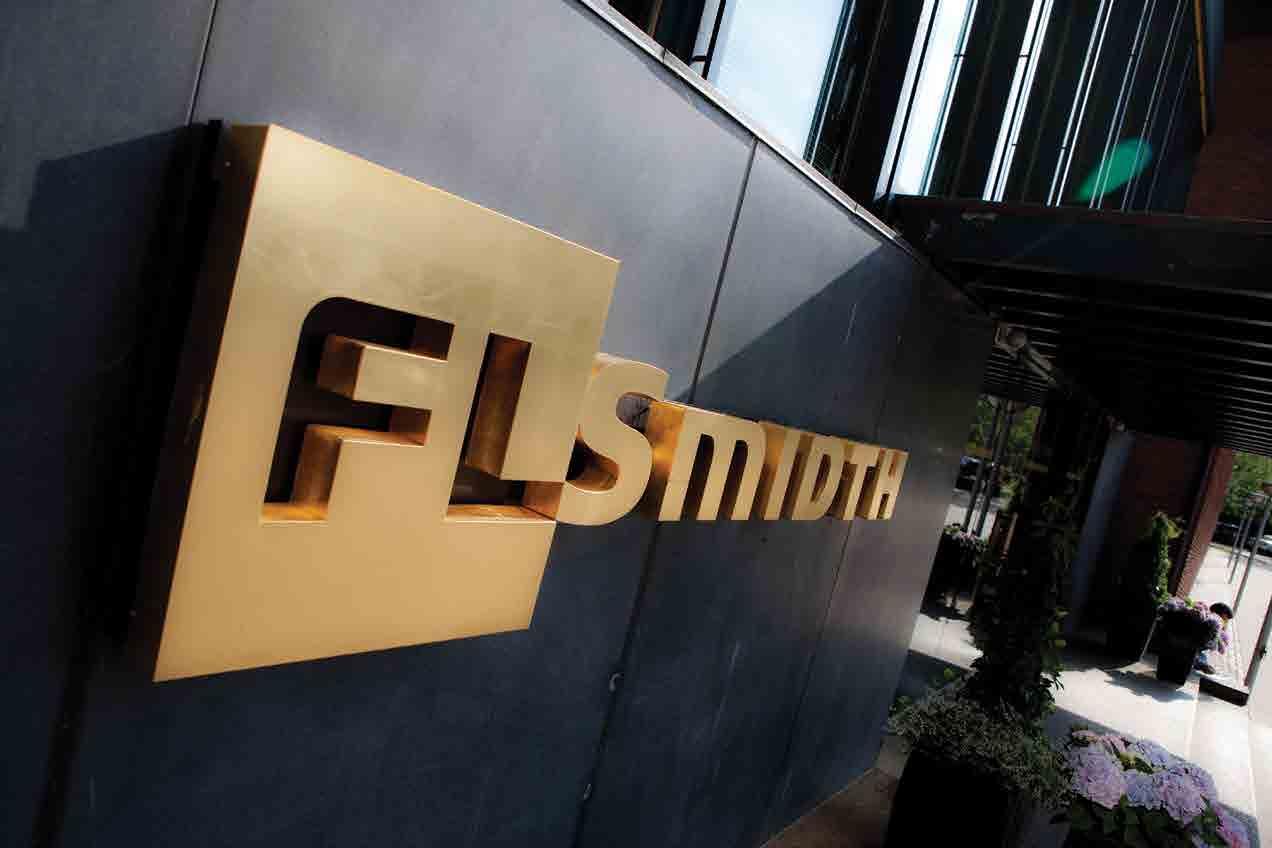
10 minute read
The full service provider FL Smith
THE FULL SERVICE PROVIDER
FLSmidth is a leader in the supply of equipment and services to the global cement and minerals industries. Peter Mercer reports on the company’s success in leveraging its expertise in cement technology into minerals processing and its fast-growing customer services business.
FLSmidth won its first contract for a cement plant, near Limhamm in Sweden, in 1887. Today the Danish company supplies the cement and minerals industries globally with engineering, single machines and complete processing plants as well as comprehensive maintenance and support services that range up to the complete operation of customers’ processing facilities. FLSmidth currently offers its full service solutions in six core focus industries: cement, coal, iron ore, copper, gold and fertilisers; its technologies and services range from material handling in the quarry through the entire processing operations of the end product.
Headquartered at Valby, near Copenhagen, a site it moved to in 1956, FLSmidth today employs more than 15,000 people all over the world and had revenues in 2013 of €3.6bn.
Until the later part of the 20th century the company was focused on designing and producing machinery for the cement industry. It introduced the coal-fired rotary kiln to the European market at the end of the 19th century – an innovation from the USA that revolutionised cement production – and by the 1950s FLSmidth machinery was used in 40 per cent of all cement production in the entire world. In the following years the company continued to introduce new machines and processes that reinforced its position as a technology leader in the industry, including the ATOX vertical mill, which combined the grinding, separation and drying processes into a single unit. Since the 1980s FLSmidth has sold more than 300 ATOX mills.
Refocusing and expansion
Then, following the economic recession of the 1980s, FLSmidth began to diversify into a number of other businesses until it had grown into a Group of some 125 companies in which two thirds of sales were in non-core activities. However at the beginning of the 21st century it was decided to dispose of the Group’s non-strategic interests and refocus on the development and production of equipment, production plants, systems and services for the global cement and minerals industries. This return to the company’s roots was marked in 2006 when it was awarded a contract by Holcim to supply the world’s biggest cement production line at Ste Genevieve, Missouri, in the USA.
At the same time the company began a series of strategic acquisitions that would enable it to expand its services into the minerals industries. Perhaps the most important of these was the acquisition in 2007 of the process division of the Canadian company GL&V, consisting of Dorr-Oliver Eimco and Krebs Engineers. The expertise in separation equipment for the metals and minerals industries that this purchase brought to the Group enabled FLSmidth to offer customers
the entire flow sheet of a typical minerals plant, from raw material extraction to the final end product.
“Our strategy is to be the leading singlesource supplier in all the industries we serve,” explains President of the Cement Division Per Mejnert Kristensen. “We have built up this position in the cement industry over many years and, thanks to our strategy of key acquisitions, we can now offer the minerals industry the same complete service. In fact today around one third of our business is in the cement industry and two thirds in industries such as copper, gold, iron ore and coal.
“This is vital to our continuing success since the cement industry typically experiences booms and downturns over cycles of six to eight years; so by leveraging our experience and technological expertise in cement equipment and plants, we can smooth out the market fluctuations. This expansion was reinforced by the global branding strategy that we adopted in 2009 – ‘One Company – One Name – One Source’ – highlighting our position as a supplier of the whole value chain to both the cement and the minerals processing industries. So customers in the copper industry, for example, can now source from us everything they need for the complete processing operation – equipment for crushing, grinding, filtration, flotation, material handling, screening, thickening and even for sampling and on-line analysis.”
Core cement competence
All of this market expansion has, of course, been made possible by FLSmidth’s experience over more than 130 years in undertaking large and small cement plant design and construction around the world. Over the last eight years the company has delivered more than 100 plants in Europe, Asia and Africa alone. Its ‘One Source’ strategy enables it to offer customers everything from process design and project management to equipment supply and commissioning, even including training for the operators who will run the plant.
Recent projects for the global cement industry have included a complete new 6,000 tonnes per day production unit near Benin City in Nigeria. The contract between FLSmidth and BUA International, the owner of local cement producer EDO, included mechanical and electrical engineering, equipment supply and sea transport, supervision of installation and commissioning and the training of staff. The complete package of FLSmidth machinery supplied included EV crushers for limestone and laterite, an ATOX 50 raw mill, a five stage in-line calciner preheater and two support kilns, a Cross-Bar clinker cooler, UMS cement mills and four packing plants.
And when Russia needed to produce more cement in the run-up to this year’s Winter Olympics, FLSmidth helped to dramatically increase capacity at the JSC Verkhnebakansky cement plant, which is located east of the Crimean peninsula. The project involved creating a new production line alongside the existing small line without disrupting current production. FLSmidth developed an energy-efficient solution using the latest technology and supplied all the machinery for the plant as well as a stateof-the-art laboratory and control systems, including a RoboLab industrial robot. The company supplied a total of 4,900 tonnes
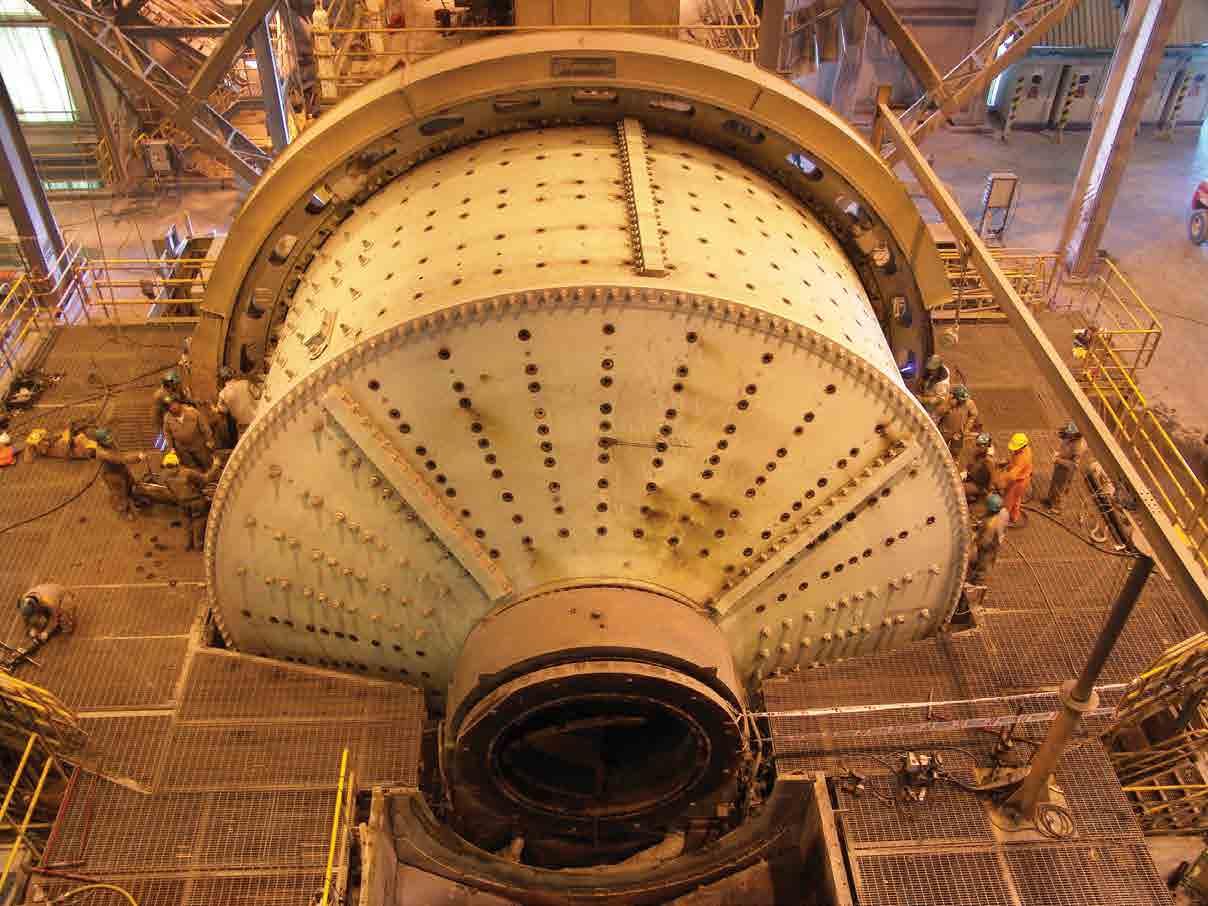
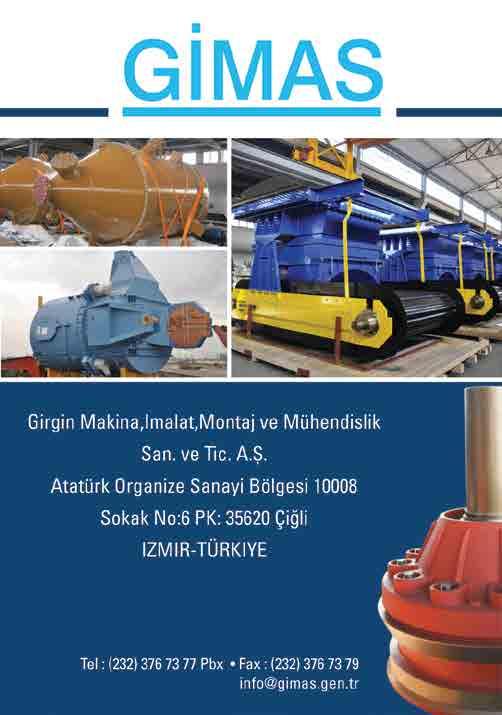

of key equipment and developed the documentation for manufacturing and the specifications for purchasing the remaining 13,000 tonnes. The new line has a capacity of 6,200 tonnes of clinker per day, making it the largest dry cement plant in Russia. It features one of the largest ATOX mills FLSmidth has supplied. During construction the old line never stopped production and, in fact, cement produced by it was used in the construction of the new line.
Cutting edge technology
In all its business areas FLSmidth leads the way in improving environmental protection through cutting edge technology and optimised product manufacturing, fabrication and installation.
“Our R&D activities are a huge part of the business we carry out in-house and our Dania R&D Centre in Denmark is the largest facility of its kind in the industry,” says Per Mejnert Kristensen, “Cement production is, of course, extremely energy intensive so a lot of our work in recent years has been in improving energy efficiency but we are also putting a lot of effort into reducing emissions. Our HOTDISC combustion system was introduced 14 years ago but it remains a highly effective process for burning alternative fuels in a controlled and environmentally-friendly manner. It can burn all forms of solid waste, from sludge or grains to huge used tyres or large pieces of timber such as old telephone poles and so turns otherwise useless and environmentally challenging solid waste into useful energy in a completely safe and economical way. Many new cement plants today are equipped with this technology.”
FLSmidth is also an industry leader in the development of air pollution technology and offers a wide range of solutions to reduce particulate matter and gaseous emissions. With more than 8,000 systems installed worldwide, the company is a one-stop source for helping customers comply with environmental regulations all the way through from project development to after-sale services. FLSmidth is also leading the way in waste heat recovery systems. Its Kalina Cycle technology is a unique system that uses a binary working fluid of ammonia and water to achieve improved heat transfer and higher efficiency. The system is ideally suited to the waste gas streams of the pre-heater and clinker cooler vent of a cement plant.
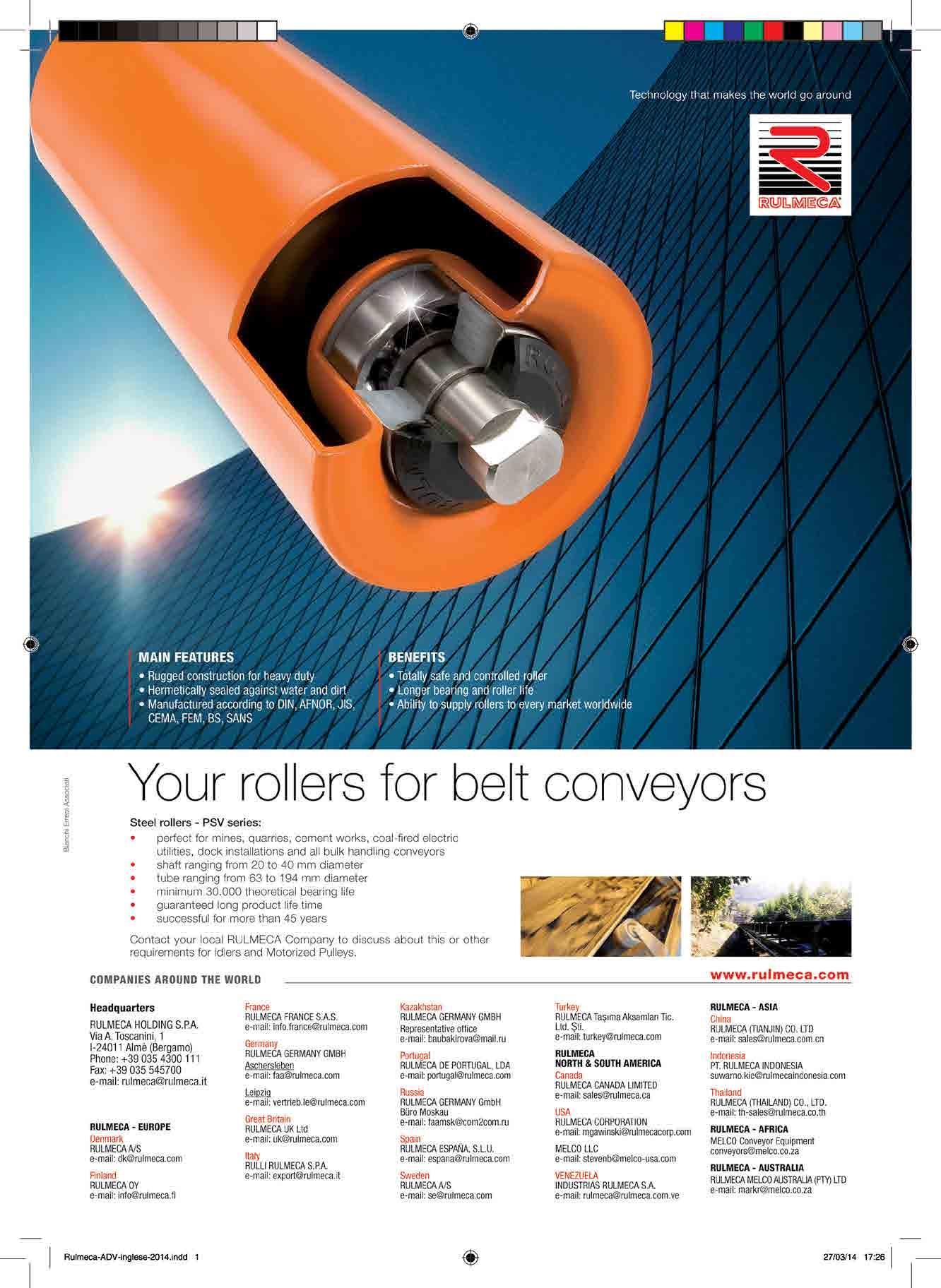
Expanding services
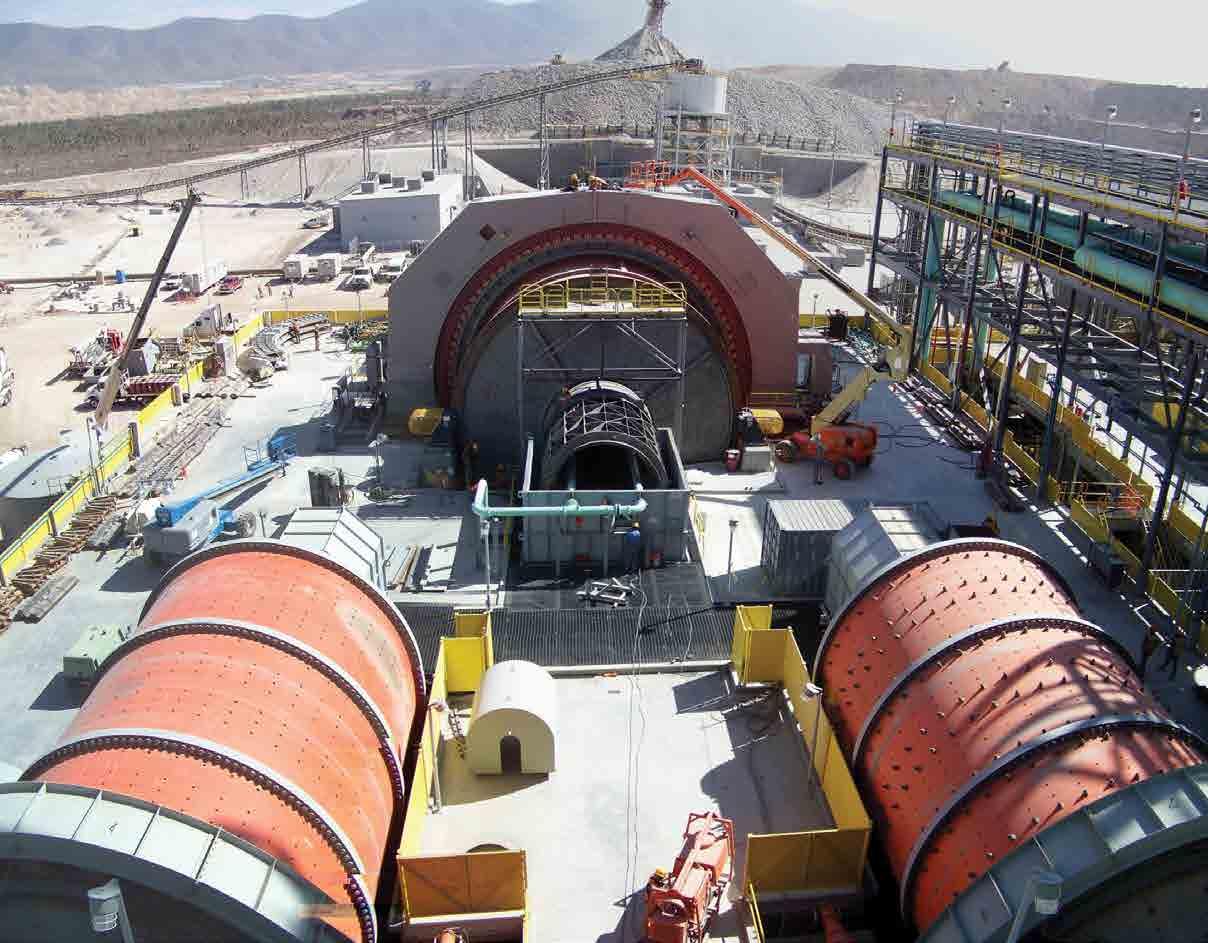
In 2010 FLSmidth won three major contracts for the complete operation and maintenance (O&M) of customers’ cement plants. At the time this was a new line of business which involved taking on the complete responsibility for staffing, equipment maintenance and spare parts and technical support for an agreed time span and within agreed production targets.
“Our O&M operations have seen huge growth in the last four years,” says Mr Kristensen. “FLSmidth has more than 100 years’ experience in designing, manufacturing and installing cement plants all over the world as well as in servicing these plants and supplying spare parts. But now we are increasingly involved in taking over the operation and maintenance of cement plants as well and we are extending our O&M business into the minerals industry too.”
“In effect we agree to take over the operation of our customer’s plant, guaranteeing output levels for an agreed price per tonne so the customer is only charged if we perform. By turning fixed costs into performance-linked variable costs, O&M offers our customers an attractive business solution and it helps us to smooth out the cyclical variations in the capital side of our business. The demand for complete new cement or minerals plants may go up and down over the years but existing plants need to be operated and maintained all the time.”
Today long-term O&M contracts are showing significant growth potential in all six of FLSmidth’s focus industries, an important development since copper and gold have already joined cement as the company’s most important industries overall. A further step in this strategy was taken in 2012 with the acquisition of Ludowici, the Australian specialist in coal centrifuges and vibrating screens for the minerals industries. This move has given FLSmidth the strategic capability to offer a complete coal preparation flowsheet and significantly boosted its programme to further expand its vital Customer Services business.
Old and new customers
“We are very excited about the growth opportunities in our Customer Services division, particularly in O&M contracts, but we are still very active in capital projects all over the world,” says Per Mejnert Kristensen. “We have long-standing relationships with many customers for whom we continue to deliver new and more efficient plants and we are also winning new orders in fast-developing regions such as the Middle East and Africa.”
The Indonesian cement producer PT Semen Gresik, for example, is a well-known customer; cooperation between the two companies goes back to 1910 and the commissioning of PT Semen Padang’s first cement production line. The latest order, the fifth from the Indonesian company, came as recently as February of this year – following another order only two months previously – and is for a €42m greenfield cement plant in Central Java. Equipment for the new plant includes a raw mill, coal mill, preheater, kiln, burner, clinker cooler and silo equipment as well as a complete control system for the entire plant.
By comparison, Qatari cement producer Al Khalij Cement is a relatively new customer, although FLSmidth has already supplied it with a cement plant in 2007. In December 2013 came a follow-up order for a duplicate cement production line for Al Khalij’s plant 100km east of Doha. This line is being supplied in cooperation with China’s CNBM International Engineering, which is the turnkey contractor for the project; FLSmidth’s role is to engineer the plant and supply the main equipment, which includes conveyor transport systems, mills, a complete pyro line and electrical and automation systems.
“The FLSmidth and CNBM offering combines environmentally cutting-edge process know-how, engineering and equipment supply from FLSmidth with a cost-effective EPC contract,” says Per Mejnert Kristensen. “Together we can offer the customer the best of both worlds.” n