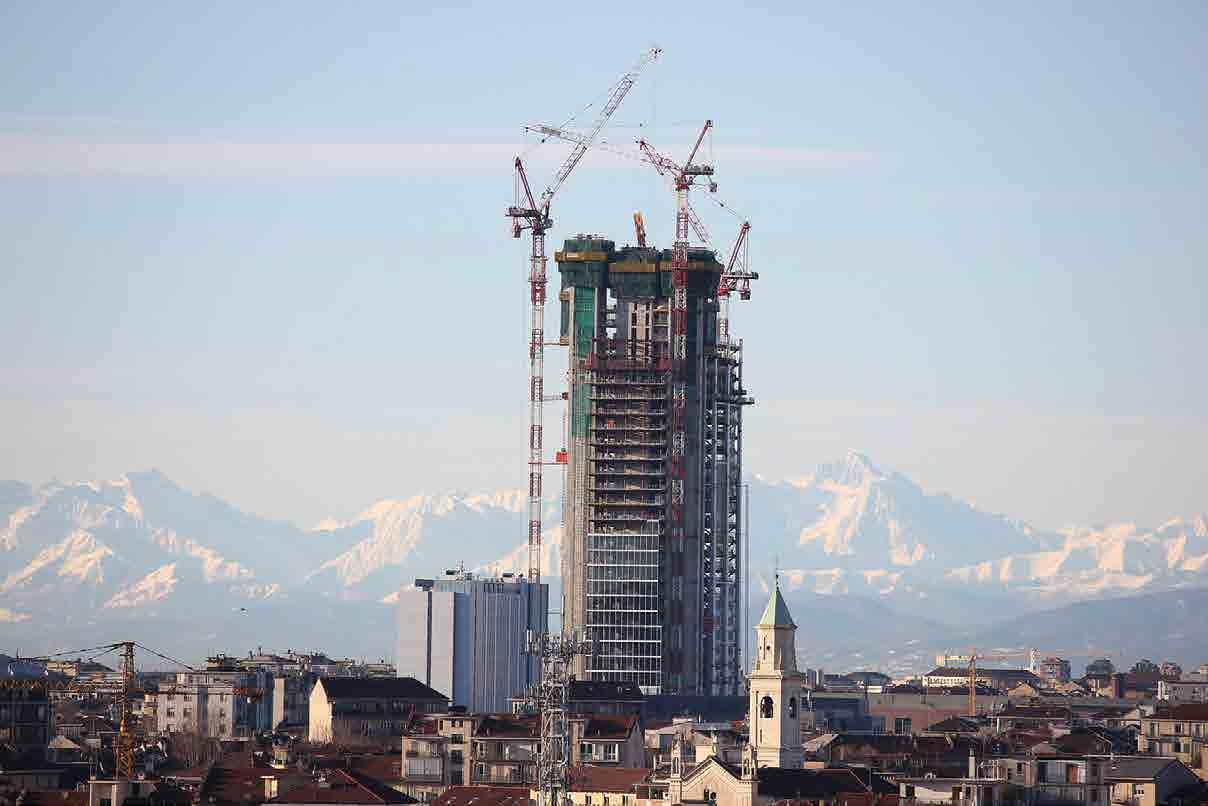
5 minute read
Building for a sustainable future KLH Massivholz
in all plants, as well as skilled and qualified technicians and labourers. Quality control is performed by in-house qualified personnel, test equipment (NDT) and testing laboratories, and a wide range of certifications are held by the company, including the UNI EN ISO 9001: 2000 for design, fabrication and erection of steel structures. Over the years, Cimolai has received strong recognition for its work, having won ECCS (European Convention for Constructional Steelworks) awards for several of its projects.
In 2012, it achieved production of about 120,000 tonnes of steel and a turnover of about €30 million, as well as making important investments (1.5 per cent of turnover is regularly invested in research). The company’s strengths are its competitiveness, quality and time performance, alongside the previously mentioned commitment to research, which keeps it in the vanguard in terms of design and engineering and enables it to offer the best customised solution for each project that it undertakes.
A wide range of impressive projects
The group has recently completed or is currently involved in several important projects: the Reggio Emilia railway station, the third set of gates for the Panama Channel, the Intesa San Paolo tower, the New Safe Confinement (Chernobyl), the World Trade Center Hub, the Sluice Gates of Mose in Venice, the 140m Crati bridge in Cosenza, the 4160m Third Orinoco River Crossing, four viaducts in Algeria, the Auditorium in Tbilisi, the Brasilia Stadium and the Bordeaux Bridge, among others.
These are challenging and cutting edge projects. For instance, the Bordeaux vertical lift bridge was built over the 400m wide Garonne river and was designed to unite the two parts of the city and to stimulate urban development on its eastern bank, while at the same time not affecting the harbour facilities located in the city centre and not impeding access to large ships during and after construction. The Reggio Emilia station, designed by Santiago Calatrava, is at about thirty metres from the A1 motorway, and its wave-like external design is such as to maximise the viewpoint of passing car drivers. Because of the area in which it is located, this high-speed railway station has a potential of about two million users. With regard to the Panama channel Cimolai is involved in a $400 million project for the design, manufacturing and transport of sixteen gates for the new channel under construction, which when completed in 2014 will allow the passage between the Atlantic and the Pacific oceans of extremely large ships, which can not use the old channel. Cimolai is also going to be involved in the wreck removal of the Costa Concordia ship, which sank off the coast of the island of Giglio in January 2012. Cimolai is going to provide four megaplatforms and 20 steel beams to be used for the large structure which will be put in place for righting the ship. Even the steel case enveloping the Chernobyl reactor will be made with Cimolai steel components. Cimolai is able to participate in these projects thanks to its skills, quality, competitiveness and financial solidity. This has definitely been a good year for the company, and its order portfolio for next year (2014) allows it to keep an extremely positive outlook, especially thanks to projects for nonEuropean markets. n

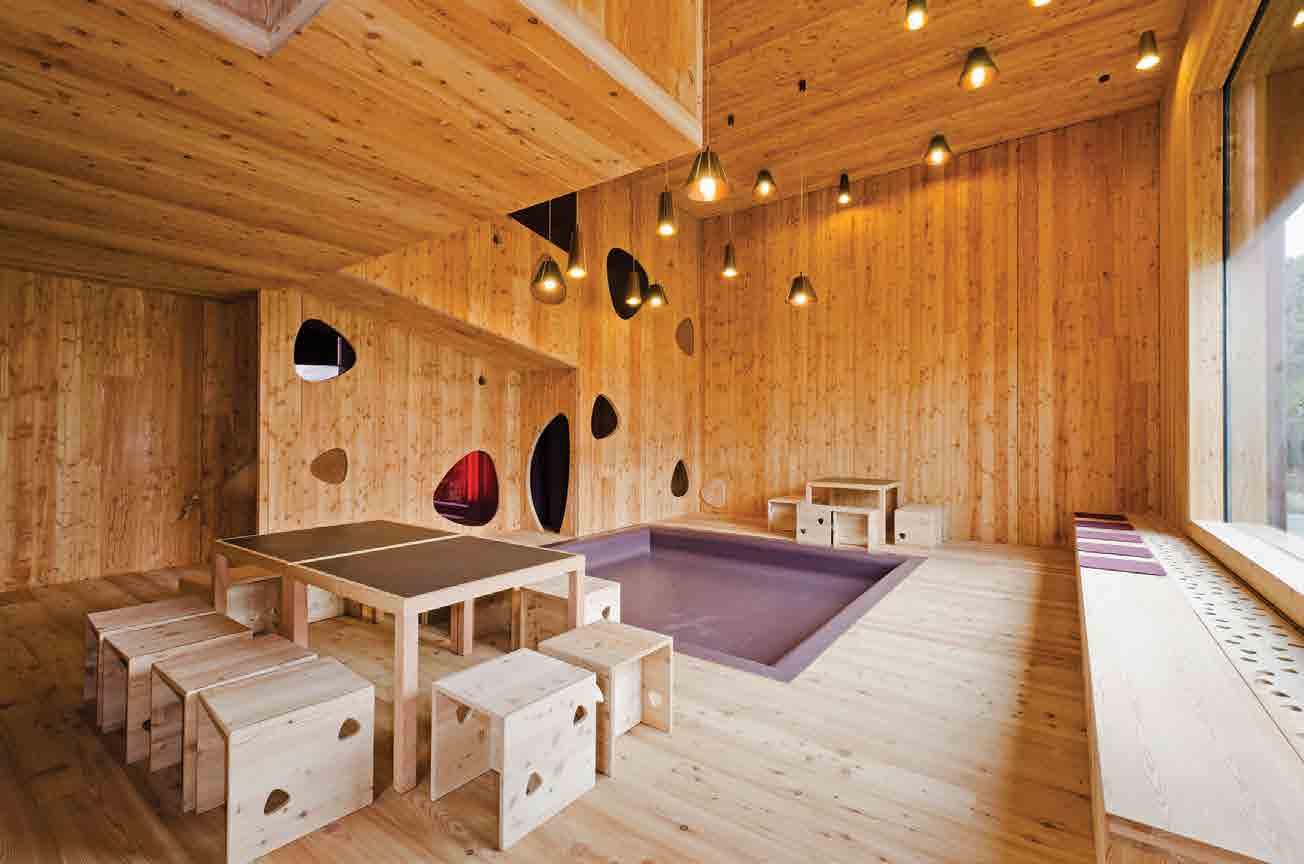
BUILDING FOR A SUSTAINABLE FUTURE
As a specialist in laminated timber, KLH Massivholz focuses on the development, manufacture and delivery of structural wall, ceiling and roofing elements made to fit the client’s project’s requirements.
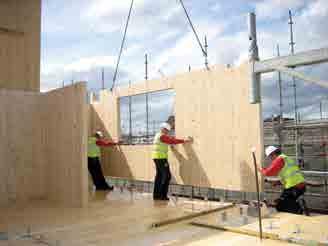
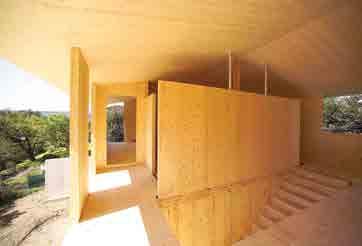
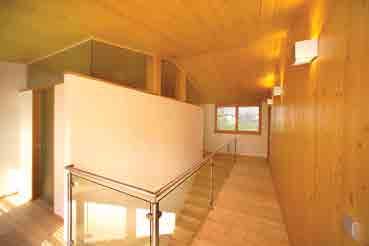
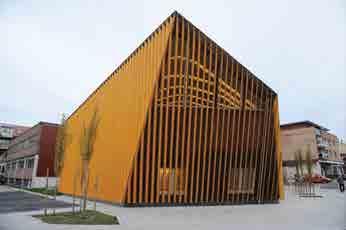
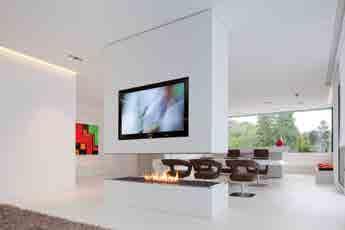
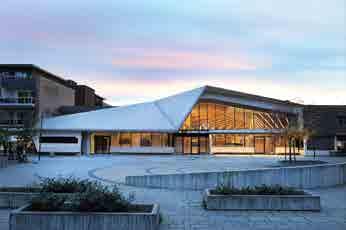
KLH Massivholz GmbH developed its first products in cooperation with the TU (University of Technology) in Graz. Based on extensive research and development, the Austrian business was able to begin the manufacture and distribution of large-format glued laminated timber elements in 1999. The following years of steady growth saw the company gain market-leader status in its field. Today, KLH employs around 130 staff, produces close to 650,000m² of timber boards per year and has an impressive portfolio of creative architectural projects located all over Europe.
Its services include technical and static consulting to ensure the smooth running of the construction process. Due to the company’s vast experience gained in numerous international projects KLH Massivholz can be considered an expert in providing sustainable construction materials.
The production process of the timber elements involves the cross-wise stacking of spruce strips which are then glued together under high pressure, forming solid wooden boards. The advantages of this manufacturing technique are numerous, as the strength of the wooden raw material is increased significantly, eliminating the swelling and shrinkage problems commonly associated with wood. Excellent static and high load-bearing properties allow the use of KLH even in earthquake zones and its fire resistance has been proven based on the European Technical Approval 06/0138. The KLH elements are delivered ready for assembly, and only require a short construction period. The slim elements’ space-saving qualities help to make excellent use of any living space and the dry construction method cuts down the waiting time for occupancy.
KHL is continuing to develop new products, such as the newly created ribbed slabs for ceiling construction. It has also created a new type of ceiling element to meet particularly strict fire-safety requirements. In cooperation with BiosLehm, a company specialising in clay render solutions, KLH has recently designed a clay render system optimised for use in combination with KLH timber. The wood and clay system, consisting of solid timber, a wooden fibre board and the clay interior render, has excellent insulation properties.
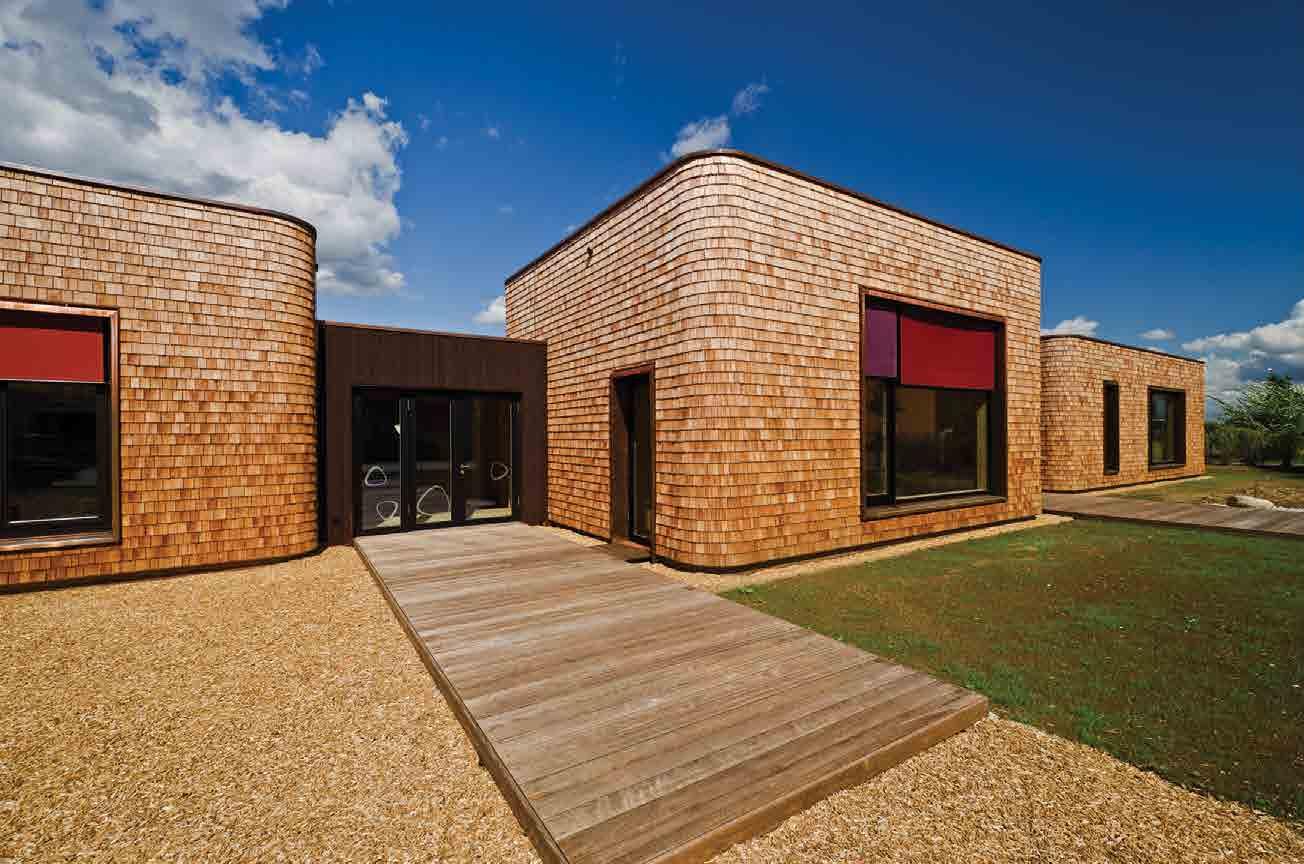