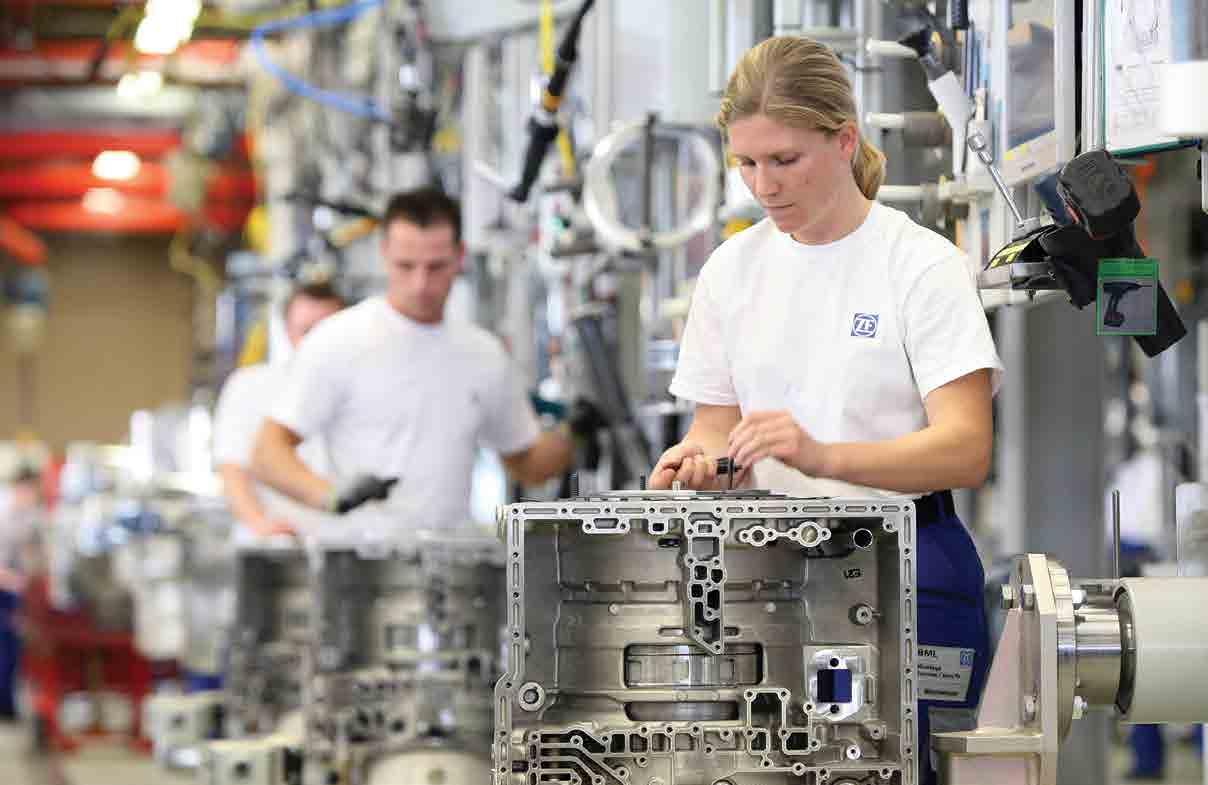
6 minute read
World-class driveline technology ZF Friedrichshafen
WORLD-CLASS DRIVELINE TECHNOLOGY
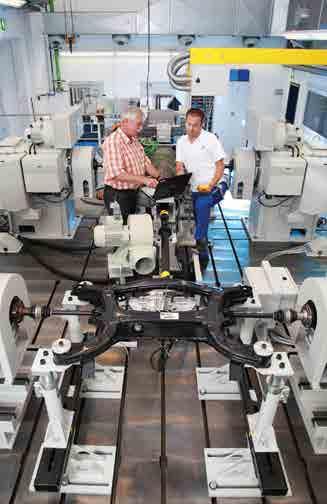
ZF Friedrichshafen is a global leader in driveline and chassis technology with 121 production facilities throughout the world. This year the company laid the foundation stone for its new corporate headquarters. Industry Europe finds out more about its European production facilities, latest supplier awards and world-class product innovations.
Founded in 1915, German ZF Friedrichshafen Group originally focused on the development and production of transmissions for airships and vehicles. Today, its product range includes transmissions and steering systems as well as chassis components and complete axle systems and modules. The group’s overall turnover for 2013 was around €17 million, confirming its position as one of the top 10 automotive suppliers worldwide.
In February 2014, ZF laid the foundation stone for a new Corporate Headquarters in Friedrichshafen. After its completion, this will offer employment for 600 office workers and provide visitors with a unique insight into the work and history of the group. It will also increase the group’s R&D capacities and ease pressure on its existing Research Centre in Graf-von-Soden-Platz, as CEO Stefan Sommer has explained: “Once the
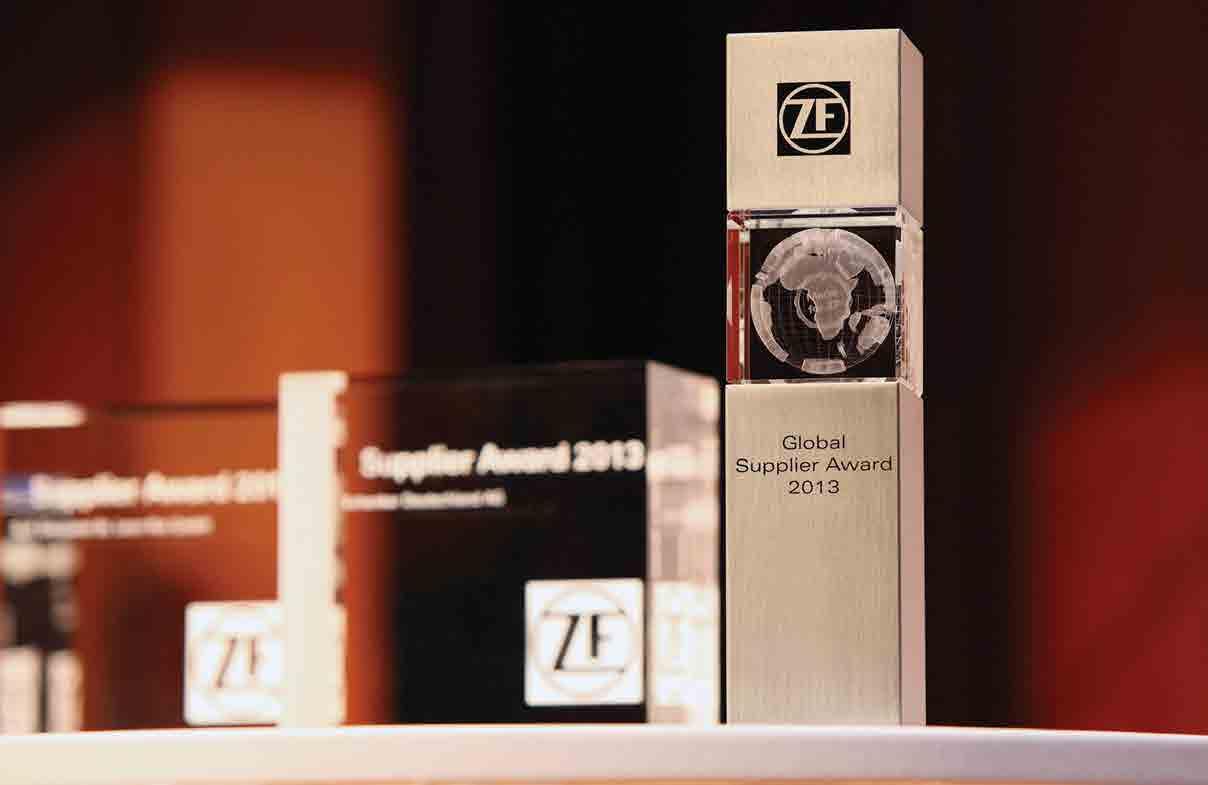
central departments are transferred to the ZF Forum, the R&D Centre will be able to refocus its core task and we can pool and rearrange ZF Group’s Corporate Research and Development.”
European presence
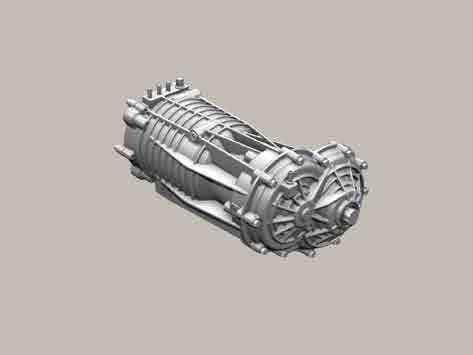
In addition to its German headquarters, ZF has many separate facilities throughout Europe. Today it is present in France, Italy, Poland, Portugal, Turkey, Spain, Ukraine, the UK, Russia and Hungary, to name just a few. To maintain its leading position, the group is constantly expanding its European production capacities.
For example, in January this year it inaugurated a new production building for commercial vehicle transmissions in Russia. Through an existing joint venture between ZF and Kamaz, Russia’s largest commercial vehicle manufacturer, a modern production facility in the city of Naberezhnye Chelny covering an area of 20,000m2 is now in operation. This is part of an ongoing investment package totaling €90 million which the partners will use to expand capacities at the location by 2016.
Key products
ZF’s range of products is so vast that it would be impossible to list them all here; it would therefore make sense to mention just some of the highlights. For example, it recently became the first transmission manufacturer worldwide to develop a modern passenger car automatic transmission with nine gears. It was designed for vehicles with transverse engines and front or four-wheel drive and can therefore be installed in 75 per cent of all cars produced worldwide. This concept can replace the company’s previous eight-speed automatic transmission for cars, designed to achieve more than 6 per cent fuel savings.
The company has also hit the news with its adaptive clamping system CDC (Continuous Damping Control), which entered volume production for the first time in the new Honda Civic Tourer in February 2014. The CDC for both axles, which has been a major success for the ZF for years, has now been specially adapted by the supplier to meet the requirements of subcompact and compact cars as well as MUVs.
Uwe Coßmann, head of ZF Car’s Chassis Technology division, said of this partnership
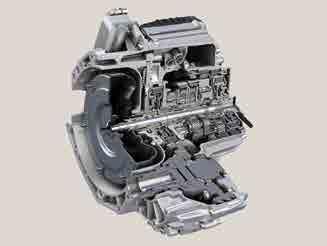
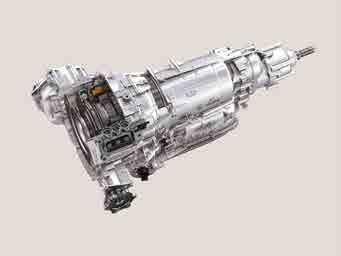
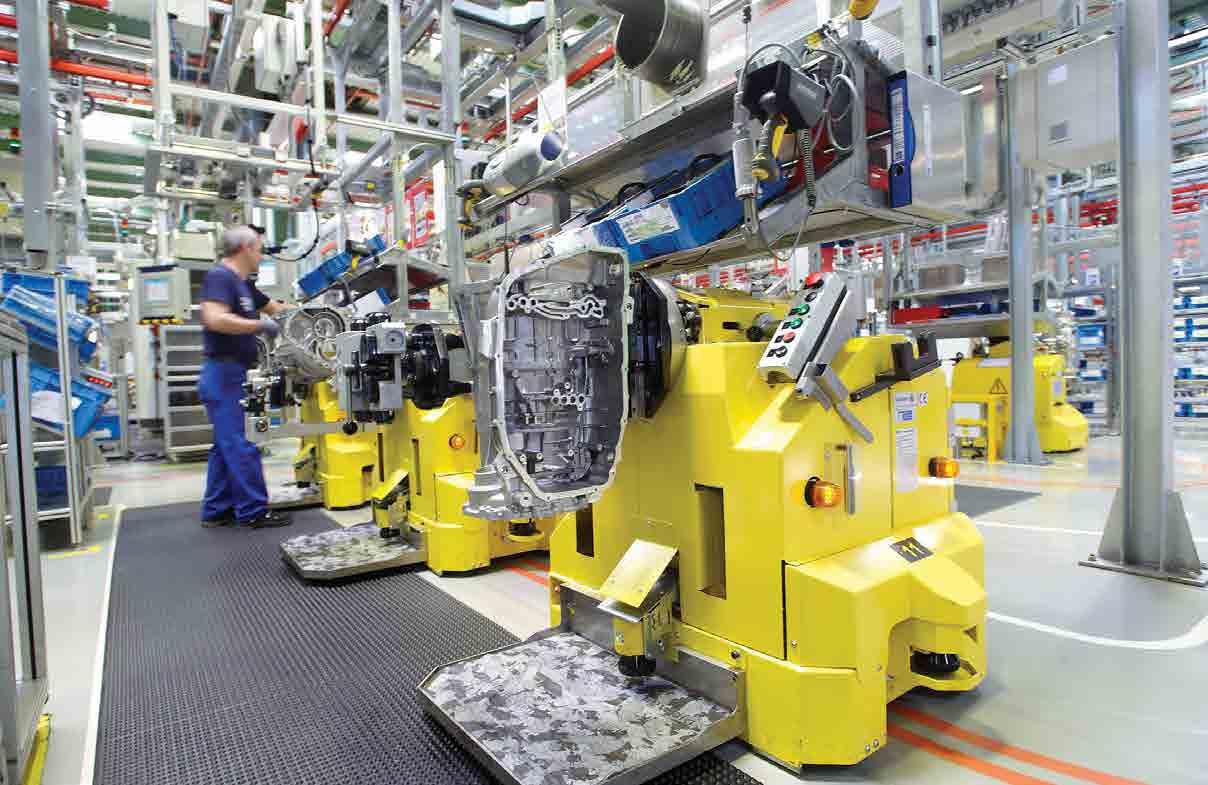
with Honda: “We are very pleased about the world’s first application of the CDC 1XL – particularly because it takes places at Honda, a large, globally active automotive manufacturer. The product showcases the potential of our technical solution for compact and subcompact cars.”
ZF’s CDC 1XL, the electronically controlled adaptive clamping system, will minimize the effects of large rear axle load fluctuations in the new Tourer. A control system analyses the data on road condition, payload, vehicle speed and drivability collected by the integrated sensor system and optimally adjusts the characteristic curve within milliseconds. All of this is possible thanks to electronically controlled proportional valves which minimise oil flow in the damper tube (for hard damping characteristics) or will expand the diameter once again (for soft suspension).
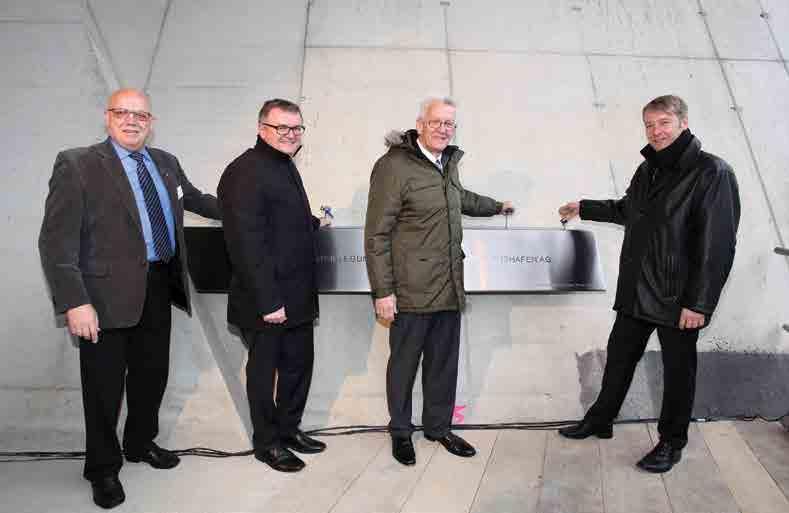
Strong in R&D
R&D is crucial to ZF’s overall business strategy, helping it to maintain its strong global position. In all, the group invests around 5 per cent of its total revenue (about €838 million) in research and development each year. In the years to come it expects this figure to grow to 1 billion annually in order to increase its strength and remain ahead of the growing competition.
In February 2014, the company announced it will be bolstering Corporate Research and Development at its headquarters with the establishment of a new testing centre for transmissions in its Research & Development Centre on Graf-von-SodenPlatz in 2015 and 2016.
The testing centre will be built in the western part of the R&D Centre. The new building will be home to test benches and workshops. The plan is for modular fixtures to be installed so the building can be used for various purposes depending on the research and development requirements.
The importance of supply relationships
In part, ZF Friedrichshafen’s worldwide success is down to the strong global supplier network it has built up since its establishment. The importance of certain of its key suppliers was recognised in November 2013 at the company’s sixth annual supplier awards ceremony. This year was a first in one way, however, as the award winner in the ‘Innovation’ category was decided through a concept competition.
The jury found the most outstanding innovation to be a concept for separation springs made of tempered flat wire, developed by Mubea Tellerfedern GmbH from Attendorn. Not only does this innovation increase the service life of springs installed in transmissions, it also saves space and weight and provides for more comfort and efficiency.
In the other categories, winners were determined in the same way as in previous years – by means of a standardised selection procedure. In the Production category there were three winners: Veldener Präzisiontechnik GmbH, which supplies ZF with a variety of finished parts from bolts and sleeves to pistons; SLR Giesserei St. Leon-Rot GmbH produces housings and axle brackets; and Rausch und Pausch GmbH in Selb that produces items such as solenoid valves for ZF’s 9-speed automatic transmission.
DB Schenker, one of the world’s biggest logistics groups, was the winner in the Non-Production Materials category. This is in recognition of the fact that DB Schenker ensures on-schedule and reliable transport for all group divisions. Meanwhile, a top supplier in the area of massive forming and machining of steel and aluminium is Hirschvogel Umfortechnik GmbH. The winner in the Global Supplier category produces and provides ZF with forged and finished parts in excellent quality.
The award in the Energy Efficiency category was presented for the second time, this year to Teamtechnik Maschinen und Anlagen GmbH. This company is an expert in highly flexible assembly and test equipment, supplying ZF’s Saarbrücken location and realising a highly innovative solution for electromobility at its headquarters in Freiberg: the first self-sufficient photovoltaic system with storage battery in Baden-Württemberg. n
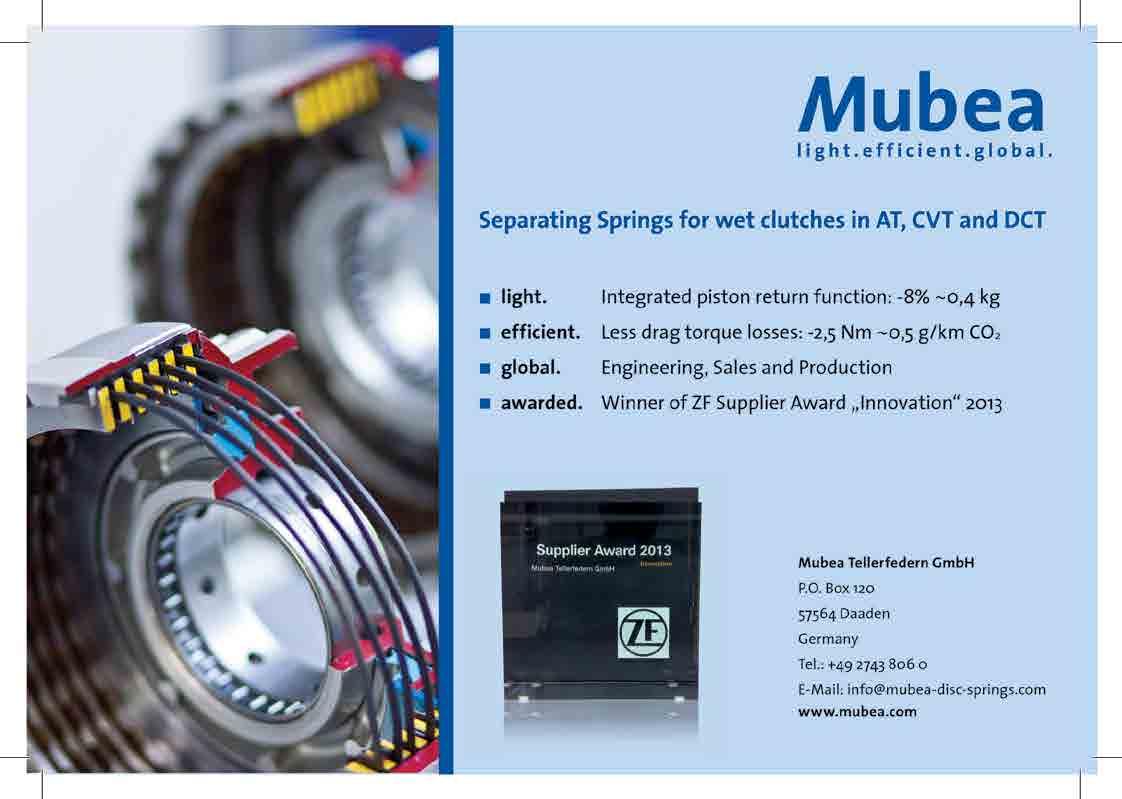