
8 minute read
Heavy lifting Bridon
HEAVY LIFTING
Bridon’s high performance wire and ropes are meeting the most demanding challenges in construction, mining and oil and gas extraction around the world. Peter Mercer reports.
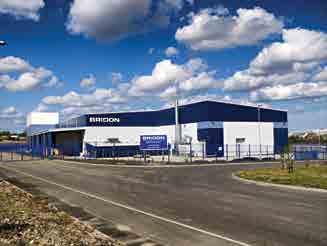
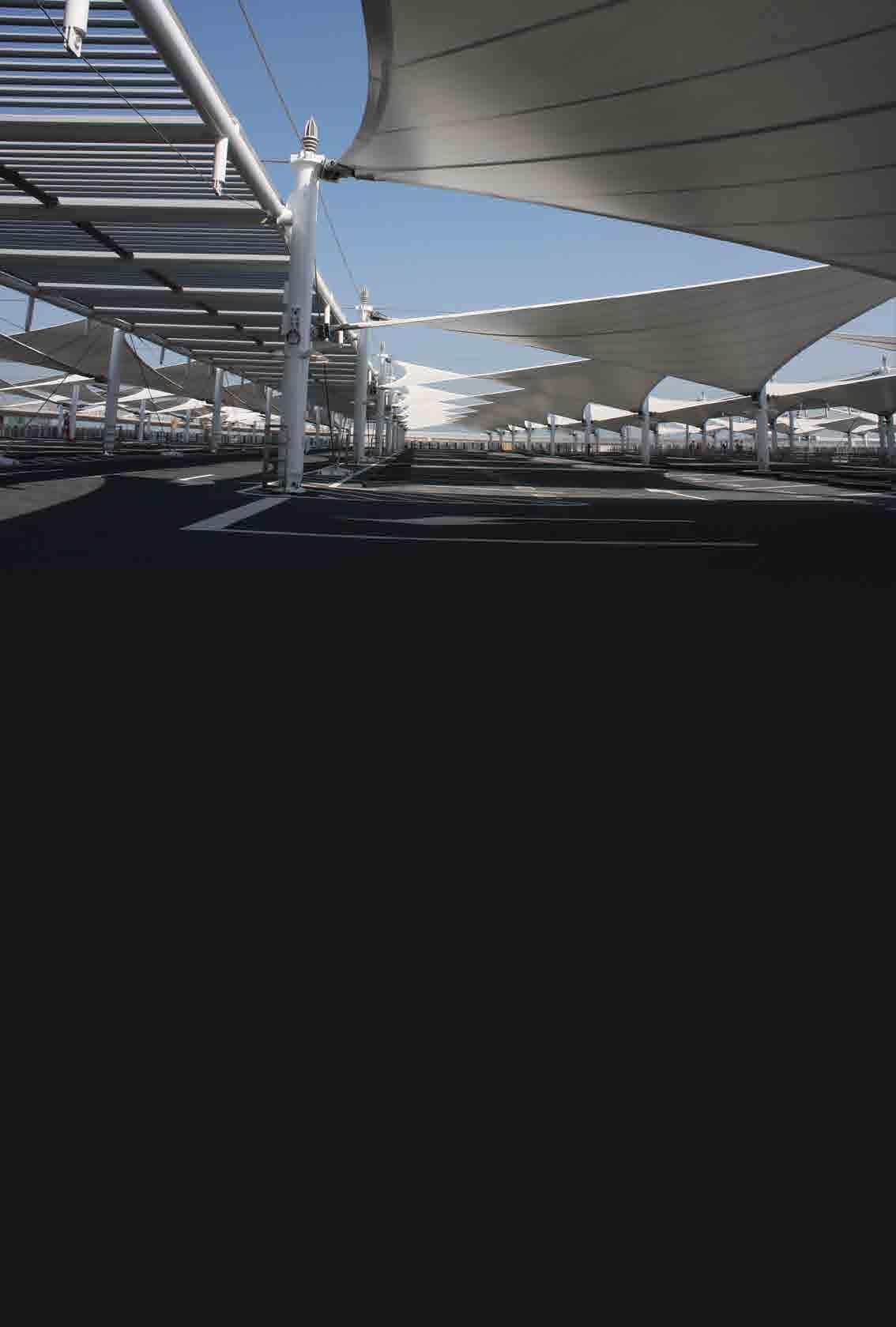
Bridon International is the world’s leading specialist in the manufacture of steel wire and ropes for technically demanding applications in mining, construction, offshore oil and gas and in many other specialised areas of engineering. Its steel and wire rope has been used in high-profile projects across the world, from Wembley Stadium and the Newport City Bridge in Wales to the Inchon Munhak Stadium in Korea and the Kiev Olympic Stadium.
“There are many rope manufacturers across the world but I think it’s fair to say that Bridon has no real direct competitor,” says managing Director Jonathon Templeman. “We produce technically advanced, very high performance ropes and wires that are almost like a machine – they are highly engineered, with moving parts that often require lubrication and they can cost as much as £1 million for a single rope. The core of our business is very heavy lifting – ropes for deep shaft mines, for example, can go down to more than 3 km in a single fall and deepwater offshore lifting can also require 3 km ropes that have to be able to withstand extreme pressures, low temperatures and corrosion from the sea.
“Modern rope design is essentially the art of an intelligent compromise between strength and flexibility. Static and structural ropes prioritise strength because they don’t need to bend much but ropes for mining or offshore mooring must be able to cope with movement.”
Bridon was formed as a company in 1924 from an amalgamation of wire rope producers, the oldest of which dates back to the late 18th century. In 2008 it was acquired by the specialist manufacturing investor Melrose PLC. Headquartered in Doncaster, South Yorkshire, Bridon currently operates eleven manufacturing units worldwide, four in the UK, three in North America and one each in Germany, China, Indonesia and New Zealand.
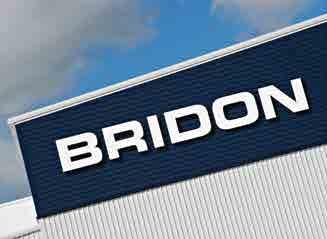
Neptune Quay
In November 2012 Bridon opened its newest manufacturing facility, a state-of-the-art factory at Neptune Quay on the banks of the River Tyne that is capable of producing the largest and most complex ropes in the world, with pieceweights of up to 600 tonnes, for the offshore oil and gas industry. Neptune Quay is home to the world’s largest rope-closing machine (the stages of rope production include drawing the wire, stranding it and then closing it around a core). This machine, which was constructed to Bridon’s own unique specification, is enabling the company to produce far more complex ropes than has ever been possible before in such large weights. These highly engineered ropes feature enhanced breaking loads, optimised bend fatigue performance, effective lubrication and minimal rotation under load.
The Neptune facility ships to the company’s customers across the world and is a key element in its strategy of expanding into a range of developing markets where its ropes are used in the most challenging environments where they have to withstand the ravages of salt water and temperatures down to minus forty degrees centigrade. It has a central role in Bridon’s vision for the future and will act as a base for technological innovation in rope manufacturing across the world.
“Neptune Quay is now our most important site for serving the offshore industry – its waterside location means we can load directly on to supply vessels and we have an innovative transport stander that can move units of more than 600 tonnes,” explains Mr Templeman. “But our nearby Willington Quay factory continues to produce many of our core products for construction, mining and industrial applications. Crane ropes, for example, for ports, steel mills and construction projects are made there. And at our headquarters, the Doncaster Wire Mill and Ropery, we have a 60,000 tonne wire mill that supports all the UK plants and the plant in Germany.”
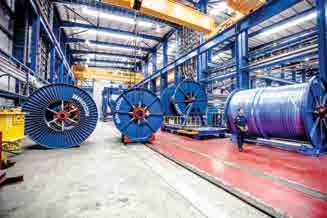
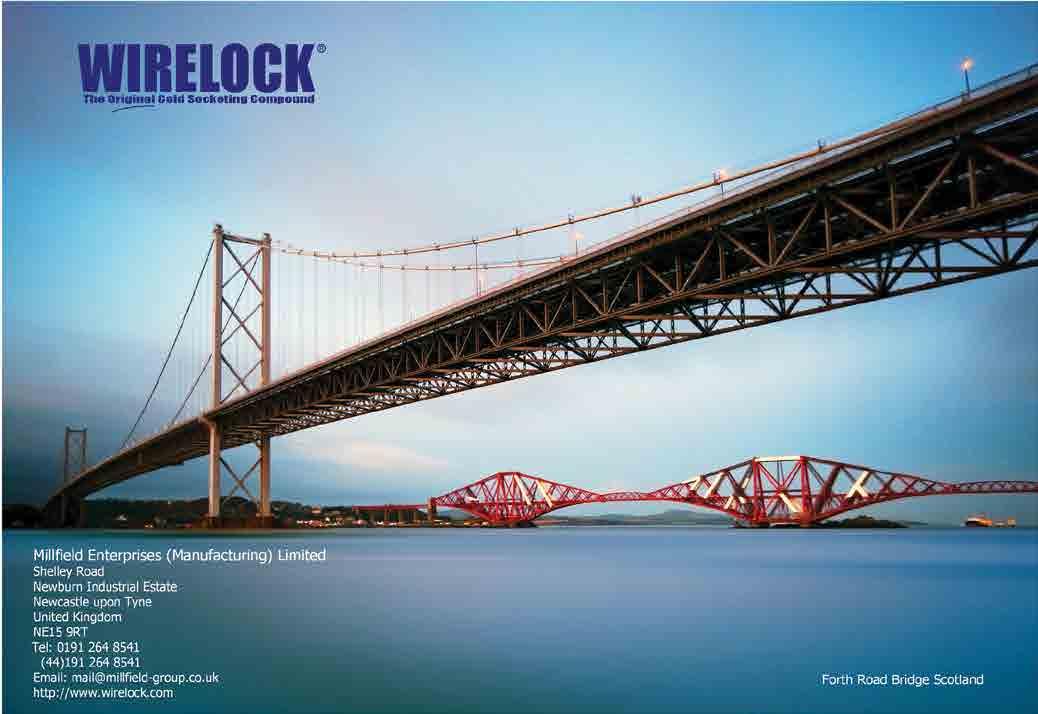


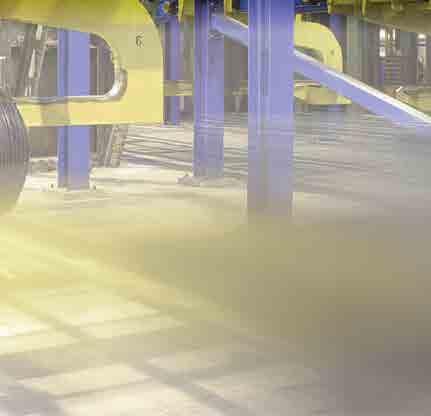
TRINECKE ZELEZARNY (TZ) is a fully integrated operation manufacturing 2.2 million tonnes of basic oxygen steel per annum in a comprehensive range of long products.
MORAVIA STEEL, the parent company, is primarily responsible for the supply of all raw materials, the sale of the final products and the many logistics activities necessary to achieve the planned production targets of TZ.
Wire rod in coil forms an important part of the product range.
The wire rod mill was reconstructed 15 years ago to improve quality and this year will be further enhanced with the installation of new equipment specifically aimed at providing our customers with material improvements which will strengthen the supply chain through to the final product.
By mutual cooperation with our customers the mission is that we can continue to develop our companies for the next generations.
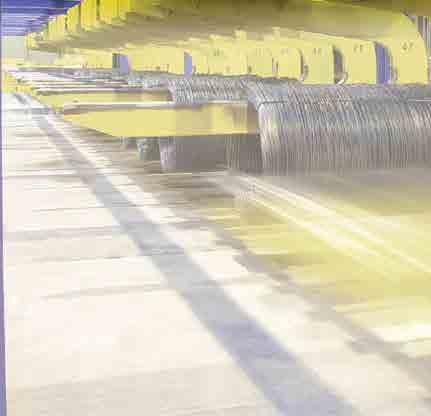
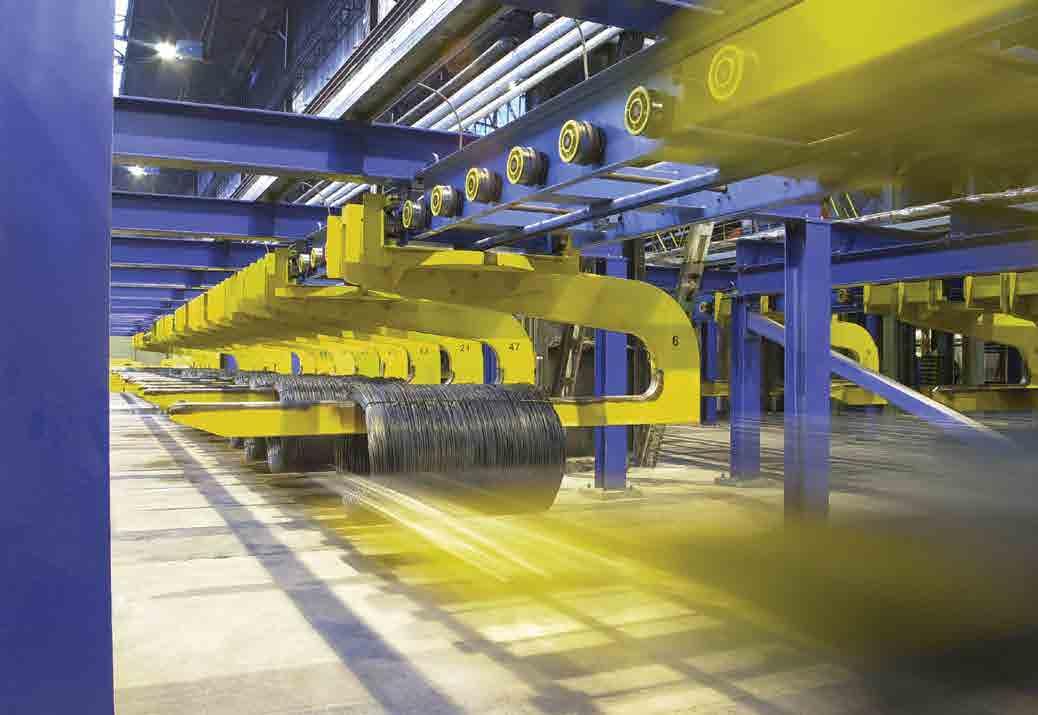
MORAVIA STEEL and TRINECKE ZELEZARNY wish BRIDON INTERNATIONALLTD every success with their future plans.
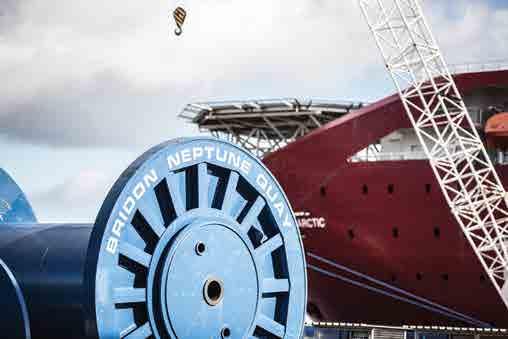
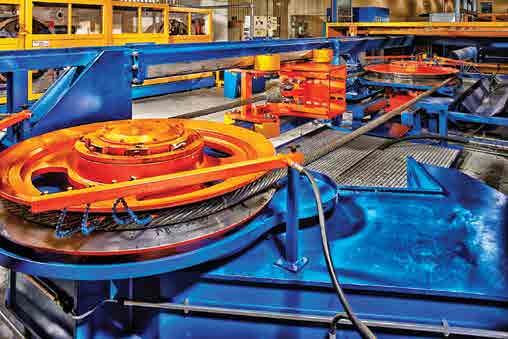
Technology innovation
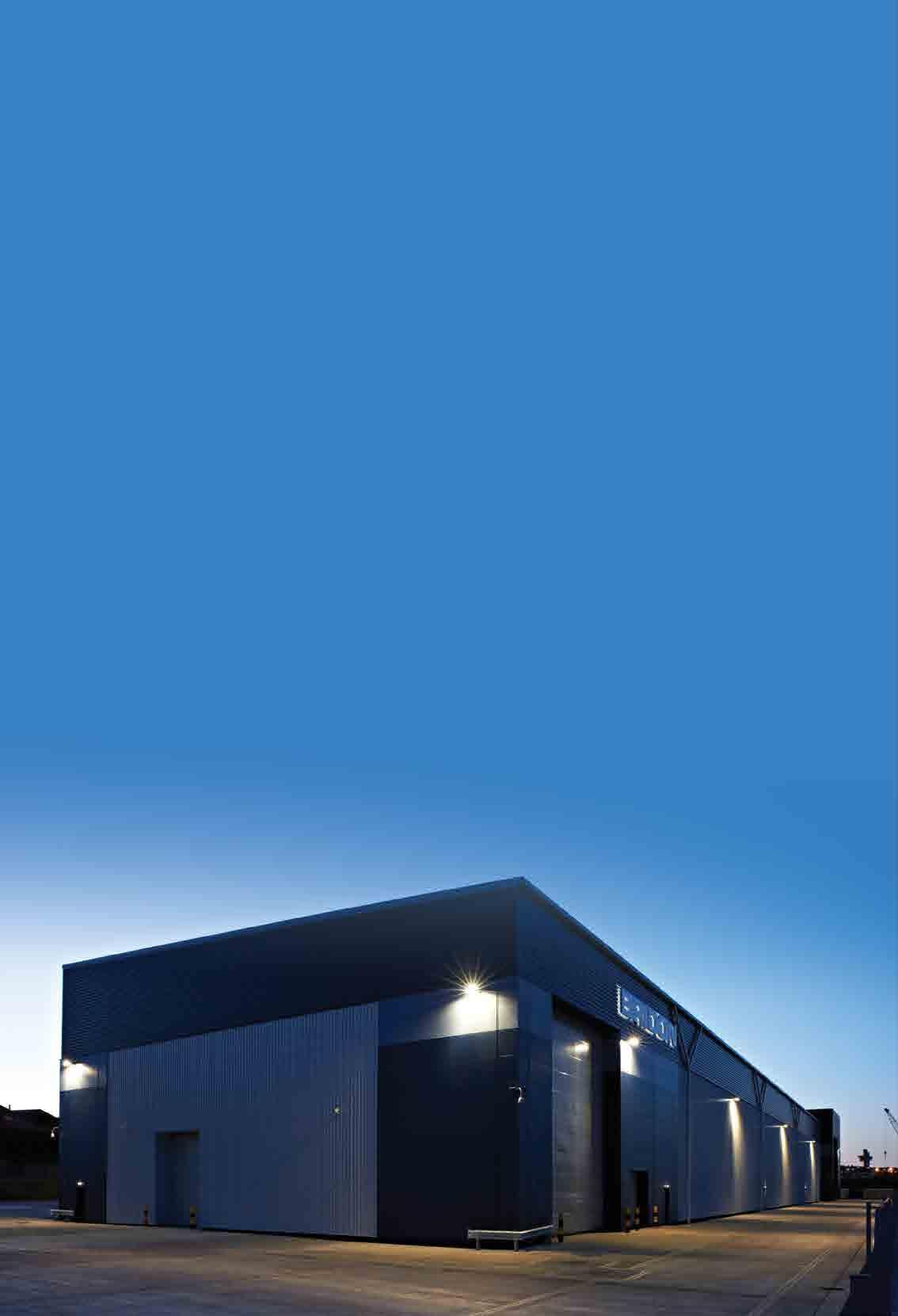
Doncaster is also home to Bridon’s new Technology Centre which was opened in February 2013 specifically to lead the development of the world’s most advanced offshore ropes. However this major investment in personnel, unique test equipment and forensic laboratories will also advance the development of rope technology across Bridon’s core markets of mining, construction and fishing as well as in oil and gas.
“As well as playing a key role in new product development the BTC also offers our customers an extensive range of unique facilities for testing, analysing and verifying new and used ropes. If a rope fails – and it won’t often be one of ours – we can carry out a detailed inquest,” says Jon Templeman. “The Centre also expands our ability to do more joint technological development with our customers. In the lifting world the demand is for longer, stronger and lighter ropes – offshore work is much deeper than in the past and mining is going to similar depths so customers want ropes that put the lightest possible load on their winches or cranes but still have massive lifting capabilities.”
Recent technological innovations from Bridon include the Big T Bristar dragline rope that has been engineered to withstand the most challenging dragline applications in open-pit mining and the Tiger 24 LS hoist rope that delivers the lowest possible cost per tonne hoisted. The Endurance Dyform DSC8 crane rope is another significant advance with its very high breaking force and crush-resistant characteristics.
“In the DSC8 we achieve the superior crush resistance by compacting the metal and it also benefits from the expertise we have developed in the technology of synthetic cores,” explains Mr Templeman. “Rather than injecting the plastic to form the core we extrude it at the same time as drawing the rope. The next generation of ropes will be hybrid products that blend steel and synthetic strands in the same rope. We are currently doing a lot of research in this field.”
Global opportunities
The global oil and gas production industry is currently Bridon’s fastest growing customer sector, making up 35 per cent of current business and expanding rapidly in regions such as the North Sea, the Gulf of Mexico, West Africa and Brazil. “Mining until last year made up around 20 per cent of our business but has fallen away following the problems in the global industry,” says Jon

Templeman. “Fishing is a fairly small sector but it is solid and growing as fishing quotas are increased across the world while the construction and industrial demand tends to follow the overall growth – or lack of it – in the UK economy.”
Of course, Bridon serves customers in the construction industry across the world. A recent major project was for the new Doha International Airport for which Bridon supplied a total of 1400 stainless steel ropes, mostly to support a car park canopy. The 150 tonnes of Dyform strand was manufactured at Gelsenkirchen and delivered in time for the grand opening of the airport on Qatar National day in December 2012.
Looking to future growth prospects, Mr Templeman sees opportunities across the world, in Asia, Africa and South America. “In China there is continuing rapid growth in the construction of ports and of other infrastructure projects and that means many more cranes that need our hoist ropes. The offshore oil and gas industry in China is also growing so that’s another valuable market for a company with our unmatched expertise. There is obviously huge potential for the offshore industry in Brazil, where we opened a warehouse and a service centre last year, and mining remains a strong market there as well as in Chile and Peru. Indeed, as our business grows in the region we may well find we need to set up a manufacturing operation in Brazil. In south-east Asia we already have facilities in Singapore and Indonesia and we have recently expanded our sales office in Russia and set up another in Poland. Africa too has huge potential for growth in oil and gas, mining and infrastructure projects. In fact, wherever in the world there is a need for really heavy lifting, Bridon will be providing the answers.” n
Basamro
Basamro aims to be not just a supplier, but an integral part of our customers’ operations. Given our long-term relationship with Bridon, we are confident that we have succeeded in this aim. Our business relationship with Bridon is based on friendship, trust and reliability, and gives them the confidence to entrust their valuable cargo to us. We at Basamro provide shipments from the UK and the Continent to the former USSR countries and beyond. We hope to be working with Bridon for many years to come.
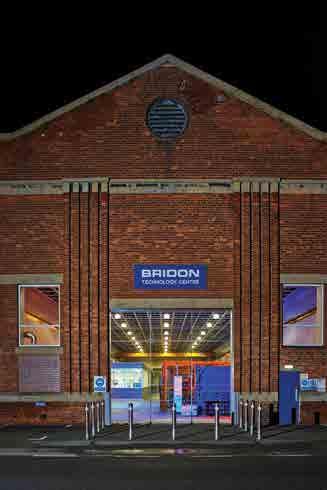