
5 minute read
The spirit of the air Wolf Anlagen
THE SPIRIT OF AIR THE SPIRIT OF AIR
Air technology is at the heart of WOLF Anlagen Technik – as it connects the business divisions of Surface Engineering, HVAC and Agricultural Engineering. Julia Snow spoke to CEO Siegfried Vogl-Wolf to find out about all three.
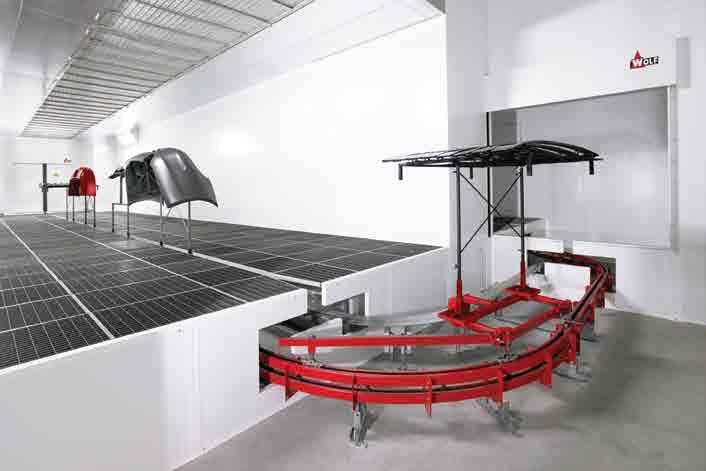
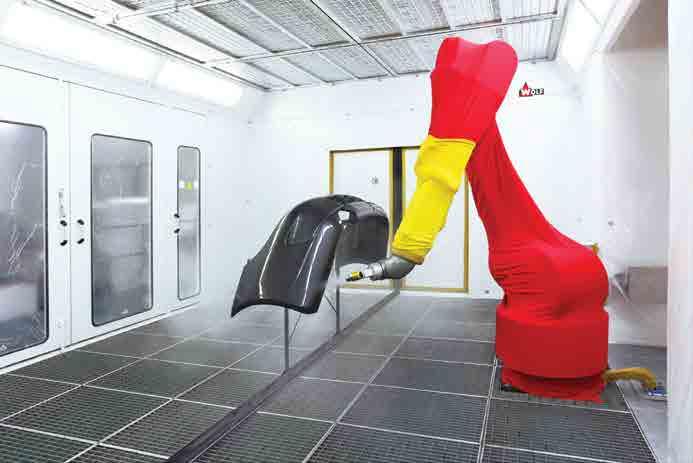
IT was back in 1950, in the heart of the world’s largest hop-growing region Hallertau, that Anton Wolf started a business that dealt with the development and construction of hop kilns. Soon he developed the first German hop-picking machine, followed by the manufacture of air heaters and hot air generators for industrial use – the birth of the air conditioning division. In 1972 WOLF added the production of painting and drying booths for refinishing which led to the Surface Technology division.
The interplay of innovative ideas, continuous product development, advanced manufacturing and production technology and, not least, the commitment and loyalty of employees has enabled the company to grow from a family business to a mediumsized industrial enterprise.
Currently around 280 people, mainly from the region, are looking after customers – from research and development, planning, design, manufacturing to installation and customer service. Planning and construction are located exclusively in-house, and the production is equipped with the most modern CNC manufacturing and processing machinery in conjunction with a CAD - bending cell. The premises cover a total area of around 93,000m².
Hi-tech products for many applications
“We have chosen the motto ‘Spirit of Air’, because the common factor between hop picking machines, air conditioning units and paint booths is the use of air in different ways. The processes range from blowing, extracting, cooling or warming, filtering and cleaning through to drying, moistening and silencing.” explains Mr Vogl-Wolf.
Air conditioning units are the company’s core products – offered in a very diverse range. There are industrial units for heating and ventilation of large areas such as warehouses, high temperature equipment for process engineering, roof top units, hygiene and refrigeration air handling units as well as full air handling units.
Satisfied customers include hotels, large hospitals, rehabilitation centres, airports, schools and institutes, swimming pools, shopping centres and many more. “We make one of the best ‘weatherproof’ air conditioning units for interior and exterior use, up to the highest class T1/TB1, as well as fulfilling the highest hygiene requirements for operating theatres.”
“We keep pushing the development of our products, so that we can stay ahead of the field. We also need to look out for constantly changing norms and guidelines that are issued by legislative and professional bodies. When we build a customised system we need to make sure that it is future proof by incorporating the latest know-how and technologies.”
The company holds German and international patents and licenses for its own technologies such as the latest Red-Eye System. This innovation minimises the energy consumption of paint and drying booths by measuring the temperature of the painted object rather than that of the environment – thereby controlling and optimising the drying process. With this system the engineers have managed to implement the principle of “not one degree too high or one minute too long.”
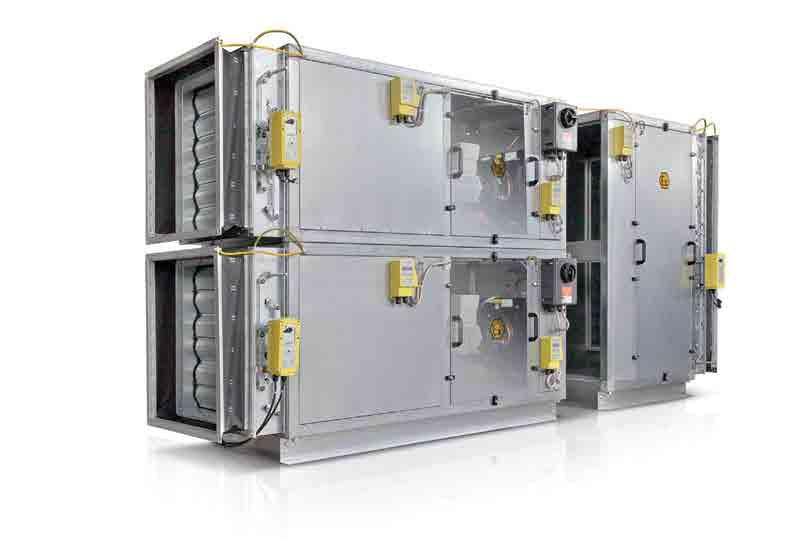
Solid setup across the market
“Our production is 100 per cent located in Geisenfeld, Germany. We are shareholders in a small refrigeration plant specialist nearby, which complements our capacities perfectly and which gives us a competitive advantage.” For the future there is enough capacity for extensions on the 93.000 square metres owned by the company. There are already plans for a second production line which will be started as soon as the order books require this – for an immediate increase of production capacity.
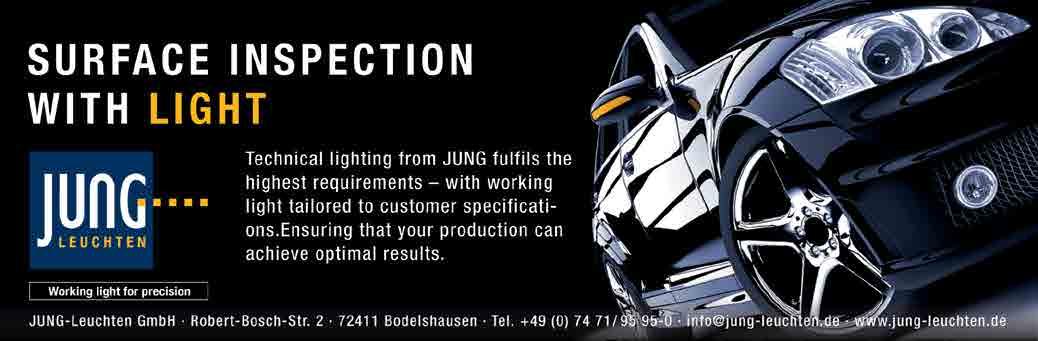
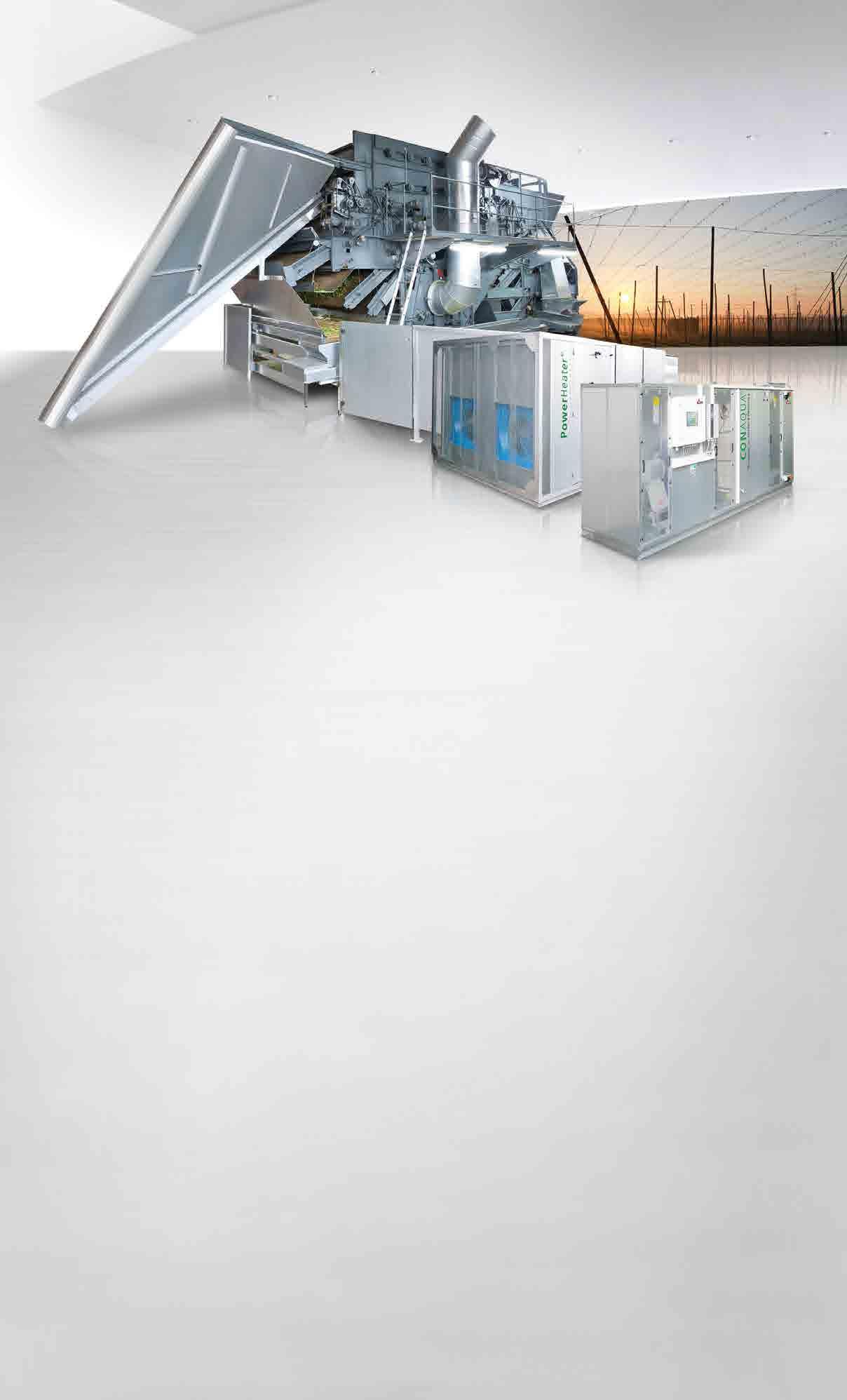
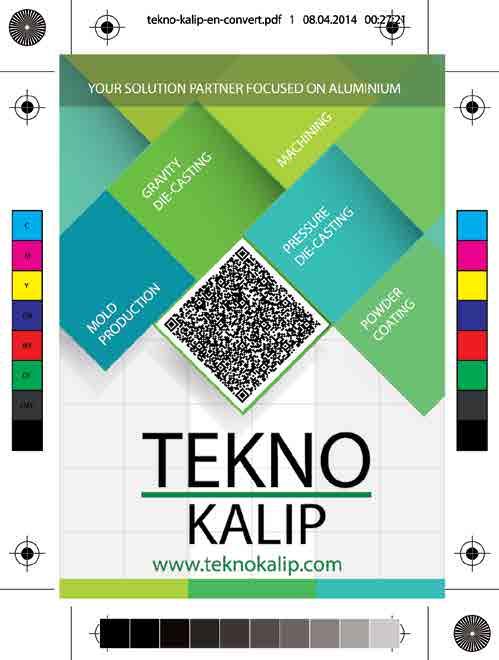
“With a tight network of service centres across Germany, an Online Service Center and excellent spare parts supply we can offer high product safety and reliability for our customers.” says Mr Vogl-Wolf. “In addition, we have a network of technical customer advisers as well as representatives within and outside of German borders.
“Our supplier list today does not differ much from the one we had 10 years ago. We are a family business, and we stand by our suppliers. To name a few, we work with AAF-Lufttechnik, Aerotechnik, BTN, Danfoss, EBM Papst, E+S Eisen+Stahl Service Center, HerkulesHebetechnik, Hombach Wärmetechnik, Jung Leuchten, Klingenburg, Pflaum & Söhne Bausysteme, Siemens, Stahl-Metall-Service und Ziehl Abegg (in alphabetical order). Technology at home in many markets
In the division of agricultural machines WOLF has customers in hops farming worldwide. Currently there is a focus on export markets and on new application areas like tea drying. Well known customers in the division of surface technologies include major automotive brands, the paint industry as well as paint institutes, but also machine builders and general industry. Within this division there is also currently much emphasis on export activities, but also in industrial coating systems. In air conditioning, which is the strongest in terms of sales, the main market is still Germany, but there are local offices in Austria, Afghanistan, Holland, Norway, Poland, Russia and Sweden.
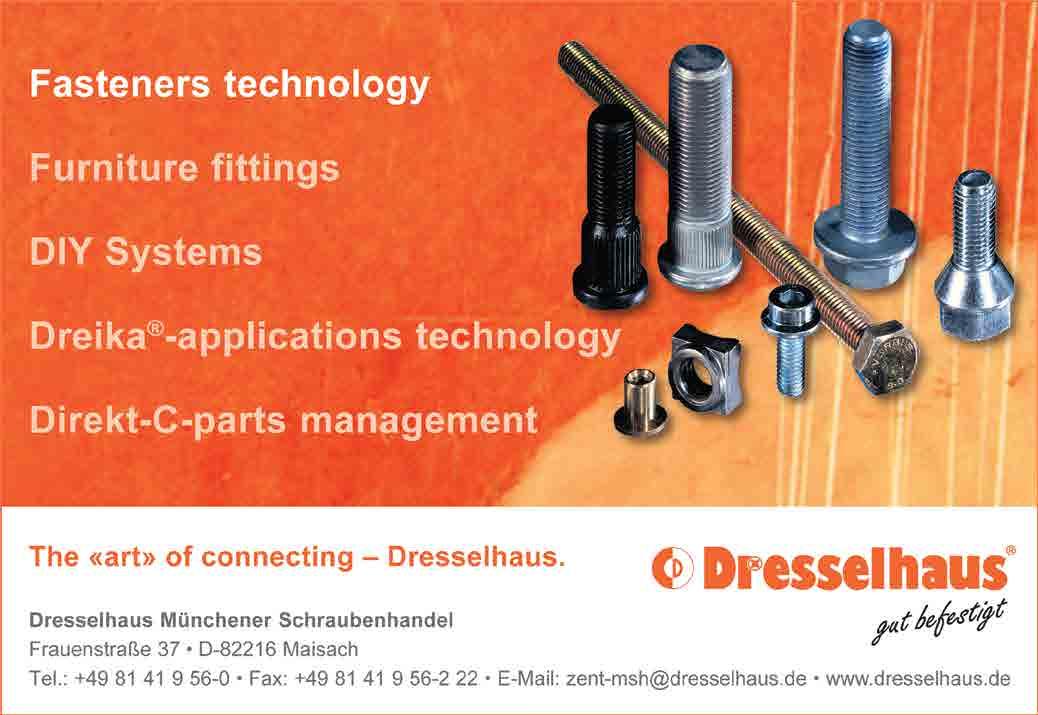
Steady path ahead
“While the world’s population is growing, we see potential for growth in surface technologies and in air conditioning. In air conditioning it is working in our favour that automated air conditioning systems have definitely replaced the manual control of room temperatures as a much more efficient method.” says Mr Vogl-Wolf. “When it comes to growth, we prefer a steady step by step approach, but of course we see that consolidation is happening all over the markets. Acquisitions are part of this, but we cannot say whether there may be one on the cards for us in the future.”
There is a strategic document entitled Agenda 2020, which outlines WOLF’s further development plans. “We are serious about reaching our goals, we work hard every day and we keep re-aligning the milestones as we go.” n
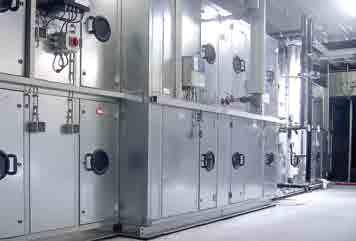
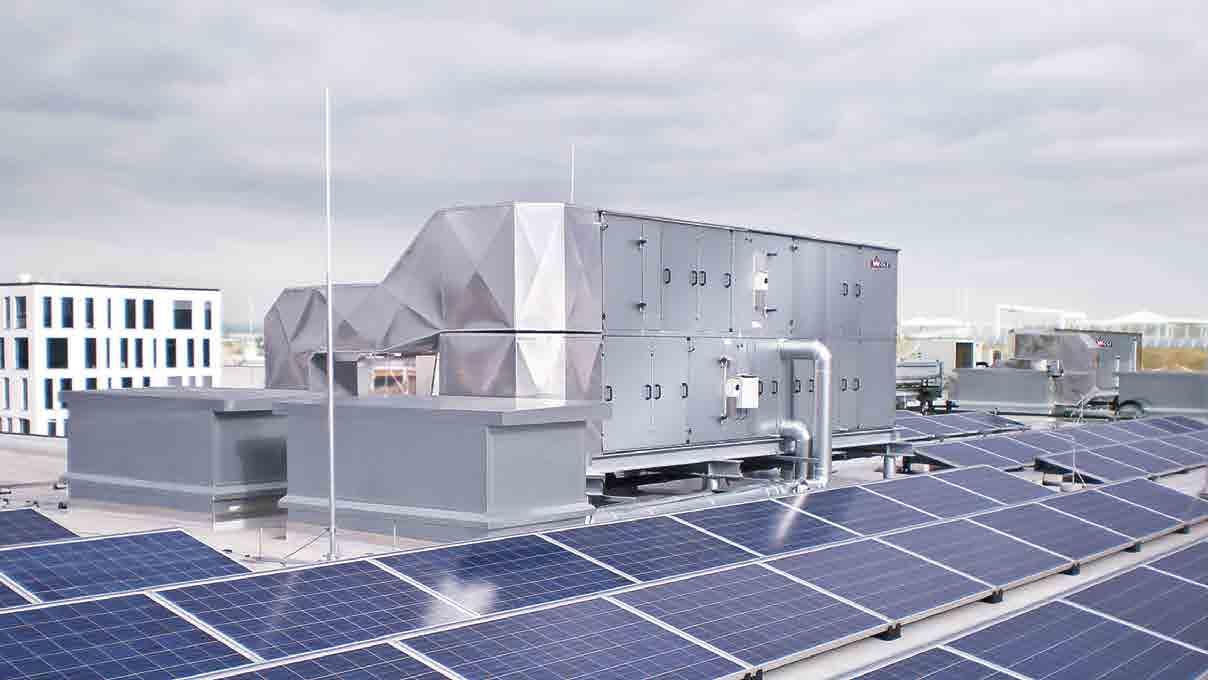