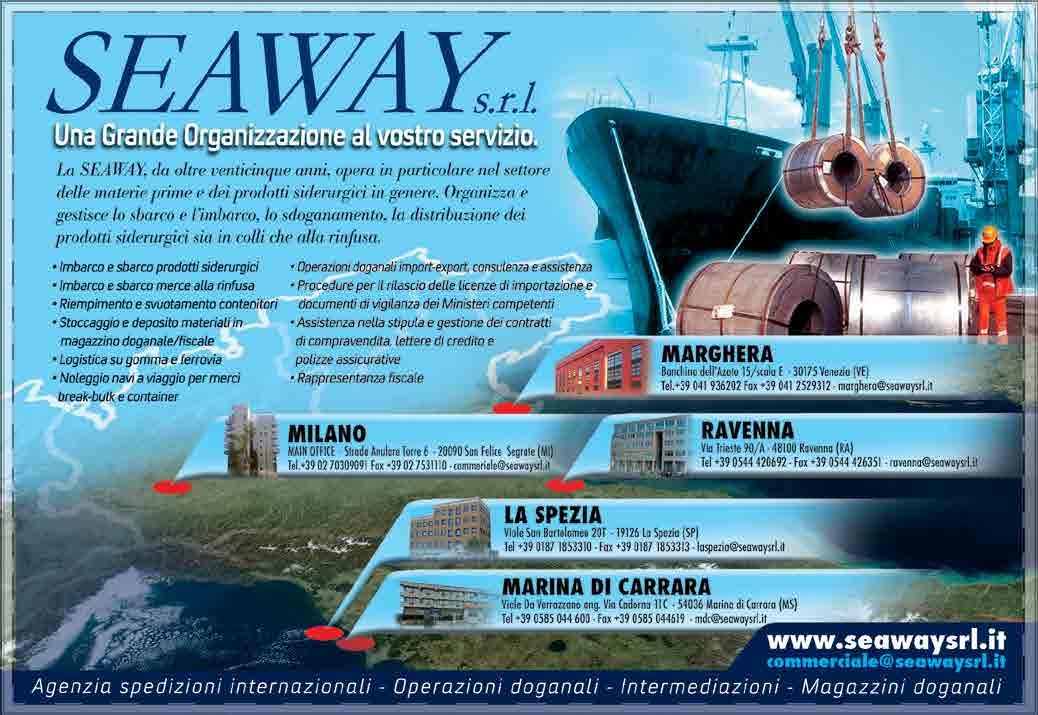
6 minute read
Delivering robust sensor technology solutions
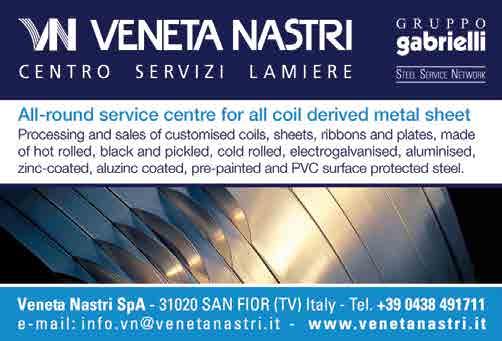
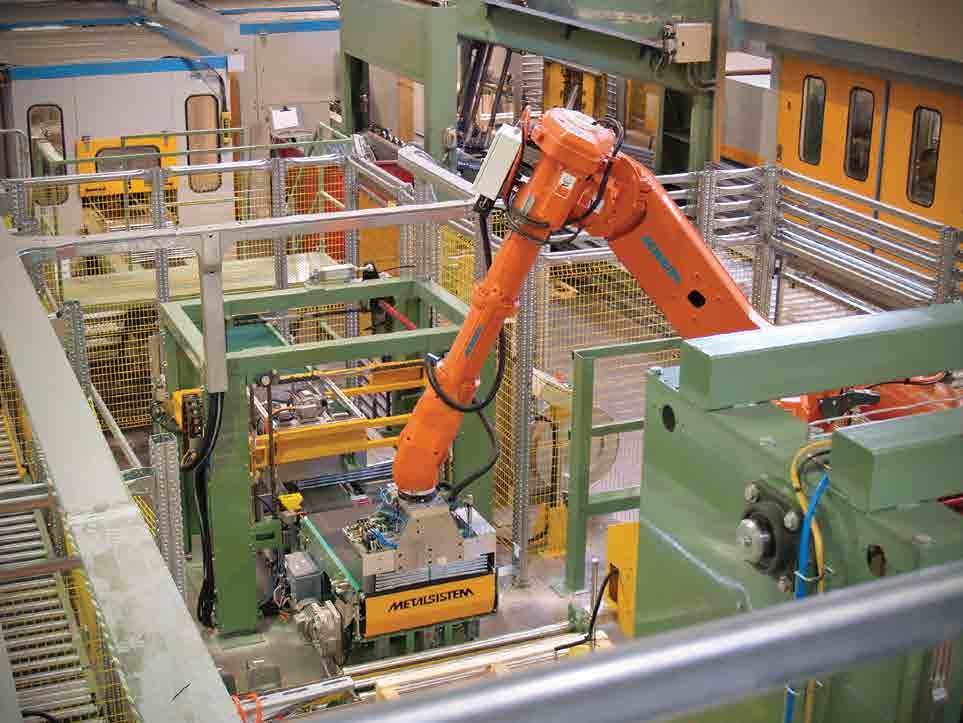
Nord Pallets is specialised in the production and supply of pallets and standard packaging, but it is also able to supply customised solutions suitable for any type of needs. The wood used – soft (coniferous) and hard (beech) – is individually selected to ensure product quality. The company is a sector leader thanks to the modern technology of its production department, its indoor warehouse and its direct deliveries, carried out with its own articulated lorry.
Pallets & Imballaggi di Asson Mario & C. s.n.c - Via Carraia, 38010 Don (Tn) Tel: 0463/875466 - Fax: 0463/875466 - E-mail: info@nordpallets.it
mation translates into productivity, competitiveness and high quality.”
The company, which holds all relevant certifications such as ISO 9001, 14001 and 18001 among others, has a strong commitment to environmental sustainability. It is involved in the Tekne Technological steel project, in collaboration with the Arvedi group. The purpose of this program is that of promoting the introduction of innovative steel smelter production cycle technologies to obtain structural steels of superior quality from recycled metals, cutting CO2 emissions and reducing both energy and water consumption. Corporate social responsibility also finds expression through the Metalsistem foundation, which operates independently and is engaged in supporting projects benefitting children in various countries.
Furthermore the company has implemented green energy at its own premises. “At our Rovereto site we have installed one of the largest photovoltaic systems in Italy, with a roof system comprising almost 12,000 solar panels and occupying a space of more than 38,000sqm. This has made the company almost self-sufficient at this production site in terms of energy requirements for the manufacturing process.”
In terms of the market segments that the company serves with its products the boundaries are very wide, with virtually no sector being left out. “Focusing on our main activity, products for the logistic sector, I can say that geographically the whole of Europe is very important, but that non EU markets are growing as well at a promising rate. We are not focused on growth in a specific market, but we are always looking at widening our sales network, so as to extend our commercial coverage. We plan to grow through organic expansion, although we never exclude that acquisitions could at some point appear on our horizon. We will continue with our current model, which has been successful, as despite a slight reduction of turnover due to the current economic climate, things are going quite well. We’ll continue to act on and improve all the elements which are within our control, Product Development, Quality, though cost optimisation and increasing productivity. A sector which I believe will offer us an opportunity for growth is that of alternative energy, to which we already offer components for many photovoltaic type of applications”
“More than 65 per cent of the material that we purchase and then process is steel, so suppliers of this are particularly important to us and our success. We continuously work with them in terms of product development, working for instance on new materials characteristics and innovative coatings.” 2013, in terms of order portfolio, was positive. Together with Luxembourg based Dematic, the company had won an important contract for the supply of the third Gucci platform in Switzerland. This €6 million order was one of the most important European contracts for 2013 in the field of warehouse logistics. n
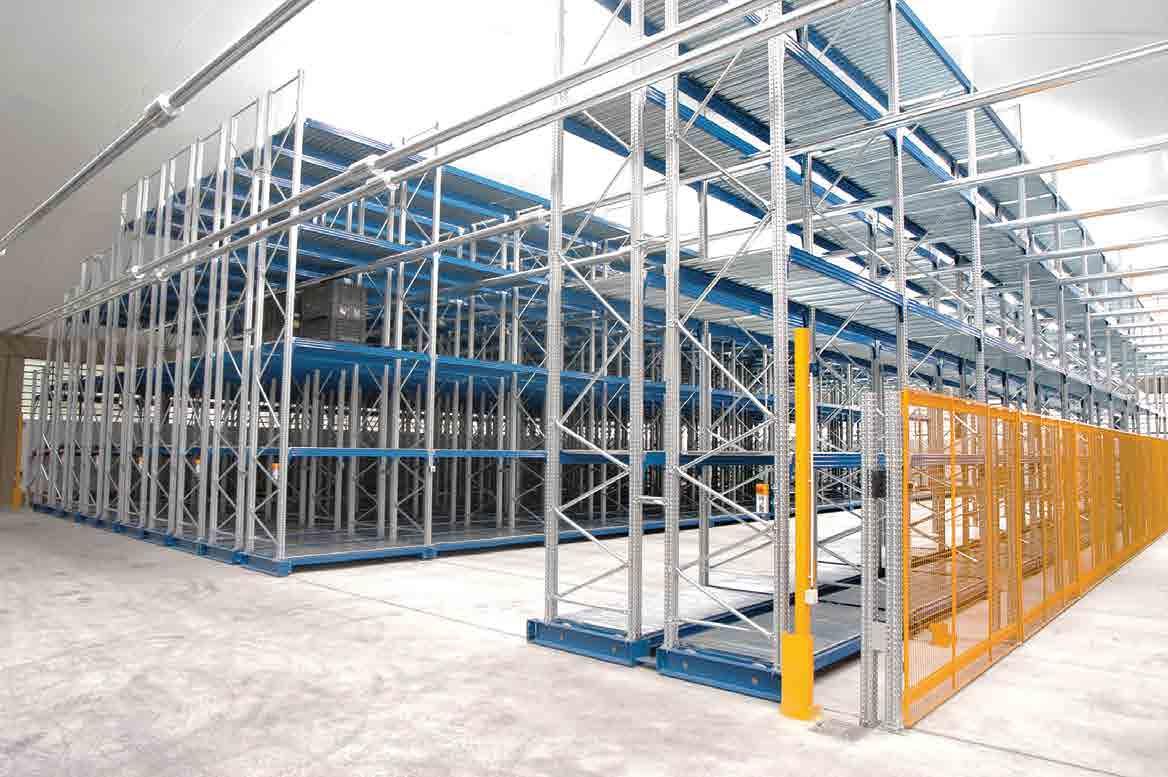
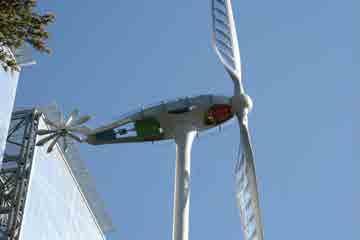
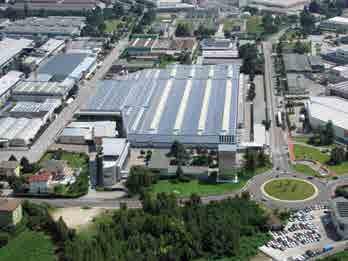
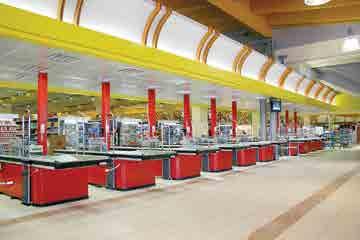
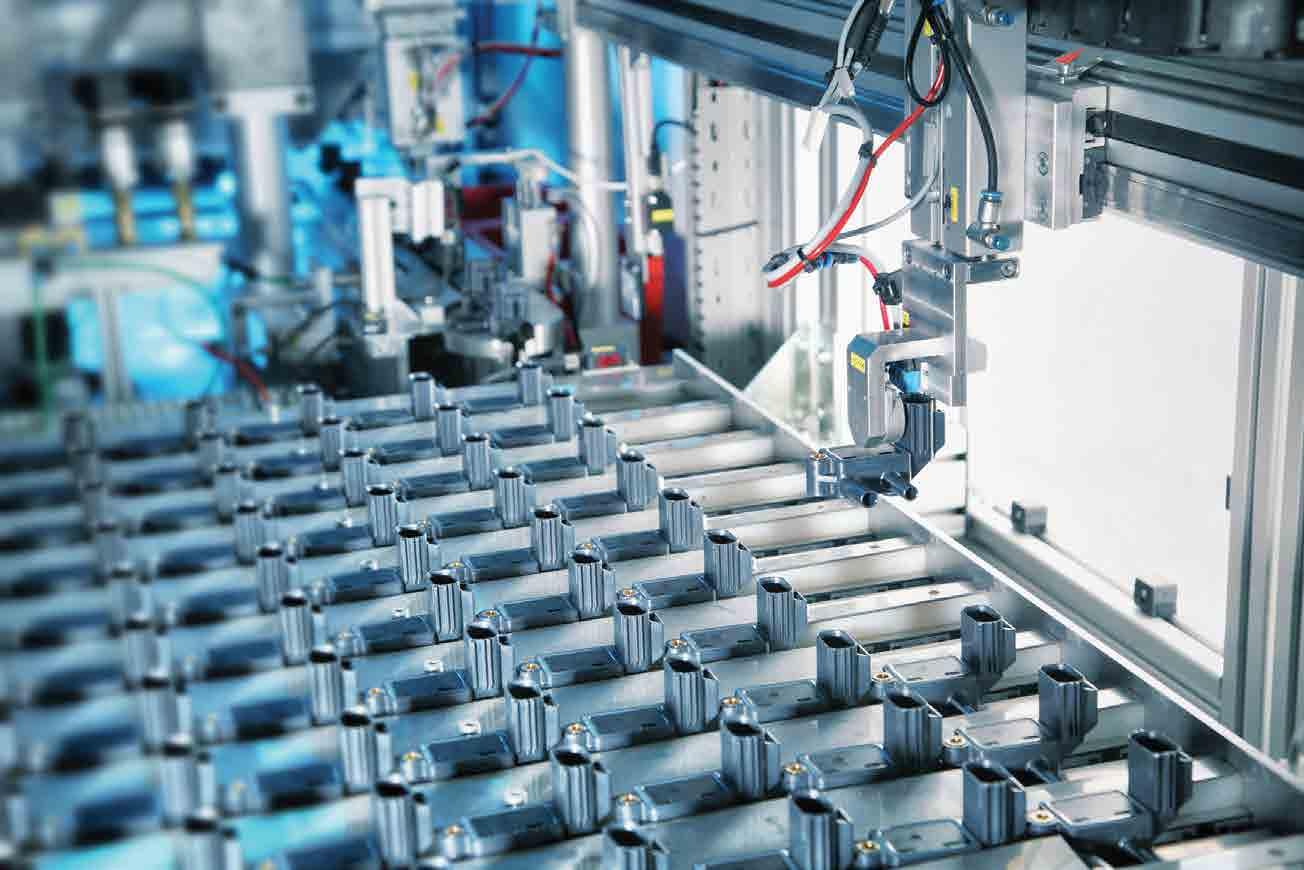
Kavlico Pressure Sensors is a global leading expert in the design and manufacture of high-precision pressure sensors and signal treatment technologies. The brand, belongs to the international company Custom Sensors & Technologies (CST) and specialises in applications involving harsh and hazardous environments. Philip Yorke talked to Horst Obermeier, managing director of Kavlico Pressure Sensors, about its latest ground-breaking products and move into new markets.
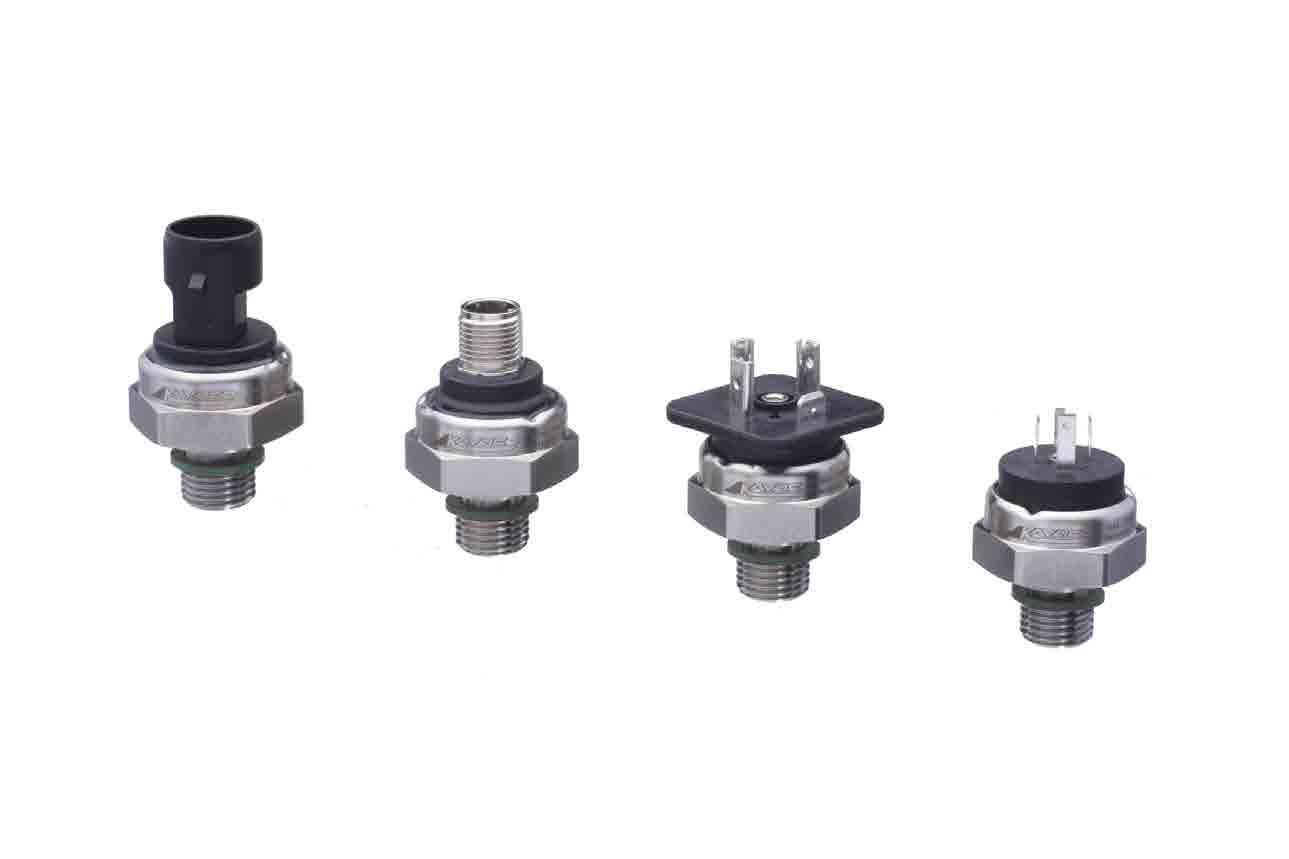
Kavlico Pressure Sensors’ history started with the foundation of Kavlico Corporation in 1958 by Fred Kavli, an entrepreneurial Norwegian immigrant living in North America. Kavli began by developing and producing innovative level-source sensors, transmitters and transducers. Consistent growth resulted in its move into speciality sensors and customised OEM products. Success in the US market led to the establishment of a European subsidiary in Minden, Germany in 1999 and to the implementation of an additional production facility in Tijuana, Mexico in 2008. More recently, China has been added to the list of countries with production and sales facilities for Kavlico’s advanced industrial sensors, in order to cover local customer needs. Over 1000 people are currently working for Kavlico Pressure Sensors.
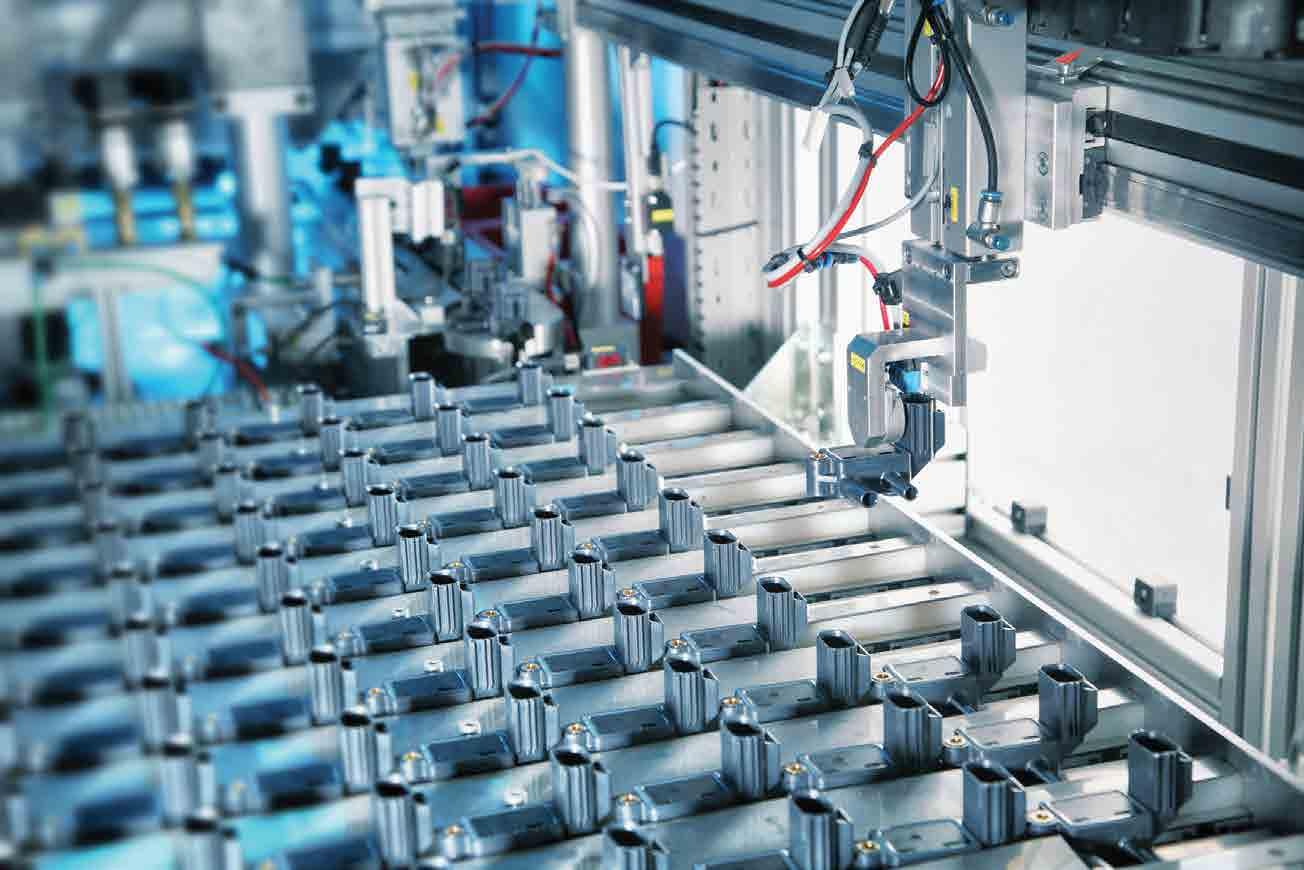
Crossing new sensor thresholds
Kavlico Pressure Sensors enjoys an unrivalled reputation for the development and manufacture of state-of-the-art pressure sensing and signal treatment equipment, based on three innovative sensing technologies: Ceramic capacitive, Silicon piezo-resitive (MEMS) and Stainless Steel thin film. Together they provide a unique combination that offers a flexibility that is ideally suited to meet its customers’ specific requirements for applications in the world’s harshest environments. The brand’s product portfolio is extensive and offers sensors starting at .0025 Bar(1”ofH2O), right up to 3000 Bar (45,000 psi). In addition to low, medium and high ranges and hermetically sealed or internally sealed products, Kavlico Pressure Sensors produces customised products for high or low volume production.
The brand’s biggest driver for growth is its ability to innovate across the board, resulting in the release of regular new product offerings. Recently these include its latest P/ PTE5000 modular sensor family for general industrial applications and its P994 range of ‘Digital I2C output signal’ products for the building automation market.
Currently Kavlico Pressure Sensors’ main focus is on construction and agricultural equipment, as well as trucks and buses, where it is a strong partner, providing reliable solutions to its customers worldwide.
Mr Obermeier said, “Today the trends in the market are the growing demand for greater flexibility and higher temperature ranges with sensors that work in extreme environments of 300°C or more. Year on year, the demands and expectations for sensor products increases. For example, 20 years ago low temperatures were considered to be between -20°C and -30°C, whereas now they are between -40°C and -60°C. Similarly, with high temperatures in the past of 125°C being acceptable, these now reach as high as 350°C (short term).
“In order to meet those requirements, we are looking at different technology ‘menus’ using silicon type sensing elements as well as developing new technologies based upon our standard ceramic solutions. This is in addition to our dual diaphragm sensors, designed for the world’s harshest environments.”
Mr Obermeier added, “We commit more than 5 per cent of our turnover to R&D, which keeps us at the forefront of the world’s sensor technology industry, and we project organic growth of between 4–5 per cent. However, we are also open to the possibility
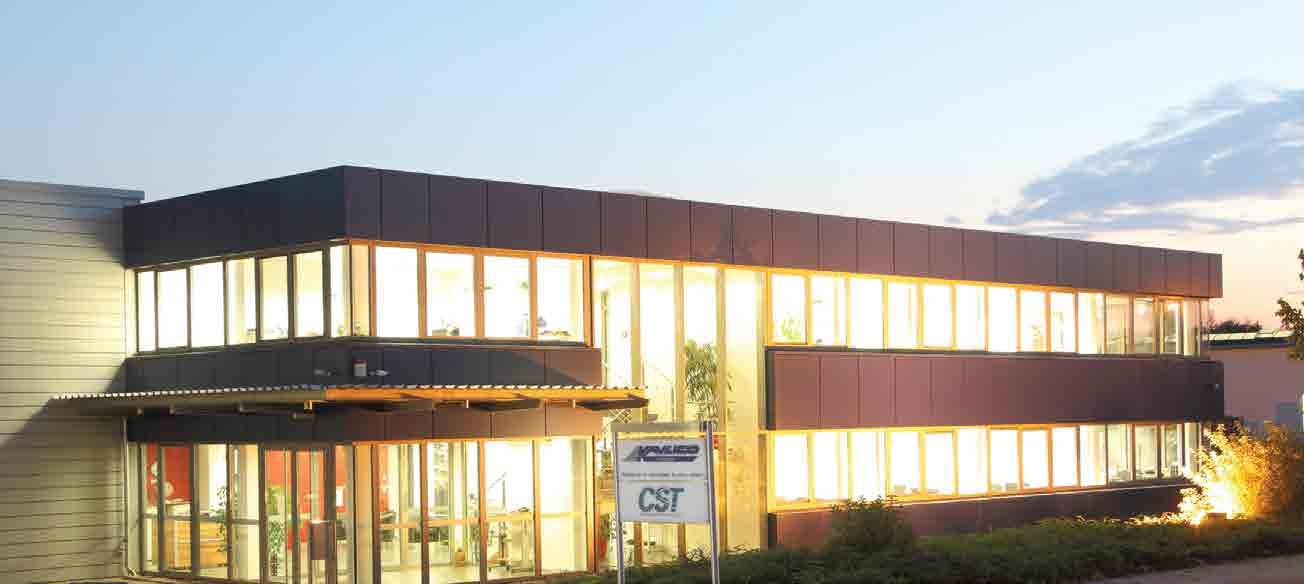
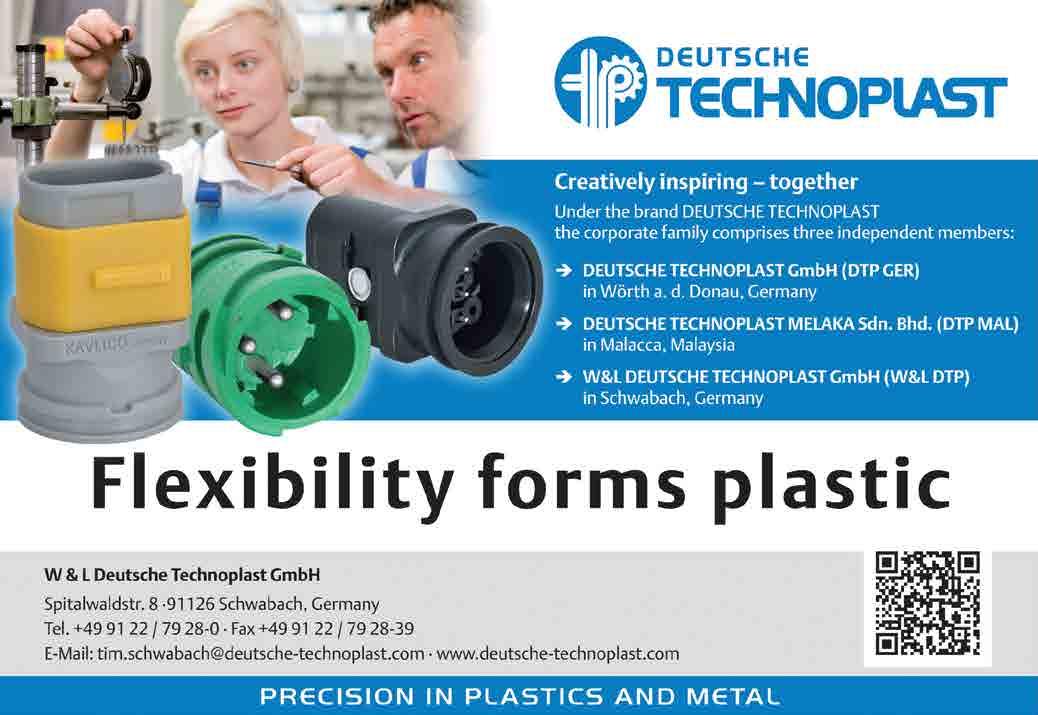

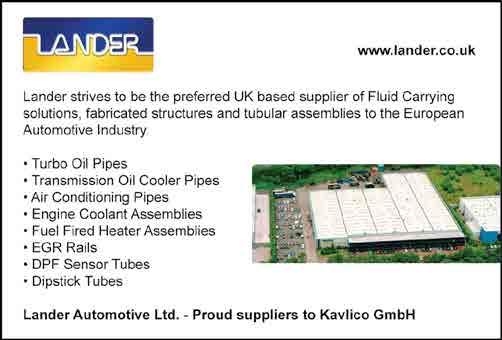
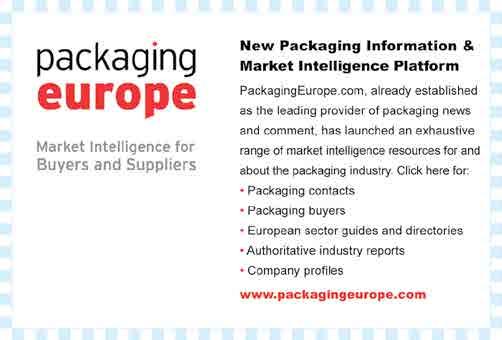