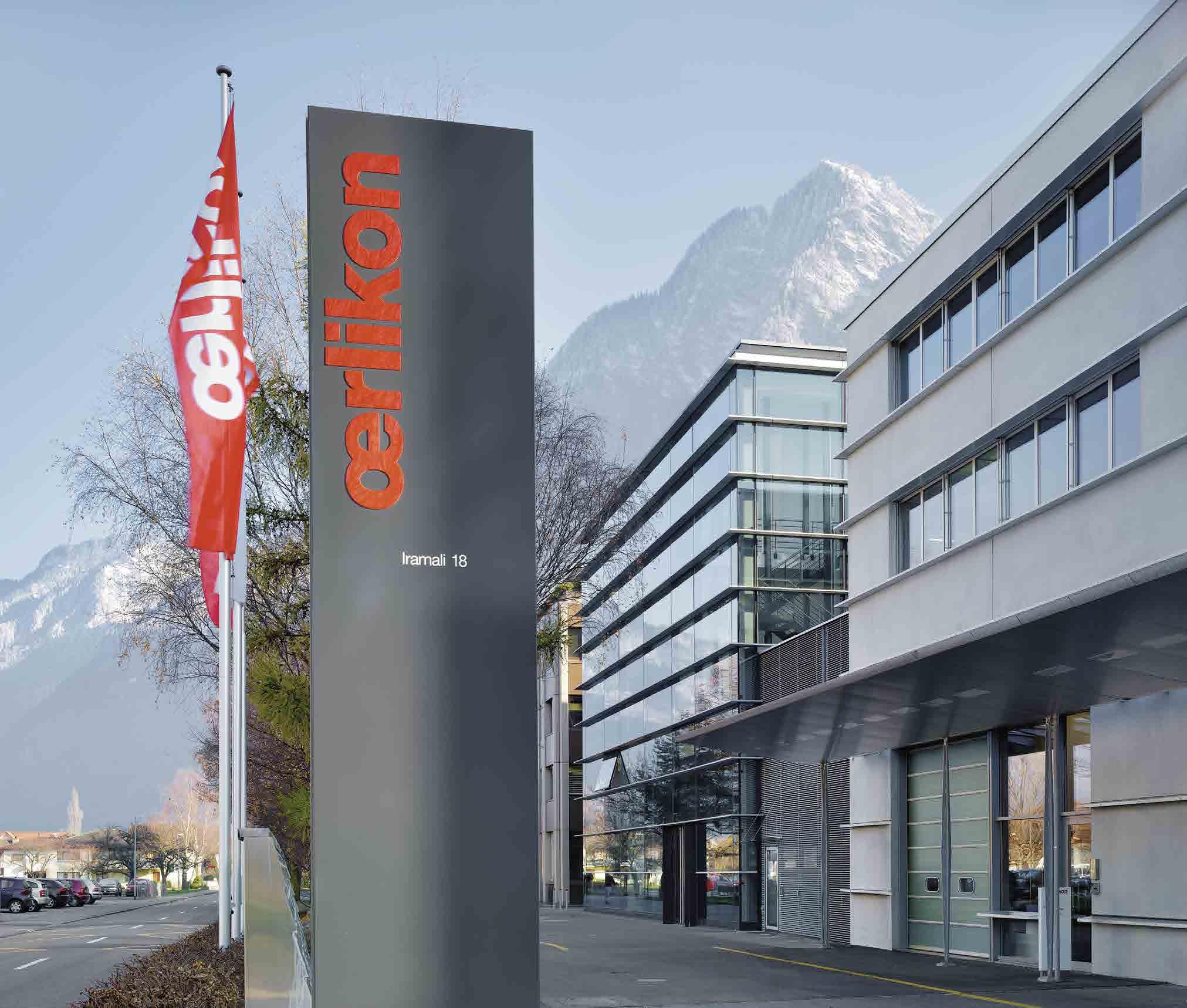
5 minute read
A pioneer in coatings Oerlikon Balzers
A PIONEER IN COATINGS
Oerlikon Balzers is the leading global provider of thin-film coatings to improve the performance and longevity of precision components and tools. Abigail Saltmarsh finds out more about its latest developments.
DR Roland Herb, the senior vice president and head of business line tools at Oerlikon Balzers, is in no doubt as to what keeps the leading global provider of thin-film coatings so successful: innovation.
The company, which is a segment of the Switzerland-based Oerlikon Group, develops and manufactures coatings that significantly improve the performance and longevity of precision components and tools.
“For us, innovation is a major pillar of any of our strategies,” he says. “Developing new technologies is essential for us if we wish to remain a leader and to ensure that we gain new markets.”
“Along with the other keystones of our business model – to ensure we have customer proximity, a good global footprint and a presence in a wide range of industries – this is an important driver for us for the future.”
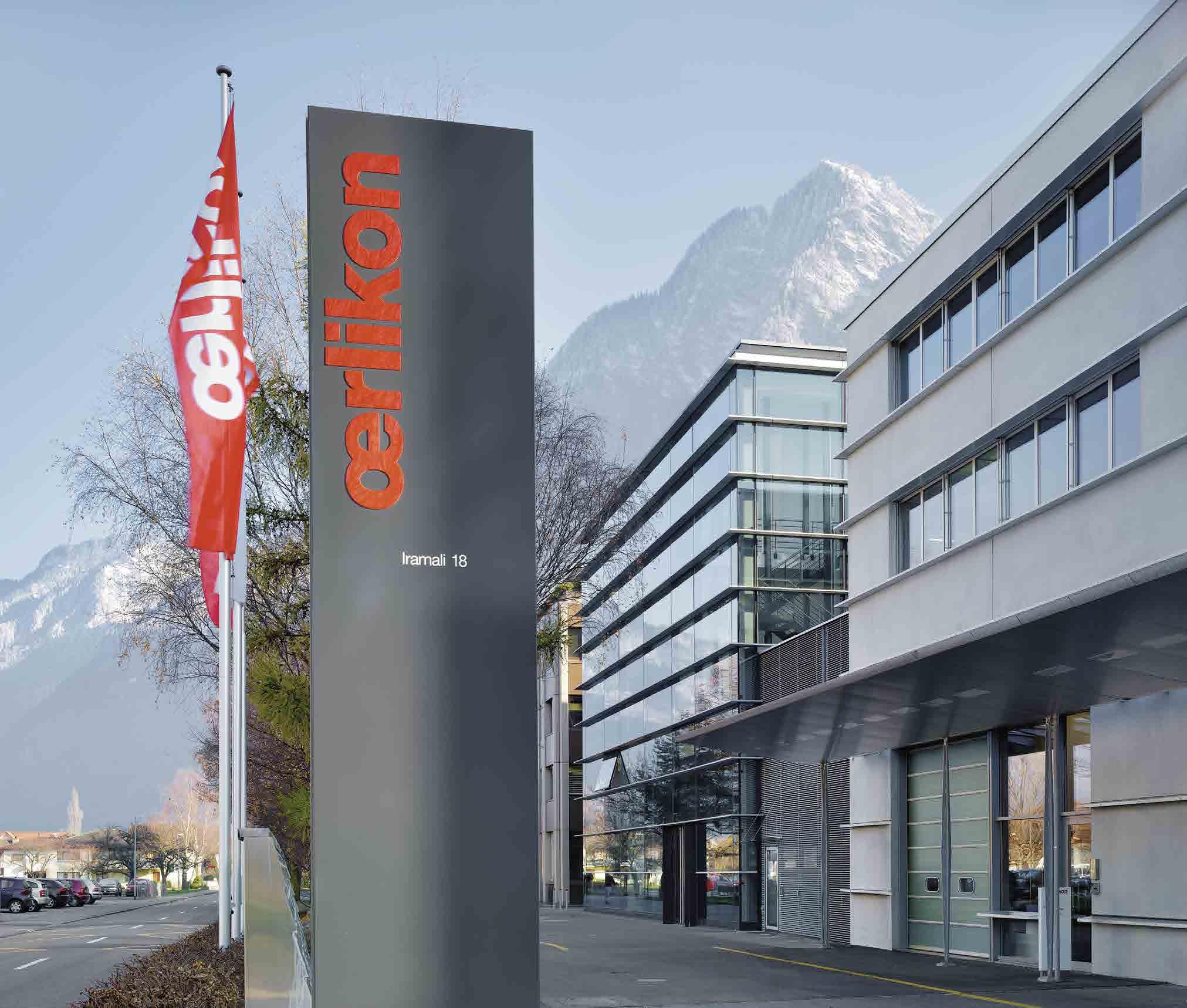
An expanding footprint
Oerlikon Balzers’ coatings, marketed under the Balinit® brand name, are extremely thin and exceptionally hard. They significantly reduce friction and wear.
The company also develops processes, manufactures and sells systems and production facilities, and offers contract coating services through a dynamically growing network. Under the technology brand ePD™, it develops integrated services and solutions for the metallisation of plastic parts with chrome effects.
“We have 91 coating centres in 33 countries across Europe, the Americas and Asia – and this footprint is constantly expanding. Last year saw expansion in Malaysia, India and China, and our plan now is to continue expansion in new countries in South East Asia and eastern Europe, as well as expanding capacity and strengthening our footprint in places such as Turkey and the USA.”
Diverse applications
The company’s solutions are used in a broad range of applications in the automotive and machine industry, in food and packaging, medical technology and increasingly in aerospace. Leading tool manufacturers and automobile manufacturers are among Oerlikon Balzers’ customers. “We have over 20,000 customers around the world and process more than 200 million precision tools and components every year – these range from items as small as watch pins up to dies for entire car bodies,” says Dr Herb.
The largest area of application for physical vapour deposition (PVD) hard material coatings is precision tools for metal cutting (drills and cutters), forming tools, plastics processing and metal die casting as well as low friction coatings for automotive applications. A relatively new but rapidly growing area of focus is the coating of precision components in order to reduce friction and improve durability.
Other industries in which PVD hard material coatings are used include general machinery industries, the aircraft industry, motor racing and the medical and hygiene technology industry. PVD coatings are also being increasingly used in the luxury goods industry (watches, cell phones) – for aesthetics and practicality.
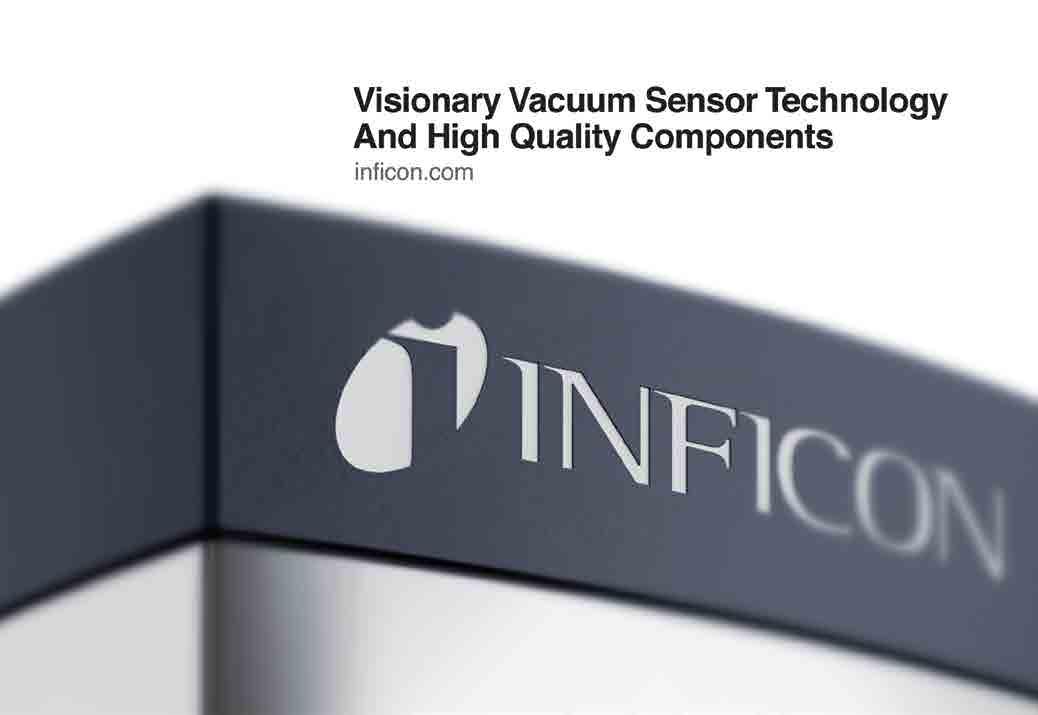



New technologies
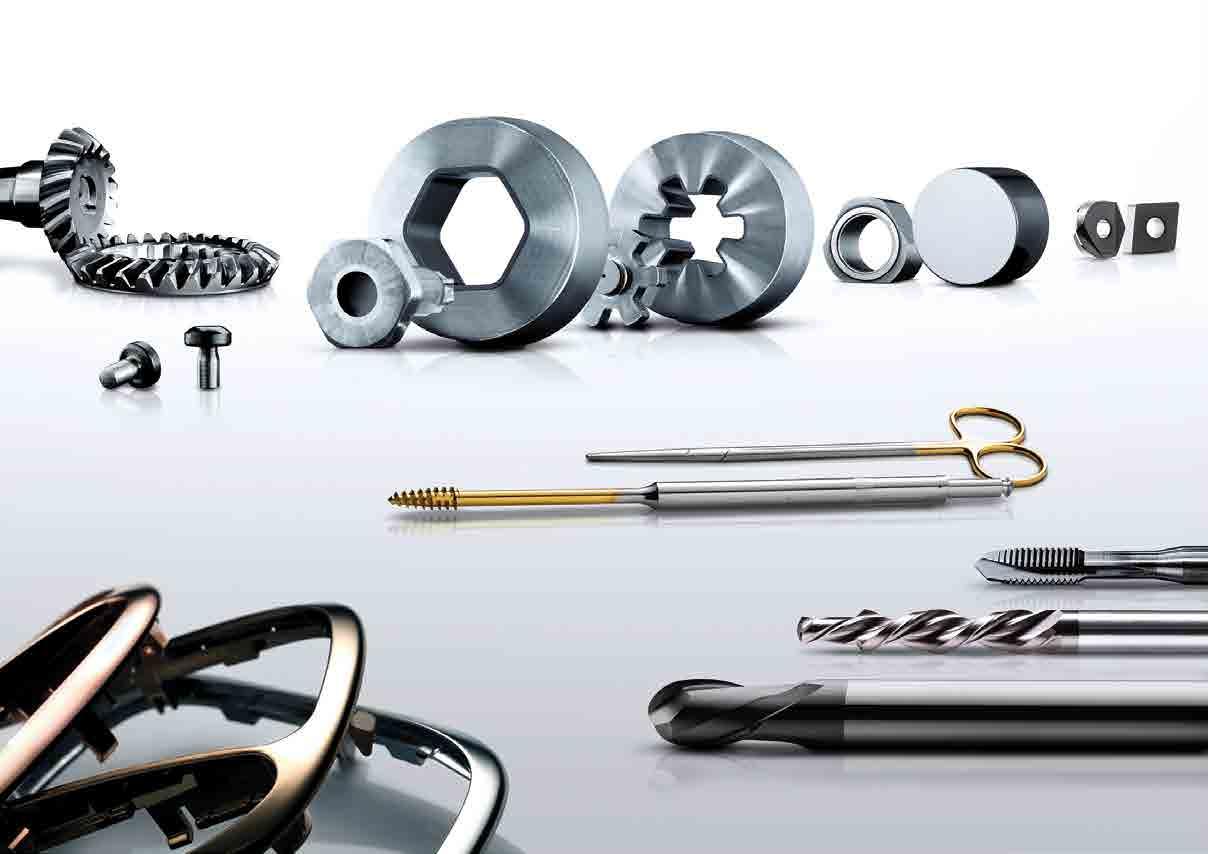
One major area of focus at the moment for Oerlikon Balzers is the industrialisation of S3p™ and ePD™ technologies. Both were launched in 2011 and are now set to propel the company into further growth.
S3p™ – also referred to as ‘scalable pulsed power plasma’ – enables extremely smooth yet dense and hard coatings to be manufactured reliably and efficiently for the first time. The application potential for this technology is wide-ranging in a large number of fields.
“Dense, hard and highly adhesive coatings, with a controlled microstructure, are extremely important for the coating of tools in order to increase productivity. For many years physical vapour deposition (PVD) – using arc evaporation technology – has proven able to deliver these properties, and for a decade researchers tried to combine this technology with the sputtering process to achieve extremely smooth surfaces,” explains Dr Franz, the regional executive manager for Europe of Oerlikon Balzers.
“Oerlikon Balzers has managed to overcome all of the limitations of the previous approaches and expanded the parameter range in several dimensions independently of one another. The technology is protected by multiple patent applications and is now ready for production.”
Greener options
Following a pilot in Germany, the first ePD™ (embedded PVD for design parts) technology centre in the world was opened at the Suzhou location, China. In contrast to traditional procedures, the low-emissions, eco-friendly ePD™ technology for the metallisation of plastic parts does not use any environmentally damaging materials, such as chromium VI.
“ePD™ offers innovative functional features, such as radar-transparent metallisation for distance sensor systems, lightweight construction and a greater variety of design possibilities. Testing by major car manufacturers is underway and certification for use in high-volume production is expected during 2013,” says Dr Franz.
“We will continue to focus on innovation as we grow and, of course, our future strategies will increasingly involve environmental concerns. ePD™ is eco-friendly and as we grow our technologies, then products and solutions will become greener,” he says.
Continued growth
Looking ahead, he says the company expects to see organic growth across all the industries in which it is involved but the medical and aerospace industries are likely to be particularly interesting. In France, it has recently opened a centre of competences, with a focus on aerospace applications.
As the company grows, it will also continue to pursue its strategy of following its customers and the developing markets.
“Our aim is to further strengthen our position as a leader, bringing new solutions in metallic and plastic-related applications and to develop our geographical footprint around the world,” says Dr Herb. “We plan to strengthen our existing markets through further innovation and outstanding services.” n
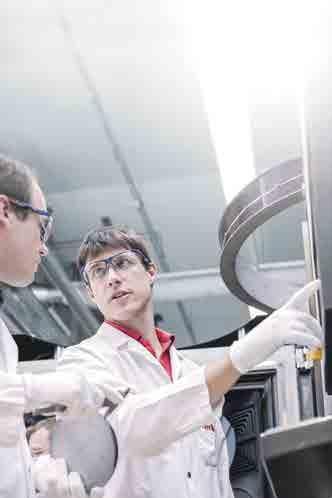
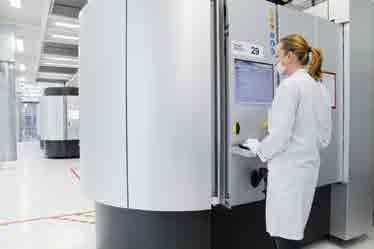
