
8 minute read
Driving in the right direction Nord Motoriduttori
Founded in 1970, Elica has long been synonymous with the design and highquality manufacturing of cooker hoods on a national and international scale. Headquartered in Fabriano in the province of Ancona in central Italy, Elica prides itself on being a ‘Made in Italy’ company with regards to the style and design of its products. Aside from the production of cooker hoods, the group is also a European leader in the design and manufacture of motors for central heating boilers for domestic use.
Investing in new markets and R&D
The group has a total of eight production sites – five in Italy and one each in Poland, Germany and Mexico. Already present in global markets including Europe and both South and North America, over the past couple of years Elica has been targeting the growing Asian markets with the establishment of a production facility in India.
New product development is very important to Elica and is something into which it puts continuous investment. It has a central R&D department at its headquarters in Fabriano with additional centres in Germany, Poland and Mexico, which cater to their specific local markets. A company spokesperson explained: “We invest a significant amount as we value R&D as one of the most important aspects of our business. With this commitment to developing new products, we are proud to say that Elica has revolutionised the traditional image of the cooker head sector – it is no longer seen as a simple accessory but a designed object that has improved the standard of kitchens all over the world.”
Elica’s commitment to innovation also extends to its eco-friendly product range. As an ISO 14001-certified company, it has developed a range of products that have contributed significantly to the reduction of noise pollution in household kitchens. In 2007, it launched its Space range as the quietest cooker hood in the world. It also has a patent known as Elica Deep Silence which allows for a 40 per cent reduction in noise compared to traditional cooker hoods.
A recent addition to the range is the company’s highly innovative L-Original – a new recirculating hood that changes the rules of kitchen air treatment. This is the first hood to employ innovative Cyclone friction technology, which makes it possible to achieve extremely high levels of filter performance compared to traditional hoods, with a grease removal efficiency of over 90 per cent. Leaders in design
As a world conglomerate, Elica has a centralised marketing department comprising of three internal divisions. This includes a design team which has worked alongside eminent international designers such as David Lewis, Gaetano Pesce and Stefano Giovannoni. “At Elica, we consider ourselves not only to be a world leader with regards to market share but also in innovation and design,” adds the spokesperson.
A recent example of the company’s focus on unique design is the 35CC cooker hood. This product is composed of two shells in the form of a ‘C’: one external, aesthetic and colourful and the other inside which is functional and made from plain or perforated steel. This offers a unique combination of beauty and functionality in one single product. The hood is available in white, orange, turtledove or lily for the Evoque version; or red, black, yellow and green for the Dynamique version. It comes with high-efficiency lighting thanks to four LEDs that together generate 12 watts, all of which can be controlled with an electronic, rotating touch remote control on the internal shell.
The company’s other two marketing divisions are divided into product managerheaded teams dedicated to developing
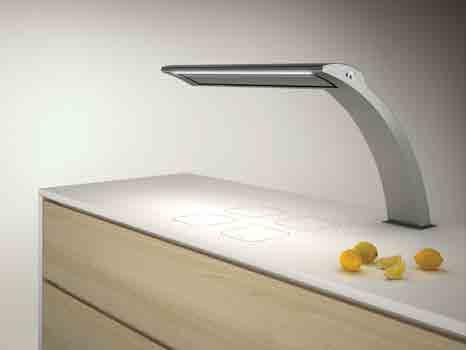
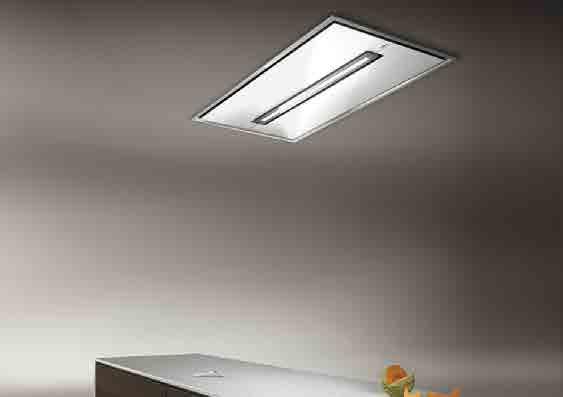
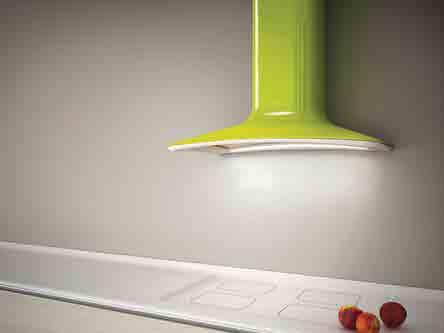
products for OEM customers and Elica’s own brands respectively. It also attends many exhibitions each year as it has invested a lot in brand building. In January this year (2013), for example, it was present at LivingKitchen, the international kitchen fair in Cologne. Along with its subsidiary company Gutmann, Elica showcased the latest models from its 2012/13 range, including highlights such as Tiffany and Sweet, which have recently received the iF Product Design Award, one of the most prestigious international recognitions in the field of product design.
With a workforce of 2300 employees, each year Elica produces approximately 16 million units spread across its cooker hood and motor activities. Around 70 per cent of its annual turnover derives from serving large multinational OEM customers such as Whirlpool, Electrolux, Bosch and Siemens whilst the remaining 30 per cent stems from Elica’s own brands which include acquisitions such as German subsidiary company Gutmann. n
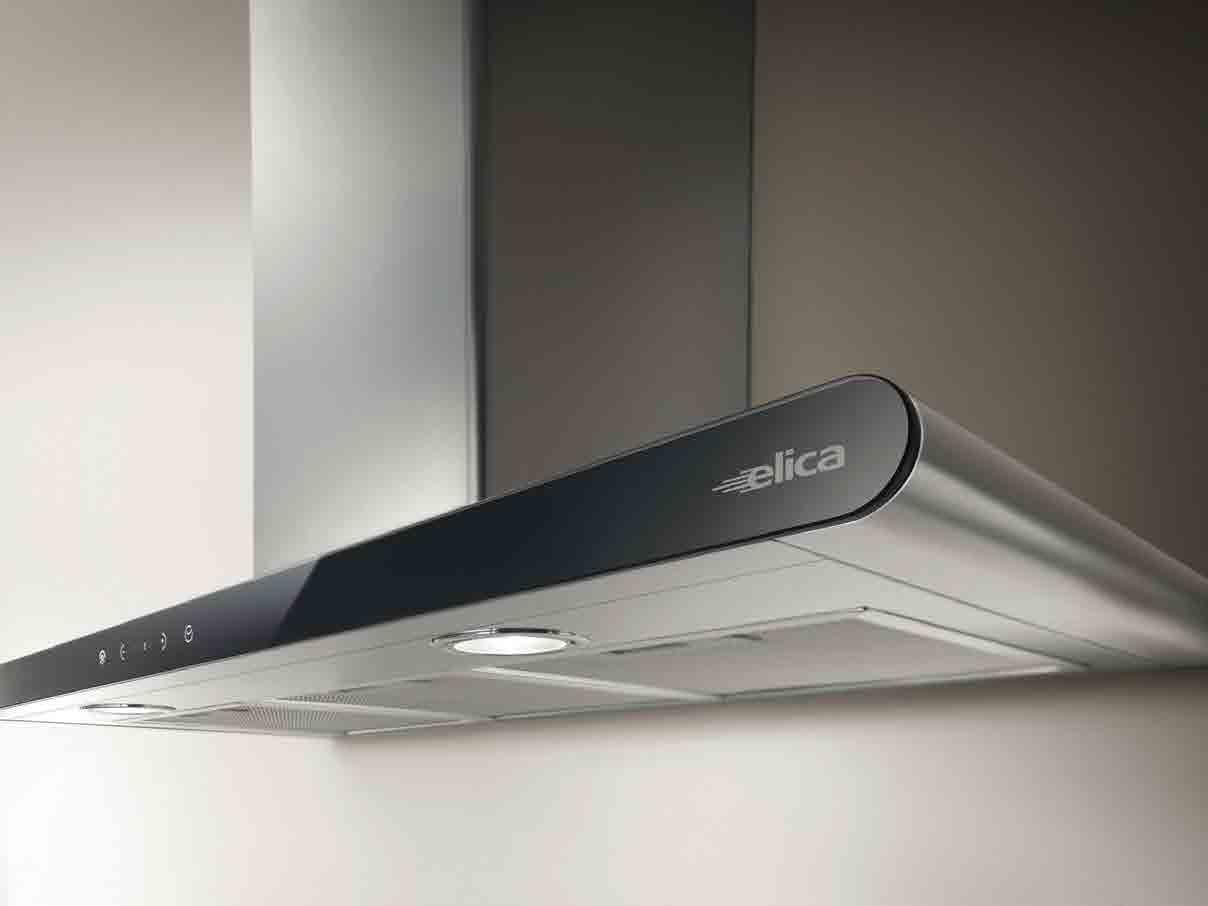
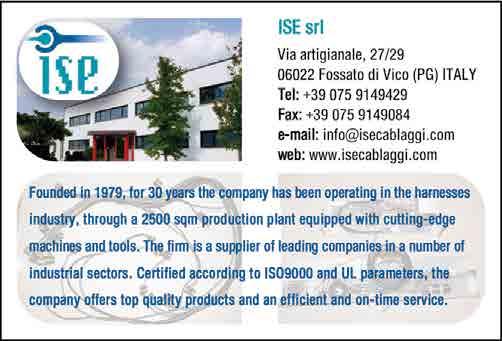
From the left the General Manager Marco, Mearini and the Sales Manager, Sergio Felicissimo
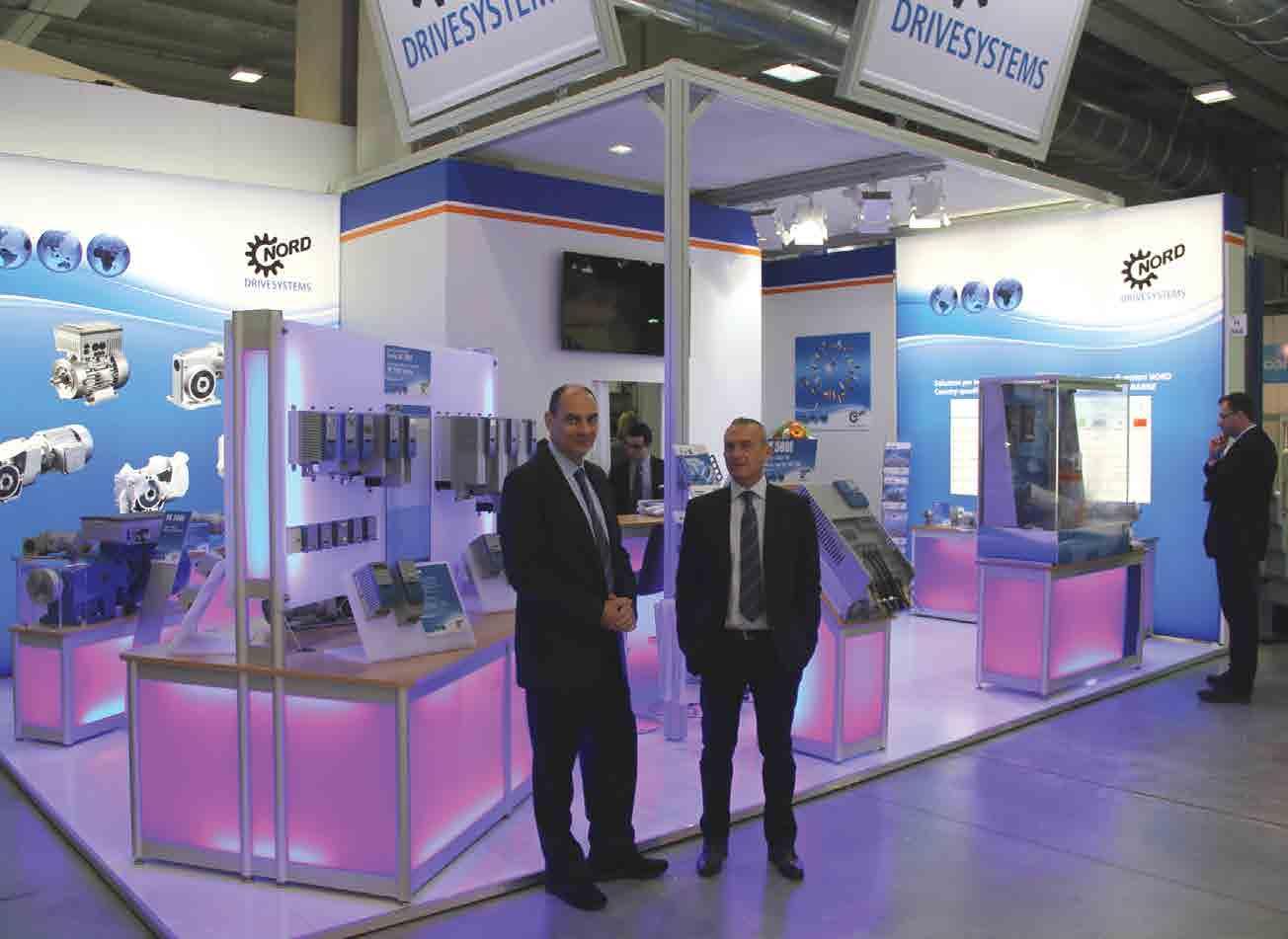
DRIVING IN THE RIGHT DIRECTION
Industry Europe speaks to Mr Marco Mearini, managing director of gearbox manufacturer Nord Motoriduttori Srl, about the company, and its future plans. Barbara Rossi reports.
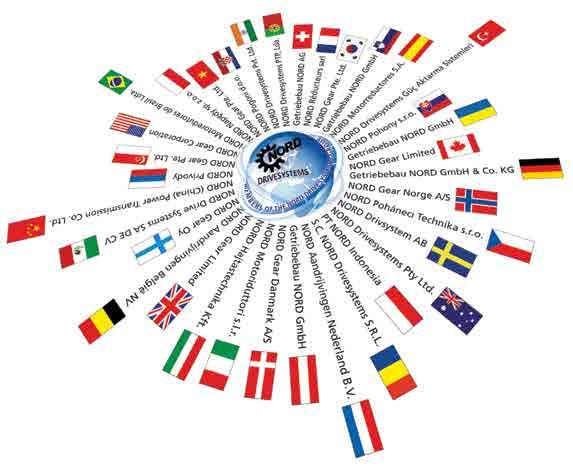
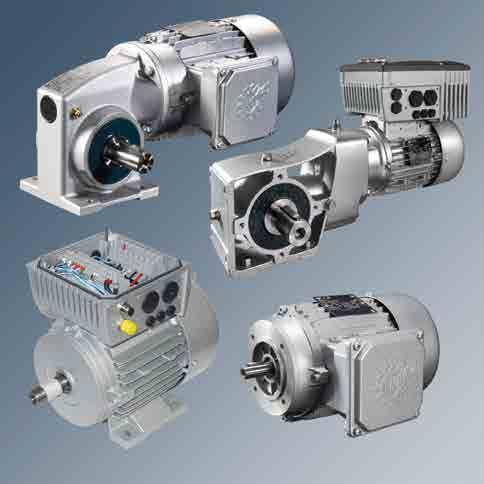
Nord supplies complete drive units, consisting of a gear unit, an engine of an optimal energy efficiency class and drive electronics. The modular systems – in the picture: the choice of Nord industrial gear units – which allow customised configurations at a reasonable price, while still offering fast delivery times.

The Plant in San Giovanni in Persiceto: the ‘extension of the new shed will open in September Figure Nord stand at the SPS IPC Drives in Parma Italy; seen the positive outcome was also confirmed at the fair for 2014
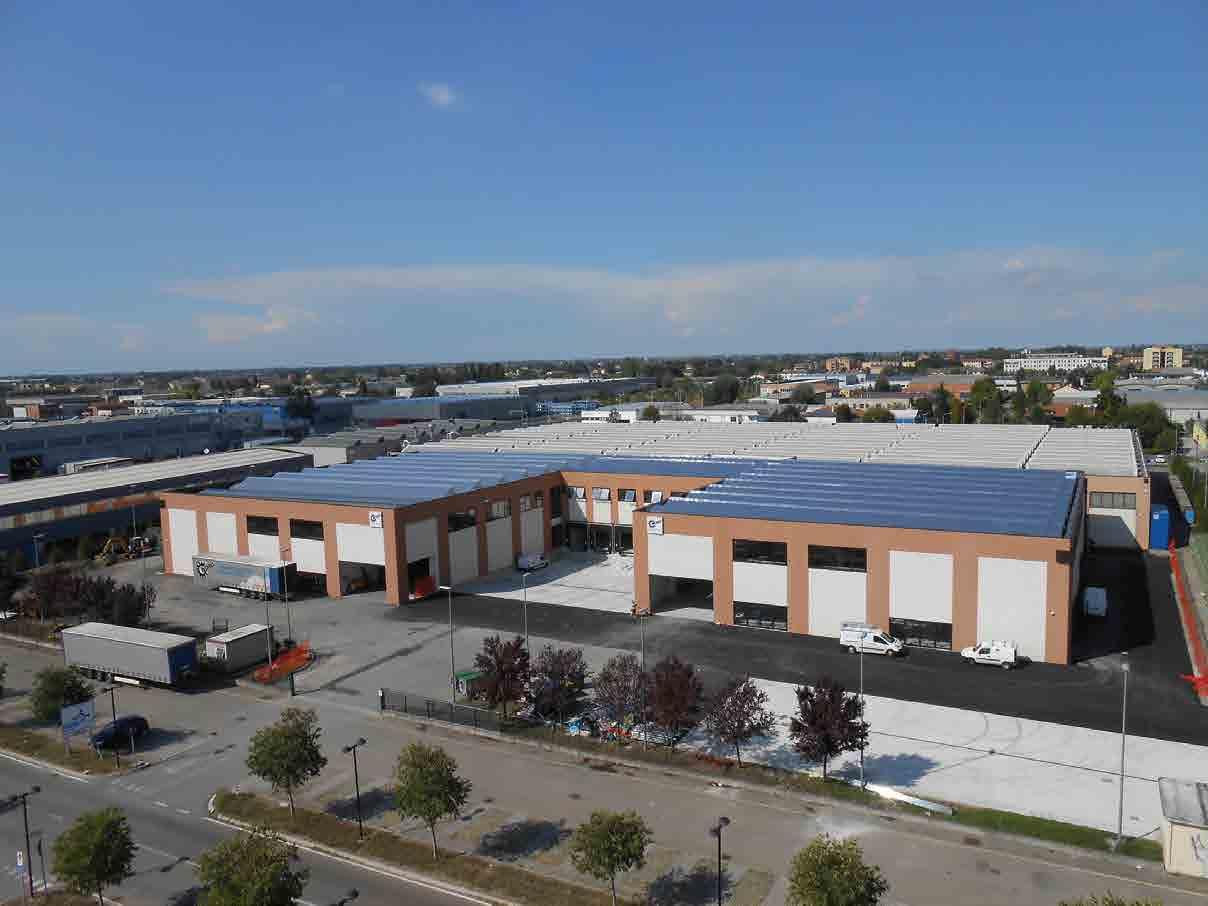
Nord was founded in 1965 in Bargteheide, near Hamburg, as a supplier of gearboxes. In-house production was initially limited to gear cases, shafts and flanges, while other components were procured elsewhere. However, Nord soon expanded its range to include all parts for the production of complete gearboxes. Later on, power electronics and electric motors were added to the line-up, so that today the group is a full-scale provider of drive solutions with a deep understanding of the industries that it supplies.
Mr Mearini further explains, “Over the years, we have maintained our leadership in gear technology. The innovation with the most lasting impact in this area was the UNICASE housing concept, developed by Nord in Bargteheide in 1981. Before that, multi-part gearbox housings used to be susceptible to oil leaks and to damage, owing to torque and radial forces. Nord was the first manufacturer to make only single-cast enclosures with integrated bearing seats. These are much more compact and have a much greater load-bearing capacity, as well as a longer lifespan.”
As Nord diversified, specialised factories were established, initially in various locations throughout northern Germany. Today, the Nord Drivesystems Group has 35 subsidiaries in different countries and an international network of sales and service partners.
Talking about the role his company plays within the Bologna-based Nord Motoriduttori Srl plays within the Nord Group, Mr Mearini says: “Nord Motoriduttori has a special position in the group. We supply the entire Nord Group with asynchronous motors for all mains voltages worldwide, IE1 to IE4 motors, ATEX motors, special variants and motors compliant with the most stringent worldwide standards such as, for example, the Canadian CSA standard or UL for the US market. In 1987, Nord Motoriduttori Srl was founded as a sales office for the Italian market with a staff of just three. In 1996, we opened a gearbox assembly plant. In 1997, the German parent company decided to diversify into electric motors. As Italy is home to many materials suppliers, it was chosen as an ideal site.
“In 2003, we moved to a larger site in San Giovanni in Persiceto, near Bologna. Meanwhile, owing to growing global demand, Nord opened a second motor production plant in Suzhou (China) in 2005, and we have expanded the floor space in San Giovanni by 50 per cent to 15,000m² to make space for additional motor production lines and for the assembly of gear units with a larger output. We now employ a staff of about 170 and have an annual capacity of 500,000 motors and 20,000 geared motors.
“The EU energy-efficiency directive that introduced a motor efficiency classification has accelerated a substantial progress to the movement for more efficient drives. We have designed IE1 to IE4 motors so as to enable our customers, who are mostly machinery and equipment manufacturers, to continue producing economically viable solutions that comply with all regulations. And we want to keep their extra engineering effort as minimal as possible. Many recently completed conversions show that Nord drive components with an IE2 or higher rating can be easily integrated. The one-off additional costs for end users are usually redeemed within a short time, since
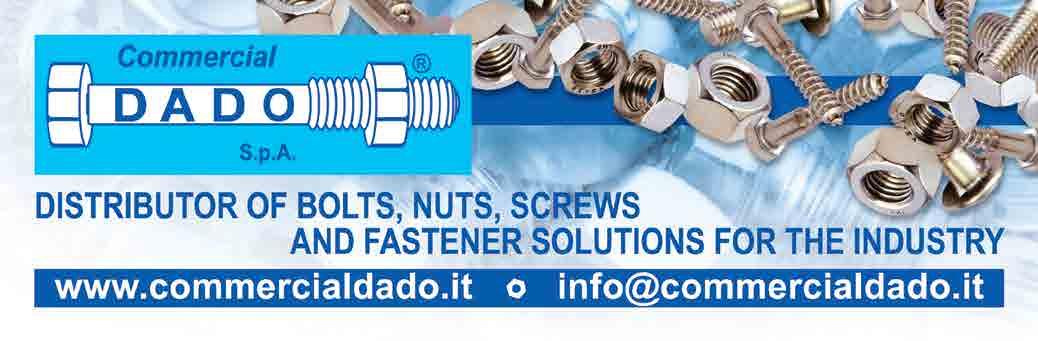
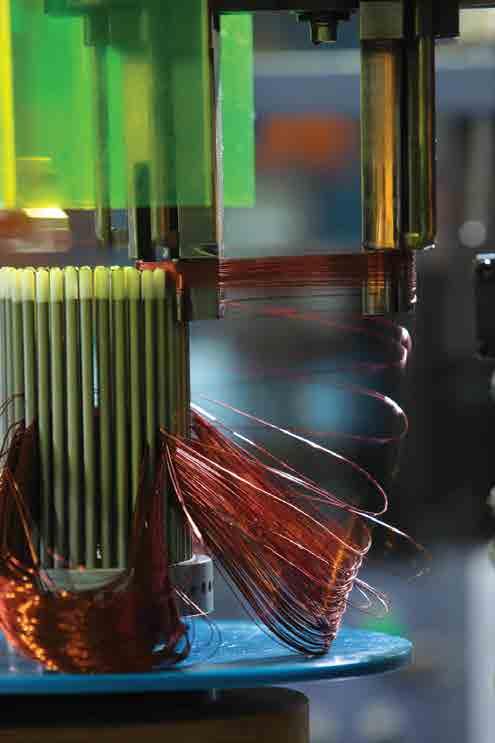
Nord manufactures engines for all grid voltages in the world, engines from IE1 to IE4, ATEX engines, special variations and engines complying with Canadian standards (CSA), as well as engines with UL certification for the US market.
on average energy costs make up 80 per cent of a drive system’s TCO (total costs of ownership).”
What makes us special
Nord supplies drives for applications such as material handling, lifting and conveying technology, as well as for pumps, mixers and fans. These products are for sectors such as the steel, construction, mining, lumber, airport,
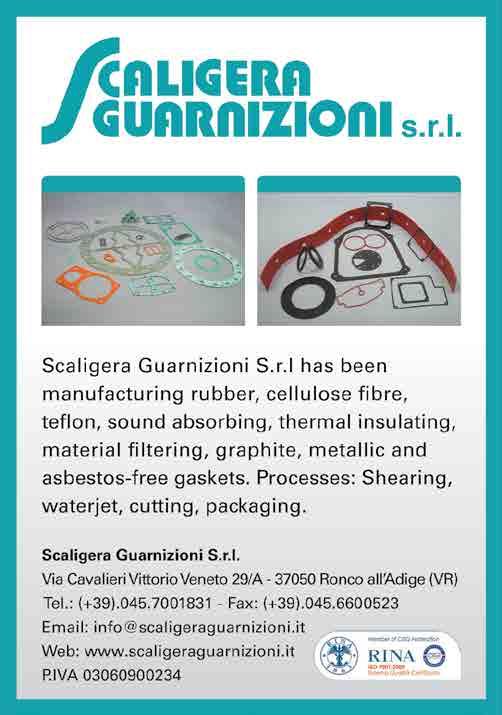
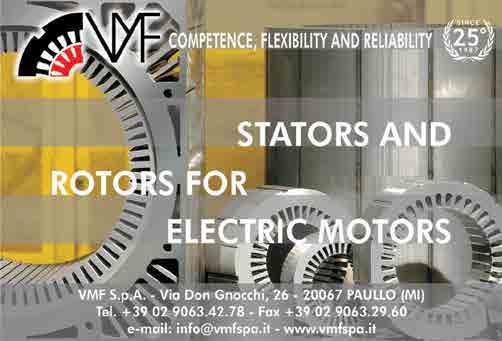