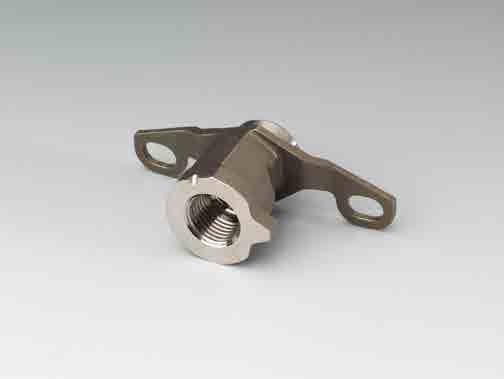
3 minute read
Technology spotlight Advances in technology
NEWS
TECHNOLOGYSPOTLIGHT
Advances in technology across industry
MTU Aero Engines produces parts by additive manufacturing Morgan Advanced
Munich-based MTU Aero Engines has produced components for production engines – borescope bosses for the PurePower® PW1100G-JM engine, the Pratt & Whitney engine to power the A320neo – using selective laser melting, or SLM.
The low-pressure turbine for the PW1100GJM geared turbofan (GTF) engine will be the first turbine ever to come equipped with borescope bosses produced by additive manufacturing processes. The bosses form part of the turbine case and allow the blading to be inspected at specified intervals for wear and damage using a borescope.
“We used to make these parts by casting or by milling them from the solid,” explains chief operating officer Dr Rainer Martens. “Now they are being manufactured by SLM. With this technique, the first step is to slice up a 3D CAD model of the component to be produced. A laser then builds up the solid equivalent of the model layer by layer from a powdered material, the layer thickness being 20 to 40 micrometers. The powder particles are locally melted and fused together.” The processes allow complex components that are extremely difficult, if not impossible to manufacture using conventional methods to be produced with only small amounts of material and few tools. The technology opens the door to entirely new designs, appreciably cuts development, production and lead times, and brings down production costs. Visit: www.mtu.de
Borescope boss for the PurePower® PW1100G-JM, the engine to power the A320neo. It’s part of the turbine case.
Biofore Concept Car drives sustainable change Materials develops armoured composite crew compartment
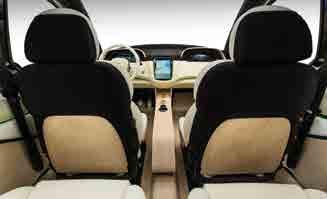
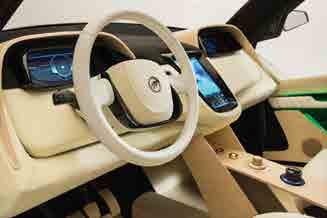
Morgan Advanced Materials, through its Composites & Defence Systems business, has drawn on its extensive materials and engineering expertise to design and develop a bespoke armoured composite crew compartment for Tata Motors’ Light Armoured Multipurpose Vehicle (LAMV) programme for the Indian Ministry of Defence.
The LAMV incorporates crew protection based upon Morgan’s bespoke composite and ceramic ‘pod’ technology, which has been developed over the past 20 years. The pod creates a detachable, blast and ballistic-resistant crew compartment, which was easily integrated onto the Tata-produced chassis and can be modified to provide higher levels of protection as and when required. The Morgan composite and ceramic ‘pod’ provided a weight saving in excess of 1000kg, making it less than half the weight of a similarly protected steel structure. www.morganadvancedmaterials.com/products/ composites-defence-systems/
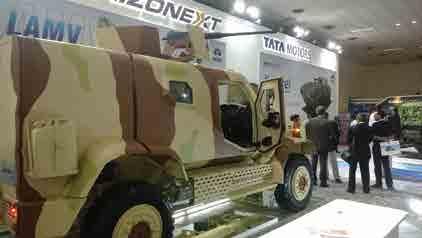
The Biofore Concept Car showcases the use of UPM’s innovative biomaterials in the automotive industry. The majority of parts traditionally made from plastics are replaced with high quality, safe and durable biomaterials, UPM Formi and UPM Grada, which can significantly improve the overall environmental performance of car manufacturing. The Biofore Concept Car is designed and manufactured by students from the Helsinki Metropolia University of Applied Sciences.
Parts made of UPM Grada thermoformable wood material are the passenger compartment floor, centre console, display panel cover and door panels. Grada technology revitalises the forming of wood with heat and pressure, and opens up new opportunities for designs not achievable with traditional methods.
Parts made of UPM Formi biocomposite include front mask, side skirts, dashboard, door panels and interior panels. UPM Formi is a durable, high quality biocomposite for injection moulding, extrusion and thermoforming production.
The vehicle runs on UPM’s wood-based renewable diesel UPM BioVerno, which will significantly reduce greenhouse gas emissions compared to fossil fuels.
“The Biofore Concept Car showcases the potential of UPM’s biomaterials not only for the automotive industry, but also for various other enduses including design, acoustics – a wide range of industrial and consumer applications. The possibilities are endless,” says Elisa Nilsson, vice-president of Brand and Communications at UPM. www.bioforeconceptcar.upm.com
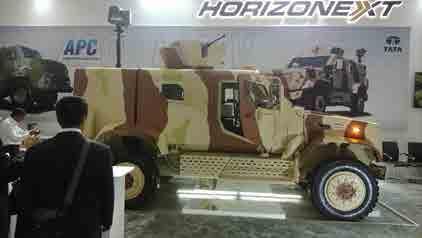