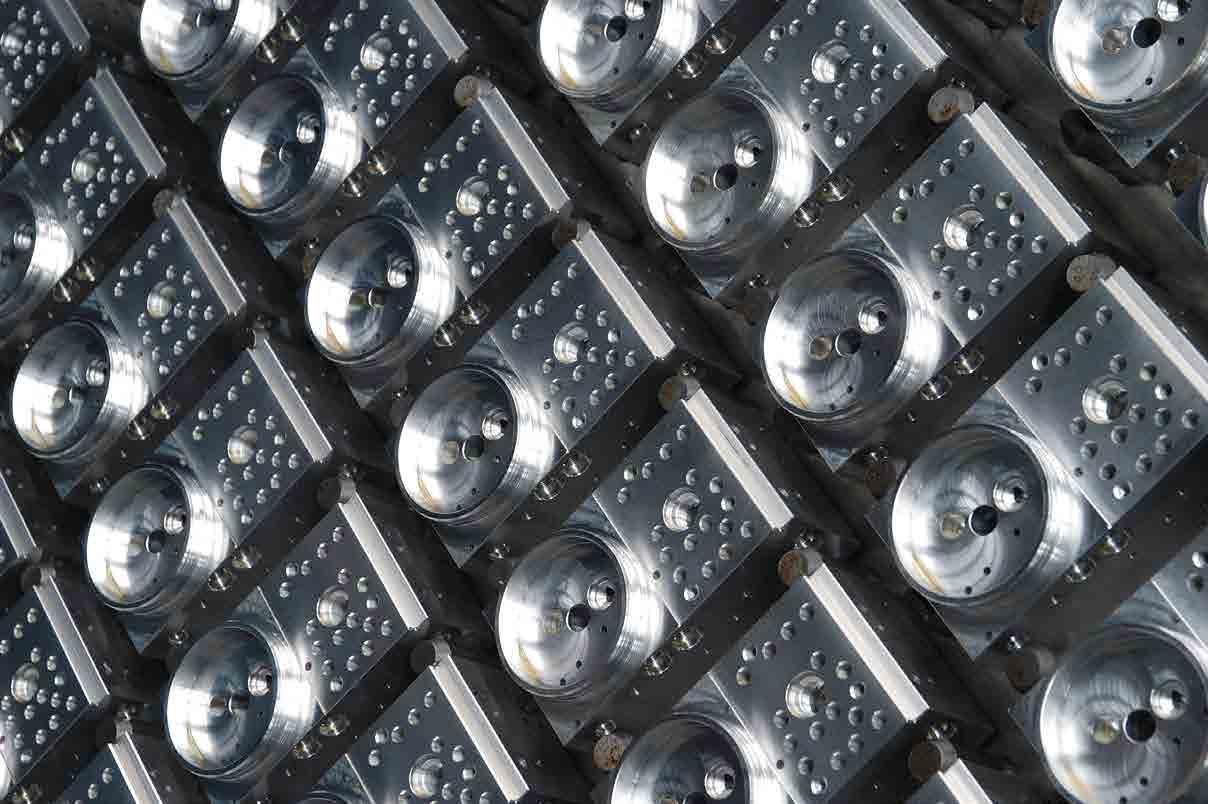
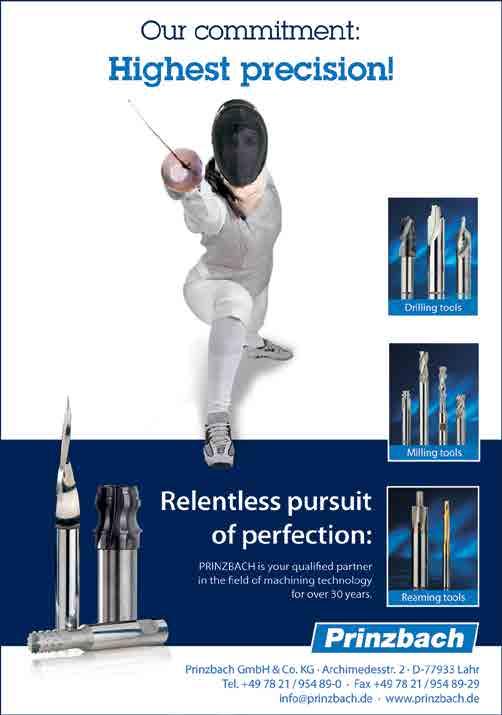
products are essential components in active suspension systems on vehicles such as the Porsche Panamera and BMW X-5.
During the last five years Brinks Metaalbewerking has made significant investments in new technology and robotised production lines. The company machines its products on single or multi-spindle machines which are fully automated for fast loading and unloading. For the deburring of parts it uses TEM thermal deburring, after which process, the parts are cleaned in cascade baths with ultrasound cleaning and then vacuum dried. Finally the products are inspected and packed in a clean room. This ensures that the parts leave the factory in the cleanest possible condition and ready to be assembled at the customer’s factory. Another high-tech deburring option is the use of high-pressure water jet deburring which involves pressures of 700–800 bar.
The company is able to manufacture and process complex hydraulic parts and can work with two or four spindles at a time; it operates 40 state-of-the-art machines at its modern plant in the Netherlands. In 2008, it made some major investments in a new building, a flexible manufacturing cell with two CNC-machines and a Palletech with 28 pallets, a high-speed linear two-spindle machine and the latest automated cleaning lines. The company is also focusing on attracting more business from the agricultural industry and already works with some of the most prestigious European manufacturers. Brinks Metaalbewerking also operates a final assembly department for companies that require a fully assembled product and is currently providing complete leveller systems for campervans where it is responsible for all the mechanics and the complete operating system.
Leaders in thermal deburring technology
Expertise gained over many years has made Brinks Metaalbewerking a technology leader in thermal deburring and many other metal cleansing processes. This special thermal process, which is known as ‘TEM’, guarantees the removal of burrs both internally and externally from the newly manufactured component. Burrs can be removed from components manufactured by metal removal machines, but also from injection moulded components.
The components to be deburred are placed in a pressure chamber and a mixture of oxygen and gas ignited and the heat it generates causes all burrs that are present to be burned off. TEM is the most efficient and practical technology for the deburring of a wide range of applications for hydraulic and pneumatic valve blocks, as well as for high-precision products. The deburring quality depends upon the size of the burr itself, and the type of material involved is an influencing factor and Brinks Metaalbewerking is committed to meeting the highest quality requirements of its customers. Therefore the company’s production processes are continuously evaluated, improved and upgraded.
Water jet deburring is another process conducted by Brinks Metaalbewerking that is ideal for larger components that won’t fit standard deburring equipment. This method is achieved by a CNC-machine with the workpiece on a turn table where very high water pressure is applied. These various processes can be tailored to clean and optimise any specific hydraulic component in any market sector and are particularly relevant to hydraulic pumps and motors. These are two areas that the company is currently targeting. n
For further information about Brinks Metaalbewerking’s cutting-edge products and services visit: www.brinksmetaal.nl