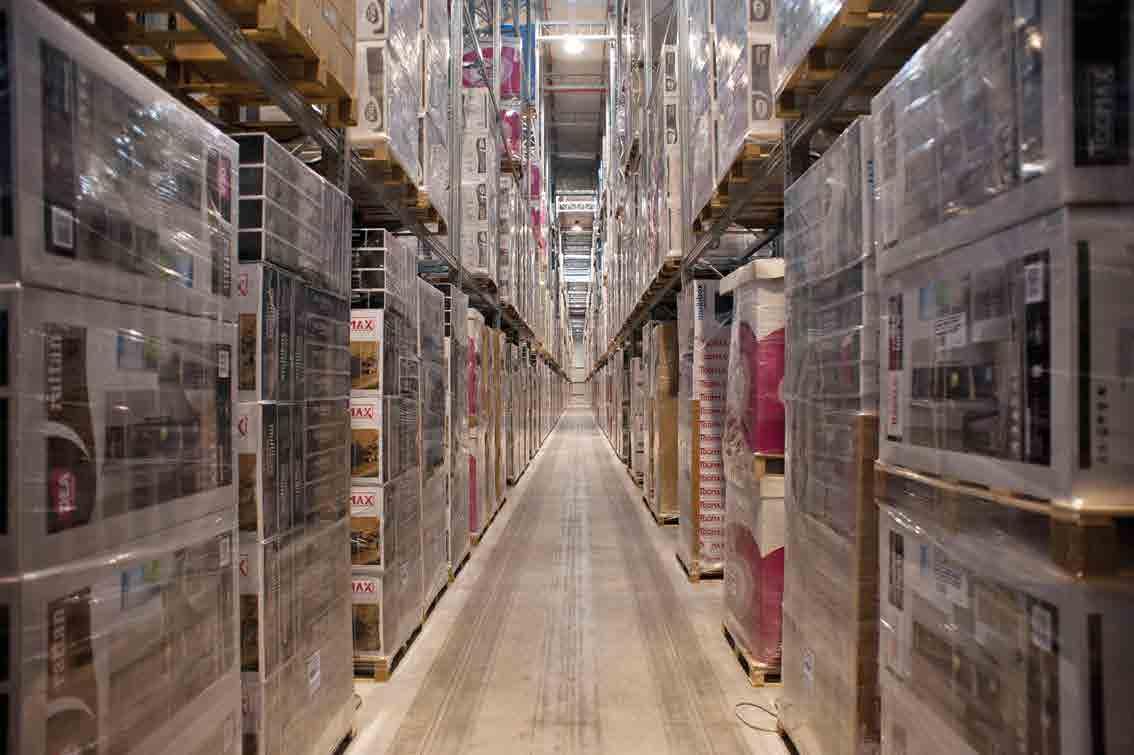
5 minute read
Clear advantage Ensinger

also sold in Russia, China and Latin America. “We have only entered the German market very recently, but we are doing extremely well there and we expect to further expand our presence.” For the mould division products the main markets are Italy and Germany, and to a lesser extent France.
“There seems to be a lot of demand for our standard products, which are all made in Italy. I think that this is due to the fact that our design style is appreciated. We have ten people dedicated to design, who are stylists and designers, as well as technicians engaged in the construction of the moulds through which we manufacture our range. Our team of highly qualified internal designers search for innovative solutions, with the aim of improving the production flow and the quality of our range, as well as for the development of new products. Modern software for flow analysis is employed in equipment design, with the aim of optimizing the filling of the mould and obtaining the best performance of the finished products.”
“We are planning to carry on in this way, as we believe that there is further scope for market growth. We have managed to
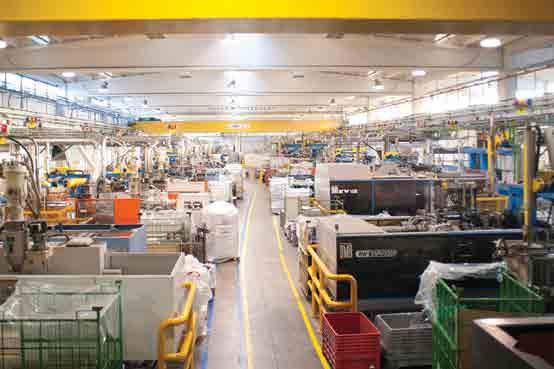

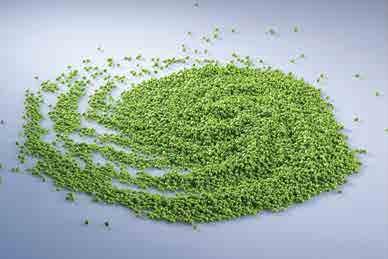
automate a lot and this allows us to be able to maintain good market prices. In the past we evolved so many times and we had to change direction every four to five years. Our way of working has allowed us to carry on. Currently we are experiencing a very good phase. The role of our style, of our design, is extremely important in our success, obviously accompanied by a good product quality. “
Does the success of the standard product division mean that the company will phase out the mould division? “No, we intend to keep the mould division alive, although currently demand for customised products of this type is suffering, due to the crisis affecting commissioning companies based in our area, the Marche region. We will carry on, strengthened by the success of our own-branded standard products. Large investments in research and development will continue, channelling €1.5 million in new product development on a yearly basis.” n

Founded in 1997, but with a twenty-year wealth of experience, today SIR operates from a fully equipped 20,000sqm site and can avail itself of cutting-edge facilities with a production capacity of up to 35,000 tonnes a year, to which must be added 25,000 tonnes of marketed products.
Thanks to continuous investments and partnership with its major partners, we can say that today SIR is one of the leading companies of its sector in Italy and is oriented towards continuous growth in foreign markets as well. Its winning formula is its ability to serve its customers by fulfilling any request, the close collaboration with its suppliers, the high quality of its products, the know-how accrued over the years, and the team of dynamic and motivated people working for the company.
With regard to production SIR manufactures its products to fulfil any need of its customers, finding the right balance between quality and price.
We regenerate and market plastic materials. Through the use of special machines and by adding additives and other materials, we produce a ready to mould product starting from selected discarded plastic.
SIR S.p.A - Via Provinciale, 41, 35010 Carmignano di Brenta – PD Tel: +39.049.5957542 - Fax: +39.049.5957021 - Website: www.sir-plastics.com Genreal e-mail: info@sir-plastics.com Commercial department: commerciale@sir-plastics.com Administration department: amministrazione@sir-plastics.com
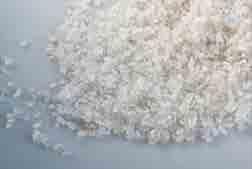
As part of the Poliblend Group, Esseti Plast GD Srl works in synergy with its sister companies to fulfi l customers’ needs by supplying a wide range of products: • Thermoplastic resins: Poliblend SpA • Thermoplastic rubber: Celloplast GD Srl • Coloured masterbatches and additives: Esseti Plast GD Srl
Thanks to its extensive sales network both in Italy and in the rest of the world, the Poliblend Group is an important player in its sector.
T: 0039 0331 837006, F: 0039 0331 831010 E: info@essetiplast.com, W: www.essetiplast.com
Wave Swiss is a world leader in automation, injection moulding machines for plastic materials, elastomer presses, thermoset presses, robots, peripherals and press accessories. Technologically at the cutting-edge and committed to environmental friendliness, Wave Swiss offers a quality service able to wholly fulfi l clients’ requirements.
Since 2012 the company has widened its production to the PET and Packaging sectors, making customised and made-to-measure products. Today it offers a comprehensive service, also dealing with the vertical production of auxiliary servo-systems, accessories and robots, in addition to its machines.
Quality standards of the highest level, a good positioning on the international market, technology and innovation are the factors which have made Wave Swiss a global benchmark in automation, injection moulding machines for plastic materials, elastomer presses, thermoset presses, robots, peripherals and press accessories.
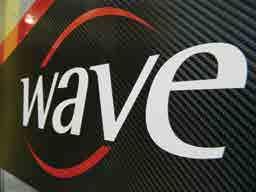
Wave Swiss is specialised in the design and manufacture of high-end machines and turn-key systems, customised according to clients’ requirements.
Wave Swiss makes full electric, hybrid and hydraulic presses for rubber, plastic and thermosetting materials, which alongside cutting-edge performances also score highly in terms of environmental friendliness and energy saving.
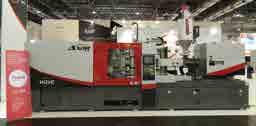
CLEAR ADVANTAGE
Ensinger is a global leader in the development and manufacture of advanced thermal insulation profiles for windows. Philip Yorke talked to Dr. Albert Lingens, the company’s sales director of the business unit Thermix® about its latest high-performance, ‘warm edge’ profiles and move into new markets.
View into the production
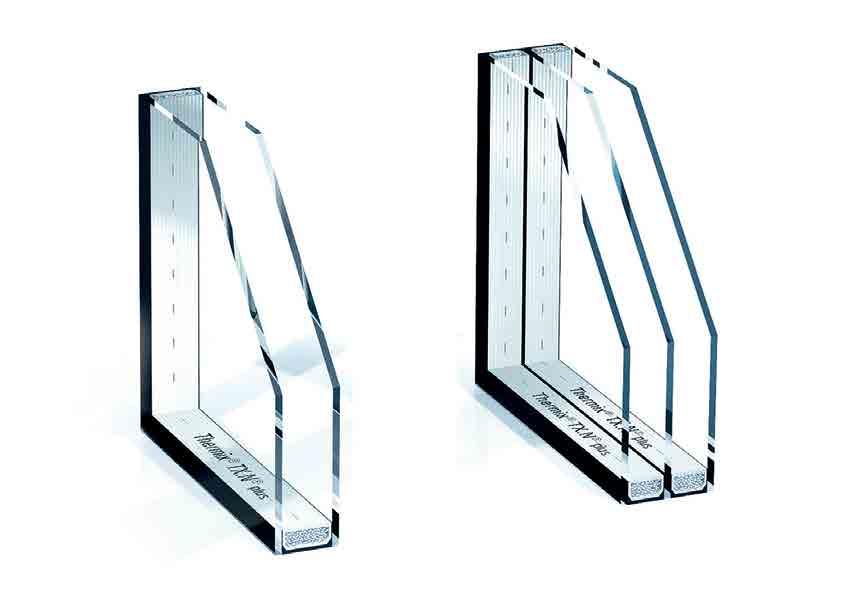
Application of Thermix spacers in triple glazed windows
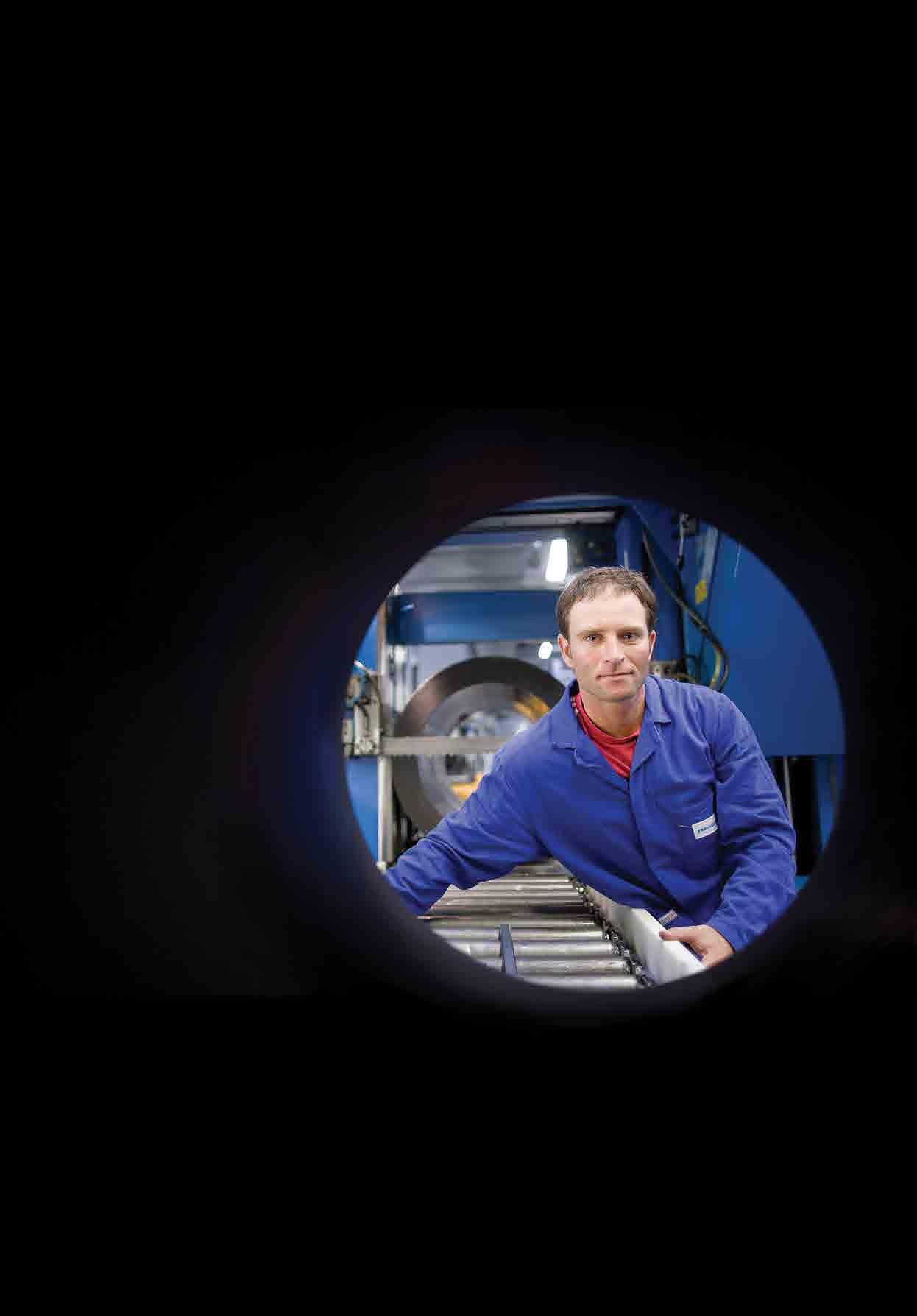
Application of Thermix spacers in double glazed windows
