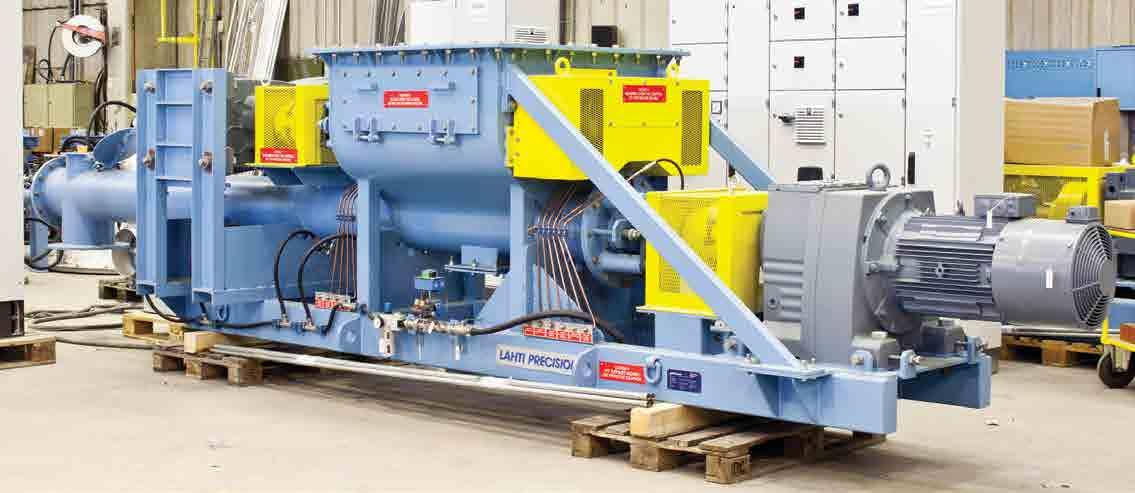
7 minute read
Design is the secret Plastmeccanica
products has played a key role in its successful history.
Mr Sopanen continued, “Accuracy is everything. It’s what Lahti stands for and has done for 100 years. We continually upgrade and innovate so customers can be sure that they are always getting the best dosing, weighing and scales. We offer strong mixing technology, automation and electrification so that the whole supply chain adds value for our customers.”
Total control
With the ability to provide the full service operation from its own facilities in Finland, Lahti Precision can be sure that its commitment to accuracy is maintained. Mr Sopanen explained, “It is imperative that we undertake all the operations ourselves; from tendering to the end of life cycle of the plant, Lahti takes care of everything.”
As one of the world’s leading suppliers of glass batch and mortar weighing plants, and the market leader in the weighing business in Finland, Lahti Precision is globally active. Expanding worldwide wherever its core market segments of glass, dry mix and other industries demanding accurate weighing and dosing are present, the company sees a great many opportunities for growth. Mr Sopanen said, “Even though we are 100 years’ old we are still very light on our feet! We seek out interesting opportunities and we keep focused on our core markets to see where our products and services will add value to new customers’ processes.”
Having experienced different phases of growth throughout its century as the market leading global technology company supplying accurate weighing and dosing systems and plants, scales and maintenance services to the process industry, Lahti Precision’s last two years have been especially innovative in terms of its product portfolio. Mr Sopanen explained, “We’ve always been innovative and always looked forward to how we can further improve our offer. In the two years since we last spoke to Industry Europe we’ve really invested heavily in improving our core equipment, we’ve been more focused on our mixing technology and we’ve put effort to manufacture a new dry mix and glass mixers, which have been very well received on the market.”
An accurate partner
As an innovative, reliable company that works as a true partner with its customers worldwide, Lahti Precision is both looking forward to celebrating its 100th birthday in 2014 and to its next chapter. With long-term co-operations with well-known customers including NSG, Saudi Arabia’s Saveto and HESS from Nederland, the company is confident about its future.
Mr Sopanen concluded, “We are proud of our past as it gives us a very strong foundation from which to grow. But we’re not satisfied. Lahti Precision is always looking for new developments in processes, new equipment to add value to our customers’ businesses and new market opportunities. We’re here to deliver accurate results for our customers, now and for the next 100 years!” n

ALLGAIER PROCESS TECHNOLOGY
Every day, the Allgaier Process Technology division takes a new approach to the complex requirements of the market. With its core brands of Allgaier, Mogensen, Gosag and Mozer as well as a global presence in more than 30 countries, this division delivers both standardized and individually produced sytems for washing, drying, cooling, screening and sorting for the bulk solids processing industry.
Based on experience of more than 20,000 test series and countless successfully realised international projects with over 8000 customers, Allgaier Process Technology division offers tailor-made systems for the processing industry in a wide variety of sectors such as chemicals and pharmaceuticals, food and feed, waste and recycling, mining and metallurgy as well as biofuels, wood, ceramics, plastics, crude and manufactured minerals.
In industrial preparation and processing of substances of extremely diverse types, the factors that really matter are the quality of the screening material, the choice of screening method and the technology of the screening machine. Allgaier offers a wide range of modern and high-quality classifier machines with a wide range of variants.
Allgaier has the appropriate solution for each task. Tumbler screening machines meet the most exacting quality requirements in ultrafine screening, while flat gyratory screens in the wood processing industry offer convincing performance and Mogensen sizers are characterised by robustness and a high throughput rate.
Allgaier also offers its customers dryer systems based on the fundamental principles of rotating drum dryers as well as fluidized bed technology. The drying technology product portfolio includes complete solutions which take the various drying processes as well as processes for cooling and calcining, and rationally link them together with granulating and screening technologies. The ‘MOZER® System’ rotating drum dryer is regarded as a classic industrial drying product; it was developed several decades ago and has been continuously optimised ever since.
The communication of knowledge in the best sense of the concept takes place in the Technical Centre at the headquarters near by Stuttgart, Germany. This is where Allgaier carries out series of scientific experiments and practical tests in order to arrive at madeto-measure solutions for customers all over the world. The insights are made available for use by all subsidiaries and agencies of the Allgaier-Group.
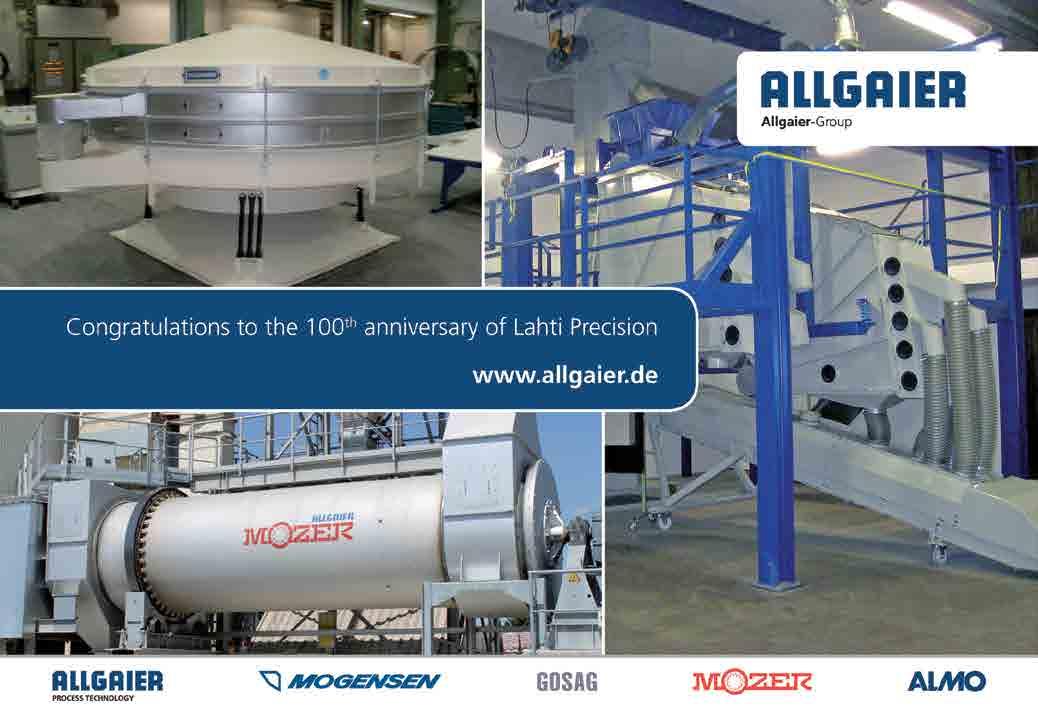
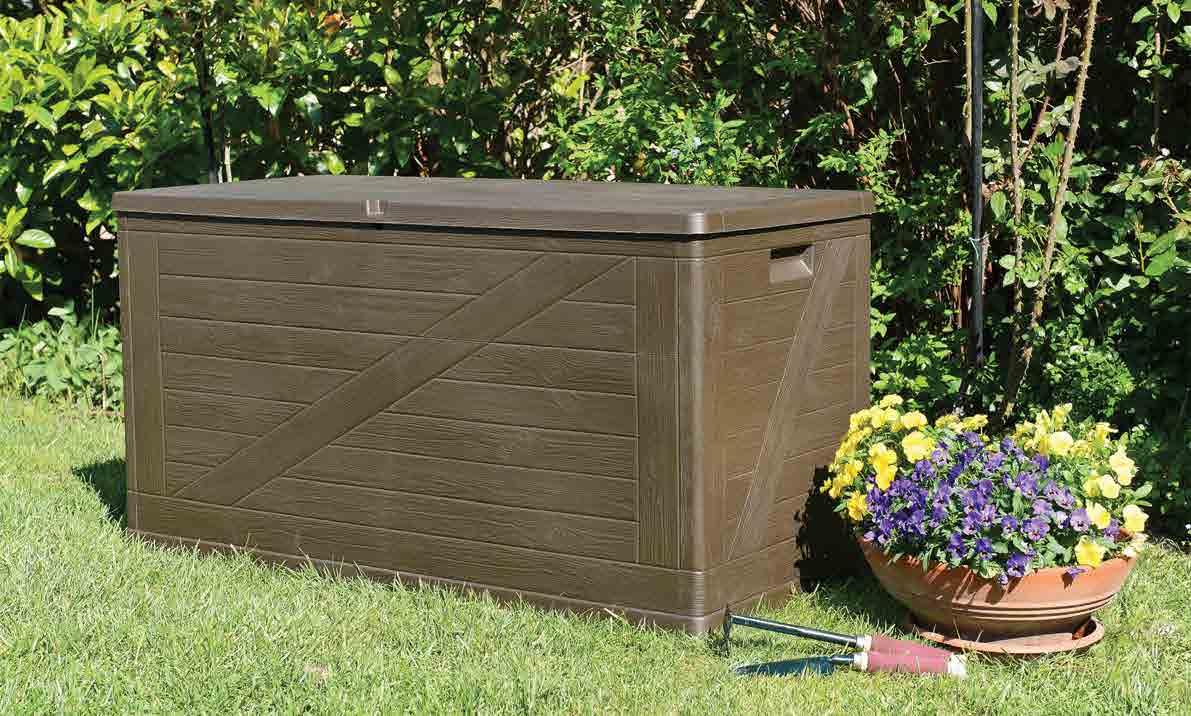
DESIGN IS THE SECRET
A leading manufacturer of stylish household goods and furnishings sold all over Europe, Plastmeccanica SpA is experiencing remarkable success, despite the current Italian and European economic situation. Its secret? Its appealing design, as Barbara Rossi is told by the company’s CEO, Mr Ezio Betti.
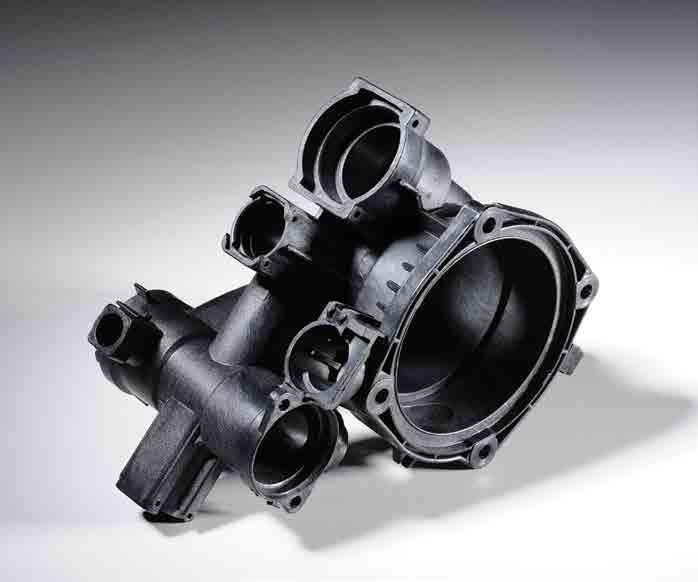
Plastmeccanica which has a turnover of about €35million and holds all relevant European certifications - started its activity at the end of the eighties. At the time it manufactured moulds and moulded products for third parties, according to their specifications. It then acquired a producer of household products. This was the starting point for its own work as a manufacturer of own- branded standard products. The nineties saw further product evolution, with the company improving quality, becoming involved in design and conducting market research.
Today 70 per cent of turnover derives from household goods and furnishing products, marketed under own brands, while the
remainder (30 per cent) is generated by contract manufacturing of moulds and accessories, mainly for the automotive and household appliance sectors. Household goods and furnishing products are commercialised under two different brands: Dea Home and Toomax. Dea Home deals with household products, while Toomax offers a DIY range, including cabinets, shelves and items for the garden. Within each of the two brands there are two product levels - a more sophisticated and a more standard range, differentiated in terms of colours and some other fine details.
“We are continuously engaged in developing new ideas. We participate in the Frankfurt fair every year, presenting new products. These are based on the work of our designers, who constantly develop new designs. The moulds through which the products are manufactured are all developed and constructed internally. Both Dea Home and Toomax products are commercialised throughout Europe using large retailers, including Adeo, Obi, Kingfisher and Bauhaus. Some of these retailers will deal with both brands, while others will concentrate on one of them” says Mr Betti.
In terms of production, the company operates from a single large site based in the Ancona area of central Italy. This site has a covered area of 27,000m2 and here the company has recently built a new, fully automated 5,000m2 warehouse. “We are increasingly moving towards automation and I have to say that we are doing very well, as we currently run three shifts a day, often at weekends as well.” The company has acquired new land for a possible site expansion, in order to house larger machinery, although the current facilities are able to accommodate any expected potential future growth. Recently investments were made in the new automated warehouse, as well as in new machinery and automation.
Our market is Europe
The standard products of the two previously mentioned brands are the motor for current growth and will also involve an increase in terms of human resources, while the mould division is growing at a slower rate. As mentioned, Europe is the main geographical market, in particular Italy (generating about 40 per cent of turnover), Germany, the UK, France, Spain and Greece; although in lower volumes own-branded standard products are
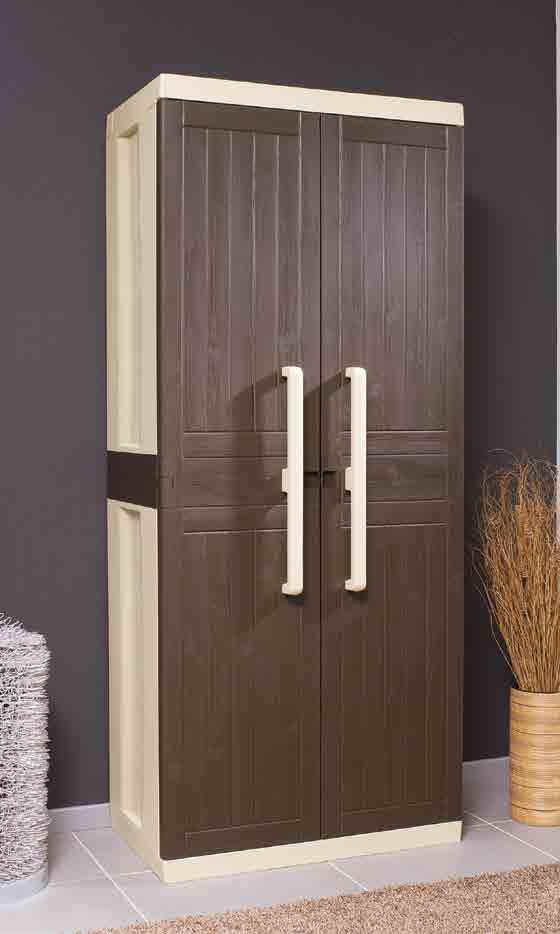
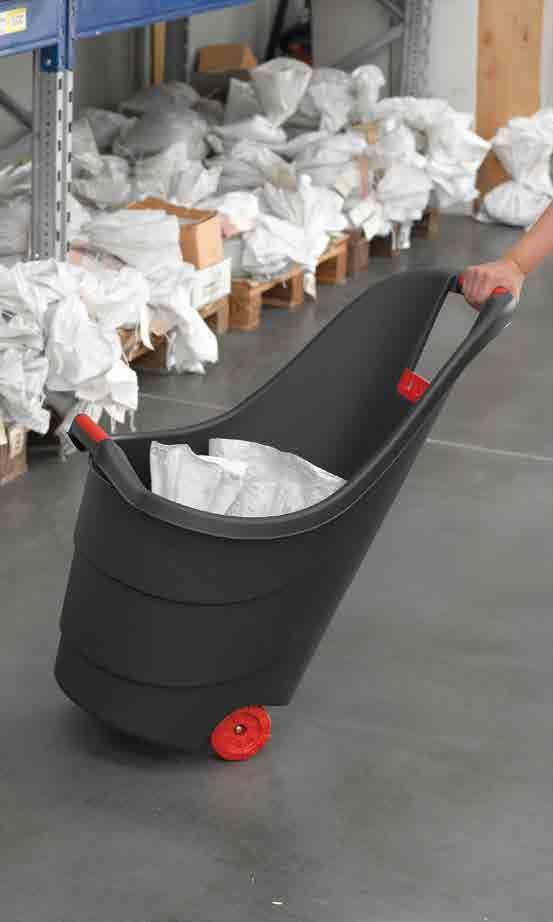