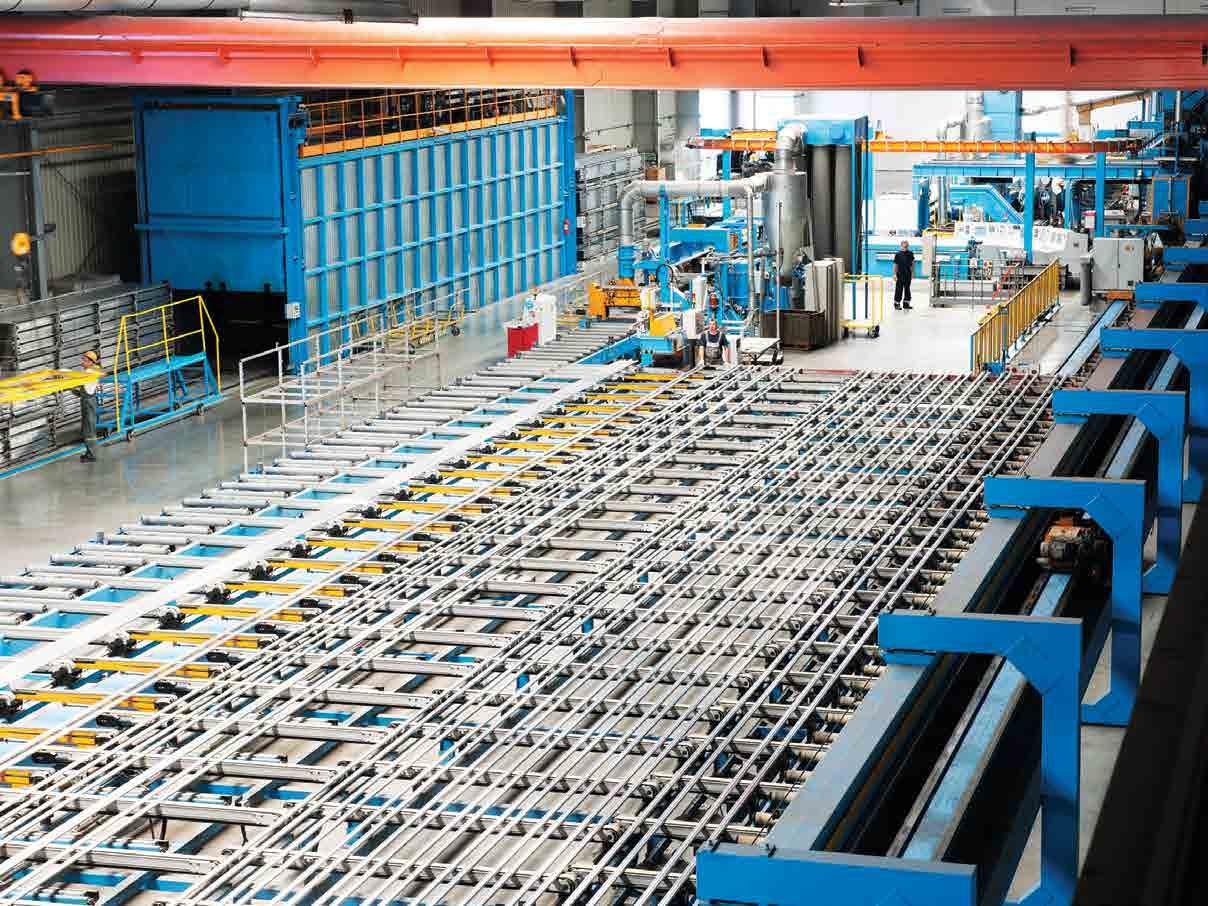
7 minute read
Technology and art in steel structures Cimolai
and AkzoNobel (Sweden). To this end, a new coil coating facility has just been started up in Minsk with technical support from BASF. It is primarily designed to coat aluminium for the production of roller shutter slats and boses, but there are also plans to coat steel coils for other applications in the future.
New products for demanding applications
“At the moment, the most complex and promising products are aluminium profile systems for facades, windows, doors and office partitions. Our range of solutions based on aluminium profile systems can bring to life practically any project.” marketing director Mr Rybakov explains.
“Our systems are in demand for a range of high-rise buildings. A construction mounted on a building 100–150 m high is extremely complex and requires a high level of calculations in thermal physics, wind- and fire- resistance and seismic stability. We are proud that the share of complex façade and interior systems today makes up 80 per cent of the whole extruded profile production.”
ALUTECH complies with market trends and energy saving: in 2010 a window frame system with better heat engineering ALT W72 was introduced, in 2011 came a new energy effective filling in the façade system ALT F50 and new options were offered for “Aquaparks”, and in 2012 an actuator access for smoke removal with a gear over 1.0 (m2°C)/Vt) was brought to market. This year sees the launch of the new structured glazing ALT F50 SG with double-chamber glass units and an integrated window of the “hidden flap” type with better heat engineering features of ALT EF65. “The level of technological processes realised at our enterprises dictates also the choice of suppliers.” Mr Mr Rybakov adds. “When producing roller shutter systems we use raw materials from leading European companies. For the production of profile systems we use aluminium from the worldwide-known company RUSAL.”
Trade Fairs
ALUTECH is a regular exhibitor at the biggest specialised exhibitions in the CIS countries such as BUILDEX (Moscow) (St-Petersburg), SibBUILD (Novosibirsk), YugBUILD (Krasnodar), MosBuild (Moscow) and others.
“Last year we took part in the biggest in western Europe specialised exhibition R+T (Germany, Stuttgart), and in 2013 we will present our products at GlassBuildAmerica in Atlanta, USA. Also we plan to take part in the biggest Middle East construction exhibition Big Five which will take place in the UAE. We have also preparing for the German R+T in 2015 with a total stand area of about 1000m2.”
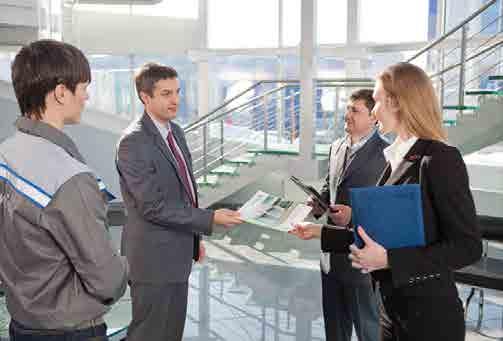
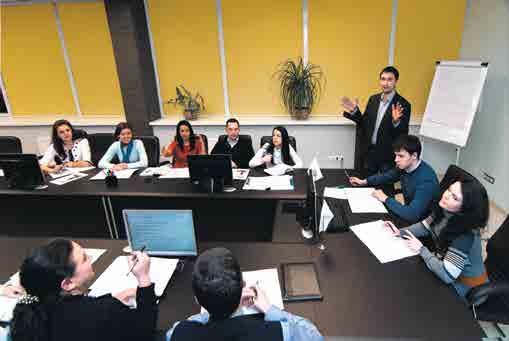

“We have many goals to achieve in the near future.” Mr Mr Rybakov says. “Right now we are completing the second line of the extrusion plant AluminTechno, and the manufacturing facility for door accessories - with a floorspace of 50 000m². This will bring capacity up to 220–240 000 doors per year, which would make us the leader in European door production within three to four years.”
Alongside dynamic development, entering new markets and broadening production and supply geography, the group knows that personal relationships are extremely important in business. The major principle: “ALUTECH is the ethics of system business, esthetics of system quality” was formulated and remains a motto of the whole group of companies; it is reflected in areas such as environment protection, product release, relationships with partners, personnel policy and charity works. n
Josef Timmer Handels. u. Bet. GmbH www.joseftimmer.de
The specialists when it comes to safety brakes for roller shutters, garage doors and industrial doors.
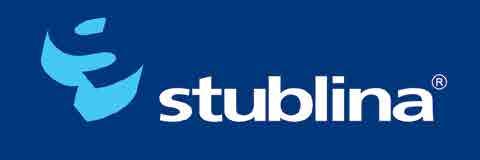
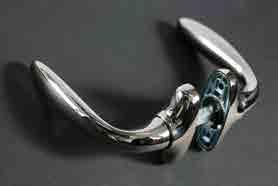
Private company “Stublina” D.O.O was founded in 1993. Due to the recognizable design and product quality, we have become the market leader in the Balkans in production of hardware for aluminum joinery. “Stublina” produces a large series of handles for windows, door handles, hinges for windows and doors, locks, latches, turn and tilt mechanism and lock cylinders. Today, the company “Stublina” employs 200 workers.
Stublina d.o.o. T: +381 34 6707 160 | E: office@stublina.com www.stublina.com
Cimolai has come a long way since its beginnings in 1949, when it was set up in Pordenone, north-eastern Italy, by Armando Cimolai and his wife Albina. Currently the Cimolai Group is one of the most advanced companies in the metal construction sector, active on both the Italian and foreign markets. Barbara Rossi reports.
TECHNOLOGY AND ART IN STEEL STRUCTURES

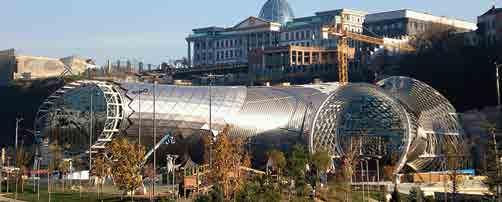

AT the beginning, the company manufactured steel gates and fixtures but soon the range of activity expanded to the making of frames for industrial buildings (for Zanussi in particular, as both companies were located in the same town) and projects for public bodies. It has to be noted that the company’s activity was not limited to manufacturing, but also included design and installation, a factor which gave it a definite advantage over its competitors, allowing it to grow and take on engineering challenges, including the manufacturing of custom-designed blast-proof enclosures for military air bases. In the 1970s, the second generation of the family, the founding couple’s two sons, Luigi and Roberto, entered the business and the company made a further leap, also favoured by the expansion of the national infrastructure market. Cimolai quickly adapted to market needs and was able to construct the larger structures demanded, such as aircraft shelters, bridges and stadiums, working both in Italy and abroad. Examples of these projects include the Grand Canal Maritime at Le Havre, the Second Severn Crossing in Bristol, the Olympic Stadium in Athens and the 95,000 capacity football stadium in Johannesburg built for the 2010 World Cup. Over the years,
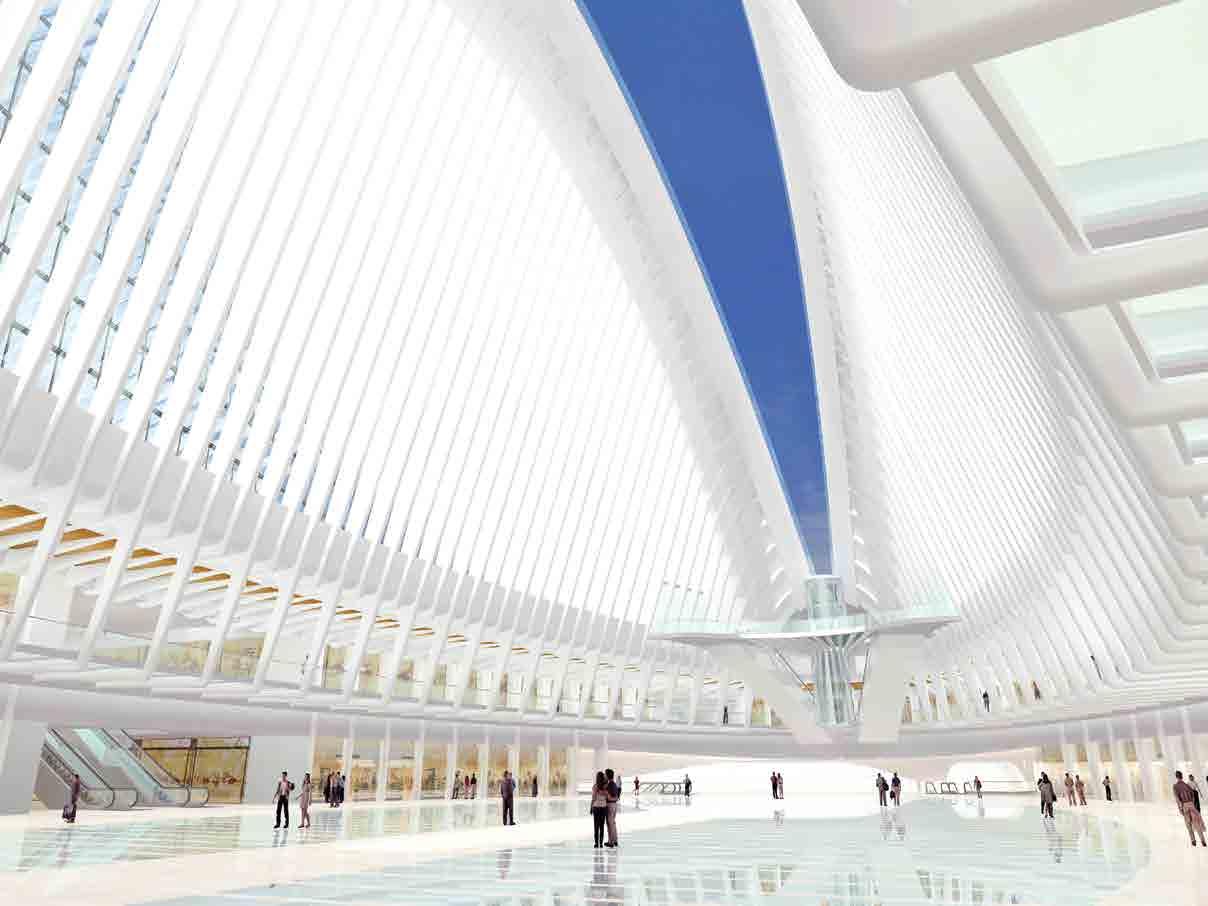
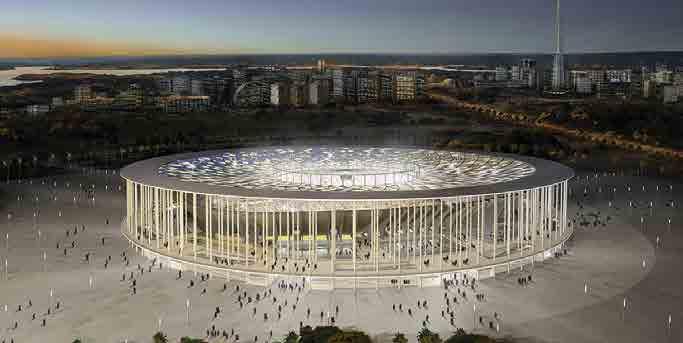
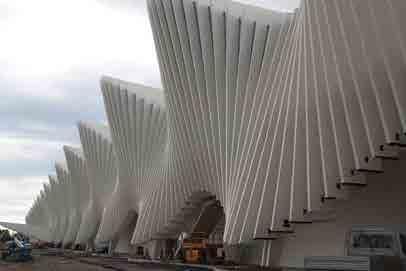
due to its expansion, which increasingly happened outside Italy and which also involved the making of ship hulls, the company built several new manufacturing units (on average one every ten years), one of which was constructed on the banks of the Aussa Corno river and equipped with a mooring quay for ocean going vessels, a facility that enabled structures to be shipped directly from the plant to global customers.
In recent years the ownership of the company passed to Luigi and Roberto, respectively owners of Cimolai SpA and Cimolai Technology, while Cimolai Centro Servizi Srl has remained in the hands of Armando and Albina. Cimolai Technology specialises in the manufacture and supply of machines for lifting and transportation operations, and Cimolai Centro Servizi Srl in the fabrication of steelwork structures and heavy steel construction works for civil and industrial buildings, as well as in making welded beams for the naval and off-shore industry.
Despite this re-organisation in terms of ownership, the group remains united, to be able to serve and expand its presence on its different markets. Since 2007, Cimolai has had a manufacturing facility in Venezuela helping it to grow into the South American market. The same year also saw the entrance in the company of the third generation of the family. This was followed by the acquisition of Fabris Srl, a company specialised in mechanics, in 2011 and of Zwahlen & Mayr SA, a Swiss firm belonging to the metal carpentry sector, in 2012. Alongside this, Cimolai has acquired new 253,000m2 production facilities in Monfalcone (north eastern Italy). Current operations
Presently the Cimolai Group specialises in the construction of bridges, viaducts, stadiums, residential and industrial buildings, military infrastructure, normal and special plate girders for the off-shore and shipbuilding industries, stainless steel bulkheads for chemical tankers, polygonal and cylindrical poles for telecommunication and power lines, pipes of great diameter and wall thickness, and ship hulls. It operates from seven plants and workshops based in north-eastern Italy, as well as from its Venezuelan facility. In addition to this, the group can also avail itself of the facilities of its recently acquired companies (Fabris and Zwahlen & Mayr SA) and of those of Cimolai Technology and Cimolai Centro Servizi Srl. Highly automated machinery is employed