
9 minute read
Perfection in your hands Wollsdorf
STAMPAGGIO MATERIE PLASTICA E GOMMA - COSTRUZIONE STAMPI
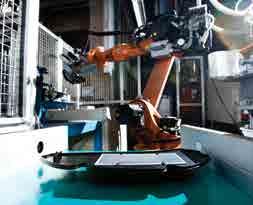
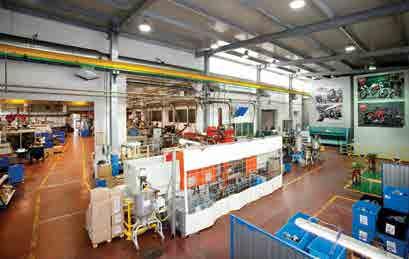
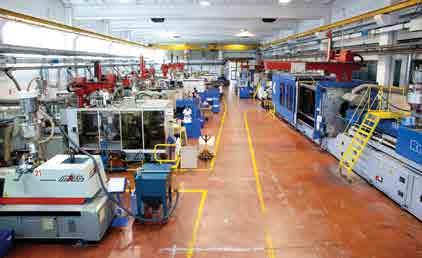

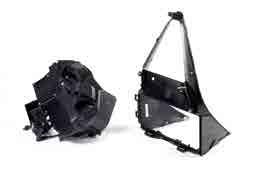
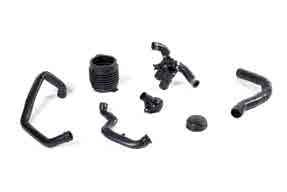
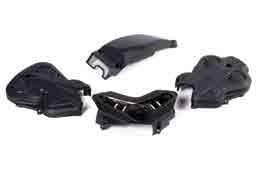
Plasgomma Srl Loc. Campocuiano 62024 Esanatoglia (MC) Tel: +39 737 889393 / 889566 • Fax: +39 737 881484 E-mail: plasgomma@plasgomma.com • www.plasgomma.com Fornitore Uffi ciale 2013
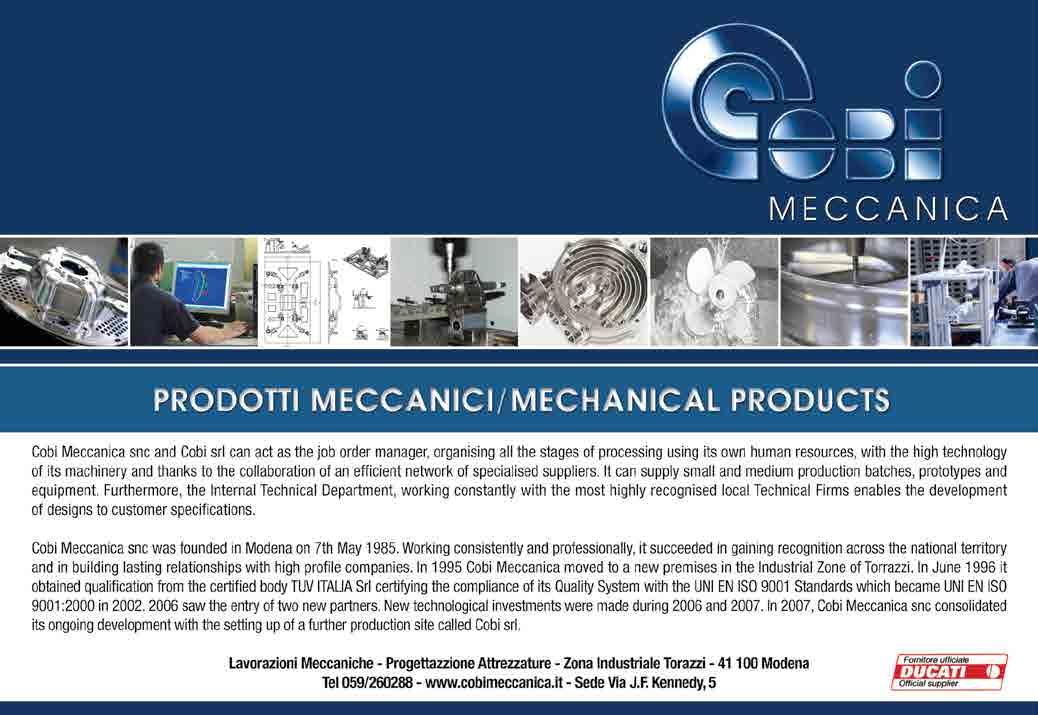
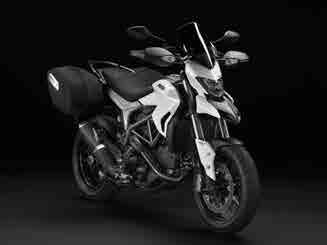
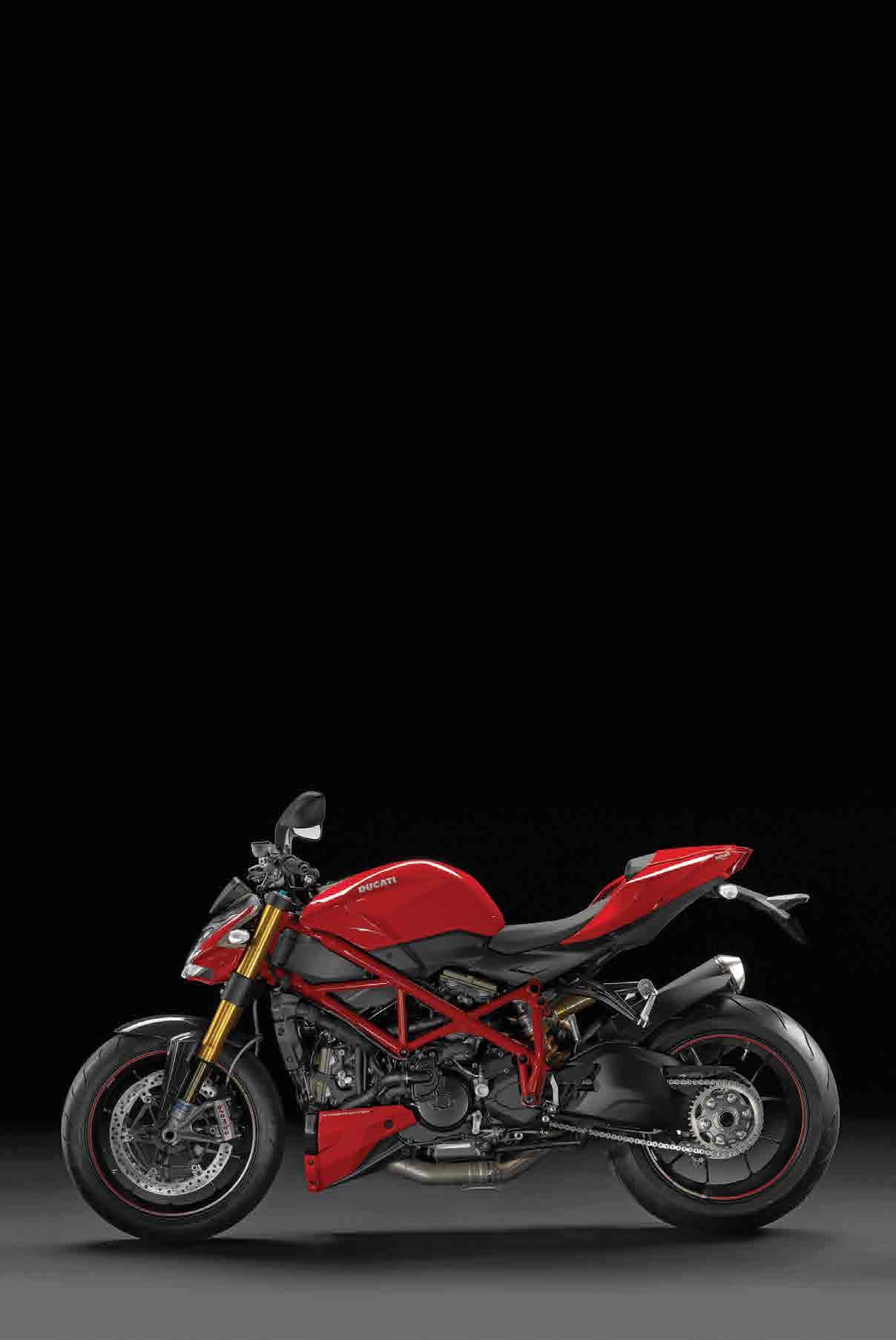
Streetfighter and Superbike with associated apparel and accessory lines. The new Diavel is available in different versions: Diavel, Diavel Dark, Diavel Carbon, Diavel Strada and Diavel Cromo. It is also available in three riding modes, namely Urban, Touring and Sport. The new Diavel, in particular the new Diavel Strada, has widened its range of use, transforming from a ‘muscle bike’ to being an excellent player on winding roads and a reliable partner for medium haul trips.
A new generation of Hypermotard was also launched on the market in November 2012, still based on the features which made this bike unique and successful – namely design, innovation, sheer fun, advanced technology and exclusive engineering solutions. Hypermotard is available in three versions: Hypermotard, Hypermotard SP and Hyperstrada – the last being a perfect cross over between the world of Motard and that of the touring bike. The Hypermotard series is characterised by a new, water-cooled, 4-valve 821cc engine. It offers simplified maintenance as, thanks to constant investments in design, state-of-the-art components and the attention Ducati has dedicated to even the tiniest detail, maintenance intervals can be extended even further. This range is also available in three riding modes, specifically designed for each model.
As this year is the 20th anniversary of the launch of the original Monster model, a unique model, the original version combined with the latest generation performance, has recently been introduced.
The new Multistrada 1200, on the other hand, offers Skyhook suspension, a stunningly smooth Testastretta 11˚DS engine, plus the usual Ducati appeal. The series includes four models, one of which is the Multistrada 1200 S Touring, described as being ‘born to travel’.
The new Ducati range for 2013 also includes the Streetfighter, which comes in two models, the new Streetfighter 848 and the latest Streetfighter S. With a fighter attitude and a naked sophistication, Streetfighter truly offers all the elements which have made the Ducati superbikes legendary.
The Superbike series also comprises several models, among which there is the 1199 Panigale R, which having been born out of the world of competitive racing and offering technological excellence, as well as an unbelievable performance, can be truly defined as the flagship of the superbike family.
Every year, Ducati collects many awards from around the world for its innovative and stylish motorcycles. These are fitting accolades for what the company proudly refers to as ‘hand-built motorcycles of authentic Italian performance’. n
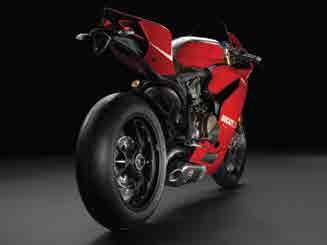
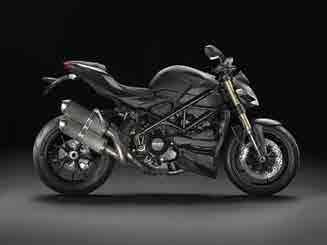
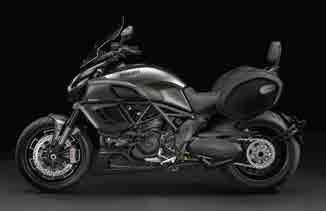
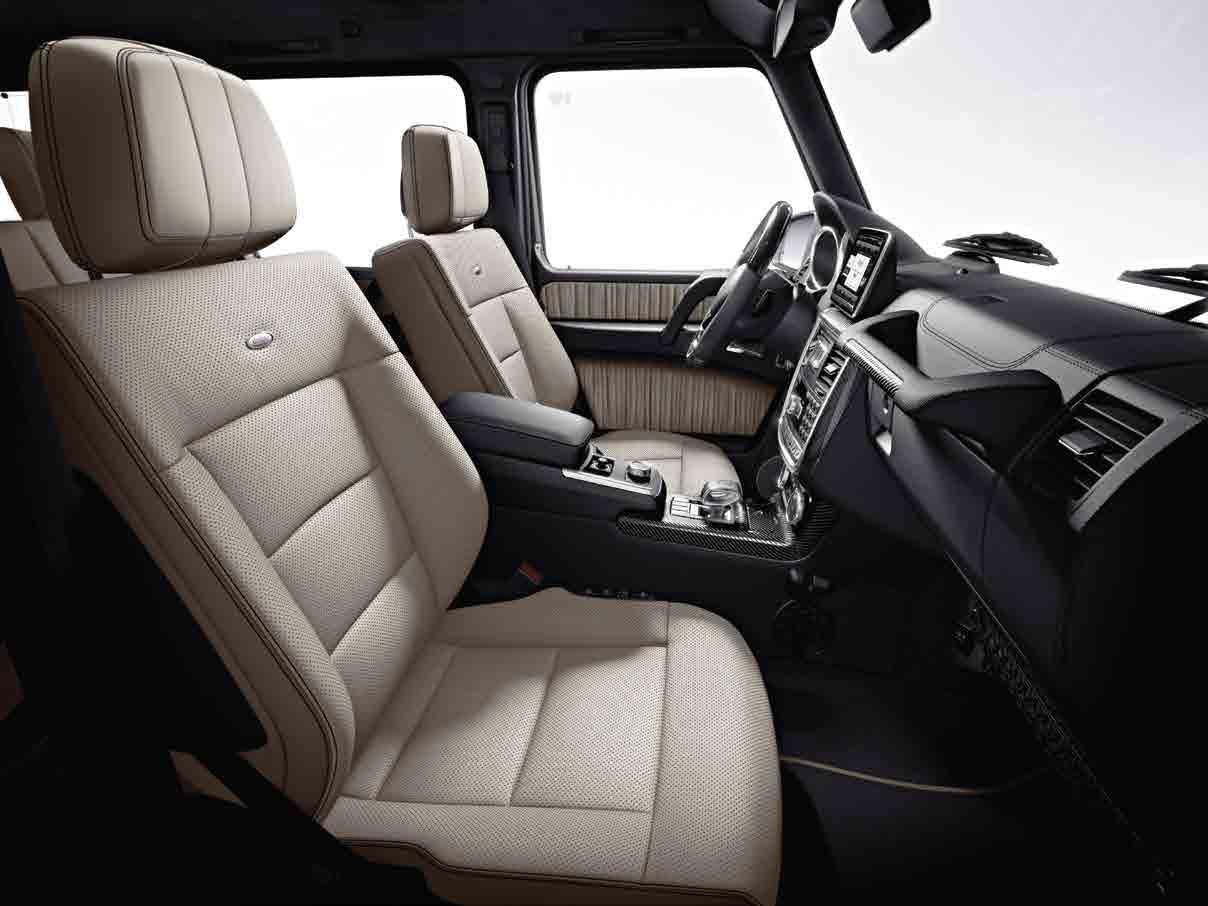
PERFECTION IN YOUR HANDS
Wollsdorf is the world’s leading manufacturer of the finest quality leather for car steering wheels. Peter Mercer finds out what exactly makes the company special.

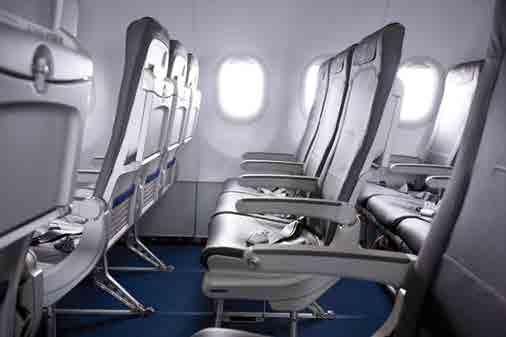
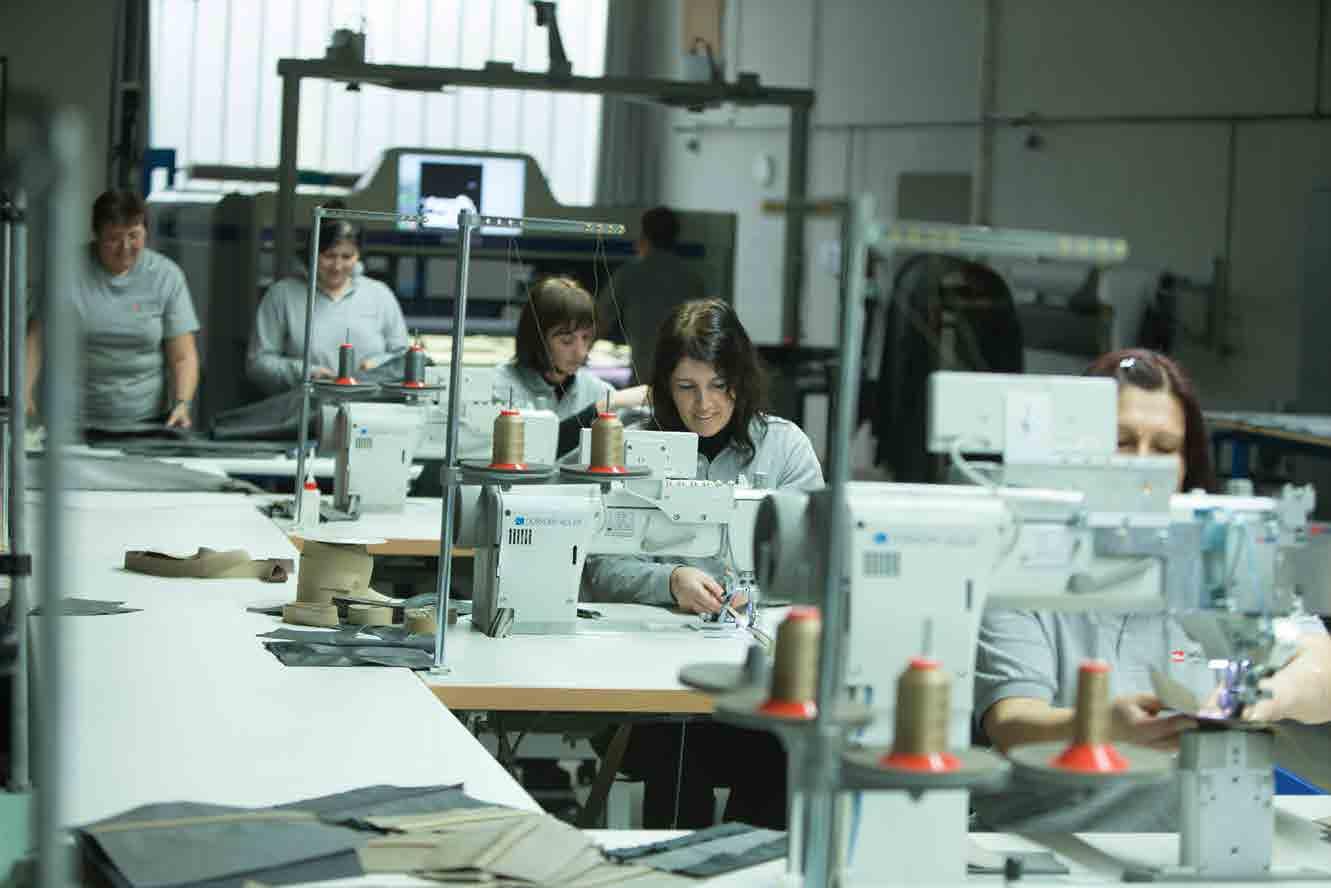
IN March 2013 Wollsdorf Leather, the global market leader in full-grain leather for car steering wheels, took another decisive step forward with the opening of its own development centre for parts and sewn seat covers. The new centre is equipped with the latest technology and has enabled the company to provide a full service in terms of surface leather as well as embossed, stitched and printed leather parts.
“In addition to our fully integrated tannery and the punching department at our Weiz facility this new development centre is the next logical step in moving even closer to the customer,” said Wollsdorf CEO Andreas Kindermann. “This expansion will further open up some highly qualified job opportunities and underline our claim to market leadership.”
Wollsdorf is one of the leading leather producers in Europe. From its production sites in Wollsdorf and Weiz, in the East Styria region of Austria, it produces the finest quality products for the global automotive, furniture, aircraft, marine and garment industries. Its core business is in producing premium leather for car steering wheels, an application which is the most demanding of all the uses of leather in car interiors. In fact the company is the world’s leading manufacturer of steering wheel leather; over 60 per cent of its entire production is dedicated to this application and it has about 60 per cent of the premium European market, supplying top range marques such as Audi, BMW Jaguar Landrover and Mercedes Volkswagen Volvo. Wollsdorf also has a plant in China which produces steering wheel leather sets for the rapidly growing Chinese auto industry as well as leather covers for aircraft seats.
Something special
Wollsdorf has been developing top-class quality products for the automotive industry for decades and now approximately 20,000 cars are sold each day upholstered in the company’s leather. It attributes its success in maintaining such a leading position to a unique combination of passion, technology, flexibility and innovation.
In fact, says Andreas Kindermann, the company has recently been taking a close look at what exactly it is that makes it special. “Fundamentally it comes down to how well we utilise our resources,” he says, “and that includes the raw materials that we process, the craftsmanship and expertise of our staff and our care for the environment, which is, after all, another resource. We think that we do something special in all three of these areas.
“To start with, we are very careful in our selection of hides, which are all sourced from Limousin bulls in southern Germany and northern Italy. To produce the finest quality hides these cattle have to be bred and fed correctly, they have to be kept very clean to avoid skin diseases and they have to be kept in the right conditions – within cattle-friendly fences, for example, to avoid tears and abrasions. Then, in every stage of the production process, we operate rigorous inspection and sorting procedures so that we can remove imperfect hides and end up with a product that has an above average content of full-grain leather.”
Mr Kindermann explains that leather producers often hide scars, insect bites and so on by embossing or working the surface
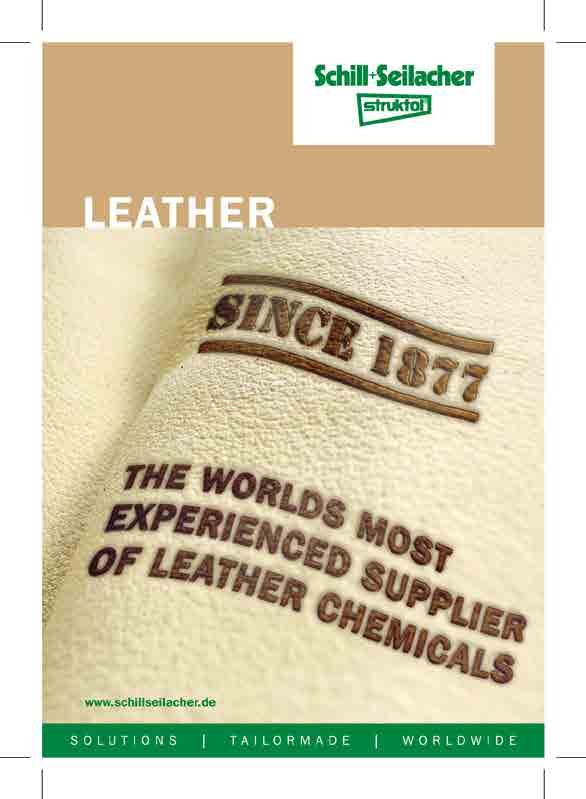
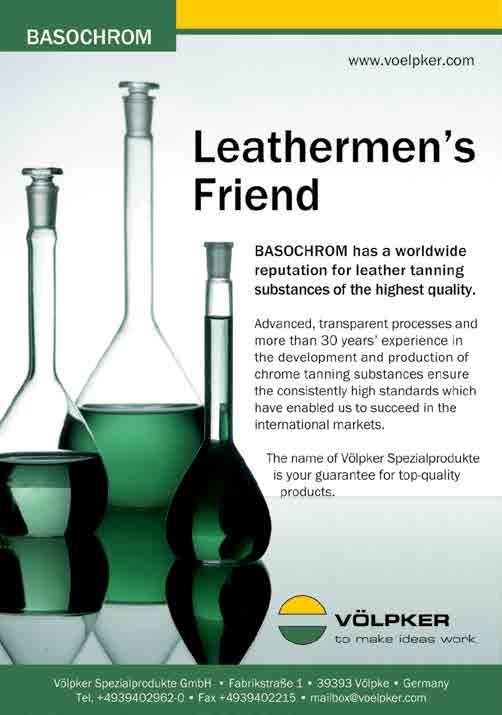
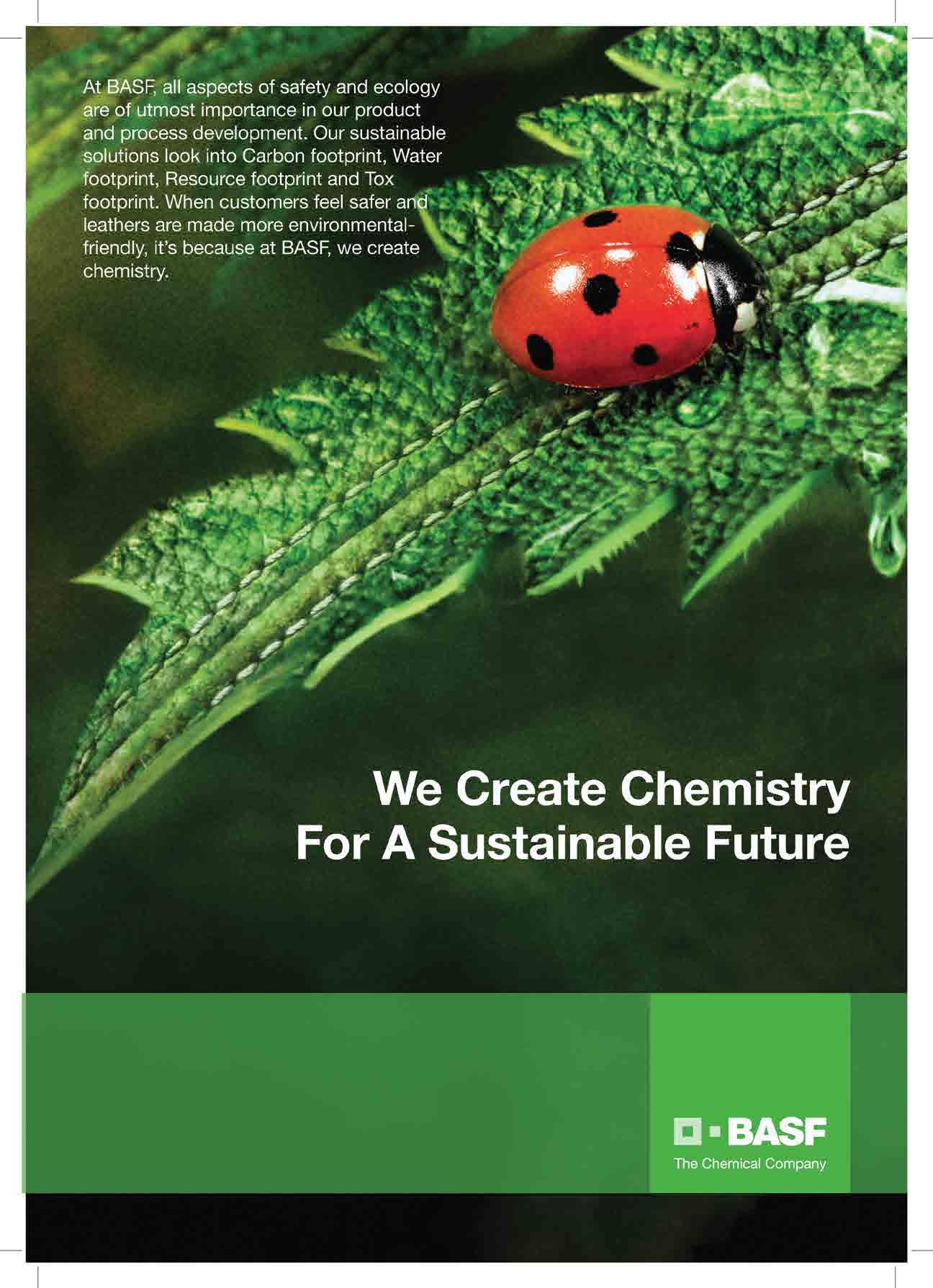
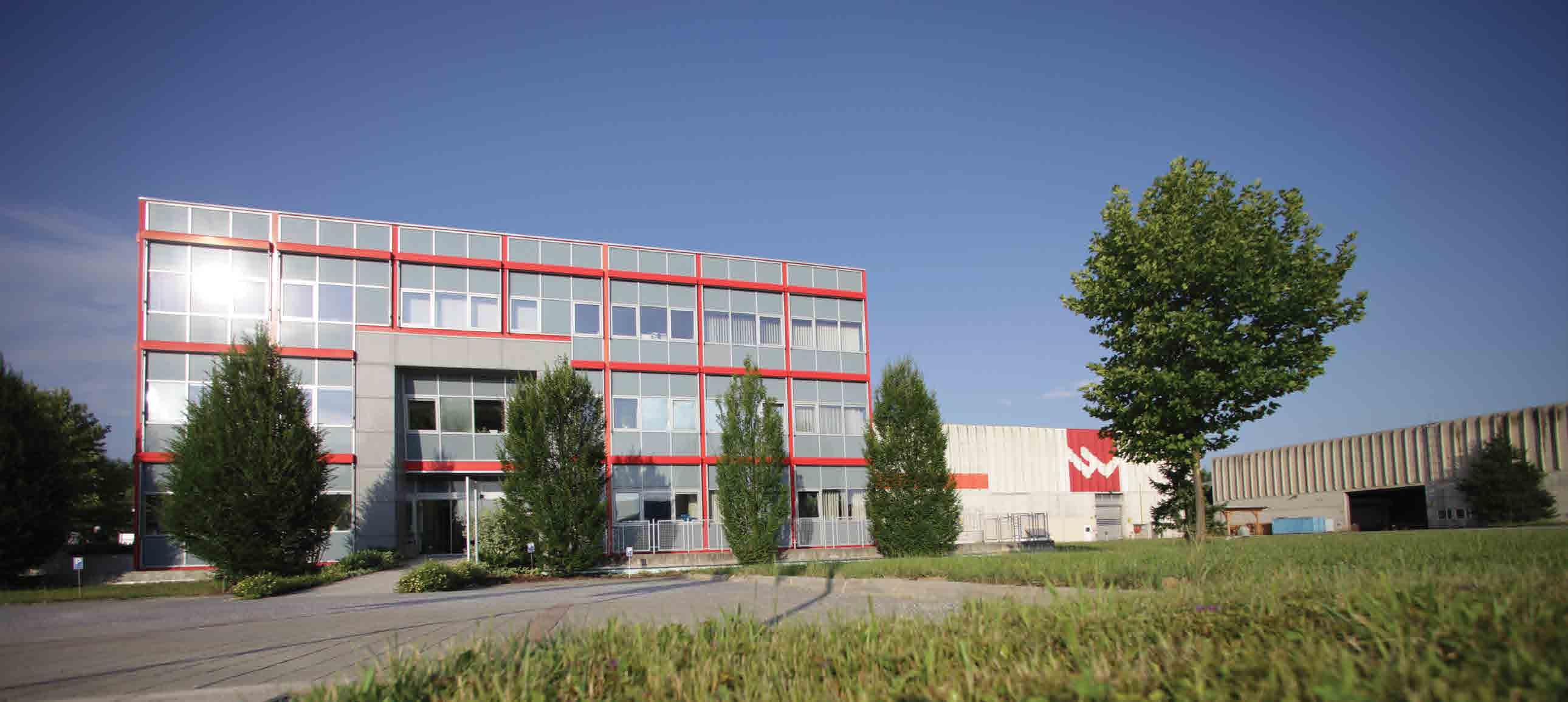
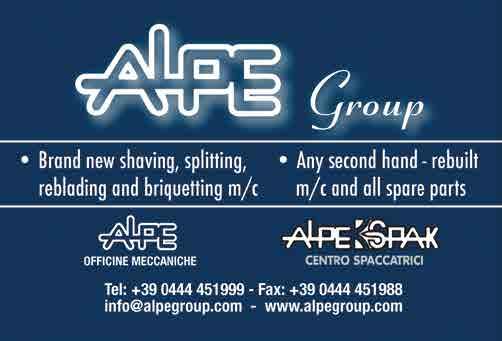
BASF
As the world’s leading chemical company, BASF has established itself in the leather industry for more than 100 years. Our key customers, such as Wollsdorf Leder, have worked with us for decades and many have seen us as a sustainable, reliable and innovative partner. Working continuously on product and process development, we help our customers produce leather in a sustainable way which enable them to meet the stringent requirements set by the OEMs, brands and consumers. With a complete product range, from beamhouse to finishing, supported with strong technical expertise, a large integrated chemical production and the newly global automotive setup in Germany, BASF is well positioned to lead this industry.
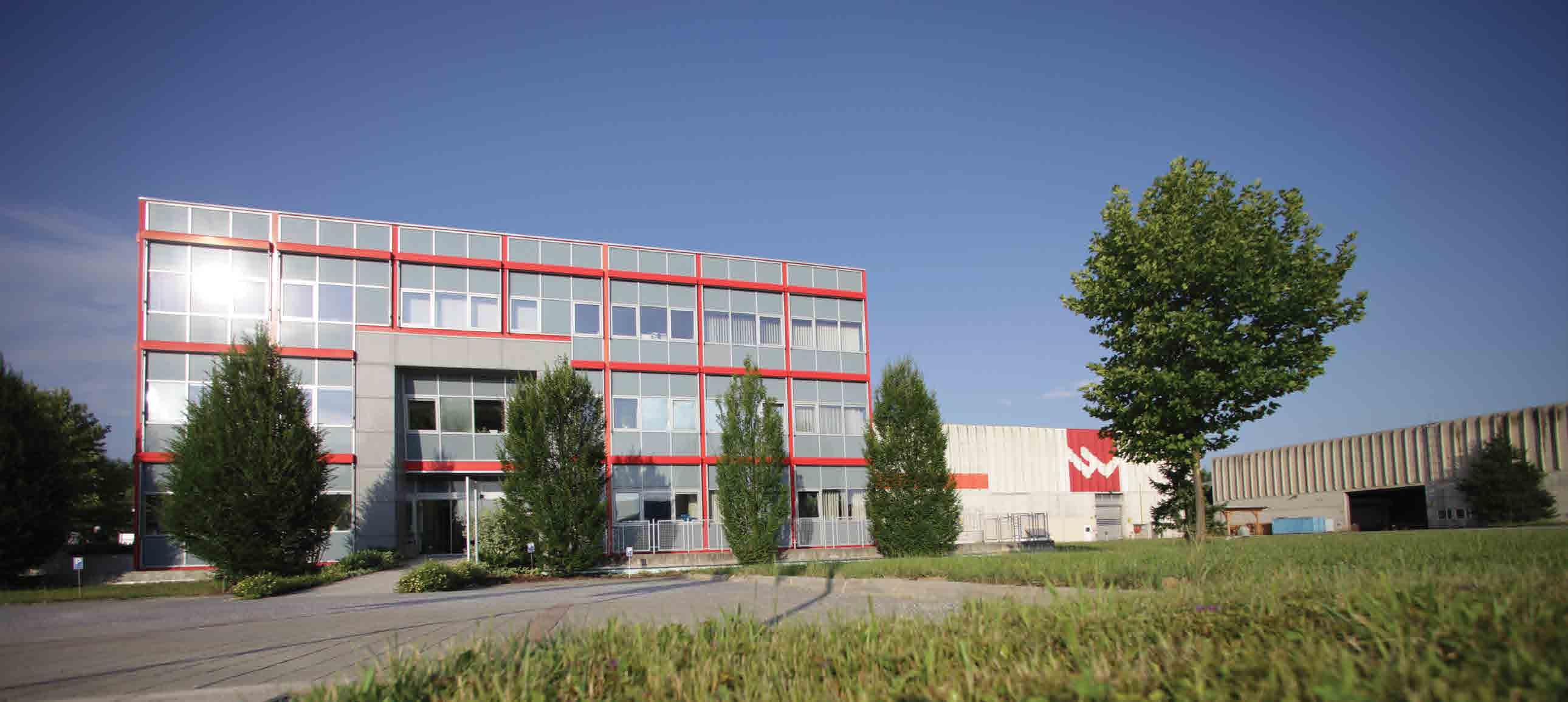
structure to hide these defects. This is a perfectly acceptable practice but for its premium steering wheel leather Wollsdorf uses as much full-grain leather as possible.
Looking after people, looking after nature
Wollsdorf also puts a lot of work into the education and welfare of its employees. It identifies strongly with the East Styria region of Austria but its workforce is multinational. There are people from more than 40 nations, from all over Europe and from the Americas, Africa and Asia, working under its factory roof, says Mr Kindermann. More than 500 work at the headquarters in Wollsdorf itself, producing leather for cars, aircraft interiors and furniture upholstery, and another 300 at nearby Weiz, where they cut leather for around 120,000 steering wheels per week and for another 100,000 small parts such as instrument panel finishes and air-bag covers. The plant in China currently employs about 50 people engaged in cutting and sewing steering wheel leather and leather for aircraft seats.
“We are committed to providing our staff with the maximum opportunities for training and advancement,” says Andreas Kindermann. “We have set up the Wollsdorf Academy and implemented a training policy that starts with the shop floor workers and goes on up through shift leaders and department managers. We want everyone, even if they have no high-school education, to realise that they can move up through the company. Our health and safety schemes have reduced accidents by 50 per cent in the last two years and we have regular health checks for all our employees. We have a profit share scheme and a company newsletter and I myself meet with everyone we employ in small groups each quarter to make sure they are all fully informed about the company’s progress.”
Wollsdorf is equally imaginative in developing programmes to protect the environment. In the last two years it has reduced its use of water in hide processing by 30 per cent and continues to improve the efficiency of its waste water treatment plant. This year the company has also introduced a plant that will convert animal fat into biodiesel. “We have to deal with around 10,000 tonnes of fat a year, and up to now we have just had to dispose of it as waste,” explains Mr Kindermann, “but we can now extract from this total some 1000 tonnes of clean fat which our new plant can convert into a quantity of biodiesel equivalent to half our own annual thermal energy requirements, although, in fact, we don’t use the fuel ourselves.”
Lightening the load
But Wollsdorf is also helping the environment through the development of its own products. It has recently introduced a unique ‘lightweight’ leather specifically for aircraft seats. Developed together with its long-term partner Schauenburg for seats that are made by Recaro, this new product offers weight savings of some 40 per cent over traditional